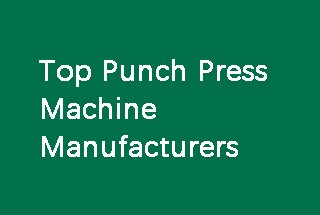
Haben Sie sich jemals gefragt, wie Autos so schnell und sicher hergestellt werden? Dieser Artikel enthüllt die Magie hinter automatisierten Stanzstraßen, in denen Roboter die manuelle Arbeit ersetzen, die Effizienz um 35% steigern und Verletzungsrisiken ausschließen. Tauchen Sie ein in die faszinierende Welt der automatisierten Hochgeschwindigkeitsfertigung und erfahren Sie, wie sie die Automobilindustrie revolutioniert!
In konventionellen Stanzproduktionslinien wurde der Materialtransport zwischen vor- und nachgelagerten Anlagen traditionell manuell durchgeführt. Da die Produktionsgeschwindigkeiten jedoch eskaliert sind, ist dieser manuelle Ansatz für das Be- und Entladen von Teilen sowohl ineffizient als auch ein erhebliches Sicherheitsproblem geworden.
Die Bediener, die unter dem Druck stehen, einen hohen Durchsatz aufrechtzuerhalten, übersehen oft die Gefahren, die mit sich schnell bewegenden Maschinen verbunden sind. Dies hat zu einer alarmierenden Häufigkeit von Unfällen geführt, insbesondere zu Unfällen, bei denen die Hände von der Presse erfasst und verletzt werden. Um diese Sicherheitsprobleme zu lösen und gleichzeitig die Produktivität zu steigern, wurden automatisierte Produktionslinien mit Robotern entwickelt und eingeführt.
Automatisierte Produktionssysteme nutzen hochentwickelte Materialhandhabungsgeräte, um Blechteile zwischen aufeinanderfolgenden Pressvorgängen zu transportieren, wodurch manuelle Eingriffe überflüssig werden. Dieser Ansatz mindert nicht nur das Risiko von Verletzungen am Arbeitsplatz, sondern steigert auch die Produktionseffizienz erheblich, mit typischen Verbesserungen von etwa 35% im Durchsatz.
In der Zeit nach 2005 beschleunigte sich die Einführung automatisierter Produktionstechnologien für Stanzvorgänge in der heimischen Automobilproduktion dramatisch. Dieser Wandel markierte den Beginn einer neuen Ära in der Stanzautomatisierung. Abbildung 1 zeigt eine schematische Darstellung einer modernen automatisierten Stanzstraße, die die Integration von Robotersystemen, Transfermechanismen und Pressenausrüstung in einen nahtlosen Arbeitsablauf verdeutlicht.
Diese fortschrittlichen Anlagen verfügen häufig über Funktionen wie servogesteuerte Pressen für verbesserte Präzision und Energieeffizienz, Bildverarbeitungssysteme für die Qualitätskontrolle in Echtzeit und intelligente Steuerungssysteme, die Produktionsparameter auf der Grundlage von Echtzeitdaten optimieren. Die Umsetzung von Industrie 4.0-Prinzipien hat diese Systeme weiter verbessert und ermöglicht eine vorausschauende Wartung, digitale Zwillingssimulationen zur Prozessoptimierung und eine nahtlose Integration mit Unternehmensressourcenplanungssystemen (ERP).
Abbildung 1 Schematische Darstellung der automatischen Stanzanlage
Die derzeit am weitesten verbreiteten Pressen sind mechanische, geschlossene Pressen, die für verschiedene Kaltumformungsprozesse wie Stanzen, Umformen, Biegen, Korrigieren und Flachziehen von Dünnblechteilen verwendet werden können. Die Prozessparameter der Presse sind von entscheidender Bedeutung, da sie nicht nur die Qualität des Produkts beeinflussen, sondern auch einen erheblichen Einfluss auf Effizienz, Kosten und Sicherheit haben.
