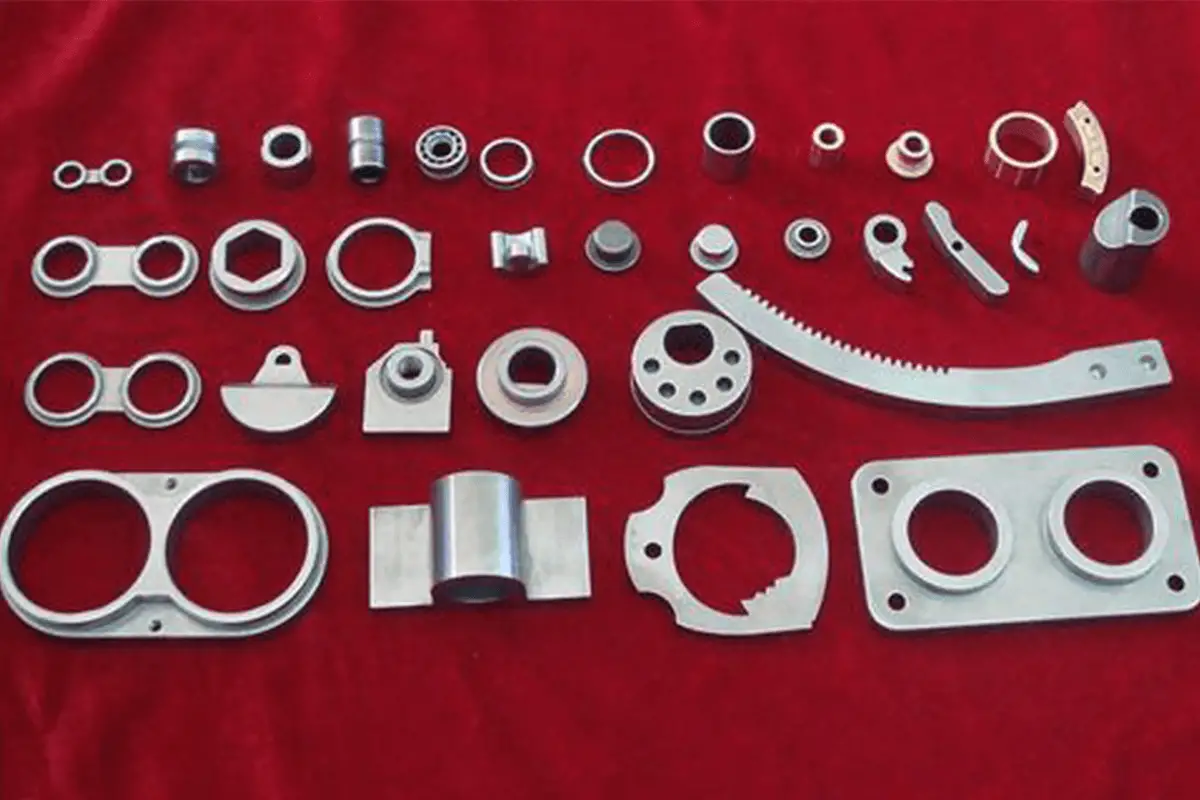
Was wäre, wenn der Schlüssel zur Herstellung des perfekten Metallpulvers in den Methoden läge, mit denen es hergestellt wird? Dieser Artikel befasst sich mit verschiedenen Verfahren zur Herstellung von Metallpulvern, von der Reduktion und Elektrolyse bis zur Zerstäubung und mechanischen Pulverisierung. Der Leser erfährt, wie sich diese Verfahren auf die Qualität und die Eigenschaften von Metallpulvern auswirken, die für Anwendungen in der Metallurgie, Elektronik und darüber hinaus unerlässlich sind. Am Ende des Buches werden Sie die Prinzipien hinter diesen Methoden verstehen und wissen, wie sie die Zukunft der Metallpulvertechnologie gestalten.
Für die Herstellung von Metall- und Metallverbindungspulvern wurden zahlreiche Verfahren entwickelt und mehrere Klassifizierungen für diese Verfahren erstellt.
Je nach Zustand des Rohmaterials können die Verfahren in feste, flüssige und gasförmige Verfahren unterteilt werden; je nach Zustand der Reaktanten können sie in nasse und trockene Verfahren eingeteilt werden; und je nach Produktionsprinzip können sie in physikalisch-chemische und mechanische Verfahren unterteilt werden.
Im Allgemeinen sind bei den physikalisch-chemischen Methoden die wichtigsten die Reduktion, die Reduktionskombination und die Elektrolyse, während bei den mechanischen Methoden die Zerstäubung und die mechanische Zerkleinerung im Vordergrund stehen.
