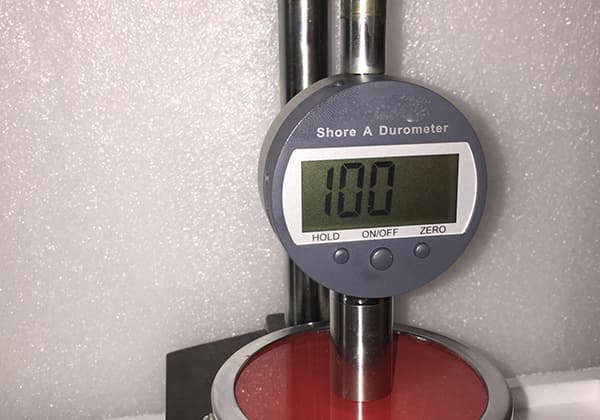
Haben Sie sich jemals gefragt, welche Kunst und Wissenschaft hinter den eleganten Metallgehäusen Ihrer Lieblingsgeräte steckt? In diesem Blogbeitrag tauchen wir in die faszinierende Welt der Blechverarbeitung ein. Als erfahrener Maschinenbauingenieur gebe ich Einblicke in die Materialien, Prozesse und Designprinzipien, die flache Metallbleche in die komplexen Formen verwandeln, die unsere moderne Elektronik beherbergen. Machen Sie sich bereit, die modernsten Techniken und kreativen Problemlösungen kennenzulernen, die die Blechbearbeitung zu einem wichtigen Bestandteil der Produktentwicklung machen.
Die Blechbearbeitung ist ein umfassendes Kaltverarbeitungsverfahren für Bleche (in der Regel weniger als 6 mm), einschließlich Scheren, ., Biegen, SchweißenNieten, Stanzformen und Oberflächenbehandlung, usw.
Das Besondere daran ist, dass die Dicke des gleichen Teils gleich bleibt.
Der Blechbearbeitungsprozess einschließlich:
Bleche sind die am häufigsten verwendeten Werkstoffe für die Konstruktion von Kommunikationsprodukten.
Das Verständnis für die umfassende Leistung von Materialien und die richtige Materialauswahl haben einen großen Einfluss auf Produktkosten, Produktleistung, Produktqualität und Verarbeitbarkeit.
1) Verwenden Sie gängige Metallmaterialien, um die Materialspezifikationen zu reduzieren und so viel wie möglich im Rahmen des Materialhandbuchs des Unternehmens zu kontrollieren;
2) Reduzieren Sie bei ein und demselben Produkt die Vielfalt der Materialien und Blechdicken so weit wie möglich;
3) Unter der Prämisse, die Funktion der Teile zu gewährleisten, wird versucht, billige Materialien zu verwenden, den Materialverbrauch zu reduzieren und die Materialkosten zu senken;
4) Für den Schrank und einige große Steckdosen ist es notwendig, das Gewicht der gesamten Maschine zu reduzieren;
5) Neben der Prämisse, die Funktion der Teile zu gewährleisten, muss auch berücksichtigt werden, dass die Stanzleistung des Materials den Verarbeitungsanforderungen entsprechen muss, um die Rationalität und Qualität der Verarbeitung der Produkte zu gewährleisten.
Stahlplatte
1) Kaltgewalztes Stahlblech
Kaltgewalztes Stahlblech ist die Abkürzung für kaltgewalztes Blech aus Kohlenstoffbaustahl.
Es wird aus einem warmgewalzten Band aus Kohlenstoffbaustahl zu einem Stahlblech mit einer Dicke von weniger als 4 mm kaltgewalzt.
Da es bei normaler Temperatur gewalzt wird, entsteht kein Eisenoxidzunder. Daher ist die Oberflächenqualität der Kühlplatte gut und die Maßgenauigkeit hoch.
Darüber hinaus ist die Ausglühvorgang hat es bessere mechanische Eigenschaften und eine bessere Prozessleistung als Warmgewalzter Stahl Blätter.
Üblicherweise werden die kohlenstoffarmen Stahlsorten 08F und 10# verwendet, die sich durch gute . und Biegeeigenschaften.
2) Kontinuierlich galvanisch verzinktes, kaltgewalztes Stahlblech
Kontinuierlich galvanisch verzinktes kaltgewalztes Stahlblech, d.h. "elektrolytisches Blech".
Bezieht sich auf das Verfahren der kontinuierlichen Abscheidung von Zink aus einer wässrigen Zinksalzlösung auf einem vorbereiteten Stahlband, um eine verzinkte Oberflächenschicht unter Einwirkung eines elektrischen Feldes auf einer galvanischen Verzinkungsanlage zu erhalten.
Aufgrund der Einschränkungen des Verfahrens ist die Beschichtung sehr dünn.
3) Kontinuierlich feuerverzinktes Stahlblech
Kontinuierlich feuerverzinktes Stahlblech wird bezeichnet als verzinktes Blech oder Weißblech.
Die kaltgewalzten, kontinuierlichen, feuerverzinkten Stahlbleche und Stahlbänder mit einer Dicke von 0,25 bis 2,5 mm werden zunächst in einem flammenbeheizten Vorwärmofen vorgewärmt, um Oberflächenrestöl abzubrennen.
Gleichzeitig bildet sich eine Eisenoxidschicht auf der Oberfläche.
Anschließend wird es in einem Reduktionsglühofen mit einem Gemisch aus H2 und N2 auf 710 bis 920 °C erhitzt, um die Eisenoxidschicht zu Eisenschwamm zu reduzieren.
Nachdem das oberflächenaktivierte und gereinigte Band auf eine Temperatur abgekühlt ist, die etwas höher ist als die des geschmolzenen Zinks, gelangt es bei 450-460 °C in den Zinktopf.
Die Oberflächenstärke der Zinkschicht wird mit einem Luftmesser kontrolliert.
Abschließend erfolgt eine Passivierung mit einer Chromatlösung zur Verbesserung der Weißrostbeständigkeit.
Im Vergleich zur Oberfläche des galvanisch verzinkten Blechs ist die Beschichtung dicker und wird hauptsächlich für Blechteile verwendet, die eine hohe Korrosionsbeständigkeit erfordern.
4) Aluminium-Zink-Platte
Die Aluminium-Zink-Legierungsbeschichtung der Aluminium-Zink-Platte besteht aus 55% Aluminium, 43,4% Zink und 1,6% Silizium bei 600° C.
Bildet eine dichte quaternäre Kristallschutzschicht mit ausgezeichneter Korrosionsbeständigkeit, die normale Lebensdauer von bis zu 25 Jahren, 3-6 mal länger als eine verzinktes Blech und vergleichbar mit rostfreiem Stahl.
Die Korrosionsbeständigkeit der Aluminium-Zink-Platte ergibt sich aus der Barrierefunktion des Aluminiums und dem Opferschutz des Zinks.
Wenn Zink für das Beschneiden, Kratzen und Zerkratzen der Beschichtung geopfert wird, bildet Aluminium eine unlösliche Oxidschicht, die als Barriere wirkt.
Die oben genannten Stahlbleche 2), 3) und 4) werden zusammenfassend als beschichtete Stahlbleche bezeichnet und finden breite Verwendung in Kommunikationsgeräten.
Nachdem die beschichtete Stahlplatte verarbeitet wird, kann es nicht mehr galvanisiert oder lackiert werden.
Der Einschnitt kann ohne besondere Behandlung direkt verwendet werden, und zur Verbesserung der Rostbeständigkeit des Einschnitts kann eine spezielle Phosphatierungsbehandlung durchgeführt werden.
Von der Kostenanalyse her wird das kontinuierliche galvanisch verzinkte Stahlblech verwendet, und der Verarbeitungsbetrieb muss die Teile nicht zur Galvanisierung schicken, was Zeit und Transportkosten spart.
Außerdem werden die Teile vor dem Sprühen nicht gebeizt, was die Verarbeitungseffizienz verbessert.
5) Rostfreier Stahl Platte
Aufgrund seiner hohen Korrosionsbeständigkeit, guten elektrischen Leitfähigkeit, hohen Festigkeit usw. ist es weit verbreitet.
