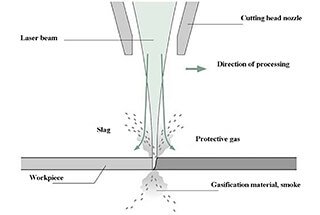
Was wäre, wenn die Einstellung des Fokus Ihres Laserschneiders den Unterschied zwischen einem sauberen Schnitt und einem misslungenen Projekt ausmachen könnte? Beim Laserschneiden ist die Position des Brennpunkts entscheidend für Präzision und Qualität. In diesem Artikel wird erklärt, wie man den richtigen Fokus wählt, wobei positive, negative und Null-Fokus-Techniken detailliert beschrieben werden, und es werden Tipps zur Maschineninspektion gegeben, um eine optimale Leistung zu gewährleisten. Entdecken Sie, wie Sie die besten Schnitte für verschiedene Materialien und Anwendungen erzielen.
Vor dem Schneiden eines Blechs muss der Abstand zwischen dem Laserbrennpunkt und dem zu schneidenden Material richtig eingestellt werden.
Unterschiedliche Brennpunktpositionen können zu unterschiedlicher Präzision im Querschnitt des geschnittenen Materials sowie zu unterschiedlicher Bodenverschlackung und sogar zum Scheitern des Schneidens des Materials führen.
Die Wahl der Brennpunktposition für die Laserschneidmaschine hängt vom Werkstück und dem zu schneidenden Material ab.
Um die richtige Wahl zu treffen, ist es wichtig, die Laserschneiden Maschine vor dem Gebrauch, um qualitativ hochwertige Schnitte und einen ordnungsgemäßen Betrieb der Maschine zu gewährleisten.
Beim Positiv-Fokus-Schneiden befindet sich der Brennpunkt des Laserstrahls oberhalb der Materialoberfläche, wobei der Brennpunkt auf dem Werkstück liegt. Diese Methode bietet mehrere Vorteile für verschiedene Schneidanwendungen, insbesondere für das Brennschneiden von Kohlenstoffstahl und das Hochleistungslaserschneiden von dicken Blechen.
Beim Brennschneiden von Kohlenstoffstahl wird im Allgemeinen ein positiver Fokus bevorzugt, da er sich positiv auf die Schnittqualität und die Prozesseffizienz auswirkt. Das resultierende Schnittprofil weist an der Unterseite des Werkstücks eine breitere Schnittfuge auf als an der Oberseite. Diese sich verjüngende Form erleichtert die Schlackenentfernung und ermöglicht ein besseres Eindringen des Sauerstoffs in den unteren Teil des Schnitts, wodurch eine vollständige Oxidation über die gesamte Materialstärke gefördert wird.
Die Wirksamkeit des Positiv-Fokus-Schneidens kann durch Anpassung des Brennweitenbereichs weiter optimiert werden. Innerhalb bestimmter Grenzen führt eine Vergrößerung des positiven Fokusbereichs zu einer größeren Punktgröße auf der Blechoberfläche. Dieser vergrößerte Strahldurchmesser verbessert die Vorwärmung und die Wärmeverteilung um die Schnittzone, was zu glatteren und helleren Schnittflächen auf Kohlenstoffstahl führt. Die verbesserte Wärmeverteilung trägt auch zu einer gleichmäßigeren Schnittqualität und einem geringeren Risiko von Fehlern wie Krätzebildung bei.
Bei Hochleistungs-Laserschneidanwendungen, wie dem 10.000-Watt-Laserpulsschneiden von dicken Edelstahlblechen, bietet das Positiv-Fokus-Schneiden erhebliche Vorteile. Es sorgt für eine stabile Schnittqualität, indem es ein gleichmäßiges Strahlprofil über die gesamte Schnitttiefe aufrechterhält. Diese Stabilität ist besonders vorteilhaft für die Schlackenentfernung beim Schneiden dicker Bleche, da sie dazu beiträgt, dass geschmolzenes Material nicht am Boden des Schnitts anhaftet. Darüber hinaus verringert die positive Fokussierungstechnik das Risiko von Blaulichtphänomenen, die auftreten können, wenn der Laserstrahl von der Unterseite des Schnitts reflektiert wird und möglicherweise die Optik des Schneidkopfs beschädigt.
Abbildung 1 veranschaulicht den Aufbau des Positiv-Fokus-Schneidens und seine Auswirkungen auf den Schneidprozess, was die verbesserte Schnittqualität und das verringerte Risiko optischer Schäden verdeutlicht.