Die Wahl des Verfahrens zur Herstellung von Metallpulver hängt vom Rohstoff, der Art des Pulvers, den Leistungsanforderungen an das Pulvermaterial und der Effizienz der Pulverherstellung ab.
Mit der zunehmenden Verbreitung von pulvermetallurgischen Produkten werden die Anforderungen an die Größe, Form und Leistung von Pulverpartikeln immer höher.
Daher wird die Technologie der Pulveraufbereitung ständig weiterentwickelt und erneuert, um den Anforderungen an Partikelgröße und Leistung gerecht zu werden.
2.1.1 Reduktionsmethode
Die Reduktion von Metalloxiden und -salzen ist eine weit verbreitete Methode der Pulverherstellung. Feste Kohle kann zur Reduktion von Eisen- und Wolframpulver verwendet werden, während Wasserstoff oder zersetzter Ammoniak zur Herstellung von Wolfram-, Molybdän-, Eisen-, Kupfer-, Kobalt- und Nickelpulvern eingesetzt wird.
Eisenpulver kann auch aus umgewandeltem Erdgas und Kohlegas hergestellt werden. Natrium, Kalzium, Magnesium und andere Metalle können als Reduktionsmittel zur Herstellung von Tantal und Niob dienen, Titan, Zirkonium, Thorium, Uran und andere seltene Metallpulver.
Das Grundprinzip dieser Reduktionsmethode besteht darin, dass die Affinität des verwendeten Reduktionsmittels für Sauerstoff größer ist als die des Metalls im Oxid oder Salz, wodurch die Reduktion des Metalls durch Einfangen des Sauerstoffs im Metalloxid oder -salz ermöglicht wird.
Da verschiedene Metallelemente unterschiedlich mit Sauerstoff reagieren, variiert auch die Stabilität der entstehenden Oxide. Der Grad der Stabilität des Oxids kann durch die Größe von ΔG während des Oxidationsprozesses charakterisiert werden. Je kleiner der ΔG-Wert während der Reaktion ist, desto höher ist die Stabilität des Oxids, was auf eine größere Affinität zu Sauerstoff hinweist.
Zu den Vorteilen dieses Verfahrens gehören seine Einfachheit, die leichte Kontrolle der Prozessparameter, die hohe Produktionseffizienz und die niedrigen Kosten, wodurch es sich für die industrielle Produktion eignet.
Sie ist jedoch nur anwendbar auf metallische Werkstoffe die leicht mit Wasserstoff reagieren und nach der Wasserstoffaufnahme spröde und bruchanfällig werden.
2.1.2 Thermische Metallreduktion und Reduktions-Kombinationsverfahren
Bei der thermischen Metallreduktion werden Rohstoffe reduziert, die fest, gasförmig oder sogar geschmolzen sein können, wobei die beiden letzteren die Merkmale der Gasphasenreduktion und der Flüssigphasenausfällung aufweisen.
Zu den üblichen industriellen Anwendungen der thermischen Metallreduktion gehören die Verwendung von Kalzium zur Reduktion von TiO2, ThO2, UO2 und anderen; Magnesium zur Reduktion von TiCl4, ZrCl4, TaCl5 und anderen; Natrium zur Reduktion von TiCl4, ZrCl4, K2ZrF6, K2TaF7 und anderen; und Kalziumhydrid (CaH2) zur Co-Reduktion von Chromoxid und Nickeloxid für die Herstellung von rostfreiem Nickel-Chrom-Stahlpulver.
Die Reduktions-Kombinations-Methode bezieht sich auf den Prozess der Gewinnung von Carbiden und Boriden durch die Reaktion von Kohlenstoff, Borkarbid, Silizium, Stickstoff und refraktären Metalloxiden.
2.1.3 Elektrolyseverfahren
Bei der Elektrolyse werden Metallpulver an der Kathode durch Elektrolyse von geschmolzenen Salzen oder deren wässrigen Lösungen abgeschieden. Fast alle Metallpulver können durch Elektrolyse hergestellt werden, wobei Kupfer-, Silber- und Zinnpulver besonders geeignet sind.
Die Elektrolyse kann weiter unterteilt werden in Elektrolyse mit wässrigen Lösungen, Elektrolyse mit organischen Elektrolyten, Elektrolyse mit geschmolzenem Salz und Elektrolyse mit Flüssigmetallkathoden.
Der Vorteil dieser Methode besteht darin, dass sie Metallpulver mit hoher Reinheit erzeugt, in der Regel mit einer Reinheit von 99,7% oder mehr für Einzelelement-Pulver. Darüber hinaus kann die Elektrolyse die Partikelgröße genau steuern, was die Herstellung von ultrafeinen Pulvern ermöglicht.
Die Elektrolysemethode verbraucht jedoch viel Strom, was zu höheren Kosten bei der Pulverherstellung führt. Mit der wässrigen Elektrolyse können Cu-, Ni-, Fe-, Ag-, Sn-, Fe-Ni- und andere Metall(legierungs)pulver hergestellt werden, während mit der Salzschmelzelektrolyse Zr-, Ta-, Ti-, Nb- und andere Metallpulver produziert werden können.
2.1.4 Hydroxyl-Methode
Bestimmte Metalle (wie Eisen, Nickel usw.) werden mit Kohlenmonoxid zu Metallcarbonylverbindungen synthetisiert, die dann thermisch zu Metallpulver und Kohlenmonoxid zersetzt werden.
Das dabei entstehende Pulver ist extrem fein und rein, aber das Verfahren ist kostspielig. In der Industrie wird es vor allem zur Herstellung von feinen und ultrafeinen Nickel- und Eisenpulvern sowie von Legierungspulvern aus Fe-Ni, Fe-Co, Ni-Co und anderen verwendet.
2.1.5 Chemische Verdrängungsmethode
Die chemische Verdrängungsmethode basiert auf der Reaktivität von Metallen, wobei ein reaktiveres Metall ein weniger aktives Metall aus seiner Salzlösung verdrängt und ein Metall (Metallpulverpartikel) erzeugt, das mit anderen Methoden weiter veredelt wird.
Diese Methode wird hauptsächlich bei der Herstellung von Pulvern aus weniger aktiven Metallen wie Cu, Ag und Au eingesetzt.
2.2.1 Zerstäubungsmethode
Das Zerstäubungsverfahren ist ein mechanisches Verfahren zur Herstellung von Pulver, bei dem flüssige Metalle oder Legierungen direkt pulverisiert werden, um Pulver zu erzeugen. Es ist weit verbreitet und steht in der Größenordnung nach dem Reduktionsverfahren an zweiter Stelle.
Diese auch als Sprühverfahren bekannte Methode kann zur Herstellung von Metallpulvern wie Blei, Zinn, Aluminium, Kupfer, Nickel und Eisen verwendet werden. Es kann auch für die Herstellung von Legierungspulvern wie Bronze, Messing, Kohlenstoffstahl und Eisen verwendet werden. legierter Stahl.
Bei der Zerstäubung werden im Allgemeinen Hochdruckgas, Hochdruckflüssigkeit oder mit hoher Geschwindigkeit rotierende Schaufeln verwendet, um geschmolzenes Metall oder Legierungen bei hohen Temperaturen und hohem Druck in winzige Tröpfchen zu zerschlagen. Diese Tröpfchen kondensieren dann in einem Sammelbehälter, um ultrafeines Metallpulver zu bilden, ein Prozess, der keine chemischen Veränderungen beinhaltet.
Die Zerstäubung ist eine der wichtigsten Methoden zur Herstellung von Metall- und Legierungspulvern. Es gibt viele Zerstäubungsmethoden, z. B. Zweistromzerstäubung, Zentrifugalzerstäubung, mehrstufige Zerstäubung, Ultraschallzerstäubungstechnologie, eng gekoppelte Zerstäubungstechnologie, Hochdruckgaszerstäubung, Laminarstromzerstäubung, eng gekoppelte Ultraschallzerstäubung und Heißgaszerstäubung.
Zerstäubtes Pulver hat Vorteile wie einen hohen Sphärizitätsgrad, eine kontrollierbare Pulverkörnigkeit, einen geringen Sauerstoffgehalt, niedrige Produktionskosten und die Anpassungsfähigkeit an die Herstellung von verschiedenen Metallpulvern.
Sie hat sich zur wichtigsten Entwicklungsrichtung für die Aufbereitungstechnologie von Hochleistungs- und Speziallegierungspulvern entwickelt. Die Zerstäubung hat jedoch Nachteile wie eine geringe Produktionseffizienz, eine geringe Ausbeute an ultrafeinem Pulver und einen relativ hohen Energieverbrauch.
2.2.2 Mechanische Pulverisierungsmethode
Die mechanische Pulverisierung von festen Metallen ist eine besondere Methode der Pulverherstellung, die eng mit dem Endzustand der festen Dehnung und der Bildung und Ausdehnung von Rissen während der Pulverisierung verbunden ist.
Darüber hinaus dient sie als unverzichtbares Komplementärverfahren für einige Pulverherstellungsverfahren, wie z. B. die Zerkleinerung von elektrolytisch erzeugten spröden Kathodenausscheidungen oder die Zerkleinerung von durch Reduktion erzeugten schwammartigen Metallbrocken. Daher nimmt die mechanische Pulverisierung einen wichtigen Platz in der Pulverherstellung ein.