Aber wir sollten auch ihre Unzulänglichkeiten berücksichtigen:
Platten aus Aluminium und Aluminiumlegierungen
Die üblicherweise verwendeten Bleche aus Aluminium und Aluminiumlegierungen bestehen hauptsächlich aus den folgenden drei Materialien:
Rostschutzaluminium 3A21, die alte Marke LF21, ist eine AL-Mn-Legierung. Es ist das am meisten verwendete rostfreie Aluminium.
Die Festigkeit dieser Legierung ist nicht hoch (nur höher als die von reinem Industriealuminium) und kann nicht wärmebehandelt und verstärkt werden.
Daher wird die Kaltverformung häufig zur Verbesserung der mechanischen Eigenschaften eingesetzt. Im geglühten Zustand weist es eine hohe Plastizität auf, und die Plastizität ist bei der Halbkalthärtung gut.
Es hat eine geringe Plastizität, gute Korrosionsbeständigkeit und gute Schweißbarkeit bei der Kaltverfestigung.
Rostschutzaluminium 5A02 ist die alte Marke LF2 Serie AL-Mg Rostschutzaluminium.
Im Vergleich zu 3A21 hat 5A02 eine höhere Festigkeit, insbesondere eine hohe Ermüdungsfestigkeit, hohe Plastizität und Korrosionsbeständigkeit.
Die Wärmebehandlung kann nicht verstärkt werden, und die Schweißbarkeit durch Kontaktschweißen und Wasserstoff-Atomschweißen ist gut, und es besteht eine Tendenz zur Bildung von Kristallrissen während der Argon-Lichtbogenschweißenund die Legierung neigt bei der Kaltverfestigung zur Bildung von Kristallrissen.
Die Legierung ist im kaltgehärteten und halbkaltgehärteten Zustand gut zerspanbar, im geglühten Zustand ist die Zerspanbarkeit schlecht, und sie kann poliert werden.
Hartaluminium 2A06 ist das alte LY6, eine häufig verwendete Hartaluminiumsorte.
Hartes Aluminium und superhartes Aluminium haben höhere Festigkeit und Härte als gewöhnliche Aluminiumlegierungen und können als einige Plattenmaterialien verwendet werden.
Die Plastizität ist jedoch schlecht, und das Biegen kann nicht durchgeführt werden, und das Biegen kann Risse oder Sprünge im äußeren abgerundeten Teil verursachen.
Es gibt neue Normen für den Grad und den Status von Aluminiumlegierungen. Der Normcode für die Methode zur Darstellung der Güteklasse ist GB/T16474-1996, der Statuscode ist GB/T16475-1996, und die Vergleichstabelle mit der alten Norm ist in Tabelle 1-1 unten dargestellt:
Tabelle 1-1 Vergleichstabelle der neuen und alten Aluminiumlegierungsgüten
Klasse | Staaten | ||||||||
Neu | Alte | Neu | Alte | Neu | Alte | Neu | Alte | Neu | Alte |
1070A | L1 | 5A06 | LF6 | 2A80 | LD8 | 2A14 | LD10 | H12 | R |
1060 | L2 | 5A12 | LF12 | 2A90 | LD9 | 2A50 | LD5 | O | M |
1050A | L3 | 8A06 | L6 | 4A11 | LD11 | 6A02 | LD2 | T4 | CZ |
1035 | L4 | 3A21 | LF21 | 6063 | LD31 | 7A04 | LC4 | T5 | RCS |
1200 | L5 | 2A02 | LY2 | 6061 | LD30 | 7A09 | LC9 | T6 | CS |
5A02 | LF2 | 2A06 | LY6 | 2A11 | LY11 | ||||
5A03 | LF3 | 2A16 | LY16 | 2A12 | LY12 | ||||
5A05 | LF5 | 2A70 | LD7 | 2A13 | LY13 |
Platten aus Kupfer und Kupferlegierungen
Es gibt zwei Haupttypen von häufig verwendeten Blechen aus Kupfer und Kupferlegierungen: Kupfer T2 und Messing H62.
Kupfer T2 ist das am häufigsten verwendete reine Kupfer. Es hat ein violettes Aussehen und wird auch Kupfer genannt. Es hat eine hohe elektrische und thermische Leitfähigkeit, gute Korrosionsbeständigkeit und Formbarkeit.
Aber die Festigkeit und Härte sind viel geringer als bei Messing, und der Preis ist sehr teuer.
Es wird hauptsächlich als Korrosionselement für leitfähige, wärmeleitende und Konsumgüter verwendet. Es wird im Allgemeinen für Teile der Stromversorgung verwendet, die große Ströme führen müssen.
rass H62, ein hochzinkhaltiges Messing, hat eine hohe Festigkeit und eine ausgezeichnete Kalt- und Warmverformbarkeit und lässt sich leicht für verschiedene Formen von Pressearbeit und Schneiden.
Hauptsächlich verwendet für verschiedene Tiefzieh- und Biegekraft Seine Leitfähigkeit ist nicht so gut wie die von Kupfer, aber es hat eine bessere Festigkeit und Härte, und der Preis ist relativ moderat.
Um die Anforderungen an die elektrische Leitfähigkeit zu erfüllen, wird so oft wie möglich Messing H62 anstelle von Kupfer verwendet, wodurch die Materialkosten erheblich gesenkt werden können.
Die meisten der derzeitigen Stromschienen bestehen aus Messing H62, das sich als völlig zufriedenstellend erwiesen hat.
Es gibt drei Hauptbereiche Arten von Blechen Verarbeitung: Stanzen und Schneiden, Biegen und Recken.
Verschiedene Verarbeitungstechniken stellen unterschiedliche Anforderungen an das Blech.
Bei der Auswahl der Bleche sollten auch die allgemeine Form und die Verarbeitungstechnologie des Produkts berücksichtigt werden.
Der Einfluss von Materialien auf die Ausblendung
Das Stanzen erfordert, dass das Blech ausreichend plastisch ist, damit es beim Stanzen nicht reißt.
Weiche Materialien (wie reines Aluminium, rostfreies Aluminium, Messing, Kupfer, kohlenstoffarmer Stahl usw.) lassen sich gut stanzen, und nach dem Stanzen können Teile mit glattem Querschnitt und geringer Neigung hergestellt werden;
Harte Materialien (wie z. B. kohlenstoffreicher StahlEdelstahl, hartes Aluminium, superhartes Aluminium usw.) haben nach dem Stanzen eine schlechte Qualität, und die Unebenheiten des Profils sind groß, insbesondere bei dicken Blechen.
Bei spröden Materialien ist es wahrscheinlich, dass nach dem Stanzen Risse auftreten, insbesondere bei geringer Breite.
Der Einfluss von Materialien auf das Biegen
Bleche, die gebogen und geformt werden müssen, sollten eine ausreichende Plastizität und eine niedrige Streckgrenze aufweisen.
Eine hochplastische Platte, die beim Biegen weniger anfällig für Risse ist.
Bleche mit niedriger Streckgrenze und niedrigem Elastizitätsmodul haben weniger Rückfederung Verformung nach dem Biegen, und es ist einfach, eine genaue gebogene Form zu erhalten.
Kunststoffmaterialien wie kohlenstoffarmer Stahl, Messing und Aluminium mit einer Kohlenstoffgehalt von <0,2% lassen sich leicht biegen und formen;
Sprödere Werkstoffe, wie Phosphorbronze (QSn6,5 ~ 2,5), Federstahl (65Mn), hartes Aluminium, superhartes Aluminium usw., müssen einen großen relativen Biegeradius (r / t) beim Biegen, da es sonst beim Biegen zu Rissen kommen kann.
Besonderes Augenmerk sollte auf die Wahl des harten und weichen Zustandes des Materials gelegt werden, der einen großen Einfluss auf die Biegeeigenschaften hat.
Bei vielen spröden Materialien kann die Biegung dazu führen, dass der Außenradius reißt oder sogar bricht.
Es gibt auch einige Stahlbleche mit höherem Kohlenstoffgehalt.
