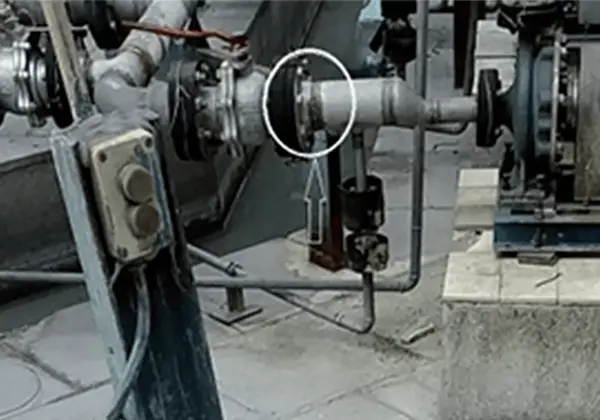
Was genau ist interkristalline Korrosion bei nichtrostendem Stahl, und warum ist es so wichtig, sie zu kontrollieren? Diese heimtückische Form der Korrosion greift entlang der Korngrenzen des Metalls an und führt oft zu katastrophalen Ausfällen ohne sichtbare Warnzeichen. In diesem Artikel werden die Mechanismen der interkristallinen Korrosion, die Umweltbedingungen, die sie verschlimmern, und die besten Methoden zu ihrer Verhinderung erläutert. Sie erhalten ein umfassendes Verständnis dafür, wie Sie Edelstahlkonstruktionen schützen können, um ihre Langlebigkeit und Zuverlässigkeit zu gewährleisten.
Die vereinheitlichten technischen Vorschriften schreiben im Allgemeinen vor, dass Behälter aus austenitischem nichtrostendem Stahl, die in Umgebungen eingesetzt werden, die interkristalline Korrosion verursachen können, nach dem Schweißen einer Mischkristall- oder Stabilisierungsbehandlung unterzogen werden müssen. Diese Anforderung ist vernünftig.
Doch selbst wenn der Konstrukteur diese Anforderung in die technischen Spezifikationen der Zeichnung aufnimmt, ist es für den Hersteller oft schwierig, die idealen Normen zu erfüllen, da die Parameter des Wärmebehandlungsprozesses schwer zu kontrollieren sind und andere unvorhergesehene Schwierigkeiten auftreten. In der Realität werden die meisten der heute verwendeten Geräte aus nichtrostendem Stahl ohne eine Wärmebehandlung nach dem Schweißen verwendet.
Dies wirft die Frage auf: Was ist der Mechanismus der interkristallinen Korrosion, die die häufigste Form der Korrosion bei austenitischem nichtrostendem Stahl ist? Welches sind die Umweltbedingungen, die zu interkristalliner Korrosion führen können? Welches sind die wichtigsten Methoden zur Vermeidung und Kontrolle interkristalliner Korrosion? Sind Wärmebehandlungen für Behälter aus austenitischem rostfreiem Stahl erforderlich, die in Umgebungen eingesetzt werden, die nach dem Schweißen interkristalline Korrosion verursachen können?
In diesem Artikel werden diese Fragen durch Verweise auf einschlägige Normen, Spezifikationen und Monografien sowie durch die Darstellung persönlicher Meinungen aufgrund von Produktionserfahrungen untersucht.
Interkristalline Korrosion ist eine Art von örtlich begrenzter Korrosion, die entlang der Korngrenzen oder in der Nähe der Korngrenzen eines Metalls oder einer Legierung auftritt. Diese Korrosion ist gekennzeichnet durch minimale Korrosion innerhalb der Körner und erhebliche Korrosion entlang der Korngrenzen, die die Bindung zwischen den Körnern schwächt.
Wenn die interkristalline Korrosion stark ausgeprägt ist, kann sie die Festigkeit und Duktilität des Metalls verringern, so dass es unter normalen Belastungen versagt. Die beiden Haupttheorien für interkristalline Korrosion sind die Theorie des geringen Chromgehalts und die Theorie der selektiven Auflösung von Verunreinigungen an den Korngrenzen.
Die interkristalline Korrosion der üblicherweise verwendeten austenitischen nichtrostenden Stähle in oxidierenden oder schwach oxidierenden Umgebungen wird in der Regel durch unsachgemäßes Erhitzen während der Verarbeitung oder Verwendung verursacht. Unter unsachgemäßem Erhitzen versteht man das Erhitzen oder langsame Abkühlen des Stahls in einem Temperaturbereich von 450-850°C, wodurch er anfällig für interkristalline Korrosion wird. Dieser Temperaturbereich gilt daher als gefährlich für austenitischen rostfreien Stahl.
