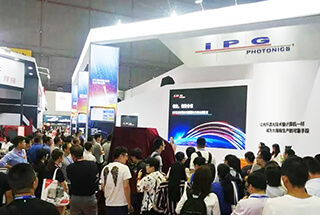
Dieser Artikel erkundet die faszinierende Welt der CO2-Laserschneidtechnologie, die die moderne Fertigung grundlegend verändert. Sie erfahren, wie diese Methode unübertroffene Präzision und Effizienz liefert und die Industrie weltweit verändert.
CO2 Beim Laserschneiden werden CO2-Laserstrahlen mit Hilfe einer Fokussierlinse auf die Materialoberfläche gerichtet, wodurch diese geschmolzen wird.
Gleichzeitig wird das geschmolzene Material durch einen koaxialen Druckgasstrom abgetragen, so dass sich die Laserstrahlen und das Material relativ zueinander entlang einer definierten Bahn bewegen können, was zu einer präzisen Schnittform führt.
Seit den 1970er Jahren hat die Entwicklung von CO2-Lasern und numerischer Steuerungstechnik das CO2-Laserschneiden zu einem hochmodernen Verfahren zum Schneiden von Blechen gemacht.
In den 1950er und 1960er Jahren, Plattenschneiden Methoden enthalten:
In den 1970er-Jahren wurde zur Verbesserung der Qualität von Brennschnitten die Präzision des Sauerstoffs Brennschneiden und das Plasmaschneiden wurde populär.
Um die Herstellungszeit für große Stanzformen zu verkürzen, wurden das CNC-Stanzen und die Elektrobearbeitungstechnologie gefördert.
Jede Art von Schneide- und Stanzverfahren hat ihre eigenen Grenzen und wird in spezifischen industriellen Produktionsanwendungen eingesetzt.
Gute Schnittqualität:
Hohe Schnittgeschwindigkeit:
Ein 2KW-Laser mit einer Schneidgeschwindigkeit von 1,6m/min kann beispielsweise 8mm dicken Kohlenstoffstahl schneiden, während bei 2mm dickem Edelstahl eine Schneidgeschwindigkeit von 3,5m/min erreicht werden kann. Die Laserschneidverfahren führt zu einem kleinen thermischen Einflussbereich und minimaler Verformung.
Sauber, sicher und schadstofffrei:
Die Verwendung von CO2 Laserschneiden verbessert die Arbeitsumgebung für die Bediener erheblich. Auch wenn es die Elektrobearbeitung in Bezug auf Präzision und Oberflächenrauheit der Schnitte nicht übertrifft und im Vergleich zum Brenn- und Plasmaschneiden Einschränkungen bei der Schnittdicke aufweist, haben seine Vorteile dazu geführt, dass es die traditionellen Schneidtechniken ersetzt, insbesondere beim Schneiden von nichtmetallische Werkstoffe.
In China herrscht seit den 1990er Jahren und der Entwicklung der sozialistischen Marktwirtschaft ein intensiver Wettbewerb zwischen den Unternehmen, der dazu führt, dass jedes Unternehmen sorgfältig fortschrittliche Fertigungstechnologien auswählt, die seinen spezifischen Anforderungen entsprechen, um die Produktqualität und die Produktionseffizienz zu verbessern. Infolgedessen ist CO2 Laserschneiden Technologie hat in China ein schnelles Wachstum erfahren.
Das erste CO2 Die Laserschneidmaschine wurde in den 1970er Jahren erfunden. In den vergangenen drei Jahrzehnten wurde die Maschine mit der Erweiterung ihrer Anwendungsbereiche kontinuierlich verbessert.
Derzeit produzieren viele internationale und inländische Unternehmen verschiedene Arten von CO2 Laserschneidmaschinen, um der Marktnachfrage gerecht zu werden, einschließlich 2D-Plattenschneidmaschinen, 3D-Raumkurvenschneidmaschinen und Rohrschneidemaschinen.
