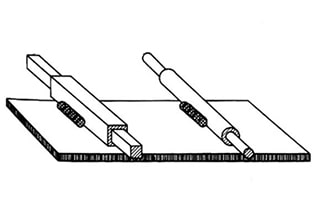
Stellen Sie sich vor, Sie sind in einer Werkstatt, umgeben vom Zischen und Funkenflug der Schweißbrenner. Haben Sie sich jemals gefragt, was eine Schweißmethode von einer anderen unterscheidet? Dieser Artikel nimmt Sie mit auf eine Reise durch zehn wichtige Schweißtechniken, vom Elektrodenschweißen bis zum Reibschweißen. Sie erfahren, wie jede Methode funktioniert, welche einzigartigen Anwendungen es gibt und welche Vorteile sie bietet. Egal, ob Sie ein erfahrener Schweißer oder ein neugieriger Anfänger sind, dieser Leitfaden bietet wertvolle Einblicke, um Ihr Verständnis für Schweißverfahren zu verbessern. Tauchen Sie ein und erweitern Sie Ihr Schweißwissen!
Ein Lichtbogen ist eine anhaltende und intensive Gasentladung, die zwischen zwei geladenen Leitern stattfindet.
Bogenentstehung
(1) Kurzschluss zwischen Schweißdraht und Werkstück
Im Falle eines Kurzschlusses werden einzelne Kontaktstellen mit hoher Stromdichte durch Widerstandswärme erwärmt, q = I^2Rt, wobei I der Strom und R der Widerstand ist. Die Intensität des elektrischen Feldes in dem kleinen Luftspalt ist sehr hoch, was zur Folge hat:
① Eine kleine Anzahl von Elektronen entweicht
② Die einzelnen Kontaktstellen werden erhitzt, geschmolzen und sogar verdampft und verdunstet
③ Das Vorhandensein vieler Metalldämpfe mit niedrigem Ionisierungspotenzial.
Weiterführende Lektüre: Wie wählt man den richtigen Schweißdraht?
(2) Anheben des Schweißdrahtes in einem angemessenen Abstand
Unter dem Einfluss einer thermischen Anregung und eines starken elektrischen Feldes emittiert die negative Elektrode Elektronen und bewegt sich mit hoher Geschwindigkeit, wobei sie mit neutralen Molekülen und Atomen zusammenstößt und diese anregt oder ionisiert. Dies führt zu:
Lichtbogenstruktur und Temperaturverteilung
Der Lichtbogen besteht aus drei Teilen: dem Kathodenbereich (in der Regel ein heller weißer Fleck am Ende der Elektrode), dem Anodenbereich (ein dünner heller Bereich im Bad, der dem Ende der Elektrode auf dem Werkstück entspricht) und dem Lichtbogensäulenbereich (der Luftspalt zwischen den beiden Elektroden).
Bedingungen für eine stabile Lichtbogenverbrennung
(1) Geeignete Stromversorgung
Es muss eine Stromversorgung vorhanden sein, die den elektrischen Anforderungen des Schweißlichtbogens entspricht.
a) Wenn der Strom zu niedrig ist, ist die Gasionisierung zwischen den Luftspalten unzureichend, der Lichtbogenwiderstand ist hoch, und es ist eine höhere Lichtbogenspannung erforderlich, um das erforderliche Ionisierungsniveau aufrechtzuerhalten.
b) Mit steigendem Strom nimmt der Ionisierungsgrad des Gases zu, die Leitfähigkeit verbessert sich, der Lichtbogenwiderstand nimmt ab und die Lichtbogenspannung sinkt. Die Spannung darf jedoch nicht über einen bestimmten Punkt hinaus abnehmen, um die erforderliche elektrische Feldstärke aufrechtzuerhalten und die Emission von Elektronen und die kinetische Energie geladener Teilchen zu gewährleisten.
(2) Richtige Auswahl und Reinigung der Elektroden
Es ist wichtig, saubere Elektroden mit der entsprechenden Beschichtung zu verwenden.
(3) Verhinderung des partiellen Ausblasens
Es müssen Maßnahmen ergriffen werden, um ein teilweises Ausblasen zu verhindern.
(4) Elektrodenpolarität
Beim Schweißen mit einem Gleichstrom-Schweißgerät gibt es zwei Methoden: die positive Verbindung und die umgekehrte Verbindung.
AC Ausrüstung für das Lichtbogenschweißen
Wechselstrom-Lichtbogenschweißgeräte sind weit verbreitet, und die Elektrodenpolarität ändert sich häufig, so dass es keine Probleme mit der Polarität gibt.
