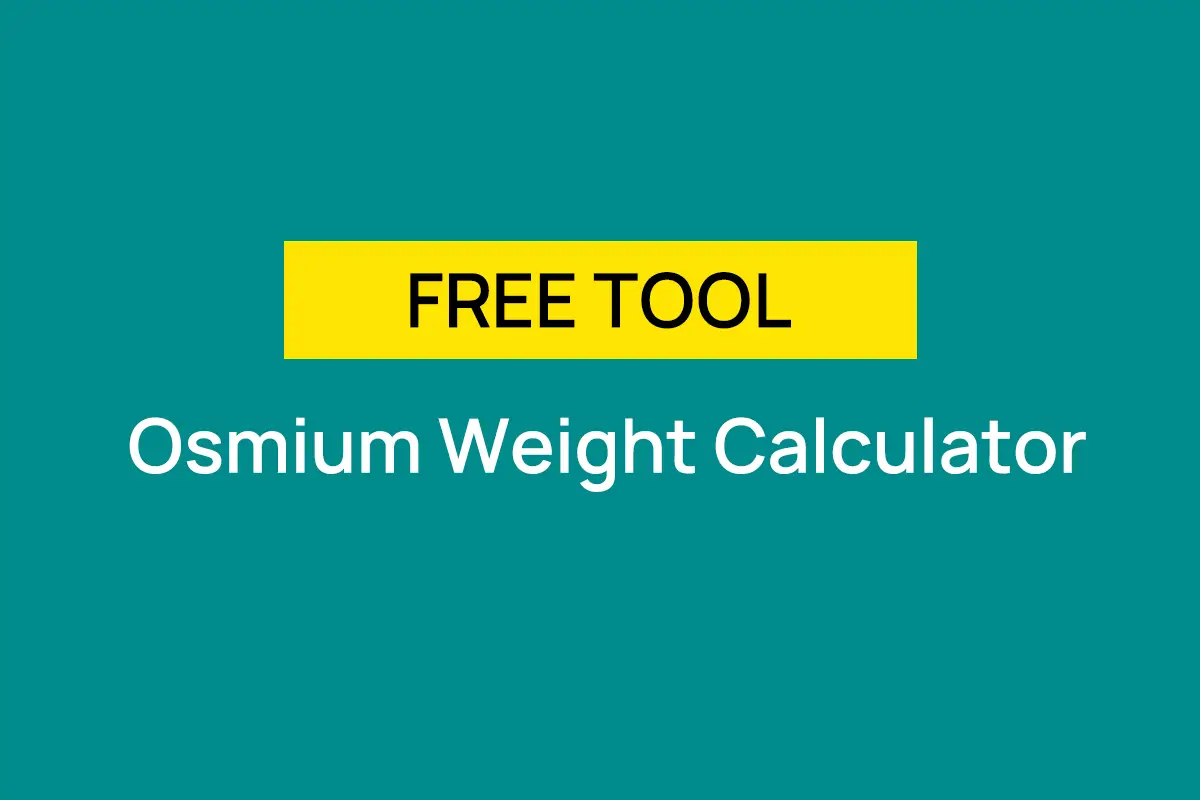
Warum versagen Metallteile nach der Wärmebehandlung manchmal unerwartet? Dieser Artikel befasst sich mit dem Phänomen der Mischkristalle und erklärt ihre Entstehung, die Rolle der Entmischung von Legierungselementen und die Verformung während der Herstellung. Wenn Sie diese Faktoren verstehen, erhalten Sie einen Einblick in die Vermeidung von Frühausfällen bei Metallteilen.
Während des Wärmebehandlungsprozesses kam es zu einem Bruch, und bei der Untersuchung wurde festgestellt, dass die Ursache das Vorhandensein von Mischkristallen war. Mischkristalle sind ein häufiger Befund bei der metallografischen Untersuchung nach dem Wärmebehandlungsprozess in der mechanischen Fertigungsindustrie. Heute wollen wir über Mischkristalle sprechen.
