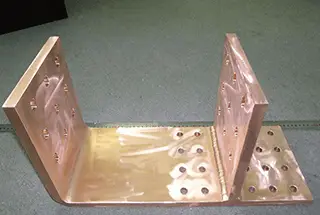
Das Schweißen von Kupfer und Kupferlegierungen stellt aufgrund ihrer hohen Wärmeleitfähigkeit und Rissneigung eine besondere Herausforderung dar. Dieser Artikel befasst sich mit verschiedenen Schweißtechniken, Werkstoffen und Vorbereitungsmethoden, die für erfolgreiche Schweißnähte an Kupfer und seinen Legierungen unerlässlich sind. Der Leser erfährt etwas über die spezifischen Probleme der Schweißbarkeit, die Vorbereitungen vor dem Schweißen und die Auswahl geeigneter Schweißverfahren und Werkstoffe. Wenn man diese Faktoren versteht, kann man die Leistung und Zuverlässigkeit von Kupferschweißnähten verbessern, die für Anwendungen in zahlreichen Branchen entscheidend sind.
Kupfer und Kupferlegierungen werden aufgrund ihrer außergewöhnlichen Eigenschaftskombination in vielen Industriezweigen eingesetzt. Diese Werkstoffe weisen eine hervorragende elektrische und thermische Leitfähigkeit, eine hohe Oxidationsbeständigkeit und eine ausgezeichnete Korrosionsbeständigkeit in verschiedenen Umgebungen wie Süßwasser, Salzwasser, alkalischen Lösungen und organischen Chemikalien auf. Es ist jedoch wichtig zu wissen, dass sie in oxidierenden Säuren korrosionsanfällig sind.
Kupferlegierungen lassen sich sowohl in der Kalt- als auch in der Warmumformung hervorragend verformen und weisen im Vergleich zu reinem Kupfer eine höhere Festigkeit auf. Ihre Vielseitigkeit hat dazu geführt, dass sie in kritischen Sektoren wie der Elektro- und Elektronikindustrie, der chemischen Verarbeitung, der Lebensmittelproduktion, der Energieerzeugung, dem Transportwesen, der Luft- und Raumfahrt und der Verteidigungsindustrie weit verbreitet sind.
Die industrielle Herstellung von Kupfer und Kupferlegierungen führt zu einer Vielzahl von Werkstoffen, die in der Regel anhand ihrer chemischen Zusammensetzung klassifiziert werden. Zu den Hauptkategorien gehören:
1. Reines Kupfer: Weichgeglühtes Reinkupfer wird für Schweißkonstruktionen bevorzugt. Gängige Sorten sind T1, T2, T3, T4 und sauerstofffreie Kupfervarianten wie TU1 und TU2.
2. Messing: Diese Kupfer-Zink-Legierungen bieten ein ausgewogenes Verhältnis von Festigkeit, Duktilität und Korrosionsbeständigkeit. Weit verbreitete Sorten sind H62, H68, H96 sowie Speziallegierungen wie Bleimessing (HPb59-1) und Zinnmessing (HSn62-1).
3. Bronze: Ursprünglich bezog sich dieser Begriff auf Kupfer-Zinn-Legierungen, heute umfasst er Kupferlegierungen, bei denen Zink oder Nickel nicht das wichtigste Legierungselement ist. Zu den bemerkenswerten Typen gehören:
4. Weißkupfer (Cupronickel): Diese Kupfer-Nickel-Legierungen weisen eine bemerkenswerte Korrosionsbeständigkeit auf, insbesondere in Meeresumgebungen.
Jeder dieser kupferbasierten Werkstoffe bietet einzigartige Eigenschaftskombinationen, die es Ingenieuren und Konstrukteuren ermöglichen, die optimale Legierung für bestimmte Anwendungen auszuwählen. Durch die kontinuierliche Entwicklung neuer Kupferlegierungen und Verarbeitungstechniken werden die Einsatzmöglichkeiten in fortschrittlichen Technologien und anspruchsvollen Umgebungen ständig erweitert.
