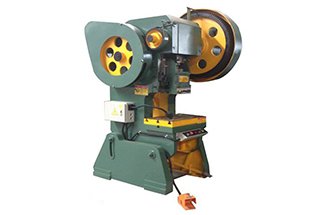
Haben Sie sich jemals gefragt, wie man eine Stanzmaschine sicher und effizient bedient? Dieser Artikel befasst sich mit den wichtigsten Verfahren für den Betrieb von Stanzmaschinen in der Fertigung. Er befasst sich mit Sicherheitsrichtlinien, Vorbereitungsschritten und detaillierten Betriebsmethoden, die eine hochwertige Produktion und eine lange Lebensdauer der Geräte gewährleisten. Egal, ob Sie ein Anfänger oder ein erfahrener Bediener sind, Sie werden wertvolle Einblicke erhalten, um Ihr Verständnis und Ihre Fähigkeiten im Umgang mit Stanzmaschinen zu verbessern.
Um den sicheren Betrieb von Stanz- und Umformprozessen bei der Herstellung petrochemischer Produkte zu standardisieren, die Qualität der verarbeiteten Produkte zu gewährleisten und die Lebensdauer der Anlagen zu verlängern, wurde diese Betriebsanweisung formuliert. Sie muss von den normalen Stanzern des Unternehmens strikt befolgt werden.
Dies gilt für die betriebliche Anleitung zum Schneiden, Stanzen und Umformen von Blechen aus kohlenstoffarmen Stählen, niedrig legierten Stählen und nichtrostenden Stählen in den Stanz- und Umformverfahren der petrochemischen Industrie.
Keine
4.1 Die Bediener gewöhnlicher Stanzmaschinen in der Produktionshalle müssen die Sicherheitsvorschriften strikt einhalten und die erforderlichen Arbeitsschutzartikel tragen.
4.2 Die Technologieabteilung sollte Produktionszeichnungen und Prozesskarten gemäß dem Produktionsplan erstellen. Sie sollte auch die Umsetzung der Stanzarbeitsanweisungen und Prozessdisziplinen überwachen und kontrollieren und sie rechtzeitig veröffentlichen.
4.3 Der Bediener sollte die Arbeitsvorgänge, die Selbstinspektion, die Qualitätssicherung, die Wartung der Ausrüstung und das Abfüllen von Berichten gemäß der Prozesskarte durchführen.
4.4 Die Inspektoren der Abteilung Qualitätskontrolle sind verantwortlich für die Erstmusterprüfung, die Stichprobenprüfung, die Qualitätsprüfung der Prozessprodukte und die Überwachung der Umsetzung der Prozessparameter.
4.5 Die Produktionswerkstatt ist für die Zerlegung des Produktionsplans und die Fortschrittskontrolle zuständig.
5.1.1 Das Stanzverfahren ist ein Verfahren zur Bearbeitung von Werkstücken mit einer bestimmten Größe, Form und Leistung, bei dem durch die Form eine äußere Kraft auf den Rohling ausgeübt wird, die eine plastische Verformung oder Trennung bewirkt.
Die Stanztechnik hat ein breites Anwendungsspektrum und kann für die Bearbeitung von Blechen, Stangen und verschiedenen Nicht-Blechen eingesetzt werden.metallische Werkstoffe. Da das Verfahren in der Regel bei Raumtemperatur durchgeführt wird, wird es auch als Kaltumformung bezeichnet.
5.1.2 Merkmale des Prägeverfahrens:
1)Sie kann Werkstücke herstellen mit komplizierte Formen die mit anderen Verarbeitungsmethoden nur schwer zu erreichen sind. So können beispielsweise dünne Schalenteile durch Kaltprägen hergestellt werden. Die Maßgenauigkeit von Kaltprägeteilen wird durch die Matrize gewährleistet, was zu stabilen Abmessungen und guter Austauschbarkeit führt.