Mischkristalle sind, wie der Name schon sagt, eine Mischung aus verschiedenen Korngrößen. Die Korngröße ist ein Maß für die Zähigkeit metallischer Werkstoffe, wobei eine größere Korngröße zu einer höheren Zähigkeit des Materials führt und eine kleinere Korngröße zu einer geringeren Zähigkeit.
Wenn minderwertige Körner mit hochwertigen Körnern vermischt werden, verringert sich die Gesamtleistung des Metallmaterials. Je größer der Anteil an minderwertigen Körnern ist, desto instabiler ist die Gesamtleistung des Werkstoffs.
In der Regel wird von Mischkorn gesprochen, wenn das Gefüge Körner mit unterschiedlichen Größen enthält, die sich um 3-4 Stufen unterscheiden. Wenn der Anteil der großen Körner 10% übersteigt, muss man sich vor dem frühzeitigen Versagen mechanischer Teile in Acht nehmen, das durch die großen Körner verursacht werden kann.
Die unvorhersehbare Natur von Mischkristallen macht sie zu einem Problem für Wärmebehandler, da es unmöglich ist, vorherzusagen, wann mechanische Teile versagen könnten. Das Bild unten zeigt das metallographische Bild von Mischkristallen.
Es gibt zwei Hauptgründe für Mischkristalle:
A. Segregation von Legierungselementen (ungleichmäßige Verteilung von Legierungselementen)
B. Kritische Verformung (Stahl verformt, Korn verändert)
Ausgehend von diesen beiden Gründen beginnt sie mit der Stahlverhüttung.
Es ist allgemein bekannt, dass bei der Stahlverhüttung Eisenerz und verschiedene Rohstoffe verwendet werden, um schließlich in einer komplexen Reihe von Schritten geschmolzenen Stahl zu erzeugen, der dann zu Blöcken gegossen wird. Stahlwerke sind die professionellsten im Entstehungsprozess von geschmolzenem Stahl, und da die flüssige Phase des geschmolzenen Stahls von Natur aus einheitlich ist, wird hier keine Bewertung vorgenommen. Stattdessen werden wir uns auf den Prozess der Erstarrung von flüssigem Stahl zu Blöcken konzentrieren.
Die Barrentrennung ist die am weitesten verbreitete Form der Entmischung.
Die Ursache für die Entmischung des Barrens ist einfach ausgedrückt: Die Legierungselemente tendieren dazu, während des Erstarrungsprozesses zuerst zu erstarren, während die Bereiche mit weniger Legierungselementen später erstarren, was zu einer ungleichmäßigen Verteilung der Legierungselemente führt.
Die typischste metallurgische Struktur, die durch diesen Prozess entsteht, ist die Dendritensegregation.
Es gibt auch Verunreinigungen, wie z. B. Schlackeneinschlüsse, die sich während des Walzens und Abkühlens von geschmolzenem Stahl an einer bestimmten Stelle ansammeln.
Das Hauptproblem bei der Seigerung ist die ungleichmäßige Verteilung der Legierungselemente, einschließlich Kohlenstoff, Chrom, Nickel, Molybdän, Aluminium und anderer.
Diese ungleichmäßige Verteilung führt zu getrennten Regionen mit unterschiedlichen chemischen Zusammensetzungen, die jeweils als eigenständige Regionen betrachtet werden können. Stahlsorte.
In diesem Stadium können diese Regionen als separate Körner identifiziert werden, die sich von den Mischkörnern unterscheiden. Ist das jetzt klarer?
Das Walzen ist ein Verfahren, bei dem ein Block in seine endgültige Form, z. B. als Stab, Blech, Walzdraht oder Profilstahl, gebracht wird.
Die Stahlbarren wird zunächst erwärmt und dann in mehreren Durchgängen gewalzt, bis es den gewünschten Spezifikationen entspricht.
Vor dem Walzen wird der Stahl in der Regel einer Diffusionsglühen.
Der Zweck des Diffusionsglühens besteht darin, die Legierungselemente im Stahl zu homogenisieren. Wie bereits erwähnt, führt die Entmischung von Legierungselementen während der Erstarrung zu einer ungleichmäßigen Zusammensetzung, die zu Problemen führen kann.
