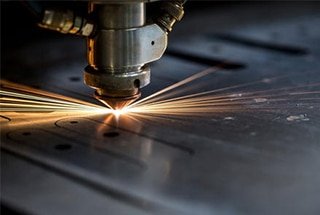
Stellen Sie sich vor, Sie könnten mühelos dicke Bleche mit der Präzision eines Skalpells durchtrennen. In diesem Blogbeitrag werden die Grundlagen des Laserschneidens von Blechen erläutert, einer revolutionären Methode, die hohe Präzision, Geschwindigkeit und Flexibilität vereint. Entdecken Sie das Innenleben von Laserschneidern, ihre Schlüsselkomponenten und verschiedene Schneidetechniken. Am Ende des Buches werden Sie verstehen, wie diese Technologie Fertigungsprozesse optimieren und eine hervorragende Qualität bei der Metallbearbeitung erzielen kann. Tauchen Sie ein und erfahren Sie, wie das Laserschneiden Ihre Arbeitsweise in der Metallverarbeitung verändern kann.
(1) Eine Laserschneidmaschine für Bleche ist eine Präzisionsfertigungsanlage, die in erster Linie dazu dient, flache Bleche mit hoher Genauigkeit und Effizienz in kompliziert geformte Komponenten zu verwandeln.
(2) Dieses fortschrittliche System nutzt die konzentrierte thermische Energie eines Laserstrahls, um Schneidvorgänge durchzuführen. Bei diesem Verfahren wird ein Hochleistungslaser auf die Metalloberfläche fokussiert, was zu einer schnellen, lokalen Erhitzung führt. Diese intensive Hitze schmilzt, verdampft oder sublimiert das Material und erzeugt eine saubere, schmale Schnittfuge, durch die unter Druck stehendes Hilfsgas das geschmolzene Metall ausstößt, was zu einem präzisen Schnitt führt.
Die Laserschneidtechnik bietet zahlreiche Vorteile gegenüber herkömmlichen Schneidverfahren:
Diese überzeugenden Vorteile haben das Laserschneiden zu einer transformativen Technologie in der Blechbearbeitung gemacht, die in modernen Fertigungsumgebungen zunehmend traditionelle Schneidverfahren wie Stanzen, Plasmaschneiden und Wasserstrahlschneiden ersetzt oder ergänzt.
(1) Laser
Laser können unterteilt werden in:
Der Faserlaser erzeugt einen Laser, der nicht nur leicht zu steuern ist, sondern auch eine gute Richtwirkung, Monochromatizität und Kohärenz aufweist. Daher findet er breite Anwendung in der mechanischen Fertigung und Feinblech Verarbeitung.
(2) Hauptmaschine
Es gibt zwei Arten von Relativbewegungen zwischen dem Schneidkopf und der Werkbank:
(1) Während des Schneidevorgangs bewegt sich nur der Schneidkopf, während die Werkbank stillsteht.
(2) Während des Schneidevorgangs bewegt sich nur der Arbeitstisch, während der Schneidkopf fixiert bleibt.
Weitere Bestandteile eines Schneidsystems sind:
(3) Kühlsystem, das Wasser zur Kühlung verwendet.
(4) Luftversorgungssystem, das Flaschengas (Sauerstoff, Ammoniak) oder Druckluft (Luftkompressor, Filter, Trockner) verwenden kann.
(5) Stromversorgung, die eine dreiphasige Spannungsstabilität von ±5% und ein Leistungsungleichgewicht von nicht mehr als 2,5% (berechnet als höchste Spannung in drei Phasen minus niedrigste Spannung in drei Phasen, geteilt durch die durchschnittliche Spannung der drei Phasen) erfordert.
1: Luftschneiden Anforderungen
Abluftvolumen des Kompressors: 2,0 m³/min.
2: Trockner:
3: Filter:
(6) Kontrollsystem:
Lichtleiter Fokussiersystem:
Je nach den Leistungsanforderungen des zu bearbeitenden Werkstücks wird der Strahl verstärkt, geformt und fokussiert, um auf das zu bearbeitende Teil einzuwirken. Die Vorrichtung, die vom Laserausgangsfenster zum zu bearbeitenden Werkstück führt, wird als Lichtleiter-Fokussiersystem bezeichnet.