2)Das Stanzen hat eine hohe Materialausnutzung, was zu leichten, steifen und festen Teilen mit geringem Energieverbrauch während des Stanzvorgangs führt. Folglich sind die Kosten des Werkstücks niedrig.
3)Dieser Vorgang ist einfach und hat eine geringe Arbeitsintensität. Außerdem ist er leicht zu mechanisieren und zu automatisieren, was zu einer hohen Produktivität führt.
4)Die bei der Stanztechnik verwendete Werkzeugstruktur ist im Allgemeinen komplex, was zu einem langen Produktionszyklus und hohen Kosten führt.
5.1.3 Grundlegende Anforderungen an Stanzmaterialien
1)Die für das Stanzen verwendeten Materialien müssen nicht nur den technischen Anforderungen des Produktdesigns entsprechen, sondern auch den Anforderungen des Stanzprozesses und den Anforderungen an die Verarbeitung nach dem Stanzen, wie Schneiden, Galvanisieren und Schweißen.
2)Anforderungen für Materialeigenschaften der Stanz- und Umformtechnik:
a. Für den Umformprozess sollten die Materialien eine gute Plastizität aufweisen, um die Verformung zu erleichtern und die Qualität der Teile zu verbessern (gleichmäßige Dehnung δb Höhe), ein kleines Streckverhältnis (σs/ σb), ein großer Richtwirkungskoeffizient für die Plattendicke, ein kleiner Richtwirkungskoeffizient für die Plattenebene und ein kleines Verhältnis von Materialstreckgrenze zu Elastizitätsmodul (σS/E).
b. Für den Trennungsprozess muss das Material keine hervorragende Plastizität aufweisen, aber es sollte ein gewisses Maß an Plastizität haben. Je schwieriger es zu trennen ist, desto besser sollte die Plastizität sein.
3)Anforderungen an die Materialdickentoleranz:
Die Dickentoleranz des Materials muss den nationalen Normen entsprechen. Wenn die Dickentoleranz des Materials zu groß ist, kann sich dies direkt auf die Qualität der Teile auswirken und auch Schäden an Matrize und Stempel verursachen. Dies liegt daran, dass eine bestimmte Schnittspalt für eine bestimmte Dicke des Materials geeignet ist.
4)Anforderungen an die Oberflächenqualität des Materials:
a. Die Materialoberfläche muss glatt und eben sein, frei von Delaminationen, mechanischen Beschädigungen, Rostflecken, Oxidhaut und anderen Anhaftungen.
b. Bei Materialien mit guter Oberflächenqualität ist die Wahrscheinlichkeit geringer, dass die Form beim Stanzen Risse oder Kratzer bekommt. Dies führt zu einer hochwertigen Oberflächenqualität des Werkstücks.
5.2.1 Verfahren zur Trennung von Brüchen:
Das Bruchtrennverfahren wird eingesetzt, um Stanzteile von Feinblech entlang einer bestimmten Konturlinie während des Stanzvorgangs. Dieser Prozess kann durch verschiedene Techniken erreicht werden, wie z. B. Schneiden, Stanzen, Beschneiden, Schneiden, Schneiden und mehr.
1) Ausblendung:
Unter Stanzen versteht man das Schneiden einer flachen Platte entlang einer geschlossenen Kontur, wobei das verbleibende Material als Ausschuss betrachtet wird. Diese Methode wird üblicherweise als erster Schritt bei der Formgebung eines Werkstücks verwendet, wie in Abbildung 1 dargestellt.
Abb. 1 Schematisches Diagramm der Ausblendung
2) Stanzen:
"Stanzen" bezieht sich auf das Verfahren zur Herstellung von Löchern verschiedener Formen unter Verwendung von Stanzteilen oder anderen Formteilen (siehe Abb. 2). Dieser Prozess kann sowohl Stanzen und Schneiden.
Abb. 2 Stanzdiagramm
3) Beschneiden:
Beim Entgraten wird überschüssiges Material von der Kante des Formteils entfernt, um die gewünschte Form und Größe des Werkstücks zu erreichen (siehe Abb. 3).