Das Werkstück wird an den Pluspol der Stromversorgung und die Elektrode an den Minuspol angeschlossen. Dies ist die normale Anschlussmethode für allgemeine Schweißarbeiten.
Das Werkstück wird an den Minuspol der Stromversorgung und die Elektrode an den Pluspol angeschlossen. Dieses Verfahren wird im Allgemeinen zum Schweißen dünner Bleche verwendet, um ein Durchbrennen zu verhindern.
1). Schweißverfahren
2). Schweißdraht Lichtbogenschweißen Heizung Eigenschaften
Zusammensetzung des Schweißdrahtes für das Lichtbogenhandschweißen
Der Schweißdraht für das Lichtbogenhandschweißen besteht aus einem Schweißkern und einer Beschichtung.
① Als Elektrode beim Lichtbogenschweißen leitet sie den Strom mit dem Werkstück, um einen Lichtbogen zu bilden.
② Während des Schweißvorgangs schmilzt es kontinuierlich und wird in das sich bewegende Schmelzbad überführt, wo es mit dem geschmolzenen Grundmetall kristallisiert und eine Schweißnaht bildet.
① Die Rolle der Beschichtung
Die Beschichtung bietet einen wirksamen Schutz für das Schmelzbad und die Schlackenverbindung, desoxidiert und entschwefelt das geschmolzene Metall im Schmelzbad und infiltriert die Legierung in das geschmolzene Badmetall, um die mechanischen Eigenschaften der Schweißnaht zu verbessern. Außerdem stabilisiert sie den Lichtbogen, um den Schweißprozess zu verbessern.
② Zusammensetzung der Beschichtung
Arten von Schweißdraht
Schweißdrähte werden in zehn Kategorien eingeteilt:
Auswahl Das Prinzip des Schweißens Stab
Bei der Auswahl eines Schweißdrahtes sollten die folgenden Grundsätze beachtet werden:
Änderung und Verteilung der Temperatur in einer Schweißnaht
Die Temperatur des Metalls in der Schweißzone beginnt zu steigen, erreicht einen stabilen Zustand und sinkt dann allmählich auf Raumtemperatur.
Veränderungen der Mikrostruktur und der Eigenschaften von Geschweißte Gelenke (am Beispiel von Stahl mit niedrigem Kohlenstoffgehalt)
Hauptmängel von Schweißnähten
Lunker sind Löcher, die entstehen, wenn die Blasen in der Schmelze während der Erstarrung nicht entweichen.
Präventionsmaßnahmen:
a) Trocknen Sie den Schweißdraht und reinigen Sie gründlich die Schweißfläche und die Umgebung des Werkstücks.
b) Verwenden Sie einen geeigneten Schweißstrom und arbeiten Sie korrekt.
Schlackeneinschlüsse sind Schlacken, die nach dem Schweißen in der Schweißnaht verbleiben.
Vorsichtsmaßnahmen:
a) Reinigen Sie die Schweißfläche sorgfältig.
b) Beim Mehrlagenschweißen ist die Schlacke zwischen den Lagen gründlich zu entfernen.
c) Verlangsamung der Kristallisationsgeschwindigkeit des geschmolzenen Pools.
a) Hot Crack
Ein Heißriss ist ein Riss in der Schweißnaht, der sich bildet, wenn das Metall während des Schweißens in der Nähe des Solidus abkühlt.
Vorbeugende Maßnahmen:
Verringerung der strukturellen Steifigkeit, Vorwärmen vor dem Schweißendie Legierung zu reduzieren, Elektroden mit niedrigem Wasserstoffgehalt und guter Rissbeständigkeit zu wählen, usw.
b) Cold Crack
Ein Kaltriss ist ein Riss in der Schweißnaht, der beim Abkühlen auf eine niedrigere Temperatur entsteht.
Vorsichtsmaßnahmen:
a) Verwenden Sie eine wasserstoffarme Elektrode, trocknen Sie die Werkstückoberfläche und entfernen Sie Öl und Rost.
b) Vorwärmen vor dem Schweißen und Wärmebehandlung nach dem Schweißen.
Unvollständige Durchdringung ist ein Phänomen, bei dem die Wurzel der Schweißverbindung nicht vollständig durchdrungen wird.
Die Ursachen:
Zu kleiner Rillenwinkel oder Spalt, zu dicke stumpfe Kante, unsaubere Rille, zu dicke Elektrode, zu schnell Schweißgeschwindigkeit, zu geringer Schweißstrom und unsachgemäße Bedienung.
Unvollständige Verschmelzung ist ein Phänomen, bei dem die Verschmelzung zwischen der Schweißnaht und dem Grundwerkstoff nicht vollständig ist.
Die Ursachen:
Unsaubere Rille, zu großer Elektrodendurchmesser und unsachgemäßer Betrieb.
Ein Hinterschnitt ist eine Rille oder Vertiefung entlang des Grundwerkstoffteils der Schweißnaht.
Die Ursachen:
Zu hoher Schweißstrom, zu langer Lichtbogen, falscher Elektrodenwinkel, usw.
Ursachen für Schweißspannungen und Verformungen
Die lokale Erwärmung beim Schweißen ist die Hauptursache für Schweißspannungen und Verformungen.
Grundformen der Verformung beim Schweißen
Prozessmaßnahmen zur Verhinderung und Reduzierung von Schweißverformungen
Prozessmaßnahmen zur Reduzierung der Schweißspannung
Die Schweißverfahren bei dem der Lichtbogen unter einer Flussmittelschicht brennt, wird als Unterpulverschweißen (SAW) bezeichnet.
SAW zeichnet sich durch eine automatische Montage für das Zünden des Lichtbogens und die Zuführung der Elektrode aus und wird daher auch als Submerged Arc Automatic Welding (SAAW) bezeichnet.
Das Unterpulverschweißen (SAW) bietet mehrere Vorteile, darunter:
SAW ist jedoch nicht für alle Schweißarten geeignet. Sie eignet sich am besten zum Schweißen von flachen, langen geraden Nähten und Rundnähten mit großem Durchmesser. Für kurze Schweißnähte, Zickzack-Nähte, schmale Positionen und dünne Blechschweißenliefert SAW möglicherweise nicht die gewünschten Ergebnisse.
Schutzgasschweißen, bei dem Argon als Schweißmittel verwendet wird Schutzgas ist bekannt als Wolfram-Inertgas-Schweißen (WIG) oder Argonlichtbogenschweißen.
Da Argon ein inertes Gas ist, schützt es die Elektrode und das geschmolzene Metall vor den schädlichen Auswirkungen der Luft.
Je nach Art der verwendeten Elektrode, Argon-Lichtbogenschweißen können in zwei Arten unterteilt werden:
Argon-Lichtbogenschweißen mit nicht abschmelzender Elektrode
Argon-Lichtbogenschweißen ohne geschmolzene Elektrode ist eine Art des Argon-Lichtbogenschweißens, bei der die Elektrode nur zur Erzeugung eines Lichtbogens und zur Abgabe von Elektronen verwendet wird. Der Zusatzwerkstoff wird separat zugegeben.
Übliche Elektroden für dieses Verfahren sind Wolfram-Elektroden, die mit Thorium- oder Ceroxid dotiert sind. Diese Elektroden haben eine hohe thermische Elektronenemissionsfähigkeit, einen hohen Schmelzpunkt und einen hohen Siedepunkt (3700K bzw. 5800K).
MIG-Schweißen
Das Wolfram-Inertgas (WIG)-Schweißen ist bekannt für seine geringe Stromstärke und sein geringes Eindringvermögen. Trotzdem wird es häufig zum Schweißen von Legierungen mit mittlerer bis hoher Dicke verwendet, wie z. B. TitanAluminium, Kupfer und andere. Dies ist auf seine Fähigkeit zurückzuführen, hohe Produktivitätsniveaus zu erreichen.
Nachstehend sind die wichtigsten Merkmale des Argon-Lichtbogenschweißens (WIG-Schweißen):
Schutzgasschweißen das Kohlendioxid (CO2) als Schutzgas verwendet, wird als Gas-Metall-Lichtbogenschweißen (GMAW) oder Metall-Inertgasschweißen (MIG) bezeichnet.
Der Hauptzweck der Verwendung von CO2 als Schutzgas besteht darin, den Schweißbereich von der Luft zu isolieren und die schädlichen Auswirkungen von Stickstoff auf das geschmolzene Metall zu verhindern. Dies trägt dazu bei, die Integrität der Schweißnaht zu erhalten und qualitativ hochwertige Ergebnisse zu erzielen.
Während des Schweißens:
2CO2=2CO+O2 CO2=C+O2
Daher wird das Schweißen in CO2CO und O2 Oxidationsatmosphäre.
Merkmale des Kohlendioxid-Schutzgasschweißens:
Das Elektroschlackeschweißen (ESW) ist ein Schweißverfahren, bei dem die Wärme, die durch den Widerstand eines elektrischen Stroms erzeugt wird, der durch eine flüssige Schlacke fließt, zur Herstellung einer Schweißnaht genutzt wird.
Normalerweise ist ein Schweißlichtbogen ein freier Lichtbogen, d. h. nur ein Teil des Gases im Lichtbogenbereich wird ionisiert und die Temperatur ist nicht hoch genug.
Wenn jedoch der freie Lichtbogen zu einem Lichtbogen mit hoher Energiedichte komprimiert wird, wird das Gas in der Lichtbogensäule vollständig ionisiert und wandelt sich in ein Plasma um, einen vierten Aggregatzustand, der aus positiven und negativen Ionen besteht.
Plasmabögen haben hohe Temperaturen (zwischen 15.000 und 30.000 K), hohe Energiedichten (bis zu 480 kW/cm2), und schnell fließende Plasmaströme (ein Vielfaches der Schallgeschwindigkeit).
Es gibt drei Kompressionseffekte in Plasmabogen Schweißen:
Diese drei Verdichtungseffekte führen zu einem Plasmalichtbogen mit einem Durchmesser von nur etwa 3 mm, aber mit deutlich verbesserter Energiedichte, Temperatur und Luftgeschwindigkeit.
Nachstehend sind die wichtigsten Merkmale von Plasma-Lichtbogenschweißen:
Das Vakuum-Elektronenstrahlschweißen (VEBW) ist ein Schweißverfahren, bei dem ein gerichteter Hochgeschwindigkeits-Elektronenstrahl auf das Werkstück gerichtet wird, der seine kinetische Energie in Wärmeenergie umwandelt und das Werkstück zu einer Schweißnaht schmilzt.
Im Folgenden sind die wichtigsten Merkmale des Vakuum-Elektronenstrahlschweißens (VEBW) aufgeführt:
Laserschweißen ist ein Schweißverfahren, bei dem ein fokussierter Laserstrahl Wärme auf die Schweißnaht überträgt.
Im Folgenden sind die wichtigsten Merkmale des Laserschweißens aufgeführt:
Widerstandsschweißen ist ein Schweißverfahren, bei dem nach dem Zusammenfügen der Werkstücke über Elektroden Druck ausgeübt wird. Die Widerstandswärme, die durch den Strom erzeugt wird, der durch die Kontaktfläche der Verbindung und den umgebenden Bereich fließt, wird zum Schweißen der Werkstücke genutzt.
Es gibt verschiedene Arten des Widerstandsschweißens, darunter PunktschweißenNahtschweißen und Stumpfschweißen. Jedes dieser Verfahren hat einzigartige Eigenschaften und wird für bestimmte Schweißanwendungen.
Punktschweißen ist ein Widerstandsschweißverfahren, bei dem die Werkstücke in einer Überlappungsverbindung zusammengefügt und zwischen zwei Elektroden platziert werden. Die Widerstandswärme, die durch den Strom erzeugt wird, der durch die Kontaktfläche der Verbindung und den umgebenden Bereich fließt, schmilzt den Grundwerkstoff auf und bildet einen Schweißpunkt.
Diese Methode wird in erster Linie verwendet für Schweißbleche und besteht aus drei Schritten: Vorspannung, um einen guten Kontakt der Werkstücke zu gewährleisten, Einschalten des Stroms, um einen Nugget und einen Kunststoffring an der Schweißstelle zu bilden, und Brechen des Schmiedepunkts, wodurch der Nugget abkühlen und unter der kontinuierlichen Einwirkung von Druck kristallisieren kann, was zu einer Lötstelle mit einer dichten Struktur und ohne Lunker oder Risse führt.
Das Nahtschweißen ist eine Form des Widerstandsschweißens, bei der das Werkstück in einer Überlappungs- oder Stumpfverbindung zwischen zwei Rollenelektroden angeordnet ist. Die Rollen üben Druck auf das Werkstück aus, während sie sich drehen, und es wird kontinuierlich oder intermittierend Strom angelegt, um eine durchgehende Schweißnaht zu bilden. Dieses Schweißverfahren wird häufig für Konstruktionen verwendet, die regelmäßige Schweißnähte erfordern und Dichtungsanforderungen stellen, wobei die Blechdicke in der Regel weniger als 3 mm beträgt.
Stumpfschweißen ist ein Verfahren beim Widerstandsschweißen, bei dem zwei Werkstücke entlang ihrer gesamten Kontaktfläche miteinander verbunden werden.
Widerstandsstumpfschweißen
Das Widerstandsstumpfschweißen ist ein Verfahren, bei dem zwei Werkstücke stumpf aneinander gefügt und anschließend durch Widerstandswärme in einen plastischen Zustand gebracht werden. Anschließend wird Druck ausgeübt, um den Schweißvorgang abzuschließen. Dieses Verfahren wird in der Regel zum Schweißen von Werkstücken mit einfachen Formen, kleinen Durchmessern oder Längen von weniger als 20 mm und geringen Festigkeitsanforderungen verwendet.
Abbrennstumpfschweißen
Das Abbrennstumpfschweißen ist ein Verfahren, bei dem zwei Werkstücke zu einer Stumpfverbindung zusammengefügt und an eine Stromquelle angeschlossen werden. Die Stirnseiten der Werkstücke werden schrittweise in Kontakt gebracht und mit Widerstandswärme erhitzt, bis sie eine vorgegebene Temperatur innerhalb eines bestimmten Tiefenbereichs erreichen. Dabei entsteht ein Lichtbogen, der das Endmetall zum Schmelzen bringt. Anschließend wird die Stromzufuhr unterbrochen und eine Stauchkraft schnell aufgebracht, um das Schweißen zu beenden.
Die Verbindungsqualität des Abbrennstumpfschweißens ist besser als die des Widerstandsschweißens, und die mechanischen Eigenschaften der Schweißnaht entsprechen denen des Grundwerkstoffs. Es ist nicht notwendig, die vorgeschweißte Oberfläche der Verbindung vor dem Schweißen zu reinigen.
Das Abbrennstumpfschweißen wird häufig zum Schweißen wichtiger Werkstücke verwendet und kann zum Schweißen von gleichartigen und ungleichartigen Metallen sowie von Metalldrähten mit einer Dicke von nur 0,01 mm und Metallstäben und Profilen mit einer Dicke von bis zu 20000 mm verwendet werden.
Das Reibschweißen ist ein Pressschweißen Verfahren, bei dem die durch die Reibung zwischen den Oberflächen der Werkstücke erzeugte Wärme genutzt wird, um die Stirnfläche in einen thermoplastischen Zustand zu bringen und dann schnell zu stauchen, um das Schweißen abzuschließen.
Hauptmerkmale von Reibungsverschweißung:
Gereinigte Oberflächen: Durch die beim Schweißen entstehende Reibung werden die Oxidschicht und Verunreinigungen auf der Kontaktfläche der Werkstücke entfernt, was zu einem dichten und fehlerfreien Gefüge in der Schweißnaht führt.
Kompatibilität mit Verschiedene Metalle: Mit dem Reibschweißen können sowohl gleiche als auch unterschiedliche Metalle geschweißt werden, wodurch es sich für eine Vielzahl von Schweißanwendungen eignet.
Hohe Produktivität: Das Reibschweißen ist für seine hohe Produktivität bekannt, was es zu einem effizienten Verfahren zum Schweißen von Werkstücken macht.
Das Hartlöten lässt sich je nach Schmelzpunkt des Hartlotes in zwei Kategorien einteilen: Hartlöten und Weichlöten.
Hartlöten
Hartlöten mit einem Lötschmelzpunkt von mehr als 450 °C wird als Hartlöten bezeichnet. Zu den für das Hartlöten verwendeten Lötmitteln gehören Kupfer-, Silber- und Aluminiumlegierungen sowie andere Legierungen. Zu den üblicherweise verwendeten Flussmitteln gehören unter anderem Borax, Borsäure, Fluorid und Chlorid. Zu den Erhitzungsmethoden beim Hartlöten gehören Flammenerwärmung, Salzbaderwärmung, Widerstandserwärmung und Hochfrequenz-Induktionserwärmung. Die Festigkeit der Lötverbindung kann bis zu 490 MPa betragen und eignet sich daher für Werkstücke, die hohen Belastungen und hohen Arbeitstemperaturen ausgesetzt sind.
Löten
Löten mit einem Lotschmelzpunkt unter 450℃ wird als Weichlöten bezeichnet. Als Weichlote werden in der Regel Zinn-Blei-Legierungen verwendet. Als Flussmittel werden üblicherweise Kolophonium und Ammoniumchloridlösungen verwendet, und zum Erhitzen werden üblicherweise Lötkolben und andere Flammenheizverfahren eingesetzt.
Im Folgenden werden die wichtigsten Merkmale des Hartlötens beschrieben: