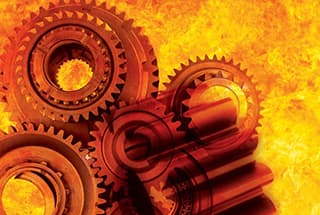
Warum versagen manche Zahnräder trotz präziser Fertigung? Dieser Artikel befasst sich mit den häufigsten Defekten bei der Aufkohlung von Zahnrädern und geht auf Probleme wie Überkohlung, flache Härtung und ungleichmäßige Einsatzhärtung ein. Sie erfahren etwas über die Ursachen dieser Probleme und über wirksame Präventivmaßnahmen, die eine optimale Leistung und Langlebigkeit der Zahnräder gewährleisten. Das Verständnis dieser Fehler und ihrer Lösungen wird Ihnen helfen, die Haltbarkeit und Zuverlässigkeit von Zahnrädern in verschiedenen Anwendungen zu verbessern.
Eine unsachgemäße Behandlung von aufgekohlten Zahnrädern kann zu einer übermäßigen Oberflächenaufkohlung führen, die blockige und netzartige Karbide auf der Oberfläche bildet.
Dies verringert die Fähigkeit des Zahnrads, sich während des Gebrauchs plastisch zu verformen, schwächt seine Stoßfestigkeit, vermindert die Biegeermüdungsleistung am Zahnfuß, macht den Zahnkopf spröde und anfällig für Ausbrüche.
Nach dem Abschrecken sind aufgekohlte Zahnräder anfällig für Rissbildung bei Schleifvorgängen.
(1) Wenn Zahnräder in festen Medien aufgekohlt werden, ist das Kohlenstoffpotential im Aufkohlungsbehälter zu hoch und kann nicht beliebig eingestellt werden.
Je höher die Aufkohlungstemperatur und je länger die Zeit, desto größer ist daher der Grad der Überkohlung der Oberfläche.
Insbesondere bei Aufkohlungsstählen, die starke karbidbildende Elemente wie Cr und Mo enthalten, ist die Kohlenstoffdiffusion langsamer, was zu einer höheren Kohlenstoffkonzentration an der Oberfläche der aufgekohlten Zahnradschicht führt.
Dadurch entsteht eine überkohlte Schicht, die beim Abkühlen eine netzartige Verteilung durch die Ausscheidung von aufgekohlten Körpern aus der Austenit Korngrenzen.
(2) Bei der Aufkohlung in einem gasförmigen Medium kann es zu einer Überkohlung der Zahnradoberfläche kommen, wenn das Kohlenstoffpotenzial im Aufkohlungsofen zu hoch ist und die Aufkohlungszeit zu lang ist.
(1) Bei der Feststoffaufkohlung ist eine niedrigere Aufkohlungstemperatur oder ein schwächeres Aufkohlungsmittel zu verwenden, um eine übermäßige Aufkohlung aufgrund eines hohen Kohlenstoffpotenzials zu vermeiden.
(2) Während GasaufkohlungUm eine übermäßige Aufkohlung der Oberfläche zu vermeiden, ist nach dem Aufkohlen eine Diffusionsphase vorzusehen. Die Dauer der intensiven Aufkohlungs- und Diffusionsphasen sollte entsprechend dem Wärmebehandlungsverfahren festgelegt werden.
(3) Für Zahnräder mit übermäßiger Oberflächenaufkohlung, diffundieren Sie sie in einem kohlenstoffarmen potentiellen Aufkohlungsofen, oder schrecken Sie sie nach der Karbid-Sphäroidisierung ab. Glühen Behandlung.
Die Oberflächenhärte von aufgekohlten Zahnrädern ist gering, was nicht nur zu einer Verringerung der Beständigkeit der gehärteten Oberflächenschicht gegen Abblättern führt, sondern auch zu einer Verkürzung der Lebensdauer.
(1) Während des Aufkohlungsprozesses ist die Aufkohlungszeit zu kurz, die Aufkohlungstemperatur ist zu niedrig und die Aufkohlungsschicht ist flach.
