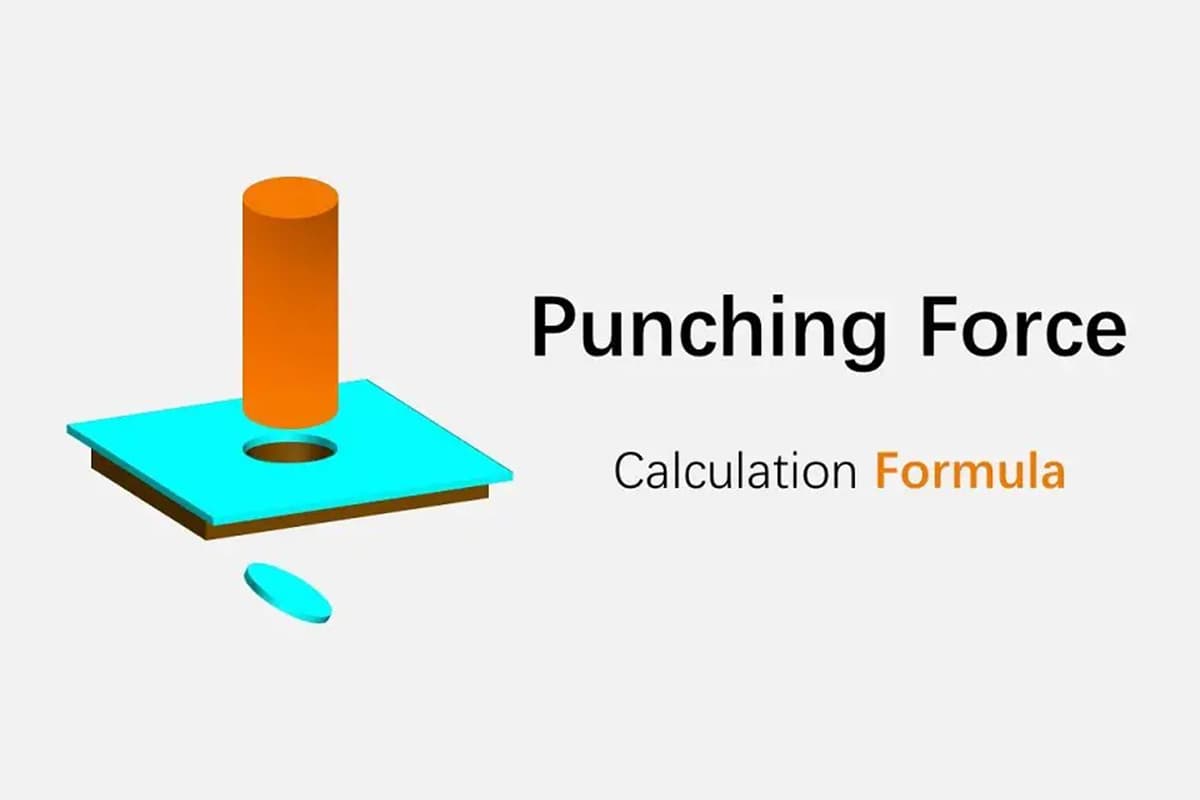
In den letzten Jahren, als die Preise für Laser und Laserschweißköpfe erheblich gesunken sind, hat die Anwendung des Laserschweißens zugenommen, und es wurde auch beim Schweißen von Schaltschränken eingesetzt. Verglichen mit dem traditionellen Lichtbogenschweißen ist das Lichtbogenschweißen von Schaltschränken weniger effizient und erfordert eine umfangreiche Nachbearbeitung des Schweißprozesses. [...]
In den letzten Jahren, als die Preise für Laser und Laserschweißköpfe erheblich gesunken sind, hat die Anwendung des Laserschweißens zugenommen, und es wurde auch beim Schweißen von Schaltschränken eingesetzt.
Im Vergleich zum traditionellen Lichtbogenschweißen ist das Lichtbogenschweißen von Schaltschränken weniger effizient und erfordert eine umfangreiche Nachbearbeitung der Schweißarbeiten.
Das Aufkommen und die Förderung der Laserschweißtechnologie hat diese Pattsituation durchbrochen und nicht nur die Effizienz des Schweißens verbessert, sondern auch die Notwendigkeit des Schleifens nach dem Schweißen beseitigt.
Die hochwertigen Schweißnähte haben einen bedeutenden Durchbruch bei der Schweißverfahren von Schaltschränken. In diesem Artikel werden die drei Schlüsseltechnologien von Schaltschränken vorgestellt Laserschweißen Einheit Integrations-, Vorrichtungs- und Laserschweißverfahren.