Zu den führenden ausländischen Unternehmen in diesem Bereich gehören Trumpf (Deutschland) und Prima (Italien), Bystronic (Schweiz), Amada und MAZAK (Japan), NTC (Japan) und HG Laser Lab (Australien).
Laut dem Jahresbericht 2000 von "Industrial Laser Solution", einer führenden amerikanischen Zeitschrift der Laserindustrie, wurde der Gesamtumsatz mit Laserschneidsystemen weltweit (vor allem CO2 Laserschneidsysteme) waren 1999 3325 mit einem Gesamtvolumen von $1,174 Milliarden.
In China werden fast 100 CO2 Laserschneidmaschinen im Gesamtwert von 150 Mio. RMB hergestellt, aber im Vergleich zu den Industrieländern werden sie nur in relativ geringem Umfang eingesetzt. Bis 2003 wurde die Zahl der CO2 Die Zahl der in China in der industriellen Produktion eingesetzten Laserschneidsysteme lag bei rund 500, was etwa 1,5% der weltweiten Gesamtzahl entspricht.
Es gibt zwei Haupttypen von Organisationen, die CO2 Laserschneidtechnik: große und mittelgroße Fertigungsunternehmen und Bearbeitungsstationen.
Große und mittelgroße Unternehmen des verarbeitenden Gewerbes verfügen über starke wirtschaftliche und technische Ressourcen und benötigen für viele ihrer Materialien das Schneiden und Stanzen.
Verarbeitungsstationen, im Ausland auch als Job Shops bekannt, sind spezialisiert auf die Bereitstellung von Laserbearbeitung Dienstleistungen für andere erbringen und keine eigenen dominanten Produkte haben. Diese Stationen können den Bedarf kleiner und mittlerer Unternehmen decken und spielen auch eine Rolle bei der Förderung der frühzeitigen Einführung der Laserschneidtechnologie.
Im Jahr 1999 gab es in den Vereinigten Staaten 2.700 Laserbearbeitungsstationen, von denen 51% auf das Laserschneiden spezialisiert waren.
In den 1980er Jahren konzentrierten sich die Laserbearbeitungsstationen in China hauptsächlich auf die Laserwärmebehandlung. Seit den 1990er Jahren ist die Zahl der Laserschneid- und -bearbeitungsanlagen jedoch gestiegen.
Da die Reformen im System der großen und mittleren Unternehmen in China fortgesetzt werden und die Wirtschaftskraft des Landes wächst, wird erwartet, dass immer mehr Unternehmen die CO2 Laserschneidetechnik.
Im Inland, CO2 Das Laserschneiden wird häufig zum Schneiden von Blechen aus kohlenstoffarmem Stahl mit einer Dicke von 12 mm oder weniger, von Blechen aus rostfreiem Stahl mit einer Dicke von 6 mm oder weniger und von nichtmetallischen Materialien mit einer Dicke von 20 mm oder weniger eingesetzt. Es wird auch in der Automobil- und Luftfahrtindustrie zum Schneiden dreidimensionaler räumlicher Kurven verwendet.
Derzeit lassen sich die für das CO2-Laserschneiden geeigneten Produkte grob in drei Gruppen einteilen:
Zusätzlich zu den oben genannten Anwendungen wird das CO2-Laserschneiden in immer mehr Branchen eingesetzt. So werden beispielsweise 3D-Laserschneidsysteme oder Industrieroboter zum Schneiden räumlicher Kurven eingesetzt, und es wurde spezielle Software entwickelt, um den Prozess von der Zeichnung bis zum Schneiden der Teile zu rationalisieren.
Die Forscher konzentrieren sich auf die Verbesserung der Produktionseffizienz durch die Entwicklung spezieller Schneidsysteme, Materialtransportsysteme und Linearmotorantriebssysteme. Die Schnittgeschwindigkeiten haben inzwischen 100 m/min überschritten.
