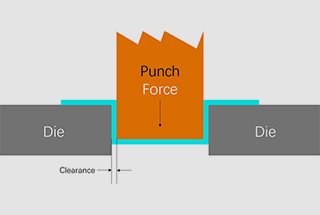
Haben Sie sich jemals gefragt, wie Präzisionsteile hergestellt werden? Das Feinschneiden ist eine bahnbrechende Technologie, die hochwertige Komponenten mit beispielloser Genauigkeit und Geschwindigkeit herstellt. In diesem Blogbeitrag tauchen wir in die faszinierende Welt des Feinschneidens ein und erforschen seine Prinzipien, Vorteile und realen Anwendungen. Entdecken Sie, wie dieses innovative Verfahren Branchen von der Automobil- bis zur Elektronikindustrie revolutioniert, und erfahren Sie, was unser Team von Maschinenbauexperten dazu zu sagen hat. Lassen Sie sich von der Präzision und Effizienz des Feinschneidens überraschen!
Der Unterschied zwischen Normalausblendung und Feinausblendung Stanzprozess
Vergleich der Schnittflächen von normalen Stanzteilen und Feinschneidteilen
Während des Stanzvorgangs wird die Zahnkranzpressplatte verwendet, um Kraft auf das Material auszuüben und es auf die Matrize zu pressen, wodurch ein seitlicher Druck auf die Innenfläche des V-förmigen Zahns entsteht. Dadurch wird ein Reißen in der Scherzone und ein seitliches Fließen des Metalls verhindert.
6mm dickes FORD Handbremslüfterteil (Handbremssektor)
Während die Stanzwerkzeuge in das Material gedrückt werden, wird das Material durch den Gegendruck des Auswerfers komprimiert. Dadurch und durch die Verwendung eines kleinen Spalts und einer konkaven Matrize mit abgerundeter Kante wird die Spannungskonzentration beseitigt und das Metall in der Scherzone in drei Richtungen unter Druckspannung gesetzt, wodurch die Zugspannung verringert und die Plastizität des Materials verbessert wird.
Dieser Ansatz verhindert das Biegen, Dehnen und Reißen, die beim herkömmlichen Stanzen typischerweise auftreten, und bewirkt stattdessen, dass das Material durch reine Scherung entlang der Kantenform der Matrize in Teile geschnitten wird, was zu hochwertigen, glatten und gleichmäßigen Scherflächen führt.
6 mm dicke TESLA-Sitzteile
Beim Feinschneiden sind die Presskraft, der Schnittspalt und der Kantenradius der Matrize voneinander abhängig und wichtig. Der Einfluss dieser Faktoren ist miteinander verbunden, und wenn der Spalt gleichmäßig und der Kantenradius geeignet ist, kann ein glatter Abschnitt mit minimalem Pressmaterial hergestellt werden.
6 mm dicke TOYOTA-Rohre Zusammensetzung Flansch
Extrem hohe Anforderungen an die Ebenheit
Das Feinschneiden, auch als Präzisionsschneiden bekannt, ist ein fortschrittliches Stanzverfahren, das sich aus den herkömmlichen Stanztechniken entwickelt hat. Beide Verfahren fallen zwar unter die Kategorie der Blechtrennung, aber beim Feinschneiden werden spezifische Parameter und Werkzeugkonfigurationen verwendet, die es vom allgemeinen Stanzen unterscheiden. Die dabei entstehenden Teile weisen hervorragende Qualitätsmerkmale auf, darunter außergewöhnlich glatte Schnittflächen, minimale Gratbildung und enge Maßtoleranzen.
Bei diesem hochpräzisen Verfahren kommen eine dreifach wirkende Presse und speziell entwickelte Werkzeuge zum Einsatz, die unter anderem über einen festen Schneidstempel, einen Gegenstempel und einen V-Ring-Eindringkörper verfügen. Der kontrollierte Materialfluss während des Vorgangs ermöglicht die Herstellung komplexer Geometrien mit nahezu vollständiger Formgenauigkeit, wodurch häufig Nachbearbeitungen überflüssig werden.
