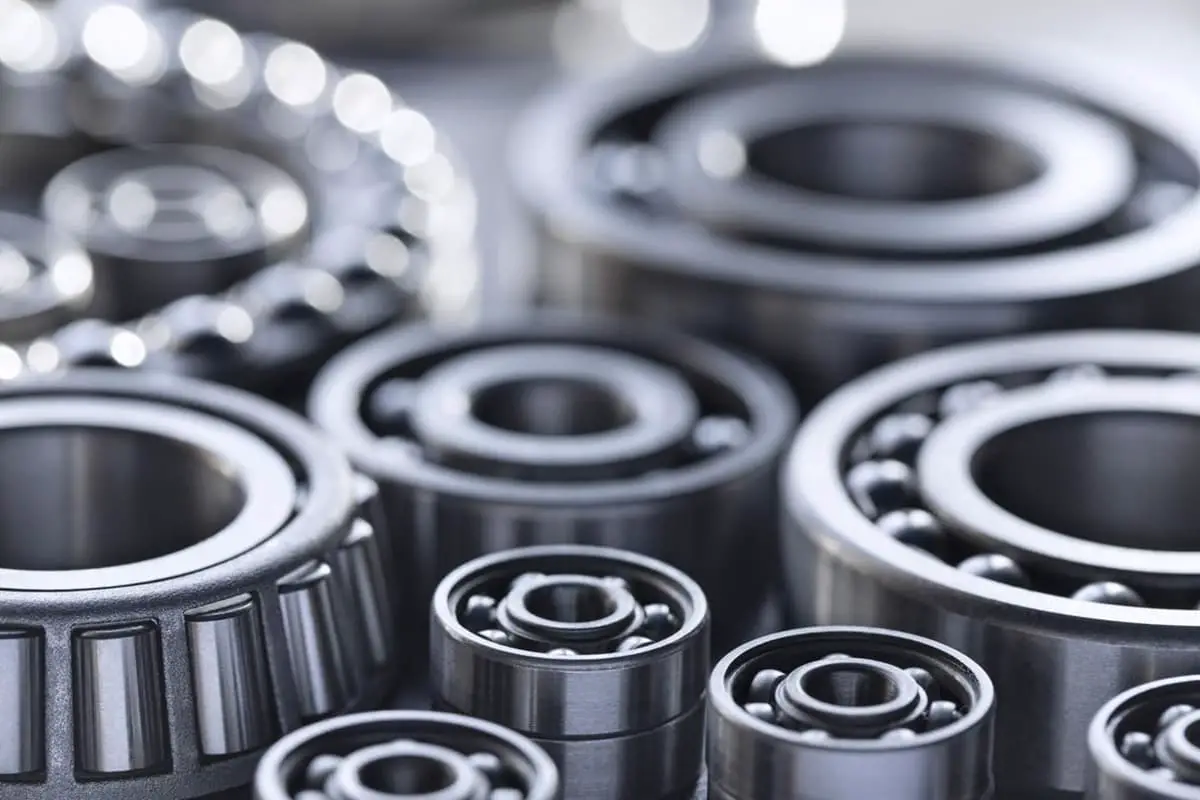
Haben Sie sich jemals gefragt, warum Ihre CNC-gefertigten Teile nicht perfekt werden? Dieser Artikel befasst sich mit neun häufigen CNC-Bearbeitungsfehlern, von Werkzeugverschleiß bis hin zu thermischer Verformung, und bietet praktische Tipps, um sie zu vermeiden. Wenn Sie diese Fehler verstehen, können Sie Ihre Bearbeitungsgenauigkeit verbessern und sowohl Zeit als auch Ressourcen sparen. Tauchen Sie ein und entdecken Sie, wie kleine Anpassungen jedes Mal zu makellosen Teilen führen können.
Unter Bearbeitungsfehler versteht man die Abweichung zwischen den tatsächlichen geometrischen Parametern (Abmessungen, Form und gegenseitige Lage) und den idealen geometrischen Parametern. Die Bearbeitungsgenauigkeit wird durch den Grad der Übereinstimmung zwischen den tatsächlichen und den idealen geometrischen Parametern bestimmt.
Je kleiner der Bearbeitungsfehler ist, desto höher ist der Grad der Übereinstimmung und der Bearbeitungsgenauigkeit. Sowohl der Bearbeitungsfehler als auch die Bearbeitungsgenauigkeit werden zur Messung desselben Sachverhalts verwendet. Daher gibt die Größe des Bearbeitungsfehlers das Niveau der Bearbeitungsgenauigkeit an.
Zu den wichtigsten Herstellungsfehlern bei Werkzeugmaschinen gehören Fehler in der Spindelrotation, der Führungsschiene und der Übertragungskette.
Der Spindelrotationsfehler bezieht sich auf die Abweichung der tatsächlichen Spindelachse zu einem bestimmten Zeitpunkt von ihrer durchschnittlichen Achse, was sich direkt auf die Genauigkeit des bearbeiteten Werkstücks auswirkt.
Zu den Ursachen für Spindeldrehfehler gehören Koaxialitätsfehler der Spindel, Lagerfehler, Koaxialitätsfehler zwischen den Lagern und die Spindelwicklung.
Die Führungsschiene dient als Referenz für die Bestimmung der relativen Positionen von Werkzeugmaschinenkomponenten und führt auch die Bewegung der Werkzeugmaschine. Führungsschienenfehler können durch Fertigungsfehler in der Führungsschiene, ungleichmäßige Abnutzung und schlechte Montagequalität verursacht werden.
Der Fehler der Übertragungskette bezieht sich auf die relativen Bewegungsfehler zwischen den Übertragungselementen an beiden Enden der Kette und wird durch Herstellungs- und Montagefehler in den einzelnen Gliedern sowie durch Verschleiß während des Gebrauchs verursacht.
