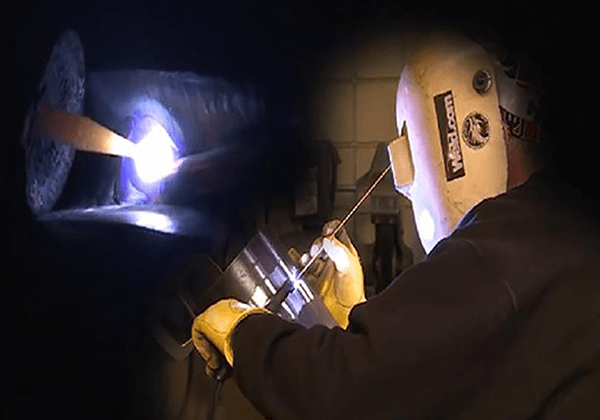
Stellen Sie sich vor, Sie erreichen eine perfekte Schweißnaht mit nur einem Durchgang! Einseitiges Schweißen und beidseitiges Umformen machen dies möglich und gewährleisten eine vollständige Durchdringung und einwandfreie Qualität, ohne dass die Rückseite nachgearbeitet werden muss. Dieser Artikel geht auf die Feinheiten dieser Techniken ein und bietet eine detaillierte Anleitung zum Erreichen gleichmäßiger, fehlerfreier Schweißnähte. Sie lernen die Methoden, Prozesse und häufigen Fallstricke kennen, damit Ihre Schweißprojekte effizienter und zuverlässiger werden. Lesen Sie weiter, um diese transformative Technik des Schweißens und der Metallbearbeitung zu beherrschen.
Einseitiges Schweißen und beidseitiges Umformen sind wesentliche Methoden und Fertigkeiten für Schweißer, die mit dem Schweißen von Druckbehältern, wichtigen Silos und Kesseln beschäftigt sind. Es wird auch bei der Herstellung und Installation wichtiger geschweißter Stahlkonstruktionen verwendet, die Folgendes erfordern vollständige Durchdringung können aber nicht bearbeitet und auf der Rückseite der Bauteile wieder verschweißt werden.
Bei solchen Schweißungen sind keine weiteren Hilfsmaßnahmen erforderlich. Wenn jedoch eine Positionierungsschweißung an der Wurzel der Nut erforderlich ist, sollten verschiedene Abstände entsprechend den unterschiedlichen Anforderungen reserviert werden. Schweißverfahren.
Wenn das Schweißen auf der Vorderseite der Nut erfolgt, können gleichmäßige, regelmäßige und qualifizierte Schweißnähte sowohl auf der Vorder- als auch auf der Rückseite der Nut erzielt werden. Dieser unkonventionelle Schweißvorgang wird als "einseitiges Schweißen und beidseitiges Umformen" bezeichnet.
1.2.1 Lichtbogen-Intervallschweißverfahren
Zum Starten der SchweißverfahrenLegen Sie die Prüfplatte mit dem kleinen Spalt auf die linke Seite. Positionieren Sie es für das Zünden des Lichtbogens und verwenden Sie einen langen Lichtbogen, um die Schweißteile eine gewisse Zeit lang vorzuwärmen. Drücken Sie dann den Lichtbogen nach unten und schwenken Sie die Elektrode zum Schweißen seitlich zwischen die beiden stumpfen Kanten.
Wenn sich das geschmolzene Metall der stumpfen Schneide mit dem geschmolzenen Metall der Elektrode verbindet, hören Sie auf das "Porphyrin"-Geräusch, das eine erfolgreiche Verbindung anzeigt. Die Lichtbogenlampe erlischt dann.
Bei jedem kontinuierlichen Lichtbogen sollte die Mitte der Schweißelektrode auf 2/3 des Schweißbades ausgerichtet sein. Dadurch wird sichergestellt, dass beide Seiten der stumpfen Kante gleichzeitig geschmolzen werden. Sobald das "Porphyrin"-Geräusch zu hören ist, ist der Lichtbogen schnell zu löschen, damit das neu gebildete Schmelzbad etwa 2/3 des zuvor gebildeten Schmelzbades bedecken kann.
1.2.2 Kontinuierlich Lichtbogenschweißen Methode
Das kontinuierliche Lichtbogenschweißen ist eine Technologie, bei der der Lichtbogen während des Schweißens kontinuierlich brennt, ohne dass der Lichtbogen erloschen ist. Dabei werden ein kleiner Fugenspalt und ein geringer Schweißstrom zu Beginn verwendet, während der Lichtbogen kurz gehalten wird. kontinuierliches Schweißen.
Die grundlegenden Elemente dieser Technologie bestehen darin, den Lichtbogen mit der Elektrode zu zünden und sie auf das Minimum zu drücken. Dann wird am Startpunkt der Schweißung die sägezahnförmige Elektrodenbewegung mit einer kleinen Steigung verwendet, um die Elektrode seitlich zu schwenken und die Schweißteile vorzuwärmen.
Die Schweißdraht sollte so weit wie möglich zur Wurzel geleitet werden, um den Elektrodendurchschlag zu bewirken. Wenn ein "Porphyrin"-Geräusch zu hören ist, wird die Schweißnaht ein aufgelöstes Loch bilden. Der Lichtbogen sollte sofort in eine beliebige Position der Rillenoberfläche übertragen werden und dann sollte ein bestimmter Elektrodenwinkel zwischen den Rillenoberflächen verwendet werden.
Der Vorgang besteht aus ununterbrochenen kleinen Aktionen, die etwa 2 Sekunden dauern. Wenn der Lichtbogen die Nutwurzel auf beiden Seiten etwa 1,5 mm aufschmilzt, sollte der Schweißdraht um 1-2 mm angehoben werden. Die Elektrode sollte im Zickzack mit einem kleinen Abstand geschwenkt werden, so dass sich der Lichtbogen vor dem Schmelzloch befindet, während das Schweißen vorwärts erfolgt.
Beim Schweißen ist unbedingt darauf zu achten, dass die Mitte des Schweißdrahtes auf die Vorderkante des Schmelzbades und den Übergang zum Grundwerkstoff ausgerichtet ist, damit sich jedes neue Schmelzbad mit dem zuvor erzeugten Schmelzbad überlappt. Beim Löschen des Lichtbogens sollte die Elektrode langsam auf die rechte oder linke Seite hinter das Schmelzbad gebracht und zum Löschen des Lichtbogens angehoben werden.
Unter VerbindungsschweißenZu Beginn sollte der Lichtbogen in einem Abstand von 10-15 mm vom Krater gezündet werden, und die Elektrode sollte mit normaler Geschwindigkeit bis zur Hälfte des Kraters bewegt werden. Die Elektrode sollte dann nach unten gedrückt werden, und wenn ein "Porphyrin"-Geräusch zu hören ist, sollte ein leichtes Schwingen für 1-2 Sekunden ausgeführt werden. Danach sollte die Elektrode um 1-2 mm angehoben werden, so dass sie zum Schweißen nach vorne bewegt werden kann, während die Vorderseite des Schmelzlochs geschmolzen wird.
(1) Plattenstärke: 12mm, Spezifikation: 300 × 200mm.
Schneiden Sie das Blech mit Sauerstoff und Acetylengas oder verwenden Sie Blechscheren und Schneidemaschinen, und bearbeiten Sie die V-förmigen Nuten dann mit mechanischen Verfahren wie Hobel oder Winkelschleifer.
Auf der Rückseite der Rillen sind keine Fasen erlaubt.
Vergewissern Sie sich, dass die Rillen gerade, glatt und frei von Graten, Ausbuchtungen und anderen Unregelmäßigkeiten sind.
(2) Zum Reinigen des Prüfblechs entfernen Sie mit einer Feile die scharfen Ecken der Rille, wobei die stumpfe Kante 0,5-1,0 mm groß sein muss. Entfernen Sie Rost, Öl, Oxide und andere Verunreinigungen aus der Rille und innerhalb von 20 mm auf beiden Seiten, so dass ein metallischer Glanz zurückbleibt.
(3) Montage und Heftschweißen des Prüfblechs.
Führen Sie die Heftschweißung an beiden Enden der Rückseite der Prüfplatte durch und reservieren Sie eine Schrumpfungszugabe.
Stellen Sie den Schweißspalt auf 3,0-3,5 mm, das endgültige Schweißende auf 3,5-4,0 mm und die positionierte Schweißlänge auf etwa 10-15 mm ein.
Stellen Sie sicher, dass die positionierte Schweißnaht fest ist, insbesondere am Ende der Schweißnaht.
Um negative Auswirkungen auf das kontinuierliche Schweißen oder Brüche während des Schweißens zu vermeiden, die durch die Verringerung des Fugenspalts im nicht geschweißten Abschnitt aufgrund der Schweißnahtschrumpfung verursacht werden, ist beim positionierten Schweißen eine Verformungszulage in umgekehrter Richtung vorzusehen, d. h. eine Verformung des Winkels in umgekehrter Richtung von 3°-4°.
(4) Schweißen Ausrüstung: ZXG Serie DC Lichtbogenschweißmaschine.
Art und Polarität der Stromzufuhr: Vergewissern Sie sich, dass der Gleichstrom-Schweißdraht nicht durch Feuchtigkeit und Verschleiß beeinträchtigt wird, dass der Schweißkern rostfrei ist und dass die Beschichtung nicht reißt oder abfällt.
Heizen Sie den Schweißdraht vor der Verwendung auf 350-400℃ auf, halten Sie die Temperatur 2 Stunden lang konstant und schweißen Sie in vier Lagen.
(5) Befestigen Sie die Prüfplatte: Legen Sie die unverformte Prüfplatte waagerecht auf den Schweißrahmen in einer geeigneten Höhe.
Der Schweißer darf sich beim Schweißen nicht hinsetzen, sondern muss in hockender Position arbeiten.
Der Rillenwinkel der Prüfplatte beträgt 60°.
2.2.1 Schweißen der unteren Lage
Das Grundierungsschweißen kann entweder durch allgemeines Schweißen oder durch Endlichtbogenschweißen oder durch kontinuierliches Lichtbogenschweißen durchgeführt werden.
Um die SchweißverfahrenDer Lichtbogen wird an der Innenseite der Nut des Prüfblechs gezündet, und der untere Lichtbogen wird gedrückt. Der Schweißdraht sollte leicht zwischen den beiden stumpfen Kanten der Nut hin und her geschwenkt werden, bis sich das geschmolzene Eisen an der Kante mit dem geschmolzenen Tropfen des Schweißdrahtes verbindet, ein "Porphyrin"-Geräusch erzeugt und das erste Schmelzbad bildet.
In diesem Stadium sollte sich vor dem Auflösungsbehälter ein 0,5-1,0 mm tiefes Auflösungsloch auf beiden Seiten der Rille der Testplatte befinden.
Das Zickzack- oder halbmondförmige Querschwingschweißverfahren wird für den Schweißdrahtbetrieb angewendet. Die Länge des Pendelbogens sollte kleiner oder gleich dem Elektrodendurchmesser sein. Ein kurzer Lichtbogen wird verwendet, um das geschmolzene Eisen durch die Wurzel der Nut auf die Rückseite des Schweißteils zu leiten.
Wenn der Schweißdraht zu beiden Seiten der Rille transportiert wird, ist eine Pause von 1-2 Sekunden erforderlich. Diese Pause begünstigt eine gute Verschmelzung des Schweißzusatzes mit dem Grundwerkstoff und verhindert außerdem die Bildung scharfer Ecken an der Verbindung von Schweißnaht und Nut, was für die Schlackenentfernung hilfreich ist.
2.2.2 Elektrodenwinkel
Der eingeschlossene Winkel der Schweißvorwärtsrichtung beträgt 70°-80°.
Ein geeigneter Elektrodenwinkel trägt dazu bei, die geschmolzene Schlacke vom geschmolzenen Eisen zu trennen, das Schmelzbad stets klar und hell zu halten und zu vermeiden, dass Spannen.
Die wichtigsten Punkte des Schweißdrahtes: hinschauen, zuhören, genau und kurz sein.
Der eingeschlossene Winkel für die vordere Schweißrichtung sollte zwischen 70° und 80° liegen.
Ein geeigneter Elektrodenwinkel hilft, die geschmolzene Schlacke vom geschmolzenen Eisen zu trennen, hält das Schmelzbad klar und hell und verhindert ein Verklemmen.
Die wichtigsten Punkte bei der Verwendung eines Schweißdrahtes sind: beobachten, zuhören, genau sein und effizient arbeiten.
"Beobachten" bedeutet, auf die Form des Schmelzbades und die Größe des Schmelzlochs zu achten, die die Höhe und Verstärkung der Gegenschweißung bestimmen.
Das Schmelzbad sollte eine runde oder ovale Form haben und immer hell und klar sein, um die Schlacke vom geschmolzenen Eisen zu trennen.
Das Schmelzloch sollte so beschaffen sein, dass der Lichtbogen alle stumpfen Kanten auf beiden Seiten schmilzt und auf jeder Seite 0,5 bis 1,0 mm in das Grundmetall eindringt.
Wenn das Loch zu groß ist, wird die Schweißnaht auf der Rückseite zu hoch, und in schweren Fällen kann es zu Schweißwülsten oder zum Durchbrennen kommen.
Um hier Abhilfe zu schaffen, hat die Schweißgeschwindigkeit sollte vergrößert werden, der Schwenkbereich der Elektrode zu beiden Seiten der Nut sollte vergrößert und der eingeschlossene Winkel zwischen Elektrode und Schweißrichtung sollte verringert werden.
Wenn das Loch zu klein ist, wird die Wurzel der Nut nicht vollständig verschweißt, und die Schweißnahtwurzel ist nicht gut verschmolzen.
Um dies zu beheben, sollte der untere Lichtbogen gedrückt werden, um den Winkel des Schweißdrahtes in Vorwärtsrichtung zu vergrößern, die Schweißgeschwindigkeit und die Schwingungsamplitude zu verlangsamen, den Winkel zwischen dem Schweißdraht und der Vorwärtsrichtung des Schweißens zu verringern und die Form des Schweißbades und die Größe des Schmelzlochs beizubehalten.
Beim Schweißen ist es wichtig, die Fließrichtung von geschmolzenem Eisen und Lösung zu kontrollieren.
Der Lichtbogen sollte immer vor dem geschmolzenen Eisen brennen.
Die umgekehrte Blaskraft des durch den Lichtbogen und das Schmelzen der Beschichtung erzeugten Gases wird genutzt, um das geschmolzene Eisen in den hinteren Teil des Schmelzbades zu blasen, so dass Einbrandverhaltendie Trennung von geschmolzener Schlacke und Eisen und die Verringerung möglicher Fehler durch Schlackeneinschlüsse und Porosität.
Darüber hinaus ist es notwendig, das Schmelzen der geschweißten Rille jederzeit zu beobachten.
Die hintere Kante des Schmelzbades sollte auf beiden Seiten vollständig mit den Rillen verschmolzen sein.
"Hören" bedeutet, dass der Schweißer während des Schweißens nicht abgelenkt werden sollte und auf das "Porphyrin"-Geräusch hören sollte, wenn der Lichtbogen die Prüfplatte durchbricht.
Wenn dieses Geräusch nicht zu hören ist, wird die Rillenwurzel nicht vom Lichtbogen durchbrochen, und das Weiterschweißen führt zu einer undurchlässigen Schweißnaht.
Im Allgemeinen sollte das Ende der Elektrode 2 bis 3 mm von der Rillenwurzel entfernt sein.
"Präzise" bedeutet, dass die Position des Lichtbogenkontakts genau sein muss. Jedes neue Schmelzbad sollte das vorherige um 2/3 überlappen, um sicherzustellen, dass 1/3 des Lichtbogens direkt vor dem Schmelzbad liegt.
Wenn der Schweißer das "por por"-Geräusch hört, sollte er den Lichtbogen hinter dem Schmelzbad schnell ausschalten. Auf diese Weise kann die schützende Wirkung des Lichtbogens auf das Schmelzbad voll zum Tragen kommen und die Bildung von Poren verhindert werden.
Kurz" bezieht sich auf die Zeit für das Löschen des Lichtbogens und die Stumpfschweißung, die so schnell wie möglich abgeschlossen sein sollte, da sonst Kaltschrumpfungsfehler auftreten können, und Rissbildung im Metall kann durch eine unzureichende Verschmelzung zwischen den Schmelzbecken entstehen.
Um Kaltlunker zu vermeiden, sollte die Häufigkeit der Lichtbogenlöschung erhöht und die Lichtbogenkontaktzeit verringert werden. Während das vorherige Schmelzbad noch flüssig ist, sollte das nächste Schmelzbad bereits gebildet werden, damit das Schmelzbad in einem Hochtemperaturzustand bleibt.
Bei der Zwei-Punkt-Durchschlagsmethode sollte die Häufigkeit der Lichtbogenlöschung 50 bis 60 Mal pro Minute betragen, während bei der Ein-Klick-Durchschlagsmethode die Häufigkeit der Lichtbogenlöschung etwa 80 Mal pro Minute betragen sollte.
2.2.3 Gelenke
Die verschiedenen Verbindungsarten werden in Warm- und Kaltverbindungen eingeteilt und im Folgenden separat beschrieben.
Heiße Verbindung:
Um im heißen Zustand des Lichtbogenkraters zu schweißen, zünden Sie den Lichtbogen an der Schräge, 10-15 Sekunden hinter dem Krater. Schweißen Sie in Richtung des vorderen Lichtbogenanschlags, um die Temperatur am Boden des Kraters allmählich zu erhöhen. Drücken Sie dann die Elektrode entlang des vorgeschmolzenen Lochs nach unten. Sobald Sie das Geräusch von "Porphyrin" hören, halten Sie an und heben Sie die Elektrode zum normalen Schweißen an.
Es ist besser, die Elektrode eher früher als später zu ersetzen.
Kalte Verbindung:
Wenn der Lichtbogenkrater abgekühlt ist, entfernen Sie den Lichtbogenkrater und die ersten 10 mm der geschmolzenen Schlacke vom Kohlenstoffstahl. Reinigen Sie den Bereich und setzen Sie den Schweißdraht wieder ein.
Drücken Sie den Schweißdraht am tiefsten Punkt der Schräge entlang des vorgeschmolzenen Lochs schnell nach unten. Sobald Sie das Geräusch von "Porphyrin" hören, halten Sie etwa 1 Sekunde lang inne, bevor Sie den Schweißdraht anheben und mit dem normalen Schweißen beginnen.
Es gibt zwei Methoden für den Lichtbogenbruch Schweißtechnik: die Ein-Klick- und Zwei-Klick-Piercing-Techniken.
Beim Lochstechen mit zwei Klicks wird der Lichtbogen auf beiden Seiten der Nut gezündet, und ein Tropfen geschmolzenes Eisen wird zuerst auf die linke stumpfe Kante und dann auf die rechte stumpfe Kante getropft, wobei sich die Tropfen allmählich hin und her bewegen.
Diese Schweißtechnik eignet sich für Arbeiten mit großem Schweißnahtabstand.
Bei der Ein-Klick-Penetrationsmethode zündet der Lichtbogen die stumpfen Kanten auf beiden Seiten der Rille und schmilzt gleichzeitig.
Die grundlegende Funktionsweise ist wie folgt: Zünden des Lichtbogens.
Beginnen Sie beim Schweißen mit dem Zünden eines Lichtbogens an der Innenseite der Nut am Anfangsende des Prüfblechs. Heizen Sie das Anfangsteil mit einem langen Lichtbogen vor, senken Sie dann den Lichtbogen und schwenken Sie die Elektrode zwischen den beiden stumpfen Kanten hin und her.
Wenn sich das geschmolzene Eisen an der stumpfen Kante der Rille mit dem Metalltropfen der Elektrode verbindet und ein Geräusch von "Porphyrin" zu hören ist, bildet sich das erste Schmelzbad und der Lichtbogen erlischt.
An diesem Punkt wird das vordere Ende des ersten Schmelzbades zu einem Schmelzloch, das auf beiden Seiten der Prüfplatte 0,5-1,0 mm tief sein sollte. Setzen Sie die Schweißdrahtverbindung wieder ein.
Das Verfahren zum Wechseln des Schweißdrahtes beim Lichtbogenunterbrechungsschweißen ist im Grunde dasselbe wie beim kontinuierlichen Lichtbogenschweißen. Vor dem Wechseln des Schweißdrahtes sollte der Lichtbogen nicht zu schnell gelöscht werden, um Kaltschrumpfungslöcher durch Lichtbogenlöschung zu vermeiden. Zwei oder drei Tropfen geschmolzenes Eisen sollten vorher schnell an den Rand oder in den Norden des Schweißbads geleitet werden, das hintere Schweißbad sollte gefüllt werden, und die Temperatur des Schweißbads sollte kontrolliert werden, um es langsam abzukühlen.
Vor dem Schweißbad sollte sich ein Schweißloch bilden. Drücken Sie den Lichtbogen auf eine Seite der Rille und schweißen Sie etwa 10 mm zurück, bevor Sie den Lichtbogen löschen. Dadurch wird sichergestellt, dass das geschmolzene Eisen im hinteren Schmelzbad voll und ausreichend ist, um Kaltschrumpfungsfehler zu vermeiden.
Nach dem schnellen Elektrodenwechsel sollte der Lichtbogen innerhalb von 10-15 mm vor der Kraterfront gezündet werden. Nach dem Zünden sollte der Lichtbogen nach hinten gestreckt werden, und das zu schweißende Metall sollte mit einem langen Lichtbogen vorgewärmt werden.
Dann sollte der Lichtbogen etwa 10 mm hinter dem Krater nach unten gedrückt werden. Der Schweißdraht sollte kontinuierlich bis zur Wurzel des Kraters geführt werden.
Wenn das "Porphyrin"-Geräusch zu hören ist, sollte der Lichtbogen für etwa 2 Sekunden angehalten werden, um ihn zu löschen. Dann sollte das ursprüngliche intermittierende Lichtbogenschweißverfahren verwendet werden, um das Schweißen fortzusetzen.
Bitte beachten Sie die folgenden Hinweise:
(1) Die Schweißnahtdicke der Grundierung an der Vorder- und Rückseite der Nut sollte zwischen 1,5 und 2,0 mm betragen.
(2) Die Schweißer sollten die Stange mit ihren Handgelenken flexibel drehen.
(3) Es müssen vier Schweißnähte von je 300 mm Länge ausgeführt werden.
2.2.4 Schweißen der Schweißzusatzschicht
Nachdem die Schweißschlacke der vorherigen Schicht abgekühlt ist, entfernen Sie gründlich Schlacke und Spritzer, wobei Sie besonders auf die Ecken achten.
Sobald die Schlacke entfernt ist, reinigen Sie den Bereich mit einer Drahtbürste, bis die Metalloberfläche freiliegt.
Zünden Sie den Lichtbogen 10 mm vom Beginn der Schweißnaht entfernt an und führen Sie den Lichtbogen dann zum Startpunkt der Schweißung zurück.
Verwenden Sie eine halbmondförmige oder sägezahnförmige Elektrode, und halten Sie leicht inne, wenn die Elektrode zu einer Seite der Rille schwenkt, um den Lichtbogen zu stabilisieren.
Bewegen Sie sich zügig durch die Mitte der Rille und halten Sie dabei den Lichtbogen so niedrig wie möglich. Dies erleichtert die Entfernung von Verunreinigungen an den scharfen Ecken der tiefen Rille und verhindert den Einschluss von Schlacke.
Halten Sie das Gleichgewicht im Schmelzbad und auf beiden Seiten der Rille aufrecht, um die Bildung von Schlackeneinschlüssen an der Verbindung zwischen dem Schweißzusatz und dem Grundmetall zu verhindern. Diese sind schwer zu beseitigen.
Der Winkel zwischen dem Schweißdraht und dem Schweißfortschritt sollte 75°-85° betragen.
Verwenden Sie beim Schweißen einen kurzen Lichtbogen und stellen Sie sicher, dass das Schweißbad rund oder oval ist und eine gleichmäßige Form und Größe hat.
Behalten Sie eine gleichmäßige Schweißgeschwindigkeit und eine gleichmäßige Dicke des Schweißfleisches bei.
Verwenden Sie beim Schweißen der Verbindung thermische Verfahren.
Bevor Sie den Schweißdraht wechseln, um den Lichtbogen zu stoppen, geben Sie etwas geschmolzenes Eisen in das gebildete Schweißbad.
Nach einem schnellen Wechsel des Schweißdrahtes zünden Sie den Lichtbogen etwa 10 mm vor dem Lichtbogenkrater.
Ziehen Sie dann den Lichtbogen auf 2/3 des Kraters, füllen Sie zuerst den Krater und fahren Sie dann mit dem normalen Schweißen fort.
Versetzen Sie die Anschlussfugen jeder Lage der Schweißnaht.
Die Füllhöhe der letzten Schicht sollte 0,5-2,0 mm niedriger als die Oberfläche des Grundmetalls sein, und die Form sollte auf beiden Seiten hoch und in der Mitte konkav sein.
Vergewissern Sie sich, dass die Schweißnaht glatt und die Rille übermäßig groß ist, damit die Rille beim Schweißen des Deckels deutlich sichtbar ist. Dadurch wird sichergestellt, dass die Kante der Deckschweißung gerade ist.
2.2.5 Schweißen der Deckschicht
Die Lichtbogenzündmethode für die Deckschicht ist die gleiche wie die für die Füllschicht. Verwenden Sie eine halbmondförmige oder sägezahnförmige Querelektrode.
Die Schwingungsamplitude der Elektrode sollte etwas größer sein als die der Füllstoffschicht. Stellen Sie sicher, dass die Schwingungsamplitude während der Schwingung konstant ist und die Elektrodengeschwindigkeit gleichmäßig ist.
Das Schweißbad hat eine ovale Form. Versuchen Sie, die Form und die Größe des Schweißbades ungefähr gleich zu halten, und verwenden Sie Kurzlichtbogenschweißen.
Wenn der Schweißdraht bis zur Kante der Nut schwingt, stabilisieren Sie den Lichtbogen und stoppen Sie die Spitze. Die Schweißnaht an der Kante der Nut sollte etwa 1,0-2,0 mm betragen.
Beide Seiten der Schweißnahtkanten sollten gut verschmolzen sein, um Hinterschneidungen zu vermeiden.
Die Schweißgeschwindigkeit sollte gleichmäßig sein, damit die Schweißfläche glatt und schön wird.
Bei der Verwendung von Schweißdrahtverbindungen ist das Heißverbindungsverfahren anzuwenden.
Bevor Sie den Schweißdraht zum Löschen des Lichtbogens austauschen, geben Sie etwas geschmolzenes Eisen in das Schweißbad.
Nach dem Auswechseln des Schweißdrahtes zünden Sie den Lichtbogen etwa 10 mm vor dem Krater, ziehen den Lichtbogen dann auf 2/3 des Kraters zurück, füllen den Krater und führen dann eine konventionelle Schweißung durch.
Wenn der Verbindungsteil abweicht, wird der Verbindungsteil höher sein. Wenn die Verbindung abgelenkt ist, wird die Schweißnaht getrennt Fehler auftreten.
Zusammenfassend kann man sagen, dass die häufigsten Fehler, die beim Stumpfstoß von Blech zu Blech, beim einseitigen Schweißen und beim beidseitigen Umformen auftreten können, folgende sind: Lufteinschlüsse, unvollständiges Eindringen, unvollständige Verschmelzung und Schweißraupe Bildung, unter anderem.
Im folgenden Abschnitt werden wir diese potenziellen Mängel genauer analysieren und aufschlüsseln.
Luftlöcher bilden sich im Schweißgut, wenn das im Schweißbad vorhandene Gas nicht entweichen kann, bevor das Schweißgut beim Schweißen erstarrt.
Dieses Gas kann vom Schmelzbad aus der äußeren Umgebung absorbiert werden, wobei Wasserstoff und Kohlenmonoxid die häufigsten Gase sind. Es kann auch durch die Reaktion des Metalls beim Schweißen entstehen.
Enthält das unedle Metall beispielsweise einen zu hohen Schwefelanteil, bilden sich während des Schmelzvorgangs mit dem Elektrodenmetall Gasblasen.
(1) Die Hauptursachen für Porosität beim Schweißen werden wie folgt analysiert:
Die Oberfläche des zu schweißenden Grund- oder Schweißzusatzwerkstoffs muss sauber und frei von Verunreinigungen wie Ölflecken und Rost sein.
Es ist wichtig, sicherzustellen, dass die Schweißflussmittel oder die Elektrode vor dem Schweißen gründlich getrocknet wird, da Feuchtigkeit dazu führen kann, dass sie sich während des Schweißvorgangs in Gas zersetzt, was zu einer verstärkten Porenbildung führt.
Eine niedrige lineare Energie beim Schweißen führt zu einer schnellen Abkühlung des Schmelzbades, was das rechtzeitige Entweichen von Gas aus dem Schweißgut erschwert.
Eine unzureichende Desoxidation des Schweißguts kann auch zu einer verstärkten Bildung von Sauerstoffporen führen.
Umwelteinflüsse wie übermäßige Luftfeuchtigkeit an Regen- oder Nebeltagen können dazu führen, dass die Schweißnaht während des Schweißens Feuchtigkeit aus der Umgebungsluft aufnimmt, was die Bildung von Porosität noch verstärkt.
(2) Schädigung der Spaltöffnungen.
Es gibt verschiedene Vorschriften, die die Anzahl der zulässigen Poren regeln.
Das Vorhandensein von Luftlöchern beim Schweißen kann jedoch die effektive Querschnittsfläche der Schweißnaht verringern, die Verbindung lockern, ihre Festigkeit verringern und zu Produktionsunfällen, wie z. B. Leckagen, führen.
Porosität kann auch zu strukturellen Defekten führen, die konzentrierte Spannungen verursachen und die Bauteile beschädigen, wodurch ihre Festigkeit verringert und ihre Lebensdauer beeinträchtigt wird.
Daher ist es wichtig, die Ursachen für Poren individuell zu analysieren und externe Faktoren, die zu ihrer Bildung führen können, zu vermeiden. Diese Vorgehensweise hilft, das Auftreten von Poren beim Schweißen zu minimieren.
3.2.1 Ursachen für eine unvollständige Durchdringung
(1) Der Rillenwinkel der Prüfplatte kann reduziert sein, die stumpfe Kante kann zu groß sein, oder der Montagespalt kann zu klein sein, was zu unzureichenden Punktschweißen Länge und eine zu dünne Schweißnaht. Zug- und Schrumpfspannungen während des Schweißens können dazu führen, dass der Spalt an der Punktschweißstelle kleiner wird, oder die gewählte Elektrode kann zu groß sein, so dass das abgeschiedene Metall die Wurzel der Nut nicht erreichen kann.
(2) Eine zu hohe Schweißgeschwindigkeit oder ein zu geringer Schweißstrom kann zu einer verringerten Einschweißkraft, zu flachen Schmelzbädern und zu einem unzureichenden Abschmelzen der Schweißnahtkanten führen. Die Brenndauer des Lichtbogens beim Durchbruchschweißen auf beiden Seiten der Nut kann auch zu kurz sein, um ein Loch einer bestimmten Größe zu bilden.
(3) Ein falscher Elektrodenwinkel oder eine magnetische Drift des Lichtbogens kann dazu führen, dass die Hitze des Lichtbogens verloren geht oder zu einer Seite abgelenkt wird, was zu einem unvollständigen Eindringen führt.
(4) Beim Grundierungsschweißen kann es zu einem unvollständigen Einbrand an der Nahtstelle kommen. Dies tritt häufig bei Plattenschweißungen nach dem Wechsel des Schweißdrahtes auf. Die Temperatur des zündenden Lichtbogens sinkt, was zu einem großen Temperaturunterschied zwischen den geschweißten und den nicht geschweißten Teilen und zu einem großen Spalt zwischen den Prüfblechen führt, und das Schweißen wird vor dem erforderlichen Vorwärmtemperatur erreicht wird. Infolgedessen kann der Lichtbogen an der Verbindungsstelle die stumpfe Kante des Prüfstücks nicht schnell durchbrechen, was zu einem Abschnitt mit unvollständiger Durchdringung an der Verbindungsstelle und damit zu Fehlern führt.
3.2.2 Maßnahmen zur Vermeidung unvollständiger Durchdringungsfehler
(1) Wählen Sie den richtigen Elektrodenwinkel.
Beim Gegenschweißen ist es wichtig, die Schweißgeschwindigkeit angemessen zu steuern, um sicherzustellen, dass der Lichtbogen die Wurzel vollständig aufschmilzt.
(2) Reinigen Sie die Rillenschweißnaht gründlich, um Öl, Rost oder andere Verunreinigungen zu entfernen.
(3) Wenn die exzentrische Elektrode während des Schweißvorgangs eine Lichtbogenablenkung verursacht, muss der Winkel der Elektrode sofort angepasst werden. Schwenken Sie die Elektrode in die entgegengesetzte Richtung der Lichtbogenablenkung, um den Lichtbogen auf das Schmelzbad auszurichten, oder tauschen Sie die Elektrode aus.
(4) Überwachen Sie den Schmelzzustand während des Schweißens genau, um ein einwandfreies Schmelzen zu gewährleisten.
(1) Die abgeschrägte Kante ist zu stumpf und das Montagespiel ist zu groß.
(2) Während FlachschweißenEin zu hoher Schweißstrom und eine langsame Schweißgeschwindigkeit können zu einer Erhöhung der Temperatur und des Volumens der Schweißnaht führen. Dies kann dazu führen, dass flüssiges Metall aufgrund der Schwerkraft herunterfällt.
(3) Ein falscher Winkel des Schweißdrahtes kann ebenfalls ein Problem beim Schweißen darstellen.
Vorbeugende Maßnahmen bei Schweißüberlappungen:
(1) Wählen Sie die geeignete Größe für die stumpfe Kante und den Montagespalt, und regulieren Sie die Größe des Schmelzlochs während des Schweißvorgangs.
(2) Strenge Kontrolle der Stromstärke und der Zwischenlagentemperatur.
(3) Wählen Sie einen geeigneten Elektrodenwinkel und schwenken Sie die Elektrode in der Mitte schneller und an den beiden Seiten langsamer.
(4) Beobachten Sie den Zustand des Schmelzbades sorgfältig.
(5) Wenn mehr kleine Funken aus dem Schmelzbad sprühen, löschen Sie den Lichtbogen sofort, um die Temperatur des Schmelzbades zu senken, bevor Sie mit dem Schweißprozess fortfahren.