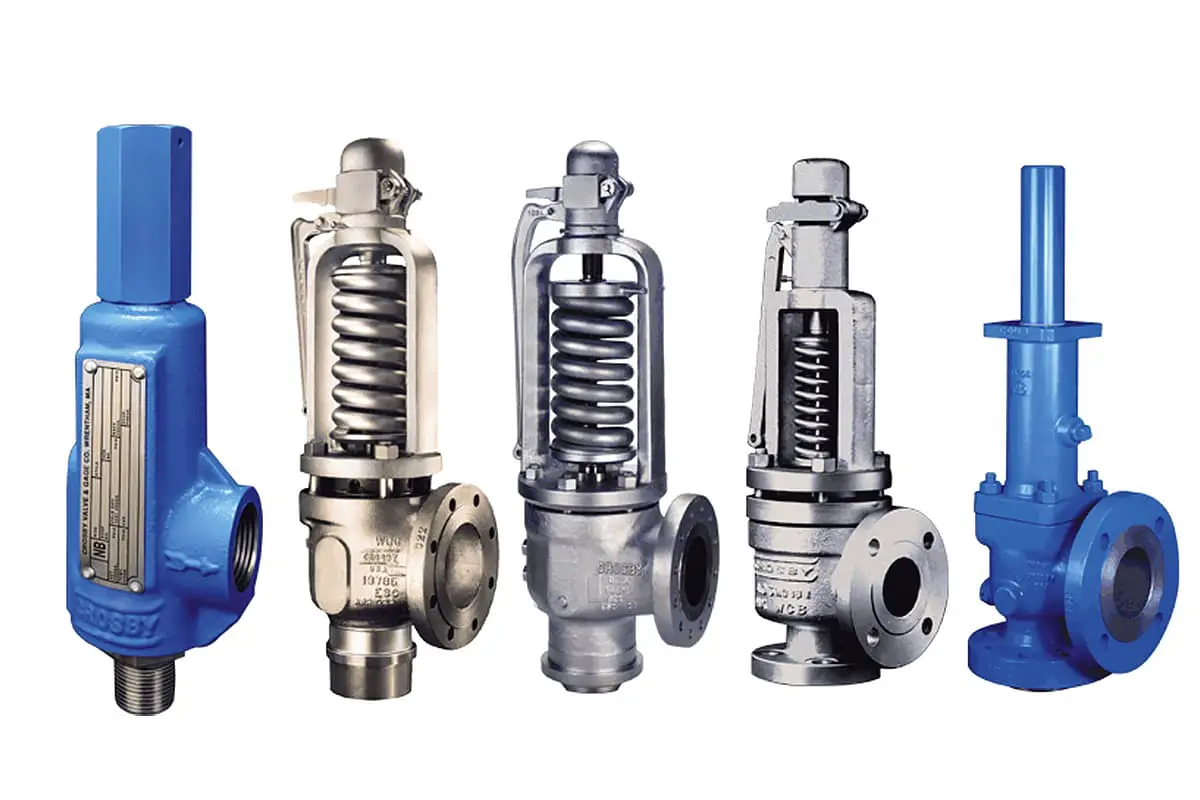
Choosing the right servo motor for your project can be a daunting task with so many options available. This article simplifies the process by breaking down the key considerations: application scenario, power supply, braking requirements, selection calculations, and brand options. By the end, you’ll understand how to match a servo motor’s specifications to your needs, ensuring precise control and optimal performance. Dive in to find the perfect motor for your automation project!
Automation, the current hot field, plays an important role, commonly used for precise speed or position control parts in projects.
Designers of automated equipment often face a variety of motor selection issues, and the motors offered by suppliers are diverse, with myriad parameters, often overwhelming for beginners.
This article shares some experiences from practical work, hoping to provide some assistance to those in need.
A servo motor is an engine that controls the movement of mechanical components in a servo system; it’s essentially an auxiliary motor with an indirect variable speed mechanism.
Servo motors are categorized by their power source: Direct Current (DC) servo motors and Alternating Current (AC) servo motors.
The functional difference between the two is that AC servos perform better due to their sinusoidal wave control, which results in less torque ripple. DC servos, on the other hand, employ trapezoidal waves.
However, DC servos are simpler and more cost-effective. Servo motors can achieve precise control; they’ll rotate exactly as instructed, and they provide feedback to ensure accuracy through what is known as a closed loop. This is achieved using an encoder to verify the rotation, which enhances control precision.
The accuracy of stepper motors is measured by their step angle. Common step angles in the market include 0.36°/0.72° (for five-phase motors), 0.9°/1.8° (for two and four-phase motors), and 1.5°/3° (for three-phase motors). BERGER LAHR, a German company, produces three-phase hybrid stepper motors with selectable step angles via DIP switches: 1.8°, 0.9°, 0.72°, 0.36°, 0.18°, 0.09°, 0.072°, and 0.036°.
Let’s consider a stepper motor with a step angle of 0.036°.
0.036 = 360/10000
Assuming an encoder is attached to the rear end of this stepper motor, the formula implies that the motor emits 10,000 pulses per revolution, indicating an encoder resolution of 10,000.