In Verbindung mit ergänzenden Kaltumformungsverfahren wie Biegen, Tiefziehen, Bördeln, Prägen und Präzisionsstrangpressen hat das Feinschneiden ein erhebliches Potenzial, herkömmliche Fertigungsverfahren zu ersetzen. Es bietet eine überzeugende Alternative zu konventionellem Stanzen, Zerspanen, Schmieden, Gießen und Pulvermetallurgie in verschiedenen Industriezweigen, darunter Automobilbau, Luft- und Raumfahrt, Elektronik und Präzisionsmaschinen. Diese Substitution wird durch die technischen Vorteile des Feinschneidens vorangetrieben, wie z. B. die bessere Materialausnutzung, die höhere Funktionalität der Teile und die kürzeren Produktionszyklen, in Verbindung mit den wirtschaftlichen Vorteilen, wie z. B. niedrigere Gesamtproduktionskosten und höhere Produktivität.
Die Fähigkeit des Feinschneidens, Komponenten mit komplizierten Merkmalen, engen Toleranzen und hervorragender Oberflächengüte in einem einzigen Arbeitsgang herzustellen, macht es besonders wertvoll für die Fertigung kritischer Teile wie Zahnräder, Kettenräder, Schlosskomponenten und komplexe Halterungen. Da die Industrie immer höhere Präzision und Effizienz verlangt, wird das Feinschneiden eine immer wichtigere Rolle in modernen Fertigungsprozessen spielen.
Die verschiedenen Methoden des Feinschneidens werden nach ihren technologischen Verfahren wie folgt kategorisiert:
1. Der Unterschied zwischen . und Feinstanzung
Das Feinschneiden, von dem wir oft sprechen, ist kein Feinschneiden im allgemeinen Sinne (wie z. B. Beschneiden, Fertigschneiden und Schnellschneiden usw.), sondern ein Feinschneiden mit einer starken Druckplatte (siehe Abbildung unten).
Das Grundprinzip des Feinschneidens besteht darin, mit Hilfe einer speziellen Presse (mit dreifacher Kraft) eine plastische und scherende Verformung des Materials mit Hilfe eines speziell strukturierten Werkzeugs zu erzeugen, um qualitativ hochwertige Feinschneidteile zu erhalten.
2. Feinschneiden Prozessmerkmale
Die folgende Tabelle zeigt die Merkmale der beiden unterschiedlichen Verfahren: Grobschnitt und Feinschnitt.
Technisches Merkmal | Blanking | Feinschneiden |
Formen der Materialtrennung | Scherverformung (kontrolliertes Reißen) | Plastisch-scherende Verformung (Rissunterdrückung) |
2. die Qualität der Arbeit | ||
●Maßhaltigkeit | ISO11-13 | ISO7-11 |
Rauhigkeit der gereinigten Oberfläche Ra (um) | Ra>6,3 | Ra1.6~0.4 |
● Form- und Lagefehler: | ||
Ebenheit | groß | klein(0,02mm/10mm) |
Nicht-Rechtwinkligkeit | groß | Klein (einseitig 0,0026mm/1mm) |
versunkener Defekt | (20~35)%S | (10~25)%S |
Klette | zweidimensional, groß | Einweg, klein |
3. sterben | ||
●Lücke | Bilateral (5-10)%S | einseitig 0,5% S |
●Kante | scharf | Fase |
4. Stanzmaterialien | Keine Anforderung | Gute Plastizität (Sphäronisierung) |
5. Schmierung | allgemein | Spezial |
6. Drückt | ||
●Kraftzustand | Normal (unidirektionale Kraft) | Spezial (dreidimensionale Kraft) |
●Prozessbelastung | kleine Verformungsarbeiten | Die Verformungsarbeit ist 2 bis 2,5 Mal höher als beim allgemeinen Feinschneiden. |
● Schutz der Umwelt | Lärm und starke Vibrationen | Geräuscharm, geringe Vibration |
7. Kosten | niedrig | Hoch (kurze Amortisationszeit) |
3. Funktionsprinzip der Matrize
Die Feinschneidmaschine ist eine Spezialausrüstung für die Durchführung des Feinschneidprozesses.