Der folgende Abschnitt gibt einen kurzen Überblick über die wichtigsten Parameter und die Genauigkeit einiger Pressen:
Grundlagen der Presse
Das Fundament der Presse muss ihr Gewicht tragen und den beim Anfahren der Presse entstehenden Schwingungskräften standhalten und diese Kräfte auf den Boden unter dem Fundament übertragen. Das Fundament muss zuverlässig einem Druck von 0,15 MPa standhalten können. Die Stärke des Fundaments wird vom Tiefbauamt auf der Grundlage der örtlichen Bodenbeschaffenheit ausgelegt und konstruiert. Das Betonfundament muss in einem einzigen Arbeitsgang ohne Unterbrechung gegossen werden.
Nach dem Auffüllen des Fundaments mit Beton sollte die Oberfläche einmal geglättet und dann mit einer Schaufel oder Schleifpapier nochmals geglättet werden. Zum Schutz vor Öl sollte die Unterseite des Fundaments mit säurebeständigem Zement beschichtet werden. In der Grundzeichnung sind die Innenmaße des Fundaments angegeben, die den Mindestplatzbedarf für die Aufstellung der Presse darstellen.
Festigkeitsindikatoren wie die Zementmarke, die Anordnung der Bewehrungsstäbe, die Größe der Fundamenttragfläche und die Dicke des Fundaments dürfen nicht verändert werden. Die Grundtragfähigkeit muss größer als 1,95 MPa sein.
Leitfaden für die Nachsynchronisation
Leitartikel: Es verbindet das Balkengetriebe mit dem Läufer und überträgt die verlangsamte Bewegung des Getriebes auf den Läufer, um die vertikale Bewegung des Läufers zu erreichen.
Im Allgemeinen gibt es Einpunkt-, Zweipunkt- und Vierpunkttypen, d. h. einen, zwei oder vier Leitpfosten.
Leitfaden für die Nachsynchronisation:
Er bezieht sich auf die Synchronisationsgenauigkeit der Zwei- oder Vierpunkt-Führungssäulen der Presse in ihrer Auf- und Abwärtsbewegung. Dieser Parameter wird normalerweise festgelegt, bevor die Presse das Werk verlässt. Die Genauigkeit der Führungssäulensynchronisation muss innerhalb von 0,5 mm gehalten werden. Eine übermäßige Fehlausrichtung führt zu einer erheblichen Zugbeanspruchung der Schieberkraft und beeinträchtigt die Qualität des am unteren Totpunkt geformten Produkts.
Einbauhöhe der Form
Die Montagehöhe bezieht sich auf den Abstand zwischen der Unterseite des Schiebers und der Oberseite des Tisches. Es gibt Höchst- und Mindestgrenzen für die Einbauhöhe. Bei der Konstruktion der Form sollte die Möglichkeit berücksichtigt werden, die Form nach dem Schleifen einzubauen und zu verwenden. Die geschlossene Höhe der Form sollte die maximalen oder minimalen Grenzwerte für die Pressformhöhe nicht erreichen.
Abbildung 2 zeigt eine schematische Darstellung der Montagehöhe der Presse.
Nennkraft der Presse
Die Nennkraft bezieht sich auf die maximale Stanzkapazität, die die Presse in ihrer Struktur sicher bewältigen kann. In der Praxis sollten Faktoren wie Materialdicke und Festigkeitsabweichung, Werkzeugschmierung und Verschleiß berücksichtigt werden, um einen angemessenen Spielraum für die Stanzkapazität zu gewährleisten.
Abbildung 2 Schematische Darstellung der Montagehöhe der Presse
Bei Stoßbelastungen wie dem Stanzen wird empfohlen, den Arbeitsdruck auf 80% oder weniger der Nennkraft zu begrenzen. Ein Überschreiten dieser Grenze kann zu erheblichen Vibrationen und Schäden an der Verbindung zwischen Schieber und Getriebe führen, was die normale Lebensdauer der Presse beeinträchtigt. Abbildung 3 zeigt die Kurve zwischen Nennkraft und zulässiger Kraft.
