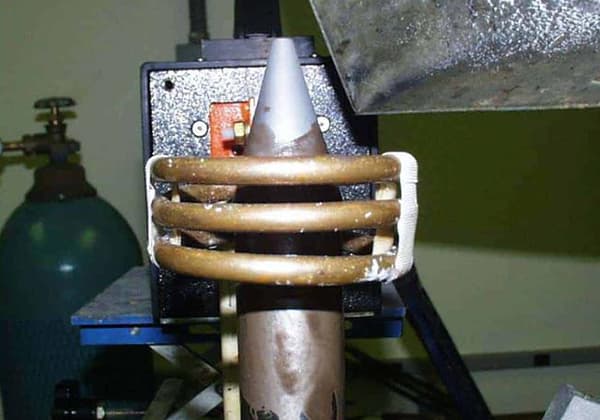
Have you ever wondered how two seemingly incompatible materials, ceramics and metals, can be seamlessly joined together? The process of brazing ceramics to metals involves overcoming challenges like poor wetting and thermal expansion differences. This article delves into the intricacies of brazing, exploring the types of filler metals used, techniques to improve joint strength, and methods to minimize thermal stress. By the end, you’ll understand the science behind creating strong, durable joints between these diverse materials.
Brazing ceramics to ceramics or ceramics to metal components can be quite challenging. Most brazing filler metals form spherical shapes on the ceramic surface, which leads to poor or no wetting.
Brazing filler metals that can wet ceramics tend to form various brittle compounds at the joint interface (such as carbides, silicides, and ternary or multicomponent compounds), which affect the mechanical properties of the joint.
Additionally, due to the significant differences in thermal expansion coefficients between ceramics, metals, and brazing filler metals, residual stress may exist in the joint after cooling from the brazing temperature to room temperature, potentially leading to joint cracking.
The use of active brazing filler metals created by adding reactive metallic elements to conventional filler metals can improve wetting on ceramic surfaces. Employing low-temperature, short-duration brazing can reduce the impact of interface reactions.
Designing suitable joint configurations and utilizing single or multiple metal layers as intermediate layers can help minimize thermal stress in the joint.
Brazing Filler Metals Brazing ceramics to metals is typically performed in a vacuum furnace, hydrogen atmosphere, or argon atmosphere. Brazing filler metals for sealing vacuum electronic devices have additional specific requirements in addition to general characteristics.
For example, the filler metal should not contain elements that generate high vapor pressures to avoid issues such as dielectric leakage and cathode poisoning in devices. It is generally specified that the vapor pressure of the filler metal during device operation should not exceed 10-3Pa, and the content of high vapor pressure impurities should be within 0.002% to 0.005%.
The filler metal’s oxygen content (W(o)) should not exceed 0.001% to avoid the generation of water vapor during brazing in a hydrogen atmosphere, which could cause splattering of the molten brazing filler metal. Furthermore, the filler metal must be clean and should not have any surface oxides.
When brazing ceramics after metallization, alloy brazing filler metals such as copper (Cu), nickel (Ni), silver-copper (Ag-Cu), and gold-copper (Au-Cu) can be used. When brazing ceramics to metals directly, brazing filler metals containing reactive elements such as titanium (Ti) and zirconium (Zr) should be selected.
Among the binary brazing filler metals, Ti-Cu and Ti-Ni are commonly used and can be employed within the range of 1100℃. In the ternary brazing filler metals, Ag-Cu-Ti (with (W)Ti content less than 5%) is frequently used for direct brazing of various ceramics to metals.
This ternary system can be used with foil, powder, or Ag-Cu eutectic filler metal combined with Ti powder. B-Ti49Be2 brazing filler metal exhibits corrosion resistance similar to stainless steel and has a lower vapor pressure, making it a preferable choice for vacuum sealed joints that require oxidation and leak prevention.
In the Ti-V-Cr system, the addition of Cr effectively reduces the melting temperature range, with the lowest melting temperature achieved at 30% W(V). B-Ti47.5Ta5 brazing filler metal, without Cr, has been used for direct brazing of alumina and magnesia, allowing the joint to operate at an ambient temperature of 1000℃. Active brazing fillers for direct bonding of ceramics to metals are shown in Table 14.
Table 14. Active Brazing Fillers for Brazing Ceramics to Metals
Solder material composition (mass fraction) (%)· | Soldering temperature (°C)· | Applications and joint materials |
B-Ag69Cu26Ti5 | 850~880 | Ceramic-Cu, Ti, Nb, etc. |
B-Ag85Ti15 | 1000 | Oxide ceramic-Ni, Mo, etc. |
B-Ag85Zr15 | 1050 | Oxide ceramic-Ni, Mo, etc. |
B-Cu70Ti30 | 900~1000 | Ceramic-Cu, Ti, refractory metals, etc. |
B-Ni83Fe17 | 1500~1675 | Ceramic-Ta (joint strength 140MPa) |
B-Ti92Cu8 | 820~900 | Ceramic-metal |
B-Ti75Cu25 | 900~950 | Ceramic-metal |
B-Ti72Ni28 | 1140 | Ceramic-ceramic, ceramic-metal, ceramic-graphite |
B-Ti50Cu50 | 980~1050 | Ceramic-metal |
B-Ti49Cu49Be2 | 1000 | Ceramic-metal |
B-Ti48Zr48Be4 | 1050 | Ceramic-metal |
B-Ti68Ag28Be4 | 1040 | Ceramic-metal |
B-Ti47.5Zr47.5Ta5 | 1650~2100 | Ceramic-tantalum |
B-Zr75Nb19Be6 | 1050 | Ceramic-metal |
B-Zr56V28Ti16 | 1250 | Ceramic-metal |
Pre-metalized ceramics can be brazed in high-purity inert gas, hydrogen, or vacuum environments. When brazing non-metalized ceramics directly, vacuum brazing is generally recommended.
(1) General Brazing Process for Ceramics and Metals
(1) General Brazing Process for Ceramics and Metals can be divided into seven process steps: surface cleaning, paste application, metalization of ceramic surfaces, nickel plating, brazing, and post-brazing inspection.
Surface cleaning is performed to remove oil stains, sweat marks, and oxide films from the base material surface. Metallic parts and brazing material should be degreased, then acid-etched or alkali-treated to remove oxide films, followed by rinsing with flowing water and drying.
High-quality parts should undergo heat treatment at an appropriate temperature and duration in a vacuum furnace or hydrogen furnace (ion bombardment can also be used) to purify the part surface.
Cleaned parts should not come into contact with oily objects or bare hands and should immediately proceed to the next process or be placed in a drying device, avoiding prolonged exposure to air.
Ceramic parts should be cleaned with acetone using ultrasonic cleaning, rinsed with flowing water, and finally boiled twice in deionized water for 15 minutes each time.
Paste application is a crucial step in the metalization of ceramics. It involves applying the paste onto the ceramic surface to be metalized using a brush or paste applicator.
The coating thickness is generally between 30-60 micrometers, and the paste is typically composed of pure metal powder with a particle size of approximately 1-5 micrometers (sometimes with the addition of suitable metal oxides) and an organic binder.
Ceramic parts with applied paste are then placed in a hydrogen furnace, and sintered at a temperature of 1300-1500°C for 30-60 minutes using wet hydrogen or cracked ammonia. For ceramics with applied hydrides, they should be heated to around 900°C to decompose the hydride and react with pure metal or residual titanium (or zirconium) on the ceramic surface to obtain a metal coating.
In the case of Mo-Mn metalization layer, in order to promote wetting with the brazing material, a nickel layer of 1.4-5 micrometers thick is electroplated or coated with nickel powder. If the brazing temperature is below 1000°C, the nickel layer also needs to undergo pre-sintering in a hydrogen furnace at a temperature and time of 1000°C/15-20 minutes.
The treated ceramics are treated like metal parts and assembled with stainless steel, graphite, or ceramic molds to form a whole. The brazing material is applied at the joint, and the workpiece must be kept clean throughout the entire operation, avoiding touching with bare hands.
Brazing is performed in an argon gas, hydrogen gas furnace, or vacuum furnace. The brazing temperature depends on the brazing material, and to prevent ceramic cracking, the cooling rate should not be too fast. Additionally, certain pressure can be applied during brazing (approximately 0.49-0.98MPa).
After brazing, the welded parts should undergo surface quality inspection, as well as thermal shock and mechanical performance testing. Sealing components used in vacuum devices must also undergo leak testing as per the relevant regulations.
(2) Direct Brazing
During direct brazing (active metal method), the ceramic and metal workpieces to be brazed are first subjected to surface cleaning and then assembled.
To prevent cracking due to different coefficients of thermal expansion, a rotating buffer layer (one or multiple metal sheets) can be placed between the joints. Whenever possible, the brazing material should be placed between the two workpieces or in the gaps filled with brazing material, and then brazed similar to conventional vacuum brazing.
When using Ag-Cu-Ti brazing material for direct brazing, the vacuum brazing method should be employed. Heating should start when the vacuum degree in the furnace reaches 2.7×10-3Pa.
At this point, rapid heating can be applied; however, when the temperature approaches the melting point of the brazing material, it should be heated slowly to ensure uniform temperature distribution across all parts of the joint.
Once the brazing material melts, the temperature should be quickly raised to the brazing temperature, with a holding time of 3-5 minutes. During cooling, slow cooling should be conducted before reaching 700°C, while after 700°C, natural cooling can be allowed.
For direct brazing with Ti-Cu active brazing material, the brazing material can take the form of Cu foil with Ti powder or Cu component with Ti foil, or Ti powder can be applied to the ceramic surface followed by the addition of Cu foil.
All metal parts must be degassed in a vacuum, with the degassing temperature for oxygen-free copper being 750-800°C, and for Ti, Nb, Ta, etc., the degassing temperature should be 900°C for 15 minutes. The vacuum degree at this stage should not be lower than 6.7×10-3Pa.
During brazing, the components to be brazed should be assembled in a fixture and heated in a vacuum furnace to a temperature between 900-1120°C, with a holding time of 2-5 minutes. Throughout the entire brazing process, the vacuum pressure should not be lower than 6.7×10-3Pa.
The brazing process using the Ti-Ni method is similar to the Ti-Cu method, with the brazing temperature being 900±10°C.
(3) Oxide Brazing Method
The oxide brazing method utilizes oxide brazing material that forms a glass phase when melted, allowing it to infiltrate the ceramic and wet the metal surface, thus achieving reliable connections. This method can be used for joining ceramics to ceramics or ceramics to metals.
The main components of oxide brazing materials are Al2O3, CaO, BaO, MgO, and the addition of B2O3, Y2O3, Ta2O3, etc. can yield brazing materials with various melting points and linear expansion coefficients.
Additionally, fluoride brazing materials primarily composed of CaF2 and NaF can also be used to join ceramics and metals, providing high-strength and heat-resistant joints.