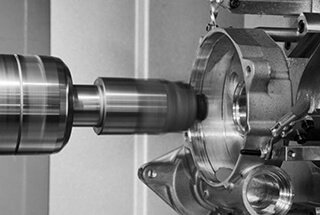
Have you ever wondered how a simple tool like a brush could transform industrial processes? Ceramic bristle brushes are revolutionizing industries by offering superior grinding, consistent performance, and impressive durability. In this article, you’ll learn about their applications in grinding, dust prevention, polishing, and cleaning, and how their unique materials and design set them apart from traditional brushes. Discover how these brushes can enhance efficiency and precision in various machining and industrial tasks.
In our series of articles on deburring, we continue to bring you fresh content. Today, we discuss the topic of brushes.
Possibly, when we mention brushes, the first things that come to mind are the ones we use daily, such as toothbrushes or shoe brushes.
However, brushes find a significant number of applications in our industrial arenas as well.
Surely, every product holds its economic value, akin to the industrial brushes we’re discussing. They typically serve functions such as grinding, dust prevention, polishing, and cleaning.
Now, let’s delve into each of these applications and functions.
Grinding brushes are seldom used in general industrial grinding; typically, grinding wheel tools are employed directly. These are outside the scope of industrial brushes.
However, for the textile industry’s sueding process, brushes with silicon carbide abrasive filaments are necessary.
The grit size (density) of the silicon carbide in the abrasive filaments should be adjusted according to the strength of the fabric being ground and the required grinding effect.
Dust-proof brushes are primarily installed on industrial equipment, assembly lines, and entrances and exits of doors and windows to prevent dust from infiltrating through these gaps and contaminating the equipment and products.
As such, the brush bristles are required to have high elasticity, better lubrication on the surface, and in special circumstances, should possess flame retardant properties, wear resistance, and anti-static functions.
For instance, escalator safety brushes fall within the category of dust-proof brushes, but with higher requirements.
Polishing brushes are primarily utilized for deburring, precision milling, and polishing the surface of the workpiece, necessitating the selection of brush types and properties according to different requirements.
For surfaces of harder steel plates requiring electroplating and polishing, the most suitable brush would be a bronze brush. For general metal materials requiring surface rust removal and deburring, a brush with a higher hardness steel wire would suffice.
Cleaning brushes are commonly used industrial roller brushes, typically employed in the deep processing of agricultural byproducts, such as the cleaning of fruits and vegetables, as well as general cleaning and dust removal in industry.
The brush bristles require excellent abrasion resistance, high elasticity, and resistance to corrosion and aging, ensuring they do not easily deform under long working hours.
If the bristle performance is subpar, placing an object in a stationary position for an extended period can cause grooves to form in the brush roller, compromising its functionality.
In severe cases, this could even result in the complete discarding of the entire brush roller.
Regarding the application scope of brush deburring, as practitioners in the machining industry, you may be more concerned about the field of deburring. So, let’s continue discussing this topic.
The most commonly used materials on the market are nylon blended with abrasive or metal wires. The nylon and abrasive blend mainly includes aluminum oxide, silicon carbide, and diamond thread.
Abrasive nylon brushes, an industrial tool originating in Europe in the 1990s and widely used in Japan, operate on a unique processing principle.
During machining, countless abrasive nylon filaments function like an equivalent number of flexible files, bending freely to conform naturally to the contour of the workpiece, reaching into grooves and holes typically inaccessible to conventional tools.
Difficult-to-remove burrs are eliminated, sharp edges are smoothed into glossy arcs, and the edges are dulled, achieving the ideal effect of edge blunting and surface polishing. The abrasive nylon filaments consist of nylon infused with abrasives such as silicon carbide and aluminum oxide.
Primarily, nylon 612 is used due to its excellent bend recovery ability, low moisture absorption, light weight, and high hardness. The abrasives, mainly silicon carbide and aluminum oxide, are cubic-shaped particles that range from 46 to 600 mesh in size.
1. Excellent Chemical Resistance
Exhibits high resistance to both acids and alkalis, and organic solvents, without compromising the original surface finish. The bristles absorb minimal moisture, making them suitable for both dry and wet conditions.