Abbildung 3 Zulässige Belastungskurve der Nennkraft
Druck der komprimierten Luft
Druckluft ist die wichtigste Energiequelle für den reibungslosen Betrieb der Presse und dient auch als Regelkreisquelle für die Stromquelle der Presse. Der Bedarf an Druckluft ist an den verschiedenen Standorten unterschiedlich hoch. Der werksseitig bereitgestellte Druckluftdruck richtet sich nach dem maximalen Bedarfswert der Presse. Teile mit niedrigeren Bedarfswerten sind zur Regulierung mit Druckminderungsventilen ausgestattet.
Druckluft im Produktionsprozess der Stanzautomation kann in zwei Kategorien unterteilt werden: Produktqualität und Aktionsfunktion. Die Kategorie Produktqualität dient der Gestaltung der Produktqualität, z. B. des Luftkissendrucks. Die Funktionskategorie dient der Steuerung der Pressenfunktionen, z. B. des Kupplungsdrucks.
Am Beispiel der Presse eines Fertigungsunternehmens zeigt Tabelle 1 die für die einzelnen Funktionsmodule der Presse erforderlichen Druckluftwerte. Es gibt noch viel mehr Parameter für die Presse als die fünf oben aufgeführten.
Im Folgenden finden Sie eine kurze Zusammenfassung und Darstellung der Presseparameter des Unternehmens (Tabelle 2).
Tabelle 1 Erforderlicher Druckluftdruckwert jedes Funktionsmoduls
Nein. | Artikel | Zuluftdruck MPa | Stellung des Druckregelventils | Hinweis | |
---|---|---|---|---|---|
1 | Gesamte Luftzufuhr | ≥0.5 | |||
2 | Kupplung | 0.32 | Begehbare Plattform | ||
3 | Balancer | 0.47 | Innenseite des linken vorderen Pfostens | Berechneter Wert ohne Schimmel | |
4 | Hydraulischer Schutz | Luftpumpe | 0.29 | Schieberegler innen | Berechnet |
5 | Entladeventil | 0.32 | Schieberegler innen | Berechnet | |
6 | Stretch-Polster | 0.04 ~ 0.8 | Innenseite des linken vorderen Pfostens |
Tabelle 2 Zusammenfassung der Pressparameter
Nein | Artikel | Wert | Einheit | |
---|---|---|---|---|
1 | Nennkraft | 10000 | kN | |
2 | Nennkraftweg (vor dem unteren Totpunkt) | 12.5 | mm | |
3 | Schieberegler Hublänge | 1000 | mm | |
4 | Anzahl der Schlittenhübe (bei Trockenlauf) | Kontinuierlich | 8-12 | Zeiten / Minute |
Maximal einfach | 8 | |||
Feinabstimmung | 3 | |||
5 | Maximale Ladehöhe | 1350 | mm | |
6 | Einstellung der Ladehöhe | 500 | mm | |
7 | Entfernung zur Schiene | L*R | 4970 | mm |
8 | Größe der Bodenfläche des Schiebers | L*R | 4600 | mm |
F*B | 2400 | mm | ||
9 | Größe des Arbeitstisches | L*R | 4600 | mm |
F*B | 2400 | mm | ||
10 | Dicke des Arbeitstisches | 300 | mm | |
11 | Beweglicher Arbeitstisch | Bewegter Weg | Nach links und rechts bewegen | |
Menge | 2 | Stück | ||
Höhe des beweglichen Tisches | 700 | mm | ||
Gewicht der Ladung | 50 | t | ||
12 | Schieberegler | Schienentyp | Rechtwinklige Führung | |
Art der Schläge | / | |||
Schlagende Kraft | / | kN | ||
Schlaganfall besiegen | / | mm | ||
Anzahl der Schläger | / | Stück | ||
13 | Stretch-Polster | Typ | Reines Gas Einzelkrone | |
Menge | 1 | Stück | ||
Auswurfkraft | 4500 | kN | ||
Rohlingshaltekraft | 4500 | kN | ||
Schlaganfall | 0 ~ 300 | mm | ||
14 | Auswuchtkraft (bei 0,62MPa Luftdruck) | 200 | kN | |
15 | Druck der Luftquelle am Einlass | 0.7 | MPa | |
16 | Verbrauch an freier Luft | 1 | m³ / min |
Schlussfolgerungen
Die Presse ist das wichtigste Gerät bei der Herstellung von Stanzteilen. Mit dem rasanten Wachstum der Automobilindustrie ist auch die Nachfrage nach hochpräzisen Anlagen gestiegen. Die Entwicklung des Stanzverfahrens hat drei Stufen durchlaufen: manuelle Produktionslinie, automatisierte intermittierende Produktion und automatisierte Hochgeschwindigkeits-Dauerproduktion. Bei jeder Aktualisierung des Modells spielen die Produktionsanlagen eine entscheidende Rolle.