Wie in der nachstehenden Abbildung dargestellt, gibt es drei Arten von Kräften (PS, PR, PG), die während des Feinschneidens auf die Matrize wirkt.
Vor dem Beginn des Durchschlagens der Ringkraft PRdurch die Scherlinie außerhalb der Führungsplatte (6), so dass die V-förmige Zahnkranz (8) in das Material gepresst und auf die Matrize gepresst, wodurch ein seitlicher Druck auf die Innenfläche des V-förmigen Zahnkranzes erzeugt wird, um das Reißen des Materials in der Scherzone und das seitliche Fließen von Metall außerhalb der Scherzone zu verhindern.
Zugleich wird der Gegendruck PG wird durch den Auswerfer (4) in der Scherlinie gepresst, der das Material gegen die Nocken drückt, und im gepressten Zustand unter Einwirkung der Stanzkraft PS.
Das Metall befindet sich in der Scherzone in einem dreifachen Druckspannungszustand, der die Plastizität des Materials erhöht.
An diesem Punkt folgt das Material der Form der Matrizenkante und stanzt das Teil in reiner Scherform.
Am Ende des Stanzens wird PR und PG Der Druck wird abgelassen, die Matrize wird geöffnet und die Teile und der Schrott werden durch die Auswerferkraft P ausgeworfen.RA und die Auswerferkraft PGA und werden mit Druckluft ausgeblasen.
4. Feinschneidarbeitsprozess
(a) Die Matrize wird geöffnet und das Material wird zugeführt;
(b) Die Matrize wird geschlossen und das Material innerhalb und außerhalb der Schnittkante (Stanzlinie) durch Ringkraft und Gegendruck komprimiert;
(c) Das Material wird mit der Schnittkraft P ausgestanztSund die Druckkraft PR und PG werden in dem gesamten Prozess effektiv gepresst;
(d) Am Ende des Stempelhubs befindet sich der Stempel in der Matrize, und der Bohrungsabfall wird in die Auslaufmatrize gespült;
(e) Die Ringkraft PR und Gegendruck PG werden entfernt und die Matrize wird geöffnet;
(f) In der Stellung, in der die Kraft des Zahnkranzes aufgebracht wird, wird der Bohrmüll ausgeworfen und die Ausstoßkraft PRA aus der Stanzrunde;
(g) In der Stellung, in der der Gegendruck aufgebracht wird, wirkt an diesem Punkt: die Aufsetzkraft PGA aus dem Würfel.
Die Materialzufuhr beginnt;
h) Abfälle von Feinschneidteilen und Innenlöchern ausblasen oder entfernen.
Die Materialzufuhr ist abgeschlossen.
Die Technologie der Feinschneidteile zielt in erster Linie darauf ab, die technischen und funktionalen Anforderungen an die Teile zu erfüllen und gleichzeitig einfach und kostengünstig in der Serienfertigung zu sein. Zu den Faktoren, die die Technologie beeinflussen, gehören:
Die Technologie der Struktur des Feinschneidteils bezieht sich auf die Elemente, aus denen sich die Geometrie des Teils zusammensetzt, einschließlich der Bestimmung des Mindestrundungsradius, der Öffnung, der Wanddicke, der Ringbreite, der Nutbreite und des Stanzmoduls, um nur einige zu nennen. Diese Werte sind für Feinschneidteile tendenziell kleiner als für Normalschneidteile, was durch das Prinzip des Feinschneidens bedingt ist. Durch eine gute Auslegung der Strukturparameter können jedoch die Produktqualität verbessert und die Produktionskosten gesenkt werden.
Hinweis: Die im Originaltext erwähnte Abbildung ist nicht enthalten.
Entsprechend der Geometrie des Teils und seiner Struktureinheiten wird es in S1, S2 und S3 in jedem der Diagramme.
In dem Bereich unter S3ist die Feinstanzung nicht geeignet, oder es sind besondere Maßnahmen erforderlich.
Bei Verwendung des Bereichs von S3Die Bedingung ist, dass das Stanzelement aus Schnellarbeitsstahl besteht und die Zugfestigkeit des Feinschneidmaterials δb≤600 N/mm beträgt.2 (Scherfestigkeit Ks≤430N/mm2).
