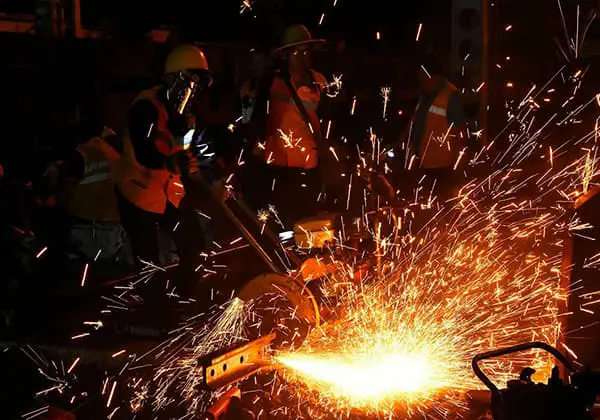
Imagine choosing materials for your next project: carbon steel or aluminum? Each has its strengths and drawbacks. Carbon steel is affordable and tough, but heavier. Aluminum is lightweight and resistant to rust, though pricier. This article explores these differences, helping you decide which material best suits your needs, from construction to aerospace applications. Dive in to discover the key factors that can influence your material choice and ensure your project’s success.
Which is better, carbon steel or aluminum alloy? Carbon steel and aluminum alloy have their own advantages and disadvantages, and are also used in different occasions.
Carbon steel is very common in building materials because of its affordable price, good stability and strong toughness.
Aluminum alloy has better stability, no rust, higher hardness and light texture;
But its price is more expensive and its toughness is slightly poor. It is often used in places where light and hard materials are needed.
High carbon steel, often called tool steel, with carbon content ranging from 0.60% to 1.70%, can be quenched and tempered.
Hammers, crowbars, etc. are made of steel with 0.75% carbon content; cutting tools such as drills, taps, reamers, etc. are made of steel with a carbon content of 0.90% to 1.00%.
After heat treatment, high hardness (HRC60-65) and good wear resistance can be obtained.
The hardness is moderate under annealing condition and has good machinability.
Aluminum alloy is the most widely used nonferrous metal structural material in industry.
It has been widely used in aviation, aerospace, automobile, machinery manufacturing, shipbuilding and chemical industry.
With the rapid development of the industrial economy, the demand for aluminum alloy welded structural parts is increasing day by day, and the weldability research of aluminum alloy is also deepening.
At present, aluminum alloy is the most widely used alloy.
Good thermal conductivity: aluminum has a high thermal conductivity, which is only three times as high as iron, next to silver, gold and copper in metals.
1. After heat treatment, high hardness (HRC60-65) and good wear resistance can be obtained.
2. The hardness is moderate under annealing condition and has good machinability.
3. Raw materials are easily available and production costs are low.
1. The thermal hardness is poor. When the working temperature of the tool is greater than 200 ℃, its hardness and wear resistance drop sharply.
2. Low hardenability.
The diameter of a fully quenched hole during water quenching is 15-18mm;
The maximum diameter or thickness (95% martensite) of complete quenching during oil quenching is only about 6mm, and it is easy to deform and crack.
Low density:
The density of aluminum is 2.7g/cm³, about 1/3 of that of copper (8.9g/cm³) or steel (7.8g/cm³).
Low density is very beneficial to vehicles and buildings such as aerospace aircraft, ships and vehicles, and it can also save moving and processing costs and reduce costs. It is more widely used in industry, construction, civil and other fields;
Good corrosion resistance:
Aluminum and aluminum alloys can form a hard and dense oxide film with good corrosion resistance in the atmosphere.
The corrosion resistance of aluminum can be further improved by surface treatment such as anodizing, electrophoretic painting, powder coating, etc;
Good decorative property:
Aluminum alloy has good plasticity and can process products of various specifications.
Through surface treatment, it can produce films of different properties and colors, with good decorative property;
Aluminum alloy is a brittle material, with tensile strength close to yield strength, poor toughness, low hardness, non-wear resistance, large thermal conductivity, large thermal deformation, poor thermal stability, and can not improve the mechanical strength of the material through heat treatment.