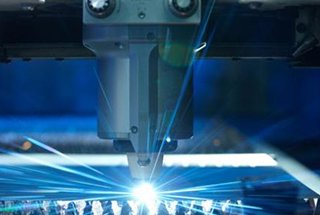
Wie entscheiden Sie sich für das Plasma-Auftragschweißen oder das Laser-Auftragschweißen für Ihre industriellen Anforderungen? In diesem Artikel werden die technischen, gerätetechnischen und verfahrenstechnischen Merkmale der beiden Verfahren aufgeschlüsselt und ihre Vor- und Nachteile klar verglichen. Ganz gleich, ob Sie Kosteneffizienz oder höchste Präzision anstreben, dieser Leitfaden wird Ihnen helfen, die wichtigsten Unterschiede zu verstehen und eine fundierte Entscheidung zu treffen. Tauchen Sie ein und erfahren Sie, wie jede Verkleidungsmethode für Ihre spezifischen Anwendungen von Nutzen sein kann und welche Faktoren Sie für optimale Ergebnisse berücksichtigen müssen.
Das wichtigste Merkmal des Laserstrahl-Auftragschweißens ist die konzentrierte Wärme, die schnelle Erwärmung, die schnelle Abkühlung und die kleine Wärmeeinflusszone. Es hat unvergleichliche Eigenschaften für die Fusion zwischen verschiedenen Materialien.
Dieser spezielle Erwärmungs- und Abkühlungsprozess führt zu einer Struktur im Gussbereich, die sich von anderen Beschichtungsmethoden (wie z. B. Sprühschweißen, Auftragschweißen, normales Schweißen usw.) unterscheidet und sogar amorphe Strukturen erzeugen kann, insbesondere bei gepulsten Lasern.
Dies ist der so genannte Grund für das Laserstrahl-Auftragschweißen ohne Glühen und Verformung. Aber ich glaube, das gilt nur aus der Makroperspektive des gesamten Werkstücks. Wenn Sie eine mikroskopische Analyse der Plattierungsschicht durchführen und Wärmeeinflusszonewerden Sie eine weitere Szene sehen.
Derzeit gibt es zwei Arten von Maschinen, die in Laserstrahl-Auftragschweißen in China: CO2-Laser und YAG-Laser. Erstere haben eine kontinuierliche Leistung mit einer Beschichtungsleistung von in der Regel über 3KW, während der YAG-Laser eine gepulste Leistung von in der Regel etwa 600W hat.
Die Geräte sind für den allgemeinen Benutzer schwer zu verstehen und hängen stark vom Service des Herstellers ab. Der Anschaffungspreis ist teuer, die Wartungskosten und der Preis für Ersatzteile sind hoch.
Darüber hinaus bleiben die Stabilität und die Haltbarkeit der Geräte im Allgemeinen hinter denen ausländischer Hersteller zurück.
Daher werden Laserstrahl-Auftragsschweißmaschinen in der Regel in speziellen Bereichen eingesetzt, und es ist schwierig, in allgemeinen industriellen Fertigungs- und Wartungsbereichen kosteneffektiv zu sein.
(1) Vorläufige Behandlung
Beim Laserstrahl-Auftragschweißen ist es im Allgemeinen nur erforderlich, das Werkstück sauber zu polieren, Öl und Rost zu entfernen, die Ermüdungsschicht zu entfernen usw., was relativ einfach ist.
(2) Pulverzufuhr
CO2-Laser haben eine höhere Leistung und verwenden in der Regel Argon für die Pulverzufuhr; YAG-Laser haben eine geringere Leistung und verwenden in der Regel ein natürliches Pulverfallverfahren.
Bei diesen beiden Methoden wird beim Beschichten grundsätzlich ein Schmelzbad in horizontaler Lage gebildet. Wenn die Neigung etwas größer ist, kann das Pulver nicht normal zugeführt werden, was den Einsatz von Lasern, insbesondere YAG-Lasern, einschränkt.
(3) Aus der Perspektive des Zustandes der Schmelzeseebildung
Aufgrund der hohen Regelgenauigkeit des Lasers, der konstanten Ausgangsleistung und des fehlenden Lichtbogenkontakts sind Größe und Tiefe des Schmelzbades konstant.
(4) Schnelles Heizen und Kühlen
Dies beeinträchtigt die Gleichmäßigkeit der Metallphasenbildung und wirkt sich auch nachteilig auf die Schlackenentfernung aus. Dies ist auch ein wichtiger Grund für die Bildung von Poren und ungleichmäßiger Härte beim Laserstrahl-Auftragschweißen, insbesondere im Falle von YAG-Lasern, die stärker betroffen sind.
Aufgrund des unterschiedlichen Absorptionsvermögens verschiedener Werkstoffe für Laser verschiedener Wellenlängen ist die Auswahl der Werkstoffe für das Laserauftragschweißen stark eingeschränkt. Für einige Werkstoffe wie selbstschmelzende Legierungen auf Nickelbasis sind Laser besser geeignet, während das Auftragschweißen mit Karbiden und Oxiden schwieriger ist.