Um den Einsatz im Maschinenbau und im Schiffbau zu erweitern, wurde die Schneiddicke für kohlenstoffarmen Stahl auf über 30 mm erhöht, und es besteht ein wachsendes Interesse an der Stickstoffgasschneidetechnik für kohlenstoffarmen Stahl, um die Qualität des Blecheinschnitts zu verbessern.
Daher ist es für die Techniker in China nach wie vor sehr wichtig, den Einsatz des CO2-Laserschneidens zu erweitern und einige technische Probleme in der Praxis zu lösen.
Die Parameter des Laserstrahls sowie die Leistung und Präzision der Maschine und CNC-System haben einen direkten Einfluss auf die Effizienz und Qualität des Laserschneidens. Schlüsseltechnologien, wie sie für Teile mit hoher Schneidgenauigkeit oder dickeren Materialien erforderlich sind, müssen beherrscht und gelöst werden.
Einer der Vorteile des Laserschneidens ist die hohe Energiedichte der Strahlen, die im Allgemeinen mehr als 10 W/cm2 beträgt. Die Energiedichte ist umgekehrt proportional zu 4/πd^2, daher wird der Brennfleckdurchmesser so klein wie möglich gehalten, um einen schmalen Spalt zu erzeugen.
Der Brennfleckdurchmesser ist direkt proportional zur Fokustiefe des Objektivs, d. h. je kleiner die Fokustiefe, desto kleiner der Brennfleckdurchmesser. Beim Schneiden können jedoch Spritzer entstehen, und wenn das Objektiv zu nahe am Werkstück ist, kann es leicht beschädigt werden.
Daher werden beim CO2-Hochleistungslaserschneiden in der Regel Linsen mit einer Brennweite von 5″ bis 7,5″ (127 bis 190 mm) verwendet. Der tatsächliche Brennfleckdurchmesser liegt zwischen 0,1 und 0,4 mm.
Die effektive Fokustiefe hängt auch vom Linsendurchmesser und dem zu schneidenden Material ab. Beim Schneiden von Kohlenstoffstahl mit einer 5″-Linse sollte die Schärfentiefe beispielsweise innerhalb eines Bereichs von +2% der Brennweite oder etwa 5 mm liegen, um eine optimale Schnittqualität zu erzielen.
Um die besten Schneidergebnisse zu erzielen, ist die Fokussierung entscheidend und hängt von der Materialstärke ab. Bei Metallwerkstoffen unter 6 mm sollte der Fokus auf der Oberfläche liegen. Bei Kohlenstoffstahl, der dicker als 6 mm ist, sollte der Fokus oberhalb der Oberfläche liegen. Bei rostfreiem Stahl, der dicker als 6 mm ist, sollte der Fokus unter der Oberfläche liegen, aber die genaue Größe sollte durch Versuche ermittelt werden.
Drei einfache Methoden zur Bestimmung der Fokusposition in der industriellen Produktion:
Es gibt drei Methoden, um den Fokus der CO2-Laserschneidmaschine zu bestimmen:
Bei Schneidmaschinen mit fliegendem Lichtweg ist die Fokusbestimmung komplexer, da der Divergenzwinkel der Laserstrahlen Unterschiede im Abstand zwischen dem nahen und dem fernen Ende verursacht, was zu Unterschieden in der Strahlgröße vor der Fokussierung führt. Je größer der Durchmesser des einfallenden Strahls ist, desto kleiner ist der Brennfleck.
