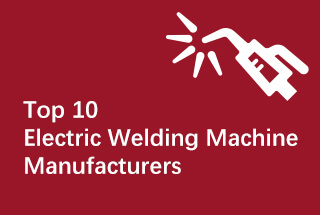
Dieser Artikel erkundet die faszinierende Welt des Schweißens, vom Lichtbogenhandschweißen bis hin zu fortschrittlichen Schutzgasverfahren. Sie erfahren mehr über die Methoden, Vorteile und Anwendungen der verschiedenen Schweißverfahren. Machen Sie sich bereit zu erfahren, wie diese wichtigen Techniken unsere moderne Welt prägen!
Schweißen ist das Verfahren zum Verbinden desselben Metalls oder verschiedener Metalle.
Nach dem Schweißvorgang bildet sich in einem bestimmten Bereich ein Polymer aus Metall und Nichtmetall, das als Schweißnaht bezeichnet wird.
Je nach den Merkmalen des Schweißverfahrens kann man zwischen Schmelzschweißen, Pressschweißen und Hartlöten.
Schmelzschweißen:
Das Schweißverfahren, bei dem das Metall an der Verbindungsstelle unter Einwirkung hoher Temperaturen geschmolzen wird usw.
Die Schweißung wird unter einem bestimmten Druck durchgeführt.
Verwenden Sie das Metall, dessen Schmelzpunkt niedriger ist als der Schmelzpunkt des Grundmetalls, als Schweißzusatz, um die Schweißnaht und den Schweißzusatz auf die Temperatur zwischen dem Schmelzpunkt des Grundmetalls und dem Schmelzpunkt des Schweißzusatzes zu erwärmen, so dass der Schweißzusatz flüssig ist und das Grundmetall benetzt, den Fugenspalt füllt und mit dem Grundmetall diffundiert, um das Schweißen zu erreichen.
Spezifische Klassifizierung:
Was ist ein Bogen?
Die starke und dauerhafte Gasentladung zwischen dem Werkstück und der Elektrode wird als Lichtbogen bezeichnet.
Um es kurz zu machen: Es handelt sich um ein Phänomen der Gasentladung.
Der Lichtbogen besteht jedoch aus drei Teilen: dem Lichtbogensäulenbereich, dem Kathodenbereich und dem Anodenbereich.
Lichtbogen-Temperatur:
Hitze in der Lichtbogenzone:
Was ist Lichtbogenschweißen?
Was ist Lichtbogenhandschweißen? Vereinfacht gesagt, ist das Lichtbogenschweißen ein Schweißverfahren, bei dem der Lichtbogen als Wärmequelle dient.
Das Lichtbogenschweißen mit handgeführten Schweißdrähten wird als Lichtbogenhandschweißen bezeichnet, kurz Lichtbogenhandschweißen genannt.
Wie wird das Elektroden-Lichtbogenhandschweißen durchgeführt?
(1) Der Lichtbogen brennt zwischen der Elektrode und dem Schweißgut, und die Hitze des Lichtbogens lässt das Werkstück und die Elektrode gleichzeitig zu einem Schmelzbad schmelzen;
(2) Der Lichtbogen schmilzt oder verbrennt die Beschichtung der Elektrode, wobei Schlacke und Gas entstehen, die das geschmolzene Metall und das Schmelzbad schützen;
(3) Wenn sich der Lichtbogen vorwärts bewegt, kühlt das nachfolgende Schmelzbad ab und erstarrt, während kontinuierlich ein neues Schmelzbad erzeugt wird, wodurch eine kontinuierliche Schweißnaht entsteht.
Vorteil des Elektroden-Lichtbogenhandschweißens:
Einfache Ausstattung, flexible Bedienung und hohe Anpassungsfähigkeit.
Nachteil des Elektroden-Lichtbogenhandschweißens:
Die Produktionseffizienz ist niedrig, die Arbeitsintensität ist hoch und die Qualität des Schweißens Gelenke sind nicht leicht zu garantieren.
Anmeldung des Elektroden-Lichtbogenhandschweißens:
Sie kann die meisten Metalle schweißen, ist für verschiedene Schweißpositionen geeignet und kann sowohl dünne als auch dicke Bleche schweißen.
Was versteht man unter dem automatischen Unterpulverschweißen?
Automatisches Schweißen - Der Schweißvorgang wird automatisch durch die mechanische Vorrichtung abgeschlossen.
Unterpulverschweißen - Schweißen, bei dem ein Lichtbogen unter einer körnigen Flussmittelschicht brennt.
Wie funktioniert der automatische Unterwasserbogen Schweißverfahren?
(1) Das Flussmittel fließt aus dem Trichter und wird gleichmäßig auf dem geschweißten Teil des Werkstücks verteilt, um eine Flussmittelschicht (30-50 mm) zu bilden;
(2) Der kontinuierlich zugeführte Schweißdraht erzeugt einen Lichtbogen zwischen dem Schweißdraht und dem Schweißgut unter der Flussmittelschicht, der den Schweißdraht, das Werkstück und das Flussmittel zum Schmelzen bringt, ein Metallschmelzbad bildet und sie von der Luft isoliert;
(3) Während sich die Schweißmaschine automatisch vorwärts bewegt, schmilzt der Lichtbogen kontinuierlich das Metall, den Draht und das Flussmittel der vorderen Schweißnaht, während die Kante hinter dem Schmelzbad abkühlt und zu einer Schweißnaht erstarrt, und die flüssige Schlacke anschließend zu einer harten Schlackenhülle kondensiert.
Warum sollte eine Flussmittelschicht auf die Oberfläche der Schweißstelle aufgetragen werden?
Sie hat die folgenden drei Funktionen:
(1) Schützende Wirkung
Das Flussmittel schmilzt und bildet Schlacke und Gas, wodurch die Luft effektiv isoliert wird, das Tröpfchen und das Schmelzbad geschützt werden und das Verbrennen von Legierungselemente;
(2) Metallurgische Wirkung
Im Schweißprozess spielt es die Rolle der Desoxidation und der Ergänzung von Legierungselemente;
(3) Verbesserung des Schweißprozesses
Lassen Sie den Lichtbogen gleichmäßig brennen, damit die Schweißnaht schön wird.
Was sind die Merkmale des automatischen Unterpulverschweißens?
In welchen Bereichen werden sie hauptsächlich eingesetzt?
Vorteil des automatischen Unterpulverschweißens:
Hohe Produktionsleistung (5~mal höher als beim manuellen Lichtbogenschweißen);
Gut Schweißqualität (weniger Porosität und Schlackeneinschlüsse);
Geringe Kosten (Einsparung von Arbeit, Zeit und Material);
Gute Arbeitsbedingungen (keine Spritzer, wenig Arbeitskräfte).
Nachteil des automatischen Unterpulverschweißens:
Nicht geeignet zum Schweißen komplexer Schweißnähte und enger Räume;
Die Ausrüstung ist komplex und der erforderliche Schweißstrom ist groß (ein kleiner Strom führt zu einem instabilen Lichtbogen);
Schlechte Anpassungsfähigkeit (gilt für Flachschweißen, lange gerade Naht und Rundnaht mit größerem Durchmesser).
Anmeldung:
Es wird für lange gerade Schweißnähte und Rundschweißnähte mit großem Durchmesser bei der Herstellung von mittelgroßen Blechen verwendet, z. B. für Kessel, Druckbehälter, Schiffe usw.
Um eine vernünftige Schweißnahtbildung und eine gute Schweißqualität zu erreichen sowie die Schweißgeschwindigkeit zu verbessern, hat sich das Mehrdraht-Unterpulverschweißen durchgesetzt.
Es wird häufig in Anwendungen eingesetzt, die eine hohe Schweißeffizienz erfordern, z. B. in der Windenergie, im Schiffbau, bei Druckbehältern, im Schwermaschinenbau, bei Pipelines und in anderen Industriezweigen.
Multi-Power-Serie Mehrdraht-Unterpulverschweißen:
Es wird hauptsächlich zum Schweißen von Rohrleitungen verwendet.
Je nach Anwendung kann es in das Außenschweißen von langen geraden Längsnähten von Rohrleitungen, das Innenschweißen von langen geraden Längsnähten von Rohrleitungen, das Außenschweißen von spiralgeschweißten Rohren, das Innenschweißen von spiralgeschweißten Rohren und andere verschiedene Typen unterteilt werden.
Einzelstrom-Parallel-Mehrdraht-Unterpulverschweißen:
Erhebliche Verbesserung der Produktionseffizienz, Erhöhung der Schweißgeschwindigkeit, Verringerung des Flussmittelverbrauchs, Verringerung des Wärmeeintrags und der Verformung, Energieeinsparung, effizientere Grundierung und gleichmäßigere Abdeckung.
Das Lichtbogenschweißen mit Gas als Lichtbogenmedium und zum Schutz des Lichtbogens und des Schweißbereichs wird als Schutzgasschweißen (GMAW) bezeichnet.
Mit anderen Worten, Schutzgasschweißen verwendet Gas als Medium und Schutz.
Welche spezifischen Arten gibt es?
Klassifiziert nach dem Schmelzen der Elektrode und der Art der Schutzgas:
Abschirmgas:
Elektrode:
Unterschiede zwischen abschmelzender und nicht abschmelzender Elektrode beim Schutzgasschweißen:
MIG/MAG: Direkte Zuführung des Schweißdrahtes, der gleichzeitig Elektrode und Schweißzusatz ist.
WIG: Wolfram-Elektrode ist die Elektrode und schmilzt nicht; der Schweißdraht wird separat zugeführt und nur als Zusatzwerkstoff verwendet
Argon-Lichtbogenschweißen
Was sind die Merkmale des Argon-Lichtbogenschweißens?
Was sind die wichtigsten Anwendungen?
Wolfram-Elektrode, manueller Drahtvorschub.
Der Schweißdraht ist nur der Zusatzwerkstoff.
Der Schweißdraht leitet den Strom nicht weiter, so dass es keine Spritzer gibt.
Um jedoch zu vermeiden, dass die Wolframelektrode schmilzt und verbrennt, was zu einer Verunreinigung des Wolframs im Schmelzbad führen kann, darf der Schweißstrom nicht zu hoch sein.
Es können nur dünne Bleche unter 4 mm geschweißt werden.
Schmelzelektrode, automatische Drahtzuführung.
Der Schweißdraht ist sowohl eine Elektrode als auch ein Schweißzusatzwerkstoff.
Es gibt kein Schmelzen und keinen Verbrennungsverlust der Wolframelektrode.
Der Schweißstrom kann in einem weiten Bereich eingestellt werden, so dass dünne und mittelstarke Bleche geschweißt werden können.
Vorteile des Argon-Lichtbogenschweißens
Es kann in alle Richtungen geschweißt werden;
Leicht zu beobachten und automatisch zu kontrollieren;
Gute Schutzwirkung, stabiler Lichtbogen und gute Schweißqualität;
Er kann fast alle Metalle schweißen.
Nachteil des Argon-Lichtbogenschweißens
Hohe Argonkosten;
Die Stromdichte beim Argon-Lichtbogenschweißen ist hoch, das ausgestrahlte Licht ist relativ stark, und die vom Lichtbogen erzeugte ultraviolette Strahlung ist groß und schädigt den Körper stärker;
Die Wärmeeinflusszone des Argon-Lichtbogenschweißens ist groß, und das Werkstück ist anfällig für Risse, Nadellöcher, Verschleiß, Kratzer, Hinterschneidungen und andere Defekte nach der Reparatur;
Anwendung des Argon-Lichtbogenschweißens
Es wird hauptsächlich zum Schweißen von Nichteisenmetallen und legierten Stählen verwendet, die leicht oxidiert werden können (hauptsächlich Schweißen von Al, Mg, Ti und deren Legierungen sowie von rostfreien Stählen).
CO2 Schutzgasschweißen
Das Prinzip der CO2 Die Funktionsweise des Schutzgasschweißens entspricht der des MIG-Schweißens, mit dem Unterschied, dass das Schutzgas CO2.
Das Volumen des CO-Gases in der Schmelze und im Tropfen dehnt sich schnell aus und platzt, was zu Spritzen führt.
Es kann Metall oxidieren und Legierungselemente verbrennen, kann aber keine Nichteisenmetalle schweißen und legierter Stahl.
Vorteile des CO2-Schutzgasschweißens
Niedrige Kosten (40%~50% für Unterpulverschweißen und Lichtbogenhandschweißen);
Hohe Effizienz (hohe Stromdichte, große Eindringtiefe und schnelle Schweißgeschwindigkeit);
Gute Schweißqualität (Luftstromkühlung, kleine Wärmeeinflusszone, geringe Verformung);
In der Lage, in allen Positionen zu schweißen.
Nachteil des CO2-Schutzgasschweißens
Schlechte Schweißnahtbildung und große Spritzer;
Ausbrennen von Legierungselementen, leichtes Entstehen von Poren;
Geringer Windwiderstand beim Schweißen, geeignet für den Betrieb in Innenräumen.
Anwendung des CO2-Schutzgasschweißens
Es ist für das Schweißen von kohlenstoffarmen Stahl und niedrig legiertem Stahlblech (0,8~4mm) geeignet.
Es muss ein Schweißdraht verwendet werden, der Desoxidationsmittel enthält, und der Gleichstromanschluss muss umgedreht werden;
Außerdem darf während des Schweißens kein Wind herrschen, und das Schweißen in geschlossenen Räumen ist vorzuziehen.
Das Elektroschlackeschweißen ist ein Schweißverfahren, bei dem der durch den Strom in der Schlacke erzeugte Widerstand genutzt wird, um den Schweißdraht und den Grundwerkstoff zu schmelzen und eine Schweißnaht zu bilden.
Wie kann man Elektroschlackeschweißen durchgeführt wird, finden Sie in der folgenden Analyse:
(1) Schließen Sie zu Beginn den Schweißdraht und die Startrille kurz, um den Lichtbogen zu starten;
(2) Kontinuierlich eine kleine Menge festes Flussmittel hinzufügen, um es mit der Hitze des Lichtbogens zu schmelzen und flüssige Schlacke zu bilden;
(3) Wenn die geschmolzene Schlacke eine bestimmte Tiefe erreicht, erhöhen Sie die Vorschubgeschwindigkeit des Schweißdrahtes und reduzieren Sie die Spannung, so dass der Schweißdraht in das Schlackenbad eintaucht und der Lichtbogen erlischt, wodurch er in den Elektroschlackeschweißen Prozess.
Was sind die Merkmale des Elektroschlackeschweißens?
Für welche Schweißbereiche?
Vorteile des Elektroschlackeschweißens
Hohe Produktivität, da die Dicke der Schweißnaht nicht berücksichtigt werden muss;
Wenig Schweißfehler und gute Schweißqualität;
Es ist keine Nut erforderlich, und die Kosten sind gering.
Dis Vorteil des Elektroschlackeschweißens
Die Wärmezufuhr ist groß, und in der Nähe der Schweißstelle kann es leicht zu Überhitzungen kommen;
Das Schweißgut hat ein grobkristallines Gefüge und eine geringe Kerbschlagzähigkeit;
Das Schweißstück muss normalisiert und Anlassen Wärmebehandlung nach dem Schweißen.
Anwendung des Elektroschlackeschweißens
Es ist für das vertikale Schweißen und Schweißen von 40~450mm dicken Blechen geeignet und wird im Allgemeinen für das Schweißen von geraden Nähten oder Rundnähten, das Verbinden von dicken Blechen, das vertikale Schweißen von Hochöfen in Stahlwerken, das Schweißen von großen Gussstücken, Schmiedestücken usw. verwendet.
Vereinfacht gesagt, ist das Schweißen unter Druck mit Widerstandswärme als Schweißwärme Quelle wird als Widerstandsschweißen bezeichnet.
Vorteil des Widerstandsschweißens
Niedrig Schweißspannung, hoher Strom und hohe Produktivität;
Geringe Kosten, keine Notwendigkeit für Schweißzusatzwerkstoffe und andere Schweißmaterialien,
Die Verformung beim Schweißen ist gering, und es ist keine Korrektur und Wärmebehandlung nach dem Schweißen erforderlich;
Gute Arbeitsbedingungen, einfache Bedienung, leicht zu realisieren automatische Produktion.
Nachteil des Widerstandsschweißens
Die Schweißausrüstung ist komplex und die Investitionen sind hoch;
Es gibt bestimmte Beschränkungen für die Dicke der Schweißnaht und die Form der Verbindung;
Gegenwärtig gibt es keine einfache und zuverlässige zerstörungsfreie Prüfung Methode.
Das Widerstandsschweißen kann unterteilt werden in PunktschweißenNahtschweißen und Stumpfschweißen.
Punktschweißen
Nahtschweißen
Widerstand Stumpfschweißen
Abbrennstumpfschweißen
1. Punktschweißen
Punkt Schweißdiagramm
Die Schweißnaht wird als Überlappungsverbindung montiert, und die zylindrische Elektrode wird unter Druck gesetzt und unter Strom gesetzt, um Widerstandswärme zu erzeugen, die das Schweißgut zum Schmelzen bringt und Nuggets (Schweißpunkte) bildet.
Punktschweißverfahren und Rangierphänomen
Punktschweißverfahren: Verdichtung → Einschalten (Nuggetbildung) → Ausschalten (Einfrieren) → Druckentnahme
Shunt-Phänomen: beim Schweißen des zweiten Punktes leitet der vorhandene Schweißpunkt Strom, was zu Leistungsverlusten führt. Der Strom an der Schweißstelle wird reduziert, was die Schweißqualität beeinträchtigt.
Verhindern Sie einen Shunt: zwischen zwei Schweißpunkten sollte ein bestimmter Abstand eingehalten werden.
Der Abstand zwischen zwei benachbarten Schweißköpfen darf nicht zu gering sein, und der Mindestpunktabstand ist in der folgenden Tabelle angegeben.
Werkstückdicke/mm | Punktabstand/mm | ||
---|---|---|---|
Konstruktionsstahl | Hitzebeständige Legierung | Aluminiumlegierung | |
0.5 | 10 | 8 | 15 |
1.0 | 12 | 10 | 15 |
1.5 | 14 | 12 | 20 |
2.0 | 16 | 14 | 25 |
3.0 | 20 | 18 | 30 |
4.0 | 24 | 22 | 35 |
Anwendung des Punktschweißens
Es wird hauptsächlich verwendet für Feinblech Stanzstruktur und Verstärkungselemente;
Es eignet sich für das Schweißen von sich überlappenden Strukturteilen aus dünnen Blechen mit Dichtungsanforderungen oder hohen Anforderungen an die Verbindungsfestigkeit, wie z. B. Öltanks, Wassertanks usw.
2. Nahtschweißen
Die Schweißnaht wird in überlappenden oder diagonalen Verbindungen zusammengesetzt und zwischen zwei Rollenelektroden platziert.
Die Rolle übt Druck auf die Schweißnaht aus und dreht sich, um die Schweißnaht vorwärts zu bewegen.
Das Schweißstück wird kontinuierlich oder intermittierend mit Strom versorgt, und das Schweißgut wird durch Widerstandshitze geschmolzen, um eine Reihe von Schweißpunkten zu bilden.