Nachdem wir nun ein grundlegendes Verständnis der Presse haben, wollen wir uns nun dem Thema der automatischen Produktionslinien zuwenden.
Zu den automatischen Stanzanlagen gehören hauptsächlich: progressiv StahlstichMehrstationenstempelungen, und Tandemstempeln.
Aufgrund ihrer einzigartigen Eigenschaften werden diese Produktionslinien für die Herstellung verschiedener Automobilprodukte verwendet. Feinblech Teile und spielen eine wichtige Rolle bei der Automatisierung von Automobilen und effizienten Produktionssystemen. Dieser Artikel vergleicht und analysiert die Merkmale dieser drei Produktionslinien für die Stanzautomatisierung und gibt Hinweise zur Auswahl einer Produktionslinie auf der Grundlage ihrer Merkmale.
Dadurch wird es für die Unternehmen einfacher, eine Produktionslinie zu wählen, die ihren spezifischen Teilemerkmalen entspricht. Mit dem rasanten Wachstum der Automobilindustrie sind auch die vier großen Stanzindustrien für die Automobilherstellung aufgeblüht. Um die steigende Produktion zu bewältigen, sind verschiedene automatisierte Produktionslinien entstanden, die jeweils für unterschiedliche Produkte geeignet sind.
In diesem Artikel werden die gängigen Produktionslinien für die Stanzautomatisierung in Folgeverbundstempel, Mehrstationenstempel und Tandemstempel kategorisiert und die Merkmale und Auswahlmethoden der einzelnen Produktionslinien kurz analysiert, um Unternehmen bei der Auswahl der richtigen Produktionsmethode für ihre Produkteigenschaften zu unterstützen.
(1)Überblick:
Die automatische Produktionslinie für das Folgeverbundstanzverfahren ist eine Produktionslinie, die das Folgeverbundstanzverfahren anwendet und in der Regel aus einem Abwickelvorschub, einem Stempel, einem Folgeverbundwerkzeug und einer automatischen Stanzlinie besteht. Sie automatisiert den Prozess des Abwickelns des Coils, des Glättens des Bandes, des Einölens des Bandes, des Stanzens in Stücke und des Offline-Sammelns der fertigen Produkte.
Die wichtigste Komponente ist das Folgeverbundwerkzeug, das aus mehreren Stationen besteht, bis zu über 20 Stationen. Jede Station ist mit einer anderen verbunden, um verschiedene Bearbeitungsaufgaben zu erledigen, wie z. B. Stanzen und Beschneiden, FlanschenUmformung, Stanzen und so weiter. Alle diese Aufgaben werden in einem einzigen Hub der Presse erledigt. Nach Beendigung eines Hubes schiebt der Vorschub das Materialband um einen festen Schritt weiter, so dass mehrere Prozesse in einem einzigen Hub der Presse abgeschlossen werden können.