Beispiel:
Die Schaltnocke in der Abbildung, das Material ist Cr15 (Sphäroidisierung), Ks=420N/mm2die den Schwierigkeitsgrad der Aufgabe bestimmt.
Die maximale Schwierigkeit dieses Teils ist Runde b, so dass die Gesamtschwierigkeit S3 und kann fein ausgeschnitten werden.
Dicke S(mm) | Zugfestigkeit 600N/mm2 | ||
I.D J | O.D A | Bohrung Dia. X | |
0.5-1 | 6-7 | 7 | 7 |
1-2 | 7 | 7 | 7 |
2-3 | 7 | 7 | 7 |
3-4 | 7 | 8 | 7 |
4-5 | 7-8 | 8 | 8 |
5-6.3 | 8 | 9 | 8 |
6.3-8 | 8-9 | 9 | 8 |
8-10 | 9-10 | 10 | 8 |
10-12.5 | 9-10 | 10 | 9 |
12.5-16 | 10-11 | 10 | 9 |
1. Toleranzen bei den Abmessungen
Die Maßtoleranzen von Präzisionsstanzteilen hängen ab von: der Form des Teils, der Qualität der Werkzeugherstellung, der Materialstärke und -eigenschaften, den Schmiermitteln und den Einstellungen der Presse, die aus Tabelle 1 ausgewählt werden können.
2. Ebenheitstoleranz
Die Ebenheit eines Präzisionsstanzteils ist die Durchbiegung der Teilebene, die den Wert hat:
f = h - s
Feinschneidteile haben eine gute Ebenheit, die auf den gepressten Zustand des Materials während des Feinschneidprozesses zurückzuführen ist. Die Ebenheit kann je nach Größe, Form, Materialstärke und mechanischen Eigenschaften der Teile variieren.
Im Allgemeinen sind dickere Teile gerader als dünne Teile, Werkstoffe mit geringerer Festigkeit sind gerader als hochfeste Werkstoffe, und Werkstoffe mit höherer Presskraft sind gerader als solche mit geringerer Presskraft.
Die Oberfläche des Materials auf der konvexen Seite der Matrize ist immer konkav, während die konkave Seite der Matrize immer konvex ist.
Wenn das Teil jedoch mit einer kontinuierlichen Matrize gestanzt, gerillt, gekerbt, gebogen oder gestanzt werden muss, kann die Ebenheit aufgrund lokaler Verformungen oder unterschiedlicher Stanzrichtungen am Teil stark schwanken.
Dennoch ist die Ebenheit von Präzisionsstanzteilen immer besser als die von normalen Stanzteilen. Die Abbildung unten zeigt die allgemeine Geradheit gemessen in einem Abstand von 100 mm.
3. PRechtwinkligkeitstoleranz
Die Oberfläche eines Feinstanzteils und die Grundfläche bilden einen Winkel mit einer bestimmten Toleranz, die als Nicht-Rechtwinkligkeit bezeichnet wird. Diese wird von Faktoren wie der Dicke und den Eigenschaften des Materials, dem Zustand der Schneide beim Stanzen, der Steifigkeit des Werkzeugs und der Einstellung der Presse beeinflusst.
Bei einer Materialstärke von 1 mm beträgt die Abweichung von der Rechtwinkligkeit im Allgemeinen 0,0026 mm, und bei einer Materialstärke von 10 mm ist die Gratseite 0,052 mm größer als die versenkte Seite. Die Beziehung zwischen der Materialstärke und der Nicht-Rechtwinkligkeit ist unten dargestellt.
4. Qualität der gestanzten Oberfläche
Die Qualität von Feinschneidteilen wird weitgehend durch die Schnittfläche bestimmt.
Diese Oberfläche wird von Faktoren wie der Art des Materials, seinen Eigenschaften und seiner metallurgischen Struktur, der Qualität der Matrize und der Schneidkante, der Verwendung von Schmiermitteln und der Einstellung der Presse beeinflusst.
Die Stanzfläche besteht aus vier verschiedenen Komponenten: glatte Oberfläche, Spaltfläche, eingesunkene Fehlerfläche und Gratfläche.