Austenitischer rostfreier Stahl wird einer Lösungsbehandlung unterzogen, bevor er das Werk verlässt. Bei der Lösungsbehandlung wird der Stahl auf 1050-1150 °C erhitzt und dann schnell abgekühlt, um einen homogenen Mischkristall zu erzeugen. Austenitischer Stahl enthält eine geringe Menge an Kohlenstoff, und seine Feststofflöslichkeit nimmt mit abnehmender Temperatur ab. Beispielsweise beträgt die Feststofflöslichkeit von Kohlenstoff in 0Cr18Ni9Ti etwa 0,2% bei 1100°C und etwa 0,02% bei 500-700°C.
Der Kohlenstoff in lösungsbehandeltem Stahl ist daher übersättigt. Wenn der Stahl auf 450-850°C erhitzt oder abgekühlt wird, kann sich der Kohlenstoff aus der Lösung absetzen. Austenit und verteilen sich entlang der Korngrenzen in Form von (Fe, Cr) 23C6. Der Chromgehalt von (Fe, Cr) 23C6 ist viel höher als der der austenitischen Matrix, und seine Ausscheidung verbraucht eine große Menge an Chrom in der Nähe der Korngrenzen, die nicht rechtzeitig durch Diffusion wieder aufgefüllt werden kann. Die langsame Diffusion von Chrom führt dazu, dass der Chromgehalt in der Nähe der Korngrenzen unter den für die Passivierung erforderlichen Grenzwert von 12% Cr fällt, wodurch ein chromarmer Bereich entsteht und der passive Zustand beschädigt wird.
Das Korn selbst befindet sich jedoch weiterhin in einem passiven Zustand mit einem hohen Potenzial. Das Korn und die Korngrenze bilden eine mikrogalvanische Batterie mit einer großen Kathode und einer kleinen Anode, was zu Korrosion im Korngrenzenbereich führt.
In der Produktionspraxis haben wir festgestellt, dass austenitischer rostfreier Stahl auch in stark oxidierenden Medien (wie konzentrierter Salpetersäure) interkristalline Korrosion erleiden kann, aber die Art der Korrosion unterscheidet sich von der in oxidierenden oder schwach oxidierenden Medien. Interkristalline Korrosion in stark oxidierenden Medien tritt in der Regel bei mischkristallbehandeltem Stahl auf, nicht aber bei sensibilisiertem Stahl.
Wenn die Verunreinigungen, wie Phosphor oder Silizium, 100 ppm bzw. 1000-2000 ppm im Mischkristall erreichen, lagern sie sich entlang der Korngrenzen ab. Diese Verunreinigungen lösen sich unter der Einwirkung starker oxidierender Medien auf und verursachen interkristalline Korrosion.
Wenn der Stahl sensibilisiert ist, wird durch die Bildung von (MP) 23C6 mit Phosphor oder die erste Seigerung von Kohlenstoff die Seigerung von Verunreinigungen an den Korngrenzen beseitigt oder verringert, wodurch die Empfindlichkeit des Stahls gegenüber interkristalliner Korrosion beseitigt oder geschwächt wird.
Diese beiden Theorien über den Mechanismus der interkristallinen Korrosion beziehen sich auf den Gefügezustand einer bestimmten Legierung und eines bestimmten Mediums und schließen sich nicht gegenseitig aus, sondern ergänzen sich vielmehr. In der Produktionspraxis treten die meisten Fälle von interkristalliner Korrosion in schwach oxidierenden oder oxidierenden Medien auf und können daher mit der Theorie des niedrigen Chromgehalts erklärt werden.
Es gibt zwei Haupttypen von Medien, die interkristalline Korrosion in austenitischem rostfreiem Stahl verursachen. Die erste Art sind oxidierende oder schwach oxidierende Medien und die zweite Art sind stark oxidierende Medien, wie konzentrierte Salpetersäure. Die erste Art von Medien ist am häufigsten.