Je nach Beschaffenheit der Materialien und dem erforderlichen Zerkleinerungsgrad variiert die Zerkleinerungsmethode.
Je nach Art der Krafteinwirkung von außen erfolgt die Materialzerkleinerung im Allgemeinen durch Kompression, Schlag, Zerkleinerung und gezielte Spaltung. Die Funktionsprinzipien der verschiedenen Zerkleinerungsgeräte beruhen auf diesen Methoden.
Beim Kugelmahlen werden vor allem rollende Kugeln und vibrierende Kugeln eingesetzt. Fräsverfahren. Diese Methode nutzt den Mechanismus, bei dem Metallpartikel durch Verformung bei unterschiedlichen Dehnungsgeschwindigkeiten in feinere Substanzen zerfallen.
Zu den Vorteilen gehören die geringe Materialselektivität, der kontinuierliche Betrieb, die hohe Produktionseffizienz und die Eignung für die Trocken- und Nassvermahlung, was die Herstellung von verschiedenen Metall- und Legierungspulvern erleichtert. Der Nachteil ist, dass die Klassifizierung während des Pulveraufbereitungsprozesses relativ schwierig ist.
2.2.3 Schleifverfahren
Beim Mahlen wird komprimiertes Gas durch eine spezielle Düse in den Mahlbereich geleitet, wodurch die Materialien in diesem Bereich zusammenstoßen und zu Pulver zermahlen werden.
Der expandierte Luftstrom steigt zusammen mit den Materialien in die Klassierzone auf, wo ein Turbinensichter die Materialien, die die gewünschte Körnung erreicht haben, trennt.
Das verbleibende grobe Pulver kehrt in den Mahlbereich zurück, wo es weiter gemahlen wird, bis es die für die Trennung erforderliche Körnung erreicht. Da es sich bei dem Mahlverfahren um einen trockenen Prozess handelt, entfällt die Notwendigkeit einer Materialentwässerung und eines Trocknungsvorgangs.
Das resultierende Produkt ist von hoher Reinheit, großer Aktivität und guter Dispergierbarkeit, mit feiner Körnung und einem engen Verteilungsbereich. Die Partikel haben eine glatte Oberfläche und werden in der Industrie, z. B. bei Nichtmetallen, chemischen Rohstoffen, Pigmenten, Schleifmitteln, Pharmazeutika und anderen Produkten zur Feinstzerkleinerung eingesetzt.
Das Mahlverfahren hat jedoch einige Nachteile, wie z. B. hohe Herstellungskosten für die Ausrüstung, und bei der Herstellung von Metallpulver ist eine kontinuierliche Zufuhr von Inertgas oder Stickstoff als Druckgasquelle erforderlich, was zu einem erheblichen Gasverbrauch führt.
Sie ist daher nur für die Zerkleinerung und Pulverisierung von spröden Metallen und Legierungen geeignet.
Mit dem technologischen Fortschritt wurden Metallpulver entwickelt und in Bereichen wie Metallurgie, Chemietechnik, Elektronik, magnetische Werkstoffe, Feinkeramik und Sensoren eingesetzt, die vielversprechende Anwendungsmöglichkeiten bieten.
Bei Metallpulvern geht der Trend zu höherem Reinheitsgrad und zur Entwicklung von ultrafeinen (Nano-)Pulvern. Obwohl es verschiedene Methoden zur Herstellung ultrafeiner Metallpulver gibt, hat jede Methode ihre Grenzen und es gibt viele Probleme, die gelöst und perfektioniert werden müssen.
Die derzeit am weitesten verbreiteten Verfahren zur Herstellung von Metallpulvern sind Reduktion, Elektrolyse und Zerstäubung.
Darüber hinaus haben Verbesserungen der traditionellen Produktionsverfahren zu vielen neuen Produktionstechniken und -methoden geführt, wie z. B. Ultraschallzerstäubung, Rotationsscheibenzerstäubung, Zwei- und Dreiwalzenzerstäubung, mehrstufige Zerstäubung, Plasma-Rotationselektrodenverfahren und Lichtbogenverfahren.
Von den Methoden zur Herstellung von Metallpulvern sind zwar viele in die Praxis umgesetzt worden, aber es gibt immer noch zwei Hauptprobleme: Der Maßstab ist klein und die Produktionskosten sind hoch.
Um die Entwicklung und Anwendung von Metallpulverwerkstoffen voranzutreiben, ist es notwendig, verschiedene Verfahren umfassend zu nutzen, ihre Stärken zu nutzen und ihre Schwächen auszugleichen sowie Verfahren zu entwickeln, die größere Produktionsmengen und geringere Kosten ermöglichen.