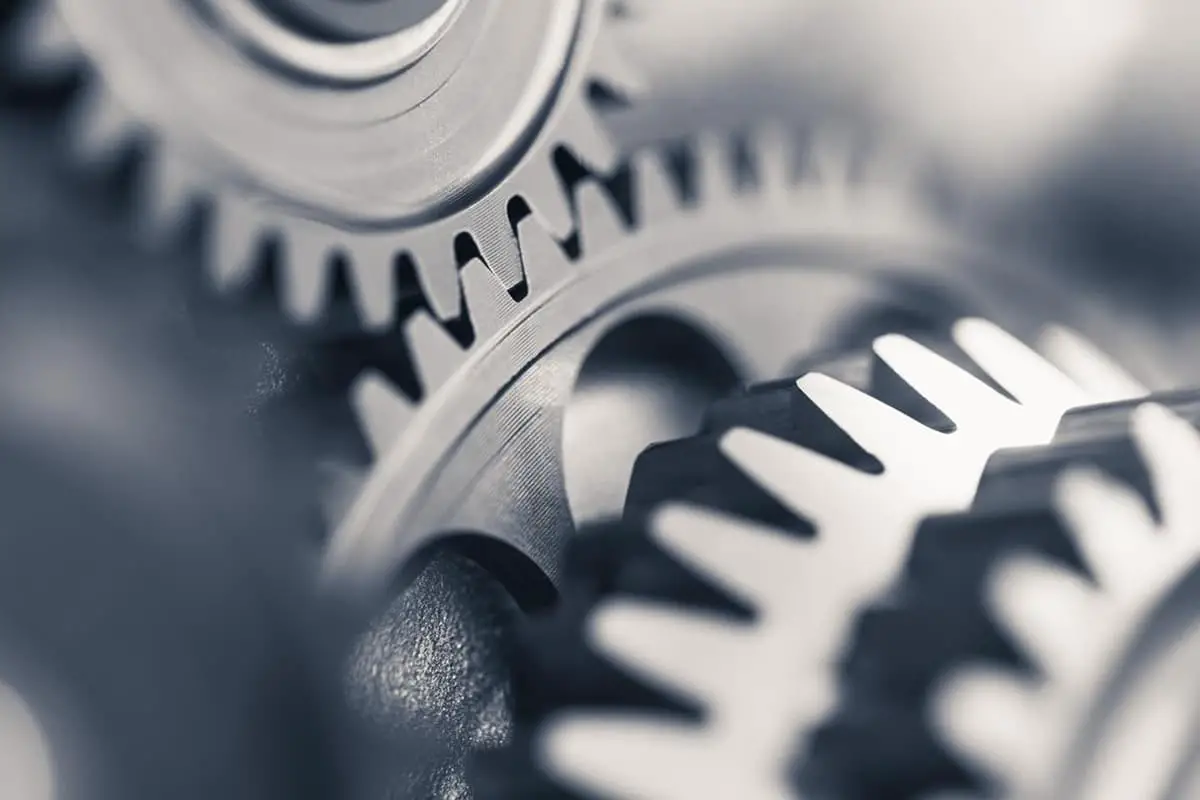
Ever wondered why thin-walled gears deform during carburizing and quenching? This article explores the causes of warpage and elliptical deformation, offering practical solutions like horizontal and vertical charging methods. By understanding these techniques, you’ll learn how to maintain gear precision and avoid costly scrapping. Get ready to dive into the detailed processes and results that ensure your gears remain perfectly shaped.
In the process of carburizing and quenching, thin-walled gears usually have plane warpage and elliptical deformation.
During grinding, the uneven distribution of tooth surface allowance results in black skin and grinding steps on the tooth surface;
The hardening layer on the left and right tooth surfaces is uneven and the surface hardness decreases, and the gear is scrapped in serious cases.
In order to solve this problem, horizontal charging and hanging charging are designed.
The carburizing and quenching process and deformation data are described in detail below.
The parameters of a gear product are shown in Table 1, and the schematic diagram is shown in Fig. 1.
Table 1 gear parameters
Mn | 4 |
Z | 138 |
α | 20° |
β | 23°4′26″ |
Addendum circle / mm | 608 |
Tooth width / mm | 80 |
Layer depth / mm | 0.9~1.2 |
Hardness (HRC) | 58~62 |
Gear accuracy / grade | 6 |
Texture of material | 20CrMnMo |
Fig. 1 gear diagram
Charging method I: horizontal placement, as shown in Fig. 2.
Fig. 2 Schematic diagram of horizontal placement
Charging mode 2: vertical hanging, as shown in Fig. 3 and Fig. 4.
Fig. 3 Schematic diagram of vertical suspension
Fig. 4 vertical hanging objects of other heats
As shown in Fig. 5, the equipment uses AICHELIN 5 / 2A box furnace.
Fig. 5 heat treatment process curve
The metallographic structure is judged according to JB / T6141.3 and GB / T3480.5, as shown in Table 2.
Table 2 metallographic structure
K / grade | Ar(%) | M / level | IGO/μm | F / level |
2 | 15~20 | 2 | 18 | 3 |
As shown in Fig. 6, the layer depth DC = 1.219mm/HV550.
Fig. 6 hardness gradient
The gear deformation data is shown in Table 3.
Table 3 Comparison of pitch circle and end face runout after carburizing and quenching between horizontal and hanging placement
Part number | location | 0° | 90° | 180° | 270° | Total runout | |
Horizontal placement | Part 1 | Pitch circle / mm | 0.74 | 0.61 | 0.61 | 0.43 | 0.31 |
End face / mm | 0 | 1.15 | 0.47 | 1.3 | 1.3 | ||
Part 2 | Pitch circle / mm | 0.86 | 0.55 | 0.86 | 0.92 | 0.37 | |
End face / mm | 1 | 1.35 | 1.82 | 1.36 | 0.82 | ||
Suspension placement | Part 1 | Pitch circle / mm | 0 | 0.01 | 0 | 0.02 | 0.02 |
End face / mm | 0 | 0.03 | 0.03 | 0.07 | 0.07 | ||
Part 2 | Pitch circle / mm | 0 | -0.01 | -0.01 | 0.05 | 0.06 | |
End face / mm | 0.01 | -0.04 | -0.04 | 0.18 | 0.22 |
Due to warpage and deformation of horizontally placed parts, the tooth shape, tooth direction and pitch circle runout are too large, resulting in a negative value of grinding allowance distribution.
After grinding, some tooth surfaces have black skin, and some tooth surfaces have obvious grinding steps, which are finally scrapped;
The hanging gear has small deformation, evenly distributed grinding allowance, and no black skin and step after grinding.
When the gear is placed horizontally, because the edge of the gear is suspended, the creep is caused by the self weight of the rim during the carburizing process, the quenching is instantaneous, the oil contact cross-sectional area is large, and the oil enters the lower end face first than the upper end face;
Due to the imbalance of thermal stress and phase change stress at both ends, the upper end face is convex and the gear warps too much;
On the contrary, there is high-temperature creep in the carburizing process, but the gear rim does not bear large bending moment.
At the same time, the two end faces are parallel to each other during quenching, the oil inlet section is small, the phase change stress and thermal stress are balanced and symmetrical, and the end face runout and pitch circle runout of the gear are smaller than that of the horizontal placement.
According to the above analysis on the causes of gear deformation, suspension charging was also carried out for the gear with a diameter of 1140mm, and very good results were obtained.
The gear parameters are shown in Table 4, the charging is shown in Fig. 7, and the deformation data are shown in Table 5.
Table 4 gear parameters
Mn | 8 |
Z | 137 |
α | 20° |
β | 12° |
Addendum circle / mm | 1140 |
Tooth width / mm | 120 |
Layer depth / mm | 1.6~2.0 |
Hardness (HRC) | 58~62 |
Gear accuracy / grade | 6 |
Texture of material | 20CrMnMo |
Fig. 7 picture of furnace loading
Table 5 runout data of end face and pitch circle of 4 gears
Part number | Location | 0° | 90° | 180° | 270° | Total runout |
Part 1 | Pitch circle / mm | 0.53 | 0.51 | 0.55 | 0.5 | 0.05 |
End face / mm | 0.45 | 0.3 | 0.6 | 0.5 | 0.3 | |
Part 2 | Pitch circle / mm | 1 | 1 | 1.07 | 1 | 0.07 |
End face / mm | — | — | — | — | 0.4 | |
Part 1 | Pitch circle / mm | 0.9 | 0.92 | 0.97 | 0.92 | 0.07 |
End face / mm | 0.58 | 0.8 | 0.7 | 0.9 | 0.32 | |
Part 2 | Pitch circle / mm | 0.25 | 0.22 | 0.23 | 0.28 | 0.06 |
End face / mm | 0.7 | 0.6 | 0.35 | 0.4 | 0.35 |
(1) For Φ600mm×80mm thin-walled gear, the pitch circle runout of carburized and quenched gear is reduced from 0.34mm to 0.04mm by hanging furnace;
The average end face runout is reduced from 1.06mm to 0.15mm.
(2) For the Φ1140mm×120mm thin-walled gear, the pitch circle runout of the carburized and quenched gear is controlled within 0.07mm through hanging charging;
The end face runout shall be controlled below 0.40mm.