Laser-Bearbeitung System (Cypcut Laserschneidsystem):
Das Laserbearbeitungssystem besteht im Wesentlichen aus dem Maschinenbett, dem Arbeitstisch, der sich im dreidimensionalen Koordinatenbereich bewegen kann, und dem elektromechanischen Steuerungssystem. Mit dem Fortschritt der elektronischen Technologie verwenden viele Laserbearbeitungssysteme Computer, um die Bewegung des Arbeitstisches zu steuern und eine kontinuierliche Laserbearbeitung zu erreichen.
Die wichtigsten technischen Parameter des CF3015 Blechschneidemaschine:
Genauigkeit der Werkzeugmaschine VDL/DGQ3441 Messlänge 1 Meter.
Hinweis: Die Schnittgenauigkeit hängt von der Blechdicke, der Blechspannung und der Zugkraft ab.
Das Laserschneiden, ein thermisches Präzisionsverfahren, kann in drei Haupttypen eingeteilt werden: Schmelzschneiden (auch bekannt als Schmelzblasen), laserunterstütztes Sauerstoffschneiden (oft auch als Laserbrennschneiden bezeichnet) und Laserverdampfungsschneiden. Jedes Verfahren bietet für bestimmte Materialien und Anwendungen unterschiedliche Vorteile:
Die Wahl des Schneidverfahrens hängt von Faktoren wie Materialart, Dicke, gewünschte Kantenqualität, Produktionsgeschwindigkeit und Nachbearbeitungsanforderungen ab. Moderne Laserschneidsysteme verfügen häufig über adaptive Steuerungsalgorithmen zur Optimierung der Parameter in Echtzeit, um eine gleichbleibende Schnittqualität bei unterschiedlichen Materialeigenschaften und -stärken zu gewährleisten.
Laserschmelzschneiden ist ein fortschrittliches thermisches Verfahren, bei dem ein fokussierter Hochleistungslaserstrahl das Werkstückmaterial lokal aufschmilzt, das dann durch einen Hochgeschwindigkeitsgasstrom ausgestoßen wird. Dieses Verfahren zeichnet sich dadurch aus, dass der Materialabtrag ausschließlich im flüssigen Zustand erfolgt. Die Synergie zwischen dem Laserstrahl und dem hochreinen, inerten Schneidgas erleichtert das Austreiben des geschmolzenen Materials aus der Schnittfuge, während das Gas chemisch inert bleibt und nur als mechanisches Hilfsmittel dient.
Die Prozesseffizienz, gemessen an der maximalen Schneidgeschwindigkeit, steht in direktem Zusammenhang mit der Laserleistung und in umgekehrter Beziehung zur Blechdicke und zum Schmelzpunkt des Materials. Bei einer gegebenen Laserleistung sind die begrenzenden Faktoren der Gasdruck in der Schneidzone und die Wärmeleitfähigkeit des Werkstückmaterials. Die Optimierung dieser Parameter ist von entscheidender Bedeutung, um qualitativ hochwertige Schnitte zu erzielen und die Produktivität zu maximieren.
Ein entscheidender Vorteil des Laserschmelzschneidens ist die Fähigkeit, oxidationsfreie Schnitte in Eisenlegierungen und Metallen auf Titanbasis herzustellen. Dies ist besonders wertvoll in Branchen, die hochreine Schnitte benötigen, wie z. B. in der Luft- und Raumfahrt und bei der Herstellung medizinischer Geräte. Das Fehlen von Oxidation ist auf die Schutzgasabschirmung, in der Regel Argon oder Stickstoff, zurückzuführen, die verhindert, dass Luftsauerstoff mit der heißen Metalloberfläche reagiert.
Die Prozessparameter, einschließlich Laserleistungsdichte, Schneidgeschwindigkeit, Fokusposition und Hilfsgasdruck, müssen präzise gesteuert werden, um eine optimale Schnittqualität zu erreichen. Moderne CNC-Systeme und Echtzeit-Überwachungstechnologien werden häufig eingesetzt, um eine gleichbleibende Schneidleistung bei unterschiedlichen Materialstärken und -zusammensetzungen zu gewährleisten.
Der Unterschied zwischen Laser Brennschneiden und dem Laserschmelzschneiden ist, dass beim Laserbrennschneiden Sauerstoff als Schneidgas verwendet wird. Zwischen dem Sauerstoff und dem erhitzten Metall entsteht eine chemische Reaktion, die das Material weiter erhitzt. Dies führt zu einer höheren Schneidrate für Baustahl derselben Dicke im Vergleich zum Laserschmelzschneiden.