Klassifizierung des Nahtschweißens
Formular | Elektrischer Strom | Elektrode | Charakteristisch | Anmeldung |
Kontinuierliches Nahtschweißen | Kontinuierliche Leitung | kontinuierliche Drehung | Einfache Ausrüstung und hohe Produktivität, aber der Elektrodenverschleiß ist hoch. | Klein Leistungsschweißen unbedeutende Struktur (Zylinderherstellung, Fass, usw.) |
Stitch-and-Name-Schweißen | Intermittierende Kontinuität | kontinuierliche Drehung | Breite Anwendung (Eisenmetalle) | |
Schrittnahtschweißen | Intermittierende Kontinuität | Intermittierende Rotation | Komplexe Ausrüstung, hohe Anforderungen, geringer Elektrodenverschleiß und hohe Schweißqualität. | Es wird hauptsächlich zum Nahtschweißen von Magnesium und Aluminiumlegierungen. |
Charakteristisch für das Nahtschweißen
Die Lötstellen überlappen sich, und die Strömungsdiffusion ist gravierend.
Der Strom ist etwa 1,5~2,0 mal so hoch wie beim Punktschweißen;
Der Druck ist etwa 1,2~1,6 mal so hoch wie beim Punktschweißen;
Daher ist eine Hochleistungsschweißmaschine erforderlich.
Üben Sie Druck aus und verwenden Sie die Rolle als Elektrode.
Anwendung des Nahtschweißens
Nahtschweißen ist hauptsächlich für dünnwandige Konstruktionen mit regelmäßigen Schweißnähten und einer Dicke von weniger als 3 mm und mit Abdichtungsanforderungen verwendet;
Zum Beispiel Flugzeug- und Autotanks, verschiedene Behälter, Stahlkühler usw.
3. Stumpfschweißen
Eine Art von Widerstandsschweißverfahren, bei dem zwei Werkstücke mit Hilfe von Widerstandswärme entlang der gesamten Stirnfläche miteinander verschweißt werden, wird als Widerstandsstumpfschweißen oder kurz Stumpfschweißen bezeichnet.
Das Stumpfschweißen kann in Widerstandsstumpfschweißen und Abbrennstumpfschweißen unterteilt werden.
3.1 Widerstandsstumpfschweißen
Beim Widerstandsstumpfschweißen werden die Stirnseiten zweier Werkstücke durchgehend gepresst, mit Widerstandswärme bis zum plastischen Zustand erwärmt und dann mit schnellem Stauchdruck (oder nur unter Aufrechterhaltung des Drucks während des Schweißens ohne Stauchdruck) fertig geschweißt.
Charakteristisch für das Widerstandsstumpfschweißen
Einfache Bedienung und symmetrische Gelenkform;
Die Anforderungen für Schweißfläche Reinigung vor dem Schweißen sind hoch;
Die Anforderungen an die Stirnseitenbearbeitung sind hoch, da die Schweißqualität sonst schwer zu gewährleisten ist.
Anwendung des Widerstandsstumpfschweißens
Es eignet sich zum Schweißen von kohlenstoffarmen Stabstahl und Rohre mit kompaktem Schweißquerschnitt, geringen Festigkeitsanforderungen, einem Durchmesser (oder einer Seitenlänge) von weniger als 20 mm oder Stangen und Rohre aus Nichteisenmetallen von weniger als 8 mm (Schweißen von stabförmigen Teilen mit ähnlicher Form und Größe der Endfläche).
3.2 Abbrennstumpfschweißen
Die Schweißnaht wird als Stumpfstoß montiert, der Strom wird angeschlossen und der Abschnitt wird schrittweise an den lokalen Kontakt herangeführt.
Das Metall in der Sektion wird geschmolzen und fliegt unter Widerstandserhitzung heraus, wobei sich ein Blitz bildet.
Wenn das Ende die vorgegebene Temperatur innerhalb eines bestimmten Tiefenbereichs erreicht, wird die Stauchkraft schnell aufgebracht, um das Schweißen abzuschließen.
Prozess: Druckbeaufschlagung - Energiezufuhr - Gratbildung - Stauchschmieden
Charakteristisch für das Abbrennstumpfschweißen
Weniger Schlackeneinschlüsse in der Verbindung, gute Schweißqualität und hohe Verbindungsfestigkeit;
Die Anforderungen an die Reinigung der Stirnfläche des Schweißteils vor dem Schweißen sind nicht streng;
Beim Abbrennstumpfschweißen gibt es große Metallverluste, und die Verbindungsgrate nach dem Schweißen müssen bearbeitet und gereinigt werden. Die Arbeitsbedingungen sind schlecht.
Anwendung des Abbrennstumpfschweißens
Im Prinzip lassen sich alle gießbaren metallischen Werkstoffe durch Abbrennstumpfschweißen verbinden.
Zum Beispiel Stahl mit niedrigem Kohlenstoffgehalt, kohlenstoffreicher Stahllegierter Stahl, rostfreier Stahl;
Aluminium, Kupfer, Titan und andere Nichteisen-Metalle und -Legierungen;
Es kann auch Verbindungen aus ungleichen Legierungen schweißen.
(Hartlöten mit Lötkolben)
(Flammlöten)
(Induktionslöten)
Das Metall mit einem niedrigeren Schmelzpunkt als das Schweißgut als Zusatzwerkstoff verwenden, das Schweißgut (Grundwerkstoff) und den Zusatzwerkstoff auf eine Temperatur erhitzen, die höher als der Schmelzpunkt des Zusatzwerkstoffs und niedriger als die Schmelztemperatur des Grundwerkstoffs ist, den Grundwerkstoff schmelzen und benetzen, den Fügespalt füllen und mit dem Grundwerkstoff diffundieren, um eine geschweißte VerbindungDies wird als Hartlöten bezeichnet.
Lötverfahren
Schmelzen des Lotes - Fließen des flüssigen Lotes in den Fügespalt - gegenseitige Diffusion zwischen Lot und Grundwerkstoff - Füllen des Spaltes - Ausbilden der Verbindung nach dem Erstarren
Merkmale des Hartlötens
1) Der Schmelzpunkt des Schweißzusatzes ist niedriger als der des Grundmetalls, und das Grundmetall schmilzt beim Löten nicht;
2) Die Zusammensetzung von Zusatzwerkstoff und Grundwerkstoff ist sehr unterschiedlich;
3) Der geschmolzene Zusatzwerkstoff wird durch Benetzung und Kapillarität angesaugt und im Grundmetallspalt gehalten;
4) Die metallurgische Verbindung entsteht durch gegenseitige Diffusion zwischen flüssigem Lot und festem Grundmetall.
Vorteil des Hartlötens
Die Struktur und die Eigenschaften des unedlen Metalls ändern sich nicht (das unedle Metall schmilzt nicht, nur das Zusatzmetall schmilzt);
Einfache Ausrüstung, geringere Produktionsinvestitionen;
Die Erwärmungstemperatur ist niedrig, die Verformung ist gering und die Verbindung ist glatt;
Hohe Produktivität, kann mehrere Schweißteile und Verbindungen gleichzeitig schweißen;
Sie kann verwendet werden, um ungleiche Metalle schweißen oder ungleiche Materialien, ohne Begrenzung des Dickenunterschieds des Werkstücks.
Nachteil des Hartlötens
Die Lötverbindung hat eine geringe Festigkeit und eine schlechte Wärmebeständigkeit.
Klassifizierung des Hartlötens
Typ/Merkmal | Weichlöten (Zinn-, Bleilot) | Hartlöten (Lote auf Kupfer- und Silberbasis) |
Schmelzpunkt des Lotes | ≤ 450℃ | > 450℃ |
Leistungsmerkmale | Verbindungsfestigkeit ≤ 100MPa, niedrige Arbeitstemperatur | Verbindungsfestigkeit > 200MPa, hohe Arbeitstemperatur |
Anmeldung | Es wird für das Schweißen von Instrumenten und leitenden Bauteilen mit geringer Belastung verwendet. | Es wird zum Schweißen von Bauteilen, Werkzeugen und Werkzeugen mit großer Kraft verwendet. |
Anwendung des Hartlötens
Es wird hauptsächlich für die Herstellung von Präzisionsinstrumenten, elektrischen Bauteilen, Bauteilen aus unterschiedlichen Metallen und für das Schweißen von komplexen Blechstrukturen wie Sandwichbauteilen, Wabenstrukturen usw. verwendet.
2.2.1 Reibschweißen
Beim Reibschweißen handelt es sich um ein Pressschweißverfahren, bei dem die durch die Reibung zwischen den Schweißflächen erzeugte Wärme genutzt wird, um die Stirnfläche in den thermoplastischen Zustand zu versetzen und sich dann schnell zu verformen, um die Schweißung abzuschließen.
Rührreibschweißen
Reibschweißen mit kontinuierlichem Antrieb
Trägheitsreibschweißen
Schweißverfahren des Reibschweißens:
1) Relativbewegung der Schweißnaht;
2) Der stirnseitige Kontakt zwischen den beiden Schweißteilen erzeugt Reibungswärme;
3) Wenn der Abschnitt den thermoplastischen Zustand erreicht hat, drücken Sie schnell auf den oberen Abschnitt, um die Schweißung abzuschließen.
Vorteil des Reibschweißens:
Hohe Schweißproduktivität, 5-6 mal höher als beim Abbrennstumpfschweißen;
Stabile Schweißqualität und hohe Maßhaltigkeit der Schweißteile;
Geringe Bearbeitungskosten, energiesparend, keine besondere Reinigung der Schweißteile erforderlich;
Einfache Mechanisierung und Automatisierung, einfache Bedienung;
Kein Funken, Lichtbogen und schädliches Gas.
Nachteil des Reibschweißens:
Große Investition;
Es ist schwierig, nicht runde Profile zu schweißen, und der Schweißbereich ist begrenzt.
Anwendung des Reibschweißens:
Es kann zum Schweißen von gleichen oder verschiedenen Metallen und verschiedenen Stahlprodukten verwendet werden, wie z. B. Kupfer-Aluminium-Übergangsverbindungen in der Elektroindustrie, Hochgeschwindigkeitsstahl-Strukturstahlwerkzeuge für ZerspanungSerpentinen, Ventile, Traktorlager, usw.
2.2.2 Laserschweißen
Die zu bearbeitende Oberfläche wird erhitzt durch LaserstrahlungDie Oberflächenwärme wird durch Wärmeübertragung in die innere Diffusion geleitet, um das Werkstück zu schmelzen und ein spezifisches Schmelzbad zu bilden. Die Schweißnaht entsteht, nachdem das Schmelzbad erstarrt ist.
Der Vorteil des Laserschweißens:
Hohe Schweißgeschwindigkeit und Effizienz;
Hohe Schweißpräzision, geringe Verformung und einfache automatische Steuerung;
Es wird keine Elektrode benötigt, so dass keine Elektrodenverschmutzung auftritt.
Nachteil des Laserschweißens:
Große Investitionen, geringe Leistung und begrenzte schweißbare Dicke;
Es ist schwierig, den Schweißpunkt mit dem Erfassungsbereich des Laserstrahls auszurichten;
Schnelle Verfestigung des Schweißraupe kann zu Porosität führen.
Anwendung des Laserschweißens:
Es wird hauptsächlich zum Schweißen von Teilen in der Präzisionsfertigung verwendet, z. B. in der Luft- und Raumfahrt, im Schiffbau, in der Automobilindustrie und in der Elektronikindustrie.
2.2.3 Plasmabogen Schweißen
Was ist ein Plasmalichtbogen?
Wie ist Plasmaschweißen durchgeführt?
Vereinfacht ausgedrückt: Der Lichtbogen, bei dem die Lichtbogensäule komprimiert und die Energie hochkonzentriert ist und das Gas in der Lichtbogensäule vollständig ionisiert ist, wird als Plasmalichtbogen bezeichnet, auch Kompressionslichtbogen genannt.
Das Gas wird durch den Lichtbogen erhitzt und zunächst ionisiert. Wenn es mit hoher Geschwindigkeit durch die wassergekühlte Düse strömt, wird es komprimiert, wodurch sich die Energiedichte und der Ionisierungsgrad erhöhen und ein Plasmalichtbogen entsteht.
Durch die hohe Hitze und Durchschlagskraft des Plasmalichtbogens wird das Werkstück an der Schweißstelle zu einem Schmelzbad aufgeschmolzen, um das Schweißen des Werkstücks zu realisieren.
Vorteil des Plasmaschweißens:
Hohe Energiedichte, starke Lichtbogenleitfähigkeit und starkes Eindringvermögen;
Das Tiefen-Breiten-Verhältnis der Schweißnaht ist groß, und die Wärmeeinflusszone ist klein;
Stabile Lichtbogenverbrennung (stabil auch bei geringem Strom);
Die Schweißkosten sind niedrig, und wenn die Schweißdicke ist klein, es gibt keine Rille und es ist nicht nötig, den Draht zu füllen;
Es hat einen stabilen Schlüsselloch-Effekt und kann die freie Formung von einseitigen und doppelseitigen Schweißungen besser realisieren.
Nachteil des Plasmaschweißens:
Die Ausrüstung ist teuer;
Schlechte Beobachtbarkeit des Aktionsbereichs des Lichtbogens;
Die schweißbare Dicke ist begrenzt (im Allgemeinen weniger als 25 mm).
Anwendung des Plasmaschweißens:
Es ist in der industriellen Produktion weit verbreitet, insbesondere in der Schweißen von Kupfer und Kupferlegierungen, Titan und Titanlegierungen, legierter Stahl, rostfreier Stahl, Molybdän und andere Metalle, die in der Militärtechnik und in industriellen Spitzentechnologien wie der Luft- und Raumfahrt verwendet werden, z. B. Raketenhüllen aus Titanlegierungen und einige dünnwandige Behälter in Flugzeugen.
Die Methode des Schweißens unter Verwendung der Wärmeenergie, die durch den beschleunigten und fokussierten Elektronenstrahl erzeugt wird, der das im Vakuum oder Nicht-Vakuum befindliche Schweißstück beschießt, wird Elektronenstrahlschweißen genannt.
Mit anderen Worten: Die zum Schweißen erforderliche Wärme wird durch den Elektronenstrahlbeschuss der Schweißnaht erzeugt.
Schweissverfahren:
1) Die Kathode der Elektronenkanone emittiert Elektronen durch direkte oder indirekte Erwärmung;
2) Unter der Beschleunigung des elektrostatischen Hochspannungsfeldes kann der Elektronenstrahl mit hoher Energiedichte durch Fokussierung des elektromagnetischen Feldes gebildet werden;
3) Der Elektronenstrahl mit hoher Energiedichte beschießt das Werkstück, und die enorme kinetische Energie wird in Wärmeenergie umgewandelt, um das Schweißteil zu schmelzen, ein Schmelzbad zu bilden und dann das Schweißen abzuschließen.
Der Vorteil des Elektronenstrahlschweißens:
Schnelle Schweißgeschwindigkeit und hohe Effizienz;
Keine Rille, kein Schweißdraht, kein Flussmittel, etc;
Geringer Energieverbrauch, schmale Wärmeeinflusszone, geringe Schweißverformung und ausgezeichnete Qualität;
Die Durchdringungsfähigkeit des Elektronenstrahls ist stark, und das Tiefen-Breiten-Verhältnis der Schweißnaht ist groß und kann 50:1 erreichen.
Nachteil des Elektronenstrahlschweißens:
Die Ausrüstung ist komplex und teuer;
Die Größe und Form der Schweißteile wird häufig durch die Vakuumkammer begrenzt;
Der Elektronenstrahl wird leicht durch elektromagnetische Streufelder gestört, was die Schweißqualität beeinträchtigt.
Vakuum-Elektronenstrahlschweißen
Anwendung des Elektronenstrahlschweißens:
Geeignet für das Feinschweißen von Refraktärmetall, Aktivmetall und hochreinem Metall.
Es findet breite Anwendung beim Schweißen in der Kernenergie, der Luft- und Raumfahrt, der Automobilindustrie, bei Druckbehältern, im Werkzeugbau und in anderen Industriebereichen.
Das Ultraschallschweißen ist ein Verfahren, bei dem die Hochfrequenzschwingung von Ultraschallwellen genutzt wird, um die Werkstückverbindung lokal zu erwärmen und zu säubern, und dann wird Druck ausgeübt, um das Schweißen zu realisieren.
Schweissverfahren
1) Niederfrequenter Wechselstrom zu hochfrequentem Wechselstrom;
2) Elektrische Energie wird umgewandelt in mechanische Vibration Energie;
3) Amplitude erhöhen;
4) Druck ausüben, und der Schweißkopf berührt das zu schweißende Werkstück.
Vorteil des Ultraschallschweißens:
Einfache Bedienung, schnelle Schweißgeschwindigkeit und hohe Produktionseffizienz;
Die Anforderungen an die Sauberkeit der Werkstückoberfläche sind nicht hoch;
Die Zugabe von Bindemitteln, Füllstoffen oder Lösungsmitteln ist nicht erforderlich.
Nachteil des Ultraschallschweißens:
Sie ist nur für das Schweißen von dünnen Teilen wie Draht, Folie, Blech, Streifen und Bändern geeignet;
In den meisten Fällen kann die Fugenform nur eine Überlappungsfuge sein.
Anwendung des Ultraschallschweißens:
Es eignet sich für das Schweißen von Materialien mit hoher Leitfähigkeit und hoher Wärmeleitfähigkeit sowie einer Vielzahl von Verbundwerkstoffen und findet breite Anwendung beim Schweißen von mikroelektronischen Geräten und in der Endbearbeitung.
Das Hochfrequenzschweißen ist ein Verfahren, bei dem die durch Hochfrequenzstrom im Werkstück erzeugte Widerstandswärme genutzt wird, um die Oberflächenschicht des Schweißbereichs des Werkstücks bis zu einem geschmolzenen oder nahezu plastischen Zustand zu erwärmen, und dann eine Stauchkraft angewendet wird (oder auch nicht), um eine Metallverbindung zu erreichen.
Wirkung auf die Haut: Wenn der Leiter mit Wechselstrom verbunden ist, fließt der größte Teil des Stroms nur entlang der Oberfläche des Leiters.
Näherungseffekt: Wenn Hochfrequenzstrom in entgegengesetzter Richtung zwischen zwei Leitern oder in einem sich hin- und herbewegenden Leiter fließt, konzentriert sich der Strom auf den Fluss in der Nähe des Leiters.
Vereinfacht ausgedrückt ist der Skin-Effekt "der Strom geht an die Oberfläche"; der Proximity-Effekt ist "Stromabkürzung".
Vorteil des Hochfrequenzschweißens:
Hohe Schweißgeschwindigkeit und Effizienz (der Strom ist im Schweißbereich hoch konzentriert);
Eine breite Palette schweißbarer Materialien kann auch zum Schweißen ungleicher Metalle verwendet werden;
Die Reinigung vor dem Schweißen ist einfach (beim Schmelzschweißen mit Druckwirkung ist eine Reinigung der Verbindungsfläche nicht erforderlich).
Nachteil des Hochfrequenzschweißens:
Die Montagegenauigkeit der Verbindungen muss hoch sein;
Hochspannung und Hochfrequenzstrom sind schädlich für den menschlichen Körper und andere Geräte.
Anwendung des Hochfrequenzschweißens:
Es ist geeignet für Schweißen von KohlenstoffstahlLegierter Stahl, rostfreier Stahl, Kupfer, Aluminium, Titan und andere ungleiche Metalle.
Es wird häufig zum Schweißen von Längs- oder Spiralnähten bei der Herstellung von Rohren verwendet.
Diffusionsschweißen bezieht sich auf das Schweißverfahren, bei dem die Schweißnaht eng anliegt, über einen bestimmten Zeitraum unter einer bestimmten Temperatur und einem bestimmten Druck gehalten wird und die gegenseitige Diffusion von Atomen zwischen den Kontaktflächen genutzt wird, um eine Verbindung herzustellen.
Schweissverfahren
a) Grober Erstkontakt
b) Phase I: Verformung und Grenzflächenbildung
c) Phase II: Korngrenzenwanderung und Mikroporenbeseitigung
d) Phase III: Volumendiffusion, Mikroporenelimination
Physikalische Schweißanzeige
Vorteil des Diffusionsschweißens:
Es können mehrere Verbindungen auf einmal geschweißt werden;
Die Verbindungsqualität ist gut, und nach dem Schweißen ist keine Nachbearbeitung erforderlich;
Geringe Verformung des Schweißteils (niedriger Druck, Gesamterwärmung des Werkstücks, Abkühlung im Ofen).
Nachteil des Diffusionsschweißens:
Große Investitionen und hohe Kosten;
Lange Schweißzeit, zeitaufwändige und arbeitsintensive Oberflächenvorbereitung und geringe Produktivität;
Es gibt keine zuverlässige zerstörungsfreie Prüfmethode für die Schweißnahtqualität.
Anwendung des Diffusionsschweißens:
Es eignet sich für das Schweißen verschiedener unterschiedlicher Materialien, spezieller Werkstoffe und besonderer Strukturen und findet breite Anwendung in der Luft- und Raumfahrt, der Elektronik, der Kernkraft und anderen Industriebereichen.
Das Explosionsschweißen ist eine Methode zum Schweißen, bei der die durch eine Explosion erzeugte Aufprallkraft genutzt wird, um eine schnelle Kollision der Werkstücke zu verursachen.
Das Explosionsschweißen ist ebenfalls eine Form des Pressschweißens.
Für das Schweißen von kleinen Werkstücken können sowohl das Parallel- als auch das Winkelverfahren eingesetzt werden;
Das Parallelverfahren wird häufig für großflächige Schweißungen verwendet.
Der Spalt zwischen den vorderen Abschnitten der beiden Bleche ist zu groß, was zu einer übermäßigen Beschleunigung des plattierten Blechs und zu einer übermäßigen Aufprallenergie führt, was wiederum eine Beschädigung und einen Riss am Rand des Blechs zur Folge hat, wodurch die wirksame Fläche des plattierten Blechs verringert und das Blech verbraucht wird.
Vorteil des Explosionsschweißens:
Geringe Investition und niedrige Kosten;
Besonders geeignet für ungleiche Metalle und großflächiges Schweißen;
Das Verfahren ist einfach, es ist keine aufwendige Reinigung erforderlich, und die Anwendung ist bequem.
Nachteil des explosiven Schweißens:
Es kann nur für das Schweißen von ebenen oder zylindrischen Strukturen verwendet werden;
Der Freilandbetrieb ist wenig mechanisiert und beeinträchtigt die Umwelt.
Anwendung des Explosionsschweißens:
Geeignet zum Schweißen unterschiedlicher Metalle, wie Aluminium, Kupfer, Titan, Nickel, Tantal, Edelstahl und Kohlenstoffstahl, Aluminium und Kupferschweißen.
Es findet breite Anwendung beim Schweißen von leitfähigen Busübergängen, Wärmetauscherrohren und Rohrböden sowie bei der Herstellung von großflächigen Verbundplatten.
Was ist Schweißmaterial?
Die allgemeine Bezeichnung für die beim Schweißen verbrauchten Materialien lautet Schweißmaterialienwie Schweißdraht, Schweißdraht, Metallpulver, Flussmittel, Gas usw.
Gängige Schweißmaterialien
Die beim Lichtbogenschweißen verwendete Elektrode, die mit einem Schutzüberzug versehen ist, wird als "Elektrode" bezeichnet.
Die Elektrode besteht aus einem Schweißkern und einer Umhüllung.
Der Kern der Elektrode, der von der Umhüllung bedeckt ist, wird als Schweißkern bezeichnet.
Der Schweißkern hat eine doppelte Funktion: als stromleitende Elektrode und als Schweißzusatzwerkstoff, der sich mit dem geschmolzenen Grundwerkstoff verbindet, um die Schweißnaht zu erzeugen.
Die Beschichtung ist eine Schicht, die auf die Oberfläche des Schweißkerns aufgetragen wird, nachdem die Rohstoffe, wie Erzpulver, Eisenlegierungspulver, organische Stoffe und chemische Produkte, in einem bestimmten Verhältnis aufbereitet wurden.
Funktion der Beschichtung:
1) Mechanischer Schutz (kombinierter Gas- und Schlackenschutz)
Gas und Schlacke werden verwendet, um die Luft abzuschirmen und den Kontakt zwischen den Schmelztropfen, dem geschmolzenen Badmetall und der Luft zu verhindern.
Die erstarrte Schlacke bildet eine Schutzschicht über der Schweißnahtoberfläche, die dazu beiträgt, die Oxidation und nitrieren des Hochtemperatur-Schweißgutes.
2) Metallurgische Behandlung (Desoxidation, Entphosphorung, Entschwefelung, Legierung)
Bei diesem Verfahren werden schädliche Elemente entfernt und Legierungselemente hinzugefügt.
3) Verbesserung der Schweißprozessleistung (Lichtbogenstabilisierung)
Der Lichtbogen zündet leicht und brennt gleichmäßig, wodurch weniger Spritzer entstehen, die Schweißnaht besser aussieht und die Schlacke leicht zu entfernen ist. Dieses Verfahren ist für alle Schweißpositionen geeignet.
Zusammensetzung der Beschichtung:
Name | Wirkung | Gemeinsame Rohstoffe |
Lichtbogenstabilisator | Enthält Materialien, die leicht zu ionisieren sind und die Stabilität des Lichtbogens verbessern | Kaliumkarbonat, Marmor, Natriumsilikat, Feldspat, Rutil, usw. |
Prüfpräparat | Bildung von Schlacke zum Schutz von Schmelzer und Bad | Ilmenit, Rutil, Marmor, Quarzit, Glimmer, usw. |
Vergaser | Erzeugen Sie Gas und isolieren Sie die Luft, um den Schweißbereich zu schützen. | Organische Stoffe (wie Stärke, Dextrin, Sägemehl usw.) und Karbonat (Marmor, Dolomit usw.) |
Bindemittel | Jede Komponente der Beschichtung muss sich mit dem Kern verbinden und verkleben. | Natriumsilikat, Kaliumnatriumsilikat |
Desoxidationsmittel | Verringern die Oxidierbarkeit von Beschichtungen und Schlacken und entfernen Sauerstoff aus dem Metall | Ferromangan, Ferrosilizium, Ferrotitan und Aluminium |
Legierungsmittel | Die Elemente, die den Verlust kompensieren, können die notwendigen Bestandteile erhalten, damit die Haut des Medikaments eine gewisse Plastizität, Elastizität und Fließfähigkeit hat | Ferrolegierungs- oder Metallpulver, wie Ferromangan, Ferrosilizium, Ferromolybdän, Ferrotitan, usw. |
Formant | Die Beschichtung weist eine gewisse Plastizität, Elastizität und Fließfähigkeit auf, was das Pressen der Elektroden erleichtert und die Oberfläche glatt und rissfrei macht. | Weißer Schlamm, Glimmer, Titan Dioxid, Dextrin, usw. |
Was sind die Arten von Schweißdrähten?
1) Klassifizierung nach Alkalität der Schlacke
a. Saure Elektrode
Charakteristisch:
(1) In der Drogenhaut sind mehrere Oxid-Säuren enthalten, darunter FeO, SiO2und TiO2und andere.
(2) Die Verarbeitbarkeit ist gut, und die Schweißnahtbildung ist attraktiv mit feinen Riffeln.
(3) Die Schlacke weist eine starke Oxidation auf.
(4) Es funktioniert sowohl mit AC- als auch mit DC-Strom.
b. Basische Elektrode (wasserstoffarme Elektrode)
Charakteristisch:
(1) Die Haut der Droge enthält einen höheren Anteil an alkalischen Oxiden, wie Marmor (CaCO3) und Fluorit (CaF2).
(2) Beim Schweißen wird CO2 und HF entstehen, wodurch der Wasserstoffgehalt in der Schweißnaht sinkt, was ihr den Beinamen "wasserstoffarme Elektrode" einbrachte.
(3) Die Schweißnaht zeichnet sich durch eine hohe Plastizität und Zähigkeit aus, obwohl ihre Verarbeitbarkeit und Form nicht so gut sind wie die der sauren Elektrode. Üblicherweise wird eine Gleichstrom-Umkehrverbindung verwendet.
2) Klassifizierung nach der Verwendung von Schweißdrähten
Baustahlelektroden, hitzebeständige Stahlelektroden, Edelstahlelektroden, Oberflächenelektroden, Niedrigtemperatur-Stahlelektroden, Gusseisenelektroden, Elektroden aus Nickel und Nickellegierungen, Elektroden aus Kupfer und Kupferlegierungen, Elektroden aus Aluminium und Aluminiumlegierungen sowie Elektroden für besondere Zwecke.
3) Klassifizierung nach der chemischen Zusammensetzung der Drogenhaut
Titanoxid-Elektrode, Kalziumtitanat-Elektrode, Ilmenit-Elektrode, Eisenoxid-Elektrode, Zellulose-Elektrode, Elektrode mit niedrigem Wasserstoffgehalt, Graphit-Elektrode und Basiselektrode.
Die Art der Schweißdraht wird auf der Grundlage der nationalen Norm für Schweißdrähte bestimmt und ist ein Mittel, um die primären Eigenschaften des Reaktionsschweißdrahtes auszudrücken.
Das Modell des Schweißdrahtes umfasst die folgenden Bedeutungen: Art des Schweißdrahtes, Eigenschaften des Schweißdrahtes (Art des Kernmetalls, Betriebstemperatur, chemische Zusammensetzung des aufgetragenen Metalls, Zugfestigkeit usw.), Art der Beschichtung und Schweißleistung Quelle.
Der Begriff Schweißdrahtsorte bezieht sich auf die spezifische Klassifizierung von Schweißdrahtprodukten auf der Grundlage ihres Verwendungszwecks und ihrer Leistungsmerkmale.
Die Güteklassen von Schweißelektroden werden in zehn Gruppen eingeteilt, darunter Baustahlelektroden, hitzebeständige Stahlelektroden, Edelstahlelektroden und andere.
Wie lässt sich feststellen, ob der verwendete Schweißdraht angemessen ist?
Um die Angemessenheit der Auswahl des Schweißdrahtes zu bestimmen, sollte dieser anhand seiner technischen Leistungsindikatoren bewertet werden.
1) Stabilität des Lichtbogens
Der Lichtbogen lässt sich leicht zünden, und der Grad der stabilen Verbrennung (keine Lichtbogenunterbrechung, Drift, magnetische Vorspannung usw.) wird beibehalten.
2) Schweißnahtbildung
Gute Formgebung bedeutet, dass die Oberfläche glatt ist, die Riffelung fein und schön ist und die geometrische Form und Größe der Schweißnaht korrekt sind.
3) Anpassungsfähigkeit beim Schweißen in verschiedenen Positionen
Anpassungsfähigkeit an alle Schweißpositionen - alle Elektroden können für das Flachschweißen verwendet werden, aber einige Elektroden sind nicht für das horizontale und vertikale Schweißen geeignet. ÜberkopfschweißenDaher ist ihre Schweißleistung in allen Positionen schlecht.
4) Spritzer
Die Metallpartikel, die beim Schweißen aus dem Tropfen oder Schmelzbad herausfliegen, werden als Spritzer bezeichnet.
Spritzerrate = Masse der Spritzer/(Schweißdrahtqualität vor dem Schweißen - Schweißdrahtqualität nach dem Schweißen)*100%
5) Entschlackungseigenschaft
Er bezieht sich auf die Schwierigkeit, Schlackenschalen nach dem Schweißen von der Schweißoberfläche zu entfernen.
6) Schmelzgeschwindigkeit des Schweißdrahtes
Sie bezieht sich auf die Qualität und Länge des geschmolzenen Kerns in einer Zeiteinheit, wenn die Elektrode angelegt wird; relativ gesehen ist die Schmelzgeschwindigkeit umso besser, je höher sie ist.
7) Rötung der Elektrodenumhüllung
Es handelt sich dabei um das Phänomen, dass bei der Verwendung der Elektrode in der zweiten Hälfte die Umhüllung aufgrund der hohen Temperatur der Umhüllung rot wird, Risse bekommt oder abfällt.
8) Schweißrauch
a. Das Prinzip der gleichen Festigkeit besagt, dass die Zugfestigkeit des von der gewählten Elektrode abgeschiedenen Metalls gleich oder ähnlich der des zu schweißenden Grundmetalls sein sollte.
b. Das Prinzip der gleichen Zähigkeit besagt, dass die Zähigkeit des von der gewählten Elektrode abgeschiedenen Metalls gleich oder ähnlich der des zu schweißenden Grundmetalls sein sollte.
c. Das Prinzip der gleichen Zusammensetzung besagt, dass die chemische Zusammensetzung des von der gewählten Elektrode abgeschiedenen Metalls mit der des Grundmetalls übereinstimmen oder ihr ähnlich sein sollte.
1. Trocknung des Schweißdrahtes
Der Schweißdraht neigt dazu, Feuchtigkeit aus der Atmosphäre zu absorbieren, was sich negativ auf seine Leistung und die Qualität der Schweißnaht auswirken kann.
Daher ist es wichtig, den Schweißdraht (insbesondere alkalische Schweißdrähte) vor der Verwendung zu trocknen.
Normalerweise liegt die Trocknungstemperatur für eine saure Elektrode zwischen 75 und 150 °C, und sie sollte 1 bis 2 Stunden lang bei dieser Temperatur gehalten werden.
Bei einer alkalischen Elektrode sollte die Trocknungstemperatur zwischen 350-400°C liegen, und sie sollte 1-2 Stunden lang bei dieser Temperatur gehalten werden.
Es ist wichtig zu beachten, dass die kumulative Trocknungszeit der Schweißdrähte 3 Jahre nicht überschreiten sollte.
2. Lagerung von Schweißdrähten
1) Schweißdrähte sollten nach Typ, Modell und Spezifikationen geordnet und gelagert werden, um Verwechslungen zu vermeiden.
2) Der Lagerraum sollte gut belüftet und trocken gehalten werden.
3) Elektroden mit niedrigem Wasserstoffgehalt, die für kritische Schweißkonstruktionen unerlässlich sind, sollten in einem speziellen Lager mit einer Temperatur von über 5°C und einer relativen Luftfeuchtigkeit von höchstens 60% gelagert werden.
4) Zum Schutz vor Feuchtigkeitsschäden sollten die Schweißdrähte auf einem Holzgestell mit einem Mindestabstand von 0,3 Metern zum Boden und zu den Wänden gelagert werden.
Im Bereich des Schweißens hat sich die Technologie ständig weiterentwickelt, was zu einer zunehmenden Mechanisierung und Automatisierung geführt hat. Dies hat zu einer höheren Produktionseffizienz, verbesserten Schweißqualitätund bessere Arbeitsbedingungen.
Um die Mechanisierung und Automatisierung des Schweißens weiter voranzutreiben, werden Schweißdrähte als Schweißmaterial eingesetzt.
Wie werden die Schweißdrähte bei den Schweißmaterialien bezeichnet?
Der Draht, der beim Schweißen als Zusatzwerkstoff oder für die Stromleitung verwendet wird, heißt Schweißdraht.
a. Klassifizierung nach Herstellungsverfahren und Schweißdrahtform
Er kann in Massivdraht und Fülldraht unterteilt werden.
b. Klassifizierung nach dem anwendbaren Schweißverfahren
Es kann in Unterpulverschweißdraht unterteilt werden, Schutzgasschweißen Draht, Elektroschlackeschweißdraht, Auftragschweißdraht und Gasschweißdraht.
c. Klassifizierung nach den Eigenschaften der zu schweißenden metallischen Werkstoffe
Er kann in Schweißdraht aus Kohlenstoffstahl, Schweißdraht aus niedrig legiertem Stahl, Schweißdraht aus rostfreiem Stahl, Schweißdraht aus Nickelbasislegierungen, Schweißdraht aus Gusseisen und Schweißdraht aus Speziallegierungen unterteilt werden.
d. Durch Verkupferung klassifiziert oder nicht
Verkupferter Draht und nicht verkupferter Draht.
Der Draht wird direkt auf den Zieldrahtdurchmesser gezogen. Der Schweißdraht ohne Pulver wird als massiver Schweißdraht bezeichnet.
1.1 Produktionsprozess von massivem Schweißdraht
1.2 Modell eines massiven Schweißdrahtes
1.3 Marke von massivem Schweißdraht
2. Welche Art von Schweißdraht wird mit Fülldraht geschweißt?
Das dünne Stahlband wird in verschiedene Querschnittsformen gewalzt, mit Pulver gefüllt und dann zu einer Art Schweißdraht, dem so genannten Fülldraht, gezogen.
Das gefüllte Pulver wird als Kern bezeichnet und hat eine ähnliche Wirkung wie die Elektrodenbeschichtung.
2.1 Modell eines Fülldrahtes
2.2 Marke des Fülldrahtes
Je nach Drahtstruktur können Fülldrähte unterteilt werden in: nahtlos und nahtlos.
Nahtlose Fülldrähte können verkupfert werden und zeichnen sich durch gute Leistung und niedrige Kosten aus, was in Zukunft die Entwicklungsrichtung sein wird.
2.3 Herstellungsverfahren für Fülldraht
Für die Herstellung von Naht-Fülldraht wird in der Regel das "Stahlbandverfahren" verwendet;
Für die Herstellung von nahtlosen Fülldrähten wird üblicherweise das "Stahlrohrverfahren" verwendet.
a. Bandstahlverfahren
b. Stahlrohr-Methode
Vorteile:
Geringe Spritzer, hohe Abscheidegeschwindigkeit und hohe Produktionseffizienz.
Schweißen von verschiedenen Stählen mit hoher Anpassungsfähigkeit.
Gute Prozessleistung und ein schönes Schweißbild.
Ein großer Schweißstrom kann zum Schweißen in allen Positionen verwendet werden.
Benachteiligungen:
Die Herstellung Schweißverfahren Draht ist kompliziert und teuer.
Die Oberfläche des Schweißdrahtes ist rostanfällig und das Pulver ist anfällig für die Aufnahme von Feuchtigkeit.