Die Schweißbarkeit von Kupfer und Kupferlegierungen ist vergleichsweise schlecht, was das Schweißen im Vergleich zu kohlenstoffarmen Stählen deutlich erschwert. Die Hauptschwierigkeiten sind in den folgenden Aspekten zu sehen:
(1) Unzureichende Fähigkeit zur Schweißnahtbildung:
Beim Schweißen von Kupfer und den meisten Kupferlegierungen kommt es häufig zu Schwierigkeiten beim Schmelzen, unvollständiger Durchdringung der Verbindung und schlechter Oberflächenbildung. Dies ist hauptsächlich auf die hohe Wärmeleitfähigkeit von Kupfer zurückzuführen. Die Wärmeleitfähigkeit von Kupfer und den meisten Kupferlegierungen ist 7 bis 11 Mal höher als die von gewöhnlichem Kohlenstoffstahl.
Infolgedessen wird die Wärme schnell aus dem Gehäuse abgeleitet. Schweißzone. Je dicker das Werkstück ist, desto stärker ist die Wärmeabgabe. Obwohl Kupfer im Vergleich zu Eisen einen niedrigeren Schmelzpunkt und eine geringere spezifische Wärmekapazität hat, ist es immer noch schwierig, die Schmelztemperatur in der Schweißzone zu erreichen, was das Verschmelzen von Grundwerkstoff und Zusatzwerkstoff erschwert.
Darüber hinaus führt die hervorragende Wärmeleitfähigkeit von Kupfer zu einer breiteren Wärmeeinflusszone, was bei einer geringen Steifigkeit des Werkstücks zu erheblichen Verformungen führen kann. Umgekehrt kann es bei hoher Steifigkeit zu erheblichen Schweißspannungen innerhalb des Werkstücks kommen.
Die schlechte Oberflächenbildung bei Kupfer und Kupferlegierungen ist vor allem darauf zurückzuführen, dass die Oberflächenspannung beim Schmelzen ein Drittel derjenigen von Stahl beträgt und die Fließfähigkeit 1 bis 1,5 Mal höher ist als bei Stahl, was die Anfälligkeit für Metallverluste beim Schmelzen erhöht.
Daher ist beim Schweißen von reinem Kupfer und den meisten hochleitenden Kupferlegierungen neben der Verwendung von hoher Leistung und hoher Energiedichte SchweißverfahrenWenn die Schweißnaht einseitig geschweißt werden soll, ist es außerdem erforderlich, eine mehr oder weniger starke Vorwärmung einzuplanen. Einseitiges Schweißen ohne Unterstützung ist nicht zulässig, und bei einseitigem Schweißen muss eine Gegenplatte hinzugefügt werden, um die Bildung der Schweißnaht zu kontrollieren.
(2) Hohe Anfälligkeit für Hitzerisse in Schweißnähten und Wärmeeinflusszonen:
Die Neigung zur Hitzerissbildung in Schweißnähten hängt mit dem Einfluss von Verunreinigungen in der Schweißnaht zusammen und wird auch durch die während der Schweißung erzeugten Spannungen beeinflusst. Schweißverfahren. Sauerstoff ist eine häufig vorkommende Verunreinigung in Kupfer und hat einen erheblichen Einfluss auf die Neigung zur Hitzerissbildung in Schweißnähten.
Bei hohen Temperaturen reagiert Kupfer mit Luftsauerstoff und bildet Cu2O. Cu2O ist in flüssigem, aber nicht in festem Kupfer löslich und bildet ein Eutektikum mit niedrigem Schmelzpunkt. Verunreinigungen wie Bi und Pb in Kupfer und Kupferlegierungen haben niedrige Schmelzpunkte.
Während des Erstarrungsprozesses des Schweißbades bilden sie niedrigschmelzende Eutektika, die sich zwischen den Dendriten oder an den Korngrenzen verteilen und eine erhebliche thermische Sprödigkeit in Kupfer und Kupferlegierungen verursachen. Wenn sich die Schweißnaht in der Fest-Flüssig-Phase befindet, schmelzen die niedrigschmelzenden Eutektika in der Wärmeeinflusszone unter dem Einfluss der Schweißspannungen wieder auf, was zu Hitzerisse.
Kupfer und Kupferlegierungen haben relativ hohe lineare Ausdehnungskoeffizienten und Schrumpfungsraten und weisen zudem eine hohe Wärmeleitfähigkeit auf. Beim Schweißen werden Wärmequellen mit hoher Leistung benötigt, was zu einer größeren Wärmeeinflusszone führt. Dies hat zur Folge, dass die Schweißnähte erhebliche innere Spannungen auftreten, was ein weiterer Faktor ist, der zu Rissen in Schweißnähten aus Kupfer und Kupferlegierungen führt.
Außerdem besteht beim Schweißen von reinem Kupfer das Schweißgut aus einem einphasigen Gefüge. Aufgrund der hohen Wärmeleitfähigkeit von reinem Kupfer neigt die Schweißnaht zur Bildung grober Körner. Dadurch wird die Bildung von Hitzerissen noch weiter begünstigt.
Um die Bildung von Hitzerissen beim Schmelzschweißen zu verhindern, sollten daher Kupfer schweißen und Kupferlegierungen sollten die folgenden metallurgischen Maßnahmen ergriffen werden:
1) Strenge Kontrolle des Gehalts an Verunreinigungen (wie Sauerstoff, Wismut, Blei, Schwefel usw.) im Kupfer.
2) Verbesserung der Desoxidationsfähigkeit der Schweißnaht durch Zugabe von Legierungselementen wie Silizium, Mangan, Phosphor usw. zum Schweißdraht.
3) Wählen Sie Schweißmaterialien die zu einer Duplexstruktur führen können, die die Kontinuität von eutektischen Filmen mit niedrigem Schmelzpunkt unterbricht und die Richtung der säulenförmigen Körner ändert.
4) Führen Sie Maßnahmen wie Vorwärmen und langsames Abkühlen ein, um die Schweißspannungen zu reduzieren, die Größe des Wurzelspalts zu minimieren und die Abmessungen der Wurzellage zu erhöhen, um Rissbildung zu vermeiden.
(3) Anfälligkeit für Porositätsbildung:
Beim Schmelzschweißen von Kupfer und Kupferlegierungen ist die Tendenz zur Bildung von Porosität im Vergleich zu kohlenstoffarmem Stahl viel größer. Die wichtigsten Maßnahmen zur Verringerung und Beseitigung von Porosität in Kupferschweißnähten sind die Reduzierung der Wasserstoff- und Sauerstoffquellen und das Vorwärmen, um die Standzeit des Schmelzbades zu verlängern und das Entweichen von Gasen zu erleichtern.
Verwendung von Schweißdrähten mit starken Desoxidationsmitteln wie Aluminium, Titan(die auch Stickstoff und Wasserstoff entfernen können) oder die Zugabe von Elementen wie Aluminium und Zinn zu Kupferlegierungen können gute Ergebnisse bei der Desoxidation erzielen.
(4) Verringert Schweißnaht Leistung:
Beim Schmelzschweißen von Kupfer und Kupferlegierungen kommt es in den Schweißnähten zu starkem Kornwachstum, Verdampfung und Abbrand von Legierungselementen sowie zum Eindringen von Verunreinigungen, was zu einer Verschlechterung der mechanischen Eigenschaften, der elektrischen Leitfähigkeit und der Korrosionsbeständigkeit der Schweißnähte führt.
1) Signifikante Abnahme der Duktilität:
In der Schweißnaht und in der Wärmeeinflusszone kommt es zu einer Kornvergröberung, und an den Korngrenzen bilden sich verschiedene spröde Eutektika mit niedrigem Schmelzpunkt, die die Haftfestigkeit des Metalls schwächen und die Duktilität und Zähigkeit der Verbindung erheblich verringern. Zum Beispiel bei der Verwendung von Schweißelektroden aus reinem Kupfer für Lichtbogenschweißen oder Unterpulverschweißen beträgt die Dehnung der Verbindung nur etwa 20% bis 50% des Grundmaterials.
2) Verringerung der elektrischen Leitfähigkeit:
Der Zusatz von Elementen zu Kupfer verringert dessen elektrische Leitfähigkeit. Daher verschlechtert das Schmelzen von Verunreinigungen und Legierungselementen während des Schweißvorgangs bis zu einem gewissen Grad die elektrische Leitfähigkeit von Kupfer Gelenke.
3) Geringere Korrosionsbeständigkeit:
Die Korrosionsbeständigkeit von Kupferlegierungen wird durch Legierung mit Elementen wie Zink, Mangan, Nickel, Aluminium usw. erreicht. Die Verdampfung und Oxidation dieser Elemente während des Schmelzschweißens verringert in gewissem Maße die Korrosionsbeständigkeit der Verbindung. Auch die Erzeugung von Schweißspannungen erhöht das Risiko von Spannungskorrosion.
Maßnahmen zur Verbesserung der Verbindungsleistung umfassen hauptsächlich die Kontrolle des Gehalts an Verunreinigungen, die Verringerung des Legierungsabbrandes und die Durchführung einer Wärmebehandlung zur Veränderung der Mikrostruktur der Schweißnaht. Die Minimierung der Wärmezufuhr während des Schweißens und die Anwendung einer Spannungsabbau-Behandlung nach dem Schweißen sind ebenfalls von Vorteil.
Das Schweißen von Kupfer und Kupferlegierungen stellt aufgrund der außergewöhnlichen Wärmeleitfähigkeit des Materials eine besondere Herausforderung dar. Es gibt eine breite Palette von Schweißtechniken, die jeweils spezifische Vorteile für verschiedene Anwendungen bieten. Zu den gängigen Verfahren gehören Gasschweißen, Metallschutzgasschweißen (SMAW), Wolfram-Inertgasschweißen (WIG), Metallgasschweißen (GMAW/MIG) und Unterpulverschweißen (SAW).
Bei der Auswahl des optimalen Schweißverfahrens sollten mehrere Faktoren berücksichtigt werden:
Die überragende Wärmeleitfähigkeit von Kupfer (fast sechsmal so hoch wie die von Stahl) erfordert Schweißverfahren mit hoher Leistungsdichte und konzentrierter Wärmezufuhr. Dies hilft bei der Bewältigung der schnellen Wärmeabfuhr und gewährleistet eine ordnungsgemäße Verschmelzung. Techniken, die einen höheren thermischen Wirkungsgrad und eine gezielte Energieeinbringung bieten, werden im Allgemeinen bevorzugt.
Die Dicke des Kupfermaterials hat einen erheblichen Einfluss auf die Wahl des Schweißverfahrens:
Aufstrebende Technologien wie Laserschweißen und das Laser-Lichtbogen-Hybridschweißen setzen sich beim Kupferschweißen immer mehr durch, da sie hohe Präzision und minimale Wärmeeinflusszonen bieten.
Die richtige Auswahl von Schweißzusatzwerkstoffen, Schutzgasen und Wärmebehandlungen vor und nach dem Schweißen sind entscheidend für eine optimale Schweißqualität bei Kupfer und seinen Legierungen. Darüber hinaus sind strenge Sauberkeit und Oberflächenvorbereitung aufgrund der Empfindlichkeit von Kupfer gegenüber Oxidation und Verunreinigung unerlässlich.
1) Schweißdraht:
Bei der Auswahl von Schweißdraht für Kupfer und Kupferlegierungen kommt es nicht nur darauf an, die allgemeinen verfahrenstechnischen und metallurgischen Anforderungen zu erfüllen, sondern auch den Gehalt an Verunreinigungen sorgfältig zu kontrollieren und die Desoxidationsfähigkeit zu verbessern. Dies ist wichtig, um die Bildung von Hitzerissen und Porosität zu verhindern, die beim Schweißen von Kupfer häufig auftreten.
Beim Schweißen von reinem Kupfer wird der Draht normalerweise mit desoxidierenden Elementen wie Silizium (Si), Mangan (Mn) und Phosphor (P) legiert. Diese Elemente tragen dazu bei, dem Schweißbad den Sauerstoff zu entziehen, was das Risiko von Porosität verringert und die Schweißqualität insgesamt verbessert. Eine weit verbreitete Option ist der Schweißdraht aus hochreinem Kupfer (HSCu). Dieser Draht ist vielseitig und kann in verschiedenen Schweißverfahren eingesetzt werden:
2) Schweißelektroden:
Lichtbogenschweißelektroden für Kupferanwendungen können in zwei Haupttypen eingeteilt werden: Kupfer und Bronze. Bronzeelektroden werden aufgrund ihrer überlegenen Leistungsmerkmale häufiger eingesetzt.
Kupferelektroden, insbesondere solche, die Zink enthalten (wie in Messinglegierungen), werden nur selten beim Lichtbogenschweißen verwendet. Dies ist in erster Linie auf den hohen Dampfdruck von Zink bei Schweißtemperaturen zurückzuführen, der zu übermäßiger Rauchentwicklung, Porosität und uneinheitlichem Lichtbogenverhalten führen kann.
Bronzeelektroden hingegen bieten einen stabileren Lichtbogen und eine bessere Schweißbarkeit. Sie eignen sich besonders gut für das Schweißen von Kupfer mit sich selbst oder mit anderen Kupferlegierungen. Zwei häufig verwendete Elektrodenarten in dieser Kategorie sind:
Bei der Auswahl von Elektroden sollten Faktoren wie die Zusammensetzung des Grundwerkstoffs, die erforderlichen mechanischen Eigenschaften und die spezifischen Anwendungsanforderungen sorgfältig berücksichtigt werden, um optimale Schweißergebnisse zu gewährleisten.
Die Anforderungen an die Vorbehandlung von Schweißnähten aus Kupfer und Kupferlegierungen sind aufgrund der hohen Wärmeleitfähigkeit und Oxidationsanfälligkeit dieser Werkstoffe sehr hoch. Das Hauptaugenmerk bei der Reinigung vor dem Schweißen liegt auf der Entfernung von Verunreinigungen und Oxidschichten, um eine optimale Schweißqualität und -leistung zu gewährleisten.
Beginnen Sie mit dem gründlichen Entfetten der Schweißnaht und des umliegenden Bereichs (ca. 30 mm auf jeder Seite) mit einem geeigneten Lösungsmittel wie Aceton oder Isopropylalkohol. Dieser Schritt ist wichtig, um Öle oder organische Verunreinigungen zu entfernen, die die Integrität der Schweißnaht beeinträchtigen könnten.
Nach der Entfettung ist ein zweistufiges chemisches Reinigungsverfahren anzuwenden:
Verwenden Sie zur mechanischen Oxidentfernung eine Drahtbürste oder ein Rad aus rostfreiem Stahl, das speziell für Kupfer geeignet ist. Druckluftwerkzeuge können die Effizienz erhöhen, aber es muss darauf geachtet werden, dass kein übermäßiger Materialabtrag oder eine Oberflächenverunreinigung erfolgt. Fahren Sie mit dem Bürsten fort, bis ein gleichmäßiger, heller Metallglanz erreicht ist.