2. Durability
The brush offers exceptional durability, with robust bristles that ensure a long service life.
3. High Bristle Strength
The bristles boast high strength and rigidity, enabling comprehensive and uniform grinding across various surfaces, including flat and uneven ones.
Some friends have messaged us to inquire about the characteristics of our ceramic bristle brushes.
Today, we’re going to explain it all at once. The surface of the brushes we use is made with abrasive ceramic fibers instead of grinding particles. A single bristle contains 1,000 cutting edges, demonstrating excellent cutting performance.
Ceramic fiber brushes have three key features: “superior grinding power”, “consistent cutting performance”, and “no deformation”. They are capable of deburring and polishing in machine processing.
The ceramic fiber itself is an abrasive, with a fiber content exceeding 80%. Each individual fiber end forms thousands of cutting edges, resulting in superior grinding power.
Compared to nylon grinding brushes, the grinding ability of the brush surface is enhanced by 20-30 times and can continuously remove burrs.
The structure of the ceramic fiber always exposes new cutting edges, so the grinding brush can maintain consistent cutting performance until the end, ideal for deburring and polishing in machining.
The grinding brush retains its linear shape and doesn’t spread out like a toothbrush, even after repeated use. It is suitable for deburring and polishing in large-scale production lines.
In conclusion, let’s summarize the advantages and disadvantages of the brush.
Advantages:
1. No additional equipment needed for application.
Simply clamp the brush to the tool handle to use.
2. Wide range of suitability.
By adjusting the size and structure of the brush, it can be used for the majority of processing surfaces and hole diameters.
3. Short cycle time for adjustments and changes.
No need for a lengthy equipment debugging period.
Disadvantages:
1. Unable to remove burrs in special locations.
For example: narrow passages or circlip slots.
2. Significant impact on the cycle time.
It requires a longer processing time as the tool path needs to cover the burr area.
3. Consumable, thus increasing costs.
The brush wears out quickly, and needs to be replaced after wear compensation reaches a certain length.
I’ve compiled some data here to provide a clearer understanding of the advantages and characteristics of ceramic brushes.
The data listed represents a performance comparison between ceramic and nylon brushes.
structure | Ceramic Brush![]() | Nylon Brush![]() |
Sturdiness | An alumina fiber is composed of 1,000 strands of fiber filaments (with the red and white fiber filaments having diameters of 10μm and 15μm respectively). | The abrasive grains are impregnated in nylon. The nylon base gives it flexibility, but its rigidity is moderate. |
Consistency | Therefore, this structure ensures that the fibers remain sturdy and undistorted during the deburring process, maintaining consistent grinding. | During the deburring process, deformation and softening can occur. |
Good grinding performance | The aluminum oxide fibers account for approximately 75% of the total weight. Throughout the grinding process, these fibers consistently maintain excellent self-sharpening characteristics, continuously offering superior grinding performance. | The grinding particles only make up 30% of the total weight; their self-sharpening ability is weak, therefore, the grinding efficiency is quite low. |
High stability | Thanks to the uniform composition of numerous alumina fibers, it can provide stable and exceptional grinding performance. | Due to the significant variation in the diameter of the grinding particles, it’s challenging to achieve optimal results. |
Reduced clogging | The secret lies in the continuous self-fracturing and sharpening of the aluminum oxide fibers, ensuring that they won’t clog during processing. | Grinding can easily lead to clogging. |
Suitable for both dry and wet grinding | Thanks to its high heat resistance (about 150°C), it still performs stably during dry grinding. Due to its excellent water resistance, it does not reduce the rigidity of the luxury material during wet grinding, providing stable grinding performance. | Due to its low heat resistance (approximately 90℃), the heat generated during dry grinding causes the abrasives to soften and the nylon to melt. Because of its poor water resistance, the abrasives soften during grinding, leading to a decline in grinding performance. |
This essentially encompasses some insights and experiences about wire brushes that I wanted to share with you all today. It may not be comprehensive, but I hope you find it enjoyable.