Wie in Abbildung 1 dargestellt.
Abbildung 1 Vereinfachtes Schema einer fortschrittlichen automatischen Produktionslinie
(2) Merkmale:
Der Produktionszyklus der Automatisierungslinie für das Folgeverbundstanzverfahren ist relativ hoch, in der Regel bis zu 30 Mal pro Minute.
Abbildung 2 Prozess der progressiven Formgestaltung
(1)Überblick:
Eine Produktionslinie mit mehreren unabhängigen Formstationen (in der Regel 4 bis 5), die sich auf einem Pressentisch mit großer Tonnage befinden, verwendet einen Entstapler oder Abwickler für die Beschickung, eine automatische Zuführungsstange für die Übergabe der bearbeiteten Teile und ein automatisches Förderband, um die fertigen Produkte offline zu sammeln. Wie in Abbildung 3 dargestellt."
Abbildung 3 Automatisierte Produktionslinie mit mehreren Stationen zum Stanzen
(2)Eigenschaften
Das Bodenmaterial kann entweder ein Rollenmaterial oder ein Rohling sein, was Flexibilität bietet und die Materialausnutzung verbessert. Die Produktionslinie verwendet eine automatische Stangenzuführung und hat eine geringere Stanzrate im Vergleich zur Folgeverbundwerkzeug-Produktionslinie, aber eine höhere Rate als die traditionelle Tandem-Produktionslinie, was zu einer höheren Produktionseffizienz führt.
Darüber hinaus können Sensoren wie Be- und Entladesensoren, Doppelmaterialerkennung, Greifersensoren, In-Mold-Sensoren usw. integriert werden, um die Position und den Status des Materials und des Produkts während der Produktion zu überwachen und ein hohes Maß an Sicherheit zu gewährleisten.
Es gibt strenge Anforderungen an die Zuführhöhe und die Prägerichtung der Formen an jeder Station, und um die Stabilität der Zuführung zu gewährleisten, müssen die Zustände jedes Prozesses im Allgemeinen gleich sein.
(1)Überblick:
Eine automatisierte Produktionslinie wird durch die Anordnung mehrerer Pressen in einer Reihe gebildet. Jeder Pressentisch enthält ein Formenpaar, das eine Stufe des Produktionsprozesses darstellt. Die Beladung, der Transfer der bearbeiteten Teile, die Entladung und die Verpackung werden von einem automatischen mechanischen Arm oder Roboter durchgeführt. Wie in Abbildung 4 dargestellt.
Abbildung 4 Automatische Produktionslinie für Tandemprägung
(2)Eigenschaften
Es hat ein breites Anwendungsspektrum und kann für die Herstellung verschiedener Stanzteile verwendet werden. Es gibt keine strengen Anforderungen an die Größe, Form und Dicke dieser Komponenten, was eine große Flexibilität bei der Herstellung großer Abdeckteile ermöglicht.
Die Produktionseffizienz ist jedoch gering, da ein Roboterarm für die Beschickung verwendet wird, wodurch die Zykluszeit begrenzt wird. Im Vergleich zu progressiven Produktionslinien und Produktionslinien mit mehreren Stationen ist diese Methode weniger effizient.
Andererseits wird die Wartung und Fehlerbehebung der Formen erleichtert. Jede Form gehört zu einer separaten Presse, was eine unabhängige Spannen und Arbeitsparameter. Das bedeutet, dass Wartung und Fehlersuche für jede Form separat durchgeführt werden können, ohne andere Prozesse zu beeinträchtigen.
Der Nachteil ist, dass diese Methode eine große Produktionsfläche erfordert. Eine herkömmliche Serienproduktionslinie umfasst in der Regel 4 bis 5 Pressen, die einen erheblichen Platzbedarf haben.
