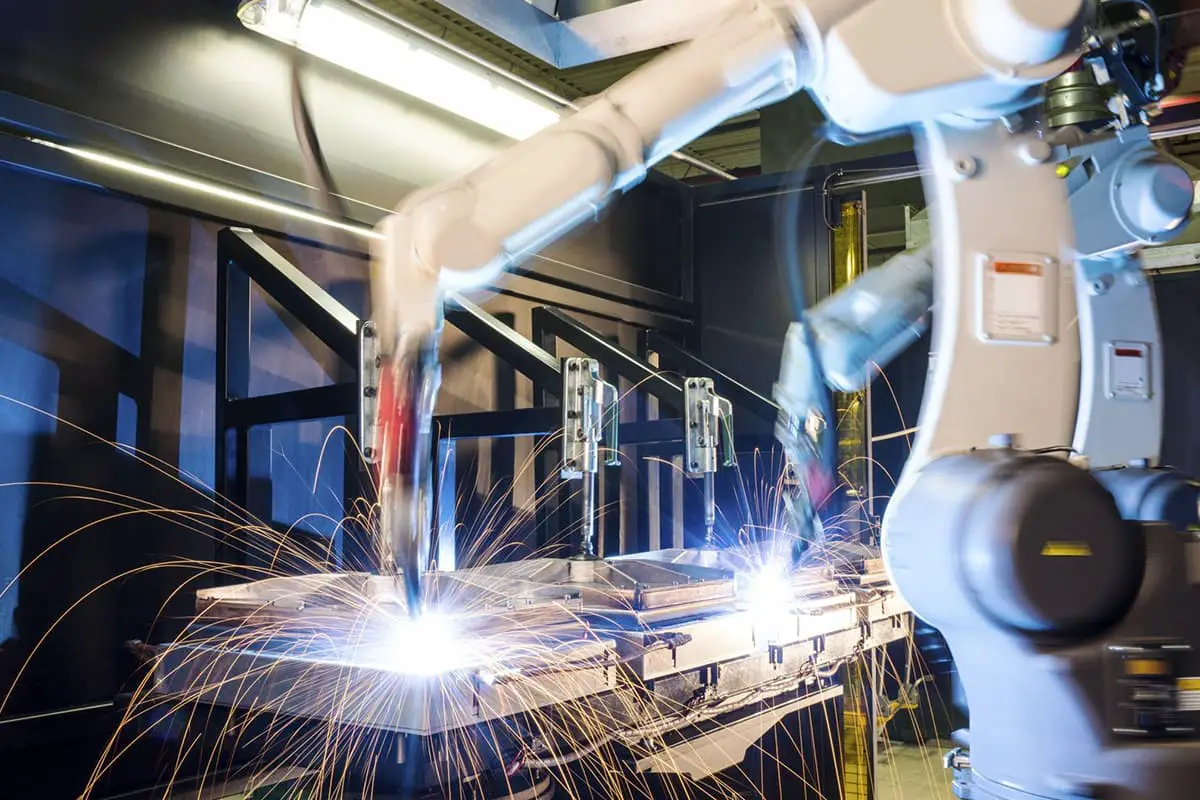
Haben Sie sich schon einmal gefragt, wie sich die Qualität des Schweißens auf die Zuverlässigkeit von Elektronikprodukten auswirkt? Beim Schweißen kann schon ein kleiner Fehler zu erheblichen Ausfällen führen. Dieser Artikel befasst sich mit den wichtigsten Normen und Prüfverfahren zur Gewährleistung der Schweißqualität und behandelt Aspekte wie elektrische und mechanische Integrität, Aussehen und Prüftechniken. Am Ende werden Sie wissen, wie Sie häufige Schweißfehler erkennen und vermeiden können, um robuste und zuverlässige elektronische Baugruppen zu gewährleisten. Tauchen Sie ein und entdecken Sie, wie die Beherrschung dieser Normen Ihre Produkte vor kostspieligen Fehlfunktionen bewahren kann.
Das Schweißen ist ein wichtiges technologisches Verfahren bei der Montage elektronischer Produkte und ein entscheidender Schritt bei deren Herstellung.
Sie wird in großem Umfang bei der Erprobung, Anpassung und Herstellung elektronischer Produkte eingesetzt und stellt eine erhebliche Arbeitsbelastung dar. Die Qualität des Schweißens hat einen direkten Einfluss auf die Qualität des Produkts.
Die meisten Fehler in elektronischen Produkten sind, abgesehen von Bauteilproblemen, in erster Linie auf schlechte Schweißqualität. Daher ist die Beherrschung der Schweißtechnik für die Produktqualität von entscheidender Bedeutung.
