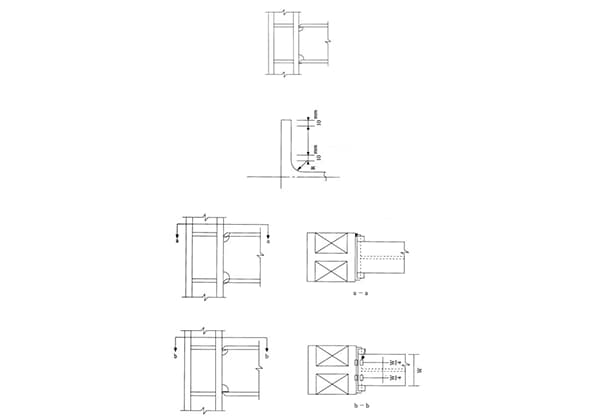
Wie kann sich die Schweißnahthärte auf die Gesamtintegrität einer Struktur auswirken? Die richtige Härte der Schweißnähte ist beim Schweißen von entscheidender Bedeutung, da sie die Zähigkeit und Haltbarkeit der Verbindungen beeinflusst. Dieser Artikel befasst sich mit praktischen Tipps und bewährten Verfahren zur Kontrolle der Schweißnahthärte, wobei Faktoren wie Zwischenlagentemperatur, Wärmebehandlung und Schweißverfahren berücksichtigt werden. Wenn Sie diese Richtlinien befolgen, können Sie die Qualität und Leistung der Schweißnähte verbessern und häufige Probleme im Zusammenhang mit der Schweißnahthärte vermeiden. Tauchen Sie ein und erfahren Sie, wie eine präzise Steuerung den Unterschied bei Ihren Schweißprojekten ausmachen kann.
Der Legierungsgehalt des Stahls SA335-P91 beträgt wCr=9%, wMo=1%, wV=0,2%, wNb=0,08%, wN=0,05%.
Er gehört zu den martensitischen hitzebeständigen Stählen, und sein metallographisches Gefüge ist kohlenstoffarmer vergüteter Martensit.
Durch die Anwendung der Mikrolegierungskontrolltechnologie und anderer Maßnahmen zur Kornfeinung wird er zu einem Feinkornstahl, der nicht nur die Schlagzähigkeit des Stahls verbessert, sondern auch äußerst förderlich für die Verbesserung der Hochtemperatur-Kriechfestigkeit des Stahls ist.
SA335-P91 ist ein martensitischer Feinkornstahl, was das Hauptproblem von P91 Stahlschweißen unterscheidet sich von anderen niedrig legierten hitzebeständigen Stählen.
Die Schwachstelle von Schweißverbindungen liegt nicht in der FusionszoneAber im Schweißgut zeigt sich vor allem, dass die Zähigkeit des Schweißguts abnimmt und die Schweißhärte hoch ist.
(1) Da es sich bei SA335-P91 um einen Feinkornstahl handelt, erhöht sich die Zwischenlagentemperatur beim Schweißen um 8/5, wodurch die Körner anwachsen und die ursprüngliche Festigkeit und Zähigkeit des Stahls verloren geht.
Es ist jedoch unmöglich, sie während des Schweißens vor Ort zu normalisieren.
Daher muss die Zwischenlagentemperatur während des Schweißens streng kontrolliert werden, um Kornwachstum zu verhindern.
(2) Die Erwärmungsbreite, die konstante Temperatur, die Dauer der konstanten Temperatur, die Isolationsbreite und die Isolationsdicke der Wärmebehandlung sind die wichtigsten Faktoren, die die Zähigkeit der Schweißnaht beeinflussen.
Eine angemessene Erhöhung der Heizbreite, der Isolierbreite, der Isolierdicke und der Konstanttemperaturzeit trägt dazu bei, den Anlaßgrad des Materials zu erhöhen. Martensitgefüge und verbessern die Zähigkeit der Schweißnaht.
(1) Das Gegenschweißen erfolgt doppellagig Argon-Lichtbogenschweißenund die anderen Lagen sind mehrlagige und mehrlagige Schweißverfahren.
Die Elektrode ist φ3,2 mm dick, und die Dicke einer einzelnen Schicht beträgt ≤ 3 mm.
Während der SchweißverfahrenDie Beziehung zwischen dem Schweißstrom und der Schweißgeschwindigkeit sollte gut verstanden werden.
Weiterführende Lektüre: Drahtvorschubgeschwindigkeit und Schweißstrom
Durch Erhöhung der Schweißgeschwindigkeit, Verringerung der Dicke der Schweißraupesollte das weit ausschwingende schnelle Dünnschichtschweißverfahren angewendet werden.
(2) Während des Schweißens verwenden die Techniker eine Ferninfrarot-Temperaturmesspistole, um die Zwischenlagentemperatur jeder Schweißlage zu messen (die Zwischenlagentemperatur ist die Temperatur 10~20mm vor dem Schmelzbad, ausgedrückt durch den höchsten Wert), und die Zwischenlagentemperatur wird streng unter 300 ℃ kontrolliert.