Beim Schweißen von Schaltschränken werden in der Regel Schweißroboter und spezielle Schweißmaschinen für die Integration der Einheiten eingesetzt.
Spezielle Schweißmaschinen sind in der Regel auf einen oder wenige Werkstücktypen ausgelegt, was zu geringer Flexibilität und hohen Kosten führt. Im Gegensatz dazu ist das Roboterschweißen flexibler, kann eine Vielzahl von Werkstückgrößen und -spezifikationen aufnehmen und ist relativ kostengünstig.
Das am häufigsten verwendete Layout ist die Zwei-Stationen-Roboter-Laserschweißanlage. Diese Einheit besteht in der Regel aus einem Sechs-Achsen-Roboter, einem Zweistationen-Drehpositionierer, einem Laser und einer Schutzkabine.
Die Beladung erfolgt manuell, das Schweißen von innen und das Be- und Entladen von außen, wodurch die Anlagenauslastung und die Produktionseffizienz verbessert werden. Dies ist derzeit die gängigste Geräteanordnung für das Schweißen von Schaltschränken.
Wie in Abbildung 1 dargestellt, ist der rotierende Positionierer in der Regel mit verstellbaren Spannvorrichtungen ausgestattet, um den Schweißanforderungen verschiedener Spezifikationen gerecht zu werden, was eine große Vielseitigkeit bietet. Je nach den unterschiedlichen Anforderungen des Kunden an den Schweißprozess können auch die in den Abbildungen 2 und 4 gezeigten Vorrichtungen konfiguriert werden.
Derzeit wird beim Schweißen von Schaltschränken in der Regel das Lichtbogenschweißen angewandt; die einzelnen Teile werden vor dem Schweißen punktgeschweißt. kontinuierliches Schweißen.
Punktschweißen wird in der Regel manuell oder mit Punktschweißvorrichtungen durchgeführt, während beim kontinuierlichen Schweißen in der Regel Roboter oder spezielle Linearmodulmaschinen mit kontinuierlichen Schweißvorrichtungen eingesetzt werden.
Das manuelle Punktschweißen stellt hohe Anforderungen an das Personal, da es sowohl den Abstand zwischen den Schweißnähten als auch die Konsistenz des Punktschweißens sicherstellen muss.
Die Qualität des Punktschweißens vor dem Schweißen beeinflusst die Maßhaltigkeit und Schweißnaht die Qualität der anschließenden Verschweißung des gesamten Gehäuses.
Punktschweißvorrichtungen werden im Allgemeinen verwendet, um den Spalt und die Qualität der Schweißnähte zu gewährleisten, aber ihre Verwendung beeinträchtigt die Schweißleistung erheblich und eignet sich nicht für das Schweißen großer Mengen.
Abbildung 5 zeigt eine Punktschweißvorrichtung für Schaltschränke, bei der die Gleitschiene manuell eingestellt wird, um mehrere Spezifikationen für das Punktschweißen von Schaltschränken zu erfüllen.
Abbildung 6 zeigt eine Vorrichtung zum kontinuierlichen Schweißen von Schaltschränken, die das punktgeschweißte Werkstück positioniert, es mit Hilfe eines Zylinders und eines Linearmoduls einspannt und das kontinuierliche Schweißen verschiedener Spezifikationen von Schaltschränken durch ein Linearmodul und ein Drehmodul realisiert.
Automatische Vorrichtungen können individuelle Teile herstellen SpannenPositionierung und automatisches Schweißen, aber sie erfordern höhere räumliche Dimensionen, strukturelle Anordnungen, Übertragung und Kontrolle.
Ein typischer Schaltschrank besteht im Allgemeinen aus drei Teilkomponenten, darunter der Schaltschrank gebogene Platte und zwei seitlichen Dichtungsplatten. Die Plattenstärke beträgt in der Regel nur 1,5 mm (je nach Hersteller unterschiedlich). Stahlplattewie in Abbildung 7 dargestellt.
Schaltschränke gibt es in vielen Spezifikationen und Größen, und alle sind dünne Bleche. Um das Laserschweißen zu realisieren, muss zunächst die interne Abstützung des gebogenen Schaltschrankblechs gelöst werden, wobei auch sichergestellt werden muss, dass die interne Abstützung Teile nach dem Schweißen vermeidet. Die interne Abstützung und die externe Pressung müssen sich automatisch an die verschiedenen Spezifikationen und Größen anpassen lassen.
