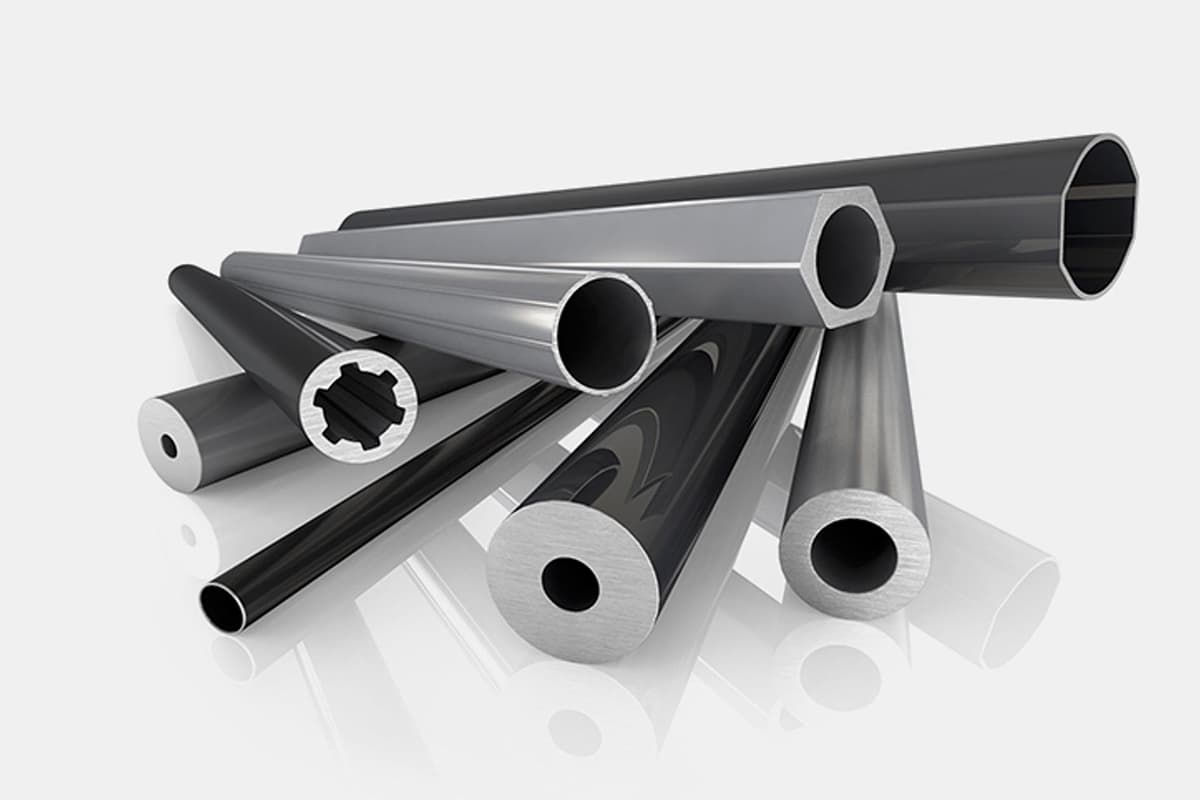
Have you ever wondered why some steel structures last for decades without rusting? This article unveils the secrets behind alloy steel, an iron-carbon mix with added elements that grant it remarkable properties like high strength and corrosion resistance. Learn how these elements transform ordinary steel into a material that can withstand extreme conditions.
Alloy steel is a type of iron-carbon alloy that contains other alloying elements besides iron and carbon.
By adding one or more appropriate alloying elements to ordinary carbon steel and adopting appropriate processing techniques, it is possible to obtain special properties such as high strength, toughness, wear resistance, corrosion resistance, low-temperature resistance, high-temperature resistance, and non-magnetism, depending on the added elements and processing methods.
Corrosion
Corrosion, which also includes the combined effects of the aforementioned factors and mechanical or biological factors.
Some physical phenomena, such as the physical dissolution of metallic materials in certain liquid metals, can also be classified as metal corrosion.
Generally speaking, rust refers specifically to steel and iron-based alloys, which under the action of oxygen and water, form mainly rust products composed of hydrated iron oxide.
Non-ferrous metals and their alloys can corrode without rusting, but instead form similar corrosion products to rust, such as copper patina on the surface of copper and copper alloys, occasionally referred to as copper rust.
Rust or metal rusting
Metal rusting is a chemical or electrochemical reaction that occurs when metals come into contact with their surrounding media, resulting in the destruction of the metal.
The impact of major alloying elements on the performance of steel.
Explanation of the effects of major alloying elements on the performance of steel in Table 1-38.