Wenn Sie einen harten Zustand wählen, führt das Biegen auch zu Rissen oder sogar zum Bruch des Außenradius.
Diese sollten so weit wie möglich vermieden werden.
Auswirkung von Materialien auf die Bearbeitung von Zeichnungen
Das Dehnen des Blechs, insbesondere das Tiefziehen, ist eine schwierige Angelegenheit in der Blechverarbeitung Prozess.
Nicht nur die Tiefe der Dehnung muss so gering wie möglich sein, auch die Form muss so einfach wie möglich und glatt sein. Außerdem muss das Material eine gute Plastizität aufweisen.
Andernfalls wird das gesamte Teil leicht verformt, teilweise faltig oder sogar an der Streckstelle gezogen.
Die Streckgrenze ist niedrig und der Richtungskoeffizient der Blechdicke ist groß.
Je kleiner das Streckverhältnis σs/σb des Blechs ist, desto besser ist die Stanzleistung und desto größer ist die Grenze der Primärverformung.
Wenn der Richtwirkungskoeffizient der Blechdicke >1 ist, ist die Verformung in der Breitenrichtung leichter als die Verformung in der Dickenrichtung.
Je größer der Wert des Streckradius R ist, desto geringer ist die Wahrscheinlichkeit, dass er während des Streckvorgangs ausgedünnt wird und bricht, und desto besser sind die Zugeigenschaften.
Gängige Zugfestigkeitseigenschaften sind: reines Aluminiumblech, 08Al, ST16, SPCD.
Auswirkungen des Materials auf die Steifigkeit
Bei der Konstruktion von Blechkonstruktionen wird die Steifigkeit von Blechbauteilen oft nicht eingehalten.
Konstrukteure verwenden oft kohlenstoffarmen Stahl oder Edelstahl anstelle von kohlenstoffarmem Stahl oder ersetzen die gewöhnliche Aluminiumlegierung durch eine harte Aluminiumlegierung mit hoher Festigkeit und Härte, was die Steifigkeit des Teils erhöhen dürfte.
Es gibt eigentlich keine offensichtlichen Auswirkungen.
Bei Werkstoffen desselben Substrats können Festigkeit und Härte des Materials durch Wärmebehandlung und Legierung erheblich verbessert werden.
Die Veränderung der Steifigkeit ist jedoch gering.
Um die Steifigkeit des Teils zu verbessern, kann nur durch eine Änderung des Materials und der Form des Teils ein bestimmter Effekt erzielt werden.
Siehe Tabelle 1-2 für den Elastizitätsmodul und den Schermodul der verschiedenen Materialien.
Tabelle 1-2 Elastizitätsmodul und Schermodul gängiger Materialien
Elastizitätsmodul E | Schermodus G | |
---|---|---|
Artikel | GPa | GPa |
Grauguss | 118~126 | 44.3 |
Sphäroguss | 173 | |
Kohlenstoffstahl, Nickel-Chrom-Stahl | 206 | 79.4 |
Stahlguss | 202 | |
Gewalztes reines Kupfer | 108 | 39.2 |
Kaltgezogenes reines Kupfer | 127 | 48 |
Gewalzte Phosphorbronze | 113 | 41.2 |
Kaltgezogenes Messing | 89~97 | 34.3~36.3 |
Gewalzte Mangan-Bronze | 108 | 39.2 |
Gewalztes Aluminium | 68 | 25.5~26.5 |
Aluminiumdraht herausziehen | 69 | |
Aluminiumguss Bronze | 103 | 11.1 |
Gegossene Zinnbronze | 103 | |
Harte Aluminiumlegierung | 70 | 26.5 |
Walzbares Zink | 82 | 31.4 |
Blei | 16 | 6.8 |
Glas | 55 | 1.96 |
Plexiglas | 2.35~29.4 | |
Gummi | 0.0078 | |
Bakelit | 1.96~2.94 | 0.69~2.06 |
Phenolischer Kunststoff | 3.95~8.83 | |
Zelluloid | 1.71~1.89 | 0.69~0.98 |
Nylon 1010 | 1.07 | |
Hartes Tetrachlorethylen | 3.14~3.92 | |
Polytetrachlorethylen | 1.14~1.42 | |
Niederdruck-Polyethylen | 0.54~0.75 | |
Hochdruck-Polyethylen | 0.147~0.24 | |
Beton | 13.73~39.2 | 4.9~15.69 |
Leistungsvergleich häufig verwendeter Platten
Tabelle 1-3 Vergleich der Leistung verschiedener häufig verwendeter Platten
Preiskoeffizient | Überlappungswiderstand (mΩ) | CNC-Stanzbearbeitungsleistung | Laserbearbeitung Leistung | Biegeleistung | Einnietmuttertechnik | Technologie der Stanzniete | Oberflächenbeschichtung | Schutzwirkung der Inzision |
---|---|---|---|---|---|---|---|---|
1 | gut | gut | gut | gut | gut | Durchschnitt | Sehr gut | |
1.2 | 27 | gut | gut | gut | gut | gut | Durchschnitt | gut |
1.7 | 26 | gut | gut | gut | gut | gut | Durchschnitt | ärmste |
1.3 | 26 | gut | gut | gut | gut | gut | Durchschnitt | relativ arm |
1.4 | 23 | gut | gut | gut | gut | gut | Durchschnitt | arm |
6.5 | 60 | arm | gut | Durchschnitt | arm | sehr arm | arm | gut |
2.9 | 46 | Durchschnitt | extrem arm | gut | gut | gut | Durchschnitt | gut |
3 | 46 | Durchschnitt | extrem arm | extrem arm | gut | gut | Durchschnitt | gut |
5.6 | gut | extrem arm | gut | gut | gut | Durchschnitt | gut | |
5 | gut | extrem arm | gut | gut | gut | Durchschnitt | gut |
Anmerkung:
Piercing und Ausblendung von CNC-Stanzmaschine
Beim CNC-Stanzen und -Stanzen wird der Ein-Chip-Mikrocomputer der CNC-Stanzmaschine verwendet, um das Bearbeitungsprogramm (Größe, Bearbeitungsweg, Bearbeitungswerkzeug usw.) des Blechteils im Voraus einzugeben, wodurch die CNC-Stanzmaschine verschiedene Werkzeuge und eine Fülle von NC-Befehlen verwendet, um eine Vielzahl von Bearbeitungsformen wie Stanzen, Beschneiden, Formen usw. zu erreichen.
Das CNC-Stanzen ist im Allgemeinen nicht in der Lage, zu komplizierte Formen zu durchbohren und zu stanzen.
Merkmale:
Sie ist grundsätzlich in der Lage, die Anforderungen der Musterausstanzung zu erfüllen.
Aufmerksamkeitsprobleme und Anforderungen:
CNC-Stanzen eignet sich im Allgemeinen zum Stanzen von kohlenstoffarmem Stahl, elektrolytischem Blech, Aluminium-Zink-Blech, Aluminiumblech, Kupferblech mit T=3,5~4mm oder weniger und Edelstahlblech mit T=3mm oder weniger.
Die empfohlene Blechdicke für das CNC-Stanzen ist:
Das CNC-Stanzverfahren hat eine starke Verformung der Kupferplatte zur Folge, während der verarbeitende PC und die PVC-Platte große Bearbeitungsgrate und geringe Präzision aufweisen.
Beim Stanzen müssen der Durchmesser und die Breite des verwendeten Werkzeugs größer sein als die Dicke des Materials. Zum Beispiel kann ein Werkzeug mit einem Durchmesser von Φ1,5 nicht ein Material von 1,6 mm stanzen.
Materialien unter 0,6 mm werden im Allgemeinen nicht von NCT verarbeitet.
Materialien aus rostfreiem Stahl werden im Allgemeinen nicht mit NCT bearbeitet. (Natürlich kann 0,6~1,5mm Material mit NCT bearbeitet werden, aber der Werkzeugverschleiß ist groß und die Wahrscheinlichkeit von Ausschuss bei der Bearbeitung vor Ort ist viel höher als bei anderen GI-Materialien).