Im Folgenden finden Sie eine Liste der üblichen Medien, die interkristalline Korrosion in austenitischem Edelstahl verursachen:
Die von G. A. Nelson erstellte "Corrosion Data Chart" listet die üblichen Medien auf, die interkristalline Korrosion in austenitischem nichtrostendem Stahl verursachen:
Wenn austenitischer rostfreier Stahl in einer Umgebung verwendet wird, die interkristalline Korrosion verursachen kann, muss die Prüfung der interkristallinen Korrosionsneigung gemäß den Prüfverfahren GB4334.1 bis GB4334 für interkristalline Korrosion von rostfreiem Stahl durchgeführt werden. Die Auswahl- und Qualifikationsanforderungen für die Prüfmethoden für die interkristalline Korrosionsneigung von austenitischem nichtrostendem Stahl müssen die folgenden Kriterien erfüllen:
(1) Austenitischer rostfreier Stahl und spezieller rostfreier Stahl für konzentrierte Salpetersäure, der in Salpetersäure mit einer Temperatur von 60°C oder höher und einer Konzentration von 5% oder höher verwendet wird, muss gemäß der GB4334.3 Prüfmethode für 65% Salpetersäurekorrosion von rostfreiem Stahl geprüft werden. Die durchschnittliche Korrosionsrate über fünf Zyklen oder drei Zyklen darf nicht mehr als 0,6 g/m2h (oder entsprechend 0,6 mm/a). Die Probe kann in Gebrauch oder sensibilisiert sein.
(2) Chrom-Nickel austenitischer rostfreier Stahl (wie 0Cr18Ni10Ti, 0Cr18Ni9, 00Cr19Ni10 und ähnliche Stähle): Allgemeine Anforderungen: Gemäß der Schwefelsäure-Kupfersulfat-Korrosionsprüfmethode GB4334.5 für nichtrostenden Stahl dürfen nach der Biegeprüfung keine interkristallinen Korrosionsrisse auf der Oberfläche der Probe auftreten. Höhere Anforderungen: Die durchschnittliche Korrosionsrate darf 1,1 g/m nicht überschreiten.2h nach der Schwefelsäure-Eisensulfat-Korrosionsprüfmethode GB4334.2 für nichtrostenden Stahl.
(3) Molybdänhaltiger austenitischer rostfreier Stahl (wie 0Cr18Ni12Mo2Ti, 00Cr17Ni14Mo2 und ähnliche Stähle): Allgemeine Anforderungen: Nach der Schwefelsäure-Kupfersulfat-Korrosionsprüfmethode GB4334.5 für nichtrostenden Stahl dürfen nach der Biegeprüfung keine interkristallinen Korrosionsrisse auf der Oberfläche der Probe auftreten. Höhere Anforderungen: Die Korrosionsrate darf 1,5 gemäß der GB4334.4 Salpetersäure-Fluorwasserstoffsäure-Korrosionsprüfmethode für nichtrostenden Stahl nicht überschreiten. Die durchschnittliche Korrosionsrate darf 1,1 g/m nicht überschreiten.2h nach der Schwefelsäure-Eisensulfat-Korrosionsprüfmethode GB4334.2 für nichtrostenden Stahl.
(4) Wenn das Medium besondere Anforderungen stellt, können auch andere als die oben genannten Prüfungen zur interkristallinen Korrosion durchgeführt werden; die entsprechenden Qualifikationsanforderungen müssen angegeben werden.
Je nach Korrosionsmechanismus können die folgenden Maßnahmen ergriffen werden, um interkristalline Korrosion in austenitischem nichtrostendem Stahl zu verhindern und zu kontrollieren:
(1) Die Verwendung von rostfreiem Stahl mit sehr niedrigem Kohlenstoffgehalt kann dazu beitragen, die Kohlenstoffgehalt auf unter 0,03%.
So kann z. B. 00Cr17Ni14Mo2 gewählt werden, um die Bildung von (Fe, Cr) 23C6 im Stahl und das Auftreten einer chromarmen Zone zu verhindern, wodurch interkristalline Korrosion vermieden wird.
Für Bauteile mit geringer Festigkeit, geringer Spannung und guter Verformbarkeit kann 0Cr18Ni9 aufgrund seiner Kosteneffizienz gewählt werden.
(2) Stabilisierter rostfreier Stahl bezieht sich auf den rostfreien Stahl, der Titan und Niob.
Bei der Herstellung des Stahls wird eine bestimmte Menge Titan und Niob zugesetzt. Diese Elemente haben eine starke Affinität zu Kohlenstoff und bilden Tic oder ABC im Stahl.
Außerdem ist die Feststofflöslichkeit von tic oder NBC viel geringer als die von (Fe, Cr) 23C6 und nahezu unlöslich in Austenit bei der Temperatur des Mischkristalls.
Auf diese Weise wird die Wahrscheinlichkeit interkristalliner Korrosion in austenitischem rostfreiem Stahl stark reduziert, selbst wenn (Fe, Cr) 23C6 bei Erreichen der Sensibilisierungstemperatur nicht an der Korngrenze ausgeschieden wird.
Beispielsweise können Stähle wie 1Cr18Ni9Ti und 1Cr18Ni9Nb in einem Temperaturbereich von 500-700°C eingesetzt werden, ohne dass es zu interkristalliner Korrosion kommt.
(3) Beim Schweißen von austenitischem rostfreiem Stahl mit einem elektrischen Lichtbogen kann die Temperatur des Lichtbogenbads bis zu 1300°C erreichen, und die Temperatur auf beiden Seiten der Schweißnaht nimmt mit zunehmendem Abstand ab, wodurch eine Sensibilisierungstemperaturzone entsteht.
Es ist ideal, den austenitischen rostfreien Stahl innerhalb des Sensibilisierungstemperaturbereichs so langsam wie möglich zu erwärmen und abzukühlen.
Bei interkristalliner Korrosionsneigung sollte der instabile nichtrostende Stahl für 1-2 Minuten pro Millimeter auf 1000-1120°C erhitzt und anschließend abgeschreckt werden.
Für stabilisierten rostfreien Stahl wird eine Erhitzung auf 950-1050°C empfohlen.
Nach der Lösungsbehandlung darf der Stahl nicht auf die Sensibilisierungstemperatur erwärmt werden, da dies zu einer erneuten Ausscheidung von Chromkarbid an der Korngrenze führen kann.
(4) Die Wahl der richtigen Schweißmethode ist wichtig, um die Empfindlichkeit der Schweißnähte zu interkristalliner Korrosion. Wenn der Betrieb unverändert bleibt oder die Schweißmaterial zu dick ist, erhöht eine längere Schweißzeit die Wahrscheinlichkeit, innerhalb der sensibilisierten Temperaturzone zu bleiben.
Um die Empfindlichkeit der Schweißnähte zu minimieren, ist es notwendig, den Eintrag von Streckenenergie beim Schweißen zu minimieren.
Ganz allgemein gesprochen, Argon-Lichtbogenschweißen hat im Vergleich zum Lichtbogenschweißen einen geringeren Energieeintrag, was es zu einer besseren Wahl für Schweiß- und Reparaturarbeiten macht.
Für das Schweißen von Teilen wird die Verwendung von rostfreiem Stahl mit extrem niedrigem Kohlenstoffgehalt oder von rostfreiem Stahl mit stabilisierenden Elementen wie Titan und Niob empfohlen. Außerdem wird die Verwendung von Schweißdrähten mit extrem niedrigem Kohlenstoffgehalt oder niobhaltigen Schweißdrähten empfohlen.
Bei Verwendung von Argon LichtbogenschweißenUm eine Überhitzung der Schweißnaht zu vermeiden, sollte der Vorgang schnell erfolgen und der Grundwerkstoff auf beiden Seiten der Schweißnaht sollte nach dem Schweißen schnell abgekühlt werden, um die Zeit innerhalb des Sensibilisierungstemperaturbereichs zu minimieren.
Die Wärmebehandlung nach dem Schweißen ist nicht immer eine Priorität im Schweißbereich.
In der Regel wird eine Mischkristallbehandlung bei einer Temperatur von 1100-1150°C für eine bestimmte Dauer durchgeführt und dann abgeschreckt. Die Abkühlung im Bereich von 925-540°C sollte innerhalb von drei Minuten abgeschlossen sein, gefolgt von einer schnellen Abkühlung auf unter 425°C.
Für eine stabilisierte Behandlung sollte das Werkstück an der Luft abgekühlt werden, nachdem es mehrere Stunden lang bei einer Temperatur zwischen 850 und 880 °C gehalten wurde.
Die Wirksamkeit der Wärmebehandlung nach dem Schweißen hängt in hohem Maße von den wichtigsten Prozessparametern ab, wie z. B. Ofentemperatur, Temperaturanstiegsrate, Temperaturunterschied zwischen verschiedenen Teilen des Werkstücks während des Temperaturanstiegs, Ofenatmosphäre, Haltezeit, Temperaturunterschied zwischen verschiedenen Teilen während der Wärmekonservierung, Abkühlungsrate und Ofentemperatur.
Bei Behältern aus austenitischem rostfreiem Stahl, die interkristalline Korrosion verursachen können, kann eine Lösungsbehandlung oder eine stabilisierte Behandlung allgemeiner Teile durchgeführt werden. Die Wärmebehandlung des gesamten Behälters (in der Regel ein Wärmetauscher) nach dem Schweißen ist jedoch mit vielen Schwierigkeiten verbunden.