Das Laserbrennschneiden kann jedoch eine schlechtere Kerbqualität aufweisen als das Laserschmelzschneiden. Es kann zu breiteren Schnitten, Rauheit, einer größeren Wärmeeinflusszone und schlechterer Kantenqualität führen. Das Laserbrennschneiden ist für die Bearbeitung von Präzisionsmodellen und scharfen Ecken nicht geeignet, da die Gefahr von Verbrennungen besteht.
Zur Verringerung des thermischen Effekts kann ein Pulslaser verwendet werden. Die Schneidgeschwindigkeit wird durch die verwendete Laserleistung bestimmt.
Siehe auch:
Bei konstanter Laserleistung ist der begrenzende Faktor beim Laserbrennschneiden die Sauerstoffzufuhr und die Wärmeleitfähigkeit des Materials.
Beim Laservergasungsschneiden wird ein Hochleistungslaser eingesetzt, um das Material an der Schneidstelle zu vergasen. Diese Schneidmethode eignet sich nur für Anwendungen, bei denen das Vorhandensein von geschmolzenem Material vermieden werden muss, und ist daher auf eine kleine Auswahl von Eisenbasislegierungen beschränkt.
Die maximale Schneidgeschwindigkeit wird durch die Vergasungstemperatur des Materials bestimmt und ist umgekehrt proportional zur Blechdicke. Um zu verhindern, dass der Materialdampf an den Spaltwänden kondensiert, darf die Materialdicke nicht größer sein als der Durchmesser des Laserstrahls.
Die für diesen Prozess erforderliche Laserleistungsdichte ist beträchtlich und liegt bei über 108 W/cm2und hängt von dem zu schneidenden Material, der Schnitttiefe und der Position des Werkzeugs ab. Laserstrahlfokus.
Bei konstanter Blechdicke und ausreichender Laserleistung ist die maximale Schneidgeschwindigkeit durch die Geschwindigkeit des Gasstrahls begrenzt.
Laserschneidetechnik
Mehrere Schlüsseltechnologien beim Laserschneiden sind eine Kombination aus Licht, Maschinen und Elektrizität.
Die Parameter des Laserstrahls, die Leistung und Genauigkeit der Maschine sowie das numerische Steuerungssystem wirken sich direkt auf die Effizienz und Qualität des Schneidens aus.
Technologie zur Steuerung der Fokusposition: Einer der Vorteile des Laserschneidens ist seine hohe Energiedichte des Strahls. Derzeit ist eine Brennweite von 120 bis 200 mm in der industriellen Faserschneidtechnik weit verbreitet. Laserschneidanwendungen.
Laserperforation Technologie: Bei allen thermischen Schneidverfahren ist im Allgemeinen ein kleines Loch in der Platte erforderlich, außer in den seltenen Fällen, in denen von der Kante der Platte ausgegangen werden kann. Es gibt zwei Hauptmethoden für Laserschneidmaschinen: Strahlen und progressives Schneiden Bohren.
Düsenkonstruktion und Luftstromsteuerungstechnologie: Gegenwärtig ist die für das Laserschneiden verwendete Düse einfach aufgebaut und besteht aus einem konischen Loch mit einem kleinen kreisförmigen Loch am Ende. Das Design wird normalerweise durch Versuch und Irrtum bestimmt.
Prozessanalyse des Laserschneidens
Beim Laserschneiden handelt es sich um ein Verfahren, bei dem sowohl geschmolzen als auch verdampft wird.
Es gibt viele Faktoren, die sich auf die Qualität des Schnitts auswirken können.
Siehe auch:
9 Faktoren, die die Qualität des Laserschneidens beeinflussen
Neben den Hardware-Faktoren, wie der Werkzeugmaschine und den Bearbeitungsmaterialien, spielen auch Software-Faktoren eine wichtige Rolle für die Qualität des Laserschneidprozesses.
Die computergestützte Prozessgestaltung ist der grundlegende Ansatz zur Untersuchung der Auswirkungen dieser Softwarefaktoren auf die Qualität des Schneidprozesses. Dies beinhaltet:
① Auswahl des Stanzpunktes: Die Position des Stanzpunktes wird auf der Grundlage der spezifischen Situation bestimmt.
② Einstellung des Hilfsschneidwegs:
③ Laserstrahlradiuskompensation und Leerhubverarbeitung:
④ Optimierung der Plattenanordnung: Die Auslastung der Platte wird durch Materialeinsparung verbessert.