Abb. 3 Schematische Darstellung des Trimmens
4) Ausklinken:
Wie in Abbildung 4 dargestellt, wird das lokale Material in einem bestimmten Winkel geschnitten und gebogen, ohne vollständig vom Hauptkörper getrennt zu werden. Dieses Verfahren ist gemeinhin als Kerb- oder Stanzformung bekannt.
Abb. 4 Schematisches Diagramm der Kerbe
5) Aufteilung:
Das Verfahren zur Erstellung einer massiven Form in Abb. 5 besteht darin, das Teil in zwei Abschnitte zu unterteilen, was als Zerschneiden bezeichnet wird.
Abb. 5 Schnittdarstellung
5.2.2 Kunststoffverformung Prozess:
Kunststoff Formgebungsverfahren umfassen die Umformung von Werkstoffen, ohne dass diese reißen, um Teile mit bestimmten Formen, Größen und Genauigkeitsanforderungen herzustellen. Beispiele für Kunststoffumformungsverfahren sind Biegen, Tiefziehen und Ausbeulen, FlanschenEinschnürung und Crimpen.
1) Biegen:
Das Diagramm in Abbildung 6 veranschaulicht der Prozess des Biegens einen Blechzuschnitt in einen bestimmten Winkel zu bringen oder den gebogenen Abschnitt durch Techniken wie Biegen, Kräuseln, Verdrehen usw. weiter zu formen.
Abb. 6 Biegediagramm
2) Dehnen:
Wie in Abbildung 7 dargestellt, wird der flache Rohling durch Walzen zu einem Hohlkörper geformt, oder der hohle Rohling wird einer zusätzlichen Verformung unterzogen.
Abb. 7 Streckdiagramm
3) Ausbeulen:
Wie in Abbildung 8 dargestellt, wird das hohle Stück von innen mit einem radialen Druck beaufschlagt, um seinen lokalen Durchmesser zu vergrößern. Diese Technik wird üblicherweise bei der Herstellung von Teekannen, Tassen und anderen ähnlichen Produkten aus Edelstahl eingesetzt.
Abb. 8 Ausbaudiagramm
4) Einschnüren:
Wie in Abbildung 9 dargestellt, wird zur Verringerung des lokalen Durchmessers von Hohlkörpern, wie z. B. Tassendeckeln aus Edelstahl, Tankprodukten usw., Druck auf die Außenseite ausgeübt.
Abb. 9 Schematische Darstellung der Einschnürung
5) Rollend:
Wie in Abbildung 10 dargestellt, wird die Kante des Hohlkörpers mit Hilfe eines Walzwerkzeugs bogenförmig nach außen gebogen. Diese Methode wird üblicherweise für Dosenprodukte verwendet.
Abb. 10 Schematische Darstellung des Rollkreises
(1) Bereiten Sie sich auf den Einsatz vor, indem Sie Geräte, Formen und Vorrichtungen überprüfen.
(2) Auswahl von Materialien, Werkzeugen und Messwerkzeuge gemäß dem Fertigungsauftrag (MO).
(3) Kalibrieren von Werkzeugen und Messgeräten und Durchführen von Selbstinspektionen von Materialien.
(4) Inbetriebnahme des Geräts.
(5) Beginn der Verarbeitung und Durchführung der ersten Kontrolle.
(6) Zur Prüfung vorlegen.
(7) Stellen Sie nach Beendigung des Vorgangs den Bediengriff zurück und schalten Sie das System ab.
5.4.1 Vorbereitung der Operation:
1)Reinigen Sie die Umgebung der Presse, um sicherzustellen, dass sie für den normalen Betrieb sauber ist.
2)Prüfen Sie die Schmierung aller Teile und stellen Sie sicher, dass alle Schmierstellen vollständig geschmiert sind.
