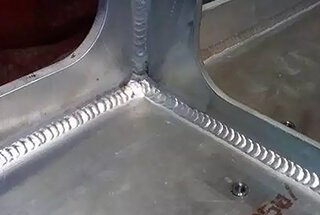
Haben Sie sich jemals gefragt, warum Schweißnähte aus Aluminiumlegierungen trotz sorgfältigen Schweißens reißen? Dieser Artikel befasst sich mit den wichtigsten Problemen wie Porosität, Heißrisse und ungleiche Verbindungsfestigkeit beim Schweißen von Aluminiumlegierungen. Er erklärt die Arten von Rissen, ihre Ursachen und wie hohe Wärmeleitfähigkeit und chemische Aktivität zu diesen Problemen beitragen. Sie erhalten Einblicke in die Mechanismen, die diesen Rissen zugrunde liegen, und entdecken praktische Präventionsstrategien zur Verbesserung Ihrer Schweißergebnisse.
Obwohl Aluminium und seine Legierungen in großem Umfang zum Schweißen wichtiger Produkte verwendet werden, sind sie bei der eigentlichen Schweißproduktion nicht ohne Schwierigkeiten. Zu den wichtigsten Problemen gehören Porosität in der Schweißnaht, Heißrisse beim Schweißen und das Erreichen einer gleichmäßigen Verbindungsfestigkeit.
Einer der Gründe für diese Probleme ist die starke chemische Aktivität von Aluminium und seinen Legierungen, die die Oberfläche sehr anfällig für die Bildung von Oxidschichten macht, die oft feuerfest sind. So liegt beispielsweise der Schmelzpunkt von Al2O3 bei 2050 ℃ und der Schmelzpunkt von MgO bei 2500 ℃. Außerdem haben Aluminium und seine Legierungen eine hohe Wärmeleitfähigkeit, so dass es beim Schweißen leicht zu Nichtschmelzen kommt.
Die Oxidschicht, die eine ähnliche Dichte wie Aluminium hat, kann zu Einschlüssen im Schweißgut führen. Außerdem kann die weniger dichte Oxidschicht mit MgO mehr Wasser absorbieren und ist oft eine wesentliche Ursache für Schweißnahtporosität. Außerdem haben Aluminium und seine Legierungen einen großen linearen Ausdehnungskoeffizienten und eine hohe Wärmeleitfähigkeit, was sie anfällig für Verformungen beim Schweißen macht.
Schließlich analysiert der Artikel die relativ schwerwiegenden Risse, die bei der Prüfung auftreten.
Beim Schweißen von Aluminiumlegierungen können verschiedene Risse in der Schweißnaht auftreten. Schweißnähte aufgrund von Unterschieden in den Arten, Eigenschaften und Schweißstrukturen der Materialien.
Die Form und Verteilung dieser Risse kann recht komplex sein.
Je nach ihrer Lage lassen sich diese Risse in zwei Typen unterteilen:
(1) Risse im Schweißgut: Längsrisse, Querrisse, Kraterrisse, Haarrisse oder Lichtbogenrisse, Wurzelrisse und Mikrorisse (insbesondere beim Mehrlagenschweißen).
(2) Risse in der Wärmeeinflusszone: Risse an der Schweißnahtspitze, lamellare Risse und thermische Mikrorisse in der Nähe der Schmelzlinie.
Risse, die beim Schweißen entstehen, lassen sich in Heißrisse und kalte RisseDie Temperaturbereiche, in denen sie auftreten, sind entscheidend.
Heißrisse entstehen bei hohen Temperaturen während des Schweißens und werden hauptsächlich durch die Entmischung von Legierungselemente an der Korngrenze oder das Vorhandensein von Materialien mit niedrigem Schmelzpunkt.
Die Form, der Temperaturbereich und die Hauptursachen für heiße Risse variieren je nach den Materialien des geschweißten Metalls.
Die heißen Risse lassen sich in drei Typen unterteilen: Kristallisationsrisse, Verflüssigungsrisse und Polygonisationsrisse.
Kristallisationsrisse entstehen hauptsächlich während der Schweißverfahren bei hohen Temperaturen. In der Nähe des Solidus schrumpft das erstarrte Metall, was zu einer unzureichenden Restmenge an flüssigem Metall führt, die sich nicht rechtzeitig auffüllen kann, was zur Bildung von Rissen führt.