Bei der Auswahl einer automatisierten Produktionslinie für das Stanzen müssen mehrere kritische Faktoren sorgfältig bewertet werden, um eine optimale Leistung, Effizienz und Produktqualität zu gewährleisten:
(1) Materialeigenschaften:
Beurteilen Sie die Eigenschaften des Materials, einschließlich seiner Verformbarkeit, Zugfestigkeit und Härte. Diese Faktoren beeinflussen die Wahl zwischen Coil- und Blechzuführungssystemen sowie die spezifischen Anforderungen an die Werkzeuge. Hochfeste Stähle können zum Beispiel robustere Pressensysteme und spezielle Werkzeugkonstruktionen erfordern, um Rückfederung zu verhindern und enge Toleranzen zu erreichen.
(2) Materialdicke und Abmessungsbereich:
Berücksichtigen Sie sowohl die Materialstärke als auch den Abmessungsbereich für Ihre Produktlinie. Diese Informationen sind entscheidend für:
(3) Produktionsvolumen und Nachfrageschwankungen:
Analysieren Sie Ihren monatlichen Produktionsbedarf und mögliche Nachfrageschwankungen. Diese Bewertung hilft bei:
(4) Produktkomplexität und Qualitätsanforderungen:
Prüfen Sie die Kompliziertheit Ihrer Stanzteile und die damit verbundenen Qualitätsstandards:
(5) Künftige Produktionserfordernisse:
Antizipieren Sie mögliche Änderungen in Ihrem Produktmix oder Volumen:
(6) Total Cost of Ownership (Gesamtbetriebskosten):
Denken Sie nicht nur an die Anfangsinvestition:
(7) Integration in bestehende Systeme:
Beurteilen Sie, wie sich die neue Stempellinie in Ihre bestehende integrieren lässt:
Automatisierte Produktionslinie für progressive Stanzformen
Je nach den Merkmalen der einzelnen Prozesse, die auf einem Band verteilt sind, und den maximalen Prozessstempeln, die erreicht werden können, kann es für die Herstellung kleiner Teile an der Karosserie verwendet werden und eine hohe Leistung bieten.
Automatisierte Produktionslinie mit mehreren Stationen zum Stanzen
Sie kann für die schnelle Produktion von mittelgroßen, verformungsbeständigen Teilen eingesetzt werden. Symmetrische Teile mit komplexer linker und rechter Form sowie Produkte, die mit dem automatischen Hebel gegriffen werden können, können auf einer automatischen Linie hergestellt werden.
Automatisierte Produktionslinie für Tandem-Stanzen
Durch die unabhängige Verteilung der einzelnen Prozesse auf die einzelnen Pressen bietet diese Produktionslinie ein Höchstmaß an Flexibilität. Sie ist ideal für die Herstellung großer, komplexer Teile und erleichtert die Fehlersuche bei einzelnen Prozessen und die unabhängige Produktion, was die Aufrechterhaltung einer hohen Qualitätskontrolle über die Produkte erleichtert.
Die Merkmale der drei Produktionslinien sind in Tabelle 1 dargestellt
Vorteile | Benachteiligungen | Anwendungen | |
---|---|---|---|
Progressiv | ① Hohe Schlagzeiten, hohe Effizienz und hohe Leistung ② Geringer Platzbedarf | ① Schlechte Materialausnutzung ② Nur für Kleinteile geeignet ③ Die Form für die einzelnen Teile ist groß und schwierig zu beheben. | ① Kleine Strukturteile mit hoher Nachfrage |
Übertragung | ① Hoher Grad an Automationseffizienz ② Fähigkeit zur Herstellung einer breiten Palette von Produkten ③ Hohe Auslastung der Materialien ④ Ausgestattet mit zahlreichen automatischen Sicherheitsvorrichtungen. | ① Der Konstruktionsprozess des Produkts stellt höhere Anforderungen an den gemeinsamen Einbau von Formen. ② Der kombinierte Einbau von Formen führt zu umständlicher Fehlersuche und Wartung. ③ Die Produktionslinien sind wenig austauschbar und erfordern spezifische Formen für die Produktion auf einer einzigen Linie. | Trägerteile, Verstärkungsteile, Umlenkteile usw. haben eine gleichmäßige Form und lassen sich leicht einspannen, und der gesamte Prozess kann auf derselben Werkbank durchgeführt werden. ② Teile mit größerem Bedarf |
Tandem | ① Die meisten anwendbaren Produkttypen ② Flexible Liefermethoden für das Be- und Entladen und die Verarbeitung von Teilen ③ Hohe Austauschbarkeit der Produktionslinie ④ Einfache Fehlersuche und Wartung ⑤ Hohe Materialausnutzung | ① Großer Fußabdruck ② Geringe Produktionseffizienz | ① Große Teile und Verkleidungsteile ② Teile mit komplizierter Technik und hohen Qualitätsanforderungen |
Bei der Wahl der Produktionslinien für die Stanzautomatisierung können zwei Prioritäten gesetzt werden: hoher Ausstoß und hohe Flexibilität.