3)Überprüfen Sie den korrekten und zuverlässigen Einbau der Form und vergewissern Sie sich, dass sich im Inneren keine Ablagerungen befinden, um Produkt- und Formschäden zu vermeiden.
4)Vergewissern Sie sich, dass der Netzschalter des Anlegers eingeschaltet ist, um ein Verrutschen durch Nicht-Zuführen zu verhindern.
5)Trennen Sie das Schwungrad von der Kupplung, um den Motor zu starten.
6)Wenn Sie den Motor starten, stellen Sie sicher, dass die Drehrichtung des Schwungrads mit dem Drehzeichen übereinstimmt. Wenn dies nicht der Fall ist, unterbrechen Sie sofort die Stromzufuhr zur Überprüfung und passen Sie die Reihenfolge der Stromzufuhr an.
7)Bewegen Sie die Presse einige Male, überprüfen Sie die Funktion der Bremse, der Kupplung und des Pferdeantriebs und nehmen Sie den normalen Betrieb auf, nachdem Sie sich vergewissert haben, dass der Stempel ordnungsgemäß funktioniert.
5.4.2 Arbeitsweise
1)Befolgen Sie die in der Betriebsanleitung der Stanze beschriebene Startmethode, um den Stanzvorgang zu starten. Schalten Sie den Schalter für das Blasrohr ein, um zu verhindern, dass das Produkt weggeblasen wird, was zu Stapelung und Beschädigung führen könnte.
2)Manuelles Probestanzen mehrerer Werkstücke zu Zwecken der Selbstinspektion. Hauptamtliche Prüfer müssen den normalen Betrieb bestätigen, bevor sie fortfahren.
3)Bei normalem Dauerstempeln halten Sie den roten Bremsknopf mit einer Hand, sitzen aufrecht und konzentrieren sich auf die Form und den Auslass. Vermeiden Sie es, sich mit anderen zu unterhalten oder zu scherzen, um eine Beschädigung der Form oder eine Disqualifikation aufgrund von Fehlstellungen oder herunterfallenden Stempeln zu vermeiden. Überprüfen Sie alle 5-10 Minuten das Aussehen des gestanzten Produkts, die Größe, die Pressung, kleine Löcher, Verformungen, Grate, Ölflecken und die Übereinstimmung der Hauptabmessungen.
4)Im persönlichen Produktions-Tagesbericht sind während des normalen Stanzens detaillierte Informationen zu vermerken, einschließlich der Produktionsmenge jeder Rolle oder Stunde. Das Stanzpersonal sollte die erforderlichen Felder genau ausfüllen.
5)Wenn während des normalen Stanzens irgendwelche Anomalien an den Produkten der Werkzeugmaschine festgestellt werden, muss die Maschine sofort gestoppt und der Vorgesetzte zur rechtzeitigen Behandlung informiert werden. Außerdem sollte man den Qualitätsprüfer bei der Unterscheidung und Isolierung der fehlerhaften Produkte unterstützen.
6)Nach dem Stanzen sollte die Umgebung des Arbeitsbereichs aufgeräumt werden, einschließlich leerer Kisten, fertiger Kisten und Hocker. Die Stanze und das Blasrohr sollten in der richtigen Reihenfolge geschlossen werden, und alle Strom- und Ölleitungsschalter sollten vor dem Verlassen des Arbeitsplatzes ausgeschaltet werden.
7)Wenn Formen, Stempel und Vorschübe während des Betriebs eingestellt oder repariert werden müssen, sollte das erste nach der Korrektur hergestellte Produkt dem Vollzeitinspektor zur Bestätigung vorgelegt werden. Außerdem sollte vor der Fortsetzung der Produktion die Erststückliste ausgestellt werden.
8)Wenn eine abnormale Abschaltung während des normalen Stanzproduktion wegen Stromausfall, unzureichendem Luftdruck usw. müssen die in dieser Zeit produzierten Teile verschrottet werden. Wenn eine Neuproduktion erforderlich ist, muss sie vor der Fortsetzung der Produktion von der Qualitätsabteilung geprüft werden.