Das Lochen und Stanzen anderer Formen sollte so einfach und einheitlich wie möglich sein.
Die Größe der CNC-Stanze sollte normalisiert sein, wie z. B. runde Löcher, sechseckige Löcher, und die Mindestbreite der Bearbeitungsnut beträgt 1,2 mm.
Piercing und Ausblendung durch Kaltstempel
Für das Stanzen und Schneiden von Teilen mit großem Ausstoß und kleinen Abmessungen werden speziell entwickelte Blechstanzwerkzeuge hergestellt und verwendet, um die Produktionseffizienz zu steigern.
Er besteht im Allgemeinen aus einem Stempel und einer Matrize.
Die Matrize ist in der Regel: Press-in-Typ, und eingelegt Typ.
Die Stempel sind in der Regel: rund, austauschbar, kombiniert, schnell be- und entladbar.
Die gebräuchlichsten Stempel sind:
Merkmale:
Weil die Stanzen und Schneiden Die Effizienz ist hoch, die Konsistenz ist gut und die Kosten sind niedrig.
Daher wird bei Bauteilen mit einer jährlichen Verarbeitungskapazität von mehr als 5.000 Stück und einer nicht allzu großen Teilegröße in der Regel eine Kaltumformung durchgeführt.
Bei der Planung des Bauwerks muss die Gestaltung der Prozessmerkmale der Kaltverformung.
Zum Beispiel sollten die Teile keine scharfen Ecken haben (außer für den Gebrauch). Sie sollten so gestaltet sein, dass sie abgerundet sind, um die Qualität und Lebensdauer der Form zu verbessern und das Werkstück schön, sicher und haltbar zu machen.
Um die funktionalen Anforderungen zu erfüllen, kann die strukturelle Form des Teils komplizierter gestaltet werden.
Durchbohren mit dem dichten Locher
Die Stanze für dichte Löcher kann als eine Art numerisch gesteuerte Stanze betrachtet werden. Bei Teilen mit einer großen Anzahl von dichten Löchern können die Effizienz und die Präzision des Stanzens verbessert werden.
Ein speziell angefertigtes Stanzwerkzeug kann eine große Anzahl von dichten Löchern zur Bearbeitung des Werkstücks stanzen.
Wie z.B.: Lüftungsschablone, Zu- und Abluftleitbleche.
Siehe Abbildung 1-1.
Das schraffierte Teil in der Abbildung ist eine Form mit dichtem Loch, und das dichte Loch des Teils kann durch die Form mit dichtem Loch schnell ausgestanzt werden. Im Vergleich zu einem Stempel wird die Effizienz erheblich verbessert.
Probleme und Anforderungen bei der Anordnung dichter Löcher
Bei der Gestaltung des dichten Lochs auf dem Produkt sollte berücksichtigt werden, dass die Verarbeitungseigenschaften des dichten Lochs mehrfach gestanzt werden, so dass das folgende Prinzip bei der Gestaltung der Anordnung des dichten Lochs angenommen werden sollte:
Die Form mit dichtem Loch aus Abbildung 1-1 a kann wie in Abbildung 1-4 gezeigt gestaltet werden.
Die Form mit dichtem Loch in Abbildung 1-1 b kann nur wie in Abbildung 1-5 gezeigt gestaltet werden.
Bei der Gestaltung der Anordnung von dichten Löchern, versuchen Sie, nach den oben genannten Anforderungen zu entwerfen, und kontinuierlich und haben eine gewisse Regelmäßigkeit, die für das Öffnen des Lochs Form und die Verringerung der Stanzen Kosten bequem ist.
Andernfalls können nur wenige Stempel oder eine Reihe von Formsätzen verwendet werden, um die Bearbeitung abzuschließen.
Wie in Abbildung 1-6 dargestellt,
Laserschneiden
Das Laserschneiden ist eine berührungslose Schneidetechnik, bei der eine Elektronenentladung als Energiequelle genutzt wird, um einen Laser fokussieren Strahl als Wärmequelle unter Verwendung einer reflektierenden Spiegelgruppe. Diese hochverdichtete Lichtenergie wird zum Stanzen und Schneiden von Blechteilen verwendet.
Merkmale:
Die Kosten sind jedoch hoch, und gleichzeitig wird der Auflagetisch des Werkstücks beschädigt, und auf der Schnittfläche kann sich leicht eine Oxidschicht absetzen, die schwer zu handhaben ist.
Im Allgemeinen nur für Einzel- und Kleinserienverarbeitung geeignet.
Achtung: wird im Allgemeinen nur für Stahlplatten verwendet.
Aluminium- und Kupferplatten werden in der Regel nicht verwendet, da die Wärmeübertragung des Materials zu schnell erfolgt, was zu einem Schmelzen um den Einschnitt herum führt und die Genauigkeit und Qualität der Bearbeitung nicht gewährleistet.
Die Laserschneiden Die Stirnfläche weist eine Oxidschicht auf, die nicht abgewaschen werden kann, und die Schneidestirnfläche mit besonderen Anforderungen sollte poliert werden;
Laserschneiden dichte Löcher sind mehr verformt, in der Regel nicht den Laser verwenden, um dichte Löcher schneiden.
Drahterodieren
Das Drahtschneiden ist ein Bearbeitungsverfahren, bei dem ein Werkstück und ein Draht (Molybdändraht, Kupferdraht) jeweils als Pol verwendet und in einem bestimmten Abstand gehalten werden, wobei sich bei einer ausreichend hohen Spannung eine Funkenstrecke bildet, und das Werkstück elektrolytisch geätzt wird. Das abgetragene Material wird von der Arbeitsflüssigkeit abtransportiert.
Merkmale: hohe Bearbeitungsgenauigkeit, aber niedrige Bearbeitungsgeschwindigkeit, hohe Kosten und Veränderung der Oberflächeneigenschaften des Materials.
Im Allgemeinen für die Bearbeitung von Formen verwendet, nicht für die Bearbeitung von Produktionsteilen.
Einige quadratische Löcher in den Profiltafeln haben keine abgerundeten Ecken, die nicht gefräst werden können, und da Aluminiumlegierungen nicht mit dem Laser geschnitten werden können, können sie, wenn kein Stanzraum vorhanden ist, nur durch Drahterodieren gestanzt werden.
Die Geschwindigkeit ist sehr langsam, der Wirkungsgrad ist sehr gering, und es ist nicht für die Massenproduktion geeignet. Die Konstruktion sollte diese Situation vermeiden.
Vergleich der drei gebräuchlichen Ausblendungs- und piercMethoden
Tabelle 1-4 Vergleich dreier gängiger Stanz- und Schneidebearbeitungsmerkmale
Hinweis: Bei den folgenden Daten handelt es sich um Daten für Kaltgewalzte Stahlbleche.
Laser | Schneiden | Stanzen | |
---|---|---|---|
Bearbeitbares Material | Stahlplatte | Stahlblech, Kupferblech, Aluminiumblech | Stahlblech, Kupferblech, Aluminiumblech |
Bearbeitbare Materialstärke | 1mm ~ 8mm | 0,6 mm ~ 3 mm | allgemein <4mm |
Mindestmaß der Verarbeitung (normales kaltgewalztes Stahlblech) | Mindestschlitz 0,2 mm | Stanzloch Ø≧t | Stanzloch Ø≧t |
Minimaler Kreis 0,7 mm | Quadratisches Loch kleiner Rand W≧t | Quadratisches Loch kleiner Rand W≧t | |
Breite der langen Rille W≧t | Breite der langen Rille W≧2t | ||
Mindestabstand zwischen Loch und Loch, Loch und Kante | ≧t | ≧t | ≧1t |
Vorzugsweise ist der Abstand zwischen den Löchern und Löchern, Löchern und den Kanten | ≧1.5t | ≧1.5t | ≧1.5t |
Allgemeine Bearbeitungsgenauigkeit | ±0,1mm | ±0,1mm | ±0,1mm |
Verarbeitungsbereich | 2000X1350 | 2000X1350 | |
Wirkung des Erscheinungsbildes | Glatte Außenkante, eine Zunderschicht an der Schnittfläche | Große rohe Kanten mit Graten | ein kleiner Anteil an rohen Kanten |
Kurveneffekt | Glatte, veränderbare Form | Große Grate und regelmäßige Formen; | Glatte, veränderbare Form |
Verarbeitungsgeschwindigkeit | Schnelles Ausschneiden des äußeren Kreises | Schnelles Stanzen von dichten Löchern | schnellste |
Textverarbeitung | Radierung, flacher, unbegrenzte Größe | Geprägter konkaver Text mit tieferen Symbolen; die Größe ist durch die Form begrenzt | Geprägter konkaver Text mit tieferen Symbolen; die Größe ist durch die Form begrenzt |
Bildung von | kann nicht | Konkave, Senkung, kleine Dehnung, etc. | Ermöglicht komplexere Formen |
Verarbeitungskosten | Höher | Niedrig | Niedrig |
Ttechnische Gestaltung von die arung
In der Großserien- und Mittelserienfertigung machen die Materialkosten der Teile einen großen Teil aus.