Element name. | Primary impact on performance. |
Al | The main function is to refine grains and deoxidize. In nitriding steels, it can promote the formation of nitrided layers. When present in high quantities, it can improve high-temperature oxidation resistance and resistance to H2S gas corrosion. It has a strong solid solution strengthening effect, improves the heat strength of heat-resistant alloys, and promotes graphitization tendency. |
B | Trace amounts of boron can improve the hardenability of steel. However, as the carbon content in the steel increases, the improvement in hardenability gradually weakens and eventually disappears. |
C | As the content increases, the hardness and strength of the steel also increase. However, the plasticity and toughness decrease accordingly. |
C0 | It has a solid solution strengthening effect, which gives the steel red hardness and improves its high-temperature performance, oxidation resistance, and corrosion resistance. It is an important alloying element in high-temperature alloys and super-hard high-speed steels. It can also increase the Ms point of the steel and reduce its hardenability. |
Cr | It improves the hardenability of steel and has a secondary hardening effect, increasing the wear resistance of high carbon steel. When the content exceeds 12%, it gives the steel excellent high-temperature oxidation resistance and resistance to oxidative media corrosion, improving the heat strength of the steel. It is the main alloying element in stainless acid-resistant steels and heat-resistant steels. However, when the content is too high, it can lead to brittleness. |
Cu | When present in low quantities, its function is similar to that of nickel. However, when the content is higher, it can be detrimental to hot deformation processing. For example, if the content exceeds 0.30%, it can lead to high-temperature copper brittleness during hot deformation processing. When the content is higher than 0.75%, age hardening can occur after solid solution treatment and aging. In low-alloy steels, especially when present with phosphorus, it can improve the steel’s resistance to atmospheric corrosion. In stainless steels, 2%-3% copper can improve their corrosion resistance to sulfuric acid, phosphoric acid, hydrochloric acid, etc., as well as their stability against stress corrosion. |
Mn | It lowers the steel’s lower critical point, increases the degree of undercooling during austenite cooling, and refines the pearlite structure to improve its mechanical properties. It is an important alloying element in low-alloy steels, significantly improving the hardenability of steel. However, it also has a detrimental tendency towards grain coarsening and temper brittleness. |
Mo | It improves the hardenability of steel. When present in a quantity of 0.5%, it can reduce temper brittleness and has a secondary hardening effect. When the content is between 2% and 3%, it increases the heat strength and creep strength of the steel, as well as its resistance to corrosion by organic acids and reducing media. |
N | It has a subtle solid solution strengthening effect and can improve the hardenability of steel, as well as increase its creep strength. When it combines with other elements in steel, it can have a precipitation hardening effect. Nitriding the surface of the steel can increase its hardness and wear resistance, as well as its corrosion resistance. In low-carbon steels, residual nitrogen can lead to temper embrittlement. |
Nb | It has a significant solid solution strengthening effect, improving the hardenability of steel (when dissolved in austenite), increasing tempering stability, and having a secondary hardening effect. It can also increase the strength and impact toughness of the steel. When the content is high (more than 8 times the carbon content), it gives the steel excellent hydrogen resistance and improves the high-temperature performance (creep strength, etc.) of heat-resistant steels. |
Ni | It increases the ductility and toughness of the steel, with a more significant improvement in low-temperature toughness. It also improves corrosion resistance. When used in combination with chromium and molybdenum, it can improve the heat strength of the steel. It is one of the main alloying elements in heat-resistant steels and stainless acid-resistant steels. |
P | It has a good solid solution strengthening and cold work hardening effect. When used in combination with copper, it can improve the atmospheric corrosion resistance of low-alloy high-strength steels but may lower its cold stamping performance. When used in combination with sulfur and manganese, it improves machinability, but increases temper brittleness and sensitivity to cold brittleness. |
Pb | It improves machinability. |
RE | This includes the lanthanide elements, as well as yttrium and scandium, totaling 17 elements. They have a deoxidizing, desulfurizing, and purifying effect that improves the cast structure of steel. A content of 0.2% can improve oxidation resistance, high-temperature strength, creep strength, and corrosion resistance. |
S | It improves machinability. However, it can produce hot brittleness, which worsens the quality of steel. High sulfur content can have a negative effect on weldability. |
Si | Common deoxidizers have a solid melting point strengthening effect, increase electrical resistance, reduce magnetic hysteresis loss, improve magnetic permeability, and enhance hardenability and temper resistance. They are beneficial for improving overall mechanical properties, increasing elastic limit, and enhancing corrosion resistance under natural conditions. However, at higher contents, they can reduce weldability and lead to cold brittleness. Medium carbon steel and high carbon steel are prone to graphitization during tempering. |
Ti | It has a strong solid solution strengthening effect, but it can decrease the toughness of the solid solution. When dissolved in austenite, it can improve the hardenability of steel, but when combining with titanium, it reduces the hardenability of steel. It improves tempering stability and has a secondary hardening effect, increasing the oxidation resistance and heat strength of heat-resistant steels, such as creep and sustained strength, and improving their weldability. |
V | When dissolved in austenite, it can improve the hardenability of steel. However, if vanadium exists in a compound state, it can reduce the hardenability of steel. It increases tempering stability and has a strong secondary hardening effect. When dissolved in ferrite, it has an extremely strong solid solution strengthening effect. It refines grains to improve low-temperature impact toughness. Vanadium carbide is the hardest and most wear-resistant metal carbide, significantly extending the life of tool steels. It also improves the creep and sustained strength of steel. When the vanadium to carbon ratio exceeds 5.7, it can greatly increase the steel’s resistance to high-temperature and high-pressure hydrogen corrosion, but may slightly reduce its high-temperature oxidation resistance. |
W | It has a secondary hardening effect, making the steel red-hard and improving its wear resistance. Its effects on the hardenability, tempering stability, mechanical properties, and heat strength of steel are similar to that of molybdenum. However, it may slightly reduce the steel’s oxidation resistance. |
Zr | Zirconium has similar effects in steel as niobium, titanium, and vanadium. In small quantities, it has a deoxidizing, purifying, and grain-refining effect, improving the low-temperature toughness of steel and eliminating aging phenomena. It can also improve the stamping performance of steel. |
Metal corrosion refers to the phenomenon where metals lose their effective properties due to corrosion after being exposed to acid-base solutions, acid-base gases, solvents, intermediates, alcohols, fats, etc.