⑤ Teilesatz Pfadauswahl:
⑥ Berücksichtigung des Einflusses von Verarbeitungsfaktoren: Der Pfad wird unter Berücksichtigung der Auswirkungen von Faktoren wie der thermischen Verformung ausgewählt.
Prozess des Laserschneidens " bezieht sich auf die Wechselwirkung zwischen Laserstrahl, Schneidgas und Werkstück.
Der Prozess des Laserschneidens findet statt, bevor das eigentliche Schneiden erfolgt. Der Laser erhitzt das Werkstück auf die erforderliche Temperatur, um das Material zu schmelzen und zu verdampfen. Die Schnittebene besteht aus einer nahezu vertikalen Fläche, die durch die absorbierte Laserstrahlung erhitzt und geschmolzen wird.
Beim Laserbrennschneiden wird die Schmelzzone durch den in den Spalt eintretenden Sauerstoffstrom weiter erhitzt und erreicht eine Temperatur nahe dem Siedepunkt. Durch die daraus resultierende Vergasung wird das Material abgetragen, und das verflüssigte Material wird durch den Einsatz von Bearbeitungsgas von der Unterseite des Werkstücks ausgetrieben. Beim Laserschmelzschneiden wird das verflüssigte Material mit dem Gas ausgetrieben, das auch den Spalt vor Oxidation schützt.
Die kontinuierliche Schmelzzone bewegt sich entlang der Schneidrichtung und erzeugt einen durchgehenden Spalt. Viele kritische Aspekte des Laserschneidprozesses finden in diesem Bereich statt, und die Analyse dieser Aktivitäten kann wertvolle Informationen über das Laserschneiden liefern. Diese Informationen können zur Berechnung der Schneidgeschwindigkeit und zur Erklärung der Bildung von Zuglinien verwendet werden.
Das Ergebnis von Schneidvorgängen an einem Werkstück kann entweder ein sauberer Schnitt oder aber eine raue oder verbrannte Kante sein.
Zu den wichtigsten Faktoren, die die Schnittqualität beeinflussen, gehören:
Die Zusammensetzung der Legierung kann die Festigkeit und das spezifische Gewicht des Materials beeinflussen, SchweißbarkeitOxidationsbeständigkeit und bis zu einem gewissen Grad auch Säurebeständigkeit. Zu den wichtigsten Elementen in Ferrolegierungen gehören Kohlenstoff, Chrom, Nickel, Magnesium und Zink. Je höher der Kohlenstoffgehaltdesto schwieriger wird es, das Material zu schneiden (wobei 0,8% als kritischer Wert gilt). Einige Arten von Kohlenstoffstahl, die sich gut für das Laserschneiden eignen, sind Q235 und SW22 (aluminiumberuhigter Stahl mit niedrigem Siliziumgehalt und niedrigem Kohlenstoffgehalt).
Im Allgemeinen gilt: Je feiner die Partikelgröße des Ausgangsmaterials, desto besser ist die Qualität der Schneidkante.
Wenn die Oberfläche rostige Bereiche oder Oxidschichten aufweist, wird das Schnittprofil unregelmäßig und weist viele beschädigte Stellen auf. Wählen Sie zum Schneiden von Riffelblech die maximale Dicke Schneidparameter.
Zu den üblichen Oberflächenbehandlungen gehören Verzinken, Fokussierungsverzinken, Lackieren, Eloxieren oder Überziehen mit einer Kunststofffolie. Bei mit Zink behandelten Blechen besteht die Gefahr der Schlackenbildung an der Kante. Bei lackierten Blechen hängt die Schnittqualität von der Zusammensetzung der Beschichtung ab.
Wie man Farbmaterialien verarbeitet:
Im ersten Durchgang wird eine Reihe von Parametern mit niedriger Leistung (für die Gravur) ausgewählt, um die behandelte Oberfläche vorzubrennen und zu markieren. Im zweiten Durchgang wird ein Parametersatz für das Schneiden des Materials ausgewählt.
Bleche mit geschichteten Materialbeschichtungen sind für das Laserschneiden sehr gut geeignet. Um eine korrekte Funktion der kapazitiven Erkennung und eine optimale Haftung der Schicht zu gewährleisten (um Blasenbildung zu vermeiden), muss die Schichtkante immer auf dem oberen Teil des zu schneidenden Werkstücks positioniert werden.