Die vollständige und effektive Nutzung von Materialien ist ein wichtiger wirtschaftlicher Indikator für die Blechproduktion.
Unter der Voraussetzung, dass die Anforderungen an die Konstruktion nicht beeinträchtigt werden, sollte der Konstrukteur daher versuchen, eine abfallfreie oder abfallarme Anordnungsmethode zu wählen.
Wie in Abbildung 1-7 zu sehen ist, gibt es keine Abfallanordnung.
Einige Teile haben eine leicht veränderte Form, wodurch viel Material eingespart werden kann.
Wie in Abbildung 1-8 gezeigt, wird in Abbildung 2 weniger Material verwendet als in Abbildung 1.
Verarbeitbarkeit von Stanzteilen
Damit die CNC-Stanzmaschine den Außenradius bearbeiten kann, ist ein spezielles externes Werkzeug erforderlich. Um das Außenkreiswerkzeug zu reduzieren, ist die Standard-Eckenrundung dieses Handbuchs wie in Abbildung 1-9 dargestellt:
1) 90 Grad rechtwinklige Abrundungsreihe, der Radius ist r2.0, r3.0, r5.0, r10
2) Der Radius der abgeschrägten 135-Grad-Ecke ist einheitlich auf R5.0
Bei runden Löchern wird das Stanzen bevorzugt.
Die runden Löcher sollten entsprechend der im Handbuch der Blechform angegebenen Reihe von runden Löchern ausgewählt werden.
Dadurch kann die Anzahl der Rundlochwerkzeuge reduziert und die Zeit für den Messerwechsel beim CNC-Stanzen verringert werden.
Aufgrund der begrenzten Stempelstärke kann die Öffnung nicht zu klein sein. Die Mindestöffnung hängt von der Materialstärke ab.
Der Mindestdurchmesser des Lochs sollte nicht kleiner sein als der in Tabelle 1-5 angegebene Wert.
Tabelle 1-5 Mindestgröße für das Stanzen mit einem herkömmlichen Stempel
Der minimale Durchmesser oder die minimale Kantenlänge des Stempels (t ist die Materialstärke) | |||
---|---|---|---|
Material | Rundes Loch D(D ist Durchmesser) | Quadratisches Loch L(L ist Kantenlänge) | Taillenloch, rechteckiges Loch a(a ist die minimale Kantenlänge) |
Stahl mit hohem und mittlerem Kohlenstoffgehalt | ≥1.3t | ≥1.2t | ≥1t |
Kohlenstoffarmer Stahl und Messing | ≥1t | ≥0.8t | ≥0.8t |
Aluminium, Zink | ≥0.8t | ≥0.6t | ≥0.6t |
Stoff-Bakelit-Laminat | ≥0.4t | ≥0.35t | ≥0.3t |
Der Abstand zwischen den Löchern und zwischen dem Loch und dem Rand sollte nicht zu klein sein. Der Wert ist in Abbildung 1-10 dargestellt:
Die Präzision zwischen der Bohrung und der Form, der Bohrung und der Bohrung, die durch die zusammengesetzte Form verarbeitet werden, ist bei der Herstellung leicht zu gewährleisten. Prägeverfahren der Form.
Außerdem ist die Verarbeitungseffizienz hoch, und die Wartungskosten der Form sind günstig.
In Anbetracht der oben genannten Gründe, der Abstand zwischen dem Loch und das Loch, wenn der Abstand zwischen dem Loch und die Form kann die Mindestwandstärke Anforderung der Composite-Form, das Verfahren ist besser, wie in Abbildung 1-11:
Tabelle 1-6 Mindestgröße des Randes der Verbundstempelausstanzung
t (<0.8 ) | t (0.8~1.59) | t (1.59~3.18) | t (>3.2) | |
---|---|---|---|---|
D1 | 3mm | 2t | ||
D2 | 3mm | 2t | ||
D3 | 1,6 mm | 2t | 2.5t | |
D4 | 1,6 mm | 2t | 2.5t |
Wie in Abbildung 1-12 dargestellt, wird zuerst durchbohrt und dann gebogen. Um sicherzustellen, dass das Loch nicht verformt wird, muss der Mindestabstand zwischen dem Loch und dem Flansch X≥2t+R
Beim Stanzen von Löchern in Tiefziehteile, siehe Abbildung 1-13, sollten die Lochwand und die gerade Wand der Teile einen bestimmten Abstand haben, d. h. die Abstände a1 und a2 sollten die folgenden Anforderungen erfüllen, um die Form- und Positionsgenauigkeit der Löcher und die Festigkeit der Form zu gewährleisten:
In der Formel steht R1, R2 für den Eckenradius und t für die Dicke.
Bearbeitungsgenauigkeit von Stanzteilen
Tabelle 1-7 Toleranztabelle von Lochmittenabstand (Einheit:mm)
Gewöhnliche Stanzgenauigkeit | Erweiterte Stanzgenauigkeit | |||||
---|---|---|---|---|---|---|
Nenngröße L | Nenngröße L | |||||
Dicke | <50 | 50~150 | 150~300 | <50 | 50~150 | 150~300 |
<1 | ±0.1 | ±0.15 | ±0.20 | ±0.03 | ±0.05 | ±0.08 |
1~2 | ±0.12 | ±0.20 | ±0.30 | ±0.04 | ±0.06 | ±0.10 |
2~4 | ±0.15 | ±0.25 | ±0.35 | ±0.06 | ±0.08 | ±0.12 |
4~6 | ±0.20 | ±0.30 | ±0.40 | ±0.08 | ±0.10 | ±0.15 |
Hinweis: Bei Verwendung der Werte in dieser Tabelle sollten alle Löcher einmal ausgestanzt werden.
Auswahlprinzip für die Größe des Stanzteils
1) Der Entwurfsmaßbezug des Stanzteils ist so nah wie möglich am hergestellten Positionierungsbezug, so dass der Herstellungsfehler des Maßes vermieden werden kann.
2) Die Lochgrößenreferenz des Stanzteils sollte so weit wie möglich vom Anfang bis zum Ende des Stanzprozesses gewählt werden und sollte nicht mit dem an der Verformung beteiligten Teil verbunden sein.
3) Für Teile, die in mehreren Schritten auf verschiedene Formen verteilt und geprägt werden, sollte so oft wie möglich derselbe Positionsbezug verwendet werden.
Tabelle 1-8 Toleranztabelle von Lochmitte und Randabstand
Dicke | Größen b | |||
---|---|---|---|---|
≤50 | 50<b≤120 | 120<b≤220 | 220<b≤360 | |
<2 | ±0.2 | ±0.3 | ±0.5 | ±0.7 |
≥2~4 | ±0.3 | ±0.5 | ±0.6 | ±0.8 |
>4 | ±0.4 | ±0.5 | ±0.8 | ±1.0 |
Hinweis: Dieser Tisch ist für das Lochen nach dem Stanzen geeignet.
Sekundäres Schneiden
Das sekundäre Schneiden wird auch als sekundäres Stanzen oder zusätzliches Schneiden bezeichnet (ein sehr schlechtes Verfahren, das bei der Konstruktion vermieden werden sollte).