9)Füllen Sie regelmäßig Schmieröl in jede Schmierstelle und ölen Sie die inneren und äußeren Führungssäulen der Form alle vier Stunden.
5.5.1 Die äußere Platte muss hohen Anforderungen genügen und darf keine sichtbaren Mängel aufweisen.
5.5.2 Die Innenplatte muss frei von Rissen, auch von versteckten, sein.
Bei der Inspektion von Tiefziehteilen sollten Sie zunächst die Druckstellen auf Klarheit prüfen. Suchen Sie dann nach versteckten Rissen. Schließlich berühren und drücken Sie die Teile mit einem Ölstein.
1) Holprig
a. Methode der Bewertung: Mit den Händen berühren, mit einem Ölstein drücken und visuell prüfen.
Es wird empfohlen, die Ölsteinschiebemethode zu verwenden. Wölbungen sollten hervorgehoben werden, während Vertiefungen als dunkle Flecken erscheinen sollten.
b. Die Ursache: Bei Unebenheiten ist zu prüfen, ob sich Sand oder andere Fremdkörper in der Form befinden.
c. Behandlung: Wenn Sand vorhanden ist, wischen Sie den Schimmel mit Schimmelpilzwischentuch ab.
2) Rissbildung (verdeckte Rissbildung)
a. Beurteilungsmethode: Prüfen Sie die Ecken der Zeichnungsteile und andere Stellen mit großen Materialverformungen mit den Augen und drehen Sie die Rückseite um, um sie zu prüfen.
b. Ursache: Möglicherweise ist die Matrize überlastet und die Niederhalterkraft ist zu groß.
c. Behandlungsmethode: Prüfen Sie, ob das Werkstück ernsthaft belastet ist, und reduzieren Sie die Seitenkraft entsprechend.
3) Faltenbildung
a. Beurteilungsmethode: mit den Augen schauen;
b. Ursache: geringe Niederhalterkraft;
c. Behandlung: Angemessene Erhöhung der Niederhalterkraft.
4) Grate
a. Beurteilungsmethode: Schau mit deinen Augen.
b. Die Ursache: Der Abstand zwischen Patrize und Matrize ist groß.
c. Behandlungsmethode: Schimmelpilzsanierung.
5) Durchbiegung der Bohrung
a. Beurteilungsmethode: Prüfung mit oberem Inspektionswerkzeug und Vergleich mit der Probe.
b. Ursache: Das Werkstück ist nicht richtig platziert, und die Positioniervorrichtung der Form ist defekt.
c. Behandlungsmethode: Wenn das Loch nach dem Richten des Werkstücks immer noch abweicht, melden Sie dies dem Schichtleiter und benachrichtigen Sie die Werkzeugreparatur.
6) Lochblende
a. Beurteilungsmethode: Vergleich mit der Stichprobe.
b. Die Ursache: Der Stempel ist gebrochen.
c. Behandlung: Sofortige Einstellung der Produktion, sofortige Meldung an den Schichtleiter und Benachrichtigung der Werkzeugreparatur.
7) Verformung des Lochs
a. Beurteilungsmethode: Schau mit deinen Augen.
b. Die Ursache: Der Stempel ist verschlissen.
c. Behandlungsmethode: Meldung an den Schichtleiter und Benachrichtigung der Werkzeugreparatur, wenn leichte und starke Verölung noch Deformationen aufweisen.
8) Die Zeichnung ist nicht vorhanden.
a. Beurteilungsmethode: Prüfen Sie, ob der Druckpunkt klar ist.
b. Die Ursache: Der Hauptdruck ist zu niedrig.
c. Behandlung: Angemessene Erhöhung des Hauptdruckes.