Um dieses Problem zu lösen, wird der Stahl einem Diffusionsglühen bei einer Temperatur von etwa 1200 °C unterzogen.
Bei dieser Temperatur nimmt die Aktivität der Legierungselemente zu, und es findet eine Diffusion innerhalb des Stahls statt, die von Bereichen mit hoher Konzentration zu Bereichen mit niedriger Konzentration führt, wodurch die Gleichmäßigkeit des Stahls verbessert wird.
Dabei bleibt der Stahl in einem festen Zustand und ist noch nicht in eine flüssige Phase übergegangen.
Auch wenn sich die Legierungselemente verschoben haben, verbessern sie nur die Gleichmäßigkeit des Stahls und können die Entmischung nicht vollständig beseitigen.
Das Walzen ähnelt den Verfahren des Schmiedens und Strangpressens.
Während dieses Prozesses wird der Stahl erhitzt, geschmiedet, stranggepresst, abgekühlt, rekristallisiert, geglüht, erneut stranggepresst und anderen Verfahren unterzogen.
Einige Fehler des ursprünglichen Stahls werden während dieses Prozesses allmählich reduziert, und auch der Grad der Entmischung der Legierungselemente nimmt ab.
Im Idealfall eliminieren diese Prozesse Fehler und verringern die Entmischung, aber in der Realität haben in Stahlwerken Kosteneinsparungen und Effizienz Vorrang.
Um dies zu erreichen, können sie die Temperatur und die Dauer des Diffusionsglühens herabsetzen, das Glühen auslassen oder das Schmiedeverhältnis während des Walzens erhöhen, was Fehler verdecken, aber nicht beseitigen kann und zu einer noch stärkeren Seigerung während des Walzens führt.
Diese Änderung wird im nächsten Abschnitt ausführlich beschrieben.
Nach der Annahme des Stahls verwendet die mechanische Verarbeitungsanlage in der Regel Warmumformung und Kaltfließpressverfahren, um das Werkstück zu formen, und schließt dann die Bearbeitung, Wärmebehandlung und das Schleifen ab, um das Endprodukt herzustellen.
Bei diesem Prozess können jedoch Probleme auftreten.
Warmumformung ähnelt dem in Abschnitt 2 erwähnten Stahlwalzen, jedoch mit anderen Anlagen, Verdichtungsverhältnissen und Produktstrukturen.
Beim Kaltfließpressen hingegen wird die Zähigkeit des Stahls genutzt, um eine plastische Verformung ohne Erhitzung zu erreichen.
Bei beiden Verfahren geht es um plastische Verformung.
Die Zähigkeit eines Metalls bezieht sich auf seine Verformungsfähigkeit, die in der Regel als seine Fähigkeit, sich zu dehnen oder zu stauchen, verstanden wird.
Je höher die Zähigkeit, desto größer die Dehnbarkeit und desto geringer die Stauchbarkeit.
Was passiert mit den Körnern bei Zug oder Druck? Betrachten Sie ein Gummiband.
Wenn der Durchmesser eines Gummibandes zunächst 10 mm beträgt und es auf das 10-fache seiner Länge gedehnt wird, was passiert dann mit seinem Durchmesser?
Er wird sicherlich nicht 1 mm dick, aber um das Problem zu verdeutlichen, weiß jeder, dass er dünner wird. Wenn man ihn weiter dehnt, wird er noch dünner, bis er bricht.
Die Verformung von Metall ist ein Prozess der Kornveränderung.
Vor der Verformung haben die Körner eine unregelmäßige Form, die jedoch im Wesentlichen die Form einer Kugel hat.
Bei Einwirkung einer äußeren Kraft werden die Körner wie ein Gummiband gedehnt und ihr Raum wird zusammengedrückt. Sie werden immer dünner, je länger die äußere Kraft anhält.
Früher waren sie ein Haufen Kartoffeln, aber jetzt sind sie ein Bündel Weizenhalme geworden.