Die Drahtzuführung während des Schweißvorgangs ist im Vergleich zur Verwendung von Massivdraht schwieriger, was zu einer starken Rauchentwicklung führt.
Dieses Bild zeigt den Prozess des Unterpulverschweißens.
Bemerken Sie den "Sand" an der Spitze?
Es ist ein wesentliches Schweißmaterial, das sogenannte Flussmittel, für das Unterpulverschweißen.
Flussmittel ist ein körniges Material, das beim Schweißen zu Schlacke und Gas schmilzt und eine schützende und metallurgische Rolle im geschmolzenen Metall spielt.
Effekt:
1) Schützen Sie das geschmolzene Pool-Metall;
2) Hinzufügen Legierungselemente in den geschmolzenen Pool.
(1) Klassifizierung nach Verwendung
Sie kann in drei Typen unterteilt werden: Untergetauchter Lichtbogen Flussmittel zum Schweißen, Elektroschlacke-Schweißpulver und Auftragsschweißpulver.
(2) Klassifizierung nach Herstellungsverfahren
Es kann in zwei Kategorien unterteilt werden: Schmelzflussmittel und Nicht-Schmelzflussmittel.
(3) Klassifizierung nach Schlackenalkalität
Es kann in drei Kategorien eingeteilt werden: Saures Flussmittel, neutrales Flussmittel und basisches Flussmittel.
a. Schmelzflussmittel
Das Flussmittel wird durch Schmelzen verschiedener Zutaten in einem genauen Verhältnis in einem Ofen hergestellt. Die Mischung wird dann granuliert, getrocknet und gesiebt, während sie mit Wasser gekühlt wird.
Charakteristisch:
1) Es ist nicht schwer, Feuchtigkeit zu absorbieren, und muss in der Regel vor der Verwendung nicht getrocknet werden.
2) Das nicht geschmolzene Flussmittel kann wiederverwendet werden.
3) Nach dem Schmelzen wird es schnell abgekühlt und nimmt oft die Form von Glas an.
4) Dem Flussmittel im Schmelzbad kann nur eine begrenzte Menge an Legierungselementen zugesetzt werden, da eine große Menge nicht übertragen werden kann.
Schmelzflussmittel
Hauptbestandteile:
b. Ungeschmolzenes Flussmittel
Das nicht schmelzende Flussmittel wird durch Mischen verschiedener Pulver nach einer bestimmten Formel, Hinzufügen eines Bindemittels zur Bildung von Partikeln einer bestimmten Größe und anschließendes Brennen oder Sintern gewonnen.
Klebeflussmittel ist eine Art Flussmittel, das bei niedrigen Temperaturen (unter 400 ℃) eingebrannt wird.
Gesintertes Flussmittel hingegen wird durch Sintern des Flussmittels bei hohen Temperaturen (700 bis 1000 ℃) hergestellt.
Charakteristisch:
1) Die Feuchtigkeitsaufnahme ist relativ hoch, und es muss vor der Verwendung erneut getrocknet werden.
2) Leicht herstellbar und gut einsetzbar.
Gesintertes Flussmittel
Wesentlicher Bestandteil(SJ101):SJ102
Klassifizierung nach der Alkalität der Schlacke:
(1) Säurefluss (Alkalinität B<1,0)
Die Schlacke besteht in erster Linie aus sauren Oxiden und hat eine hervorragende Schweißleistung, was zu einem optisch ansprechenden Schweißbild führt. Das Schweißgut weist jedoch einen hohen Sauerstoffgehalt auf, was zu einer geringen Kerbschlagzähigkeit führt.
(2) Neutraler Fluss (Alkalität 1,0 ~ 1,5)
Die Zusammensetzung des abgeschiedenen Metalls ähnelt der des Schweißdrahtes, mit einem geringeren Sauerstoffgehalt im Schweißgut.
(3) Alkalifluss (Alkalinität B>1,5)
Die Hauptbestandteile der Schlacke sind alkalische Oxide und Kalziumfluorid. Das Schweißgut zeichnet sich durch einen niedrigen Sauerstoffgehalt, hohe Schlagzähigkeit und gute Zugeigenschaften aus.
Bei modernen, hochmodernen wissenschaftlichen und technologischen Projekten, wie z. B. Kühlerlamellen für Flugzeuge, Raketenschalen, Triebwerksdüsen usw., sind hohe Präzision und Schärfe erforderlich, die keine Fehler zulassen. Fast alle Produkte müssen von tadelloser Qualität sein.
Hartlöten Technologie ist in diesen Bereichen aufgrund ihrer Vorteile wie geringe thermische Belastung, hohe Präzision, breite Anwendbarkeit und hohe Schweißleistung weit verbreitet. Sie ermöglicht die Verbindung mehrerer, komplexer, hochpräziser Teile.
Das Hartlot spielt eine entscheidende Rolle bei der Lötprozess.
Um die Kombination von zwei Materialien (oder Teilen) zu realisieren, wird der in oder neben dem Spalt hinzugefügte Füllstoff als Schweißzusatz bezeichnet.
(1) Ein geeigneter Schmelzpunkt (einige zehn Grad niedriger als der des Grundmetalls);
(2) Ausgezeichnete Benetzbarkeit;
(3) Vollständig aufgelöst und mit dem Grundmetall verbunden;
(4) Eine einheitliche und stabile Zusammensetzung;
(5) Es ist kostengünstig und sicher (es enthält weniger Edelmetalle und toxische Metalle).
1) Klassifizierung nach Schmelzpunkt
"Weichlot" (auch bekannt als "schmelzbares Lot") bezieht sich auf Lote mit einem Schmelzpunkt von weniger als 450 °C, darunter Zinn-Blei-Lot, Cadmium-Silber-Lot und Blei-Silber-Lot.
"Hartlot" (auch "feuerfestes Hartlot") bezieht sich auf Hartlötmittel mit einem Schmelzpunkt über 450 °C, darunter Hartlötmittel auf Aluminium-, Kupfer-, Silber- und Nickelbasis.
2) Klassifizierung nach chemischen Hauptbestandteilen
Laut der wichtigsten Metallelemente des Lots wird es × Basislot genannt, wie z. B. Hartlötbasislot, Zinkbasislot usw.
3) Nach Form sortieren
Man unterscheidet zwischen Draht, Stangen, Blechen, Folien, Pulver und Lötmitteln mit spezieller Form (z. B. ringförmiges Lot oder Pastenlot).
(1) Weichlot
Es wird vor allem für das Schweißen von Werkstücken mit geringer Spannung und niedrigen Betriebstemperaturen verwendet, z. B. zum Verbinden verschiedener elektrischer Drähte und Lötgeräte, Komponenten von Instrumenten und anderen elektronischen Schaltungen.
(2) Hartlötkolben
Es wird hauptsächlich zum Schweißen von Werkstücken mit großer Kraft und hoher Arbeitstemperatur verwendet, wie z. B. Fahrradrahmen, Hartmetallfräser, Bohren Bit und andere mechanische Teile.
Um ein besseres Ergebnis zu erzielen SchweißnahtBei der Verwendung von Hartlötmitteln ist es notwendig, das Flussmittel auf die verschiedenen Hartlote abzustimmen, die gemeinsam als Schweißmaterial für den Lötprozess verwendet werden.
Das Flussmittel, das beim Hartlöten verwendet wird, heißt Hartlötflussmittel, einschließlich Paste, Pulver, usw.
1) Entfernen Sie die Oxidschichten von der Oberfläche des Lots und des Grundmetalls.
2) Verbessern Sie die Fähigkeit des flüssigen Lots, die Schweißnähte zu benetzen.
3) Verhindern Sie, dass das Schweißgut und das flüssige Lot während des Lötvorgangs oxidiert werden.
1) Vergewissern Sie sich, dass genügend Kapazität vorhanden ist, um Oxide von der Oberfläche des Grundmetalls und des Zusatzwerkstoffs zu entfernen.
2) Der Schmelzpunkt und die minimale Aktivtemperatur des Flussmittels sollten niedriger sein als der Schmelzpunkt des Hartlotes.
3) Sicherstellung einer ausreichenden Benetzungsfähigkeit an der Löttemperatur.
4) Die flüchtigen Bestandteile des Flussmittels sollten ungiftig sein.
5) Das Flussmittel und seine Rückstände sollten nur minimale Korrosion am Lot und am Grundmetall aufweisen und sich leicht entfernen lassen.
1) Weichlötflussmittel
Die Flussmittel, die zum Löten bei Temperaturen unter 450 ℃ verwendet werden, lassen sich in zwei Arten unterteilen: anorganische und organische.
a. Anorganisches Weichlot (korrosives Weichlot) - Es besteht aus anorganischen Salzen und Säuren und hat eine starke chemische Aktivität und thermische Stabilität. Diese Art von Lot fördert die Benetzung des flüssigen Lots mit dem Grundmetall effektiv, aber seine Rückstände haben eine starke korrosive Wirkung.
b. Organisches Flussmittel (nicht-korrosives Flussmittel) - Seine chemische Aktivität ist relativ schwach und greift das Grundmetall nicht an. Beispiele für nicht korrosive Flussmittel sind Kolophonium, Amine und organische Halogenide.
2) Hartlötflussmittel
Das Flussmittel, das zum Löten bei Temperaturen über 450 ℃ verwendet wird, hat eine hohe Viskosität und muss bei hohen Temperaturen aktiviert werden.
Es muss bei Temperaturen über 800 ℃ verwendet werden, und seine Rückstände sind schwer zu entfernen.
Zu den gebräuchlichen Hartlötflussmitteln gehören Borax, Borsäure und deren Mischungen. Die Zugabe von Fluorid und Chlorid von Alkali- und Erdalkalimetallen zu Boriden kann die Benetzbarkeit von Borax- und Borsäure-Lotflussmitteln verbessern, die Oxidentfernung verbessern und die Schmelz- und Aktivierungstemperatur der Lotflussmittel senken.
Schweissgas bezieht sich in erster Linie auf das Schutzgas, das bei Schutzgasschweißverfahren wie dem CO2-Schutzgasschweißen und dem Schutzgasschweißen verwendet wird, sowie auf das beim Gasschweißen und -schneiden verwendete Gas.
Beim Schweißen muss die Schutzgas dient nicht nur als Schutzmedium für den Schweißbereich, sondern auch als Gasmedium, das den Lichtbogen erzeugt.
Gasschweißen und Schneiden werden in der Regel mit einer Hochtemperaturflamme durchgeführt, die durch die Verbrennung von Gas erzeugt wird, das eine konzentrierte Wärmequelle darstellt.
Emotionales Gas | Molekulares Gas | Zusammengesetztes Gas |
Argon, Ammoniak | Sauerstoff, Stickstoff, Wasserstoff | Kohlendioxid |
Das heißt, dass verbrennungsförderndes Gas (O2) und brennbares Gas (Acetylen C2H2).
Gas | Symbol | Wichtigste Eigenschaften | Anwendung beim Schweißen |
Kohlendioxid | CO2 | Es hat stabile chemische Eigenschaften, brennt nicht und unterstützt die Verbrennung nicht, kann bei hohen Temperaturen in C0 und 0 zersetzt werden und hat eine gewisse Oxidierbarkeit gegenüber Metallen. Es kann flüssiges CO2 verflüssigen, beim Verdampfen viel Wärme aufnehmen und sich zu festem CO2 verfestigen, das gemeinhin als Trockeneis bekannt ist. | Schweißdraht kann während des Schweißens als Schutzgas verwendet werden, wie z.B. CO2-Schutzgasschweißen und C02+O2, C02+A und andere Mischgas-Schutzgasschweißen |
Argon | Ar | Emotionales Gas, nicht chemisch aktiv, reagiert nicht mit anderen Elementen bei Raumtemperatur und hoher Temperatur | Als Schutzgas für den mechanischen Schutz beim Lichtbogenschweißen, Plasmaschweißen und Schneiden |
Sauerstoff | O2 | Farbloses Gas, verbrennungsfördernd, sehr aktiv bei hohen Temperaturen, direkt mit verschiedenen Elementen verbunden. Während des Schweißens wird Sauerstoff oxidieren Metallelemente wenn es in die Schmelze eintritt, was eine schädliche Rolle spielen wird | Es kann extrem hohe Temperaturen erreichen, wenn es mit brennbarem Gas zum Schweißen und Schneiden gemischt wird, wie Sauerstoff-Acetylen-Flamme und Wasserstoff-Sauerstoff-Flamme. Mischen Sie mit Argon, Kohlendioxid, etc. im Verhältnis, und führen Sie gemischte Gas-Schutzgas-Schweißen |
B schnell | CH2 | Allgemein bekannt als Kalziumkarbidgas, ist es wenig wasserlöslich, löslich in Alkohol und weitgehend löslich in Aceton. Es mischt sich mit Luft und Sauerstoff zu einem explosiven Gasgemisch. Es verbrennt in Sauerstoff und erzeugt hohe Temperaturen und starkes Licht. | Für Autogen Flammenschweißen und Schneiden |
Wasserstoff | H2 | Es kann brennen, ist bei normaler Temperatur nicht aktiv und ist bei hoher Temperatur sehr aktiv. Es kann als Reduktionsmittel für Metallerze und Metalloxide verwendet werden. Es kann beim Schweißen in flüssigem Metall geschmolzen und beim Abkühlen ausgefällt werden, wodurch sich leicht Poren bilden können. | Beim Schweißen kann es als reduzierendes Schutzgas verwendet werden, das zur Verbrennung mit Sauerstoff gemischt wird, und es kann als Wärmequelle für das Gasschweißen verwendet werden. |
Stickstoff | N2 | Die chemische Eigenschaft ist nicht aktiv, und es kann bei hohen Temperaturen direkt mit Wasserstoff und Sauerstoff kombiniert werden. Es ist schädlich, wenn es beim Schweißen in das Schmelzbad gelangt. Es reagiert grundsätzlich nicht mit Kupfer und kann als Schutzgas verwendet werden | Beim Stickstofflichtbogenschweißen wird Stickstoff als Schutzgas verwendet, um Kupfer schweißen und rostfreiem Stahl. Stickstoff wird auch häufig in Plasmen verwendet Lichtbogenschneiden als das äußere Schutzgas |
Gas | Komponente | Potentialgradient der Bogensäule | Stabilität des Lichtbogens | Eigenschaften von Metallübergängen | Chemische Eigenschaften | Eindringen der Schweißnaht Form | Heizverhalten |
CO2 | 99,9%-Reinheit | hoch | zufrieden | Zufrieden, aber einige Spritzer | Starke Oxidation | Flache Form mit großer Eindringtiefe | – |
Ar | Reinheit 99,995% | niedrig | gut | zufrieden | – | Pilzform | – |
Er | 99,99%-Reinheit | hoch | zufrieden | zufrieden | – | Wohnung | Der Wärmeeintrag beim Stumpfschweißen ist höher als bei reinem Ar |
N2 | 99,9%-Reinheit | hoch | Unterschied | Unterschied | Erzeugung von Porosität und Nitrid in Stahl | Wohnung | – |
1)Ar + He
Sie kann Folgendes verbessern Einbrandverhalten, verringern die Porosität und verbessern die Produktionseffizienz.
Es kann für Kupfer, Aluminium und deren Legierungen sowie für Titan, Zirkonium und andere Metalle verwendet werden.
2)Ar + H2
Der Zusatz von Wasserstoff kann die Lichtbogentemperatur erhöhen, den Wärmeeintrag in das Grundmetall steigern und die Bildung von CO-Porosität verringern.
Das Gasgemisch ist ein Reduktionsmittel und eignet sich ideal zum Schweißen von Nickel und seinen Legierungen sowie von Edelstahlrohren.
3)Ar + N2
Um die Lichtbogentemperatur zu erhöhen, sollten Sie N2 hinzufügen. Eine geringe Zugabe von N2 kann die Steifigkeit des Lichtbogens erhöhen und die Schweißnahtbildung verbessern.
Diese Technik eignet sich zum Schweißen von Nichteisenmetallen, wie z. B. Kupfer und Aluminium.
4)Ar + O2
Der Sauerstoffgehalt in Ar+O2 (niedriger Gehalt) liegt im Bereich von 1-5%, was die Benetzbarkeit der Lösung verbessert, die Porosität minimiert und den Lichtbogen stabilisiert. Diese Methode ist geeignet für Schweißen von rostfreiem Stahleinschließlich Stahl mit niedrigem Kohlenstoffgehalt und niedrig legiertem Stahl.
Ar+O2 (hoher Gehalt) hat einen Sauerstoffgehalt von etwa 20%, was die Produktionseffizienz erhöht, die Porosität verringert und die Schlagzähigkeit der Schweißnähte verbessert. Dieses Verfahren ist für das Schweißen von Kohlenstoffstahl und niedrig legiertem Baustahl geeignet.
5)Ar + CO2
Stabiler Lichtbogen, minimale Spritzer, einfach zu erreichender axialer Sprühübergang, optimale Schweißnahtausbildung und ein breites Anwendungsspektrum (sowohl für Sprühübergang als auch für Kurzschlussübergang geeignet).
6)Ar + CO2 + O2
Es hat sich bestätigt, dass das optimale Gasgemisch zum Schweißen von kohlenstoffarmen und kohlenstoffarmen legierter Stahl ist 80% Argon, 15% Kohlendioxid und 5% Sauerstoff. Diese Mischung liefert hervorragende Ergebnisse in Bezug auf Schweißnahtbildung, Verbindungsqualität, Metallübertragung und Lichtbogenstabilität und ist sehr zufriedenstellend.
7)CO2 + O2
Hohe Abschmelzleistung, tiefer Einbrand, niedriger Wasserstoffgehalt im Schweißgut, starkes Schweißen mit hohen Stromspezifikationen, stabiler Lichtbogen und minimale Spritzer.
Eine Rille, die entlang des Fußes oder der Wurzel einer Schweißnaht entsteht.
1) Übermäßiger Schweißstrom;
2) Der Schweißbogen ist zu lang;
3) Der Elektrodenwinkel ist falsch.
Unvollständige Durchdringung der Verbindungswurzel beim Schweißen.
1) Falsche Rillengröße;
2) Falsche Auswahl der Schweißprozessparameter;
3) Die Elektrode weicht von der Rillenmitte ab oder der Winkel ist falsch.
Unvollständige Verschmelzung und Bindung zwischen Schweißgut und Grundwerkstoff oder Schweißraupe Metall.
1) Der Schweißstrom ist zu gering oder die Schweißgeschwindigkeit zu hoch ist;
2) Ungeeignete Reinigung vor dem Schweißen;
3) Die Elektrode weicht von der Schweißmitte ab.
Eine Vertiefung, die sich am Ende einer Schweißnaht oder an einer Verbindung bildet.
Während des Schweißens fließt das geschmolzene Metall aus der Rückseite der Rille und bildet eine Perforation.
Ein Metallknötchen, das sich bildet, wenn geschmolzenes Metall außerhalb der Schweißnaht auf das ungeschmolzene Grundmetall fließt.
Schlacke oder nicht-metallisch Verunreinigungen, die nach dem Schweißen in der Schweißnaht verbleiben.