The accuracy of a servo motor is measured by the resolution of the encoder attached to its rear end. Currently, servo encoder resolutions can reach 223, demonstrating that servo motor precision far exceeds that of stepper motors.
A standard motor powers up and starts spinning, then stops when the power is cut. Apart from rotation, if one were to attribute any additional functionality to it, that would be its ability to reverse direction.
Control motors in the automation field can be divided into servo motors, stepper motors, and variable frequency motors. For components that require precise speed or position control, servo motors are chosen.
The control method of the inverter plus variable frequency motor changes the speed of the motor by changing the frequency of the power source input to the motor. This is generally only used for motor speed control.
Comparing servo motors and stepper motors:
a) Servo motors use closed-loop control, while stepper motors use open-loop control.
b) Servo motors use rotary encoders for measuring accuracy, while stepper motors use step angles. At the common product level, the former’s accuracy can reach a hundred times the latter’s.
c) The control methods are similar (pulse or directional signal).
Servo motors can be classified into AC servo motors and DC servo motors based on the power supply.
Both are relatively easy to choose from. For general automation equipment, clients usually provide a standard 380V industrial power supply or 220V power supply, in which case one simply selects a servo motor for the corresponding power supply, eliminating the need to convert power types.
However, some equipment, such as shuttle boards in three-dimensional warehouses and AGVs, due to their mobile nature, mostly use built-in DC power supplies, and hence usually use DC servo motors.
Based on the design of the motion mechanism, consider whether there will be a reversal tendency for
the motor in a power-off state or stationary state. If there is a tendency to reverse, a servo motor with a brake should be selected.
Before making the selection calculation, you first need to determine the position and speed requirements of the end of the mechanism, and then identify the transmission mechanism.
At this point, you can select the servo system and corresponding reducer.
During the selection process, consider the following parameters:
Calculate the required power and speed of the motor based on the structural form and the speed and acceleration requirements of the final load.
Notably, in general, you need to choose the reduction ratio of the reducer in conjunction with the speed of the selected motor.
In actual selection, for example, if the load is horizontal motion, due to the uncertainty of the friction coefficient and wind load factor of various transmission mechanisms, the formula P=TN/9549 often cannot clearly calculate (cannot accurately calculate the torque size).
In practice, it has also been found that the place where the maximum power is needed when using a servo motor is often the acceleration and deceleration stage.
Therefore, through T=F*R=m*a*R, you can quantitatively calculate the required power and reduction ratio of the motor and the reducer (m: load mass; a: load acceleration; R: load rotation radius).
The following points need attention:
a) The power surplus factor of the motor;
b) Consider the transmission efficiency of the mechanism;
c) Whether the input and output torques of the reducer meet the standard and have a certain safety factor;
d) Whether there will be a possibility of increasing speed later.
It’s worth mentioning that in traditional industries, such as the crane industry, ordinary induction motors are used for driving, there are no clear acceleration requirements, and empirical formulas are used in the calculation process.
Note: In the case of vertical load operation, remember to include the gravitational acceleration in the calculation.
To achieve high-precision control of the load, you need to consider whether the inertia of the motor and the system match.
As for why inertia matching is needed, there is no unified explanation on the internet.
The principle of inertia matching is: considering the system inertia converted to the motor shaft, the ratio to the motor’s inertia should not be greater than 10 (Siemens); the smaller the ratio, the better the control stability, but it requires a larger motor, and the cost performance is lower.
Please refer to the university’s “Theoretical Mechanics” if you have any questions about the specific calculation methods.
After going through the reducer and transmission mechanism, calculate whether the control accuracy of the motor can meet the requirements of the load. The reducer or some transmission mechanisms have a certain backlash, all of which need to be considered.
This mainly involves communication and confirmation with electrical designers, such as whether the communication method of the servo controller matches the PLC, the type of encoder, and whether data output is needed.
The selection of a servo motor is influenced not only by the weight of the mechanism but also by the operational conditions of the equipment, which can alter the choice of servo motor. Greater inertia requires higher torque for acceleration and deceleration, and shorter times for acceleration and deceleration, thus necessitating a servo motor with greater output torque.
When selecting a servo motor specification, please follow these steps:
Currently, there are many brands of servo motors on the market, with varying performances. Generally speaking, if budget is not a concern, choose European or American brands. If you’re more budget-conscious, choose Japanese brands, followed by those from Taiwan and mainland China.
This is not the author being biased towards foreign brands; it’s a lesson learned from actual use.
Based on past experience, there’s generally no issue with the basic performance of domestic servo motors, but the control algorithm, integration, and stability of the servo controller can lag behind.
Some commonly used servo motor brands:
European and American: Siemens, ABB, Lenze, etc.;
Japanese: Panasonic, Mitsubishi, Yaskawa, etc.
Worth noting is that in automation design, you must learn to leverage external forces. Especially in non-standard automation, faced with the selection and calculation of too many devices, it is often overwhelming, and working overtime is the norm.
Now, servo motor manufacturers all provide technical support. As long as you provide load, speed, acceleration, and other parameter requirements, they have their own software to automatically help you calculate and choose the right servo motor, which is very convenient.