Das sekundäre Schneiden besteht darin, dass das Dehnen eine Verformung des Materials bewirkt. Wenn die Biegeverformung groß ist, wird der Zuschnitt erhöht. Zuerst wird geformt, dann werden Löcher oder Konturen geschnitten, um das reservierte Material zu entfernen und die vollständige korrekte Strukturgröße zu erhalten.
Anwendung: Wenn die Spannnase nahe an der Kante liegt, muss ein zusätzlicher Schnitt durchgeführt werden.
Nehmen Sie als Beispiel die Senkbohrung, wie in Abbildung 1-16 dargestellt.
Sie können diesen Beitrag lesen um alle Einzelheiten über das Blechbiegen zu erfahren.
Gängige Formen von Einnietmuttern sind selbstsichernde Abstandshalter, selbstsichernde Muttern, Ankernietmuttern, Zugnietmuttern und schwimmende Einnietmuttern.
SElfenhaftes Unentschieden
Stanznieten bedeutet, dass in der NietverfahrenUnter dem äußeren Druck verformt das Nietteil das Basismaterial plastisch und wird in die vorgefertigte Nut gepresst, die speziell in der genieteten Schrauben-Mutter-Struktur entworfen wurde, wodurch die zuverlässige Verbindung der beiden Teile realisiert wird.
Es gibt zwei Arten von nicht genormten Nietmuttern: eine selbstklemmende Abstandshalterung und eine selbstklemmende Mutter.
Die Verbindung mit dem Untergrund wird durch eine solche Nietform hergestellt.
Solche Nietformen erfordern in der Regel, dass das genietete Teil eine größere Härte aufweist als das Substrat.
Gewöhnlicher kohlenstoffarmer Stahl, Bleche aus Aluminiumlegierungen und Kupferbleche eignen sich zum Verpressen des selbstklemmenden Abstandhalters.
Für Bleche aus rostfreiem Stahl und Stahl mit hohem Kohlenstoffgehalt ist aufgrund des harten Materials eine spezielle hochfeste Nietmutter erforderlich, die nicht nur teuer, sondern auch schwer zu verpressen ist, und die Verpressung ist nicht zuverlässig, und sie kann nach der Verpressung leicht abfallen.
Um die Zuverlässigkeit zu gewährleisten, müssen die Hersteller oft Schweißnähte an der Seite der Mutternsäule anbringen, was nicht gut für den Prozess ist.
Deshalb sind die Blechteile mit der Einnietmuttersäule und der Einnietmutter möglichst nicht rostfrei.
Dies gilt auch für Einnietschrauben und Einnietmuttern, die für die Verwendung auf Edelstahlblechen nicht geeignet sind.
Der Crimpvorgang der Einnietmuttersäule ist in Abbildung 1-41 dargestellt:
Self-klingende Einnietmutter
Der Crimpvorgang der Nietschraube ist in Abbildung 1-42 dargestellt:
AAnkereinnietmutter
Beim Dübelnieten wird ein Teil des Materials der vernieteten Schraube oder Mutter unter der Einwirkung einer äußeren Kraft plastisch verformt und ein fester Sitz mit dem Grundmaterial hergestellt, wodurch eine zuverlässige Verbindung der beiden Teile erreicht wird.
Das üblicherweise verwendete ZRS wird durch diese Nietart mit dem Untergrund verbunden.
Das Nietverfahren ist relativ einfach, die Verbindungsfestigkeit ist gering und wird in der Regel verwendet, um die Höhe des Verbindungselements zu begrenzen und einem geringen Drehmoment standzuhalten. Wie in Abbildung 1-43 dargestellt:
Ziehen Sie Einnietmutter
Beim Zugnieten wird das Nietelement während des Nietvorgangs unter der Einwirkung einer äußeren Spannung plastisch verformt.
Die Position der Verformung befindet sich in der Regel in einem speziell entwickelten Teil, und das Substrat wird durch den Verformungsteil geklemmt, um eine zuverlässige Verbindung zu erreichen.
Die üblicherweise verwendeten Einnietmuttern werden durch diese Nietart mit dem Untergrund verbunden.
Die Vernietung erfolgt mit einer speziellen Nietpistole, die häufig dort eingesetzt wird, wo der Einbauraum klein ist und keine Universalnietwerkzeuge verwendet werden können, wie z. B. bei geschlossenen Rohren. Wie in Abbildung 1-44 dargestellt:
FEinnietmutter
Einige der Nietmuttern auf der Blechstruktur, weil die gesamte Chassis-Struktur ist komplex, die Akkumulation Fehler der Struktur ist zu groß, so dass die relative Position Fehler dieser Nietmuttern ist groß, was die Montage von anderen Teilen schwierig.
Dies ist eine gute Verbesserung gegenüber der Verwendung einer vernieteten schwimmenden Mutter an der Stelle der entsprechenden Einnietmutter.
Wie in Abbildung 1-45 gezeigt: (Hinweis: In der Nietposition muss genügend Platz vorhanden sein)
Verankerung rIvet-Mutter oder selbstsichernd Einnietmutter zum Seitenabstand
Die Verankerungsnietmutter oder die selbstsichernde Nietmutter werden durch Zusammendrücken des Blechs mit diesem vernietet.
Wenn die Ankerniete oder die selbstklemmende Niete zu nahe an der Kante liegt, kann dieses Teil leicht verformt werden.
Wenn keine besonderen Anforderungen bestehen, sollte der Mindestabstand zwischen der Mittellinie des genieteten Befestigungselements und dem Rand des Blechs größer als L sein, siehe Abbildung 1-46.
Andernfalls müssen spezielle Klemmen verwendet werden, um zu verhindern, dass die Kanten des Blechs mit Gewalt verformt werden.
Faktoren, die die Qualität von Nieten beeinflussen
Es gibt viele Faktoren, die die Qualität der Nietung beeinflussen. Zusammenfassend kann man sagen, dass es hauptsächlich die folgenden sind: Leistung des Substrats, Größe des Bodenlochs und Nietmethode.
1) Substrateigenschaften.
Wenn die Härte des Substrats angemessen ist, ist die Nietqualität gut, und die Kraft des Nietelements ist gut.
2) Größe des Bodenlochs.
Die Größe des Bodenlochs wirkt sich direkt auf die Qualität der Nietung aus. Wenn die Öffnung groß ist, ist der Spalt zwischen dem Substrat und dem Niet groß.
Beim Nieten darf die Verformung nicht ausreichen, um die Nut des Nietstücks auszufüllen, so dass die Scherkraft unzureichend ist, was sich direkt auf den Druckwiderstand der Einnietmutter (des Nagels) auswirkt.
Bei der Nietschraube ist das untere Loch zu groß, und die durch die plastische Verformung während des Nietvorgangs erzeugte Druckkraft ist gering, was sich direkt auf den Schubwiderstand und die Torsionsfestigkeit der Nietschraube (Innengewinde) auswirkt.
Auch beim Nieten ist das untere Loch zu groß, so dass die effektive Reibung zwischen den beiden Teilen nach der plastischen Verformung verringert wird, was die Qualität der Nietung beeinträchtigt.
Die Größe des Bodenlochs ist klein, und obwohl die Nietkraft bis zu einem gewissen Grad erhöht werden kann, ist die Qualität des Nietbildes wahrscheinlich schlecht.
Die Nietkraft ist groß, die Installation ist umständlich, und die Verformung der Bodenplatte wird leicht verursacht, was die Produktionseffizienz der Nietarbeit und die Qualität der Nietung beeinträchtigt.
3) Nietverfahren.
Sie wurde bereits im vorherigen Abschnitt vorgestellt. Bei der Verwendung von Nietschrauben und Nietmuttern sollte man den Gelegenheiten große Aufmerksamkeit schenken. Unterschiedliche Situationen und unterschiedliche Kraftanforderungen erfordern unterschiedliche Typen.
Bei unsachgemäßer Anwendung wird der Kraftbereich der Nietschrauben und -muttern reduziert, was zum Versagen der Verbindung führt.