Während dieses Prozesses scheinen die Körner unverändert zu sein, aber bei näherer Betrachtung ist ihre Größe viel kleiner geworden.
Es ist wichtig, sich vor Augen zu halten, dass der Schein trügen kann und sich nicht von dem, was auf der Oberfläche zu sehen ist, täuschen zu lassen.
Bei der Wärmebehandlung handelt es sich um einen Zwischenprozess, den man nicht sehen oder anfassen kann und der nicht sofort erkannt oder während des Prozesses eingestellt werden kann.
Der Zustand des Produkts kann nur durch Prozesskontrolle und Endkontrolle festgestellt werden.
Die Probleme, die bei allen bisherigen Verfahren aufgetreten sind, werden jedoch bei der Wärmebehandlung deutlich.
Bei der Wärmebehandlung müssen Aufkohlung und Abschreckung über die Austenitisierungstemperatur des Stahls hinaus erwärmt werden.
Daher muss das Werkstück auf eine Temperatur über AC3 erhitzt werden, damit der Vorgang stattfinden kann. Während dieses Prozesses treten mehrere wichtige Veränderungen auf.
Das kubisch-raumzentrierte Ferritgitter wandelt sich in das kubisch-flächenzentrierte Gitter um Austenit Gitter und die Menge an gelöstem Kohlenstoff, inkorporierten Legierungselementen und die Diffusion von Legierungselementen treten während dieses Prozesses auf.
Auch die Grenzen zwischen den Körnern werden aufgebrochen und rekristallisiert, wodurch sich die ursprünglichen Körner verändern und umgestaltet werden.
Der Prozess der Kornrekombination ist im Wesentlichen ein Energiewettbewerb, ähnlich wie die derzeitige internationale Situation, in der die Größe eines Landes durch seine Hightech-, Atomwaffen- und Kampffähigkeiten bestimmt wird.
Je stärker ein Land ist, desto größer wird es, während ein schwächeres Land eher zur Zersplitterung neigt.
In ähnlicher Weise wirken Karbide, die von Legierungselementen gebildet werden, als Bollwerke in den Körnern und behindern deren Wachstum.
In Gebieten, in denen Legierungselemente knapp sind, sind sie unaufhaltsam und ihr Territorium dehnt sich aus, so dass die Körner wachsen.
Um die gewünschte Verformungsgröße des Produkts zu gewährleisten, muss die Erwärmungstemperatur auf einem moderaten Niveau gehalten werden, um das Diffusionsverhalten der Legierungselemente zu begrenzen.
Ist die Erwärmungstemperatur zu hoch, kann es zu einer fehlenden Phasenumwandlung kommen, und wenn die Temperatur zu niedrig ist, um die erforderliche Austenitisierung zu erreichen, führt dies ebenfalls zu einer fehlenden Phasenumwandlung.
Daher erfordert das Erhitzungsproblem bei der Wärmebehandlung eine Erhitzung bei mittlerer Temperatur, die stark eingeschränkt ist.
Normalerweise liegt die Aufkohlungstemperatur bei 900-940°C und die Abschrecktemperatur 30-50°C über der AC3-Temperatur.
Dies sind Werte wie aus dem Lehrbuch. Betrachten wir nun die möglichen Folgen der vorangegangenen Abschnitte bei diesen Temperaturen.
a. Auswirkung der Entmischung der Legierungselemente:
Mit dem Fortschreiten des Austenitisierungsprozesses weisen verschiedene Bereiche unterschiedliche Gehalte an Legierungselementen auf, was zu unterschiedlichen Austenitisierungstemperaturen in diesen Bereichen führt.
Auch wenn das Werkstück die gleiche Temperatur erreicht, haben einige Bereiche bereits mit der Austenit Umstellung, während sich andere noch in der Vorbereitungsphase befinden.
In einigen Bereichen ist die Umwandlung in Austenit abgeschlossen, in anderen noch nicht, so dass in den Bereichen, die sich bereits in Austenit umgewandelt haben, kontinuierlich Körner wachsen, während in den Bereichen, in denen die Umwandlung noch nicht abgeschlossen ist, feine Körner entstehen.