9) Schlechte Faltung
a. Beurteilungsmethode: Vergleich mit der Stichprobe
b. Die Ursache: Die Teile sind nicht richtig platziert, und die Positioniervorrichtung ist defekt.
c. Handhabungsmethode: Legen Sie das Werkstück richtig ein. Wenn es immer noch defekt ist, melden Sie sich beim Schichtleiter und benachrichtigen Sie das Werkzeugreparaturpersonal, um das Werkzeug zu reparieren.
10) Impressum
a. Beurteilungsmethode: Schau mit deinen Augen.
b. Die Ursache: Auf der Arbeitsfläche der oberen Form befinden sich körnige Verunreinigungen.
c. Behandlung: Wischen Sie die obere Form sauber.
11) Dehnung
a. Beurteilungsmethode: Schau mit deinen Augen.
b. Die Ursache: Die Arbeitsfläche der Matrize ist abgenutzt und die Härte der Matrize ist nicht ausreichend.
c. Behandlungsmethode: Schimmelpilzsanierung.
12) Sandkorn
a. Beurteilungsmethode: Drücken Sie mit einem Ölstein.
b. Die Ursache: Das Material oder die Oberfläche der Form ist nicht sauber.
c. Behandlung: Überprüfen Sie die Materialien oder wischen Sie die Oberfläche der Form sauber.
13) Beulen und Kratzer
a. Beurteilungsmethode: Schau mit deinen Augen.
b. Ursache: Die ein- oder ausgehenden Materialien berühren harte Gegenstände wie z. B. Formen.
c. Behandlung: Seien Sie vorsichtig bei der Beschickung und Entnahme von Materialien, behandeln Sie die Produkte mit Sorgfalt und erhöhen Sie die Schließhöhe der Form, falls erforderlich.
6.1.1 Wenn es länger als 10 Minuten dauert, das Gerät zu verlassen, schalten Sie es aus, um Strom zu sparen.
6.1.2 Ölhaltige Lappen oder Baumwollgarne, die während des Betriebs und der Wartung der Maschine anfallen, müssen an den dafür vorgesehenen Stellen entsorgt werden.
6.1.3 Die während des Betriebs anfallenden Abfälle müssen in den dafür vorgesehenen Abfallbereich gebracht werden, und es ist strengstens verboten, sie irgendwo hinzuwerfen.
6.1.4 Öl, das für den Betrieb und die Wartung von Maschinen verwendet wird, muss getrennt gelagert und gleichmäßig recycelt werden.
6.2.1 Nicht-Elektriker dürfen den Verteilerkasten nicht ohne Erlaubnis öffnen und den Stromkreis berühren, um einen Stromschlag zu vermeiden.
6.2.2 In der Nähe von Öl- und Gaslagertanks darf nicht geraucht werden, um Brände oder Explosionen zu verhindern.
6.2.3 Während des Betriebs der Maschine muss der Motorriemen mit einer Schutzabdeckung versehen sein. Die Schutzvorrichtung kann nicht willkürlich entfernt werden.
6.2.4 Drücken Sie den Startknopf mit beiden Händen, um Arbeitsunfälle zu vermeiden.
6.2.5 Der Stanzvorgang muss hoch konzentriert sein, um sicherzustellen, dass die Produkte und Formen normal sind.
6.2.6 Während des Betriebs des Stempels ist es aus Gründen der Gesundheit und Sicherheit verboten, mit der Hand in die Form oder neben die Form zu greifen.
6.2.7 Beim normalen Stempeln ist es strengstens verboten, mit zwei oder drei Personen an derselben Maschine zu arbeiten.
Achten Sie besonders auf die Selbstinspektion bei der Entnahme von Produkten und auf die Entnahme von Produkten aus dem Aufnahmeschacht, um die persönliche Sicherheit zu gewährleisten.
6.2.8 Das Gerät ist sofort stillzulegen, wenn es als anormal eingestuft wird.
6.2.9 Trennen Sie das Schwungrad von der Kupplung und schalten Sie nach der Arbeit den Strom ab.
6.2.10 Wischen und reinigen Sie die Presse und tragen Sie Öl auf die unlackierte bearbeitete Oberfläche auf.