Der Plasmastrahl, der in der Mikrostrahl-Plasmaschweißmaschine verwendet wird, ist ein Ionisationslichtbogen, der konzentrierter ist als bei der Lichtbogenschweißmaschine, daher ist die Erwärmungsgeschwindigkeit höher.
Um einen konzentrierteren Plasmastrahl zu erhalten, werden in der Regel eine Öffnung mit hohem Verdichtungsverhältnis und ein niedriger Strom verwendet, um die Basistemperatur nicht zu hoch werden zu lassen und eine Verformung der Rückzündung zu verhindern.
Dies ist natürlich nicht mit der Erwärmungsgeschwindigkeit eines YAG-Lasers vergleichbar. Da die Plasmabogen arbeitet kontinuierlich, die Maschine kühlt relativ langsam ab und bildet eine Übergangszone, die tiefer ist als beim Laserauftragschweißen. Dies führt zu einem besseren Spannungsabbau bei Auftragsschweißmaterialien.
Mikrostrahl-Plasmaschweißanlagen werden auf der Grundlage von Gleichstrom-Schweißmaschinen entwickelt.
Die Stromquelle, die Sprühpistole, der Pulverförderer und der Oszillator haben eine niedrige technische Schwelle, sind einfach herzustellen, zuverlässig, einfach zu warten und zu benutzen, verbrauchen weniger Strom, haben niedrige Nutzungskosten, eine gute Vielseitigkeit, niedrige Produktionskosten, eine gute Anpassungsfähigkeit und sind leicht für die Produktion zu erweitern, was erhebliche Vorteile bietet.
Es stellt geringe Anforderungen an die Umwelt und bietet eine breite Materialanpassung.
Mit dem Fortschritt in der Elektrotechnik hat sich das Niveau der Schweißtechnik in unserem Land ausreichend unterstützt wird. Außerdem sind Größe und Gewicht der Ausrüstung gering, und die Schweißpistole kann mit der Hand gehalten werden, was sie flexibler und bequemer in der Anwendung macht. Die Kosten für Hilfswerkzeuge sind ebenfalls niedrig.
(1) Die Vorbehandlung ist einfach
Es ist lediglich eine Entrostung, Entfettung und Entfernung von Ermüdungsschichten erforderlich.
(2) Puderzufuhr
Für die Pulverförderung wird Argongas verwendet. Die Anforderungen an die Fördergenauigkeit sind gering, und ein gewisser Neigungsgrad ist zulässig. Dies ermöglicht einen manuellen Betrieb, der für die Metallreparatur geeignet ist.
(3) Micro-Beam Plasma hat eine gute Stabilität
Die Stabilität des Mikrostrahlplasmas ist gut, und die Bildung des Schmelzbades ist leicht zu kontrollieren. Das Füllmaterial und der Maschinenkörper sind vollständig verschmolzen, und der Übergangsbereich ist gut.
(4) Heiz- und Kühlgeschwindigkeiten sind niedriger als bei Laser
Der geschmolzene Zustand wird lange aufrechterhalten, was der gleichmäßigen Bildung metallurgischer Strukturen förderlich ist. Die Abgasschlacke ist besser. Das Pulver wird während des Sprühvorgangs erhitzt und durch Argongas und ionisierte Luft geschützt.
Daher ist die Gleichmäßigkeit der Deckschicht besser, und es gibt weniger Fehler wie Poren und Einschlüsse.
(5) Materialauswahl
Bei der Plasmaerwärmung gibt es weniger Einschränkungen bei der Materialauswahl, und es ist einfacher, Karbide und Oxide zu überlagern.
Wir müssen uns darüber klar werden, dass es unabhängig von der verwendeten Terminologie (Schweißen, Auftragschweißen, thermisches Spritzen, Auftragen usw.) immer um das Gießen auf ein erhitztes Metallsubstrat geht.
Daher treten beim Übergang vom Erhitzen zum Gießen und dann zum Abkühlen unweigerlich Spannungen auf.
Abgesehen von sehr spezifischen Materialien ist der wichtigste Einfluss in der Regel die Schwindungsspannung. Verschiedene Schweißverfahren variieren in den Heizmethoden, der Geschwindigkeit, den Füllstoffen und einigen anderen Bedingungen.
Daher ist die Minimierung der Auswirkung dieser Belastung auf das Substrat und die Gussschicht ein wichtiger Aspekt, den wir bei der Verfolgung der Schweißqualität.
Ich glaube, dass Schrumpfungsspannungen unvermeidlich sind. Daher liegt der Schlüssel zur Lösung des Problems der Schweißspannungen im Spannungsabbau. Mit anderen Worten, die Frage, wo diese Schrumpfspannung abgebaut wird und wie die Spannung vom Substrat auf den Gussbereich verteilt wird, ist ein Problem, das wir lösen müssen und können.
Die Hauptgründe dafür sind die kleine Gussfläche, der kleine Übergangsbereich und die geringe Schrumpfung.