Ein Loch, das durch Gas entsteht, das nach dem Schweißen in der Schweißnaht verbleibt.
Porenbildende Gasquelle:
1) Außenluft;
2) Luftfeuchtigkeit;
3) Ölverschmutzung und Verunreinigungen.
(1) Je nach Schweißposition
(2) Entsprechend der Rissrichtung
① Der Längsriss verläuft parallel zur Schweißnaht
② Querriss senkrecht zur Schweißnaht
(3) Je nach den Bedingungen der Rissbildung
① Heißer Riss Riss in der Nähe der Solidustemperatur der Schweißnaht und Wärmeeinflusszone
② Ein unter die martensitische Umwandlungstemperatur abgekühlter Riss
③ Wiedererwärmungsriss
④ Leiterförmige Risse entlang der Walzrichtung des Blechs aufgrund von Lamellenrissen
In CO2 Beim CO-Schweißen wird der größte Teil des geschmolzenen Metalls aus dem Schweißdraht in das Schweißbad übertragen, aber ein Teil davon entweicht und bildet Spritzer. Bei der Verwendung von dickem Schweißdraht für CO2 Schutzgasschweißen Bei großen Parametern können die Spritzer besonders stark werden, mit einer Rate von bis zu 20%.
Dies führt dazu, dass ein normales Schweißen nicht mehr möglich ist. Die Spritzer sind schädlich, da sie die Effizienz des Schweißens verringern, die Qualität der Schweißnaht beeinträchtigen und schlechte Arbeitsbedingungen schaffen.
Spritzwassergefahr
Der Metallspritzerverlust in CO2 Beim Schutzgasschweißen können zwischen 10% und 30-40% des geschmolzenen Metalls aus dem Schweißdraht anfallen. Der ideale Verlust wird auf 2-4% kontrolliert.
Dieser Verlust hat mehrere negative Auswirkungen:
Die Verhinderung und Verringerung von Metallspritzern ist ein entscheidender Aspekt bei der CO2 Schutzgasschweißen.
Maßnahmen zur Verringerung von Spritzern
(1) Richtige Auswahl der Prozessparameter
Beim CO2-Lichtbogenschweißen besteht eine Korrelation zwischen der Spritzerrate und dem Schweißstrom für jeden Schweißdrahtdurchmesser. Im Niederstrombereich (Kurzschlussübergangsbereich) ist die Spritzerrate gering. Wenn der Strom in den Hochstrombereich (Feinpartikelübergangsbereich) eintritt, nimmt die Spritzerrate wieder ab. Die Spritzerrate ist jedoch im mittleren Bereich am höchsten.
Die Spritzerrate ist gering, wenn der Schweißstrom unter 150 A oder über 300 A liegt, und sie ist hoch zwischen diesen beiden Werten. Um die Spritzerrate zu minimieren, ist es am besten, Schweißströme in diesem Bereich mit hoher Spritzerrate zu vermeiden.
Nach der Bestimmung des Schweißstroms sollte die geeignete Spannung gewählt werden, um eine möglichst geringe Spritzerquote zu gewährleisten.
Die Spritzermenge ist am geringsten, wenn die Schweißpistole senkrecht gehalten wird. Mit zunehmendem Neigungswinkel der Pistole nimmt auch die Spritzermenge zu. Es wird empfohlen, die Schweißpistole um nicht mehr als 20 Grad nach vorne oder hinten zu neigen.
Die Spritzerquote wird auch von der Länge des Schweißdrahtes beeinflusst. Am besten ist es, die Länge des Schweißdrahtes so kurz wie möglich zu halten, um Spritzer zu minimieren.
(2) Wählen Sie das geeignete Schweißdrahtmaterial und die Schutzgaszusammensetzung.
Zum Beispiel:
Die Erfahrung zeigt, dass, wenn die Kohlenstoffgehalt im Schweißdraht auf 0,04% reduziert wird, können Spritzer deutlich verringert werden.
Der Fülldrahtkern im Rohrschweißdraht enthält Desoxidationsmittel und Lichtbogenstabilisatoren, die die Gasschlackenverbindung schützen, den Schweißprozess stabiler machen und Spritzer erheblich reduzieren. Die Metallspritzerrate von Fülldraht beträgt etwa ein Drittel derjenigen von Massivdraht.
(3) CO2 Gemisch wird beim Schweißen mit langem Lichtbogen als Schutzgas verwendet.
Obwohl die Spritzerrate durch die richtige Wahl der Spezifikationsparameter und die Anwendung des Unterpulververfahrens reduziert werden kann, ist die Menge der erzeugten Spritzer immer noch erheblich.
Die Beimischung einer bestimmten Menge Argon (Ar) in Kohlendioxid (CO2) ist die wirksamste Methode zur Verringerung von Metallspritzern, die durch übermäßiges Schweißen von Partikeln verursacht werden.
Die physikalischen und chemischen Eigenschaften von reinem CO2 Gas verändern sich, wenn Argon zu der Mischung hinzugefügt wird.
Mit zunehmendem Anteil an Argongas nimmt die Menge der Spritzer allmählich ab.
Die CO2Das +Ar-Gasgemisch reduziert nicht nur Spritzer, sondern verbessert auch die Schweißnahtbildung, indem es den Einbrand, die Höhe und die Verstärkung der Schweißnaht beeinflusst.
Wenn der Argongehalt 60% erreicht, kann die Größe der Übertragungströpfchen merklich reduziert und eine gleichmäßige Sprühübertragung erreicht werden, wodurch die Eigenschaften der Tröpfchenübertragung verbessert und Metallspritzer reduziert werden.
1. Skala schweißen
Reparaturmethode
Schweißnahtoberfläche nach dem Entzundern
2. Luftloch
Reparaturmethode: Schleifen und Entfernen der Schweißnaht und erneutes Schweißen.
3. Krater nadelförmiges Luftloch
4. Luftloch (Sandloch)
5. Schrumpfungshohlraum
6. Endriss/Schweißriss
7. Auftreten von schlechten Schweißnähten
8. Überlappung und Blitzlicht
9. Unterschnitt
10. Ungleichmäßige Schweißnaht
11. Schlechtes Aussehen
Das Schweißnahtsymbol besteht aus einem Basissymbol und einer Führungslinie sowie ggf. zusätzlichen Symbolen, Zusatzsymbolen und Symbolen, die die Größe der Schweißnaht angeben.
Das Basissymbol stellt die Querschnittsform der Schweißnaht dar und ist ähnlich dem Symbol für die Querschnittsform der Schweißnaht in Tabelle 4-2.
Hilfssymbole sind Symbole, die die Formmerkmale der Schweißnahtoberfläche angeben. Diese Symbole können weggelassen werden, wenn die Angabe der Oberflächenform der Schweißnaht nicht erforderlich ist.
Zusätzliche Symbole werden verwendet, um die Symbole zu ergänzen, die bestimmte Merkmale der Schweißnahtoberfläche darstellen. Die Methoden zur Darstellung dieser Symbole sind in Tabelle 4-3 aufgeführt.
Wenn die Größe der Schweißnaht während der Konstruktion oder Fertigung angegeben werden muss, wird sie durch das Symbol für die Schweißnahtgröße gekennzeichnet, wie in Tabelle 4-4 dargestellt.
Tabelle 4-2 Grundsymbole der Schweißformen
Laufende Nummer | Name der Schweißnaht | Typ der Schweißnaht | Grundlegende Symbole |
1 | I-förmige Schweißnaht | ![]() | ![]() |
2 | V-förmige Schweißnaht | ![]() | ![]() |
3 | Stumpfe V-Naht | ![]() | ![]() |
4 | Unilaterale V-förmige Schweißnaht | ![]() | ![]() |
5 | Einzelne V-förmige Schweißnaht mit stumpfer Kante | ![]() | ![]() |
6 | U-förmige Schweißnaht | ![]() | ![]() |
7 | Unilaterale U-förmige Schweißnaht | ![]() | ![]() |
8 | Bördelschweißung | ![]() | ![]() |
9 | Kehlnaht | ![]() | ![]() |
10 | Schweißstopfen | ![]() | ![]() |
11 | Schweißpunkt | ![]() | ![]() |
12 | Schweißnaht | ![]() | ![]() |
13 | Rückseite Wulst | ![]() | ![]() |
Tabelle 4-3 Hilfssymbole und ergänzende Symbole für Schweißnähte
Laufende Nummer | Name | Typ | Hilfssymbol | Erklären Sie |
1 | Symbol der Ebene | ![]() | ![]() | Zeigt an, dass die Schweißfläche bündig ist |
2 | Symbol der Depression | ![]() | ![]() | Bezeichnet die Vertiefung der Schweißnahtoberfläche |
3 | Erhöhtes Symbol | ![]() | ![]() | Anzeige der Schweißnahtoberflächenwölbung |
Laufende Nummer | Name | Typ | Ergänzendes Symbol | Erklären Sie |
1 | Symbol mit Rückwandplatte | ![]() | ![]() | Zeigt an, dass sich an der Unterseite der Schweißnaht eine Verstärkungsplatte befindet. |
2 | Dreiseitiges Schweißsymbol | ![]() | ![]() | Die Öffnungsrichtung des dreiseitigen Schweißsymbols muss grundsätzlich mit der tatsächlichen Richtung der dreiseitigen Schweißnaht übereinstimmen. |
3 | Symbol für Umfangsschweißung | ![]() | ![]() | Zeigt das Schweißen um das Werkstück herum an |
4 | Standort-Symbole | ![]() | ![]() | Zeigt Schweißen auf der Baustelle oder auf der Baustelle an |
Tabelle 4-4 Größensymbole für Schweißnähte
Symbol | Name | Skizze Karte |
δ | Blechdicke | ![]() |
α | Rillenwinkel | ![]() |
b | Freiraum am Hintern | ![]() |
p | Höhe der stumpfen Kante | ![]() |
c | Breite der Schweißnaht | ![]() |
K | Filetgröße | ![]() |
d | Nugget-Durchmesser | ![]() |
S | Effektive Dicke der Schweißnaht | ![]() |
N | Anzahl der identischen Schweißnähte Symbol | ![]() |
K | Filetgröße | ![]() |
R | Wurzelradius | ![]() |
l | Länge der Schweißnaht | ![]() |
n | Anzahl der Schweißsegmente | |
H | Tiefe der Rille | ![]() |
h | Schweißnahtverstärkung | ![]() |
β | Winkel der Nutenfläche | ![]() |
(1) Die Führungslinie besteht aus einer Pfeillinie mit einer Pfeilspitze und zwei Bezugslinien (eine dünne durchgezogene Linie und eine gepunktete Linie).
(2) Die gepunktete Linie kann entweder über oder unter der dünnen durchgezogenen Linie liegen.
Die Bezugslinie verläuft in der Regel parallel zur Längsseite des Schriftfeldes, kann aber bei Bedarf auch senkrecht zur Längsseite des Schriftfeldes verlaufen.
Die Pfeillinie wird mit einer dünnen durchgezogenen Linie gezeichnet, und der Pfeil zeigt auf die betreffende Schweißnaht. Falls erforderlich, kann die Pfeillinie einmal gebogen werden.
Wenn es erforderlich ist, das Schweißverfahren zu beschreiben, kann am Ende der Bezugslinie ein Schwanzsymbol eingefügt werden.
(1) Die Abmessungen über den Querschnitt der Schweißnaht sind auf der linken Seite des Grundsymbols angegeben.
(2) Die Längenmaße der Schweißnaht sind auf der rechten Seite des Grundsymbols angegeben.
(3) Der Rillenwinkel (α), der Rillenflächenwinkel (β) und der Wurzelspalt (b) sind entweder über oder unter dem Grundsymbol angegeben.
(4) Dieselbe Schweißnahtmenge und derselbe Schweißverfahrenscode sind am Ende angegeben.
(5) Wenn eine große Menge von Abmessungsdaten zu kennzeichnen ist und die Unterscheidung schwierig wird, können den Daten entsprechende Abmessungssymbole vorangestellt werden, um die Informationen zu verdeutlichen.
Tabelle 12-1 Schweißnahtsymbole und Kennzeichnungsmethoden
Die gemeinsame Schweißnähte sind Stumpfstoß, T-Stoß, Eckstoß und Überlappstoß, wie in der Abbildung dargestellt.
Die Auswahl von Schweißverbindungen richtet sich in erster Linie nach dem Aufbau der Schweißung, der Dicke der Schweißnaht, den Festigkeitsanforderungen an die Schweißnaht und den Bedingungen, unter denen die Konstruktion ausgeführt wird.
Spezifizierte Zeichnungsmethode der Schweißnaht
Die Linie, die nach dem Zusammenschweißen der Werkstücke entsteht, wird als Schweißnaht bezeichnet.
Wenn eine einfache Darstellung der Schweißnaht in einer Zeichnung erforderlich ist, kann sie in einer Ansicht, einem Schnitt oder einem axonometrischen Diagramm dargestellt werden.
Die spezifische Methode zur Darstellung der Schweißnaht in einer Zeichnung ist in der Abbildung dargestellt.
Strukturelles Schweißen führt immer zu Schweißverformungen und Spannungen.
Während des Schweißvorgangs werden die Verformung und Eigenspannung die in der Schweißnaht erzeugt werden und sich im Laufe der Zeit ändern, werden als vorübergehende Verformung bzw. vorübergehende Schweißspannung bezeichnet.
Die Verformung und die Spannung, die in der Schweißnaht verbleiben, wenn die Temperatur nach dem Schweißen auf Raumtemperatur abgekühlt ist, werden als Schweißrestverformung bzw. Schweißrestspannung bezeichnet.
Die Hauptursache für Schweißspannungen und -verformungen liegt in der ungleichmäßigen Erwärmung und Abkühlung der Schweißzone.
Während des Schweißvorgangs wird die Schweißnaht lokal erwärmt, was zu einer Verformung führt, da sich das Metall ausdehnt und zusammenzieht.
Allerdings ist die Stahlplatte ist ein festes Stück, und diese Ausdehnung kann nicht frei erfolgen.
Das Ende der Stahlplatte kann sich nur gleichmäßig um einen Betrag von Δι ausdehnen.
(a) Während des Schweißens;
(b) Nach dem Schweißen.
Während der Abkühlung hat sich das Metall in der Nähe der Schweißnaht während des Schweißens dauerhaft plastisch verformt und wird außerdem durch das Metall auf beiden Seiten eingeschränkt.
Um die Gesamtkonsistenz zu erhalten, wird Δι' gleichmäßig reduziert, was eine gewisse elastische Spannung im Schweißbereich und eine gewisse elastische Kompression im Metall auf beiden Seiten erzeugt.
Die Folge sind Zugspannungen in der Schweißzone und im umgebenden Metall sowie Druckspannungen im Metall auf beiden Seiten.
Die Spannung im Bauteil befindet sich in einem Zustand des Gleichgewichts. Es kann beobachtet werden, dass nach Stumpfschweißen einer flachen Platte ist die Länge von Δι' kürzer als vor dem Schweißen.
Gleichzeitig wird in der Schweißzone eine Zugspannung erzeugt, und das Metall auf beiden Seiten, fern von der Schweißnaht, erfährt eine Druckspannung.
Mit anderen Worten: Die Schweißspannung und -verformung bleiben bei Raumtemperatur erhalten und werden als Schweißeigenspannung und -verformung bezeichnet.
Schweißspannungen lassen sich in vier Kategorien einteilen: thermische Spannungen, Zwangsspannungen, Phasenwechselspannungen und Schweißeigenspannungen. Die Schweißeigenspannung ist oft sehr hoch.
Bei Strukturen mit dicken Schweißnähten kann die Schweißeigenspannung in der Regel die Streckgrenze des Materials.
(1) Longitudinalspannung: Spannung entlang der Länge der Schweißnaht.
(2) Querspannung: Spannung senkrecht zur Länge der Schweißnaht und parallel zur Oberfläche des Bauteils.
(3) Spannung in Richtung der Dicke: Spannung senkrecht zur Länge der Schweißnaht und zur Oberfläche des Bauteils.
(1) Längsspannung der Schweißnaht σ x
Die Spannung entlang der Längsrichtung der Schweißnaht wird als Längsspannung (σ x) bezeichnet.
Die Spannung senkrecht zur Längsrichtung der Schweißnaht wird als Querspannung (σ y) bezeichnet.
In der Zone der plastischen Druckverformung in der Nähe der Schweißnaht ist die Längsspannung (σ x) eine Zugspannung, die typischerweise die folgenden Werte erreichen kann Streckgrenze des Materials.
(2) Querbelastung der Schweißnaht
Die Abbildung veranschaulicht die Verteilung der Querspannung (σy) in einem Schweißplatte einer bestimmten Länge.
σy ist die Zugspannung in der Schweißnaht und die Zone der plastischen Druckverformung in der Nähe der Schweißnaht, während die beiden Enden Druckspannungen erfahren.
Je weiter man sich von der Mitte der Schweißnaht entfernt, desto schneller nimmt σy ab.
Zusätzlich zu den Längs- und Querspannungen treten bei geschweißten Dickblechkonstruktionen auch Spannungen entlang der Dickenrichtung auf.
Die Spannungsverteilung in den drei Richtungen ist in Dickenrichtung sehr ungleichmäßig.
Beim Elektroschlackeschweißen dicker Bleche treten in der Mitte der Schweißnaht drei axiale Zugspannungen auf, die mit zunehmender Blechdicke zunehmen, während an der Oberfläche Druckspannungen auftreten.
(1) Auswirkungen auf die Festigkeit und Stabilität von Druckteilen
Wenn das Bauteil auf Zug belastet wird, addiert sich die Schweißeigenspannung zur Lastspannung und beeinträchtigt die Festigkeit des Bauteils.
(2) Einfluss auf den Sprödbruch von Bauteilen
Der Anstieg der Nennspannung des Bauteils in Verbindung mit der Abnahme der Materialzähigkeit im Bereich der Schweißnaht und dem Vorhandensein von Schweißfehlererhöht die Wahrscheinlichkeit eines Sprödbruchs bei geringen äußeren Belastungen.
(3) Auswirkung auf Ermüdungsfestigkeit
Die Zug-Eigenspannung in der Schweißzone kann den durchschnittlichen Zugspannungswert der Struktur erhöhen und ihre Ermüdungslebensdauer verringern.
(4) Auswirkungen auf die Bearbeitungsgenauigkeit und Maßhaltigkeit von Schweißteilen
(5) Auswirkungen auf die Rissausbreitung
Bei der Bewertung des Risszustandes in der Schweißzone muss die Schweißeigenspannung berücksichtigt werden.
Bei der Berechnung des Spannungsintensitätsfaktors (KI), der das Risswachstum antreibt, wird der Eigenspannung (σr) wird berücksichtigt, indem die äquivalente Zugspannung (σ3), der den Beitrag der Eigenspannung zum Risswachstum darstellt:
σ3 = αrσr
Wobei σr ist abhängig von der Art des Risses (durchgehender Riss, vergrabener Riss, Oberflächenriss) und der Richtung des Risses (Risse parallel zur Schmelzlinie, Risse senkrecht zur Schmelzlinie und Kehlnaht) Schweißrisse).
