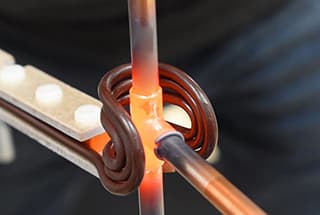
Have you ever wondered how cast iron, with its complex structure, can be seamlessly joined? This article explores the fascinating process of brazing cast iron, detailing the types of filler metals and fluxes used, and the precise techniques required. Whether you’re looking to enhance your metalworking skills or understand the science behind this method, you’ll find valuable insights on achieving strong, durable joints. Dive into the world of brazing and learn the secrets to perfecting this essential skill.
(1) Filler Metals
Copper-zinc filler metals and silver-copper filler metals are mainly used for brazing cast iron. Common copper-zinc filler metal grades include B-Cu62ZnNiMuSiR, B-Cu60ZuSnR, and B-Cu58ZnFeR, etc.
The tensile strength of brazed cast iron joints is generally between 120-150 MPa. By adding elements such as Mn, Ni, Sn, and Al to the copper-zinc filler metals, the strength of the brazed joints can be made equivalent to that of the base material.
Silver-copper filler metals have low melting temperatures and can avoid the formation of harmful structures when brazing cast iron. The performance of brazed joints is good, especially with the addition of Ni, such as B-Ag50CuZnCdNi and B-Ag40CuZnSnNi.
These strengthen the bond between the filler metal and cast iron, making them particularly suitable for brazing ductile iron, achieving joint strength equivalent to that of the base material.
(2) Flux
When brazing cast iron with copper-zinc filler metals, FB301 and FB302 fluxes are mainly used, which are mixtures of borax or a mixture of borax and boric acid. In addition, fluxes composed of 40% H3BO3, 16% Li2CO3, 24% Na2CO3, 7.4% NaF, and 12.6% NaCl have better effects.
When brazing cast iron with silver-copper filler metals, FB101 and FB102 fluxes can be selected, which are mixtures of borax, boric acid, potassium fluoride, and potassium fluoroborate.
Before brazing cast iron, it is necessary to carefully remove impurities such as graphite, oxides, sand, and oil from the surface of the casting.
Organic solvents can be used to remove oil, while mechanical methods such as sandblasting or shot blasting can be used to remove graphite and oxides. Electrochemical methods can also be used. In addition, graphite can be removed by burning it with an oxidizing flame.
Brazing of cast iron can be done using flame, furnace, or induction heating methods. Due to the formation of SiO2 on the surface of cast iron, the brazing effect in a protective atmosphere is not good, so flux is usually used for brazing.
When brazing large workpieces with copper-zinc filler metals, a layer of flux should be sprinkled on the cleaned surface, and then the workpiece should be heated in a furnace or with a torch.
When the workpiece is heated to about 800°C, additional flux should be added and heated to the brazing temperature. The filler metal should be melted and filled into the gap by scraping with a needle tool along the edge of the joint. To improve the strength of the brazed joint, annealing treatment should be performed at 700-750°C for 20 minutes, followed by slow cooling.
Excess flux and residue after brazing can be removed by rinsing with warm water. If it is difficult to remove, it can be washed with a 10% sulfuric acid solution or a 5-10% phosphoric acid solution, followed by rinsing with clean water.