Bei großen Werkstücken müssen die Probleme der mittleren Hilfsunterstützung und der Spannsteifigkeit berücksichtigt werden, ebenso wie die Lösung der Konsistenz langer Schweißnahtabstände und die wiederholte Positioniergenauigkeit der Schweißstelle des Werkstücks.
Es sollten keine übermäßig großen Nähte vorhanden sein, die zum Laser führen. Schweißfestigkeit und Qualitätsfragen.
Schließlich muss durch eine enge räumliche Strukturierung Platz für das Schweißen gelassen werden, damit der Roboter in der optimalen Haltung schweißen kann.
Abbildung 8 zeigt eine automatische Vorrichtung zum Laserschweißen von Schaltschränken, die Funktionen wie Innenunterstützung, Teilevermeidung und Außenpressung für verschiedene Schrankgrößen und -spezifikationen erfüllen kann.
Neben der Sicherstellung von Montagespalten und der Lagegenauigkeit von Schweißnähten durch Vorrichtungen muss die Werkstückstruktur entsprechend der Laserschweißverfahren Anforderungen an den Schrank.
Durch das Hinzufügen von Positionierungsrillen in der Biegeteller und der Endplatte in der Vorphase hat sich die Qualität der Schweißung des Gehäuses in der späteren Phase erheblich verbessert.
Die Größe der Rille wirkt sich jedoch auf die Qualität der nachfolgenden Schweißnähte aus. Durch Tests haben wir eine zufriedenstellende Rillengröße erreicht. Durch die Durchführung von Chargenprüfungen mit dieser Nutgröße wurden die Festigkeit und die Ästhetik der Schweißnähte den Kundenanforderungen gerecht, wie in Abbildung 10 dargestellt.
Durch den Einsatz von Laser KehlnahtschweißenDurch das Kehlnahtschweißen entfällt die Notwendigkeit des Schleifens nach dem Schweißen, was die Schweißeffizienz und die Ästhetik des Schrankes verbessert. Allerdings stellt das Kehlnahtschweißen strenge Anforderungen an den Fokusabstand und den Einfallswinkel der Schweißung.
Zahlreiche Schweißversuche haben gezeigt, dass die selbstschmelzende Hohlkehle einen großen Punkt benötigt, um die obere und untere Platte zu bedecken, so dass ein großer defokussieren. Bei gleicher Punktgröße ist die Schweißposition des 300-mm-Fokus-Schweißkopfes weiter von der Schutzscheibe entfernt, was sicherer ist.
Gleichzeitig kann der 300-mm-Fokus-Schweißkopf bei negativem Defokus mit der koaxialen Blaskomponente des 200-mm-Schweißkopfes gepaart werden, so dass die Schweißnaht auch bei großem Defokus durch Gas geschützt ist.
Ausführliche Tests haben gezeigt, dass eine Änderung des Einfallswinkels auf 35° zu den besten Schweißergebnissen führt. Abbildung 11 vergleicht die Schweißeffekte bei verschiedenen Einfallswinkeln.
(1) Das Laserschweißen des Schaltschrankgehäuses erfolgt mit einer Doppelstation Roboterlaser Schweißeinheit zum internen Schweißen und externen Be- und Entladen, wodurch die Auslastung der Anlagen und die Produktionseffizienz verbessert werden.
(2) Das Laserschweißen des Schaltschrankkörpers ist mit einer speziellen automatischen Vorrichtung ausgestattet, die alle Funktionen wie interne Unterstützung für verschiedene Spezifikationsgrößen, Teilevermeidung und externes Spannen ermöglicht.
(3) Das Laserschweißen des Schaltschrankgehäuses erfolgt mit einer Positionierungsrillenstruktur und einem Kehlnahtschweißverfahren, wodurch das Schleifen nach dem Schweißen entfällt, die Schweißeffizienz und die Ästhetik des Gehäuses verbessert werden. schlechtes Schweißen Qualität des Schaltschrankkörpers.
Als Gründer von MachineMFG habe ich mehr als ein Jahrzehnt meiner Karriere der metallverarbeitenden Industrie gewidmet. Meine umfangreiche Erfahrung hat es mir ermöglicht, ein Experte auf den Gebieten der Blechverarbeitung, der maschinellen Bearbeitung, des Maschinenbaus und der Werkzeugmaschinen für Metalle zu werden. Ich denke, lese und schreibe ständig über diese Themen und bin stets bestrebt, in meinem Bereich an vorderster Front zu bleiben. Lassen Sie mein Wissen und meine Erfahrung zu einem Gewinn für Ihr Unternehmen werden.