Daher reicht die während des Schrumpfungsprozesses des Materials erzeugte Schrumpfkraft nicht aus, um den gesamten Maschinenkörper zu verformen.
Dies ist der Grund dafür, dass sich das Laser-Overlay nicht verformt (wenn der Maschinenkörper zu klein ist, kann es trotzdem zu einer Verformung kommen), und es ist auch ein Vorteil der Laserschweißen (überlagernd).
Wohin geht nun diese Schweißspannung? Sie wird hauptsächlich im Gussbereich und im Übergangsbereich freigesetzt. Daraus ergeben sich zwei Probleme:
Erstens ist der Gussbereich anfällig für Risse. Daher erfordert das Laser-Overlaying eine hohe Duktilität des Materials, z. B. Pulver auf Nickelbasis.
Zweitens ist die Übergangszone einer großen Belastung ausgesetzt. Aufgrund der schnellen Erwärmung und Abkühlung im Laser SchweißverfahrenDie Größe der Übergangszone ist zu gering, was zu einer Spannungskonzentration in diesem Bereich führt, was die Klebewirkung des Laserschweißens beeinträchtigt (Überlappung).
Vor allem dann, wenn sich die mechanischen Eigenschaften des Grundmaterials deutlich von denen des Schweißmaterialist die Tendenz stärker, und es kann sogar zur Delamination kommen. Dies erfordert ein besonderes Augenmerk auf das Material und die Dicke der Übergangsschicht beim Laser-Overlaying.
Dafür gibt es drei Hauptgründe:
Eine davon ist, dass Plasma als Wärmequelle für das Auftragschweißen konzentrierter ist als das Unterpulverschweißen, Schutzgasschweißen, usw.
Die Stabilität des Plasmalichtbogens ist besser, es gibt keinen Elektrodenverbrauch, die abgegebene Wärme ist gleichmäßig und lässt sich leicht steuern.
Dies führt zu einer gleichmäßigen Wärmeverteilung im Gussbereich, einem vollständigen und gleichmäßigen Aufschmelzen des Materials, einer ausreichenden Schlackenmenge und einer gleichmäßigen Verteilung der Schrumpfspannungen.
Zweitens ist es aufgrund der hohen Kontrollpräzision der Plasmaausrüstung bequem, den Gussbereich und den Übergangsbereich zu kontrollieren, die Gleichmäßigkeit ist gut, und die Spannungsverteilung ist einfacher, vernünftig zu kontrollieren.
Drittens sind bei der Verwendung von Argongas keine verschiedenen Zusatzstoffe erforderlich, und es treten keine Probleme wie Wasserstoffausscheidung und Oxidation auf.
Daher eignet sich das Plasmaplattieren (Aufschweißen) besser für großflächige, dicke, hochwertige Gussstücke mit harter Oberfläche (z. B. hochmanganhaltige, hochchromhaltige keramische Werkstoffe usw.), die sich für die Herstellung von verschleißfesten Platten, Ventilen, Walzen usw. eignen.
Zum Thema Laser- und Plasma-Auftragschweißen haben viele Fachkollegen zahlreiche Artikel veröffentlicht, von denen die meisten die Vorteile des Lasers hervorheben, was auch von allen angestrebt wird.
Die meisten werden jedoch mit der Methode der metallografischen Analyse aus mikroskopischer Sicht bewertet.
Alles hat zwei Seiten, und auch das Laserstrahl-Auftragschweißen hat seine Nachteile.
Das Verfahren weist viele Einschränkungen auf, und die tatsächliche Produktion erfordert ein höheres Maß an Bedienungskompetenz, was für viele Kunden Schwierigkeiten mit sich bringt.
Ich glaube, dass es vor allem auf die kurze Schmelzzeit der Beschichtung durch schnelle Erwärmung und Abkühlung, was zu einem großen Unterschied zwischen den äußeren und inneren Rändern der Stelle, ungleiche Organisation Bildung, ungleiche Spannungsverteilung, unzureichende Abgas Schlacke, was zu ungleichmäßigen Härte, leicht zu bilden Poren und Schlacke Einschluss Probleme, ist es schwierig, eine perfekte Beschichtung der großen Fläche zu erhalten, vor allem für YAG-Laser.
Daher sollte beim Laserstrahl-Auftragschweißen von der Materialauswahl bis zum Betrieb besonders sorgfältig vorgegangen werden.
Im Vergleich zum Laser wird beim Plasmabeschichten mehr Wärme zugeführt, und die Substratverformung ist größer als beim Laser.
Aber seine Schmelzleistung ist ausreichend, die Härteverteilung ist gleichmäßig, die Abgasschlacke ist gründlich, der Materialauswahlbereich ist breit, einfach zu bedienen, und es ist einfach, eine relativ intakte Gesamtverkleidungsschicht zu erhalten, niedrige Kosten, gute Vorteile, daher hat es offensichtliche Vorteile in großen Bereich, dicke Verkleidung.