Die folgende Abbildung zeigt die drei Hauptmerkmale der Ausblendfläche und ihre Bedeutung.
In der Abbildung:
(1) Ausblendung Oberflächenrauhigkeit
Die Oberflächenbeschaffenheit der Stanzfläche variiert in verschiedenen Richtungen und an verschiedenen Stellen des Umfangs. In der Regel ist die Seite, die zusammengebrochen ist, glatter als die Gratseite. Die Rauheit der gestanzten Oberfläche wird durch den arithmetischen Mittelwert aR dargestellt, der typischerweise zwischen Ra = 0,2 und 3,6 liegt und in sechs Stufen unterteilt wird (siehe Tabelle 2).
Die Messrichtung ist senkrecht zur Stanzrichtung, und die Messstelle befindet sich in der Mitte der Stanzfläche (wie in Abbildung 6a dargestellt). Die Beziehung zwischen der Rauheit der Stanzfläche und der Zugfestigkeit des Materials ist in Abbildung 6b dargestellt.
Tabelle 2 Ausblendung Oberflächenrauhigkeit
Rauheitsklasse | 1 | 2 | 3 | 4 | 5 | 6 |
Ra(μm) | 0.2 | 0.4 | 0.6 (0.8) | 2.4 | 3.4 | 3.8 (3.6) |
Codename | N4 | N5 | N6 | N7 | N | N8 |
(2) Integritätsrate der Ausblendfläche
Es gibt fünf Stufen der Unversehrtheit auf der Stanzfläche von Feinschneidteilen.
Unversehrtheit der Oberfläche beim Ausblenden | |
h | l |
100% S | 100% S |
100% S | 90% S |
90% S | 75% S |
75% S | — |
50% S | — |
(3) Spaltgrad der Stanzfläche
Es gibt vier Stufen der Spaltung auf der Stanzfläche von Feinschneideteilen.
Spaltmaß der Stanzfläche | |
E (mm) | Klasse |
0.3 | 1 |
0.6 | 2 |
1 | 3 |
2 | 4 |
(4) Methode und Bedeutung der Qualität der Stanzfläche
Die Darstellung und Bedeutung der Qualitätsmerkmale der Stanzfläche sind in der folgenden Abbildung dargestellt.
Zum Beispiel,
Der Einfallwinkel bezieht sich auf die unregelmäßige plastische Verformung der konvexen Kurve am Übergang zwischen der glatten Oberfläche, der inneren und der äußeren Konturebene der Feinstanzteile (siehe Abbildung 8).
Die Größe des Einsturzes wird von verschiedenen Faktoren wie der Materialstärke beeinflusst, Materialeigenschaften, Teileform, Gegendruck und Zahnkranzhöhe. Eine Berechnungsmethode für den Einfallwinkel kann anhand der nachstehenden Abbildung ausgewählt werden.
Im Allgemeinen gilt: tE≈(5~10)S, bE≈(5~10)tE.
Berechnen Sie den Wert des Kollapswinkels tE und bE
Grate sind unregelmäßige Erhebungen an der Kante der Stanzfläche von Feinstanzteilen. Die Größe der Grate hängt von verschiedenen Faktoren ab, z. B. von der Art des Materials, dem Freiraum, dem Zustand der Schneidkante der Matrize, der Tiefe der Matrize im Material und der Anzahl der Stanzzyklen.
Der beim Feinschneiden entstehende Grat ist kein Ergebnis des Schneidens, sondern ein Fließpressgrat. Die Größe des Grats wird nicht nur durch seine Höhe, sondern auch durch die Dicke seiner Wurzel bestimmt.
Nach der Norm VDI3345 entsteht bei einer scharfen Stanzkante nur ein dünner Grat mit einer Größe von 0,01 bis 0,08 mm. Wird die Stanzkante hingegen stumpf, entsteht ein dickerer Grat mit einer Größe von 0,1 bis 0,3 mm (wie in der Abbildung unten dargestellt).