Abb. 1 Die Wirkung einer 12000W Laserschneiden Kohlenstoffstahl mit positivem Brennpunkt
Das Negativfokus-Schneiden ist eine fortschrittliche Laserschneidtechnik, bei der der Brennpunkt innerhalb des Werkstücks, unterhalb der Materialoberfläche, positioniert wird. Diese strategische Platzierung des Brennpunkts bietet bei bestimmten Anwendungen deutliche Vorteile.
In diesem Modus führt die tiefere Position des Brennpunkts zu einem breiteren Strahl an der Schnittfläche, wodurch eine relativ größere Schnittfugenbreite im Werkstück entsteht als beim Schneiden mit positivem Fokus. Dieser Ansatz erfordert zwar einen erhöhten Schneidgasfluss und einen höheren Energieeintrag, um eine ausreichende Temperatur während des gesamten Schnitts aufrechtzuerhalten, bietet jedoch mehrere Vorteile:
Die Anwender müssen jedoch die Vorteile des Negativfokus-Schneidens sorgfältig gegen den erhöhten Energie- und Gasverbrauch abwägen. Die richtige Optimierung der Schneidparameter, einschließlich der Laserleistung, des Hilfsgasdrucks und der Schneidgeschwindigkeit, ist entscheidend, um die Vorteile dieser Technik voll auszuschöpfen und gleichzeitig die Prozesseffizienz zu erhalten.
Abb. 2 Die Wirkung eines 6000-W-Lasers mit negativem Fokus auf rostfreien Stahl
Das Null-Fokus-Schneiden ist ein Präzisions-Laserschneidverfahren, bei dem der Brennpunkt des Laserstrahls genau auf der Oberfläche des Werkstücks positioniert wird. Diese Methode erzeugt ein ausgeprägtes Schnittprofil: Die obere Oberfläche in der Nähe des Brennpunkts weist eine relativ glatte Oberfläche auf, während die untere Oberfläche, die weiter vom Brennpunkt entfernt ist, eine vergleichsweise raue Textur aufweist.
Diese Technik wird in erster Linie für zwei wichtige Anwendungen eingesetzt:
Das Null-Fokus-Schneiden bietet mehrere Vorteile, darunter eine geringere Schnittspaltbreite, eine bessere Kantenqualität auf der Auftreffseite und die Möglichkeit, komplizierte Muster in dünne Materialien zu schneiden. Es erfordert jedoch eine präzise Steuerung der Brennweite und ist im Allgemeinen weniger geeignet für dickere Materialien, bei denen die Konsistenz über die gesamte Dicke entscheidend ist.
Abb. 3 2000-W-Laserschneiden von dünnen Kohlenstoffstahlblechen bei Nullfokus
Die Linse des 10.000-Watt-Schneidkopfes ist für die 10.000-Watt-Laserschneidmaschine von entscheidender Bedeutung. Ihre Sauberkeit wirkt sich direkt auf die Bearbeitungsleistung und die Schnittqualität der Maschine aus.
Eine verschmutzte Linse kann sich nicht nur negativ auf die Schneidergebnisse auswirken, sondern auch Schäden an den internen Komponenten des Schneidkopfes und des Laserausgangskopfes verursachen.
Eine Vorprüfung vor dem Schneiden kann schwere Schäden verhindern.
Die Methode zur Erkennung von Rotlicht ist in Tabelle 1 dargestellt.
Tabelle 1 Rotlichtnachweisverfahren
Düse | Einzelne Düse über 2mm | Saubere Linse | Verschmutzte Linse |
Methoden | 1. Rotes Licht wird angezeigt, wenn der Laser eingeschaltet ist; | ![]() | ![]() |
2. Das weiße Papier ist etwa 300 mm von der Schneidkopfdüse entfernt, um das rote Licht zu sehen; | |||
3. Wenn schwarze Flecken oder unregelmäßige schwarze Objekte im roten Licht zu sehen sind, ist die Linse verschmutzt und muss vor dem Schneiden und der Fehlersuche gereinigt werden. |
Die Koaxialität der Düsenaustrittsöffnung und des Laserstrahls ist ein entscheidender Faktor, der sich auf die Schnittqualität auswirkt. Unstimmigkeiten, die durch eine falsche Ausrichtung der Düse und des Laserstrahls verursacht werden, können zu einer unregelmäßigen Schnittfläche führen. In schweren Fällen kann der Laserstrahl auf die Düse treffen, was zu Überhitzung und Verbrennung der Düse führt.
Die Methode der koaxialen Fehlersuche ist in Tabelle 2 dargestellt.
