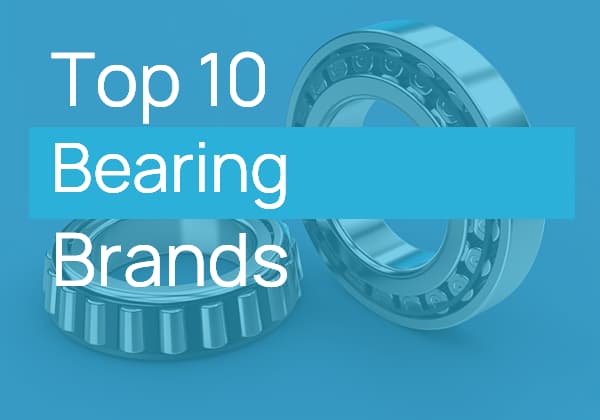
Have you ever wondered how industrial robots achieve their precise and efficient operations? The secret lies in their control methods. This article delves into the four primary control methods: point-to-point, continuous trajectory, force (torque), and intelligent control. Each method is tailored for specific tasks, from simple positioning to complex adaptive behaviors. By the end, you’ll understand how these control techniques enhance industrial robots’ performance, making them indispensable in modern manufacturing.
The most commonly used robots on the market are industrial robots, which are also the most mature and perfected type of robot. The widespread application of industrial robots is attributed to their diverse control modes.
Based on different operational tasks, they can be primarily divided into four types: point-to-point control, continuous trajectory control, force (torque) control, and intelligent control. Let’s briefly understand these.
This control method only regulates the position and orientation of the robot’s end effector at certain discrete points in the operational space. During control, the robot only needs to move quickly and accurately between adjacent points; the trajectory to reach the target point is not specified.
The positioning accuracy and time required for motion are the two main technical indicators of this control method. With its easy implementation and low positioning accuracy requirement, point-to-point control is often used in loading and unloading, handling, spot welding, and component placement on circuit boards, where only the accurate positioning of the end effector at the target point is required.
This method is relatively simple, but achieving a positioning accuracy of 2-3μm is quite challenging.
This control method continuously controls the position and orientation of the robot’s end effector in the operational space. It requires strict adherence to predefined trajectories and speeds within a certain accuracy range, ensuring controllable speed, smooth trajectory, and stable motion for task completion.
The continuous, synchronized motion of all joints in the industrial robot allows the end effector to form a continuous trajectory. The main technical indicators of this control method are the trajectory tracking accuracy and stability of the robot’s end effector.
This control method is commonly used in arc welding, painting, deburring, and inspection robots.
When assembling or picking up objects, in addition to accurate positioning, the force or torque used must be suitable.
In such cases, force (torque) servo control is necessary. The principle of this control method is similar to position servo control, but the input and feedback are not position signals, but force (torque) signals.
Therefore, a force (torque) sensor must be present in the system. Sometimes, adaptive control is carried out using proximity, sliding, and other sensor functions.
Intelligent control of robots involves acquiring knowledge of the surrounding environment through sensors and making corresponding decisions based on the robot’s internal knowledge base.
Intelligent control technology endows robots with strong environmental adaptability and self-learning ability.
The development of intelligent control technology relies on the rapid advancement of artificial intelligence in recent years, including artificial neural networks, genetic algorithms, and expert systems.
This control method gives industrial robots a genuine “artificial intelligence” flavor, but it is also the most difficult to control effectively. Besides the algorithm, it also heavily depends on the precision of components.