Die ungleichmäßige Verteilung der effektiven Heizzonentemperatur im Ofen, die unsachgemäße Steuerung des Kohlenstoffpotenzials während der starken Aufkohlungs- und Diffusionsphasen, die fehlende Reinigung der Ölflecken auf den Zahnrädern vor dem Einlegen in den Ofen und das übermäßige Beschickungsvolumen, das zu kleine Lücken hinterlässt, tragen alle zur flachen Härteschicht der aufgekohlten Zahnräder bei.
(2) Der gewählte Getriebestahl und die schlechte Härtbarkeit, gepaart mit unzureichender Kühlleistung der Abschreckungsmediumführen nach einer normalen Aufkohlungsabschreckung zu einer flachen Härteschicht.
(1) Auswahl von Stahl mit geeigneter Härtbarkeit als Material für aufgekohlte Zahnräder, strenge Qualitätskontrolle des Zahnradstahls und Durchführung von Qualitätskontrollen des Stahls, bevor er das Werk verlässt.
(2) Strenge Kontrolle der Oberflächenqualität der Zahnräder vor der Aufkohlung, das Ladevolumen im Ofen, die Temperatur im Ofen, die Kohlenstoffpotentialatmosphäre im Ofen, die Zeit der intensiven Aufkohlung und Diffusion, die Abschrecktemperatur nach der Aufkohlung, die Kühlmedium, usw.
(3) Zahnräder mit unzureichender Aufkohlung sollten einer zusätzlichen Aufkohlung unterzogen werden.
Die ungleichmäßige Tiefe der einsatzgehärteten Schicht auf der Oberfläche des Zahnrads führt zu einer ungleichmäßigen Leistung in verschiedenen Bereichen. Sie verursacht erste Schäden in schwächeren Zonen, die dann zum Gesamtversagen des Zahnrads führen und seine Lebensdauer stark beeinträchtigen.
(1) Bei der Feststoffaufkohlung bestehen erhebliche Temperaturunterschiede innerhalb des Aufkohlungsbehälters, und die ungleichmäßige Verteilung des Aufkohlungsmittels führt zu großen Unterschieden in der Aufkohlungstiefe.
Darüber hinaus beeinflussen die Größe des Aufkohlungsbehälters, das Ladevolumen, die Beladungsmethode, die Heizrate und die geringe Wärmeleitfähigkeit der Kohle des Aufkohlungsmittels die Tiefe der aufgekohlten Schicht.
(2) Während der Gasaufkohlung können ungleichmäßige Ofentemperaturen und eine schlechte Zirkulation der Ofenatmosphäre, ungereinigte Ölflecken auf dem Zahnrad vor der Beladung und Rußablagerungen auf der Zahnradoberfläche zu einer ungleichmäßigen Aufkohlungsschichttiefe beitragen.
(1) Bei Zahnrädern, die in Massenproduktion hergestellt werden, sollte die Feststoffaufkohlung so weit wie möglich vermieden werden. Wenn eine Feststoffaufkohlung durchgeführt werden muss, ist die strikte Einhaltung der Betriebsverfahren erforderlich: angemessene Füllmengen und gründliches Mischen von Aufkohlungsmittel und Kohle.
Der Aufkohlungskasten sollte in der Mitte des Ofens platziert werden, wo die Temperatur gleichmäßig ist, und die Position des Kastens sollte während des Aufkohlungsvorgangs entsprechend angepasst werden.
(2) Bei der Gasaufkohlung ist auf eine ausreichende Zirkulation der Ofenatmosphäre, eine gleichmäßige Ofentemperatur, die Entfernung von Ölflecken auf der Zahnradoberfläche und ein angemessenes Beladungsvolumen zu achten.
Der Aufkohlungsofen sollte gut abgedichtet sein, undichte Muffelbehälter sollten umgehend ausgetauscht werden, und eine regelmäßige Wartung des Aufkohlungsofens ist notwendig.
Die geringere Oberflächenhärte von aufgekohlten Zahnrädern kann zu einer geringeren Verschleiß- und Ermüdungsfestigkeit führen, was sich negativ auf die Reibungs- und Verschleißfestigkeitseigenschaften des Zahnrads auswirkt.
(1) Oberfläche Entkohlungmit einer bei der metallografischen Untersuchung festgestellten Entkohlungsschicht ist das Ergebnis eines unzureichenden Schutzes während des Glühens oder Abschreckens nach der Aufkohlung.
