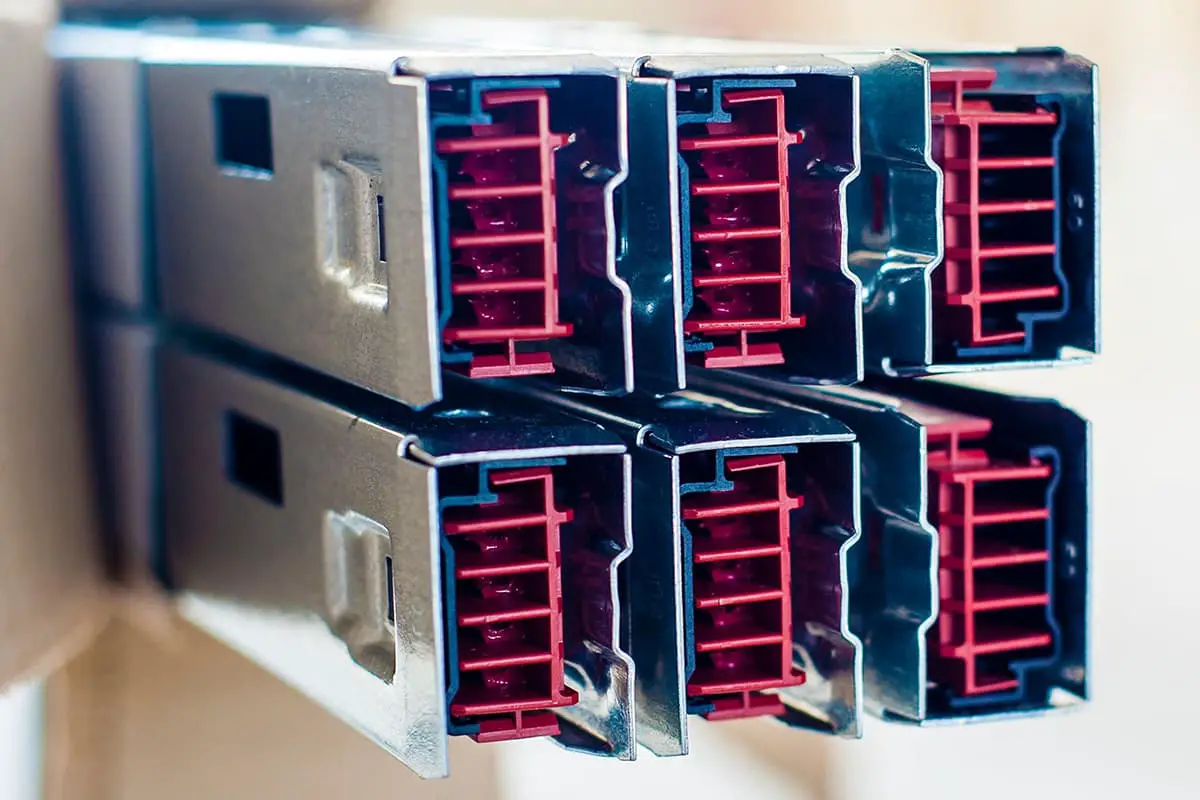
Are you aware that improper installation of busbars can lead to costly and dangerous electrical failures? This article details the comprehensive standards for installing and inspecting busbars, including support brackets, insulators, and bus duct systems. You’ll learn essential guidelines and quality checks to ensure safety, reliability, and compliance in your electrical installations. Dive in to safeguard your projects from common pitfalls and ensure they meet the highest industry standards.
1.0.1 This chapter applies to the installation of busbar support (suspension) brackets, distribution devices, and protective net barriers between electrical equipment.