Metals are often subjected to chemical and electrochemical reactions under the influence of external environmental factors, causing corrosion, which can lead to safety hazards by damaging the metal.
The failure caused by metal corrosion is a common phenomenon found in laboratory studies.
For example, steel structures rust in the atmosphere, ship metal hulls corrode in seawater, metal containers for storing acidic or basic liquids corrode, underground metal pipes puncture, thermal power plant boilers are damaged, and metal containers in chemical plants are damaged.
All these are examples of metal corrosion failure, caused by chemical or electrochemical reactions between the metal surface and the environment medium, resulting in the destruction or deterioration of the metal, known as metal corrosion.
To prevent metal corrosion, it is necessary to prevent both chemical and electrochemical corrosion.
Chemical corrosion is the damage caused by the chemical reaction between the metal surface and the surrounding medium, where an electrically conductive electrolyte solution is present during the corrosion process, and hence electrical current is generated.
This type of corrosion is the most common and includes atmospheric corrosion, soil corrosion, seawater corrosion, electrolyte solution corrosion, and molten salt corrosion.
The three main causes of metal rusting are:
1. Humidity: The critical humidity level of many metals is between 50% and 80%, with steel being around 75%. If the environmental humidity is lower than the critical humidity of the metal, the rate of metal oxidation and corrosion will be slower. Conversely, if the humidity is higher, it will accelerate the occurrence of metal rusting.
2. Temperature: It is generally believed that when the working temperature of a metal reaches 30%-40% of its melting point (absolute temperature), it can be considered as a high-temperature corrosion environment. The higher the temperature, the higher the probability of metal corrosion and the faster the corrosion rate.
3. Corrosion factors: During the processing of certain metals, corrosive gases such as chlorides and sulfides may be produced, which are direct factors that accelerate metal oxidation and rusting.
Alloy steel is formed by adding alloying elements to steel materials. During this process, the basic elements of steel, namely iron and carbon, will interact with the newly added alloying elements.
Under such interactions, the structure and substance of the steel will undergo certain changes, and the overall performance and quality of the steel will also be improved.
Therefore, the production of alloy steel is increasing, and its application range is becoming more and more extensive.
Corrosion-resistant alloys have the ability to resist media corrosion, but they cannot be used in environments containing fluorine.
Among them, metal corrosion-resistant materials mainly include three types: iron-based alloys (i.e., stainless steel), nickel-based corrosion-resistant alloys, and reactive metals:
1. Corrosion-resistant stainless steel mainly refers to the 300 series of stainless steel, such as 304 which is resistant to atmospheric or seawater corrosion, and the most commonly used corrosion-resistant alloy – Hastelloy C-276, 316L, 317L, etc.; austenitic stainless steel with stronger corrosion resistance, such as 904L, 254SMO; duplex steel 2205, 2507, etc.; Cu-containing corrosion-resistant alloy 20 alloy, etc.
2. Nickel-based corrosion-resistant alloys mainly include Hastelloy alloys and Ni-Cu alloys.
Due to the face-centered cubic structure of nickel itself, its crystallographic stability allows it to accommodate more alloying elements such as Cr and Mo than Fe, thereby achieving the ability to resist various environments.
At the same time, nickel itself has a certain corrosion resistance, especially the stress corrosion resistance caused by chloride ions.
In strongly reducing corrosive environments, complex mixed acid environments, and solutions containing halide ions, nickel-based corrosion-resistant alloys represented by Hastelloy have absolute advantages over iron-based stainless steels.
3. Reactive metals, which have excellent corrosion resistance, are typically represented by Ti, Zr, and Ta. Titanium is the most typical representative, and titanium materials have extensive applications, mainly in corrosive environments that stainless steel cannot adapt to.
The corrosion resistance principle of titanium material is to form a dense oxide film in an oxidizing atmosphere to provide protection.
Therefore, it generally cannot be used in highly reducing or high-sealing corrosive environments.
At the same time, the application temperature of titanium material is generally below 300 degrees Celsius. It is important to note that reactive metals cannot be used in environments containing fluorine.
The advantages of using corrosion-resistant alloys are as follows:
1. Alloys are not as temperature-sensitive as rubber and resin linings, and are less likely to be damaged under abnormal operating conditions.
2. All-alloy devices generally do not require emergency cooling systems.
3. Cleaning and descaling alloy components is much easier than coating, without worrying about damaging the coating.
4. Inspection and repair of alloy surfaces are also much easier, and only qualified welders are needed for repair work.
5. Although there are certain requirements for the construction method and environment of alloy components, they are far less strict than those for rubber and resin linings.