Verringern Schweißeigenspannung durch Design und Schweißprozess
(1) Der Schlüssel zur Verringerung der Schweißspannung bei der Konstruktion liegt in der richtigen Anordnung der Schweißnähte, um Spannungsüberlagerungen zu vermeiden und Spannungsspitzen zu reduzieren.
① Minimieren Sie die Anzahl der Schweißnähte und reduzieren Sie die Größe und Länge der Schweißnähte.
② Die Schweißnähte sollten in ausreichenden Abständen angeordnet sein und sich möglichst nicht kreuzen, um komplexe dreidimensionale Spannungen zu vermeiden.
③ Schweißnähte sollten nicht in Bereichen mit hoher Spannung und abrupten Querschnittsänderungen liegen, um Spannungskonzentrationen zu vermeiden.
④ Die flexiblere Tischverbindung sollte verwendet werden, und Flanschen sollte das Einführungsrohr ersetzt werden.
(2) Techniken zur Reduzierung der Schweißspannung im Prozess
① Wählen Sie eine vernünftige Schweißreihenfolge und -richtung und führen Sie die meisten Schweißnähte mit geringerer Steifigkeit aus.
② Minimieren Sie den Temperaturunterschied zwischen dem Schweißbereich und der gesamten Struktur, um innere Schweißspannungen zu reduzieren. Verwenden Sie eine allgemeine Vorwärmung und eine niedrige lineare Energie.
③ Verwenden Sie das Hammerschweißen, um Schweißspannung und Verformung zu reduzieren.
④ Verringern Sie den Wasserstoffgehalt und eliminieren Sie Wasserstoff.
(3) Die Methode zur Beseitigung von Eigenspannungen beinhaltet in erster Linie die Beseitigung von Eigenspannungen nach dem Schweißen. Bei Kesseln und Druckbehältern mit einer Dicke des Druckteils, die eine bestimmte Größe überschreitet, ist eine Wärmebehandlung nach dem Schweißen erforderlich, um Folgendes zu beseitigen Eigenspannung.
Im Allgemeinen führt das Schweißen zu einer Verformung des Werkstücks. Übersteigt die Verformung die zulässige Grenze, beeinträchtigt sie die Funktionalität.
Die Hauptursache für Verformungen ist die ungleichmäßige Erwärmung und Abkühlung der Schweißnaht während des Schweißens.
Beim Schweißen wird die Schweißnaht nur lokal erwärmt, aber das Metall im erwärmten Bereich kann sich nicht frei ausdehnen, weil das Metall in der Umgebung eine niedrigere Temperatur hat.
Beim Abkühlen kann es nicht frei schrumpfen, da es vom umgebenden Metall eingeschlossen wird.
Dies hat zur Folge, dass dieser Teil des erhitzten Metalls Zugspannungen ausgesetzt ist, während andere Teile des Metalls im Gleichgewicht dazu Druckspannungen erfahren.
Wenn diese Spannungen die Streckgrenze des Metalls überschreiten, kommt es zu einer Schweißverformung.
Risse entstehen, wenn die Festigkeitsgrenze des Metalls überschritten wird.
1. Formen der Schweißverformung
Die Formen der Schweißverformung können vielfältig sein. Die häufigsten Formen sind fünf Grundformen oder Kombinationen dieser Formen.
Abbildung (a) zeigt die Längs- und Querschrumpfverformung in einem flachen Blech nach dem Stumpfschweißen;
Abbildung (b) zeigt die Winkelverformung in einer flachen Platte nach dem Andocken;
Abbildung (c) zeigt die Biegeverformung, die durch die Abweichung der Schweißanordnung in einem Zylinder von der Schwerpunktsachse des Schweißstücks verursacht wird;
Abbildung (d) zeigt die wellenförmige Verformung in einer dünnwandigen Schweißnaht nach dem Schweißen.
Außerdem sind Träger-Stützen-Strukturen anfällig für Verformungen beim Schweißen.
Schwundverformung und Biegeverformung sind Formen der Gesamtverformung, während die anderen Formen als lokale Verformung betrachtet werden.
2. Einflussfaktoren auf die Schweißverformung
(1) Der Einfluss der Schweißnahtposition auf die Schweißverformung
Wenn die Schweißnähte in der Struktur symmetrisch angeordnet sind, treten nur Längs- und Querverkürzungen auf. Sind die Schweißnähte jedoch asymmetrisch in der Struktur angeordnet, kommt es zu einer Biegeverformung. Eine Winkelverformung tritt auf, wenn der Schwerpunkt des Schweißnahtabschnitts vom Schwerpunkt des Verbindungsabschnitts abweicht.
(2) Einfluss der strukturellen Steifigkeit
Bei gleicher Kraft weisen Strukturen mit hoher Steifigkeit eine geringere Verformung auf, während Strukturen mit geringer Steifigkeit eine größere Verformung aufweisen. Die Verformung beim Schweißen erfolgt immer in die Richtung mit der geringsten Einschränkung durch die Steifigkeit der Struktur oder der Schweißnaht.
(3) Einfluss der Montage- und Schweißreihenfolge
Die Steifigkeitsbeschränkung beim Schweißen einer Bandschweißung hängt von der Montage und dem Schweißverfahren ab. Für Strukturen mit symmetrischen Abschnitten und Schweißnähten kann eine Methode verwendet werden, bei der zunächst ein Ganzes zusammengesetzt wird. Bei komplexen Schweißkonstruktionen wirkt sich die von jeder Schweißnaht verursachte Verformung auf die anderen Schweißnähte aus, so dass sie schwer zu kontrollieren ist. Daher muss ein Verfahren der Teilmontage, des Schweißens, des Zusammenbaus und des erneuten Schweißens angewandt werden, um die gesamte Schweißverformung zu kontrollieren.
(4) Andere einflussreiche Faktoren
Die Verformung steht auch in engem Zusammenhang mit dem Nuttyp, dem Montageabstand, den Schweißspezifikationen und dem Schweißverfahren.
3. Methoden zur Kontrolle der Schweißverformung
Um die Verformung beim Schweißen zu kontrollieren und zu minimieren, ist es wichtig, geeignete Konstruktionspläne und Prozessmaßnahmen anzuwenden.
(1) Reduzieren Sie die Anzahl, Länge und Größe der Schweißnähte so weit wie möglich und stellen Sie gleichzeitig eine angemessene Auslegung für die Tragfähigkeit sicher.
Ordnen Sie die Schweißnähte sinnvoll an, so dass alle Schweißnähte in der Konstruktion symmetrisch zur neutralen Achse des Profils oder so nahe wie möglich an ihr liegen. Dies trägt dazu bei, die Verformung der Schweißnaht zu verringern.
(2) Erforderliche Prozessmaßnahmen:
① Schrumpfungsreserve:
Fügen Sie bei der Vorbereitung des Werkstücks ein angemessenes Schrumpfungsmaß hinzu.
In der Regel wird die Längsschrumpfung der Schweißnaht auf der Grundlage der Länge der Schweißnaht berechnet und hängt von Faktoren wie der Nut, der Art der Verbindung und der Blechdicke ab.
② Umgekehrte Verformungsmethode:
Verwenden Sie Erfahrungswerte oder Berechnungsmethoden, um die Methode der umgekehrten Verformung zu bestimmen.
Vor dem Schweißen ist es wichtig, die Größe und Richtung der möglichen Verformung des Werkstücks zu beurteilen. Um eine Restverformung zu vermeiden, sollte das Schweißstück in die entgegengesetzte Richtung der Verformung gelegt oder vorher bei der Montage künstlich verformt werden. Die richtige Kontrolle trägt dazu bei, dass das Werkstück die richtige Form erhält.
③ Wählen Sie geeignete Schweißmethoden und Spezifikationen:
Verwenden Sie energiereiche Wärmequellen und schnelle Schweißverfahren, um Verformungen zu reduzieren.
④ Optimale Montage- und Schweißreihenfolge:
Teilen Sie die große Struktur in kleinere Teile auf, montieren und schweißen Sie jedes Teil einzeln und fügen Sie die Teile dann zu einem Ganzen zusammen.
⑤ Stabile Fixierung:
Fixieren und klemmen Sie die Struktur vor dem Schweißen, um Verformungen durch äußere Zwänge zu verringern. Allerdings sind starre Spannen kann die freie Schrumpfung der Schweißnaht verhindern, was zu hohen Eigenspannungen im Bauteil führt.
Daher ist es von entscheidender Bedeutung, das Material und die Struktur der Schweißnähte sorgfältig auszuwählen.
⑥ Angemessene Schweißfolge verwenden
4. Korrektur von Schweißverformungen
Trotz der Einführung von Methoden zur Kontrolle der Verformung ist es immer noch schwierig, Verformungen nach dem Schweißen zu vermeiden. Wenn die Verformung des Schweißteils die in den technischen Anforderungen an das Produkt festgelegten Grenzwerte überschreitet, ist eine Korrektur nach dem Schweißen erforderlich, um die Qualitätsstandards des Produkts zu erfüllen.
Ziel der Korrektur ist es, eine neue Verformung in den geschweißten Bauteilen herbeizuführen, um die beim Schweißen entstandene Verformung auszugleichen. Der Korrekturprozess erhöht jedoch häufig die Eigenspannung in den Bauteilen.
Um lokale Frakturen während der Korrektur zu vermeiden, ist es ratsam, die Schweißeigenspannung bevor die Verformung korrigiert wird. Dies trägt dazu bei, die Integrität und Stabilität des Bauteils zu gewährleisten.
Gemeinsame Methoden der mechanischen und flammtechnischen Korrektur in der Produktion:
(1) Mechanische Korrekturmethode:
Bei der mechanischen Korrekturmethode wird mechanischer Druck oder kaltes Hämmern eingesetzt, um eine plastische Verformung zu erzeugen und die Schweißverformung zu korrigieren.
(2) Flammenkorrekturverfahren:
Bei der Flammenkorrektur wird die durch die lokale Erwärmung mit einer Flamme verursachte Kontraktion genutzt, um der Dehnung und Verformung im betroffenen Bereich entgegenzuwirken. Es ist entscheidend, die Heizposition richtig zu bestimmen, und die Heiztemperatur für die Flammenkorrektur liegt in der Regel zwischen 600 und 800 °C.
(3) Achten Sie bei der Korrektur besonders auf den Stahltyp:
Bei der Durchführung von Korrekturen ist es wichtig, auf die Stahlsorte verwendet werden:
Schweisstechnik ist ein entscheidender Faktor bei der Gewährleistung der Qualität von Schweißnähten. In der Fertigung werden die Elemente des Schweißprozesses in den detaillierten Schweißverfahrensrichtlinien beschrieben.
Die detaillierte Schweißanweisung wird auf der Grundlage der Ergebnisse der entsprechenden Verfahrensprüfung erstellt.
Die in der detaillierten Schweißverfahrenskarte aufgeführten Elemente umfassen:
① Vorbereitung vor dem Schweißen;
② Marke und Spezifikationen von Schweißmaterialien;
③ Parameter der Schweißverfahrensspezifikation;
④ Schweißtechnik;
⑤ Inspektion nach dem Schweißen, usw.
Elektrische Parameter beim Schweißen:
(1) Beim kontinuierlichen AC- oder DC-Schweißen sind die wichtigsten elektrischen Parameter in den Schweißspezifikationen die folgenden Schweißspannung und Strom.
(2) Beim Impulsstromschweißen gehören zu den zusätzlichen elektrischen Parametern die Wechselfrequenz, das Ein-Aus-Verhältnis, der Grundstrom und der Spitzenstromwert.
(3) Der Grundsatz für die Auswahl der Schweißspezifikationsparameter ist die Gewährleistung eines guten Einbrandes und einer rissfreien Schweißraupe bei gleichzeitiger Erfüllung der in den technischen Bedingungen festgelegten Leistungsanforderungen.
Bei der Auswahl der elektrischen Parameter ist es wichtig, die Auswirkungen der folgenden Faktoren zu berücksichtigen Schweißwärme Beitrag zur gemeinsamen Leistung.
Die Auswahl der Elektroden-Durchmesser für das Lichtbogenhandschweißen und der entsprechende Schweißstrombereich sind der Tabelle 4-8 zu entnehmen.
Tabelle 4-8 Auswahl des Elektrodendurchmessers und des Schweißstroms für das Lichtbogenhandschweißen
Dicke der Stahlteile (mm) | 1.5 | 2 | 3 | 4~5 | 6~8 | 9~12 | 12~15 | 16~20 | >20 |
Durchmesser der Elektrode (mm) | 1.6 | 2 | 3 | 3~4 | 4 | 4~5 | 5 | 5~6 | 6~10 |
Schweißstrom (A) | 25~40 | 40~65 | 65~100 | 100~160 | 160~210 | 160~250 | 200~270 | 260~300 | 320~400 |
Tabelle 4-9 Auswahl der Spezifikationen für das beidseitige UP-Automatikschweißen für abgeschrägte Werkstücke
Automatisches Unterpulverschweißen | Rillenform | Durchmesser des Schweißdrahtes (mm) | Reihenfolge der Schweißung | Schweißstrom(A) | Lichtbogenspannung(V) | Schweißgeschwindigkeit(m/h) |
14 | ![]() | 5 | positiv | 830~850 | 36~38 | |
5 | negativ | 600~620 | 36~38 | |||
16 | 5 | positiv | 830~850 | 36~38 | ||
5 | negativ | 600~620 | 36~38 | |||
18 | 5 | positiv | 830~850 | 36~38 | ||
5 | negativ | 600~620 | 36~38 | |||
22 | 6 | positiv | 1050~1150 | 38~40 | ||
5 | negativ | 600-620 | 36~38 | |||
24 | ![]() | 6 | positiv | 1100 | 38~40 | |
5 | negativ | 800 | 36~38 | |||
30 | 6 | positiv | 100~1100 | 36~40 | ||
5 | negativ | 900~1000 | 36~38 |
Risse beim Schweißen beziehen sich auf die Trennung des Metallmaterials (lokaler Bruch) innerhalb der Schweißverbindung aufgrund schweißtechnischer Ursachen, wie Metallurgie, Werkstoffe oder innere und äußere Kräfte, während oder nach dem Schweißen.
Risse sind eine der gefährlichsten SchweißfehlerDie Risse sind durch scharfe Enden und eine wesentlich geringere Trennungsbreite (Öffnungsverschiebung) als Risslänge gekennzeichnet.
Die Verhinderung von Schweißrissen ist ein entscheidender Aspekt bei der Konstruktion und Herstellung von Schweißkonstruktionen.
Es gibt verschiedene Arten des Schweißens Risse und ihre Klassifizierungsmethoden haben sich mit der Vertiefung unseres Verständnisses der Natur von Rissen weiterentwickelt.
Die folgende Tabelle enthält eine allgemeine Klassifizierung auf der Grundlage von Zeitpunkt und Ort der Risse.
Tabelle 4-11 Aktuelle Rissklassifizierungsmethode
Zeitraum des Rissauftretens | Ort des Vorkommens | Name | ||
Schweissverfahren | In der Nähe der durchgezogenen Linie | Bindenaht | Erstarrungsriss | Heißes Crack |
Wärmebeeinflusste Zone | Verflüssigungsriss | |||
Unterhalb der festen Phasenlinie | Bindenaht | Polygonaler Riss | ||
Nahe der Rekristallisationstemperatur T | Wärmebeeinflusste Zone | Hochtemperatur-Kunststoffriss | ||
Nahezu Raumtemperatur | Wärmebeeinflusste Zone | Kalter Riss | ||
Wärmeeinflusszone und Walzschicht des Grundmetalls | Lamellarer Riss | |||
Beim erneuten Anlassen bei hoher Temperatur nach dem Schweißen | Wärmebeeinflusste Zone | Riss wieder aufwärmen | ||
Bei Verwendung von korrosiven Medien | Schweißnähte, Wärmeeinflusszone | Spannungsrisskorrosion |
Risse in Brücken aus hochfestem Stahl und Stahlkonstruktionen im Schiffbau sind in erster Linie Kaltrisse, die 90% aller Risse ausmachen. In petrochemischen Anlagen und Energieanlagen, heiße Risse sind häufiger anzutreffen. Perlitischer hitzebeständiger Stahl ist anfällig für Wiedererwärmungsrisse.
Für die Rissbildung gibt es zwei Hauptgründe:
(1) Die Spannungen und Dehnungen, die sich aus der Einspannung ergeben, sind eine der Hauptursachen für Rissbildung. Für das Auftreten von Rissen ist ein bestimmtes Spannungsniveau erforderlich, und der ungleichmäßige Erwärmungsprozess beim Schweißen kann zu Zugspannungen und Dehnungen in der Verbindung führen, da die gesamte Struktur während des Abkühlungsprozesses beim Schweißen eingespannt wird.
(2) In einem bestimmten Temperaturbereich kommt es aufgrund von Sprödigkeitsfaktoren in bestimmten Teilen der Verbindung zu Rissen unter Zugspannung.
(1) Merkmale von Rissen durch Heißschweißen:
Heiße Risse weisen die folgenden morphologischen Merkmale auf, die sie von anderen Rissen unterscheiden:
① Die meisten Risse öffnen sich an der Schweißnahtoberfläche und haben eine oxidierte Farbe.
② Risse treten häufig an den Verbindungsstellen der Dendriten und in Längsrichtung in der Mitte des Schweißnahtquerschnitts auf.
③ Risse sind typischerweise interkristallin und weisen interkristalline Brucheigenschaften bei hohen Temperaturen auf.
④ Sie treten meist während und nach der Erstarrung auf.
(2) Mechanismus der Bildung:
Bei der Erstarrung SchweißverfahrenWenn ein Eutektikum mit niedrigem Schmelzpunkt vorhanden ist, kann die schnelle Abkühlung beim Schweißen dazu führen, dass die Korngrenze auseinandergezogen wird und sich Risse bilden, wenn das Korn erstarrt ist und die Korngrenze sich noch in einem flüssigen Zustand mit fast null Verformungswiderstand befindet, und die Zugspannung beim Schweißen hoch ist.
(3) Beeinflussende Faktoren:
① Einfluss der chemischen Zusammensetzung der Schweißnaht:
Viele eutektische Kristalle beim Schweißen sind das Ergebnis von schweißmetallurgischen Reaktionen.
Elemente, die ein Eutektikum bilden können, sind Elemente, die die Heißrissbildung fördern.
Elemente, die Körner verfeinern, Verbindungen mit hohem Schmelzpunkt herstellen oder Eutektika mit niedrigem Schmelzpunkt in kugelförmiger oder blockiger Form verteilen können, sind wirksam bei der Verhinderung von Heißrissen.