Die Qualitätsanforderungen an Schweißpunkte sollten einen guten elektrischen Kontakt, einen stabilen mechanischen Kontakt und ein ästhetisches Aussehen umfassen.
Der wichtigste Aspekt bei der Sicherstellung der Qualität der Schweißpunkte ist die Vermeidung kalter Lötstellen.
Schweißen ist die wichtigste Methode zur Herstellung elektrischer Verbindungen in elektronischen Schaltungen. Lötverbindungen werden nicht durch Druck hergestellt, sondern durch die Bildung einer festen Legierungsschicht während des Schweißverfahren um den Zweck der elektrischen Verbindung zu erreichen.
Wenn das Lot nur auf der Oberfläche der geschweißten Teile gestapelt ist oder nur ein kleiner Teil eine Legierungsschicht bildet, kann es schwierig sein, Probleme mit der Schweißstelle während der ersten Tests und des Betriebs zu erkennen.
Eine solche Schweißstelle kann kurzfristig Strom leiten, aber bei veränderten Bedingungen und im Laufe der Zeit oxidiert die Kontaktschicht, löst sich ab und erzeugt intermittierende oder nicht funktionierende Stromkreise.
Die Beobachtung des Äußeren der Schweißstelle kann noch in Ordnung sein, was bei der Verwendung elektronischer Instrumente ein großes Problem darstellt, das bei der Produktherstellung ernst genommen werden muss.
Schweißen dient nicht nur der elektrischen Verbindung, sondern fixiert auch Bauteile und sorgt für eine mechanische Verbindung. Damit die geschweißten Teile bei Vibrationen oder Stößen nicht abfallen oder sich lösen, müssen die Schweißpunkte eine ausreichende mechanische Festigkeit aufweisen.
In der Regel kann dies erreicht werden, indem die Anschlussklemmen der zu verschweißenden Bauteile gebogen und dann die Schweißung durchgeführt wird.
Die als Lötmaterial verwendete Blei-Zinn-Legierung hat eine relativ geringe Festigkeit, wobei die Zugfestigkeit der üblicherweise verwendeten Blei-Zinn-Lötmaterialien bei etwa 3-4,7 kg/cm2 liegt, was nur 10% von gewöhnlichem Stahl entspricht.
Um die Festigkeit zu erhöhen, ist eine ausreichende Verbindungsfläche erforderlich. Wenn es sich um eine kalte Lötstelle handelt, bei der das Lötzinn lediglich auf dem Lötauge aufgeschichtet ist, wird sie keine Festigkeit haben.
Ein guter Schweißpunkt benötigt eine angemessene Menge an Lot, hat einen metallischen Glanz, weist keine Spitzen oder Brücken auf und beschädigt nicht die Isolierschicht des Drahtes oder benachbarte Bauteile. Ein gutes Aussehen spiegelt die Qualität der Schweißung wider.
Hinweis: Das Vorhandensein eines metallischen Glanzes deutet auf eine geeignete Schweißtemperatur und die Bildung einer Legierungsschicht, die nicht nur aus ästhetischen Gründen erforderlich ist.
Das Aussehen eines typischen Schweißpunktes ist in Abbildung 1 dargestellt und weist die folgenden gemeinsamen Merkmale auf:
Neben der Sichtprüfung (oder der Verwendung einer Lupe oder eines Mikroskops), um zu prüfen, ob der Schweißpunkt den oben genannten Normen entspricht, umfasst die Prüfung der Schweißqualität auch Folgendes: fehlende Schweißnähte, spitzes Lot, durch Lot verursachte Kurzschlüsse zwischen Drähten (d. h. "Überbrückung"), Schäden an der Isolierung von Drähten und Bauteilen, Drahtformung, Lotspritzer.
Bei der Inspektion werden neben visuellen Kontrollen auch Methoden wie Berührung, Abtasten mit einer Pinzette und Ziehen von Drähten eingesetzt, um Defekte wie Drahtbruch und Ablösen von Pads festzustellen.
Bei der Sichtprüfung wird die Schweißqualität von außen geprüft, um eventuelle Mängel an der Schweißstelle festzustellen.
Zu den wichtigsten Inhalten der Sichtprüfung gehören:
1. Ob es fehlende Schweißnähte gibt, d.h. Schweißpunkte, die gelötet werden sollten, sind nicht vorhanden.
2. Der Glanz der Schweißstelle.
3. Ob genügend Lot an der Schweißstelle vorhanden ist.
4. Ob um die Schweißstelle herum Restflussmittel vorhanden sind.
5. Ob es durchgehende Schweißnähte gibt und ob die Polster abgerutscht sind.
6. Ob die Schweißstelle Risse aufweist.
7. Ob der Schweißpunkt ungleichmäßig ist; ob es eine stachelige Erscheinung am Schweißpunkt gibt.
Abbildung 2 zeigt die richtige Form des Schweißpunktes. In der Abbildung ist (a) die Form eines gerade eingefügten Schweißpunktes und (b) die Form eines halb gebogenen Schweißpunktes dargestellt.
Die Berührungsprüfung bezieht sich hauptsächlich darauf, ob bei der Berührung lockere oder unsicher verschweißte Bauteile vorhanden sind.
Halten Sie das Bauteilkabel mit einer Pinzette fest und ziehen Sie vorsichtig daran, um zu sehen, ob es sich lockert. Ob das Lot auf der Oberseite abfällt, wenn der Schweißpunkt geschüttelt wird.
Nachdem die äußere Prüfung abgeschlossen und die korrekte Verdrahtung bestätigt wurde, kann die Einschaltprüfung durchgeführt werden, die für die Prüfung der Schaltkreisleistung entscheidend ist.
Wenn die externe Inspektion nicht sorgfältig durchgeführt wird, ist die Einschaltkontrolle nicht nur schwieriger, sondern kann auch zu Schäden an der Ausrüstung und zu Sicherheitsunfällen führen.
Wenn zum Beispiel die Stromversorgungsverbindung nicht gut verlötet ist, kann das Gerät bei der Einschaltkontrolle nicht eingeschaltet werden, was eine Überprüfung unmöglich macht.
Einschaltinspektion und Analyse der Grundursache
Elektrifizierung Inspektion
(1) Ausfall eines Bauteils
(2) Schlechte elektrische Leitfähigkeit
Bei der Prüfung nach dem Einschalten lassen sich viele kleinere Defekte feststellen, z. B. Schaltkreisüberbrückungen, die mit dem bloßen Auge nicht sichtbar sind. Es ist jedoch schwierig, potenzielle Probleme wie interne Trockenlötungen zu erkennen.
Daher liegt die grundlegende Lösung in der Verbesserung des Qualifikationsniveaus des Schweißers, anstatt die Aufgabe dem Prüfverfahren zu überlassen.
Der Zusammenhang zwischen möglichen Fehlern, die bei der Einschaltkontrolle auftreten können, und Schweißfehler ist in Abbildung 3 als Referenz dargestellt.
Es gibt zahlreiche Ursachen für Schweißfehler. Bei bestimmten Materialien (Lot und Flussmittel) und Werkzeugen (Lötkolben, Schablone) werden die angewandten Methoden und das Verantwortungsbewusstsein des Bedieners zu entscheidenden Faktoren.
Die häufigsten Fehler, die bei der Positionierung von PCBA-Komponenten und Lötstellen auftreten, sind in den Tabellen 1 und 2 aufgeführt.
In diesen Tabellen sind das Aussehen, die Eigenschaften und die Gefahren von häufigen Lötstellenfehlern zusammen mit einer Analyse ihrer Ursachen aufgeführt.
Tabelle 1: Analyse der häufigsten Lötstellenfehler
Fehler an der Schweißstelle | Merkmale der Konstruktion | Schaden | Analyse der Grundursache |
Falsches Schweißen![]() | Es gibt eine deutliche schwarze Linie zwischen dem Lot und dem Anschluss des Bauteils oder der Kupferfolie, wobei das Lot zur Grenze hin zurückweicht. | Kann nicht richtig funktionieren. | 1. Die Bauteilanschlüsse wurden nicht ordnungsgemäß gereinigt, sind nicht ausreichend verzinnt, oder das Lötzinn ist oxidiert. 2. Die Leiterplatte wurde nicht gründlich gereinigt, und die Qualität des aufgetragenen Flussmittels war mangelhaft. |
Lötkurzschluss![]() | Übermäßiges Löten hat zu einem Kurzschluss geführt, weil das Lötzinn zwischen benachbarten Punkten eine Brücke bildet. | Elektrischer Kurzschluss. | 1. Die Schweißtechnik ist falsch. 2. Es gibt einen Überschuss an Lot. |
Überbrückung![]() | Benachbarte Drähte verbunden. | Elektrischer Kurzschluss. | 1. Die Bauteilanschlüsse sind nach dem Schneiden zu lang. 2. Reste von Bauteilanschlüssen wurden nicht beseitigt. |
Kratzbewegung Schweißen![]() | Es gibt Risse, rau wie zerbröckeltes Brot, mit Lücken in den Fugen. | Die Stärke ist gering, es funktioniert entweder nicht oder nur zeitweise. | Wenn das Lot noch feucht ist und Bewegungen ausgesetzt ist. |
Unzureichendes Lot![]() | Der Schweißbereich ist kleiner als 75% des Pads, und das Lot hat keine glatte überplattete Oberfläche gebildet. | Unzureichende mechanische Festigkeit. | 1. Schlechter Lotfluss oder vorzeitiges Abziehen des Schweißdrahtes. 2. Unzureichender Fluss. 3. Die Schweißdauer ist zu kurz. |
Überschüssiges Lot![]() | Die Oberfläche des Lots ist konvex. | Die Verschwendung von Lötzinn könnte möglicherweise Defekte verbergen. | Der Abzug des Geldes wurde verzögert. |
Überhitzung![]() | Der Schweißpunkt erscheint weiß, ohne Metallglanz und mit einer eher rauen Oberfläche. | Das Lötpad ist anfällig für Ablösungen, was zu einer geringeren Festigkeit führt. | Die Leistung des Lötkolbens ist zu hoch, was zu langen Erhitzungszeiten führt. |
Kaltes Löten![]() | Die Oberfläche stellt sich als tofuähnliches Granulat dar, und manchmal kann sie Risse aufweisen. | Die Festigkeit ist gering, und die Leitfähigkeit ist schlecht. | Rühren Sie das Werkstück um, bevor das Lot erstarrt. |
Kein Docht![]() | Wenn der Kontaktwinkel mehr als 90 Grad beträgt, kann sich das Lot nicht ausbreiten oder bedecken, ähnlich wie ein Öltropfen, der auf einer feuchten Oberfläche ruht. | Die Festigkeit ist gering, und die Leitfähigkeit ist schlecht. | Die gelöteten Metallflächen sind nicht symmetrisch, und auch die Wärmequelle selbst ist nicht symmetrisch. |
Lockerheit![]() | Die Leitungen von Drähten oder Bauteilen können sich verschieben. | Schlechte oder keine Leitfähigkeit. | 1. Das Blei hat sich bewegt, bevor das Lötzinn erstarrt war, wodurch ein Spalt entstand. 2. Das Blei wurde nicht behandelt (schlechte oder keine Benetzung). |
Ziehen bis zu einem Punkt![]() | Die Entstehung der Schneidekante. | Das Erscheinungsbild ist mangelhaft, was leicht zu Brückenbildung führen kann. | Ein unsauberer Lötkolben oder ein Lötkolben, der zu früh entfernt wird, bevor die Lötstelle den Schmelzpunkt des Lots erreicht hat, kann dazu führen, dass das Lot anhaftet und sich beim Herausziehen des Lötkolbens neu bildet. |
Lochkamera![]() | Bei einer Sichtprüfung oder mit einer schwachen Lupe können Löcher in der Kupferfolie entdeckt werden. | Eine unzureichende Festigkeit kann dazu führen, dass die Schweißpunkte korrosionsanfällig sind. | Die Verschmutzung von Lötmaterialien, Bauteilmaterialien und der Umwelt. |
Delamination von Kupferfolie![]() | Die Kupferfolie wird von der Leiterplatte abgezogen. | Die Leiterplatte ist beschädigt. | Die Schweißdauer ist zu lang. |
Tabelle 2: Standard- und Defektanalyse von SMT-Lötverbindungen für oberflächenmontierte Bauteile.
Projekt | Diagramm | Wichtige Punkte | Inspektionswerkzeuge | Beurteilungskriterien: |
1. Position des Teils. | ![]() | Die Amplitude "W" der Verbindungselektrode deckt mehr als die Hälfte der leitenden Oberfläche ab. Wichtig: Die Versetzung des Bauteils sollte durch Sichtprüfung ermittelt werden, nicht durch Überprüfung mit einem Prüfgerät. Verwenden Sie stattdessen ein Vergrößerungsglas zur direkten Beobachtung. | Bremssättel | Mehr als die Hälfte |
2. Position des Teils. | ![]() | Mehr als die Hälfte der Länge E der Verbindungselektrode ist von der leitenden Oberfläche bedeckt. Vorsichtsmaßnahme: Der Versatz des Teils sollte durch Sichtprüfung festgestellt und nicht mit einem Prüfgerät und einer Lupe überprüft werden. | Bremssättel | Mehr als die Hälfte |
3. Position des Teils. | ![]() | Bei der Neigung der Verbindungsteile reicht es aus, wenn mehr als die Hälfte der Amplitude W der Verbindungselektrode auf der leitenden Oberfläche liegt. Hinweis: Verlassen Sie sich bei Unstimmigkeiten in der Teilepositionierung auf die Sichtprüfung und verwenden Sie kein Prüfgerät zur Bestätigung, sondern eine Lupe zur direkten Beobachtung. | Bremssättel | Mehr als die Hälfte |
4. Menge des Lötzinns. | ![]() 1/2F | Die Elektrode ist mit Zinn verlötet, dessen Ausdehnung die Hälfte der Höhe F und die Hälfte der Breite W überschreitet. | Bremssättel | Mehr als die Hälfte |
5. Menge des Lötzinns. | ![]() | Löten Sie die Verbindungselemente in der längeren Richtung, ausgehend von der Endfläche der Verbindungselektrode, mit einer Lötdicke von mehr als 0,5 mm. Zum Beispiel, G. | Bremssättel | Über 0,5 mm |
6. Menge des Lötzinns. | ![]() | Die Höhe des Lotes sollte weniger als 0,3 mm über der Oberfläche des zu verbindenden Bauteils liegen. | Skalenanzeige | Weniger als 0,3 mm |
7. Menge des Lötzinns. | ![]() | Die Lötstellen an den Verbindungsteilen dürfen sich nicht überlappen, wie z. B. in Form eines "I". | Visuelle Inspektion | Kann nicht übereinander gestapelt werden |
8. Haftung des Teils. | ![]() Qualitätsprodukt | Zwischen der Elektrode des Verbindungselements und der Leiterplatte befindet sich kein Klebstoff. | Visuelle Inspektion | Kann nicht unter der Elektrode liegen |
![]() Qualitätsprodukt | ||||
9. Haftung des Teils. | ![]() Defektes Produkt | Zwischen der Elektrode des Verbindungselements und der Leiterplatte befindet sich kein Klebstoff. | Visuelle Inspektion | Kann nicht unter der Elektrode liegen |
10. Haftung des Teils. | ![]() Darf keine Bindemittel enthalten. | Auf den Elektrodenbereich der Verbindungselemente dürfen keine Klebstoffe aufgebracht werden. | Visuelle Inspektion | Kann nicht geklebt werden |
11. Position des Teils. | ![]() Nicht berühren G | Die Positionierung der Verbindungselemente sollte nicht versetzt oder geneigt sein, um benachbarte Leiter zu berühren. Für Aspekte, die nicht visuell bestimmt werden können, sind Prüfgeräte zu verwenden. | Visuelle Inspektion | Kann keinen Kontakt herstellen |
12. Menge des Lötzinns. | ![]() Lötmittelüberlauf | Das Lötzinn darf nicht über die Breite der leitenden Oberfläche hinausfließen. | Visuelle Inspektion | Kann nicht überlaufen |
13. Position des Teils. | ![]() | Mehr als die Hälfte der Breite J der Schenkel des IC-Bauteils liegt oberhalb der leitenden Oberfläche. | Bremssättel | Mehr als die Hälfte |
14. Position des Teils. | ![]() | Mehr als die Hälfte der Länge K der Schenkel des IC-Bauteils berührt die leitende Oberfläche. | Bremssättel | Mehr als die Hälfte |
15. Position des Teils. | ![]() | Die Verschiebung der Bauteilposition gegenüber dem benachbarten Leiter sollte ≥0,2 mm betragen; sie darf den benachbarten Leiter nicht berühren. | Visuelle Inspektion | Kann keinen Kontakt herstellen |
16. Instabiles Bein. | ![]() | Bei Gegenständen mit angehobenen Enden sollte die Anhebung weniger als 0,5 mm betragen. | Bremssättel | Weniger als 0,5 mm |
17. Instabiles Bein. | ![]() | Bei Gegenständen, bei denen die Basis angehoben wird, sollte die Anhebung an der Basis weniger als 0,5 mm betragen. | 0,5 mm Spurweite | Weniger als 0,5 mm |
18. Instabiles Bein. | ![]() | Bei Artikeln, bei denen der gesamte Fuß angehoben wird, sollte die Erhöhung weniger als 0,5 mm betragen. | 0,5 mm Spurweite | Weniger als 0,5 mm |
19. Instabiles Bein. | ![]() | Die Höhe des Lots von der Oberfläche der Leiterplatte bis zur Spitze des Lots beträgt weniger als 1 mm. | Bremssättel | Weniger als 1mm |
20. Instabiles Bein. | ![]() | Die Höhe des Lots am Bauteilbeinchen liegt unter 0,5 mm. | Bremssättel | Weniger als 0,5 mm |