Für ein großes Volumen an Teilen sollte eine automatisierte Produktionslinie mit hoher Effizienz und hohem Ausstoß gewählt werden.
Wenn die Teile komplex sind und eine fortschrittliche Produktionstechnologie erfordern, sollte eine flexible Produktionslinie in Betracht gezogen werden.
Dies wird in Abbildung 5 in einer einfachen Darstellung veranschaulicht.
Abbildung 5 Besondere Absicht der 3 Produktionslinien
Aufgrund ihrer einzigartigen Eigenschaften werden Stanzautomaten in den großen Automobilwerken weit verbreitet eingesetzt, um das Wachstum der Automobilindustrie und den raschen Anstieg der Automobilproduktion zu unterstützen.
Das Verständnis und die Analyse der Produktionslinie für die Stanzautomatisierung hilft bei der Auswahl der Stanzproduktionsmethode und nutzt die Stärken der jeweiligen automatischen Linien zum Vorteil des Automobilsektors.
Im Ausland abgekürzt::P.R.G /T.R.F/T.D.M
Welches Produktionsverfahren für die Stanzautomation gewählt werden sollte, hängt im Allgemeinen von den folgenden Faktoren ab:
Progressiv die Automatisierung Methode
Ein Folgeverbundwerkzeug ist eine Art von Kaltprägewerkzeug, das ein streifenförmiges Rohmaterial verwendet und in einem Prägezyklus mit mehreren Stationen mehrere Prägevorgänge gleichzeitig durchführt.
Bei jedem Stanzvorgang bewegt sich der Streifen um eine bestimmte Strecke, bis das Endprodukt fertig ist.
Mehrstationen-Automatisierungsverfahren (Transfer)
Bei der Mehrstationen-Stanztechnik werden mehrere Prozessformen auf einer Stanzpresse angeordnet und die einmalige Hin- und Herbewegung des Stanzschlittens genutzt, um verschiedene Arbeitsgänge wie Schneiden, Stanzen, Biegen, Strecken, Beschneiden usw. gleichzeitig an den auf der Werkzeugmaschine installierten Formen durchzuführen. Der Roboter transportiert das Werkstück bei jedem Zyklus von einer Station zur nächsten, um ein fertiges Teil herzustellen.
Sie können in zweidimensionale und dreidimensionale Manipulatoren unterteilt werden.
Dreidimensionales Handlingverfahren
Tandem-Automatisierungsverfahren (Tandem)
Mehrere Stempel werden in einer Reihe angeordnet, um eine ganze Stanzlinie zu bilden, wobei die Matrize jedes Stempels einem separaten Umformverfahren entspricht.
Der Materialtransport zwischen den Stanzen wird durch Roboterautomation erledigt.
Diese Methode eignet sich vor allem für Produktlinien mit geringem Leistungsbedarf, begrenzten Verarbeitungsschritten und unabhängigen Produktionslinien mit hoher Flexibilität.
-END-