Die Art und Weise, wie der Lichtstrahl auf der Oberfläche des Werkstücks reflektiert wird, hängt von dem darunter liegenden Material, der Oberflächenrauheit und der Behandlung ab.
Siehe auch:
Einige Aluminiumlegierungen, Kupfer und Messing weisen ein hohes Reflexionsvermögen auf und eignen sich nicht zum Schneiden mit einer Faserlaserschneiden Maschine.
Siehe auch:
Werkstoffe mit geringer Wärmeleitfähigkeit benötigen weniger Energie zum Schweißen als Werkstoffe mit hoher Wärmeleitfähigkeit. Zum Beispiel, Chrom-Nickel legierter Stahl benötigt weniger Energie als Baustahl und erzeugt weniger Wärme, die bei der Bearbeitung absorbiert wird. Andererseits absorbieren Materialien wie Kupfer, Aluminium und Messing den größten Teil der vom Laserlicht erzeugten Wärme. Da die Wärme vom Zielpunkt des Strahls weggeleitet wird, wird es schwieriger, das Material in der Wärmeeinflusszone zu schmelzen.
Beim Laserbrennschneiden und Laserschmelzschneiden kann es in der Nähe der Schnittkante zu Materialveränderungen kommen. Bei der Bearbeitung von kohlenstoffarmen oder sauerstofffreien Stählen ist die Abschreckung in der Wärmeeinflusszone geringer. Allerdings ist bei kohlenstoffreicher Stahl (60#), wird der Randbereich härter.
SBaustahl
Beim Schneiden des Materials mit Sauerstoff werden bessere Ergebnisse mit einem Dauerstrichlaser erzielt. Das kleine Kurvensteuerungssystem passt die Laserleistung an die Vorschubgeschwindigkeit der Welle an. Wenn Sauerstoff als Bearbeitungsgas verwendet wird, wird die Schnittkante leicht oxidiert.
Bei Blechen mit einer Dicke von weniger als 3 mm kann Ammoniakgas zum Hochdruckschneiden verwendet werden, was zu einer nicht oxidierten Schnittkante führt.
Komplexe Konturen und kleine Löcher mit einem Durchmesser, der kleiner als die Materialstärke ist, sollten im Impulsbetrieb geschnitten werden, um das Abschneiden scharfer Ecken zu vermeiden. Je höher der Kohlenstoffgehalt ist, desto leichter lässt sich die Schneide abschrecken und desto wahrscheinlicher ist es, dass die Ecke verbrannt wird. Bleche mit hohem Legierungsgehalt sind schwieriger zu schneiden als solche mit niedrigem Legierungsgehalt.
Eine oxidierte oder sandgestrahlte Oberfläche führt zu einer schlechten Schnittqualität, und die Restwärme auf der Blechoberfläche kann sich negativ auf die Schnittergebnisse auswirken. Um Spannungen zu vermeiden, sollten nur nachbehandelte Stahlplatten geschnitten werden. Verunreinigungen in geschmolzenem Stahl unter Siedebedingungen beeinträchtigen die Schneidergebnisse erheblich.
Für saubere Oberflächenschnitte in Baustahl müssen die folgenden Tipps beachtet werden:
Srostfreier Stahl
Schneiden von rostfreiem Stahl erfordert das Folgende:
Bei nichtrostendem Stahl ist Folgendes zu beachten:
Laserschnitt-Verfahren:
Die Wahl des Schnittmodus erfolgt in der Regel bei der Erstellung eines Programms oder durch Änderung der Maschinenparameter an der Maschine.
Die Gasparameter umfassen:
Der Luftdruck und die Düsengeometrie spielen eine Rolle bei der Bestimmung der Kantenrauhigkeit und der Graterzeugung. Der Verbrauch an Bearbeitungsgas ist abhängig vom Düsendurchmesser und Luftdruck. Luft schneiden Ein Druck unter 1,0 MP gilt als Niederdruck, während 1,5 MP als Hochdruck gilt.
Die am häufigsten verwendeten Schneiddüse hat eine kegelförmige runde Öffnung. Es ist wichtig, den Abstand zwischen der Düse und der Werkstückoberfläche so gering wie möglich zu halten, um die Qualität des Gases, das auf die Schlitzwand trifft, zu maximieren. Häufig wird ein Abstand zwischen 0,5 und 1,5 verwendet.
Der Parameterwert des Perforierens unterscheidet sich von dem des Schneidens.
Perforation im Endlosmodus
Perforation im Impulsbetrieb
Anmerkung: die Blechdicke (mm) entspricht ungefähr der Perforationszeit (s).
Zum Perforieren wird in der Regel der CW-Modus verwendet, der zwar schneller ist, aber ein größeres Loch erzeugt als das Perforieren mit einem Impuls. Aus diesem Grund befindet sich die Position des ausgestanzten Lochs in der Regel außerhalb der Kontur. Der Abstand zwischen der Perforation und der eigentlichen Kontur wird als Vorhaltebereich bezeichnet.
Unebenheiten in der Kerbkante am Werkstück können auf eine Veränderung des Fokus des Schwachlichtstrahls vom Ende des Ausgangsschneidteils zur Kontur hin hinweisen. Der Benutzer sollte das Ausgangsteil so weit wie möglich auf die ideale Verlängerungslinie auf einer Seite der geometrischen Einheit einstellen.
Beim Schneiden von kleinen Innenkonturen auf der Oberfläche ist es wichtig, die beim Einstechen entstehende Wärme vor dem Schneiden abfließen zu lassen. Vermeiden Sie es, die Perforationen in einem engen Bereich zu setzen und positionieren Sie sie in einem großen Winkel zur Kontur, was die Wärmeableitung fördert.
Die Leitungslänge hängt von der Dicke der Platte und dem Durchmesser des Lochs ab.
Bearbeitung eines stumpfen Winkels mit Radius
Vermeiden Sie nach Möglichkeit Wurfwinkel ohne Radius.
Die Ecke mit Radius hat gegenüber der Ecke ohne Radius folgende Vorteile:
Optimaler Rundungsradius:
R optimal = Plattendicke (mm) geteilt durch 10, jedoch nicht weniger als 1 mm;
Wenn an der Innenplatte kein Eckenradius erforderlich ist, beträgt der maximale Radius:
R-Rand = halbe Breite des Einschnittes.
Mit diesem Balken kann immer noch eine radiusfreie Ecke erzeugt werden, und jetzt bewegt sich die Achse dynamisch:
Für das Hochgeschwindigkeitsschneiden von dünnen Blechen wird der Einsatz der Lochtechnologie empfohlen. Diese Lösung hat die folgenden Vorteile:
Einschnitte beim Laserschneiden bewerten
Baustahl: Schnitt mit O2 | ||
Defekt | Mögliche Ursachen: | Bedingungen der Abrechnung |
Kein Grat, konsistente Traktionslinie![]() | Richtige LeistungAngemessene Vorschubgeschwindigkeit | |
Die untere Zuglinie hat einen großen Versatz, und die Kerbe am Boden ist breiter.![]() | Vorschubgeschwindigkeit zu hochLaserleistung zu niedrigLuftdruck zu niedrigFokus zu hoch | Vorschubgeschwindigkeit verringernLaserleistung erhöhenLuftdruck erhöhenFokus verringern |
Der Grat an der Unterseite ist ähnlich wie die Schlacke in Form von Tropfen und leicht zu entfernen.![]() | Vorschubgeschwindigkeit zu hoch-Der Luftdruck ist zu niedrigFokus zu hoch | Vorschubgeschwindigkeit reduzierenLuftdruck erhöhenFokus senken |
Die Metallfrässtifte miteinander verbunden sind, können als Ganzes entfernt werden.![]() | Der Fokus ist zu hoch. | Senken Sie den Fokus. |
Metallgrate auf der Unterseite sind schwer zu entfernen![]() | Vorschubgeschwindigkeit zu hochDer Luftdruck ist zu niedrigReingasDer Fokus ist zu hoch. | Vorschubgeschwindigkeit verringernLuftdruck erhöhenReineres Gas verwendenFokus senken |
Grate sind nur auf einer Seite vorhanden![]() | Falsche Ausrichtung des Mundstücks Defekte Düsenöffnung | ZentrierdüseDüse wechseln |
Baustahl: Schnitt mit O2 | ||
Defekt | Mögliche Ursachen: | Ausgeschlossen sind |
Von oben abgegebenes Material![]() | Leistung zu niedrig, Vorschubgeschwindigkeit zu hoch | Drücken Sie in diesem Fall sofort die Pausentaste, um zu verhindern, dass die Schlacke auf die Fokussierlinse spritzt, und erhöhen Sie dann die Leistung. |
Schneiden mit schräger Oberfläche, auf beiden Seiten gut, auf beiden Seiten schlecht![]() | Ungeeigneter, falscher oder defekter Polarisationsspiegel; der Polarisationsspiegel ist an der Position des Umlenkspiegels angebracht | Polarisationsspiegel prüfen; Umlenkspiegel prüfen. |
Blaues Plasma, Werkstück nicht durchgeschnitten![]() | Prozessgasfehler (N2);Die Vorschubgeschwindigkeit ist zu hoch; Leistung zu niedrig | Drücken Sie in diesem Fall sofort die Pausentaste, um zu verhindern, dass die Schlacke auf die Fokussierlinse spritzt; Verwenden Sie Sauerstoff als Prozessgas; Reduzieren Sie die Vorschubgeschwindigkeit; Erhöhen Sie die Leistung |
Ungenaue Schnittfläche![]() | Der Luftdruck ist zu hoch; die Düse ist beschädigt; der Düsendurchmesser ist zu groß; das Material ist nicht gut. | Reduzieren Sie den Luftdruck; tauschen Sie die Düse aus; installieren Sie geeignete Düsen; verwenden Sie ein Material mit einer glatten und gleichmäßigen Oberfläche. |
Es gibt keinen Grat und die Zuglinie ist geneigt; der Einschnitt wird nach unten hin schmaler.![]() | Vorschubgeschwindigkeit zu hoch | Reduzieren Sie die Vorschubgeschwindigkeit. |
Erzeugung von Kratern![]() | Der Luftdruck ist zu hoch; die Vorschubgeschwindigkeit ist zu niedrig; der Fokus ist zu hoch; auf der Plattenoberfläche befindet sich Rost; das bearbeitete Werkstück ist überhitzt; das Material ist nicht rein. | Reduzieren Sie den Luftdruck; erhöhen Sie die Vorschubgeschwindigkeit; senken Sie den Fokus; verwenden Sie hochwertigere Materialien. |
Sehr raue Schnittfläche![]() | Der Fokus ist zu hoch; der Luftdruck ist zu hoch; die Vorschubgeschwindigkeit ist zu niedrig; das Material ist zu heiß. | Senken des Fokus;Verringern des Luftdrucks;Erhöhen der Vorschubgeschwindigkeit;Kühlen des Materials. |
Rostfreier Stahl: Schnitt mit N2 hoher Druck | ||
Defekt | Mögliche Ursachen: | Bedingungen der Abrechnung |
Herstellung von feinen, regelmäßigen Graten in Form von Tropfen;![]() | Die Schärfe ist zu niedrig; Der Vorschub ist zu hoch. | Erhöhen Sie den Fokus; verringern Sie den Vorschub. |
Auf beiden Seiten wachsen unregelmäßige, fadenförmige Grate, und die Oberfläche der großen Platten verfärbt sich.![]() | Die Vorschubgeschwindigkeit ist zu niedrig; der Fokus ist zu hoch; der Luftdruck ist zu niedrig; das Material ist zu heiß. | Erhöhen Sie die Vorschubgeschwindigkeit; Senken Sie den Fokus; Erhöhen Sie den Luftdruck; Kühlen Sie das Material. |
Unregelmäßiger Grat, der nur auf einer Seite der Schneidkante wächst![]() | Die Düse ist nicht zentriert; der Fokus ist zu hoch; der Luftdruck ist zu niedrig und die Geschwindigkeit ist zu gering. | Zentrieren der Düse; Absenken des Fokus; Erhöhen des Luftdrucks; Erhöhen der Geschwindigkeit. |
Vergilbung der Schnittkante | Die Atmosphäre enthält Sauerstoffverunreinigungen. | Verwenden Sie Stickstoff von guter Qualität. |
Das Plasma wird auf einer geraden Strecke erzeugt.![]() | Die Vorschubgeschwindigkeit ist zu hoch. | Drücken Sie in diesem Fall vorübergehend auf . |
Erzeugung eines Plasmas auf der geradlinigen Oberfläche | Die Vorschubgeschwindigkeit ist zu hoch; die Leistung ist zu niedrig; der Fokus ist zu niedrig. | Drücken Sie in diesem Fall sofort die Pausentaste, um zu verhindern, dass die Schlacke auf die Fokussierlinse spritzt;Reduzieren Sie die Aufnahmegeschwindigkeit;Erhöhen Sie die Leistung;Erhöhen Sie den Fokus. |
Strahldispersion | Die Vorschubgeschwindigkeit ist zu hoch; die Leistung ist zu niedrig; der Fokus ist zu niedrig. | Reduzieren Sie den Vorschub; erhöhen Sie die Leistung; erhöhen Sie den Fokus. |