Um die Schwankungen in der Brennfleckgröße zu minimieren, die durch Änderungen der Strahlgröße vor der Fokussierung verursacht werden, bieten die Hersteller von Laserschneidsystemen einige spezielle Geräte an, aus denen die Benutzer wählen können:
Die Laserschneidetechnik erfordert, von wenigen Ausnahmen abgesehen, in der Regel eine kleine Bohrung im Material. In der Vergangenheit wurde bei Laserstanzmaschinen zunächst ein Loch mit einem Stempel gebohrt und dann mit einem Laser aus dem Loch geschnitten. Für nicht stanzende Laserschneidmaschinen gibt es zwei grundlegende Verfahren Bohren Methoden:
Beim Pulsbohren sollte der verwendete Laser nicht nur eine hohe Ausgangsleistung, sondern auch eine hohe zeitliche und räumliche Strahlcharakteristik aufweisen. Der Prozess des Pulsbohrens sollte auch über ein zuverlässiges Gaspfadsteuerungssystem verfügen, um die Gasart, die Gasdruckumschaltung und die Bohrzeit zu steuern. Der Übergang vom Pulsbohren zum kontinuierlichen Schneiden des Materials sollte ebenfalls hervorgehoben werden, um qualitativ hochwertige Schnitte zu erzielen.
In der industriellen Produktion ist es praktischer, die durchschnittliche Leistung des Lasers zu ändern, z. B. durch Änderung der Pulsbreite, der Frequenz oder beides gleichzeitig. Es hat sich gezeigt, dass die dritte Methode die beste Wirkung hat.
Wenn Schneidestahl Mit einem Laser werden Sauerstoff und Laserstrahl durch eine Düse auf das Material gerichtet, um einen Strom zu bilden. Damit das Schneiden effektiv ist, muss der Luftstrom groß und schnell sein, um eine ausreichende Oxidation und exotherme Reaktion im geschnittenen Material zu erzeugen. Außerdem muss der Luftstrom genügend Schwung haben, um das geschmolzene Material zu entfernen. Die Konstruktion der Düse und die Steuerung des Luftstroms, wie z. B. der Druck und die Position der Düse und des Werkstücks, sind entscheidende Faktoren, die die Schnittqualität beeinflussen.
Die derzeit beim Laserschneiden verwendeten Düsen sind einfach aufgebaut und bestehen aus einem Kegel mit einer kleinen Öffnung an der Spitze. Die Konstruktion der Düse erfolgt in der Regel durch Experimente und Ableitungsmethoden. Da die Düse jedoch in der Regel aus Kupfer besteht und klein und anfällig ist, muss sie häufig ausgetauscht werden und wird bei strömungsmechanischen Berechnungen und Analysen normalerweise nicht berücksichtigt.
Bei der Anwendung tritt Gas mit dem Druck Pn in die Düse ein und erzeugt einen Düsendruck. Das Gas strömt aus der Düse aus und erreicht nach einer gewissen Entfernung die Oberfläche des Werkstücks, wodurch der Schneiddruck Pc entsteht. Schließlich dehnt sich das Gas aus und bildet den atmosphärischen Druck Pa. Untersuchungen haben gezeigt, dass mit steigendem Pn auch die Geschwindigkeit des Luftstroms und Pc zunehmen.
Die Formel zur Berechnung der Luftstromgeschwindigkeit lautet:
V = 8.2d^2 (Pg + 1)
wo:
V = Luftstromgeschwindigkeit in L/min
d = Düsendurchmesser in mm
Pg = Düsendruck (Flächenpressung) in bar
Wenn der Düsendruck einen bestimmten Wert überschreitet, kann der Luftstrom von Unterschall in Überschall übergehen und zu einer normalen schrägen Stoßwelle werden. Der Schwellenwert hängt vom Verhältnis des Düsendrucks (Pn) zum atmosphärischen Druck (Pa) und dem Freiheitsgrad (n) der Gasmoleküle ab. Wenn zum Beispiel n=5 für Sauerstoff und Luft gilt, liegt der Schwellenwert Pn bei 1,89 bar.