6. The performance changes of alloy products are generally smaller than those of rubber and resin, which have a shelf life. In addition, the inspection of alloy materials is relatively simple.
Corrosion resistance: The ability of a metal material to resist the corrosive destruction of the surrounding medium is called corrosion resistance. It is determined by the composition, chemical properties, and structural morphology of the material. Chromium, nickel, aluminum, and titanium can be added to steel to form a protective film, while copper can change the electrode potential and titanium and niobium can improve intergranular corrosion, which can improve corrosion resistance.
Introduction
Metal materials are widely used in various fields due to their versatility and accessibility, but their susceptibility to corrosion also affects their performance, limiting the use of metal materials.
To address this, metal usage can be reduced or direct contact with reactive media can be avoided as much as possible when using metal materials.
In addition, electrochemical corrosion protection can be carried out using the polarizing effect of yin and yang to improve protection for metal materials. This is of great practical significance for extending the life of metal materials, reducing application costs, and improving application efficiency.
1. Corrosion of Metal Materials and Its Hazards
1.1 Corrosion of Metal Materials
Corrosion of metal materials refers to a phenomenon in which metal materials are damaged by chemical or electrochemical reactions when they come into contact with surrounding media.
In nature, most metals exist in various forms of compounds, and the chemical activity of metal elements is usually higher than that of their compounds.
Therefore, these metals spontaneously evolve into their natural existence states, making metal corrosion a spontaneous and universal phenomenon that is unavoidable.
According to the mechanism of metal material corrosion, corrosion can typically be divided into chemical corrosion and electrochemical corrosion.
Chemical corrosion refers to the phenomenon of corrosion that occurs when metal materials come into contact with non-electrolytes in the surrounding media and undergo oxidation-reduction chemical reactions.
This is the corrosion that occurs when metal materials are in organic solutions (aromatic hydrocarbons, crude oil, etc.).
Electrochemical corrosion mainly refers to the phenomenon of corrosion that occurs when metal materials come into contact with electrolytes, and the metal surface reacts chemically with the electrolyte solution to form hydrogen absorption corrosion or hydrogen evolution corrosion. For example, carbon steel reacts with oxygen, carbon dioxide, and water in the air to form rust.
1.2 Hazards of Corrosion
Corrosion weakens the strength and mechanical properties of metal materials, shortening their service life, and even rendering metal materials ineffective, causing economic losses. According to reports, China’s economic losses caused by corrosion in 2014 have already exceeded 200 billion RMB.
On a global scale, the economic losses caused by corrosion are beyond imagination. The losses caused by corrosion also include the energy consumed during metal smelting and recycling.
At the same time, corrosion can also cause pollution of land and water resources. Corrosion can also cause damage to industrial equipment, bridge constructions, and ships, resulting in economic losses or even posing a threat to personal safety. Many accidents are directly or indirectly caused by corrosion.
Therefore, the research on anti-corrosion of metal materials is of great significance.
2. Factors affecting corrosion
2.1 Metal intrinsic reasons
Metal corrosion has a close relationship with metal itself, such as the forces generated on the surface of metal materials and internal characteristics, all of which have a direct relationship with metal corrosion. Metals with external shapes that are regular and structurally intact usually have a better resistance to corrosion than metals with surface defects.
When internal forces are concentrated, the accelerated corrosion rate of metal can threaten the metal’s quality and cause greater damage to the metal surface.
2.2 External conditions of metal
The main external causes of accelerating metal corrosion include:
(1) Operating media. The most significant factor affecting steel materials in operating media is the pH value, which is an important index for distinguishing electrolyte solutions. Therefore, the impact of pH value on corrosion degree is complex.
(2) Changes in temperature. In general, the higher the temperature, the faster the metal corrosion rate.
(3) Differences in pressure. In general, increasing pressure enhances the solubility of gas in the solution, causing the corrosion area of metal to expand until it spreads to the entire metal surface gradually.
3. Prevention of Metal Corrosion
3.1 Protecting the Metal Surface
There are two methods of treatment, namely phosphating and chlorination.
Phosphating of metal:
After removing oil and rust from steel products, they are immersed in a solution composed of metal and carbonate ion. After treatment with a solution containing phosphates of Zn, Mn, Cr, Fe, etc., an insoluble phosphate salt film is formed on the metal surface, which forms a component that is insoluble in water.
This process is called phosphate treatment. The color of the phosphate film changes from dark gray to black gray, and is five to twenty microns thick with strong anti-corrosion erosion resistance.
The structure of the phosphate film has many pores, easily adsorbs paint, and if used at the bottom of the paint layer, it can enhance its anti-corrosion resistance.
Chlorination of metal: Steel products are treated with a mixture of sodium chloride and sodium nitrite solution after hot treatment, and a blue iron oxide film is formed on the surface, which is called “blue”. This hydrogen film is flexible and lubricating, and does not affect the accuracy of the parts.
Precision equipment such as spring steel and fine iron wire, as well as optical equipment components, can be used for blue treatment.
Another anti-corrosion method is non-metallic coating: the metal surface coated with plastic is better than that of paint, the plastic covering layer is delicate and smooth, the color is very bright, and it has the function of corroding erosion and decoration. Ceramics containing SiO2, such as glass ceramics with a high content of SiO2, have good anti-corrosion erosion effects.