Erzeugen von Plasma an der Ecke | Die Winkeltoleranz ist zu hoch; die Modulation ist zu hoch; die Beschleunigung ist zu hoch. | Verringern Sie die Winkeltoleranz; verringern Sie die Modulation oder Beschleunigung. |
Der Strahl divergiert am Anfang | Die Beschleunigung ist zu hoch; der Fokus ist zu niedrig; geschmolzenes Material konnte nicht entladen werden | Verringern Sie die Beschleunigung; erhöhen Sie den Fokus und durchstoßen Sie das kreisförmige Loch. |
Grober Einschnitt | Die Düse ist beschädigt; die Linse ist verschmutzt. | Tauschen Sie die Düse aus; reinigen Sie die Linse, falls erforderlich. |
Von oben abgegebenes Material![]() | Leistung zu geringZu hohe VorschubgeschwindigkeitDer Luftdruck ist zu hoch | Drücken Sie in diesem Fall sofort die Pausentaste, um zu verhindern, dass geschmolzene Tränen auf die Fokussierlinse spritzenErhöhen Sie die Leistung und verringern Sie die VorschubgeschwindigkeitReduzieren Sie den Luftdruck |
Um die beste Verarbeitungsqualität zu erreichen, beachten Sie bitte die folgenden Hinweise:
Wenn eine Verschlechterung der Bearbeitungsqualität festgestellt wird, sind folgende Faktoren zu prüfen:
Ändern Sie nicht die Standardparameter, die beim Kauf der Laserschneidmaschine festgelegt wurden;
Siehe auch:
Um die Parameter zu optimieren, legen Sie ein neues Verzeichnis für sie an. Wenn sich die Verarbeitungsqualität verschlechtert, vergleichen Sie die Standardparameter der Maschine mit den optimierten Parametern, um festzustellen, ob wesentliche Änderungen vorgenommen wurden.
Die Oberflächenbeschaffenheit der Materialien hat großen Einfluss auf die Qualität des Laserschneidens. Rohmaterialien müssen vor Rost und Schmutz geschützt werden. Wenn die Oberfläche rostig, schmutzig oder uneben ist, sollte das Material vor dem Schneiden mit der Laserschneidmaschine behandelt werden.
Um die beste Schnittqualität zu erreichen, sollte der Bediener diese Grundsätze beachten:
Die Betriebsart mit geringer Lichtstärke umfasst den Dauerbetrieb und den Impulsbetrieb. Der Dauermodus wird für normales Schneiden verwendet, während der Impulsmodus für die Bearbeitung von kleinen Löchern und Perforationen verwendet wird, die kleiner als die Dicke des Materials sind.
Zum Schneiden von Werkstücken, die wiederverwendet werden sollen, kann die Impulsperforation an der grafischen Kontur durchgeführt werden. Die Perforation im Dauermodus wird in der Regel zum schnelleren Schneiden verwendet, führt aber im Vergleich zur Impulsperforation zu einem größeren Loch.
Die Wärmeableitung vor und nach dem Einstechen ist beim Schneiden kleiner Materialien von entscheidender Bedeutung. Vermeiden Sie es, die Schnittlinie mit schmalen Teilen des Werkstücks zu verbinden und stellen Sie sicher, dass ein ausreichender Winkel mit der Figur eingeschlossen ist, um die Wärmeableitung zu ermöglichen.
Die maximale Schnittgröße der Laserschneidmaschine beträgt 3000 x 1500 mm. Die maximale Schneidkapazität eines 500W Faserlaserschneidmaschine beträgt 6 mm für Kohlenstoffstahl und 4 mm für rostfreien Stahl.
Siehe auch:
Das kleinste Loch, das geschnitten werden kann, muss einen Durchmesser haben, der größer ist als die Dicke der Platte.
Sicherheitsvorschriften für den Betrieb der Laserschneidmaschine:
Siehe auch:
Siehe auch:
Ich denke, dass Sie durch die oben genannten Schulungsinhalte ein tieferes Verständnis für das Blatt Metall-Laserschneidendie für Sie sicherlich hilfreich sein werden.
Wenn Sie noch weitere Fragen haben zu Laserschneiden von Blechendann hinterlassen Sie bitte eine Nachricht im Kommentarbereich.