Wenn der Düsendruck höher ist, d. h. Pn/Pa > 4 bar, kann sich die normale schräge Stoßwelle des Luftstroms in einen normalen Stoß verwandeln, wodurch der Schneiddruck (Pc) sinkt, die Luftgeschwindigkeit abnimmt und sich ein Wirbel auf der Werkstückoberfläche bildet, was die Wirkung des Luftstroms beim Entfernen von geschmolzenem Material schwächt und die Schneidgeschwindigkeit beeinträchtigt.
Um dies zu vermeiden, wird der Düsendruck von Sauerstoff oft unter 3 bar gehalten, wenn eine Düse mit einem Kegel und einem kleinen Loch an der Spitze verwendet wird.
Um die Geschwindigkeit des Laserschneidens zu erhöhen, wurde eine konvergent-divergente Düse, die so genannte Laval-Düse, auf der Grundlage aerodynamischer Prinzipien entwickelt. Diese Düse erhöht den Druck, ohne normale Stoßwellen zu verursachen. Die Struktur der Düse ist in Abbildung 4 dargestellt, um die Herstellung zu erleichtern.
Das Laserzentrum der Universität Hannover in Deutschland führte Experimente durch, bei denen ein 500-W-CO2-Laser (mit einer Brennweite von 2,5) mit einer Kegellochdüse und einer Lavaldüse kombiniert wurde. Die Ergebnisse der Experimente sind in den Abbildungen dargestellt, die die Beziehung zwischen der Oberflächenrauheit (Rz) und der Schnittgeschwindigkeit (Vc) für die Düsen Nr. 2, Nr. 4 und Nr. 5 bei unterschiedlichen Sauerstoffdrücken zeigen.
Wie aus den Abbildungen hervorgeht, erreicht die Schnittgeschwindigkeit der Lochdüse Nr. 2 bei einem Druck (Pn) von 400 Kpa (oder 4 bar) nur 2,75 m/min (für eine 2 mm dicke Kohlenstoffstahlplatte). Bei einem Pn von 500 Kpa oder 600 Kpa erreicht die Schnittgeschwindigkeit der Laval-Düsen Nr. 4 und Nr. 5 jedoch 3,5 m/min bzw. 5,5 m/min.
Es ist wichtig zu wissen, dass der Schneiddruck (Pc) vom Abstand zwischen Werkstück und Düse abhängt. Die schräge Stoßwelle wird wiederholt an der Luftstromgrenze reflektiert, wodurch der Schneiddruck periodisch schwankt.
Die erste Zone mit hohem Schneiddruck befindet sich in der Nähe des Düsenauslasses, wobei der Abstand zwischen der Oberfläche des Werkstücks und dem Düsenauslass etwa 0,5 bis 1,5 mm beträgt. Dies führt zu einem hohen und stabilen Schneiddruck (Pc), der in der industriellen Produktion weit verbreitet ist.
Die zweite Zone mit hohem Schneiddruck ist etwa 3 bis 3,5 mm vom Düsenaustritt entfernt und weist ebenfalls einen hohen Schneiddruck auf, der zu guten Schneidergebnissen und zum Schutz der Linse beiträgt und damit deren Lebensdauer erhöht.
Andere Bereiche mit hohem Schneiddruck auf den Kurven sind jedoch zu weit vom Düsenaustritt entfernt, um sich auf den fokussierten Strahl auszurichten.
Zusammenfassend lässt sich sagen, dass die CO2-Laserschneidtechnologie in der industriellen Produktion Chinas zunehmend eingesetzt wird. Im Ausland werden Anstrengungen unternommen, um Schneidtechnologien und -anlagen zu erforschen, die höhere Schneidgeschwindigkeiten erreichen und dickere Stahlplatten bearbeiten können.
Um den wachsenden Anforderungen an eine qualitativ hochwertige industrielle Produktion und eine höhere Effizienz gerecht zu werden, ist es wichtig, sich auf die Lösung wichtiger technologischer Fragen und die Einführung von Qualitätsstandards zu konzentrieren, damit diese neue Technologie in unserem Land eine größere Verbreitung findet.