Hier sind einige Beispiele, die die korrekte Verwendung der normalen Situation veranschaulichen.
1) Montieren Sie keine genieteten Befestigungselemente aus Stahl oder Edelstahl, bevor die Aluminiumplatte eloxiert oder oberflächenbehandelt ist.
2) Wird zu viel auf einer geraden Linie genietet, hat das extrudierte Material keinen Platz zum Fließen, was zu großen Spannungen führt und das Werkstück in eine gekrümmte Form biegt.
3) Versuchen Sie sicherzustellen, dass die Oberfläche der Platte vor dem Anbringen der Nietbefestigungen beschichtet ist.
4) M5-, M6-, M8- und M10-Muttern werden im Allgemeinen geschweißt. Zu große Muttern erfordern im Allgemeinen eine hohe Festigkeit. Lichtbogenschweißen verwendet werden kann. Unterhalb von M4 (einschließlich M4) sollte die Anker-Nietmutter verwendet werden. Wenn sie galvanisch beschichtet ist, kann die Einnietmutter mit stromloser Beschichtung verwendet werden.
5) Beim Einnieten der Mutter auf der gebogenen Seite ist es zur Sicherstellung der Nietqualität der Einnietmutter notwendig, auf Folgendes zu achten: 1.
Der Abstand zwischen dem Rand des Nietlochs und der Seite der Biegung muss größer sein als die Verformungszone des gebogenen Teils. 2.
Der Abstand L von der Mitte der Einnietmutter zur Innenseite der gebogenen Seite sollte größer sein als die Summe aus dem äußeren zylindrischen Radius der Einnietmutter und dem inneren Radius der Biegung. Das heißt, L>D/2+r.
Die Buckelschweißung Mutter (Punktschweißmutter) wird häufig bei der Konstruktion von Blechteilen verwendet.
Bei vielen Entwürfen entspricht die Größe des Vorlochs jedoch nicht der Norm und kann nicht genau positioniert werden.
Die Konstruktionsart und die Abmessungen sind in Abbildung 1-47 und Abbildung 1-48 dargestellt. Die empfohlenen Werte für den Lochdurchmesser D0 und die Dicke H vor dem Schweißen der Stahlplatte zum Schweißen sind in Tabelle 1-17 angegeben.
Tabelle 1-17 Abmessungen der geschweißten Sechskantmutter und Öffnungsdicke der entsprechenden Stahlplatte (mm)
Gewindegröße (D oder D×P) | M4 | M5 | M6 | M8 | M10 | M12 | M16 | |
---|---|---|---|---|---|---|---|---|
─ | ─ | ─ | M8×1 | M10×1 | M12×1. 5 | M16×1. 5 | ||
─ | ─ | ─ | ─ | (M10×1.25) | (M12×1. 25) | ─ | ||
e | min | 9.83 | 10.95 | 12.02 | 15.38 | 18.74 | 20.91 | 26.51 |
dy | max | 5.97 | 6.96 | 7.96 | 10.45 | 12.45 | 14.75 | 18.735 |
min | 5.885 | 6.87 | 7.87 | 10.34 | 12.34 | 14.64 | 18.605 | |
h1 | max | 0.65 | 0.7 | 0.75 | 0.9 | 1.15 | 1.4 | 1.8 |
min | 0.55 | 0.6 | 0.6 | 0.75 | 0.95 | 1.2 | 1.6 | |
h2 | max | 0.35 | 0.4 | 0.4 | 0.5 | 0.65 | 0.8 | 1 |
min | 0.25 | 0.3 | 0.3 | 0.35 | 0.5 | 0.6 | 0.8 | |
m | max | 3.5 | 4 | 5 | 6.5 | 8 | 10 | 13 |
min | 3.2 | 3.7 | 4.7 | 6.14 | 7.64 | 9.64 | 12.3 | |
D0 | max | 6.075 | 7.09 | 8.09 | 10.61 | 12.61 | 14.91 | 18.93 |
min | 6 | 7 | 8 | 10.5 | 12.5 | 14.8 | 18.8 | |
H | max | 3 | 3.5 | 4 | 4.5 | 5 | 5 | 6 |
min | 0.75 | 0.9 | 0.9 | 1 | 1.25 | 1.5 | 2 |
Hinweis: Verwenden Sie die Angaben in Klammern so wenig wie möglich.
Übliche Grobgewindebohrergröße
Gewindedurchmesser M | Dicke t | Innendurchmesser D1 | Außendurchmesser D2 | Höhe h | Vorstanzdurchmesser D0 | Radius |
---|---|---|---|---|---|---|
M2.5 | 0.6 | 2.1 | 2.8 | 1.2 | 1.4 | 0.3 |
0.8 | 2.8 | 1.44 | 1.5 | 0.4 | ||
1 | 2.9 | 1.8 | 1.2 | 0.5 | ||
1.2 | 2.9 | 1.92 | 1.3 | 0.6 | ||
M3 | 1 | 2.55 | 3.5 | 2 | 1.4 | 0.5 |
1.2 | 3.5 | 2.16 | 1.5 | 0.6 | ||
1.5 | 3.5 | 2.4 | 1.7 | 0.75 | ||
M4 | 1 | 3.35 | 4.46 | 2 | 2.3 | 0.5 |
1.2 | 4.5 | 2.16 | 2.3 | 0.6 | ||
1.5 | 4.65 | 2.7 | 1.8 | 0.75 | ||
2 | 4.56 | 3.2 | 2.4 | 1 | ||
M5 | 1.2 | 4.25 | 5.6 | 2.4 | 3 | 0.6 |
1.5 | 5.75 | 3 | 2.5 | 0.75 | ||
2 | 5.75 | 3.6 | 2.7 | 1 | ||
2.5 | 5.75 | 4 | 3.1 | 1.25 |
Der Mindestabstand von der Anbohrung zur Biegekante
Tabelle 1-19 Abstand zwischen der Gewindemitte und der Biegekante H-Wert-Vergleichstabelle
Dicke/Gewindedurchmesser | 1 | 1.2 | 1.5 | 2 |
---|---|---|---|---|
M3 | 6.2 | 6.6 | - | - |
M4 | 7.7 | 8 | - | |
M5 | - | 7.6 | 8.4 | - |
Tabelle 1-20 Vergleich der Einnietmutter, der selbstsichernden Mutter, des Zugnietens und des Gewindebohrens
Verbindungsmethode / Merkmal | Verankerungsnietmutter | selbstsichernde Einnietmutter | Zugnieten | Bördeln & Gewindeschneiden |
---|---|---|---|---|
Verarbeitbarkeit | es ist gut | gut | gut | Durchschnitt |
Anforderungen an Bleche | Nieten aus rostfreiem Stahl, die leicht abfallen können | Nieten aus Edelstahl ist sehr schlecht, verwenden Sie spezielle Nietmuttern, und benötigen Punktschweißen | keine | Dünnes Blech und Kupfer, Aluminium weiches Material leicht zu rutschen |
Präzision | gut | gut | gut | Durchschnitt |
Dauerhaftigkeit | gut | gut | gut | Kupfer und Aluminium weiche Materialien sind schlecht, andere Materialfäden haben 3 bis 4 Knickstellen oder mehr |
Kosten | hoch | hoch | Durchschnitt | niedrig |
Qualität | gut | gut | gut | Durchschnitt |
Die Blechstrecke ist in Abbildung 1-50 dargestellt.
Überlegungen zum Strecken von Blechen:
Für die Form und Größe des konvexen Blechs sind im Handbuch der Blechform mehrere Seriengrößen angegeben. Es gibt ein entsprechendes Formmodell in der Intralink-Bibliothek.
Das Design sollte entsprechend der im Handbuch angegebenen Größe ausgewählt werden, und die Form aus der Bibliothek wird direkt verwendet.
Begrenzung der Größe der konvexen Teilung und des konvexen Randes
Tabelle 1-21 Grenzabmessungen der konvexen Teilung und des konvexen Randes
Schematische Darstellung | L | B | D |
---|---|---|---|
![]() | 6.5 | 10 | 6 |
8.5 | 13 | 7.5 | |
10.5 | 15 | 9 | |
13 | 18 | 11 | |
15 | 22 | 13 | |
18 | 26 | 16 | |
24 | 34 | 20 | |
31 | 44 | 26 | |
36 | 51 | 30 | |
43 | 60 | 35 | |
48 | 68 | 40 | |
55 | 78 | 45 |
Wie in 1-52 gezeigt, kann eine 0,3-Zoll-Halbschnittprägung auf Blech als Aufkleber für ein Etikett oder ähnliches verwendet werden, um die Zuverlässigkeit des Etiketts zu verbessern.
Die Verformung ist viel geringer als die normale Streckung, aber es gibt immer noch eine gewisse Verformung für eine großflächige Deckplatte und eine Bodenplatte, die nicht gebogen ist oder eine geringe Biegehöhe hat.
Alternative Methode: Zur Verbesserung der Verformung können zwei rechtwinklige Linien in den Beschriftungsbereich gestanzt werden.
Allerdings ist die Zuverlässigkeit der Etikettenanbringung geringer.
Diese Methode kann auch für die Verarbeitung von Produktkodierung, Produktionsdatum, Version und sogar Muster verwendet werden.
Das Aufpressen der Rippen auf die plattenförmigen Metallteile, siehe Abbildung 1-53, trägt zur Erhöhung der strukturellen Steifigkeit bei.
Wie in Abbildung 1-54 dargestellt,
Die Bohren Nieten ist ein Nietverfahren zwischen Blechen, das hauptsächlich für die Verbindung von beschichteten Stahlblechen oder Edelstahlblechen verwendet wird.
Eines der Teile ist gestanzt, das andere gestanzt und mit einer Manschette versehen, um es zu einem nicht lösbaren Verbinder zu machen.
Vorteile: der Flansch ist mit dem geraden Loch abgestimmt, und es hat die Positionierungsfunktion selbst. Die Nietfestigkeit ist hoch, und die Nieteffizienz durch die Form ist auch hoch.
Der konkrete Weg ist in Abbildung 1-55 dargestellt:
Tabelle 1-22 Bohrnietabmessungen
Parameter | Dicke T(mm) | Flanschen Höhe H(mm) | Flansch-Außendurchmesser D(mm) | |||||||||||
---|---|---|---|---|---|---|---|---|---|---|---|---|---|---|
Nein. | 3 | 3.8 | 4 | 4.8 | 5 | 6 | ||||||||
Entsprechender Innen-Ø der geraden Bohrung d und Vorlochung d0 | ||||||||||||||
d | d0 | d | d0 | d | d0 | d | d0 | d | d0 | d | d0 | |||
1 | 0.5 | 1.2 | 2.4 | 1.5 | 3.2 | 2.4 | 3.4 | 2.6 | 4.2 | 3.4 | ||||
2 | 0.8 | 2 | 2.3 | 0.7 | 3.1 | 1.8 | 3.3 | 2.1 | 4.1 | 2.9 | 4.3 | 3.2 | ||
3 | 1 | 2.4 | 3.2 | 1.8 | 4 | 2.7 | 4.2 | 2.9 | 5.2 | 4 | ||||
4 | 1.2 | 2.7 | 3 | 1.2 | 3.8 | 2.3 | 4 | 2.5 | 5 | 3.6 | ||||
5 | 1.5 | 3.2 | 2.8 | 1 | 3.6 | 1.7 | 3.8 | 2 | 4.8 | 3.2 |
Anmerkung: Nach dem allgemeinen Prinzip H=T+T'+(0,3~0,4)
D = D'-0,3;
D-d=0,8T
Bei T≧0,8mm beträgt die Wandstärke der Flanschbohrung 0,4T.
Wenn T<0,8 mm ist, beträgt die Wandstärke des Flansches normalerweise 0,3 mm. H ist in der Regel 0,46±0,12
Beim Nieten von Blechen gibt es auch eine Nietmethode, das Tox-Nieten.
Das Prinzip besteht darin, dass zwei Stapel zusammengelegt werden, wie in Abbildung 1-56 dargestellt.
Stanzen und Ziehen mit Hilfe einer Form, die hauptsächlich für die Verbindung von beschichteten Stahlblechen oder Edelstahlblechen verwendet wird.
Sie hat die Vorteile der Energieeinsparung, des Umweltschutzes und der hohen Effizienz.
In der Vergangenheit wurden die Fahrgestelle in der Kommunikationsbranche häufiger vernietet, aber die Qualitätskontrolle bei der Massenproduktion war schwierig. Sie wurde weniger angewendet und wird nicht empfohlen.
Die Konstruktionsmaße der Schneckensenkung werden wie in der folgenden Tabelle angegeben gewählt.
Wenn die Platte für den Senkkopf der Senkkopfschraube zu dünn ist, ist es schwierig, das Durchgangsloch d2 und die Senkung D gleichzeitig zu gewährleisten, und das Durchgangsloch d2 sollte bevorzugt gewährleistet werden.
Der Senkkopf und das Durchgangsloch für Senkkopfschrauben: (Die gewählte Blechdicke t ist vorzugsweise größer als h)
Tabelle 1-23 Abmessungen der Schraubensenkung
![]() | d1 | M2 | M2.5 | M3 | M4 | M5 |
---|---|---|---|---|---|---|
d2 | Φ2.2 | Φ2.8 | Φ3.5 | Φ4.5 | Φ5.5 | |
D | Φ4.0 | Φ5.0 | Φ6.0 | Φ8.0 | Φ9.5 | |
h | 1.2 | 1.5 | 1.65 | 2.7 | 2.7 | |
Bevorzugte Mindestdicke | 1.2 | 1.5 | 1.5 | 2 | 2 | |
α | 90° |
Tabelle 1-24 Abmessungen der Senkbohrungen für Lochsenknieten
![]() | d1 | Φ2 | Φ2.5 | Φ3 | Φ4 | Φ5 |
---|---|---|---|---|---|---|
d2 | Φ2.2 | Φ2.7 | Φ3.3 | Φ4.3 | Φ5.3 | |
D | Φ4.0 | Φ5.0 | Φ5.5 | Φ7.0 | Φ9.0 | |
h | 1 | 1.1 | 1.2 | 1.6 | 2 | |
α | 120° |
Die Verbindung der Bleche erfolgt mit M3-Senkkopfschrauben.
Wenn die Dicke des plattierten Lochs 1 mm beträgt, ist es nach der herkömmlichen Methode problematisch.
In der Praxis stößt man jedoch auf eine Vielzahl solcher Probleme.
Die Einnietmutter wird unten verwendet, und der Durchmesser der Senkung beträgt 6 mm, womit die Verbindung effektiv hergestellt werden kann, wie in der Abbildung gezeigt.
Diese Größe wird in einer großen Anzahl von Einlegekästen verwendet.
Es ist wichtig zu beachten, dass bei dieser Art der Verbindung die untere Mutter eine Ankernietmutter sein muss.
Die selbstsichernde Einnietmutter und der Gewindeschneider können die Verbindung nicht herstellen.
Um solche Abmessungen zu standardisieren, sollte das d/D wie folgt sein:
Tabelle 1-25 Vereinheitlichung von Dünnplattensenkungen
Blechdicke | 1 | 1.2 | 1.5 |
---|---|---|---|
M3 | 4/6 | 3.6/6.0 | 3.5/6 |
M4 | - | - | 5.8/8.8 |
Als Gründer von MachineMFG habe ich mehr als ein Jahrzehnt meiner Karriere der metallverarbeitenden Industrie gewidmet. Meine umfangreiche Erfahrung hat es mir ermöglicht, ein Experte auf den Gebieten der Blechverarbeitung, der maschinellen Bearbeitung, des Maschinenbaus und der Werkzeugmaschinen für Metalle zu werden. Ich denke, lese und schreibe ständig über diese Themen und bin stets bestrebt, in meinem Bereich an vorderster Front zu bleiben. Lassen Sie mein Wissen und meine Erfahrung zu einem Gewinn für Ihr Unternehmen werden.