1.0.2 Inspection of Support (Suspension) Bracket Installation
Operation | Inspection Items | Properties | Quality Standards | Inspection Methods and Instruments | |
Profiled SteelInspection | Structural Steel Specifications | In accordance with design specifications | Comparative Blueprint Design Review | ||
Permissible Deviation for Full Length Straightness of Structural Steel | ≤5mm | Dimensional Examination with a Ruler | |||
Appearance of Bolts and Machined Surfaces | Smooth, without deformation | Visual Inspection | |||
Bracket Installation | Elevation Error | ≤5mm | Level Instrument Check | ||
Horizontal Error | Measurement Verification Using a Ruler | ||||
Vertical Error Along Direction | |||||
Diagonal Error of Brackets | |||||
Fixation of Supports (Hangers) | Mainly | Sturdy and reliable | Lever Operation Inspection | ||
Miscellaneous | Paint | Rust removal | Clean, rust-free | Visual Examination | Visual Examination |
Application of anti-corrosive paint | Uniform, no missed spots | Uniform, no missed spots | |||
Grounding | Mainly | Solid, with good conductivity | Engage and conduct inspection. |
1.0.3. Inspection of Protective Mesh Installation
Process | Inspection Items | Properties | Quality Standards | Inspection Methods and Tools | |
Structural Steel Inspection | Profile Steel Specifications | As per design specifications | Comparative review against blueprint designs | ||
Permissible Tolerance for Full Length Straightness of Profile Steel | ≤5mm | Measurement inspection | |||
Appearance of Bolts and Machined Surfaces | Smooth, no deformation | Visual observation inspection | |||
Fabrication of Framework | Frame Welding | Mainly | Sturdy, the appearance and process comply with welding specification requirements. | Pull and observe for inspection. | |
Dimensional Deviation | ≤5mm | Check with a ruler | |||
Diagonal Error | ≤5mm | ||||
Frame Unevenness | ≤5mm | ||||
Installation of Mesh Fence | Mesh Panel Flatness Inspection | No protrusions or depressions. | Inspect with a ruler. | ||
Mesh Opening Inspection | Sturdy, uniform, and consistent. | Perform a lever check. | |||
Gap between Frame and Mesh Panel | ≤5mm | Inspect with a ruler | |||
Vertical Error of Mesh Fence | Mainly | ≤5mm | |||
Miscellaneous | Paint | Mainly | Mainly | Clean, free from rust. | Observation and Inspection |
Application of Anti-Corrosion Paint | Uniform, no uncoated areas. | ||||
Grounding | Grounding of Wire Mesh | Mainly | Reliably grounded with flexible wiring. | Engage and conduct inspection | |
Earthing of Framework | Sturdy, with excellent conductivity. |
2.1 This section applies to the installation of suspension insulator strings, post insulators, and wall-through bushings, among others.
2.2 Inspection of suspension insulator string installation.
Process | Inspection Items | Properties | Quality Standards | Inspection Methods and Tools |
Visual Inspection | Verification of Specifications and Models | As per design specifications, | Observation and inspection. | |
Ceramic Parts Appearance | Mainly | Smooth, intact, and crack-free, | ||
Inspection of Ceramic-Metal Adhesive Joints | Mainly | Firmly bonded, | ||
Connection Hardware and Accessories | Complete and undamaged, | |||
Spring Pin Inspection | Adequately elastic, | Lever Operation Inspection | ||
Uniform Pressure Ring and Shield Check | Whole, without deformation, | Visual Inspection | ||
Installation of Insulator String | Tests Before Insulator Assembly | Mainly | Qualified, | Inspection Test Report |
Direction of Connection Bolts, Rivets, Spring Pins, etc. | Consistent, | Visual Inspection | ||
Coordination between Ball Head Rings, Bowl Head Plates and Locking Pins | Flexible, without obstruction, | Lever Operation Inspection | ||