(2) Die langsame Abkühlungsgeschwindigkeit zeigt sich bei der mikroskopischen Untersuchung, bei der die Oberflächenstruktur Sorbit ist, nicht Martensit.
Bei der metallografischen Betrachtung ist der nadelförmige Martensit eindeutig korrosionsbeständig, während der Sorbit dunkler erscheint (anfälliger für Korrosion). Ein signifikanter Unterschied ergibt sich bei der Prüfung der Härte mit einem Mikrohärteprüfgerät.
(3) Übermäßige Mengen an Reststoffen Austenit auf der Oberfläche nach dem Abschrecken sind auf eine zu hohe Aufkohlungstemperatur der Zahnräder und eine zu hohe Abschreckungstemperatur zurückzuführen.
(4) Schlechte Härtbarkeit des Getriebematerial und unzureichende Kühlleistung des Abschreckmediums.
(5) Hohe Anlasstemperatur nach dem Abschrecken und zu lange Dauer der Isolierung.
1. Für Zahnräder mit geringer Oberfläche Kohlenstoffgehalteine geeignete Aufkohlungsbehandlung durchführen.
2. Wählen Sie Werkstoffe mit geeigneter Härtbarkeit und Kühlmedien mit entsprechenden Kühlmöglichkeiten für das Abschrecken.
3. Ergreifen Sie vorbereitende Maßnahmen, um das Restaustenitvolumen nach dem Abschrecken zu reduzieren.
Bei aufgekohlten Zahnrädern mit übermäßigem Restaustenit sollte ein Hochtemperaturanlassen bei 650-670°C über 3 Stunden durchgeführt werden, um eine teilweise Ausscheidung von Legierungskarbiden zu ermöglichen, wodurch die Stabilität des Austenits beim Wiedererwärmungshärten verringert und die Umwandlung von Austenit in Martensit gefördert wird.
4. Das Aufkohlen und Wiedererwärmungshärten von Zahnrädern sollte unter Schutzatmosphäre durchgeführt werden.
Bei Zahnrädern, die eine Oxidation aufweisen, sollten die Oxidschichten entfernt und die Oberfläche vor dem Abschrecken aufgekohlt werden.
5. Wenn die Oberflächenhärte des Zahnrads aufgrund zu hoher Anlasstemperaturen zu niedrig ist, muss das Zahnrad erneut gehärtet werden, wobei eine geeignete Temperatur für das Anlassen zu wählen ist.
Der Kern des aufgekohlten Zahnrads erfordert einen bestimmten Härtegrad. Ist die Härte zu niedrig, sinkt die Streckgrenze des Zahnradmaterials, was zu einer plastischen Verformung des Kerns führen kann.
Dies wiederum verringert die Widerstandsfähigkeit der oberflächengehärteten Schicht gegen Abplatzungen und schwächt die Biegeermüdungsleistung am Zahnfuß.
(1) Schlechte Härtbarkeit des Zahnradmaterials, minderwertige Zahnradqualität und starke Bandstruktur im Stahl.
(2) Vor dem direkten Abschrecken nach der Aufkohlung ist die Vorkühltemperatur zu niedrig, oder die Abschrecktemperatur ist während des erneuten Abschreckens nach der Aufkohlung nicht ausreichend.
(3) Die Abkühlgeschwindigkeit ist nicht ausreichend. Die metallografische Untersuchung zeigt, dass es sich nicht um kohlenstoffarmen Martensit, sondern um Sorbit handelt.
(4) Es gibt eine Fülle von ungelöst Ferrit im Kern, das durch eine zu niedrige Heiztemperatur oder eine unzureichende Heizdauer verursacht wird.
(1) Verwendung eines Kühlmediums mit hervorragenden Kühleigenschaften zum Abschrecken, um eine kohlenstoffarme martensitisches Gefüge im Kern.
(2) Wählen Sie die geeignete Abschrecktemperatur und Erwärmungsdauer, um eine gleichmäßige austenitische Struktur im Kern zu erhalten, die die Bildung einer martensitischen Struktur nach dem Abschrecken ermöglicht.
(3) Wählen Sie Stahl mit guter Härtbarkeit und Qualität als Material für das Aufkohlen von Zahnrädern.