Interkristalline Risse entstehen durch Schrumpfungsspannungen bei der Erstarrung oder durch äußere Krafteinwirkung, hauptsächlich bei Kohlenstoffstahl, Schweißnähten aus niedrig legiertem Stahl und einigen Aluminiumlegierungen mit mehr Verunreinigungen.
Verflüssigungsrisse entstehen durch die Schwindungsspannungen während der Erstarrung von auf hohe Temperaturen erhitzten Korngrenzen in der Wärmeeinflusszone.
Bei den Tests wurde festgestellt, dass eine unzureichende Reinigung der Oberfläche des Schweißzusatzwerkstoffs dazu führte, dass nach dem Schweißen Einschlüsse und Poren in der Schweißnaht vorhanden waren. Da es sich bei dem Schweißzusatzwerkstoff um eine Gussstruktur handelt und der Einschluss ein Material mit hohem Schmelzpunkt ist, verbleibt er nach dem Schweißen in der Schweißnaht.
Das Gussgefüge ist relativ dünn und weist viele Löcher auf, so dass es leicht Komponenten mit Kristallwasser und Ölqualität aufnehmen kann. Diese Faktoren können beim Schweißen zu Porosität führen, und Einschlüsse und Poren werden zu Schlüsselkomponenten, die Mikrorisse verursachen, wenn die Schweißnaht unter Zugspannung steht.
Weitere mikroskopische Untersuchungen ergaben eine Wechselwirkung zwischen diesen Einschlüssen und den durch Poren verursachten Mikrorissen. Es ist jedoch schwierig festzustellen, ob die Einschlüsse hauptsächlich als Quelle der Spannungskonzentration zur Rissbildung oder als spröde Phase zur Rissbildung dienen.
Außerdem wird allgemein angenommen, dass Porosität in Schweißnähten aus Aluminium-Magnesium-Legierungen die Zugfestigkeit der Schweißnaht nicht wesentlich beeinträchtigt. In dieser Studie wurden jedoch durch Einschlüsse und Porosität verursachte Mikrorisse in den Zugproben der Schweißnähte gleichzeitig festgestellt.
Die Frage, ob durch Poren verursachte Mikrorisse ein sekundäres Phänomen oder einer der Hauptfaktoren sind, die einen erheblichen Rückgang der Zugfestigkeit von Schweißnähten verursachen, muss weiter untersucht werden.
Gegenwärtig gilt die von Prokhorov vorgeschlagene Theorie des Schweißens heißer Risse sowohl im Inland als auch international als sehr ausgereift.
Zusammenfassend lässt sich sagen, dass die Theorie besagt, dass die Entstehung von Kristallrissen hauptsächlich von den folgenden drei Faktoren abhängt:
Die Größe des spröden Temperaturbereichs und der Duktilitätswert innerhalb dieses Bereichs werden gemeinhin als metallurgische Faktoren bezeichnet, die zu Heißrissen beim Schweißen führen können, während die Verformungsgeschwindigkeit des Metalls innerhalb des spröden Temperaturbereichs als mechanischer Faktor bezeichnet wird.
Der Schweißprozess beinhaltet eine Reihe von unausgewogenen technologischen Verfahren. Dieses Merkmal steht in engem Zusammenhang mit den metallurgischen und mechanischen Faktoren des Metallbruchs in Schweißverbindungen, wie z. B. physikalische, chemische und organisatorische Heterogenität, Schlacke und Einschlüsse, Gaselemente und Hohlräume mit übersättigten Konzentrationen der Produkte der schweißtechnischen und metallurgischen Prozesse.
All diese Faktoren sind eng mit der Entstehung und Entwicklung von Rissen in der Metallurgie verbunden.
Was die mechanischen Faktoren betrifft, so sind der spezifische Temperaturgradient und die Abkühlungsgeschwindigkeit der Schweiß-Wärme-Zyklus kann dazu führen, dass sich die Schweißverbindung unter bestimmten Zwangsbedingungen in einem komplexen Spannungs-Dehnungs-Zustand befindet, der die notwendigen Voraussetzungen für die Entstehung und Entwicklung von Rissen bietet.