Schweißzusatzwerkstoffe erfordern eine ähnliche Aufmerksamkeit. Reinigen Sie Schweißdrähte mechanisch mit einem fusselfreien Tuch oder feinem Schleifpapier, um Oberflächenoxide unmittelbar vor der Verwendung zu entfernen. Bei größeren Betrieben sollten Sie automatische Drahtreinigungssysteme in Betracht ziehen, um eine gleichbleibende Qualität zu gewährleisten.
Nach der Reinigung sollte die Zeit zwischen der Vorbereitung und dem Schweißen möglichst kurz gehalten werden, um eine erneute Oxidation zu verhindern. Wenn ein sofortiges Schweißen nicht möglich ist, lagern Sie die vorbereiteten Bauteile in einer kontrollierten Umgebung mit niedriger Luftfeuchtigkeit und schützen Sie die Oberflächen mit geeigneten Antioxidationsmitteln, die mit dem Schweißverfahren kompatibel sind.
Treffen Sie beim Umgang mit Chemikalien angemessene Sicherheitsmaßnahmen, einschließlich geeigneter persönlicher Schutzausrüstung (PSA) und ausreichender Belüftung. Halten Sie sich bei der Entsorgung von verbrauchten Reinigungslösungen an die örtlichen Umweltvorschriften.
Gasschweißen:
Das Gasschweißen eignet sich zum Verbinden dünner Kupferkomponenten, zur Reparatur von Kupferteilen oder zum Schweißen unkritischer Strukturen. Seine Vielseitigkeit macht es besonders nützlich bei Wartungs- und Reparaturarbeiten.
1) Vorwärmen vor dem Schweißen:
Das Vorwärmen ist beim Gasschweißen von reinem Kupfer unerlässlich, um innere Spannungen zu verringern, Risse zu verhindern, Porosität zu reduzieren und ein vollständiges Eindringen zu gewährleisten. Bei dünnen Blechen und kleinen Schweißstücken ist auf 400-500°C (752-932°F) vorzuwärmen. Erhöhen Sie die Vorwärmtemperatur auf 600-700°C (1112-1292°F) für dicke und große Schweißteile. Messing- und Bronzelegierungen erfordern aufgrund ihrer unterschiedlichen thermischen Eigenschaften in der Regel etwas niedrigere Vorwärmtemperaturen.
2) Auswahl der Schweißparameter und -technik:
Aufgrund der hohen Wärmeleitfähigkeit von Kupfer sollte die Flammenenergie beim Schweißen 1-2 mal höher sein als bei Kohlenstoffstahl. Beim Schweißen von reinem Kupfer ist es wichtig, eine neutrale Flamme zu erhalten.
Eine oxidierende Flamme kann zur Oxidation der Schweißnaht und zum Verlust von Legierungselementen führen, was die Integrität der Verbindung beeinträchtigt. Umgekehrt erhöht eine aufkohlende Flamme den Wasserstoffgehalt in der Schweißnaht und fördert die Porositätsbildung.
Bei dünnen Blechen sollten Sie das linke Schweißverfahren anwenden, um das Kornwachstum zu minimieren. Bei Werkstücken, die dicker als 6 mm sind, wird das Rechtsschweißverfahren bevorzugt, da es eine höhere Erwärmung des Grundmetalls ermöglicht und eine bessere Sicht auf das Schmelzbad bietet, was die Betriebseffizienz verbessert.
Achten Sie auf eine zügige, kontinuierliche Bewegung des Schweißbrenners und vermeiden Sie zufällige Unterbrechungen in jeder Schweißnaht. Idealerweise sollte jede Schweißnaht in einem Durchgang ausgeführt werden, um Gleichmäßigkeit zu gewährleisten und das Risiko von Fehlern zu verringern.