Tabelle 4-12 Auswirkung von Legierungselemente auf die Tendenz zum Heißriss
die Bildung von Heißrissen ernsthaft beeinträchtigen | Eine geringe Menge hat kaum Auswirkungen, während eine große Menge die Heißrissbildung fördert. | Verringerung der Heißrissneigung der Schweißnaht | Unbestimmt |
Kohlenstoff, Schwefel, Phosphor, Kupfer, Wasserstoff, Nickel, Niob | Silizium (>0,4%) Mangan (>0,8%) Chrom (>0,8%) | TitanZirkonium, Aluminium, seltene Elemente, Mangan (innerhalb von 0,8%) | Stickstoff, Sauerstoff, Arsen |
② Einfluss der Form des Schweißnahtabschnitts:
Bei tiefen und schmalen Schweißnähten kommt es aufgrund der Makroseigerung, die sich in der Mitte der Schweißnaht konzentriert, häufig zur Bildung von Heißrissen. Daher ist es beim automatischen Unterpulverschweißen von dicken Blechen entscheidend, das Verhältnis von Schweißstrom und Lichtbogenspannung so einzustellen, dass der Schweißnahtformkoeffizient größer als 1,3 bis 1,5 ist.
Beim Lichtbogenhandschweißen ist der Schweißbereich klein und die Stromstärke gering, so dass es weniger wahrscheinlich ist, dass tiefe und schmale Schweißnähte entstehen.
③ Einfluss des Schweißverfahrens und der Schweißnahtstruktur:
Die Schweißnahtstruktur und das Schweißverfahren wirken sich direkt auf die Festigkeit der Schweißverbindung aus, was sich in der Schweißzugspannung widerspiegelt. Ihr Einfluss auf Heißrisse wird als mechanischer Faktor betrachtet.
(4) Maßnahmen zur Verhinderung von Heißschweißrissen:
① Die grundlegenden Maßnahmen zur Vermeidung von Heißrissen sind die strenge Kontrolle der chemischen Zusammensetzung der Schweißnaht, die Begrenzung des Gehalts an Kohlenstoff-, Schwefel- und Phosphorverunreinigungen und die Zugabe ausreichender Entschwefelungsmittel zu den Schweißmaterialien.
② Umsetzung von Prozessmaßnahmen wie Vorwärmen vor dem Schweißen, Begleitheizung und Schweißen mit hoher Drahtenergie (um sicherzustellen, dass der Formfaktor der Schweißnaht nicht zu klein ist).
③ Reduzieren Sie die Steifigkeit der Schweißnaht so weit wie möglich, um die inneren Spannungen beim Schweißen zu minimieren.
(1) Merkmale von Kaltrissen:
Kaltrisse sind die am häufigsten auftretenden Schweißfehler beim Schweißen von niedriglegierten hochfesten Stählen, mittellegierten Stählen, mittelkohlenstoffhaltigen Stählen und anderen leicht abgeschreckten Stählen.
① Sie treten nach der Erstarrung des Schweißgutes auf, meist unterhalb der Martensit Transformationstemperatur oder bei Raumtemperatur.
② Sie treten hauptsächlich in der Wärmeeinflusszone und selten in der Schweißzone auf.
③ Sie sind oft verspätet.
(2) Ursache: Die Hauptursache für Kaltrisse ist die kombinierte Wirkung von geringer Plastizität (Härtegefüge) in der Wärmeeinflusszone der Schweißnaht, Wasserstoff in der Schweißnaht und Schweißspannung.
(3) Beeinflussende Faktoren:
① Verhärtungseffekt:
Wenn leicht abgeschreckter Stahl geschweißt wird, bildet sich in der überhitzten Zone ein grobes Martensitgefüge, das die Plastizität des Metalls in der Wärmeeinflusszone verringert und seine Sprödigkeit erhöht. Dies macht es anfällig für Risse unter hoher Schweißzugspannung.
② Die Rolle des Wasserstoffs:
Durch Wasserstoff verursachte Kaltrisse weisen die Merkmale eines verzögerten Bruchs auf, von der Latenzzeit über die Einleitung und Ausbreitung bis hin zur Rissbildung. Die Länge der Verzögerungszeit hängt von der Wasserstoffkonzentration und dem Spannungsniveau der Schweißnaht ab.
③ Einfluss der Schweißspannung:
Kaltrisse treten mit größerer Wahrscheinlichkeit auf, wenn die Schweißspannung eine Zugspannung ist und gleichzeitig mit Wasserstoffausscheidung und Materialverfestigung auftritt.
Das Schweißen von dicken Blechen ist anfälliger für Kaltrisse an der Wurzel. Dies ist auf die Steifigkeit des dicken Blechs und die schnelle Abkühlung zurückzuführen, die zur Bildung einer Abschreckstruktur führt und hohe Schweißspannungen zur Folge hat.
(1) Merkmale von Wiedererwärmungsrissen
① Wiedererwärmungsrisse treten im Temperaturbereich von 540-930°C nach einer Spannungsarmglühung nach dem Schweißen auf.
② Die Risse breiten sich entlang der Korngrenzen in der Grobkornzone der Wärmeeinflusszone aus.
③ Intergranulare Risse mit einer verzweigten Form hören auf, wenn sie den Feinkornbereich der Schweißnaht oder des Grundmetalls erreichen.
(2) Mechanismus der Rissbildung bei Wiedererwärmung
Nach der Wärmebehandlung zum Spannungsabbau nach dem Schweißen und dem Wiedererwärmen werden die Karbide der Legierung dispergiert und auf den Versetzungslinien nach der Wärmekonservierung bei 550-700 °C ausgeschieden, was die intragranulare Struktur stärkt.
Gleichzeitig ist die Korngrenzenfestigkeit im Grobkornbereich gering und die Plastizität schlecht.
Während des Wiedererwärmungsprozesses werden Eigenspannungen freigesetzt, und die Festigkeit der Korngrenze ist schwächer als die des Korns, was zu Rissen in der Korngrenze führt.
(3) Beeinflussende Faktoren
Es gibt mehrere Faktoren, die sich auf Risse bei der Wiedererwärmung auswirken:
Dazu gehören die chemische Zusammensetzung, der Zustand der Einspannung und die Schweißspezifikationen, Schweißdraht Festigkeit, Spannungsentlastung und Betriebstemperatur des Grundmetalls.
Die chemische Zusammensetzung beeinflusst hauptsächlich die Plastizität der Korngrenzen in der Wärmeeinflusszone.
② Der Zustand der Einspannung und die Schweißspezifikationen beeinflussen die Schweißeigenspannung.
Die Spezifikationen der Spannungsarmglühung und die Betriebstemperatur wirken sich hauptsächlich auf die plastische Verformung und den Grad der Ausscheidung von Legierungskarbid durch Wiedererwärmung aus.
Daher sind die plastische Verformungsfähigkeit der grobkörnigen Zone in der Wärmeeinflusszone, die Schweißeigenspannung und die durch die Wiedererwärmung verursachte plastische Dehnung die drei grundlegenden Faktoren, die die Wiedererwärmungsrisse beeinflussen.
(4) Maßnahmen zur Verhinderung von Rissen bei der Wiederaufheizung
① Die wichtigste Maßnahme ist die Auswahl eines unedlen Metalls mit geringer Empfindlichkeit gegenüber Wiedererwärmungsrissen.
② Ergreifen Sie alle notwendigen Maßnahmen, um die Restspannung zu verringern.
③ Vermeiden Sie die Kombination von Schweißeigenspannungen mit anderen Spannungen, wie z. B. strukturellen Spannungen und thermischen Spannungen beim Wiedererwärmen.
④ Die Verwendung von Schweißwerkstoffen mit geringem Anpassungsvermögen hilft, Verformungen zu absorbieren.
⑤ Unter der Bedingung, dass der Spannungsabbau gewährleistet ist, sollten Sie die niedrigstmögliche Wiedererwärmungstemperatur und die kürzeste Haltezeit verwenden.
Wenn möglich, ersetzen Sie die Nacherwärmung durch eine Nacherwärmung, die etwas niedriger ist als die Vorwärmtemperatur für bessere Ergebnisse.
(1) Merkmale des lamellaren Tränens
① Während der schnellen Abkühlung der Schweißnaht entstehen im Stahlblech Risse, die parallel zur Walzfläche des Grundmetalls verlaufen und auf die Schweißzugspannung in Richtung der Blechdicke zurückzuführen sind. Diese Risse werden als Lamellenrisse bezeichnet und treten häufig bei T- und K-förmigen Dickblechverbindungen auf.
Lamellenriss ist eine Rissart, die bei Raumtemperatur auftritt, typischerweise nach Abkühlung auf unter 150 °C oder Raumtemperatur nach dem Schweißen. Wenn jedoch die strukturelle Beanspruchung sehr hoch ist und der Stahl sehr empfindlich gegenüber Lamellenriss ist, kann er auch bei Temperaturen zwischen 300 und 250 °C auftreten.
(a) Typische Position eines Lamellenrisses im T-Gelenk
(b) Lamellenriss in der Fallrohrverbindung der Kesseltrommel
(2) Hauptfaktoren, die einen Lamellenriss verursachen
① Einfluss von Einschlüssen
Einschlüsse sind die Hauptursache für die Anisotropie des Stahls und die Ursache für das Reißen von Lamellen.
② Einfluss der Eigenschaften des Grundmetalls
Die Plastizität und Zähigkeit der Metallmatrix selbst haben einen erheblichen Einfluss auf das Lamellenreißen. Geringe Plastizität und Zähigkeit führen zu einer geringen Beständigkeit gegen Lamellenriss.
③ Einfluss der Zwangsspannung
Alle Schweißrisse entstehen unter der Einwirkung von Zugspannungen, und Lamellenrisse sind keine Ausnahme. Lamellenrisse entstehen nur dann, wenn Eck- und T-Verbindungen dazu neigen, große zweiseitige Zwangsspannungen zu bilden.
(3) Vorsichtsmaßnahmen bei Lamellenrissen
Lamellenrisse lassen sich nur schwer reparieren, daher ist die Vermeidung dieses Defekts das wichtigste Ziel.
① Wenn die Schweißverbindung zu Lamellenrissen neigt, ist die Lamellenrissempfindlichkeit des verwendeten Stahlblechs zu bewerten und ein Stahlblech mit geringer Empfindlichkeit zu wählen.
② Wählen Sie einen vernünftigen Rillentyp, um die Schmelzlinie der Schweißnaht so eng wie möglich an der Stahlplatte auszurichten.
③ Bei Stahlsorten, die empfindlich auf Lamellenrisse reagieren, sollten nach Möglichkeit Schweißwerkstoffe mit geringerer Festigkeit, besserer Plastizität und Zähigkeit verwendet werden, um die Spannungen in der Dickenrichtung des Stahlblechs zu verringern.
④ Bei Stahlsorten mit hoher Empfindlichkeit gegenüber Lamellenriss sind mehrere Lagen niedrigfesten Schweißguts auf der Blechoberfläche an der Schweißfuge.
Die Anordnung der Schweißnähte in einer Schweißkonstruktion hat einen erheblichen Einfluss auf die Qualität und die Effizienz der Schweißnähte.
Die Schweißanordnung muss so beschaffen sein, dass die Schweißer ungehindert arbeiten können und die Schweißgeräte normal funktionieren.
Achten Sie beim Unterpulverschweißen auf eine einfache Lagerung der Schweißflussmittel.
Zum Punktschweißen und Nahtschweißensollte die Leichtigkeit des Einsetzens der Elektroden in Betracht gezogen werden.
Bei Bauteilen mit großen und komplexen Spannungen sollten Schweißnähte nicht an Stellen mit maximaler Spannung und Spannungskonzentration angebracht werden.
Zum Beispiel sollte die Verbindungsnaht für einen geschweißten Stahlträger mit großer Spannweite nicht in der Mitte des Trägers liegen, sondern eine zusätzliche Schweißnaht sollte hinzugefügt werden.
Dichte oder kreuzweise Schweißnähte können zu Überhitzung führen, die Wärmeeinflusszone vergrößern und die Struktur schwächen.
In der Regel sollte der Abstand zwischen zwei Schweißnähten mehr als das Dreifache der Blechdicke und nicht weniger als 100 mm betragen.
Wenn vor dem Schweißen eine Bearbeitung erforderlich ist, sollte die Schweißstelle so weit wie möglich von der bearbeiteten Oberfläche entfernt sein.
Bei Oberflächen mit hohen Bearbeitungsanforderungen ist es am besten, Schweißnähte zu vermeiden.
Um ein Schmelzen während des Schweißens zu verhindern, sollten am Ende der Schweißnaht keine scharfen Winkel vorhanden sein. Der Übergang zwischen zwei Schweißnähte sollte glatt sein, um Spannungskonzentrationen zu vermeiden.
GB/T 19804-2005/ISO 13920:1996
(1) Allgemeine Abmessungstoleranz und geometrische Toleranz Angebot an geschweißten Strukturen
Tabelle 1 Lineare Maßtoleranz Einheit: mm
Bereich der Nenngröße l |
Toleranzklasse |
A |
B |
C |
D | |
2~30 |
Toleranz t |
± 1 | ||||
>30~120 |
± 1 |
± 2 |
± 3 |
± 4 | ||
>120~400 |
± 1 |
± 2 |
± 4 |
± 7 | ||
>400~1000 |
± 2 |
± 3 |
± 9 | |||
± 6 | ||||||
>1000~2000 |
±3 |
±4 |
±8 |
±12 | ||
>2000~4000 |
±4 |
±6 |
±11 |
±16 | ||
>4000-~8000 |
±5 |
±8 |
±14 |
±21 | ||
>8000~12000 |
±6 |
±10 |
±18 |
±27 | ||
>12000~16000 |
±7 |
±12 |
±21 |
±32 | ||
>16000~20000 |
±8 |
±14 |
±24 |
±36 | ||
>20000 |
±9 |
±16 |
±27 |
±40 |
(2) Toleranz des Winkelmaßes
Die kürzere Seite des Winkels sollte als Bezugskante verwendet werden, und seine Länge kann bis zu einem bestimmten Bezugspunkt verlängert werden. In diesem Fall sollte der Bezugspunkt auf der Zeichnung markiert werden. Die Toleranzen sind der Tabelle 2 zu entnehmen. Die Abbildungen 1 bis 5 enthalten konkrete Beispiele.
Tabelle 2 Toleranz der Winkelmaße
Toleranzklasse | Nennmaß (Werkstücklänge oder kurze Seitenlänge) Bereich/mm | ||
0~400 | >400~1000 | >1000 | |
Winkeltoleranz △ a/(°) | |||
A | ± 20 | Gelehrte 15 | ±10 |
B | ± 45 | ±30 | ± 20 |
C | ± 1 ° | ± 45 | ± 30 |
D | ±130 | Schi 115 | Boden 1 |
Längentoleranz t/(mm/m) | |||
A | Boden 6 | Boden 4,5 | ±3 |
B | Gelehrte 13 | ±9 | Gelehrte 6 |
C | Gelehrter 18 | Gelehrte 13 | ±9 |
D | Gelehrte 26 | Boden 22 | Boden 18 |
(3) Geradheit, Ebenheit und Parallelität
Die GeradheitDie in Tabelle 3 aufgeführten Ebenheits- und Parallelitätstoleranzen gelten für alle Abmessungen von Schweißteilen, geschweißten Baugruppen oder geschweißten Bauteilen sowie für die in den Zeichnungen angegebenen Maße. Koaxialitäts- und Symmetrietoleranzen sind nicht angegeben. Wenn diese Toleranzen für die Produktion erforderlich sind, sollten sie gemäß GB/T1182 auf der Zeichnung vermerkt werden.
Tabelle 3 Toleranzen für Geradheit, Ebenheit und Parallelität Einheit: mm
Öffentlicher Dienst | E | F | G | H | ||
Bereich des Nennmaßes l (entspricht der längeren Seite der Oberfläche) | >30~120 | Toleranz t | ± 0.5 | ±1 | ± 1.5 | ± 2.5 |
>120~400 | ±1 | ± 1.5 | ±3 | ±5 | ||
>400~1000 | ±1.5 | ±3 | ± 5.5 | ±9 | ||
>1000~-2000 | ±2 | ± 4.5 | ±9 | ±14 | ||
>2000~4000 | ±3 | ±6 | ±11 | ±18 | ||
>4000~8000 | ±4 | ±8 | ±16 | ±26 | ||
>8000~-12000 | ±5 | ±10 | ± 20 | ±32 | ||
>12000~16000 | ±6 | ±12 | ±22 | ±36 | ||
>16000~20000 | ±7 | ±14 | ± 25 | ±40 | ||
>20000 | ±8 | ±16 | ± 25 | ±40 |
1.1.1 Bleche Dicke und Qualität Die Dicke und Qualität des Blechs muss der nationalen Norm entsprechen, und der Bericht über die Leistungsprüfung und das Zertifikat des Herstellers für das verwendete Blech müssen vorgelegt werden.
1.1.2 Erscheinungsbild des Materials Das Material muss eben, frei von Rost, Rissen und Verformungen sein.
1.1.3 Abmessungen Die Abmessungen müssen mit den Zeichnungen oder den technischen Anforderungen übereinstimmen. Wenn sie nicht von unserem Unternehmen bereitgestellt werden, müssen sie den geltenden nationalen Normen entsprechen.
1.2.1 Konsistenz des Kunststoffpulvers Die gesamte Charge des Kunststoffpulvers muss eine gute Konsistenz aufweisen, mit einem Werkszertifikat und einem Prüfbericht, der die Pulvernummer, die Farbnummer und verschiedene Prüfparameter enthält.
1.2.2 Testanforderungen Das Kunststoffpulver muss nach dem Test die Produktanforderungen erfüllen, einschließlich Farbe, Glanz, Nivellierung, Haftung usw.
1.3.1 Aussehen Die Oberfläche muss frei von Stickereien und Graten sein, und das Aussehen der gesamten Charge der eingehenden Materialien muss einheitlich sein.
1.3.2 Größe Die Größe muss den Anforderungen der Zeichnungen und der nationalen Normen entsprechen.
1.3.3 Leistung Die Leistung muss den Produktanforderungen nach Probemontage und Betriebsleistung entsprechen.
Alle scharfen Ecken, Kanten und rauen Oberflächen, die Schäden verursachen können, müssen entgratet werden.
Die durch das Stanzen entstandenen Grate dürfen keine erkennbaren Vorsprünge, Vertiefungen, Rauheiten, Kratzer, Rost oder andere Unvollkommenheiten auf den freiliegenden und sichtbaren Oberflächen der Türverkleidungen und Platten aufweisen.
Grate: Nach dem Stanzen darf die Grathöhe 5% der Blechdicke (t) nicht überschreiten.
Kratzer und Messerspuren: Das Produkt gilt als qualifiziert, wenn es bei Berührung mit der Hand keine sichtbaren Kratzer aufweist und die Kratzer nicht größer als 0,1 sind.
Die Spezifikationen für die Oberflächentoleranz sind in Tabelle I aufgeführt.
Beigefügte Tabelle 1. Anforderungen an die Ebenheitstoleranz
Abmessungen der Oberfläche (mm) | Größe der Verformung (mm) |
Unten 3 | Weniger als ±0,2 |
Mehr als 3 aber weniger als 30 | Weniger als ±0,3 |
Mehr als 30, aber weniger als 400 | Weniger als ±0,5 |
Mehr als 400, aber weniger als 1000 | Weniger als ±1,0 |
Mehr als 1000 aber weniger als 2000 | Weniger als ±1,5 |
Mehr als 2000 aber weniger als 4000 | Weniger als ± 2,0 |
2.2.1 Grat: Die Höhe des extrudierten Grats nach dem Biegen darf 10% der Blechdicke (t) nicht überschreiten. Wenn nicht anders angegeben, muss der Biegeradius muss R1 sein.