Während des Schweißvorgangs kann die kombinierte Wirkung von metallurgischen und mechanischen Faktoren die Metallverbindung auf zwei Arten verstärken oder schwächen.
Wenn während des Abkühlens eine feste Verbindung im Schweißnahtmetall hergestellt wird, kann die Dehnung unter bestimmten starren Zwangsbedingungen gehorsam bleiben. Wenn die Schweißnaht und das Metall in der Nähe der Naht einer äußeren Zwangsspannung und einer inneren Zwangsspannung standhalten können EigenspannungDas Auftreten von Rissen ist weniger wahrscheinlich, und die Rissempfindlichkeit des Metalls ist gering.
Kann die Spannung hingegen nicht ausgehalten werden, ist die Wahrscheinlichkeit größer, dass die Festigkeitsverbindung im Metall unterbrochen wird, was zu Rissen führt. In diesem Fall ist die Rissempfindlichkeit des Schweißnahtmetalls hoch.
Das Schweißnahtmetall wird mit einer bestimmten Geschwindigkeit von der Kristallisationserstarrungstemperatur auf Raumtemperatur abgekühlt. Die Rissempfindlichkeit hängt vom Vergleich des Verformungsvermögens und der aufgebrachten Dehnung sowie vom Vergleich des Verformungswiderstands und der aufgebrachten Spannung ab.
Während des Abkühlungsprozesses können jedoch unterschiedliche Temperaturstufen zu unterschiedlicher intergranularer Festigkeit und Kornfestigkeitswachstum, unterschiedlicher Verformungsverteilung zwischen und innerhalb der Körner, unterschiedlichem Diffusionsverhalten durch Dehnung, unterschiedlichen Spannungskonzentrationsbedingungen und Faktoren, die zu Metallversprödung führen, führen. Dies kann zu unterschiedlichen spezifischen Schwachstellen in Schweißverbindungen führen, und auch der Grad der Schwächung kann variieren.
Das Auftreten von Rissen im Schweißnahtmetall hängt sowohl mit metallurgischen als auch mit mechanischen Faktoren eng zusammen.
Das Spannungsgefälle bei den mechanischen Faktoren hängt mit dem Temperaturgefälle zusammen, das durch die thermischen Zykluseigenschaften bestimmt wird. Die Wärmeleitfähigkeit des Metalls bestimmt die thermischen Zykluseigenschaften, die als metallurgische Faktoren betrachtet werden. Dazu gehören die thermoplastischen Veränderungseigenschaften des Metalls, die thermische Ausdehnung und die strukturelle Umwandlung.
Der Spannungs-Dehnungs-Zustand des geschweißten Metalls wird sowohl von metallurgischen als auch von mechanischen Faktoren stark beeinflusst. Außerdem ändern sich diese Faktoren mit sinkender Temperatur und Abkühlgeschwindigkeit.
Unterschiedliche Temperaturbereiche beeinflussen die Festigkeit der Schweißnaht Metall unterschiedlich. So führen beispielsweise der große Kristallisationstemperaturbereich und die niedrige Solidustemperatur wahrscheinlich zu einer Spannungskonzentration im verbleibenden niedrig schmelzenden flüssigen Metall zwischen den Körnern, was zu Rissen im festen Metall führt. Wenn die Schrumpfung groß ist, vor allem unter der Bedingung einer schnellen Abkühlung, ist die Wahrscheinlichkeit groß, dass Risse auftreten, wenn die Schrumpfungsdehnungsrate hoch und der Spannungs-Dehnungs-Zustand rau ist.
In der späteren Phase der Erstarrung und Kristallisation des Schweißguts bei Aluminium LegierungsschweißenDas Eutektikum wird in der Mitte der Kristallüberschneidung zusammengepresst und bildet einen "Flüssigkeitsfilm". An diesem Punkt ist aufgrund der großen Schrumpfung während der Abkühlung keine freie Schrumpfung verfügbar, um große Zugspannungen zu erzeugen. Infolgedessen bildet der Flüssigkeitsfilm eine schwache Verbindung, die in der schwachen Zone unter der Wirkung von Zugspannung reißen kann.
Um das Auftreten von Heißrissen beim Schweißen von Aluminiumlegierungen zu untersuchen, wird der Kristallisationsprozess des Schweißbades in drei Stufen unterteilt.
Die erste Phase ist die Flüssig-Fest-Phase, in der eine kleine Anzahl von Kristallkeimen existiert, wenn die Schweißschmelze von hoher Temperatur abkühlt. Mit sinkender Temperatur und längerer Abkühlzeit wachsen die Kristallkeime allmählich und es entstehen neue.
Allerdings überwiegt noch die flüssige Phase, und es gibt keinen Kontakt zwischen benachbarten Körnern, so dass die flüssige, noch nicht erstarrte Aluminiumlegierung frei fließen kann. Daher können selbst bei Zugbeanspruchung alle geöffneten Lücken sofort durch das fließende Flüssigmetall gefüllt werden, wodurch die Wahrscheinlichkeit von Rissen in diesem Stadium sehr gering ist.
Die zweite Phase ist die Fest-Flüssig-Phase. Hier nimmt die feste Phase in der Schmelze mit fortschreitender Kristallisation weiter zu, und die zuvor gebildeten Kristallisationskeime wachsen weiter.
Wenn die Temperatur auf einen bestimmten Punkt sinkt, kommen die erstarrten Metallkristalle der Aluminiumlegierung miteinander in Kontakt und rollen kontinuierlich zusammen. In diesem Stadium ist der Fluss der flüssigen Aluminiumlegierung blockiert, und die Schmelzbadkristallisation tritt in die fest-flüssig Phase ein.
Aufgrund der geringen Menge an flüssigem Aluminiumlegierungsmetall kann die Verformung des Kristalls selbst in diesem Stadium stark ausgeprägt sein, und die verbleibende flüssige Phase zwischen den Kristallen ist nicht leicht zu fließen.
Die winzigen Lücken, die unter Zugspannung entstehen, können nicht gefüllt werden, und schon eine geringe Zugspannung kann zu Rissen führen. Dieses Stadium wird als "spröde Temperaturzone" bezeichnet.
Die dritte Phase ist die Phase der vollständigen Erstarrung. Wenn die Schweißnaht, die nach der vollständigen Erstarrung des geschmolzenen Badmetalls entsteht, einer Zugspannung ausgesetzt wird, weist sie eine gute Festigkeit und Plastizität auf, und die Wahrscheinlichkeit einer Rissbildung in diesem Stadium ist relativ gering.
Wenn also die Temperatur höher oder niedriger ist als die spröde Temperaturzone zwischen a-b, hat das Schweißgut eine größere Widerstandsfähigkeit gegen Kristallrisse und eine geringere Rissneigung. Im Allgemeinen gilt für Metalle mit weniger Verunreinigungen (einschließlich Grundwerkstoff und Schweißmaterialien), ist der Temperaturbereich für die Sprödigkeit eng.
Die Zugspannung wirkt in diesem Bereich nur für kurze Zeit, so dass die Gesamtspannung der Schweißnaht relativ gering ist, was zu einer geringeren Neigung zur Rissbildung beim Schweißen führt.
Wenn jedoch viele Verunreinigungen in der Schweißnaht vorhanden sind, ist der spröde Temperaturbereich relativ groß und die Einwirkungszeit der Zugspannung in diesem Bereich relativ lang, was zu einer größeren Neigung zur Rissbildung führt.
Um die Wahrscheinlichkeit von Heißrissen beim Schweißen von Aluminiumlegierungen zu verringern, können Verbesserungen durch zwei Aspekte erzielt werden: metallurgische Faktoren und technologische Faktoren.
Was die metallurgischen Faktoren anbelangt, so müssen zur Vermeidung interkristalliner Heißrisse beim Schweißen das Legierungssystem der Schweißnaht angepasst oder dem Schweißzusatzstoff Modifikatoren zugesetzt werden.
Um eine angemessene Menge an schmelzbarem Eutektikum zu kontrollieren und den Kristallisationstemperaturbereich unter dem Gesichtspunkt der Rissbeständigkeit einzugrenzen, muss der Schwerpunkt des Schweißlegierungssystems angepasst werden.
Da die Aluminiumlegierung eine typische eutektische Legierung ist, entspricht der "maximale" Erstarrungstemperaturbereich der Legierung der maximalen Rissneigung.