3.2 Heavy-duty Anti-corrosion Coating Technology
The coating process of heavy-duty anti-corrosion coatings is very elegant and simple, and is still used in many places. According to the development of coating technology, the anti-corrosion coating of the steel bridge surface is the key to the anti-corrosion of steel bridges.
In this regard, both foreign brand coatings and domestic old-brand coatings have similar anti-corrosion coating processes and types, which are composed of many coating systems, including primer, intermediate coat and topcoat.
The types of coatings are epoxy rich-zinc primer, epoxy mica iron oxide intermediate coat, epoxy polyurethane and epoxy color topcoat and chlorinated rubber topcoat, etc. Steel and corrosive environment are separated by the coating of coatings.
In the passive corrosion-resistant effect of the coating system, the first factory primer has a passive corrosion-resistant effect, but the sterilization effect is not ideal.
Under the cathodic protection of anti-corrosion primer, if zinc powder and rich-zinc primer are added, it will help the cathodic protection of steel.
3.3 Hot Spray Anti-corrosion Technology
There are two types of spray coatings, flame spray and arc spray. Flame spray: its heat source is combustible gas, its method is to melt metal wire and powder, then atomize and spray on the object surface.
O2 and C2H2 flame spray was the initial anti-corrosion spray of European and American steel bridges and achieved significant anti-corrosion effects.
Arc spray: using an arc spray device, heating, melting, atomizing and spraying two charged metal wires to produce anti-corrosion coatings, as well as long-lasting anti-corrosion composite coatings with organic sealing, is the anti-corrosion principle of arc spray.
3.4 Ion Implantation Technology
Ion implantation technology was developed in the 1970s and is a surface modification technology, different from ordinary coating technologies such as electroplating, electro-lithium plating and chemical vapor deposition.
It is a new technique that uses high-speed high-energy impacts to change the surface characteristics, and high-energy ions are rapidly implanted into the substrate surface in a vacuum state, which can dense the surface structure, implant the substrate surface with highly saturated solid solutions, metastable phases and non-crystalline and equilibrated alloys, and thus improve the anti-corrosion and erosion resistance of the substrate surface.
For example, ion implantation of metals is used to improve the chemical properties of the surface and enhance the anti-corrosion erosion function of the metal surface. The modification of aluminum and zinc alloy surfaces was already a research hot spot when ion implantation technology was developed.
In recent years, ion implantation technology has been gradually applied to magnesium alloys to improve its anti-corrosiveness.
3.5 Hot-dip Galvanizing Anti-Corrosion Technology
Hot-dip galvanizing is an anti-corrosion technology that is used for metal coatings such as zinc, tin, lead and other low melting point metals.
The metal coatings are produced by immersing the metal in a bath of molten metal. This technology is widely used for producing thin steel plates and food storage containers, as well as for chemical corrosion resistance and coating of electrical cables.
The hot-dip galvanizing of aluminum is mainly used for the protection against high-temperature oxidation of steel components.
As the demand for anti-corrosive coatings and cost control in the manufacturing process increases, hot-dip galvanizing technology is gradually evolving towards the development of metal alloy coating technology.
3.6 Electrochemical Corrosion Protection Technology
Based on the related theory in electrochemistry, “electrochemical protection method” is used on metal devices and becomes the cathode of the corrosion cell, thus preventing or reducing corrosion and erosion of the metal.
The first method is the “sacrificial anode protection method”, which uses a metal or alloy with an electrode potential lower than the protected metal as the anode, fixed on the protected metal to form a “corrosion electrode”, thus protecting the metal as the cathode. Zinc, aluminum, and alloys are commonly used as sacrificial anodes.
This method is mainly used to protect various metal devices located in the sea, such as the hull of ships and to increase the corrosion resistance of devices such as oil tanks and oil pipelines.
The second method is to apply external current, using the protected metal and another additional electrode as the two poles of the battery, so that the metal is protected as the cathode under the action of external direct current.
This method is mostly used to prevent corrosion and erosion of metal devices by soil, seawater, and river water.
Conclusion
In conclusion, metal materials have important application value, and the corrosion protection of metal materials is also an important topic of research for technology workers.
Recently, with the in-depth research of metal material corrosion work, metal material anti-corrosion technology and process have achieved certain results.
However, some new materials with strong corrosion resistance are restricted in their promotion and use due to cost reasons, and some anti-corrosion process methods are also facing problems such as harm to the environment, high process cost, and complicated operating conditions.
Therefore, further research on corrosion protection measures for metal materials still has important research value and practical significance.
Corrosion resistance of non-ferrous metals and their alloys
Metal Material Usage Selection Table | ||||||||||||||
Fluid | material | |||||||||||||
carbon steel | cast iron | 302/304 | 316 | bronze | Monel | Hastelloy B | Hastelloy C | stainless steel | titanium | Cobalt -chromium | 416 | 440C | 17-4PH | |
stainless steel | stainless steel | 20# | Alloy6# | stainless steel | stainless steel | |||||||||
acetaldehyde | A | A | A | A | A | A | I、L | A | A | I、L | I、L | A | A | A |
Acetic acid, gas | C | C | B | B | B | B | A | A | A | A | A | C | C | B |
Acetic acid, vaporization | C | C | A | A | A | A | A | A | A | A | A | C | C | B |
Acetic acid, steam | C | C | A | A | B | B | I、L | A | B | A | A | C | C | B |
acetone | A | A | A | A | A | A | A | A | A | A | A | A | A | A |
acetylene | A | A | A | A | I、L | A | A | A | A | I、L | A | A | A | A |
alcohol | A | A | A | A | A | A | A | A | A | A | A | A | A | A |
Lead sulfate | C | C | A | A | B | B | A | A | A | A | I、L | C | C | I、L |
ammonia | A | A | A | A | C | A | A | A | A | A | A | A | A | I、L |
ammonium chloride | C | C | B | B | B | B | A | A | A | A | B | C | C | I、L |
Ammonium nitrate | A | C | A | A | C | C | A | A | A | A | A | C | B | I、L |
Ammonium phosphate (monobasic) | C | C | A | A | B | B | A | A | B | A | A | B | B | I、L |
ammonium sulphate | C | C | B | A | B | A | A | A | A | A | A | C | C | I、L |
Ammonium sulfite | C | C | A | A | C | C | I、L | A | A | A | A | B | B | I、L |
aniline | C | C | A | A | C | B | A | A | A | A | A | C | C | I、L |
benzene | A | A | A | A | A | A | A | A | A | A | A | A | A | A |
Benzoic acid | C | C | A | A | A | A | I、L | A | A | A | I、L | A | A | A |
boric acid | C | C | A | A | A | A | A | A | A | A | A | B | B | I、L |
butane | A | A | A | A | A | A | A | A | A | I、L | A | A | A | A |
calcium chloride | B | B | C | B | C | A | A | A | A | A | I、L | C | C | I、L |
Calcium hypochlorite | C | C | B | B | B | B | C | A | A | A | I、L | C | C | I、L |
Carbolic acid | B | B | A | A | A | A | A | A | A | A | A | I、L | I、L | I、L |
Carbolic acid | A | A | A | A | A | A | A | A | A | A | A | A | A | A |
Carbon dioxide (dry) | C | C | A | A | B | A | A | A | A | A | A | A | A | A |
Carbon dioxide (wet) | A | A | A | A | C | B | A | A | A | A | A | B | B | I、L |
carbon dioxide | B | B | B | B | A | A | B | A | A | A | I、L | C | A | I、L |
carbon tetrachloride | C | C | B | B | B | A | A | A | A | I、L | I、L | A | A | A |
Carbonic acid H2C03 | A | A | B | B | B | A | A | A | A | C | B | C | C | C |
Chlorine, dry | C | C | C | C | C | C | C | B | C | A | B | C | C | C |
Chlorine, wet | C | C | C | C | B | C | C | A | B | C | B | C | C | C |
Chlorine, liquid | C | C | C | B | C | A | C | A | C | A | B | C | C | C |
Chromic acid H2Cr04 | A | A | A | A | B | B | A | A | A | A | A | A | A | A |
Coke oven gas | C | C | B | B | B | C | I、L | A | A | A | I、L | A | A | A |
copper sulphate | A | A | A | A | A | A | A | A | A | A | A | A | A | A |
ethane | B | B | A | A | A | A | A | A | A | A | A | A | A | A |
ether | C | C | A | A | A | A | A | A | A | A | A | B | B | I、L |
Chloroethane | A | A | A | A | A | A | I、L | A | A | A | A | A | A | A |
ethylene | A | A | A | A | A | A | I、L | I、L | A | I、L | A | A | A | A |
glycol | C | C | C | C | C | C | C | B | C | A | B | C | C | I、L |
Ferric chloride | B | B | A | A | A | A | A | A | A | A | A | A | A | A |
Methylketone HCHO | I、L | C | B | B | A | A | A | A | A | C | B | C | C | B |
Formaldehyde HCO2H | B | B | B | A | A | A | A | A | A | A | A | I、L | I、L | I、L |
Freon, wet | B | B | A | A | A | A | A | A | A | A | A | I、L | I、L | I、L |
Freon, dry | A | A | A | A | A | A | A | A | A | A | A | B | B | I、L |
Gasoline, refined | A | A | A | A | A | A | A | A | A | A | A | A | A | A |
Hydrochloric acid, vaporization | C | C | C | C | C | C | A | B | C | C | B | C | C | C |
Hydrochloric Acid, Free | C | C | C | C | C | C | A | B | C | C | B | C | C | C |
Hydrofluoric acid, vaporization | B | C | C | B | C | C | A | A | B | C | B | C | C | C |
Hydrofluoric Acid, Free | A | C | C | B | C | A | A | A | B | C | I、L | B | B | I、L |
hydrogen | A | A | A | A | A | A | B | A | A | A | A | A | A | A |
hydrogen peroxide | I、L | A | A | A | C | B | A | B | A | A | I、L | B | B | I、L |
Hydrogen sulfide, liquid | C | C | A | A | C | C | A | A | B | A | A | C | C | I、L |
magnesium hydroxide | A | A | A | A | B | A | A | A | A | A | A | A | A | I、L |
Methylethyl ketone | A | A | A | A | A | A | A | A | A | I、L | A | A | A | A |
natural gas | A | A | A | A | A | A | A | A | A | A | A | A | A | A |
nitric acid | C | C | A | B | C | C | C | B | A | A | C | C | C | B |
oxalate | C | C | B | B | B | B | A | A | A | B | B | B | B | I、L |
oxygen | A | A | A | A | A | A | A | A | A | A | A | A | A | A |
methanol | A | A | A | A | A | A | A | A | A | A | A | A | B | A |
Lubricating oil, refined | A | A | A | A | A | A | A | A | A | A | A | A | A | A |
Phosphoric Acid, Vaporization | C | C | A | A | C | C | A | A | A | B | A | C | C | I、L |
Phosphoric Acid, Free | C | C | A | A | C | B | A | A | A | B | A | C | C | I、L |
Phosphoric acid vapor | C | C | B | B | C | C | A | I、L | A | B | C | C | I、L | |
Picric acid | C | C | A | A | C | C | A | A | A | I、L | I、L | B | B | I、L |
calcium chlorite | B | B | A | A | B | B | A | A | A | A | I、L | C | C | I、L |
Potassium hydroxide | B | B | A | A | B | B | A | A | A | A | I、L | B | B | I、L |
propane | A | A | A | A | A | A | A | A | A | A | A | A | A | A |
Rosin, rosin | B | B | A | A | A | A | A | A | A | I、L | A | A | A | A |
Sodium acetate, sodium carbonate, sodium chloride | A | A | B | A | A | A | A | A | A | A | A | A | A | A |
Sodium chromate | A | A | A | A | A | A | A | A | A | A | A | B | B | A |
sodium hydroxide | C | C | B | B | A | A | A | A | A | A | A | B | B | B |
sodium hypochlorite | A | A | A | A | A | A | A | A | A | A | A | A | A | A |
Sodium thiosulfate | A | A | A | A | C | A | A | A | A | A | A | B | B | A |
Tin dichloride | C | C | C | C | B-C | B-C | C | A | B | A | I、L | C | C | I、L |
Hard acid | C | C | A | A | C | C | A | A | A | A | I、L | B | B | I、L |
Sulfate solution | B | B | C | A | C | B | A | A | A | A | I、L | C | C | I、L |
sulfur | A | C | A | A | B | B | A | A | A | A | B | B | B | I、L |
Oxygen disulfide dry | A | A | A | A | C | A | A | A | A | A | A | I、L | I、L | I、L |
Sulfur dioxide dry | A | A | A | A | C | A | A | A | A | A | A | A | A | A |
Sulfuric acid, vaporization | A | A | A | A | A | A | B | A | A | A | A | B | B | I、L |
Sulfuric acid, free | A | A | A | A | A | A | B | A | A | A | A | B | B | I、L |
Sulfite | C | C | C | C | C | C | A | A | A | B | B | C | C | C |
Tar | C | C | C | C | B | B | A | A | A | B | B | C | C | C |
Sulfite | C | C | B | B | B | C | A | A | A | A | B | C | C | I、L |
Tar | A | A | A | A | A | A | A | A | A | A | A | A | A | A |
Trifluoroethylene | B | B | B | A | A | A | A | A | A | A | A | B | B | I、L |
turpentine | B | B | A | A | A | B | A | A | A | A | A | A | A | A |
Vinegar | C | C | A | A | B | A | A | A | A | I、L | A | C | C | A |
Water, boiler water supply | B | C | A | A | C | A | A | A | A | A | A | B | A | A |
Water, distilled water | A | A | A | A | A | A | A | A | A | A | A | B | B | I、L |
seawater | B | B | B | B | A | A | A | A | A | A | A | C | C | A |
Zinc chloride | C | C | C | C | C | C | A | A | A | A | B | C | C | I、L |
zinc sulfate | C | C | A | A | B | A | A | A | A | A | A | B | B | I、L |
Symbol: | A – Capable of or currently being successfully applied | |||||||||||||
B – Attention to application process | ||||||||||||||
C – Cannot be applied | ||||||||||||||
I.L. – Lack of information | ||||||||||||||
This table is used to outline how to select the appropriate material when reacting with a fluid. The recommendations in the table are not absolute, as the corrosivity of materials is related to factors such as fluid concentration, temperature, pressure, and impurities. Therefore, it must be emphasized that this table can only serve as a guide. | ||||||||||||||
Monel | ||||||||||||||
Hastelloy“B”、(“C”) | ||||||||||||||
Stainless Steel # 20-Durimet20 | ||||||||||||||
Cobalt Chromium Alloy # 6-Alloy6 (Co Cr) |
Corrosion resistance of non-ferrous metals and alloys
In industry, steel is referred to as a black metal while all other metals are referred to as non-ferrous metals. Non-ferrous metals and their alloys are often used for making water treatment equipment, chemical containers, and related equipment components due to their good corrosion resistance and low temperature performance.
Copper and its Alloys
Copper and its alloys have high conductivity, thermal conductivity, plasticity, and cold workability, and have good corrosion resistance in many media.
1. Pure Copper
Also known as red copper. Copper is relatively stable in general atmospheric conditions, industrial atmospheric conditions, marine atmospheric conditions, and is also stable in alkalis and weak to medium-strength non-oxidizing acids.
If the solution contains oxygen or oxidants, corrosion will be more severe. Copper is not resistant to sulfides (such as H2S) corrosion.
Copper has high conductivity, thermal conductivity, plasticity, and good processing properties, and also has good cold workability. However, copper has low strength, poor castability, and poor corrosion resistance in some media, and is rarely used as a structural material.
2. Copper Alloys
Common copper alloys are brass and bronze.
1)Brass
An alloy of copper and zinc is called brass. To improve its performance, tin, aluminum, silicon, nickel, manganese, lead, iron, and other elements are often added, forming a special brass alloy.
Features: The mechanical properties are closely related to the zinc content; castability is good; corrosion resistance is good; brass with a zinc content greater than 20% can cause stress corrosion cracking in damp atmospheres, seawater, high temperature and high pressure water, steam and all environments containing ammonia after cold working.
Brass is susceptible to dezincification corrosion in neutral solutions, seawater, and acid pickling solutions after annealing, which can be prevented by adding 0.02% arsenic to the brass.
2)Bronze
All copper alloys in which the main added element is not zinc but tin, aluminum, silicon, and other elements are commonly referred to as bronze. Common bronzes include tin bronze, aluminum bronze, and silicon bronze.
Features: Tin bronze has worse castability than brass and better corrosion resistance than pure copper and brass, but poor resistance to acid corrosion.
Aluminum bronze has better mechanical properties than brass and tin bronze, and higher corrosion resistance in atmospheres, seawater, carbonic acid, and most organic acids than brass and tin bronze.
Silicon bronze has higher mechanical properties than tin bronze and a lower price, and has good castability and cold and hot pressure processing properties.
Aluminum and its Alloys
1. Aluminum
Features: Aluminum has a low density, with a specific gravity of 2.7, about one-third of copper; it has good conductivity, thermal conductivity, plasticity, and cold workability, but low strength, which can be improved by cold deformation; it can withstand various pressure processing.
Aluminum is a highly negative electrode potential element, and aluminum is also stable in strong oxidizing media and oxidizing acids (such as nitric acid).
Halogen ions have a destructive effect on the aluminum oxide film, so aluminum is not corrosion-resistant in hydrofluoric acid, hydrochloric acid, seawater, and other solutions containing halogen ions.
Applications: widely used in the manufacture of reactors, heat exchangers, coolers, pumps, valves, tank cars, pipe fittings, etc.
Pure aluminum has low strength, but if some elements such as copper, magnesium, zinc, manganese, silicon, etc. are added to aluminum
Titanium and its Alloys:
1. Pure titanium:
Characteristics: Pure titanium is a reactive element. It has good passivation properties, with a stable passivating film that demonstrates good corrosion resistance in many environments. It is known as the “king of seawater corrosion resistance”.
At high temperatures, titanium is highly chemically active and reacts violently with elements such as halogens, oxygen, nitrogen, carbon, and sulfur.
Titanium generally does not undergo pitting corrosion, and except for a few individual media (such as smoky nitric acid and methanol solution), it does not undergo intergranular corrosion; titanium has a low sensitivity to stress corrosion cracking and has good anti-corrosion fatigue properties, and good resistance to crevice corrosion.
2. Titanium Alloys:
Characteristics: The mechanical and corrosion resistance properties of titanium alloys are significantly improved compared to pure titanium.
In industry, titanium alloys are used instead of pure titanium. The main forms of corrosion in titanium alloys are hydrogen cracking and stress corrosion cracking.
Nickel and its Alloys:
1. Nickel:
Characteristics: Nickel has a very high corrosion resistance in all temperature and concentration ranges of alkaline solutions and all types of fused alkalis.
However, nickel is not very corrosion-resistant in environments containing sulfur gases, concentrated ammonia water, and strongly aerated ammonia solutions, as well as oxygen acids and hydrochloric acid.
Nickel has high strength, high plasticity, and cold hardiness and can be cold-rolled into very thin sheets and drawn into fine wires.
Nickel is rare and expensive and is mainly used in water treatment engineering and chemical engineering to manufacture equipment for alkaline media, and in processes where iron ions would cause catalytic interference and stainless steel cannot be used.
2. Nickel Alloys:
The Monel alloy in Ni-Cu alloys has good mechanical properties and machinability, is easy to process under pressure and to cut, and has good corrosion resistance. It is mainly used for corrosion-resistant parts and equipment that work under high temperature loads.
The Hastelloy alloy (0Cr16Ni57Mo16Fe6W4) in Ni-Mo alloys is resistant to all concentrations of hydrochloric and hydrofluoric acid at room temperature.
The Inconel alloy (0Cr15Ni57Fe) in Ni-Cr alloys has good mechanical properties at high temperatures and high oxidation resistance, and is one of the few materials that can resist the corrosion of concentrated MgCl2.
In this article, we introduce what alloy is, explain the difference between corrosion and rust, and analyze in detail the advantages of corrosion-resistant alloys and the use of corrosion-resistant alloys. In addition, we also discuss in detail the factors that affect the corrosion resistance of metal materials. Finally, we provide a corrosion resistance performance table of the main metal materials and analyze the corrosion resistance of non-ferrous metals and their alloys.
After reading this, I believe you now have a clear answer to the question of “Does alloy rust?”.