Wenn die Ferninfrarot-Temperaturmesspistole anzeigt, dass die Temperatur 300 ℃ übersteigt, unterbrechen Sie das Schweißen sofort und setzen Sie es fort, wenn die Temperatur auf 230 ℃ sinkt.
Nach dem Schweißen der einzelnen Lagen misst der Techniker mit einem Messschieber die Schweißwulstverdickung.
Die maximale Verdickung beträgt ≤ 3 mm.
Es ist strengstens verboten, eine Kehlnaht zwischen der Rille und der Schweißraupe.
Der Schweißstrom wird entsprechend den Eigenschaften der Elektrode gewählt.
Bei der Elektrode mit Umhüllungsübergang kann die Elektrode mit einem geringeren Strom geschmolzen werden, wodurch die Wärmezufuhr reduziert werden kann.
Der Nachteil ist, dass der Schmelzpunkt des Wolframs in der Beschichtung hoch ist, was leicht zu Wolframeinschlüssen in der Schweißnaht führen kann.
Mit einem Wort, unabhängig davon, welche Art von Schweißdraht verwendet wird, ist es notwendig, die Fließfähigkeit des geschmolzenen Eisens und das klare Schmelzbad zu gewährleisten, insbesondere die gute Verschmelzung an der Wurzel der Rille.
Auf dieser Grundlage sollen so weit wie möglich kleine Spezifikationen verwendet werden.
Der Posten Schweißwärme Die Wärmebehandlung erfolgt mit der Wärmebehandlungsmaschine DKPC-12360-12, die durch einen keramischen Widerstand beheizt wird, und das Thermoelement ist fest eingebaut.
Es werden ein gepanzertes Thermoelement vom Typ K, ein angepasster Kompensationsdraht und ein automatischer Temperaturschreiber verwendet, und es wird Aluminiumsilikat-Isolierwatte verwendet.
Zum Vorwärmen wird eine elektrische Heizung verwendet.
Zur Kontrolle der Temperatur werden vier Thermoelemente verwendet.
Die Temperaturkontrollpunkte sind 3, 6, 9 und 12.
Das Ende des Thermoelements ist 20 mm von der Kante der Schweißnaht entfernt (siehe Abbildung 1), und das Vorwärmtemperatur beträgt 150 ℃.
Wenn die Temperatur die konstante Temperatur von 0,5h erreicht hat, kann mit dem Gegenschweißen begonnen werden, um das Temperaturgleichgewicht zu erhalten und die Schweißbarkeit des unedlen Metalls.
Während der abgeschirmten Metall LichtbogenschweißenWenn die Temperatur auf 230 ℃ ansteigt, wird der Übertemperaturalarm auf 260 ℃ eingestellt, und die Zwischenlagentemperatur muss 200-300 ℃ betragen.
Die Wärmebehandlungsanlage überwacht die Temperatur und heizt sie sofort auf, wenn die Temperatur zu niedrig ist.
Wenn die Temperatur zu hoch ist, muss das Schweißen sofort unterbrochen werden, und das Schweißen muss wieder aufgenommen werden, wenn die Temperatur wieder auf 230 ℃ gesunken ist.
Die Zwischenlagentemperatur muss von der Wärmebehandlungsmaschine während des gesamten Prozesses überwacht und kontrolliert werden. Schweißverfahren.
Abb. 1 Thermoelement 20 mm vom Rillenrand entfernt bei der Zwischenlagentemperaturkontrolle
Erstens muss das Thermoelement während der Wärmebehandlung in gutem Kontakt mit der Schweißnaht stehen.
Das heiße Ende des Thermoelements wird im Allgemeinen auf der ersten Schweißnaht in der Nähe des Rillenrandes platziert und muss fest mit 20 # Eisendraht verbunden werden, um zu verhindern, dass sich das Thermoelement aufgrund der thermischen Ausdehnung bei konstanter Temperatur lockert, wie in Abb. 2 und Abb. 3 gezeigt.
Abb. 2 Legen Sie das heiße Ende des Thermoelementes auf die erste Schweißnaht, um einen guten Kontakt zwischen dem heißen Ende und der Schweißnaht zu gewährleisten.
Abb. 3 Installationsschema der Thermoelemente für die Temperaturkontrolle in Zone 4 und Zone 3 der PWHT
Zweitens sind beim Einbau des Heizgeräts Schweißperlen, Schweißschlacke und Spritzer auf der Oberfläche des Schweißteils zu entfernen, damit das Heizgerät und die Oberfläche des Schweißteils dicht zusammenliegen.
Nach dem Einbau des Heizgeräts ist es mit 20 # Eisendraht zu umwickeln, um die Ausdehnung des Heizbands bei hohen Temperaturen zu verhindern (siehe Abb. 4).
Abb. 4 Das Heizgerät muss nach dem Einbau mit dickem Eisendraht abgebunden werden.
Drittens, erhöhen Sie die Dicke und Breite der Wärmebehandlung Isolierung, und die Isolierung Dicke ist 100mm, wie in Abb. 5 gezeigt.
Abb. 5 Dicke und Breite der Wärmekonservierung bei zunehmender Wärmebehandlung
Viertens sollten bei Bögen, T-Stücken oder Schweißnähten in der Nähe von Ventilen und Zylindergehäusen zusätzlich zu den Raupenheizungen auch Seilheizungen als Zusatzheizung verwendet werden.
Wickeln Sie das Heizseil an der Stelle ein, an der das Heizseil das Werkstück nicht gut berühren kann, wie in Abb. 6 gezeigt.
Abb. 6
Fünftens: Die Wärmebehandlungsparameter für P91-Rohre sind in der beigefügten Tabelle aufgeführt.
Eine angemessene Erhöhung der Konstanttemperaturzeit, der Erwärmungsbreite usw. trägt zur Erhöhung der Zähigkeit der Schweißnaht bei.
Die Verringerung der Schweißhärte darf jedoch nicht zu sehr von der Erhöhung der Konstanttemperaturzeit und der Heizbreite abhängen, da sonst der Grundwerkstoff erweicht wird.
Stattdessen sollten Lösungen für die Genauigkeit der Temperaturkontrolle und die Art der Umhüllung gefunden werden.
Parameter der Wärmebehandlung
Spezifikation mm × mm | Konstante Temperatur Zeit/h | Heizbreite/mm | Breite der Isolierung/mm | Dicke der Isolierung/mm |
φ achtundfünfzigtausendneunundfünfzig × dreiundsiebzig Komma sechs | 8 | 600 | 1200 | 100 |
φ vierhundertvierunddreißig Punkt sieben neun × siebenundfünfzig Punkt sechs | 8 | 570 | 1200 | 100 |
φ neunhundertfünfundachtzig Punkt acht × vierunddreißig Punkt sechs | 5 | 600 | 1200 | 100 |
φ siebenhundertzwei Punkt sieben × sechsundzwanzig Punkt vier | 4 | 400 | 1000 | 100 |
φ fünfhundertdreiundzwanzig Punkt sieben × neunzehn Punkt acht | 4 | 400 | 800 | 100 |
Sechstens: Wärmebehandlungsverfahren
Nach dem Schweißen muss die Temperatur für 60 Minuten auf 110 ℃ gesenkt werden, damit die Martensit vollständig umgewandelt werden kann, und dann ist die Temperatur für die Wärmebehandlung zu erhöhen.
Die Wärmebehandlung nach dem Schweißen erfolgt durch elektrische Ferninfrarot-Erwärmung, und der Wärmebehandlungsprozess ist in Abb. 7 dargestellt.
Abb. 7
(1) Während des Vorwärmens muss das Thermoelement 20 mm von der Kante der Nut entfernt sein. Wenn die Temperatur auf die Vorwärmtemperatur ansteigt, ist die Schweißung mit einer konstanten Temperatur von 30 Minuten zu beginnen.
Die Zwischenlagentemperatur muss während des Schweißens streng kontrolliert werden.
Da die Temperaturmessung der Wärmebehandlungsmaschine im Allgemeinen um etwa 30 ℃ verzögert ist, wird der Übertemperaturalarm auf 260 ℃ eingestellt.
Bei Überschreitung der Temperatur sofort mit dem Schweißen aufhören und mit dem Schweißen beginnen, wenn die Temperatur auf 230 ℃ gesunken ist.
(2) Die Genauigkeit der Temperaturmessung ist der wichtigste Faktor für die Wirkung der Wärmebehandlung.
Thermoelemente und Temperaturschreiber müssen vor ihrer Verwendung von qualifizierten Stellen geeicht werden, und die Verwendungsdauer von Thermoelementen muss aufgezeichnet werden.
Thermoelemente müssen einmal nach einer Verwendungsdauer von mehr als 200 Stunden kalibriert werden.
Da die Zwischenlagentemperatur 200~300 ℃ beträgt, sind die Thermoelementkontrollpunkte 200 ℃, 400 ℃, 600 ℃ und 800 ℃.
(3) Die Polarität des Kompensationsdrahtes muss beim Anschluss an das Thermoelement korrekt sein.
Die beiden Anschlüsse des Kompensationsdrahtes und des Thermoelementes sowie die beiden Anschlüsse der Wärmebehandlungsmaschine sollten jeweils die gleiche Umgebungstemperatur haben, da es sonst leicht zu ungenauen Temperaturmessungen kommen kann.
Die Verbindung zwischen dem Kompensationsdraht und dem Thermoelementdraht muss durch die Verwendung des Verdrahtungssockels zuverlässig sein.
Es ist nicht erlaubt, die beiden Drähte direkt miteinander zu verschrauben. Auf diese Weise wird der Leitungswiderstand die Potenzialdifferenz aufzehren und leicht zu Überhitzung führen.