Tabelle 2 Koaxiales Fehlersuchverfahren
Düse | Düse 1,2 mm | Normal koaxial | Abnormale koaxiale |
Werkzeuge | Klebebänder | Drei koaxiale ![]() | ![]() |
Methoden | 1. Koaxiale Einstellung im Brennpunkt 0, so dass sich der Laser in der Mitte der Düse befindet; | ||
2. Licht im Brennpunkt ±6mm; | |||
3. Wenn der Fokus 0 und der ±6mm treffende Lichtpunkt in der Mitte der Düse liegen, ist dies normal. Ist dies nicht der Fall, muss der Schneidkopf oder der Laserlichtwegversatz ausgetauscht werden. |
Die Form des Laserspots spiegelt direkt die Verteilung der Laserenergie in seitlicher Richtung wider. Die Rundheit des Flecks zeigt die Gleichmäßigkeit der Energieverteilung in verschiedene Richtungen an.
Ein stark abgerundeter Punkt mit gleichmäßiger Energieverteilung in alle Richtungen garantiert eine glatte Schnittfläche und eine gleichmäßige Schnittgeschwindigkeit in alle Richtungen, wodurch die Qualität der Schneidprodukte gewährleistet wird.
Tabelle 3 ist die Methode zur Überprüfung der Punktverteilung.
Tabelle 3 Koaxiales Fehlersuchverfahren
Düse | Einzelne Düse über 2mm | Normaler Laserspot | Abnormaler Laserpunkt |
Werkzeuge | Schwarzes Laserpunktpapier |
![]() |
![]() |
Methoden | 1. Das schwarze Laserpunktpapier ist etwa 300 mm von der Schneidkopfdüse entfernt, um einen Punkt zu erzeugen; | ||
2. Wenn im Spot schwarze Flecken zu sehen sind, ist das Objektiv verschmutzt; | |||
3. Wenn der Fleck nicht rund ist und die Mitte verschoben ist, dann ist der Laserspot schlecht verteilt |
Eines der Hauptprobleme beim Einsatz von 10.000-Watt-Lasern zum Schneiden dicker Kohlenstoffstahlplatten ist die Überhitzung der Düse. Deshalb ist es wichtig, die Düsentemperatur für verschiedene Düsengrößen und Brennpunkte bei voller Leistung zu testen, bevor der Schneidprozess beginnt.
Vor der Durchführung der Tests muss die Koaxialität so ausgerichtet werden, dass der Lichtpunkt am Düsenausgang zentriert ist. Außerdem sollte für die Düse ein Kühlgassystem zum Schneiden installiert werden.
Prüfverfahren:
Unter dem Schneidkopf sollten mit einer geeigneten Menge Wasser gefüllte Eiseneimer aufgestellt werden.
Das Hilfsgas (die Gasart und der Luftdruck sollten entsprechend den spezifischen Anforderungen für das Schneiden eingestellt werden) sollte zuerst eingeblasen werden, und der Laser sollte 30 Sekunden lang mit voller Leistung betrieben werden, um etwaige Veränderungen der Düsentemperatur zu überwachen.
Die Düsengröße sollte dann geändert und der Testvorgang wiederholt werden.
Die Wärmeentwicklung der verschiedenen Düsen sollte aufgezeichnet werden und als Referenz für die anschließende Einstellung des Schneidprozesses dienen.
Wenn die Düsentemperatur nicht innerhalb eines engen Bereichs bleibt, kann dies auf ein Problem mit dem Schneidkopf, der Düse, der Linse oder dem Laser hinweisen, und es sollte eine weitere Fehlersuche durchgeführt werden, bevor mit dem nächsten Schritt in der Einrichtung des Schneidprozesses fortgefahren wird.
Ob ein positiver oder negativer Brennpunkt für das Laserschneiden verwendet wird, hängt nicht von der Metallmaterial (z. B. nichtrostender Stahl oder Kohlenstoffstahl), sondern vielmehr auf das verwendete Schneidverfahren (z. B. Oxidationsschneiden oder Schmelzschneiden).
Verschiedene Werkstücke, die mit der Laserschneidmaschine bearbeitet werden, können unterschiedliche Fokusmuster erfordern.
Unter Berücksichtigung der unterschiedlichen Auswirkungen von positivem und negativem Fokus beim Schneiden von rostfreiem Stahl und Kohlenstoffstahl und unter Berücksichtigung der individuellen Bearbeitungsbedürfnisse können die Anwender die geeignete Fokusschneidmethode auswählen, um die Leistungsvorteile der Laserschneidmaschine voll auszuschöpfen.
Die 15-kW-Laser der verschiedenen Marken haben im Allgemeinen ähnliche Schnittergebnisse und eine ähnliche Bearbeitungseffizienz sowohl für Kohlenstoffstahl als auch für rostfreien Stahl.