2.2.2 Faltenbildung: Das Produkt kann sichtbare Falten aufweisen, die jedoch bei Berührung nicht spürbar sein sollten. Das Produkt kann mit einer Referenzprobe verglichen werden.
2.2.3 Normen für die Biegeverformung: Die Normen für die Biegeverformung müssen mit den Tabellen II, III und IV übereinstimmen.
2.2.4 Biegerichtung und -größe: Die Richtung und Größe der Biegung muss mit den Zeichnungen übereinstimmen.
Beigefügte Tabelle 2: Anforderungen an die Diagonaltoleranz
Diagonale Abmessung (mm) | Maßunterschied der Diagonalen (mm) |
Weniger als 300 | Weniger als ±0,3 |
Mehr als 300 aber weniger als 600 | Weniger als ±0,6 |
Mehr als 600 aber weniger als 900 | Weniger als ±0,9 |
Mehr als 900 aber weniger als 1200 | Weniger als ±1,2 |
Mehr als 1200 aber weniger als 1500 | Weniger als ± 1,5 |
Mehr als 1500 aber weniger als 1800 | Weniger als ± 1,8 |
Mehr als 1800 aber weniger als 2100 | Unter±2,1 |
Mehr als 2100 aber weniger als 2400 | Unter±2,4 |
Über 2400 bis 2700 | Weniger als ±2,7 |
Der Winkel muss entsprechend den Angaben in den Zeichnungen geprüft und gemessen werden. Die Toleranz für den Winkel ist in Tabelle III angegeben.
Grenzabweichungswert des Winkelmaßes
Grenzabweichungswert des Winkelmaßes | |||||
Toleranzklasse | Grundlegende Größensegmentierung | ||||
0-10 | >10-50 | >50-120 | >120-400 | >400 | |
Präzision f | ± 1 ° | ±30' | +20' | ±10' | ±5' |
Mittel m | |||||
Grob c | +1°30 | +1° | +30 | +15′ | +10' |
Gröbste v | +3° | ±2° | +1° | +30' | +20' |
Die Abmessungen sind gemäß den Zeichnungsanforderungen zu prüfen, und die Maßtoleranz ist in Tabelle IV angegeben.
Beigefügte Tabelle 4: Anforderungen an die Maßtoleranz
Standardgröße | Abmessungstoleranz (mm) |
Unten 3 | ±0.2 |
Mehr als 3 aber weniger als 30 | ±0.3 |
Mehr als 30, aber weniger als 400 | ± 0.5 |
Mehr als 400, aber weniger als 1000 | ±1.0 |
Mehr als 1000 aber weniger als 2000 | ± 1.5 |
Mehr als 2000 aber weniger als 4000 | ± 2.0 |
2.5.1 Die Schweißnähte müssen fest und gleichmäßig sein und dürfen keine Mängel wie unzureichende Schweißung, Risse oder unvollständige Durchdringung aufweisen, Einschweißen, Kerben oder Hinterschneidungen.
Die Länge und Höhe der Schweißnähte darf 10% der erforderlichen Länge und Höhe nicht überschreiten.
2.5.2 Anforderungen an die Schweißpunkte: Die Länge jedes Schweißpunktes muss zwischen 8 mm und 12 mm liegen, mit einem Abstand von 200 ± 20 mm zwischen zwei Schweißpunkten. Der V-Schweißpunkt muss symmetrisch sein und eine einheitliche obere und untere Position haben.
Wenn die Verarbeitungszeichnungen besondere Anforderungen an die Schweißpunkte enthalten, haben diese Vorrang.
2.5.3 Der Abstand zwischen den Schweißpunkten muss weniger als 50 mm betragen, der Schweißpunktdurchmesser muss weniger als φ5 betragen, und die Schweißpunkte müssen gleichmäßig verteilt sein. Die Eindringtiefe an den Schweißpunkten darf 15% der tatsächlichen Blechdicke nicht überschreiten, und nach dem Schweißen sollten keine erkennbaren Schweißnarben zurückbleiben.
2.5.4 Nach dem Schweißen können keine anderen, nicht schweißenden Teile durch Schweißschlacke oder Lichtbogen beschädigt werden, und alle Oberflächenschweißen Schlacke und Spritzer müssen entfernt werden.
2.5.5 Nach dem Schweißen muss die Außenfläche der Teile frei von Schlackeneinschlüssen, Luftlöchern, Überlappungen, Ausbuchtungen, Vertiefungen oder anderen Mängeln sein. Die Mängel an der Innenfläche dürfen nicht auffallen und die Montage nicht beeinträchtigen.
Auch wichtige Teile wie Türverkleidungen und Paneele müssen nach dem Schweißen entlastet werden, um eine Verformung des Werkstücks zu verhindern.
2.5.6 Die Außenfläche der Schweißteile muss durch Schleifen geglättet werden. Bei pulvergespritzten und galvanisch beschichteten Teilen muss die Rauheit nach dem Schleifen Ra3,2-6,3 betragen, bei lackierten Teilen Ra6,3-12,5.
3.1.1 Vor dem Sprühen muss die Werkstückoberfläche entfettet werden, entrostet, phosphatiert und gereinigt.
3.1.2 Die Werkstückoberfläche darf keine Wasserflecken oder Reste von Reinigungslösung aufweisen.
3.1.3 Die Werkstückoberfläche darf keine Ölflecken, Staub, Fasern oder andere unerwünschte Erscheinungen aufweisen, die die Qualität oder Haftung der gespritzten Oberfläche beeinträchtigen könnten.
3.1.4 Die Farbe muss mit der Musterplatte übereinstimmen (unter natürlichem Licht oder einer 60-Watt-Leuchtstofflampe für normale Sehkraft sollte kein offensichtlicher Farbunterschied zu erkennen sein), und es darf keine Farbunterschiede bei der gleichen Charge von Produkten geben (Anmerkung: Farbunterschiede umfassen Farbe und Glanz).
3.1.5 Die Beschichtungsoberfläche muss glatt, eben und gleichmäßig sein und darf keine der folgenden Mängel aufweisen:
Nicht trocknend und rückseitig klebend: Die Oberfläche scheint trocken zu sein, ist aber in Wirklichkeit nicht vollständig trocken, mit (oder anfällig für) Narben auf der Oberfläche und Stoffflusen;
Absacken: An der Oberfläche befinden sich flüssige Ausstülpungen, die oben wulstförmig sind;
Partikel: Die Oberfläche hat ein sandähnliches Aussehen und fühlt sich blockiert an;
Orangenschale: Die Oberfläche erscheint uneben und unregelmäßig wie die Schale einer Orange;
Bodenleckage: Die Oberfläche ist transparent und die Farbe des Substrats ist sichtbar;
Pits: kleine Löcher (Pits) auf der Oberfläche aufgrund von Schrumpfung, auch Pinholes genannt;
Mit Muster: Die Oberflächenfarbe variiert in der Tiefe und zeigt Muster;
Falten: Die Oberfläche ist örtlich aufgehäuft und erhaben und weist Falten auf (außer bei Faltenpulver);
Einschluss: Es befinden sich Fremdkörper in der Beschichtung;
Mechanische Schäden: Kratzer, Abschürfungen und Druckstellen, die durch äußere Kräfte verursacht werden.
3.1.6 Normen für die Klassifizierung der Oberflächenbeschaffenheit:
Oberfläche der Güteklasse A: die äußere Oberfläche, die nach der Montage häufig zu sehen ist, wie z. B. die Schrankwand, die Schranktür, die Seiten um den Schrank herum, die obere Oberfläche, die für normale Menschen sichtbar ist, und die untere Oberfläche, die ohne Bücken sichtbar ist.
Oberfläche der Güteklasse B: die Oberfläche, die selten zu sehen ist, aber unter bestimmten Bedingungen zu sehen ist, wie z. B. das innere Zubehör, die Verstärkungsrippen und die Innenseite des Tors, die nach dem Öffnen zu sehen ist.
Oberfläche der Güteklasse C: die Oberfläche, die im Allgemeinen nicht oder nur bei der Montage zu sehen ist, wie z. B. die Kontaktfläche zwischen dem Wagen und der Führungsschiene im Schrank.
3.1.7 Inspektionsbedingungen:
Anforderungen an die Lichtquelle: Arktisches Tageslicht oder hocheffiziente Leuchtstofflampen für Innenräume mit zwei Lichtquellen (Beleuchtungsstärke von 1000 Lumen).
Abstand der Sichtprüfung: 300 mm für die Oberfläche der Klasse A, 500 mm für die Oberfläche der Klasse B und 1000 mm für die Oberfläche der Klasse C.
3.1.8 Inspektionsstandards:
Die Oberfläche des Produkts muss nach der Norm der Lichtquelle unterschieden werden.
Der Beschichtungsfilm aller Oberflächen darf keine Freilegung des Grundmaterials, kein Abblättern oder andere Mängel aufweisen, und alle Oberflächen dürfen keine Kratzer, Blasen, Nadellöcher, Pulveransammlungen oder andere unerwünschte Erscheinungen aufweisen.
Farbe und Muster: Der Hersteller muss je nach Bedarf Muster anfertigen, die von beiden Parteien bestätigt werden müssen.
Die Abnahme muss entsprechend dem Muster erfolgen, ohne offensichtliche Farbunterschiede (nicht mehr als 3 Grad), und die Maserung muss mit dem Muster übereinstimmen.
Die Inspektion muss auf Augenhöhe erfolgen, wobei mit einer Geschwindigkeit von 3m/min gescannt wird.
3.1.9 Erscheinungsbild-Mangel-Standard:
Siehe beigefügte Tabelle 5 für die Bestimmungskriterien.
Beigefügte Tabelle 5: Beurteilungskriterien für Oberflächenmängel
Laufende Nummer | Art des Defekts | Spezifischer Wert (mm) | Grenzfläche (mm2) | Inspektionswerkzeuge | ||||||||
Weniger als 100 | 100-300 | Über 300 | ||||||||||
A | B | C | A | B | C | AB | C | |||||
1 | Abrasion, Kratzer, Kratzer | 10 in der Länge und weniger als 0,1 in der Breite | 0 | 2 | 2 | 0 | 3 | 1 | 4 | 4 | Nonius-Band | |
Länge: 10, Breite: weniger als 0,15 | 0 | 1 | 1 | 0 | 2 | 21 | 3 | 3 | ||||
15 in der Länge und weniger als 0,1 in der Breite | 0 | 0 | 0 | 0 | 1 | 1 | 1 | 2 | 2 | |||
Mehr als 0,15 breit | 0 | 0 | 0 | 0 | 0 | 0 | 1 | 1 | ||||
2 | Fremdkörper | Unten 1 | 1 | 2 | 3 | 2 | 3 | 4 | 3 | 4 | 5 | . |
Weniger als 1,5 | 0 | 1 | 2 | 1 | 2 | 3 | 2 | 3 | 4 | |||
Unten 2 | 0 | 0 | 1 | 0 | 1 | 2 | 0 | 2 | 3 | |||
3 | Schrumpfungshohlraum | Unterhalb von φ0,3 | 1 | 1 | 2 | 2 | 2 | 3 | 3 | 3 | 4 | . |
Weniger als φ0,5 | 0 | 0 | 1 | 1 | 1 | 2 | 2 | 2 | 3 | |||
Über φ0,5 | 0 | 0 | 0 | 0 | 0 | 1 | 0 | 0 | 2 | |||
4 | Schwarzer Punkt Weißer Punkt Andere Farbpunkte | Weniger als 0,3 | 1 | 2 | 2 | 2 | 3 | 3 | 3 | 4 | 4 | . |
5. | Biege-Eindruck | 3 in der Länge und weniger als 0,2 in der Breite. | 2 | 3 | 3 | 3 | 4 | 4 | 4 | 5. | 5. | . |
Länge: 5, Breite: weniger als 0,2 | 1 | 2 | 2 | 2 | 3 | 3 | 3 | 4 | 4 | |||
Mehr als 5 lang | 0 | 1 | 1 | 1 | 2 | 2 | 2 | 3 | 3 | |||
Mehr als 0,2 breit. | 0 | 0 | 1 | 1 | 0 | 2 | 0 | 2 | 3 | |||
6. | Farbe und Glanz | - | Zusätzlich zu den Ober- und Untergrenzen der angegebenen Farbpalette sind keine Mischfarben und Farbverläufe erlaubt | Visuelle Kontrolle | ||||||||
7. | Glanz | - | Es darf keine Unebenheiten geben, die im Entwurf angegeben sind. | Visuelle Kontrolle | ||||||||
8. | Ölflecken und Flecken | - | Nein | Visuelle Kontrolle | ||||||||
Bemerkungen: Die Werte in den fettgedruckten schwarzen Kästen sind die Bewertungskriterien. Zum Beispiel bedeutet "2", dass unter den angegebenen Bedingungen nicht mehr als 2 Punkte erlaubt sind: |
Einheit: µm
Projekt | Outdoor-Pulver | Pulver für drinnen | Malerei | Prüfverfahren |
Dicke der Produktoberfläche | 60~120 | 50~100 | 40~70 | Schichtdickenmessgerät |
Innere Dicke des Produkts | 60~100 | 50~80 | 30~60 | Schichtdickenmessgerät |
3.3.1 Herstellung der Sprühfarbplatte
A. Beim Backen sollten für jeden Ofen zwei Farbplatten erstellt werden, um einen Leistungstest durchzuführen. Das verwendete Metallplättchen sollte aus demselben Material wie das Produkt bestehen, eine Größe von 80 × 120 haben und dem Produkt unter normalen Bedingungen hinzugefügt werden. Die Pulvernummer, die Aushärtungsbedingungen, das Datum und die Uhrzeit sollten deutlich gekennzeichnet und vom Qualitätsingenieur (QE) unterzeichnet werden.
Nach der Bestätigung sollten die Nummer, der Name und die Registrierung aufgezeichnet und verwaltet werden. Ein Schild sollte für Prüfzwecke und das andere für die Archivierung aufbewahrt werden.
B. Die Gültigkeitsdauer der im Pulversprühverfahren verwendeten Farbplatte beträgt zwei Jahre, und sie sollte bei Raumtemperatur (70 ± 15%) in einer lichtgeschützten Umgebung gelagert werden. Die Lagerungsumgebung sollte außerdem eine konstante Temperatur und Luftfeuchtigkeit aufweisen.
3.3.2 Glanz- und Farberkennungsmethode
Glanz: Der Glanz sollte mit einem Glanzmessgerät mit einem Einfallswinkel von 60° und einer Fehlertoleranz von ± 5% bewertet werden. Wenn die Ergebnisse diese Kriterien erfüllen, gilt das Produkt als qualifiziert.
Farbe: Die Farbe des Produkts muss mit der Konstruktionszeichnung übereinstimmen oder darf sich nicht wesentlich von der Standardfarbplatte unterscheiden.
3.4.1 Baige-Testverfahren
Nach dem Sprühvorgang wird eine Farbplatte aus dem Ofen entnommen und 11 Beschichtungsschichten in vertikaler und horizontaler Richtung mit einem Abstand von 1 mm auf die Oberfläche geritzt. Das Einritzen sollte mit angemessener Stärke erfolgen, so dass der Kratzer das Substrat nicht erreicht.
Anschließend wird die Beschichtungsfläche in 100 Quadrate unterteilt und mit einem starken transparenten Klebstoff in einem Winkel von 45 Grad befestigt. Der Klebstoff sollte dann plötzlich entfernt werden. Zu diesem Zeitpunkt sollte der Inhalt jedes Quadrats daraufhin überprüft werden, ob er heruntergefallen ist.
Jedes Raster steht für 1 Prozent, und der Akzeptanzstandard ist Stufe 5, was bedeutet, dass die Anzahl der Quadrate mit fallendem Gehalt 5 nicht überschreiten sollte.
3.4.2 Bewertungsmethode
Stufe 0: An allen Kreuzungen sollte es keine Ablösung geben.
Stufe 1: Weniger als 5% des Inhalts an Kreuzungen sollten abgefallen sein.
Stufe 2: Zwischen 5% und 15% des Inhalts an den Kreuzungen sollten abgefallen sein.
Stufe 3: Zwischen 15% und 25% des Inhalts an den Kreuzungen sollten abgefallen sein.
Stufe 4: Zwischen 25% und 35% des Inhalts an den Kreuzungen sollten abgefallen sein.
Stufe 5: Mehr als 35% des Inhalts an den Kreuzungen sollten abgefallen sein.
3.4.3 Beurteilungsmethode
Bei einer Schichtdicke von weniger als 40 μm sollte die Seitenlänge jedes Quadrats 1 mm nicht überschreiten und muss den Anforderungen der Güteklasse 2 entsprechen.
Wenn die Schichtdicke zwischen 40μm und 90μm liegt, sollte die Seitenlänge jedes Quadrats zwischen 1mm und 2mm betragen und muss den Anforderungen der Güteklasse 3 entsprechen.
Wenn die Schichtdicke zwischen 90μm und 120μm liegt, sollte die Seitenlänge jedes Quadrats 2mm betragen und muss den Anforderungen der Güteklasse 4 entsprechen.
Wenn die Schichtdicke 120μm überschreitet, kann die Haftung verringert werden. Im Allgemeinen ist es vorzuziehen, dass die Beschichtungsdicke 120μm nicht überschreitet.
Als vorläufiger Standard gilt, dass das Produkt als unqualifiziert gilt, wenn es ein komplettes Quadrat mit fallendem Inhalt aufweist.
Nach dem Sprühvorgang sollte eine Ofenfarbplatte genommen und um 180 Grad gebogen werden, so dass der innere Biegewinkel gleich der Dicke ist (r=t). Alternativ kann die Farbplatte auch einmal um 90 Grad gebogen werden, wobei die Beschichtung nicht abfallen sollte.
Die Beschichtungsoberfläche sollte mit einem weißen, in Alkohol getränkten Baumwolltuch 10 Mal abgewischt werden (ohne übermäßigen Druck). Nach dem Abwischen sollte keine sichtbare Beschichtung mehr auf dem Baumwolltuch zu sehen sein, die abgefallen ist. Sobald der Alkohol vollständig verdunstet ist, sollte kein Unterschied in Farbe oder Glanz zwischen der abgewischten und der nicht abgewischten Fläche mehr zu erkennen sein.
Mit dem Prüfgerät sollte ein 500 g schwerer Hammer aus einer Höhe von 500 mm frei fallen gelassen werden. Die Bewertungskriterien lauten wie folgt: Nach dem Aufprall eines Viertels des Stempels auf die Vorderseite sollten keine Risse oder Filme auf der Oberflächenbeschichtung zu sehen sein.
Mit einem angespitzten 2H-Bleistift wird ein 45-Grad-Winkel mit der Filmoberfläche gebildet und entlang eines Lineals 15-30 mm weit vorgeschoben. Die Folienoberfläche sollte dann überprüft werden, nachdem die entstandene Markierung mit einem Gummi abgewischt wurde. Das Produkt gilt als geeignet, wenn kein Substrat freigelegt ist.