Check of Connection Hardware Anti-loosening Measures | Mainly | Locknuts tightened against loosening, cotter pins opened, | Visual Inspection | |
Allowable Tilt Angle of Suspension Insulator String (when not designed) | ≤5°, | Visual Inspection | ||
Tension Received by Each String When Insulator Strings are in Parallel | Mainly | Uniform, | ||
Overall Check Before Lifting Insulator Strings | Clean, correctly assembled, cup facing upwards. |
2.0.3 Installation Inspection of Pillar Insulators
Process | Inspection Items | Properties | Quality Standards: | Inspection Methods and Tools |
Visual Inspection | Exterior of Ceramic Components | Mainly | Smooth, intact, and free of cracks. | Visual Examination |
Verification of Ceramic-Iron Adhesion | Adhered securely, without gaps. | |||
Insulator Installation | Error in Insulator Base Level | ≤5mm | Check with a ruler. | |
Error in Centerline of Insulator Pillars within Busbar Branch Segment | Mainly | ≤2mm | Check with a ruler. | |
Vertical Error in Stacked Insulator Pillars | ||||
Thickness of Gasket Between Pure Ceramic Insulator and Metal Contact Surface | Mainly | ≥1.5mm | ||
Fixation of Insulators | Mainly | All bolts are in place and tightly secured. | Check with a wrench. | |
Grounding | Arrangement of Ground Wires | There is consistent directionality. | Conduct a visual inspection. | |
Connection to Grounding Grid | Mainly | The structure is sturdy, with excellent conductivity. | Toggle and check for continuity. |
2.0.4 Installation and Inspection of Wall Penetration Sleeves
Process | Inspection Items: | Property | Quality Standards: | Inspection Methods and Tools | ||
Visual Inspection | Ceramic Part Appearance | Mainly | Smooth, unbroken, and free from cracks. | Observation and inspection. | ||
Ceramic-Iron Adhesion Check | Mainly | Securely bonded with no gaps. | ||||
Installation of Casing | Compatibility of Reserved Hole Diameter and Bushing Insertion Part | >5mm | Check with a ruler | |||
Maximum Thickness of Concrete Installation Plate | ≤50mm | |||||
Steel Plate for Fixing Bushings of 1500A and Above | Does not form a closed magnetic circuit. | Observation and inspection. | ||||
Flange Position | Vertical installation | The flange should be oriented upwards. | ||||
Horizontal installation | The flange should be on the outside. | |||||
600A and above casing. | End Metal Clamp | Clamp material | Mainly | Non-magnetic materials. | Observation and inspection. | |
Thickness | ≥3mm | |||||
Connected at the same potential as the busbar | Mainly | Sturdy and reliable | Observation and inspection. | |||
Oil Filling Casing | Seal Inspection | Mainly | Leak-free | Leak-freeNormal | ||
Oil Level Indicator | Mainly | Normal | ||||
Connecting Bolts | Mainly | Complete and securely fastened | Inspect with a wrench. | |||
Grounding Terminal and Unused Voltage Extraction Terminal | Mainly | Reliable grounding | Turn and establish grounding. |
3.0.1 This chapter applies to the installation of AC and DC rectangular busbars as well as slotted busbars.
3.0.2 Inspection of Rectangular Busbar Installation
Process | Inspection Items: | Property | Quality Standards | Inspection Methods and Instruments | ||
Busbar Processing Configuration | Visual Inspection | Surface Inspection | Smooth, free from cracks and creases | Observation and inspection. | ||
External Inspection | Flat, devoid of deformations and twists | |||||
Threaded Surface Machining | Overlap Length | Mainly | Compliant with GBJ 149-1990 regulations | Check against the standard. Inspect with a ruler. | ||
Screw Hole Layout and Specifications | Mainly | |||||
Center Distance Error Between Screw Holes | ±0.5mm | Inspect with a ruler. | ||||
End Face Appearance | Flat, smooth, free of sharp corners and burrs. | Observation and inspection. | ||||
Contact Surface Flatness | Even and void of local depressions. | Measure with a steel ruler. | ||||
Contact Surface Cross-Section Reduction | Mainly | Copper ≤3%, Aluminum ≤5%. | Inspect with a vernier caliper. | |||
Busbar bending | Allowed Minimum Bending Radius | Mainly | In accordance with GBJ 149-1990 regulations. | Check against standards using a template. | ||
Minimum Distance from Bending Start Point to Joint Edge | ≥50mm | Inspect with a ruler. | ||||
Distance from Bending Start Point to Busbar Supporter Edge | ≥50mm; ≤0.25 pivot distance. | |||||
Twisting Length of 90° Bend in mm | 2.5 to 5 times the width of the busbar | |||||
Appearance of Bending Part | Mainly | No cracks, no noticeable creases. | Observation and inspection. | |||
Bending Radius on the Same Section of Three Phases | Consistent. | Inspect using a template. | ||||
Bending Radius of Multiple Busbars in the Same Phase | Consistent. | Observation and inspection. | ||||
Bending Radius of Branch Busbars with Same Layout | ||||||
Busbar Installation | Hardware Installation | Hardware Inspection | Clean, undamaged. | Observation and inspection. | ||
Single-Phase AC Busbar Hardware Connection | Mainly | Secure, with no closed magnetic circuit. | ||||
Appearance of Fixing Device | No sharp angles or burrs. | |||||
Busbar Installation | Gap Between Busbar and Upper Clamp When Busbar is Horizontal | 1mm~1.5mm | Inspect with a ruler. | |||
Distance Between Upper Clamp and Busbar When Busbar is Vertical | 1.5mm~2mm | |||||
Stress Check Between Busbar and Support | Mainly | No external stress. | Observation and inspection. | |||
Interlayer Gap of Multiple Layers of Busbar in the Same Phase | Uniform thickness along the generatrix. | Inspect with a ruler. | ||||
Busbar Fixation Dead Point on Insulator | Set one for each segment, either along the entire length or at the midpoints of the two expansion sections. | 观察检查 | ||||
Busbar connection | Distance Between Supporter and Joint Edge | ≥50mm | Inspect with a ruler. | |||
Connections Between Busbars and Between Busbar and Equipment Terminals | Mainly | No external stress | Check during connection. | |||
Overlap Surface | Mainly | Smooth, without an oxidation layer, the silver plating must not be ground, coated with electrical load grease. | Observation and inspection. | |||
Terminal Connection and Screw Shape | Appearance | Mainly | No spring pads | |||
Flat Washer | Tin-coated copper | Observation and inspection. | ||||
Lock Nut | Complete and tight-fitting | |||||
Connecting Bolt | Matched with Hole Diameter | ≤1mm | Inspect with bolts | |||
Bolt Insertion Direction | When the busbar is laid flat, it goes from bottom to top, and all other nuts are on the maintenance side. | Observation and inspection. | ||||
Anti-loose Component Appearance | Complete, intact, and flattened. | |||||
Tightening Torque | According to the stipulations of GBJ 149-1990. | Inspect with a torque wrench according to the standard. | ||||
Exposed Length After Bolt Tightening | 2~3 buttons | Observation and inspection. | ||||
Gap Between Adjacent Washers | Mainly | ≥3mm | Observe or inspect with a ruler | |||
Installation of Expansion Joint | No streaking, breakage, or creasing phenomena. | Observation and inspection. | ||||
Overall inspection | The distance between charged bodies and between charged bodies and other objects. | Mainly | In accordance with GBJ 149-1990 regulations. | Inspect according to the standard using a ruler. | ||
Color matching and painting. | Complete and correct | Observation and inspection. |
4.0.1 This chapter applies to the installation of enclosed bus ducts (rectangular, slot-type, heavy-duty, cable bus) in shared boxes.
4.0.2 Inspection of enclosed bus duct installation in shared boxes.
Process | Inspection Item | Property | Quality Standards | Inspection Methods and Tools | ||
Shared Busbar Inspection | Exterior Appearance of the Case | Complete, free of cracks and deformations. | Observation and inspection. | |||
Conductor | Appearance | Observation and inspection. | Observation and inspection. | |||
Threaded Interface Inspection | Mainly | Observation and inspection. | ||||
Cable Busbar | Mainly | Observation and inspection. | ||||
Insulator Inspection | Appearance Inspection | Observation and inspection. | Observation and inspection. | |||
Base Connection | Mainly | Bolt Fastening | Lever Inspection | |||
Insulation Test | Good Insulation | Measure with a megaohmmeter. | ||||
Shared Busbar Installation | Interphase distance error. | ≤5mm | ≤5mm | |||
Conductor Expansion Joint | Telescopic Joint Appearance | Mainly | No Local Fractures | Observation and inspection. | ||
Threaded Interface Protective Layer | Coating Adequate and Uniform | |||||
Threaded Fastening Torque | Mainly | As per GBJ 149-1990 standards | Inspect according to the standard. | |||
Rectangular Busbar Installation | Mainly | Install according to the rectangular busbar guidelines. | As per Rectangular Busbar Installation Guidelines | |||
Cable Busbar Installation | Mainly | Follow the cable routing regulations. | As per Cable Line Guidelines | |||
Change of position required for busbar lengths exceeding 300m~400m | Mainly | No less than one cycle or as stipulated by the design. | Not less than one cycle or as per design specifications | |||
Soft Connection between Heavy-Duty Busbar and Equipment | The cross-sectional area of the connection line should be no less than that of the busbar. | Connection line cross-section not less than busbar cross-section | ||||
Shell Interface Assembly | It must be sturdy and well-sealed. | Sturdy and Well-Sealed | ||||
Shell Expansion Joint | Telescopic joint seal. | Mainly | Good | Observation and inspection. | ||
The two ends of the telescopic joint are conductively connected. | Good and Sturdy | Observation and Lever Operation Inspection | ||||
Chassis Grounding | Mainly | Reliable, full-length conductivity is good. | Reliable, Full-Length Conductivity Excellent |
5.0.1 This chapter applies to the installation of indoor and outdoor high voltage distribution device six-tube busbars.
5.0.2 Inspection of six-tube busbar installation.
Process Steps | Inspection Items | Property | Quality Standards | Inspection Methods and Instruments | |
Aluminum Alloy Tubing and Fittings | Aluminum Alloy Tube Surface Inspection | Smooth, free of cracks | Observation and inspection. | ||
Aluminum Alloy Tube End | Flat and perpendicular to the axis | Check with a ruler. | |||
Aluminum Alloy Tube Bend Radius | Compliant with GBJ 149-1990 regulations | Inspect according to the standard. | |||
Metal Fittings Inspection | Smooth, undamaged, and crack-free | Observation and inspection. | |||
Tube Busbar Welding | Welding Method | Mainly | Argon arc welding | Observation and inspection. | |
Weld Seam Dimensions | Mainly | In accordance with GBJ 149-1990 regulations, | Inspect according to the standard. | ||
Bevel Processing | Surface treatment within a 50mm range on both sides | Clean, free of oxidation film, | Clean, free of oxidation film, | Observation and inspection. | |
Bevel machining surface | No burrs, no flash. | No burrs, no flash. | |||
Alignment | Bending offset | ≤0.2% | Check with a ruler. | ||
Centerline deviation | ≤0.5mm | ||||
Liner Pipe | Longitudinal axis position | Mainly | Located at the center of the weld. | Check with a ruler. | |
Gap between the pipe and the generatrix | ≤0.5mm | ||||
Weld Seam Inspection | Weld seam height | 2mm~4mm | Check with a ruler. | ||
Weld seam appearance | Mainly | Complies with DL/T 754-2001 specifications | Observation and inspection. | ||
Tube Busbar Installation | Hardware Connection | Mainly | No closed magnetic circuit | No closed magnetic circuit. | |
Hardware Fastening | Flat and sturdy | Flat and sturdy. | |||
Distance from Weld to Support Edge | ≥50mm | Check with a ruler. | |||
Clearance Between Busbar and Sliding Supporter Shaft Seat | 1mm~2mm | ||||
Expansion Joint Appearance | Mainly | No cracks, breaks, or creases. | Observation and inspection. | ||
Busbar Terminal Shield Device | Surface is smooth, without burrs or unevenness. | Observation and inspection. | |||
Three-Item Busbar Tube Axis | Parallel to each other. | Observation and inspection. | |||
Equalizing Ring and Shield Inspection | Mainly | Complete, without distortion, and securely fastened. | |||
Overall Inspection | Distance Between Live Parts and Other Objects | As stipulated by GBJ 149-1990. | Inspect according to the standard. | ||
Busbar Phase Color Indicator | Complete and correct. |
6.0.1 This section applies to the installation of distribution device soft busbars and generator set combined wires.
6.0.2 Inspection of Soft Busbar Installation
Process | Inspection Items | Property | Quality Standard | Inspection Methods and Instruments | |
Wire and Hardware Inspection | Wire Appearance | Mainly | No breakage, looseness, or damage, and expanded wires should be free from dents and deformations. | Observation and Inspection | |
Wire Cut-off Section | Neat, no looseness or burrs, and perpendicular to the wire axis. | ||||
Connector Model and Specifications | Mainly | Matches with the connecting wires. | |||
Connector and Fastener Appearance | Mainly | Smooth, without cracks, burrs, or unevenness. | |||
Wire and Terminal Clamp Contact Surface Treatment | Mainly | Clean, without oxide film, and coated with electrical composite grease. | |||
Hydraulic Crimping | Expanded Wire and Strain Clamp Crimp Connection | Mainly | The central gap is filled with the corresponding material. | Observation and Inspection | |
Wire Insertion Length into Clamp | Mainly | Equal to the length of the line clip. | |||
Crimping Die and Crimping Pliers Inspection | Specifications match. | ||||
Overlap Length of Adjacent Crimp Sections | ≥5mm | Check with a ruler | |||
Inspect after crimping | Swage tube bending degree | ≤2% | Check with a ruler | ||
Surface of the swaged tube | Smooth, without cracks or indentations. | Observation and Inspection | |||
Wire appearance at the tube end | Mainly | No bulges or looseness. | |||
Hexagonal across-flats dimension in millimeters | Mainly | Outer diameter of the continuation tube is less or equal to 0.866D+0.2. | Check with a ruler | ||
Compression Test Specimen Experiment | Mainly | Approved | Inspect the Test Piece Experiment Report | ||
Bolt Connection | The aluminum strip is wound between the conductor and the wire clamp | Consistent with the outer aluminum strand’s direction of rotation. | Observation and Inspection | ||
The exposed length of the aluminum tape clamp | ≤10mm | Check with a ruler | |||
Aluminum tape port processing | Press back into the clamp. | Observation and Inspection | |||
Connecting Bolt | Mainly | Ensure uniform tightening, with the bolt revealing two to three threads beyond the nut. | Check with a torque wrench | ||
Nail Zhang wire clamp leads to the busbar arrangement of the equipment. | Complete, without interruptions. | Observation and Inspection | |||
Flexible Busbar Installation and Overall Inspection | The busbar arrangement within the gear pitch. | Seamless | Observation and InspectionObservation and Inspection | ||
The configuration of connecting hardware parts. | Complete, secure. | ||||
Busbar sag error. | Mainly | -2.5% ~ +5% (under design temperature) | Observation and Inspection | ||
The sag of the three busbars within the same pitch. | Consistent | Observation and Inspection | |||
The bend and sag of branch lines with the same layout. | |||||
The inter-line and frame structure distance of jumper and lead down lines. | Mainly | As stipulated by GBJ 149-1990. | Inspect in accordance with standards | ||
Composite Conductor | Fixed Wire Clamp Spacing Error | Mainly | ≤±3% | Check with a ruler | |
Intersection Angle Between Fixed Wire Clamp and Conductor | 90° | Check with a square ruler | |||
Runout | Consistent | Observation and Inspection | |||
Busbar is connected to the electrical terminal. | The terminal is undamaged and free of deformations. | Observation and Inspection | |||
Adjustable fixture inspection. | The adjustment nut is securely tightened. | Inspect with a wrench | |||
Busbar phase color identification. | Complete and correct. | Observation and Inspection |