Bei jedem Zerspanungsprozess führt der Verschleiß des Werkzeugs zu Veränderungen der Größe und Form des Werkstücks. Die Auswirkungen der geometrischen Fehler des Werkzeugs auf die Bearbeitungsfehler sind je nach Werkzeugtyp unterschiedlich. Bei Werkzeugen mit fester Größe wirken sich die Fertigungsfehler direkt auf die Bearbeitungsgenauigkeit des Werkstücks aus. Bei allgemeinen Werkzeugen (wie z. B. Drehwerkzeugen) wirken sich die Fertigungsfehler dagegen nicht direkt auf die Bearbeitungsfehler aus.
Der Zweck einer Vorrichtung ist es, sicherzustellen, dass das Werkstück im Verhältnis zum Fräser und zur Werkzeugmaschine richtig positioniert ist. Folglich haben die geometrischen Fehler in der Aufspannung einen erheblichen Einfluss auf die Bearbeitungsfehler, insbesondere auf die Positionsfehler.
Der Positionierungsfehler setzt sich in erster Linie aus Ungenauigkeiten des Bezugspunktes und Fertigungsungenauigkeiten des Positionspaares zusammen.
Bei der Bearbeitung des Werkstücks auf der Werkzeugmaschine müssen bestimmte geometrische Elemente des Werkstücks als Bezugspunkt gewählt werden. Wenn der gewählte Referenznullpunkt nicht mit dem Konstruktionsnullpunkt übereinstimmt (der Nullpunkt, der verwendet wird, um die Größe und Position einer bestimmten Fläche in der Werkstückzeichnung zu bestimmen), tritt ein Nichtübereinstimmungsfehler des Nullpunkts auf.
Die Positionierfläche des Werkstücks und die Positionierelemente der Spannvorrichtung bilden das Positionierpaar. Die maximale Positionsabweichung des Werkstücks, die durch Ungenauigkeiten bei der Herstellung des Positionierpaares und den Passungsspalt zwischen den Positionierpaaren verursacht wird, wird als Herstellungsungenauigkeit des Positionierpaares bezeichnet.
Die Ungenauigkeiten im Positionspaar können nur bei der Justiermethode auftreten, nicht beim Probeschneiden.
Steifigkeit des Werkstücks
Wenn in einem Bearbeitungssystem das Werkstück im Vergleich zur Werkzeugmaschine, zum Werkzeug und zur Vorrichtung eine geringere Steifigkeit aufweist, hat die Verformung aufgrund der unzureichenden Steifigkeit des Werkstücks unter dem Einfluss der Schnittkräfte einen erheblichen Einfluss auf die Bearbeitungsfehler.
Steifigkeit des Werkzeugs
Die Steifigkeit eines zylindrischen Drehwerkzeug in der Normalenrichtung (y) der bearbeiteten Oberfläche ist sehr hoch, und seine Verformung kann vernachlässigt werden. Beim Bohren einer Innenbohrung mit kleinerem Durchmesser hat der Mähbalken jedoch eine geringe Steifigkeit und die kraftbedingte Verformung des Mähbalkens beeinträchtigt die Bearbeitungsgenauigkeit der Bohrung erheblich.
Steifigkeit von Werkzeugmaschinenkomponenten
Werkzeugmaschinenteile setzen sich aus vielen Komponenten zusammen, und derzeit gibt es keine einfache Berechnungsmethode zur Bestimmung ihrer Steifigkeit. Die Steifigkeit von Werkzeugmaschinenteilen wird in erster Linie durch Experimente ermittelt. Zu den Faktoren, die sich auf die Steifigkeit von Werkzeugmaschinenteilen auswirken, gehören die Verformung der Verbindungsflächen während des Kontakts, die Reibungskraft, Komponenten mit geringer Steifigkeit und das Spiel.
Thermische Verformungen im Bearbeitungssystem haben einen erheblichen Einfluss auf Bearbeitungsfehler, insbesondere bei der Präzisionsbearbeitung und der Bearbeitung großer Werkstücke. In einigen Fällen können die durch thermische Verformung verursachten Bearbeitungsfehler bis zu 50% des Gesamtfehlers des Werkstücks ausmachen.
Bei jedem Bearbeitungsprozess muss das Bearbeitungssystem in irgendeiner Weise justiert werden. Da die Einstellung jedoch nicht perfekt genau sein kann, kommt es zu Einstellfehlern. Die gegenseitige Positionsgenauigkeit von Werkstück und Fräser auf der Werkzeugmaschine wird durch Einstellungen an der Werkzeugmaschine, dem Fräser, der Vorrichtung oder dem Werkstück gewährleistet.
Wenn die ursprüngliche Genauigkeit der Werkzeugmaschine, des Fräsers, der Vorrichtung und des Rohteils den Prozessanforderungen entspricht, ohne dynamische Faktoren zu berücksichtigen, wird der Einstellfehler zum wichtigsten Faktor bei der Bestimmung des Bearbeitungsfehlers.
Bei der Messung von Teilen während oder nach der Bearbeitung wird die Genauigkeit der Messung direkt von der Messmethode, der Genauigkeit des Messgeräts, dem Werkstück sowie von subjektiven und objektiven Faktoren beeinflusst.
Spannungen, die innerhalb eines Teils ohne äußere Kraft auftreten, werden als Eigenspannung. Sobald Eigenspannung in einem Werkstück erzeugt wird, befindet sich das Metall in einem Zustand mit hohem Energiepotenzial und Instabilität. Um einen Zustand mit geringerer Energie und Stabilität zu erreichen, wird das Metall verformt, was zum Verlust der ursprünglichen Bearbeitungsgenauigkeit des Werkstücks führt.