Wird die Austenitisierung an diesem Punkt gestoppt und schnell abgekühlt, kommt es zu einer Koexistenz von großen und kleinen Körnern, und in schweren Fällen können sich Mischkörner bilden.
Die meisten Legierungselemente, wie V, Ti, Nb usw., behindern das Kornwachstum.
Legierungselemente wie Cr, Mo, W usw. verlangsamen die Bildung von Austenit.
Diese Elemente können die Korngröße beeinflussen und spielen eine Rolle bei der Verfeinerung der Körner.
Andererseits gibt es einige Elemente, wie Mn und P, die das Wachstum von Getreide fördern können.
Wenn sich diese Elemente im Stahl stark entmischen, kann es zu Mischkristallen kommen.
b. Einfluss der Verformung beim Walzen, Schmieden und Kaltumformen:
Beim Ziehen und Strangpressen werden die Körner verformt, wodurch sich die Energie an den ursprünglichen Korngrenzen verringert.
Mit steigender Erwärmungstemperatur rekombinieren die Körner, wenn die Rekristallisationstemperatur des Stahls erreicht ist.
Zu diesem Zeitpunkt wird die Energie des Legierungselements größer, und zwei benachbarte dünne Körner können leicht verschmelzen.
Elemente, die sich bisher nur innerhalb eines einzelnen Korns bewegen konnten, können nun die beiden Korngrenzen durchbrechen und eine Abkürzung nehmen, um die beiden dünnen Körner in sehr kurzer Zeit zu einem großen Korn zu verschmelzen.
Wenn sich die Erhitzungstemperatur und die Zeit weiter ändern, wachsen diese Körner weiter, bis keine Energie mehr vorhanden ist, um die Korngrenzen zu durchbrechen.
Zu diesem Zeitpunkt haben sich viele große Körner gebildet.
Allerdings wachsen nicht alle verformten Körner bis zu der für das Wachstum erforderlichen kritischen Verformung. Dadurch entstehen einige normale Körner, was zur Bildung von Mischkörnern führt.
C. Einfluss der Temperatur:
Das Schmiedeverfahren sowie die Temperatur und die Dauer der Wärmebehandlung haben einen erheblichen Einfluss auf das Korn.
Wenn die Temperatur hoch und die Haltezeit lang ist, wachsen die Körner.
Diese Temperaturgrenze hängt vom Material ab, und verschiedene Materialien haben unterschiedliche Grenztemperaturen.
Die Wärmebehandlungstemperaturen sind in der Regel festgelegt, und die typische Aufkohlungstemperatur liegt nicht über 950 °C.
Bei dieser Temperatur kommt es bei den meisten Feinkornstählen zu keinen nennenswerten Veränderungen.
Eine zu hohe Temperatur aufgrund von Parameterfehlern oder ungenauer Temperaturmessung kann jedoch zu grobkörnigem Stahl führen.
Die durch das Schmieden bei Übertemperatur erzeugten Körner sind grob, und in der Metallographie nach dem Schmieden ist häufig eine Widmanstatten-Struktur zu erkennen.
Widmanstatten können durch mehrmaliges Normalisieren beseitigt werden, und die temperaturbedingte Kornveränderung kann durch Normalisieren kompensiert werden.
Es wird jedoch generell nicht empfohlen, eine Widmanstatten-Struktur zu verwenden, wenn sie in der Realität auftritt.
Zusammenfassend lässt sich sagen, dass der Hauptgrund für Mischkristalle die Entmischung der Elemente ist und dass es schwierig ist, sie durch Wärmebehandlung in späteren Prozessen zu beseitigen.
Darüber hinaus ist es von entscheidender Bedeutung, bei allen Verfahren, die zu Verformungen führen, auf die Korngröße zu achten.
Die allein durch die Verformung verursachte Korngrößenmischung kann durch eine Wärmebehandlung verbessert werden.
Wenn das Korn jedoch bereits gewachsen und stabilisiert ist und sich die Legierungselemente an der Korngrenze abgeschieden haben, kann es schwierig sein, dieses Problem zu lösen.