Das Feinschneiden ist ein Fließscherenverfahren, bei dem die Stanzwerkzeug führt zu einer starken Verformung der Metallgewebekristalle, was zu einer Trennung führt. Die Art des Feinschneidmaterials wirkt sich auf die Oberflächenqualität, die Maßgenauigkeit und die Werkzeugstandzeit der Feinschneidteile aus.
Die Grundvoraussetzungen dafür sind:
1. Es muss eine gute Formbarkeit und ein hohes Denaturierungsvermögen aufweisen.
Dies ermöglicht in erster Linie, dass der Materialfluss in der Scherzone bis zum Ende der Scherung anhält, ohne zu reißen.
Die besten Ergebnisse des Feinschneidens werden mit Stählen mit einer Zugfestigkeit δb ≤ 650 N/mm erzielt.2 und eine Kohlenstoffgehalt von 0,35%.
[1] Feinschneidverhalten des Materials
-Verformungsgrad der Aufkohlungskörper und Karbide (Sphäronisierung)
[2] Verformbarkeit von Materialien
Feinschneidstoffe mit höheren Werten für Bruchdehnung und Endschrumpfung weisen bessere Verformungseigenschaften auf. Eine niedrige Streckgrenze zeigt an, dass das Material bei niedrigem Druck zu fließen beginnt. Der entsprechende Festigkeitsbereich für Feinschneidstoffe ist in der folgenden Abbildung dargestellt, wobei der Kohlenstoffgehalt als äquivalenter Kohlenstoffgehalt angegeben ist.
2. Sie muss eine gute Organisationsstruktur haben.
Feinschneidmaterialien stellen hohe Anforderungen an ihr metallurgisches Gefüge. Die Qualität des Feinschneidens kann durch das metallurgische Gefüge erheblich beeinflusst werden, selbst wenn der verwendete Werkstoff zwar der gleiche ist, aber anders behandelt wird.
Für Kohlenstoffstahl und legierter Stahl mit einem Kohlenstoffgehalt von mehr als 0,35% spielen die Form und die Verteilung des Zementits (Fe3C) eine entscheidende Rolle für die Oberflächenbeschaffenheit beim Scheren.
Die gleichmäßig feinkörnig verteilten Karbide nach der Sphäroidisierung und die Spanperlitstruktur führen zu einer guten, glatten Schnittfläche.
Die nachstehende Abbildung zeigt, wie die unterschiedlichen metallografischen Strukturen von Kohlenstoffstahl mit 0,45%-Kohlenstoff zu einer unterschiedlichen Scherflächenqualität führen. Links ist die unbehandelte Vorferrit-Perlglanzstruktur zu sehen, rechts der sphärolithische aufgekohlte Körper nach der Sphäroidisierung.
3. Kaltverfestigung während des Feinschneidens
Das Feinschneiden ist ein komplexer Prozess, der das Strangpressen und Scheren von Werkstoffen umfasst. Das Material wird in der Scherzone stark kalt verformt, was zu einer höheren Härte in der Kaltverfestigungszone im Vergleich zur Härte der Grundmasse führt.
Um den Prozess des Feinschneidens zu verstehen, ist es entscheidend, die Gesetze der Kaltverfestigung zu kennen und die Größe, Form und Tiefe der Kaltverfestigung sowie ihre tatsächlichen Auswirkungen auf die fertigen Feinschneidteile zu bestimmen.
Abb. 12 zeigt die Kaltverfestigung von Werkstoffen während des Grob- und Feinschneidens.
1. Grundsatz der Auswahl
Es ist wichtig, die funktionalen Anforderungen an Feinschneidteile zu erfüllen und gleichzeitig die Kosteneffizienz zu berücksichtigen. Dabei sind Faktoren wie Materialart und -verfügbarkeit, Maßtoleranzen, Oberflächenqualität und der Schwierigkeitsgrad beim präzisen Stanzen zu berücksichtigen.
2. Materialvielfalt
Zu den Eisenmetallen gehören: weicher Stahl (C≤0,13%); unlegierter Stahl (0,12-1,0%C); legierter Stahl (0,15-0,20%C); rostfreier Stahl (C≤0,15%); Feinkornstahl (0,10-0,22%C).
Zu den Nichteisenmetallen gehören: Kupfer und Kupferlegierungen, Aluminium und Aluminiumlegierungen.