Berücksichtigen Sie beim Schweißen langer Nähte vor dem Schweißen eine angemessene Schrumpfung und sorgen Sie für die richtige Positionierung. Wenden Sie beim Schweißen die Methode der segmentierten Rückwärtsschweißung an, um Verformungen und Eigenspannungen zu minimieren.
Bei spannungsführenden oder kritischen Kupferschweißnähten sind Nachbehandlungen durchzuführen:
Diese Nachbehandlungen tragen dazu bei, die Kornstruktur zu verfeinern, Eigenspannungen abzubauen und die Schweißqualität insgesamt zu verbessern, um eine optimale Leistung der geschweißten Kupferkomponenten zu gewährleisten.
Es gibt einen Elektrodenwassermantel aus desoxidiertem Kupfer TU1. Die Elektrodenverbindung wird im MIG-Schweißverfahren geschweißt; das spezifische Schweißverfahren ist in Tabelle 5-37 angegeben.
Tabelle 5-37 Schweißprozesskarte für TU1-Verbindung
Schweißprozesskarte für Fugenschweißung | Nummer | |||
Gemeinsames Diagramm:![]() | Grundmaterial Material | TU1 | TU1 | |
Dicke des Grundmaterials | 15mm | 15mm | ||
Position beim Schweißen | Flachschweißung | |||
Technik des Schweißens | Gerade Schweißnaht | |||
Vorwärmtemperatur | 500℃ | |||
Interpass-Temperatur | ≥500℃ | |||
Düsendurchmesser | Φ26mm | |||
Schutzgas | Ar | Gasdurchsatz (L/min) | Vorderseite: 25~30 Zurück: |
Reihenfolge der Schweißung | |
1 | Überprüfen Sie die Abmessungen der Rillen und die Oberflächenqualität. |
2 | Entfernen Sie jegliches Öl oder Schmutz aus der Nut und ihrer Umgebung. Reinigen Sie das Fett mit einer 10% NaOH-Wasserlösung bei einer Temperatur von 30~40℃, dann spülen Sie mit sauberem Wasser und trocknen. Entfernen Sie die Oxidschicht durch Schleifen mit einer rostfreien Stahldrahtscheibe, spülen Sie sie mit alkalischem Wasser ab, und spülen Sie sie anschließend mit sauberem Wasser ab und trocknen Sie sie. |
3 | Führen Sie die Heftschweißung für die erste Lage mit einer äußeren Positionierungsschweißtechnik durch. Die Länge sollte 100 mm betragen, und der Abstand zwischen den Schweißpunkten sollte 300 mm nicht überschreiten. Wenn in der Heftschweißnaht Risse auftreten, entfernen Sie diese und schweißen Sie erneut. |
4 | Verbinden Sie die Elektroden auf einer speziell dafür vorgesehenen Halterung. Das Werkstück mit einer elektrischen Heizung auf eine Vorwärmtemperatur von 500℃ vorwärmen und sicherstellen, dass die Zwischenlagentemperatur nicht niedriger als 500℃ ist. |
5 | Beginnen Sie das Schweißen von außen, um die Bildung von Schweißraupen auf der Innenseite der Schweißnaht zu vermeiden. Sicherstellen, dass die Rundheit des Elektrodeninnenkreises und der Glätte der Innenfläche. |
6 | Führen Sie eine Sichtprüfung durch. |
7 | Gegebenenfalls begradigen. |
8 | Führen Sie eine Wärmebehandlung nach dem Schweißen durch. |
Parameter der Schweißspezifikation
Pässe | Verfahren zum Schweißen | Schweißgutqualität | Spezifikation des Schweißmaterials | Stromarten und Polarität | Schweißstrom (Ampere) | Lichtbogenspannung (Volt) | Geschwindigkeit beim Schweißen (mm/pro Durchgang) | Bemerkungen |
1~2 | MIG (halbautomatisch) | HSCu | 1.6 | DCEP | 350~400 | 30~35 | 250~300 |