Das Vorhandensein einer geringen Menge an schmelzbarem Eutektikum erhöht immer die Erstarrungsrissneigung. Um dem entgegenzuwirken, wird der Gehalt an Hauptlegierungselementen in der Regel über die Legierungskomponente mit der maximalen Rissneigung hinaus erhöht, um einen "Heilungseffekt" zu erzielen.
Zusätzlich werden dem Zusatzwerkstoff Spurenelemente wie Ti, Zr, V und B als Modifikatoren zugesetzt, um die Plastizität und Zähigkeit durch Verfeinerung der Körner zu verbessern und Heißrisse beim Schweißen zu verhindern. Dieser Versuch wird schon seit einiger Zeit unternommen und hat zu positiven Ergebnissen geführt.
Abbildung 3 zeigt die Ergebnisse der Rissbeständigkeitsprüfung von Al-4.5% Mg-Schweißdraht mit einem Modifikator unter den Bedingungen einer starren Überlappung. Kehlnaht. Der Test umfasste den Zusatz von 0,15% Zr und 0,1% Ti+B. Die Ergebnisse zeigen, dass die gleichzeitige Zugabe von Ti und B die Rissbeständigkeit deutlich verbessert.
Ti, Zr, V, B und Ta haben gemeinsam, dass sie mit Aluminium zu einer Reihe von peritektischen Reaktionen reagieren können, die zur Bildung von Refraktärmetallverbindungen wie Al3Ti, Al3Zr, Al7V, AlB2, Al3Ta usw. führen.
Diese kleinen feuerfesten Partikel können während des Erstarrungsprozesses von Flüssigmetall als nicht spontan erstarrende Kristallkeime wirken und so die Kornfeinung erleichtern.
Prozessfaktoren wie Schweißspezifikationen, Vorwärmung, Fugenform und Schweißfolge sind entscheidend für die Lösung von Schweißrissen, die auf Schweißspannungen beruhen. Die Parameter des Schweißprozesses wirken sich auf das Ungleichgewicht des Erstarrungsprozesses und den Zustand des Erstarrungsgefüges sowie auf die Geschwindigkeit des Dehnungswachstums während der Erstarrung aus und beeinflussen damit die Rissbildung.
Schweissverfahren die mit konzentrierter Wärmeenergie arbeiten, erleichtern das schnelle Schweißen und können die Bildung grober säulenförmiger Kristalle mit starker Richtwirkung verhindern, wodurch die Rissfestigkeit verbessert wird.
Verringerung der Schweißgeschwindigkeit und die Verwendung eines geringen Schweißstroms können die Überhitzung des Schmelzbades verringern und die Rissbeständigkeit verbessern. Eine Erhöhung der Schweißgeschwindigkeit erhöht jedoch die Dehnungsrate der Schweißnähte und die Neigung zur Heißrissbildung. Es ist daher offensichtlich, dass eine Erhöhung der Schweißgeschwindigkeit und des Schweißstroms die Rissneigung erhöht.
Während der Montage und Schweißen von Aluminium Strukturen weist die Schweißnaht keine große Steifigkeit auf. Daher können Maßnahmen wie das Schweißen in Abschnitten, Vorwärmen oder die Reduzierung der Schweißgeschwindigkeit ergriffen werden.
Durch das Vorwärmen kann die relative Ausdehnung der Probe und damit die Schweißspannung verringert werden, was die Spannung im spröden Temperaturbereich reduziert. Stumpfschweißen mit Fuge und kleinen Spalten sollten so weit wie möglich verwendet werden, während Kreuzstöße und falsche Positionierung und Schweißfolgen vermieden werden sollten. Nach Beendigung oder Unterbrechung des Schweißens sollte der Krater sofort aufgefüllt und die Wärmequelle entfernt werden, da sonst leicht Kraterrisse entstehen können.
Beim Schweißen von mehrlagigen Schweißverbindungen aus 5000er-Legierungen entstehen häufig Mikrorisse durch lokales interkristallines Aufschmelzen, was eine Kontrolle der Schweißwärme Eingabe der nächsten Schweißraupenlage.
Nach den Erkenntnissen dieser Arbeit ist die Reinigung der Oberfläche des Grund- und Zusatzwerkstoffs beim Schweißen von Aluminiumlegierungen von entscheidender Bedeutung. Materialeinschlüsse werden zur Quelle von Rissen in der Schweißnaht und sind der Hauptgrund für den Rückgang der Schweißleistung.