Weiterführende Lektüre: Eisenhaltige Metalle vs. Nichteisenmetalle
3. Stand der Versorgung
Für Stahlanforderungen:
FSG I: Maximale Zugfestigkeit, ohne die Anforderung an die metallurgische Organisation.
FSG II: nach Glühen Behandlung, Material C>0.15%, mit etwa 80-90% kugelförmigen Aufkohlungskörpern.
FSGIII: Erweicht und geglüht, Material C>0.15%, mit ca. 100% kugelförmigem Aufkohlungskörper.
Für Nichteisenmetalle wie Kupfer, Aluminium und ihre Legierungen gelten bestimmte Anforderungen an die chemische Zusammensetzung und den Walzzustand.
4. Bewertung der Feinausblendung
Die Bewertung der Feinschneidmaterialien und ihre Auswahl sind in Tabelle 5 dargestellt.
Stahlsorte | Maximale Stanzdicke | Bewertung der Feinschneidleistung | ||||
China (YB) | USA (AISI) | Deutschland (DIN) | Japan (JIS) | Sowjetunion (rOCT) | ||
08 | 1008 | 15 | 1 | |||
10 | 1010 | C10 | S10C | #10 | 15 | 1 |
15 | 1015 | C15 | S15C | #15 | 12 | 1 |
20 | 1020 | C22 | S20C | #20 | 10 | 1 |
25 | 1025 | S25C | #25 | 10 | 1 | |
30 | 1030 | S30C | #30 | 10 | 1 | |
35 | 1035 | C35 | S35C | #35 | 8 | 2 |
40 | 1040 | S40C | #40 | 7 | 2 | |
45 | 1045 | C45 | S45C | #45 | 7 | 2 |
50 | 1050 | CK53 | S50C | #50 | 6 | 2 |
55 | 1055 | Cf56 | S55C | #55 | 6 | 2 |
60 | 1060 | C60 | SWRH4B | #60 | 5 | 2 |
1064 | CK60 | S58C | 6 | |||
65 | 1065 | CK67 | SUP2 | #65 | 3 | |
70 | 1070 | 3 | 2 | |||
1074 | C75 | 3 | ||||
T8A | C85W2 | SKU3 | Y8A | 3 | ||
T10A | W1-0.8C | 3 | 3 | |||
15Mn/16Mn | 8 | 3 | ||||
15CrMn | 16MnCr5 | 15XI | 5 | 2 | ||
14Ni6 | 8 | 2 | ||||
14NiCr10 | SNC21H | 7 | ||||
E3316 | 14NiCr14 | SNC22H | 7 | |||
14NiCr18 | 7 | |||||
15CrNi6 | 6 | |||||
18CrNi8 | 5 | |||||
4317 | 17CrNiMo6 | 5 | ||||
15Kr | 15Cr3 | SCr21 | 15X | 5 | 2 | |
15CrMo5 | 4 | |||||
20CrMo | 4118 | 20CrMo5 | SCM22 | 20XM | 4 | 2 |
20CrMo | 20MnCr5 | 4.5 | 2 | |||
20MnMo | 8 | 2 | ||||
42Mn2V | 42MnV7 | 6 | 2 | |||
GCr15 | E52100 | 100Cr6 | SUJZ | IIIX15 | 6 | 3 |
0Cr13 | 410 | X7Cr13 | ||||
1Cr13 | 403 | X10Cr13 | SUS21 | 1X13 | ||
4Cr13 | X40Cr13 | 4X13 | ||||
Cr17 | 430 | X8Cr17 | SUS24 | X17 | ||
0Cr18Ni9 | 304L | X5CrNi189 | SUS27 | 0X18H9 | ||
1Cr18Ni9 | 302 | X12CrNi188 | SUS40 | 1X18H9 | ||
1Cr18Ni9Ti | 321 | X10CrNiTi189 | SUS29 | 1X18H9T | ||
304L | X2Crni189 | SUS28CP | ||||
X8CrNi1212 | ||||||
301 | X12CrNi177 | SUS39CP | ||||
X2NiCr1816 |
Anmerkungen: