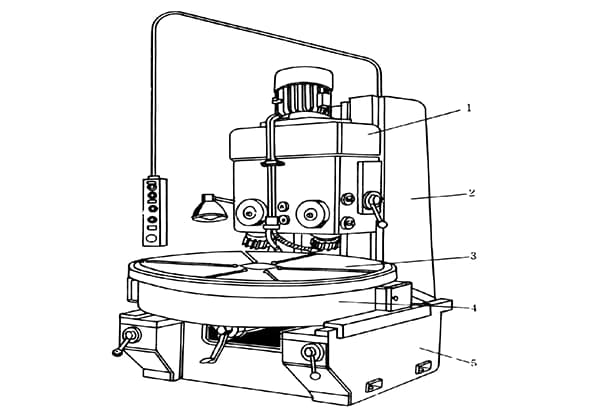
Which milling method offers better results for CNC machining: climb milling or conventional milling? This article dives into the pros and cons of each technique, detailing how the direction of cutter rotation and feed can impact chip formation, tool wear, and surface finish. Discover why climb milling might be preferred for smoother cuts and how conventional milling can be beneficial for tougher materials. By the end, you’ll understand the practical applications of both methods, helping you make informed decisions for your machining projects.
In CNC machining, the direction of rotation of the milling cutter is generally constant, but the feed direction is changing.
So, there are two common phenomena in milling: climb milling and conventional milling.
The cutting edge of the milling cutter is subjected to an impact load on each cut.
To complete successfully in milling, it is important to consider the correct contact between the cutting edge and the material in a single cut as well as the cutting edge when cutting out.
During the milling process, the workpiece is fed in the same or opposite direction as the milling cutter rotation, which affects the way milling is done in and out and whether climb milling or conventional milling is used.
When milling, it always needs to consider chip formation.
The determining factor for chip formation is the position of the milling cutter, so it needs to be sure to try to form thick chips when the blade cuts in, and thin chips when the blade cuts out to ensure a stable milling process.
It needs to remember the golden rule of milling, “from thick to thin”, to ensure the smallest possible chip thickness when the cutting edge comes out of the cutter.
In climb milling, the cutting tool is fed in the direction of rotation.
As long as the machine, fixture and workpiece allow, climb milling is always the preferred method.
In edge climb milling, the chip thickness decreases from the beginning of the cut and eventually reaches zero at the end of the cut.
This prevents the cutting edge from scratching and rubbing against the surface of the part before participating in cutting.
High chip thickness is advantageous because the cutting force tends to pull the workpiece into the cutter, keeping the cutting edge in the cut.
However, because the milling cutter is easily pulled into the workpiece, the machine tool needs to deal with the table feed gap by eliminating backlash.
If the cutter is pulled into the workpiece, the feed will increase unexpectedly, which can lead to excessive chip thickness and cracked cutting edges.
In these cases, conventional milling is considered to use.
In conventional milling, the cutting tool is fed in the opposite direction of its rotation.
The chip thickness gradually increases from zero until the end of the cut.
The cutting edge has to be forced in, resulting in a rubbing or polishing effect due to friction, high temperatures and constant contact with the work-hardened surface caused by the front cutting edge.
All of these will shorten tool life.
The thicker chips and higher temperatures caused by cutting out the cutting edge result in high tensile stresses, which shorten tool life and often lead to rapid damage to the cutting edge.
It can also cause chips to stick or weld to the cutting edge, which can then carry it to the start of the next cut, or cause the cutting edge to collapse instantly.
The cutting force tends to push the cutter and workpiece away from each other, while the radial force tends to lift the workpiece off the table.
When the machining allowance changes significantly, conventional milling may be more advantageous.
Conventional milling is also recommended when machining high-temperature alloys with ceramic inserts, as ceramics are sensitive to the impact of the cut into the workpiece.
The feed direction of the tool puts forward different requirements on the workpiece fixture.
During conventional milling, it should be able to resist lifting forces.
In conventional milling, it should be able to resist a downward force.
Item | Climb milling | Conventional milling |
Cutting thickness | from large to small | from small to large |
Slippage | no | yes |
Tool wear | slowly | fast |
The cold hard phenomenon on the workpiece surface | no | yes |
Effects on workpieces | compress | raise |
Eliminate clearance between screw and nut | no | yes |
Vibration | large | small |
Loss of energy | small | large 5% to15% |
Surface roughness | good | bad |
Applicable occasions | finish machining | rough machining |