Bei dieser Art der Behandlung handelt es sich nicht um eine lokale Wärmebehandlung nach dem Schweißen, sondern um eine Wärmebehandlung nach dem Schweißen des gesamten geschweißten Teils oder Behälters.
Aufgrund der komplexen Struktur und Form der meisten chemischen Behälter, wie z. B. der häufig verwendeten Rohrbündelwärmetauscher, ist es nahezu unmöglich, die wichtigsten Prozessparameter für die Mischkristall- oder Stabilisierungsbehandlung des gesamten Rohrbündelwärmetauschers zu kontrollieren, geschweige denn die Qualität der Wärmebehandlung nach dem Schweißen zu gewährleisten.
In vielen Fällen kann sich diese Behandlung sogar als kontraproduktiv erweisen, da sie nicht nur die Schweißnahtstruktur nicht verbessert, sondern auch die Struktur des Grundmetalls unnötig verschlechtert.
Daher werden mehr als 90% der chemischen Behälter aus austenitischem nichtrostendem Stahl, die in Umgebungen mit interkristalliner Korrosion eingesetzt werden, noch in ihrem Zustand nach dem Schweißen verwendet und nicht einer Wärmebehandlung nach dem Schweißen unterzogen.
Chrom-Nickel-Austenit-Stahl ist das am häufigsten verwendete korrosionsbeständige Material, und interkristalline Korrosion ist die häufigste Form des Versagens bei Behältern aus Chrom-Nickel-Austenit-Stahl.
Interkristalline Korrosion schwächt die Verbindung zwischen den Körnern erheblich und kann in schweren Fällen die mechanische Festigkeit vollständig aufheben. Die Oberfläche des nichtrostenden Stahls, der dieser Art von Korrosion unterworfen wurde, bleibt blank, kann aber durch leichtes Klopfen in feine Partikel zerlegt werden.
Interkristalline Korrosion ist schwer zu erkennen und kann zu plötzlichen Geräteschäden führen und sollte ernst genommen werden.
Behälter aus austenitischem Chrom-Nickel-Stahl werden in der Regel durch Schweißen hergestellt, und die beiden Seiten der Schweißnaht sind interkristalline korrosionssensibilisierte Bereiche, die im Vergleich zum Grundmetall anfälliger für Korrosionsschäden sind.
Eine Wärmebehandlung nach dem Schweißen kann die Beständigkeit gegen interkristalline Korrosion im Schweißzone auf das gleiche Niveau wie das Grundmetall zu bringen. Dies ist das eigentliche Ziel der Wärmebehandlung nach dem Schweißen.
In der Praxis sind jedoch viele Faktoren zu berücksichtigen, wie z. B. die komplexe Gesamtstruktur und Form des Schweißstücks, die es schwierig machen, die Prozessparameter der Wärmebehandlung nach dem Schweißen zu garantieren.
Infolgedessen werden die meisten nichtrostenden Chrom-Nickel-Stähle nach dem Schweißen verwendet.
Ob die Schweißzone eines Behälters aus austenitischem Chrom-Nickel-Stahl, der für interkristalline Korrosionsbeständigkeit verwendet wird, einer Mischkristallbehandlung oder einer stabilisierten Behandlung unterzogen wird, kann nicht verallgemeinert werden. Die strukturelle Form des Behälters muss analysiert werden, um festzustellen, ob die Wärmebehandlung effektiv durchgeführt werden kann. Selbst wenn eine Wärmebehandlung nach dem Schweißen erforderlich ist, kann sie andernfalls nachteilige Auswirkungen haben, da sie nicht nur nicht das gewünschte Ergebnis erzielt, sondern auch die Struktur des Grundmetalls beeinträchtigt.
Um die interkristalline Korrosionsbeständigkeit von Behältern aus austenitischem Chrom-Nickel-Stahl zu verbessern, müssen nicht rostende Stähle mit extrem niedrigem Kohlenstoffgehalt und stabilisierte nicht rostende Stähle unter Berücksichtigung der spezifischen Korrosionsumgebung und des Korrosionsmechanismus ausgewählt werden, die richtige Schweißmethode beim Schweißen gewählt und die zuvor erwähnten Präventions- und Kontrollmaßnahmen richtig kombiniert werden, um gute Ergebnisse zu erzielen.
Sich auf einen Mischkristall oder eine Stabilisierungsbehandlung nach dem Schweißen zu verlassen, ist nicht ausreichend.