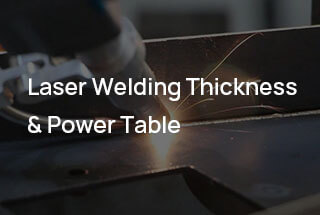
¿Se ha preguntado alguna vez cómo la tecnología moderna puede revolucionar la soldadura tradicional? Este artículo explora el fascinante mundo de la soldadura láser, destacando sus ventajas, retos y aplicaciones en industrias que van desde la aeroespacial hasta la automovilística. Descubra cómo esta tecnología de vanguardia está transformando la soldadura de aleaciones de aluminio, ofreciendo una precisión y eficacia nunca vistas.
La soldadura por láser ofrece ventajas significativas sobre los métodos de soldadura tradicionales, como un aporte mínimo de calor, una influencia térmica reducida, relaciones de aspecto elevadas y un control automatizado del proceso. Estas ventajas se traducen en una mejora de la calidad de la soldadura, un aumento de la productividad y una mayor precisión en las aplicaciones de unión de metales.
Las aleaciones de aluminio gozan de gran aceptación en diversos sectores debido a sus excepcionales propiedades, como su baja densidad, su elevada relación resistencia-peso, su excelente resistencia a la corrosión y su superior conformabilidad. Estas características hacen que las aleaciones de aluminio sean ideales para aplicaciones en la fabricación de contenedores, producción de maquinaria, equipos de energía eléctrica, componentes de la industria química y estructuras aeroespaciales.
La sustitución del acero por aleaciones de aluminio en estructuras soldadas puede suponer mejoras sustanciales en el rendimiento estructural global y en la reducción de peso. Sin embargo, el aluminio presenta desafíos únicos en la soldadura debido a su alta conductividad térmica, bajo potencial de ionización y tendencia a formar un óxido de aluminio tenaz (Al2O3) en su superficie. Esta película de óxido puede impedir la fusión y contribuir a defectos de soldadura como la falta de fusión, porosidad, inclusiones y agrietamiento en caliente, comprometiendo potencialmente la integridad mecánica de la unión soldada.
En comparación con las técnicas convencionales de soldadura por arco, como la soldadura por arco de tungsteno con gas (GTAW) o la soldadura por arco metálico con gas (GMAW), la soldadura por láser ofrece varias ventajas claras. Entre ellas se incluyen cordones de soldadura más estrechos, zonas afectadas por el calor minimizadas, requisitos de solapamiento de juntas reducidos, control preciso de los parámetros de soldadura y capacidades de automatización mejoradas. Estas características contribuyen a mejorar la calidad de la soldadura, reducir la distorsión y aumentar la eficacia de la producción.
En la actualidad, la tecnología de soldadura láser tiene una amplia aplicación en la unión de componentes electrónicos de paredes finas, piezas estructurales y componentes aeroespaciales. La trayectoria futura de la investigación en soldadura láser se centra en el desarrollo y la aplicación de láseres de fibra de alta potencia, especialmente en el rango de 10 kW, para la soldadura de penetración profunda de materiales a gran escala y de sección gruesa. Este avance ampliará las capacidades de la soldadura láser para abordar aplicaciones más exigentes en la industria pesada y la fabricación a gran escala.
Rendimiento/tipo | Láser de dióxido de carbono | NdYAG láser | YbYAG Láser Dac | Láser de fibra |
---|---|---|---|---|
Longitud de onda / um | 10.6 | 1.06 | 1.06 | 1-2 |
Eficiencia de conversión eléctrica/% | 12-15 | 2-6 | 20 | 8-10 |
Densidad de potencia/(MW/cm-2) | 10 | 10 | 100 | 100 |
Potencia máxima/kW) | 50 | 6 | 15 | 50 |
Salida del haz | Lente óptica | Fibra óptica | Fibra óptica | Fibra óptica |
Absortividad del metal/% | 8 | 20 | 20 | 20 |
Ciclo de mantenimiento/hora | 1000 | 1000 | 1ooo | 20000 |
Brillo láser (103 W/mm2steradiano) (4 kW/h) | — | 7,5(distancia focal:200; Diámetro de la fibra:0,6 mm) | 134,2(distancia focal:200; Diámetro de la fibra:0,2 mm) | 264.4 (distancia focal:160; Diámetro de la fibra:0,1 mm) |
Láser de gas CO2
El láser de CO2 utiliza gas dióxido de carbono como medio activo y emite a una longitud de onda de 10,6 μm. Estos láseres se clasifican en los tipos de flujo cruzado y de flujo axial en función de su estructura de excitación. Aunque los láseres de CO2 de flujo cruzado han alcanzado potencias de salida impresionantes de hasta 150 kW, la calidad de su haz no es óptima para aplicaciones de soldadura de precisión. En cambio, los láseres de CO2 de flujo axial ofrecen una calidad de haz superior, lo que los hace adecuados para soldar materiales muy reflectantes, como las aleaciones de aluminio. Sin embargo, la mayor longitud de onda de los láseres de CO2 puede provocar un aumento de las zonas afectadas por el calor y una posible distorsión térmica en materiales finos.
YAG Láser de estado sólido
Los láseres de estado sólido emplean materiales cristalinos o de vidrio como medio activo. Entre los tipos más comunes se encuentran el rubí, el vidrio de neodimio y el granate de aluminio e itrio dopado con neodimio (Nd:YAG). Estos láseres suelen emitir a una longitud de onda de 1,06 μm. Los láseres de YAG ofrecen varias ventajas sobre los láseres de CO2 para la soldadura de metales: mayor absorción por las superficies metálicas, reducción de los efectos de apantallamiento del plasma y compatibilidad con el suministro de haces de fibra óptica. Esta capacidad de fibra óptica permite operaciones de soldadura flexibles y una mejor accesibilidad a geometrías complejas. La longitud de onda más corta también permite puntos focales más pequeños, lo que aumenta potencialmente la densidad de potencia y la velocidad de soldadura. Estas características han convertido a los láseres YAG en la elección predominante para la soldadura estructural de aleaciones de aluminio en muchas industrias.
Láser de fibra óptica YLR
Desarrollados después de 2002, los láseres de fibra YLR representan un avance significativo en la tecnología láser. Estos láseres utilizan fibras ópticas dopadas con iones de tierras raras como medio de ganancia y emiten normalmente a 1,08 μm. La revolucionaria estructura de fibra de doble revestimiento de estos láseres mejora drásticamente la eficiencia de bombeo y la potencia de salida en comparación con los láseres de fibra tradicionales. Los láseres de fibra YLR ofrecen numerosas ventajas sobre los sistemas YAG, entre las que se incluyen:
Estas características hacen que los láseres de fibra YLR sean cada vez más populares para la soldadura de alta precisión de aleaciones de aluminio, especialmente en aplicaciones aeroespaciales y de automoción en las que la calidad de la soldadura y la fiabilidad del proceso son fundamentales.
El aluminio y las aleaciones de aluminio se clasifican en siete series principales:
En función de sus características de procesamiento, las aleaciones de aluminio se clasifican en dos categorías principales: aleaciones de aluminio forjado y aleaciones de aluminio fundido. Las aleaciones forjadas se subdividen a su vez en aleaciones no tratables térmicamente y aleaciones tratables térmicamente.
La soldabilidad de las aleaciones de aluminio varía significativamente entre las distintas series:
Las aleaciones no tratables térmicamente (series 1000, 3000 y 5000) presentan generalmente una buena soldabilidad. Las aleaciones de la serie 4000 muestran una baja susceptibilidad al agrietamiento en caliente.
Sin embargo, las aleaciones de la serie 5000 con un contenido de magnesio superior a 2% se vuelven propensas al agrietamiento. Aunque el aumento del contenido de magnesio mejora el rendimiento de la soldadura, afecta negativamente a la ductilidad y la resistencia a la corrosión de la aleación.
Las aleaciones tratables térmicamente (series 2000, 6000 y 7000) presentan mayores retos en la soldadura. Son más susceptibles al agrietamiento en caliente, presentan una formación deficiente del cordón de soldadura y experimentan una reducción significativa de la resistencia debido a la disolución de precipitados de endurecimiento en la zona afectada por el calor (ZAT).
Para conseguir uniones soldadas de alta calidad en aleaciones de aluminio, es fundamental aplicar técnicas de soldadura adecuadas, seleccionar procesos de soldadura apropiados y utilizar materiales de aportación compatibles. La preparación de la superficie antes de la soldadura es esencial y normalmente implica:
Para mantener la limpieza de la superficie, la soldadura debe realizarse en las 24 horas siguientes a la preparación de la superficie. Además, se recomienda realizar pruebas de cualificación del procedimiento de soldadura para optimizar los parámetros para combinaciones de aleaciones y configuraciones de unión específicas.
Desde la década de 1990, los avances significativos en la tecnología láser, en particular el desarrollo de láseres de alta potencia y alto brillo, han impulsado la soldadura láser a nuevas cotas de integración, inteligencia, flexibilidad y versatilidad. Esta evolución ha suscitado un creciente interés por la aplicación de la soldadura láser a estructuras de aleación de aluminio en diversos sectores industriales de todo el mundo.
En el sector de la automoción, varios fabricantes chinos ya han incorporado la tecnología de soldadura láser a sus últimos modelos. Como la capacidad de soldar con láser placas gruesas de aleación de aluminio sigue mejorando, esta tecnología está preparada para su futura aplicación en estructuras de vehículos blindados, lo que ofrece ventajas potenciales en términos de relación resistencia-peso y eficiencia de fabricación.
La búsqueda de una fabricación ligera ha hecho de la soldadura láser de estructuras sándwich de aleación de aluminio un área clave de investigación para las industrias naval y ferroviaria de alta velocidad. Estas estructuras de materiales compuestos ofrecen un equilibrio óptimo entre resistencia, reducción de peso y gestión térmica, fundamentales para mejorar el rendimiento y la eficiencia energética en aplicaciones marítimas y ferroviarias.
Las aleaciones de aluminio siguen siendo cruciales en las estructuras aeroespaciales, lo que ha impulsado la investigación intensiva de técnicas de soldadura láser en países tecnológicamente avanzados como Japón, Estados Unidos, Reino Unido y Alemania. La atención se ha desplazado hacia la soldadura por láser de fibra y la soldadura híbrida láser-arco, sobre todo para la unión de chapas gruesas y la soldadura de metales distintos, ya que estos métodos ofrecen una calidad de soldadura superior, una penetración más profunda y una reducción de las zonas afectadas por el calor.
La evolución de la tecnología láser de fibra ha situado la soldadura láser de fibra y la soldadura híbrida láser-arco a la vanguardia de la unión de aleaciones de aluminio en la fabricación aeronáutica avanzada. Estas técnicas destacan por su precisión, velocidad y capacidad para soldar geometrías complejas, lo que las hace ideales para aplicaciones aeroespaciales. Un ejemplo destacado es el proyecto estadounidense NALI (National Aerospace Leadership Initiative), que está llevando a cabo una investigación puntera sobre soldadura láser de fibra y soldadura híbrida láser-arco para estructuras de cámaras de combustión tanto en aviones comerciales como en motores de aviones de combate Joint Strike Fighter (JSF).
Esta investigación en curso y la aplicación de técnicas avanzadas de soldadura láser para aleaciones de aluminio están impulsando innovaciones en el diseño estructural, los procesos de fabricación y el rendimiento de los materiales en múltiples industrias de alta tecnología, allanando el camino para productos más ligeros, resistentes y eficientes en los sectores de automoción, defensa, naval, ferroviario y aeroespacial.
La soldadura por láser de aleaciones de aluminio ofrece ventajas significativas sobre las técnicas convencionales de soldadura por fusión, como un aporte de calor muy concentrado, una relación superior entre profundidad y anchura de soldadura y una deformación estructural mínima. Sin embargo, este avanzado proceso también presenta retos únicos:
En conclusión, aunque la soldadura láser ofrece ventajas convincentes para la unión de aleaciones de aluminio, para aprovechar todo su potencial es necesario abordar estos retos inherentes. El principal objetivo del avance de esta tecnología es desarrollar estrategias para mitigar los defectos de soldadura, mejorar las propiedades de las uniones y aumentar la estabilidad del proceso mediante un control preciso de los parámetros de soldadura, diseños innovadores de las uniones y, potencialmente, la integración de sistemas de supervisión y control adaptativo en tiempo real.
La soldadura por láser utiliza el láser como fuente de luz de alta densidad que ofrece un calentamiento rápido y una solidificación instantánea, con una relación de aspecto de hasta 12:1. Sin embargo, debido a la alta reflectividad y buena conductividad térmica de las aleaciones de aluminio, así como al efecto de blindaje del plasma, es probable que se produzcan defectos durante el proceso de soldadura.
Los dos defectos más significativos son los poros y las grietas térmicas. El reto en la soldadura láser de aleaciones de aluminio es mejorar eficazmente la absorción de la luz láser por parte del material debido a su fuerte reflexión.
En proceso de soldadura láser para aleaciones de aluminio es más compleja, y es crucial mejorarla y perfeccionarla debido a las características de la propia aleación de aluminio.
Cuanto mayor sea la tasa de absorción del láser por el material, o cuanto menor sea el coeficiente de transferencia de calor y el coeficiente de conductividad de la temperatura, más fácilmente absorberá la superficie del material la energía láser, lo que provocará un rápido aumento de la temperatura de la superficie y la fusión o evaporación del material.
La tabla 1 muestra la reflectividad de varios metales a láseres con diferentes longitudes de onda.
Tabla 1 La reflectividad de los metales a los láseres de diferentes longitudes de onda a temperatura ambiente (%)
λ/μm | Ag | Al | Cu | Cr | Ni | Acero |
---|---|---|---|---|---|---|
0.7 | 95 | 77 | 82 | 56 | 68 | 58 |
1.06 | 97 | 80 | 91 | 58 | 75 | 63 |
10.6 | 99 | 98 | 98 | 93 | 95 | 93 |
La reflectividad de diferentes metales disminuye a medida que la longitud de onda se acorta, siendo la reflectividad de Ag, Al y Cu a la luz láser de hasta 90% o más. Esto aumenta significativamente la dificultad de procesamiento láser.
A temperatura ambiente, la tasa de absorción de CO2 por las aleaciones de aluminio es muy baja, con 98% de la energía láser reflejada por la superficie de la aleación de aluminio. La reflectividad de los láseres Nd:YAG es también de hasta 80%.
Está claro que las aleaciones de aluminio tienen una alta reflectividad a la luz láser y una baja tasa de absorción, debido a su alta densidad de electrones libres. La fuerte vibración de las ondas electromagnéticas de la luz da lugar a la generación de ondas reflejadas fuertes y ondas transmitidas más débiles. Las ondas reflejadas no son fácilmente absorbidas por la superficie de la aleación de aluminio, lo que da lugar a su alta reflectividad a los láseres a temperatura ambiente.
En el proceso de soldadura lásercuando la densidad de energía del láser es superior a 3,5 * 106W/cm2se generarán iones. Este método de soldadura se realiza mediante soldadura de penetración profunda y se basa en el efecto de "pequeños agujeros". La presencia de "pequeños orificios" aumenta significativamente la tasa de absorción del láser por parte del material y da lugar a un buen efecto de soldadura mediante la fusión de la pieza soldada con una alta densidad de energía.
El principal reto en la soldadura láser de aleaciones de aluminio es inducir y mantener la estabilidad de los agujeros pequeños, lo que se debe tanto a la propiedades del material de las aleaciones de aluminio y las propiedades ópticas del rayo láser. Como se ha mencionado anteriormente, el aluminio refleja 80% de energía a temperatura ambiente y tiene una buena conductividad térmica, lo que requiere un gran umbral de densidad de energía láser para producir "pequeños agujeros."
Una vez que la potencia de entrada supera este valor, la transmisión de la energía láser al material deja de estar limitada por la conducción del calor, y la soldadura se realiza por penetración profunda. La dirección radiación láser provoca una fuerte evaporación del metal base y forma una ranura de evaporación. El rayo láser penetra en el material a través de este surco, lo que se traduce en un fuerte aumento tanto de la profundidad como de la eficacia de la soldadura.
Para materiales altamente reflectantes, como las aleaciones de aluminio y las aleaciones de cobre, se requiere una gran densidad de potencia durante la soldadura. Esto impone ciertos requisitos a la hora de seleccionar los modelos de soldadura y las lentes de colimación y enfoque.
El refuerzo por refinamiento, el refuerzo por solución sólida y el refuerzo por precipitación por envejecimiento son tres formas diferentes de reforzar las aleaciones de aluminio. A pesar de estos mecanismos, la gran cantidad de evaporación de elementos de aleación de bajo punto de fusión, como el Mg y el Zn, durante la soldadura láser provoca el hundimiento de la soldadura y reduce su dureza y resistencia.
Durante el proceso de solidificación rápida, la transformación de la estructura reforzada de grano fino en una estructura en bruto provoca una disminución de la dureza y la resistencia. Además, la presencia de grietas y poros en la soldadura disminuye la resistencia a la tracción.
En conclusión, el reblandecimiento de las juntas es otro reto en la soldadura láser de aleaciones de aluminio.
Existen dos tipos principales de poros en el proceso de soldadura láser de aleaciones de aluminio: los poros de gas hidrógeno y los poros de colapso de ojo de cerradura.
(1) Poros de hidrógeno: Las aleaciones de aluminio forman una película de óxido en su superficie a altas temperaturas, que absorbe fácilmente la humedad del ambiente. Cuando se calienta con un láser, el agua se descompone en hidrógeno, y la solubilidad del hidrógeno en el aluminio líquido es unas 20 veces mayor que en el aluminio sólido. Durante la rápida solidificación de la aleación, la solubilidad del hidrógeno disminuye drásticamente al pasar del aluminio líquido al estado sólido. Si el exceso de hidrógeno en el aluminio líquido no asciende y rebosa suavemente, formará poros de hidrógeno. Estos poros suelen tener una forma regular y un tamaño mayor que el de las dendritas, y en la superficie interior pueden verse los patrones de solidificación de las dendritas.
(2) Colapso del ojo de la cerradura: El orificio de soldadura está en equilibrio con su propia gravedad y la presión atmosférica. Una vez que se rompe este equilibrio, el metal líquido del baño de fusión no puede fluir y rellenarse a tiempo, lo que da lugar a agujeros irregulares. Los estudios han descubierto que el contenido de magnesio de la pared interior del agujero es aproximadamente 4 veces superior al de las proximidades de la soldadura. Debido a que la velocidad de enfriamiento de la soldadura láser es demasiado rápida, el problema de los poros de gas hidrógeno es más grave, y hay más agujeros causados por el colapso de pequeños agujeros en la soldadura láser.
La aleación de aluminio es una aleación eutéctica común que es propensa a grietas calientes durante la soldadura, incluidas las grietas de cristalización de la soldadura y las grietas de licuefacción de la ZAC (Zona Afectada por el Calor). Normalmente, las grietas de cristalización aparecen en la zona de soldadura, mientras que las grietas de licuefacción aparecen cerca de la unión. Entre las aleaciones de aluminio, las aleaciones Al-Mg-Si de la serie 6000 son especialmente susceptibles al agrietamiento.
El metal base se somete a un calentamiento y enfriamiento rápidos, lo que puede dar lugar a un proceso instantáneo de solidificación y cristalización. El alto grado de subenfriamiento durante este proceso hace que los granos de cristal crezcan perpendiculares al centro de la soldadura, formando compuestos eutécticos de baja fusión como Al-Si o Mg-Si, Al-Mg2Si y otros. Esto debilita la fuerza de unión del plano cristalino, haciéndolo más propenso a las grietas cristalinas bajo tensión térmica.
En el aluminio soldadura de aleación los elementos de bajo punto de ebullición, como el Mg, el Zn, el Mn y el Si, se evaporan y queman con facilidad. Cuanto más lenta sea la velocidad de soldadura, más grave será la combustión, lo que modifica la composición química del metal de soldadura. Debido a la segregación de componentes en la zona de soldadura, se produce segregación eutéctica y fusión del límite de grano, lo que provoca grietas de licuefacción en el límite de grano bajo tensión, reduciendo el rendimiento de la unión soldada.
Para lograr una soldadura láser satisfactoria de las aleaciones de aluminio y abordar los problemas mencionados anteriormente, se suelen adoptar varios enfoques.
Uno de los factores más importantes que afectan a la pérdida de elementos de bajo punto de fusión en las aleaciones de aluminio durante la soldadura es la presión del gas expulsado por la boquilla. Para mitigar este problema, se puede reducir el diámetro de la boquilla y aumentar la presión y el caudal del gas. Esto reducirá la pérdida por combustión de elementos como el Mg y el Zn durante el proceso de soldadura, y también aumentará la penetración.
Existen dos métodos de soplado: soplado directo y soplado lateral. Además, es posible soplar simultáneamente hacia arriba y hacia abajo de la pieza soldada. La elección del método de soplado debe determinarse en función de las circunstancias específicas de la soldadura.
La aleación de aluminio tiene una fuerte reacción a la energía láser. Preparación adecuada de la superficie de la aleación de aluminio, como la oxidación anódica, pulido electrolítico, chorro de arena, etc., pueden mejorar en gran medida la absorción de energía del haz en la superficie.
Las investigaciones han demostrado que la eliminación de la película de óxido de las aleaciones de aluminio aumenta su tendencia a formar grietas de cristalización. Para evitar dañar el estado de la superficie de la aleación de aluminio y, al mismo tiempo, simplificar el proceso de soldadura láser, se puede aumentar la temperatura de la superficie de la pieza antes de soldarla, lo que mejorará la tasa de absorción del láser por parte del material.
La soldadura láser se divide en dos categorías: láser pulsado y láser continuo. Los láseres pulsados con una longitud de onda de 1064 nm tienen un haz muy concentrado, y la energía de punto único del pulso es mayor que la de los láseres continuos. Sin embargo, la energía de los láseres pulsados suele ser limitada, por lo que son más adecuados para soldar materiales de paredes finas.
Soldadura por impulsos
Al realizar una soldadura láser, es importante seleccionar la forma de onda de soldadura adecuada. Las formas de onda de pulso más comunes son la onda cuadrada, la onda de pico y la onda de doble pico. Normalmente, las ondas de pulso duran milisegundos. Durante un pulso láser, la reflectividad del metal cambia drásticamente. Las aleaciones de aluminio tienen una alta reflectividad a la luz, lo que significa que 60-98% de la energía láser que incide en la superficie del material puede perderse debido a la reflexión. Esta reflectividad cambia con la temperatura de la superficie.
La onda aguda y la onda de doble pico son las mejores opciones para soldar aleaciones de aluminio, ya que la fase ascendente de la onda proporciona más energía para fundir la aleación de aluminio. Una vez que se forma un "pequeño orificio" en la pieza, la tasa de absorción del metal líquido al láser aumenta rápidamente durante la soldadura de penetración profunda. En este punto, es importante reducir rápidamente la energía del láser y realizar la soldadura a baja potencia para evitar salpicaduras.
La parte de ralentización de la forma de onda de soldadura tiene una anchura de impulso mayor, lo que reduce eficazmente la formación de poros y grietas. Esta forma de onda hace que la soldadura se funda y solidifique repetidamente, reduciendo la velocidad de solidificación del baño de fusión. La forma de onda puede ajustarse según sea necesario al soldar diferentes tipos de muestras.
Figura 1 Forma de onda del impulso de soldadura de una aleación de aluminio
Seleccionar la cantidad adecuada de desenfocar también puede minimizar la formación de poros. El cambio en el desenfoque tiene un impacto significativo en la formación de la superficie de soldadura y la penetración. El desenfoque negativo puede aumentar la penetración, mientras que el desenfoque positivo en la soldadura por pulsos puede hacer que la superficie de soldadura sea más lisa y visualmente más atractiva.
Debido a la alta reflectividad de las aleaciones de aluminio a la energía láser, el cabezal de soldadura suele estar inclinado para evitar que el haz láser se refleje verticalmente y dañe el enfoque láser lente. El diámetro de la unión soldada y la superficie de unión efectiva aumentan a medida que aumenta el ángulo de inclinación del láser. Cuando el ángulo de inclinación del láser es de 40° se alcanzan la mayor unión soldada y la mayor superficie de unión efectiva. Sin embargo, la penetración del punto de soldadura y la penetración efectiva disminuyen con el aumento del ángulo de inclinación del láser, y cuando supera los 60°, la penetración efectiva del punto de soldadura y la penetración efectiva disminuyen con el aumento del ángulo de inclinación del láser. penetración de la soldadura disminuye hasta cero. Inclinar el cabezal de soldadura hacia un ángulo determinado puede aumentar la profundidad de penetración y la anchura de la soldadura.
Además, es importante señalar que cuanto mayor sea la velocidad de soldadura, mayor será el riesgo de fisuración. Esto se debe a que una velocidad de soldadura rápida provoca un gran grado de subenfriamiento, lo que hace que los granos de la zona de soldadura se refinen y que crezca un gran número de "cristales de haz" en la misma dirección, lo que aumenta la probabilidad de que se formen grietas en el plano cristalino entre estos cristales de haz. Si la velocidad de soldadura es demasiado rápida, la profundidad de penetración de la soldadura será relativamente escasa.
Soldadura en modo continuo
La soldadura láser tradicional puede provocar fragilización o grietas. En cambio, la soldadura láser continua no tiene el mismo proceso repentino de enfriamiento y calentamiento que la soldadura láser pulsada, lo que provoca menos grietas durante el proceso de soldadura. Además, la soldadura por láser de fibra de la mayoría de las aleaciones de aluminio mejora la tenacidad después de la soldadura y reduce el riesgo de fragilidad.
La soldadura por láser pulsado es adecuada para soldar aluminio puro industrial, con poco riesgo de grietas tras la soldadura. Sin embargo, algunas industrias pueden requerir un pulido superficial posterior a la soldadura, y la soldadura por láser pulsado puede causar abolladuras y aumentar la cantidad de pulido necesario, lo que conlleva un aumento del tiempo de procesamiento y de los costes de producción. Los láseres continuos pueden resolver estos problemas.
Como se muestra en la Figura 2, la comparación de la costura de soldadura de la carcasa de la batería tras la soldadura láser por impulsos y la soldadura láser continua demuestra las ventajas de la soldadura láser continua. Las juntas de soldadura por impulsos son desiguales y presentan superficies socavadas y abolladas, con muchas salpicaduras, y una menor resistencia posterior a la soldadura. En cambio, la soldadura láser continua da como resultado una superficie lisa y uniforme. costura de soldadura superficie, libre de defectos y salpicaduras, sin que se encuentren grietas en el cordón de soldadura.
Figura 2 Pulso y soldadura continua de la aleación Al-Mn
Los cráteres de arco son habituales durante soldadura por arco de argóny lo mismo puede ocurrir durante la soldadura láser. Para minimizar la aparición de pequeños cráteres, se puede establecer una fase de subida y bajada lentas en la forma de onda durante la soldadura, y aumentar la velocidad de soldadura según sea necesario.
La soldadura láser en continuo presenta numerosas ventajas a la hora de soldar aleaciones de aluminio. En comparación con la soldadura métodos de soldaduraLa soldadura láser continua es más eficaz y elimina la necesidad de rellenar el alambre. En comparación con la soldadura láser pulsada, la soldadura láser continua elimina defectos como grietas, poros y salpicaduras, y garantiza que la aleación de aluminio tenga buenas propiedades mecánicas después de la soldadura. Además, no habrá abolladuras después de la soldadura y se reduce la cantidad de pulido y esmerilado necesarios, lo que ahorra en costes de producción.
Sin embargo, es importante tener en cuenta que los láseres continuos tienen un tamaño de punto relativamente pequeño, por lo que la precisión de ensamblaje de la pieza debe ser alta.
La prevención de grietas térmicas es una tecnología crítica para la soldadura láser de aleaciones de aluminio, especialmente para las aleaciones de la serie 6000 que son muy sensibles a las grietas. Si el contenido de ω(Mg2Si) alcanza 1%, es probable que se produzcan grietas en caliente. Para reducir el riesgo de grietas, se pueden añadir elementos de aleación adecuados para ajustar la composición química del baño de fusión, como añadir polvo de Al-Si o Al-Mg-Si.
Además, la alimentación de alambre puede mejorar el efecto de la soldadura y producir un cordón de soldadura uniforme con una dureza mejorada. La introducción de material de relleno aumenta el contenido de Mg y Si en la dendrita en el zona de fusión, lo que conlleva un aumento de la resistencia de la junta debido al efecto de refuerzo de la solución sólida β".
Normalmente, las aleaciones de aluminio 6063 y 6082 se rellenan con alambres de soldadura Al-5Si y Al-7Si, mientras que las placas 6013 y 6056 se sueldan con CO2 y Nd: YAG, respectivamente, y rellenados con alambres de soldadura Al-12Si.
Estabilidad y calidad en la soldadura láser de aleaciones de aluminio.
El objetivo actual de la investigación en soldadura láser de aleaciones de aluminio es el uso de un proceso compuesto que combine la alta densidad de energía de los haces láser con el rango de calentamiento más amplio de los arcos, utilizando los puntos fuertes de ambas fuentes de calor y mejorando sus características de alta densidad de energía y arcos estables.
Para materiales con alta reflectividad, como la aleación de aluminio, la soldadura láser híbrida puede precalentar o fundir la superficie del material utilizando la energía del arco, mejorando significativamente la absorción de la energía láser por la aleación de aluminio.
Shida et al. utilizaron con éxito un láser de CO2 de 10 kW junto con arcos TIG y MIG para soldar aluminio aleaciones. La introducción de arcos mejoró el índice de utilización de la energía láser y aumentó el índice de penetración de la soldadura en 5-20%. El resultado fue una superficie de soldadura lisa y bien formada.
La soldadura híbrida por láser amplía el tamaño del baño de fusión y modifica las condiciones de flujo del material en estado fundido mediante el acoplamiento de haces y arcos láser, lo que resulta beneficioso para eliminar los poros.
La eliminación de los orificios de aire en la soldadura de aleaciones de aluminio también puede lograrse mediante la soldadura de doble haz. Para la soldadura de doble haz se utilizó un láser de fibra continua de 6 kW. soldadura a tope de aleación de aluminio 5052, y se estudiaron los efectos de los modos de soldadura de dos haces en paralelo y en serie y de las diferentes velocidades de soldadura sobre la morfología y la estructura del cordón. La investigación descubrió que la soldadura paralela de dos haces producía grandes agujeros en las soldaduras, mientras que la soldadura en serie de aleaciones de aluminio producía una buena formación de la soldadura sin poros.
Bajo la influencia de láseres de alta potencia, los principales defectos en la soldadura por penetración profunda con láser de aleaciones de aluminio son la porosidad, el colapso de la superficie y la socavación. Los defectos de colapso superficial y socavado pueden mejorarse mediante la soldadura láser de relleno con alambre o la soldadura híbrida por arco láser. Sin embargo, controlar los defectos de porosidad es todo un reto.
Las investigaciones han demostrado que existen dos tipos de poros característicos en la soldadura por penetración profunda con láser de aleaciones de aluminio. Un tipo son los poros metalúrgicos, causados por la contaminación del material o la intrusión de aire durante el proceso de soldadura, similar a la soldadura por fusión de arco. El otro tipo es la porosidad de proceso, causada por la fluctuación inestable de pequeños orificios inherente al proceso de soldadura por penetración profunda con láser.
Durante la soldadura por penetración profunda con láser, el pequeño orificio suele ir a la zaga del movimiento del haz debido a la viscosidad del metal líquido, y su diámetro y profundidad fluctúan bajo la influencia del plasma/vapor de metal. A medida que el haz se mueve y fluye el metal del baño fundido, la soldadura de penetración profunda incompleta se cierra debido al flujo del metal del baño fundido, provocando la aparición de burbujas en la punta del pequeño orificio. En la soldadura de penetración profunda completa, las burbujas aparecen en la cintura del pequeño orificio del centro.
Estas burbujas migran y ruedan con el flujo de metal líquido, escapan de la superficie del baño de fusión o son empujadas hacia el interior del pequeño orificio. Cuando las burbujas son solidificadas por el baño de fusión y capturadas por el frente metálico, se convierten en poros de soldadura.
Los poros metalúrgicos pueden controlarse mediante un tratamiento superficial previo a la soldadura y una protección adecuada contra los gases durante el proceso de soldadura. La clave para controlar los poros del proceso es garantizar la estabilidad durante el proceso de soldadura por penetración profunda con láser.
De acuerdo con la investigación sobre la tecnología nacional de soldadura láser, el control de los agujeros de aire en la soldadura por penetración profunda con láser de aleaciones de aluminio requiere la consideración de todos los eslabones, incluyendo antes de la soldadura, el proceso de soldadura y el tratamiento posterior a la soldadura. Esto puede lograrse mediante los siguientes nuevos procesos y tecnologías.
Método de tratamiento previo a la soldadura
El tratamiento superficial previo a la soldadura es un método eficaz para controlar los poros metalúrgicos en la soldadura láser de aleaciones de aluminio. Los métodos habituales de tratamiento de superficies incluyen la limpieza física mecánica y la limpieza química. Recientemente, también ha surgido la limpieza por impacto láser, que mejora aún más la automatización de la soldadura láser.
Control de la optimización de la estabilidad de los parámetros
Los parámetros del proceso de soldadura láser de aleaciones de aluminio suelen incluir la potencia del láser, el desenfoque, la velocidad de soldadura y la composición y el flujo del gas de protección. Estos parámetros no sólo influyen en el efecto protector de la zona de soldadura, sino que también afectan a la estabilidad del proceso de soldadura por penetración profunda con láser, que a su vez afecta a porosidad de la soldadura.
Mediante la soldadura por penetración profunda con láser de chapas de aleación de aluminio, se ha descubierto que la estabilidad de la penetración de pequeños orificios influye en la estabilidad del baño de fusión, lo que repercute en la formación de la soldadura y da lugar a defectos de porosidad. Además, la estabilidad de la soldadura por penetración profunda con láser está relacionada con la adecuación de la densidad de potencia láser y la energía lineal.
Por lo tanto, la determinación de parámetros de proceso razonables para la formación de soldaduras estables es un método eficaz para controlar la porosidad de la soldadura láser de aleaciones de aluminio. Los resultados de la investigación sobre las características de formación de soldaduras estables de penetración total han demostrado que la relación entre la anchura de la parte posterior de la soldadura y la anchura de la superficie de la soldadura (relación de anchura de la parte posterior de la soldadura) se puede utilizar para evaluar la formación de la soldadura y la estabilidad de las chapas de aleación de aluminio.
Al ajustar adecuadamente la densidad de potencia láser y la energía de línea durante la soldadura láser de placas finas, se puede garantizar una determinada relación de anchura de retroceso de la soldadura, controlando eficazmente la porosidad de la soldadura.
Soldadura láser por puntos dobles
La soldadura láser por puntos dobles se refiere a un proceso de soldadura en el que dos haces láser enfocados actúan simultáneamente sobre el mismo baño de soldadura. En la soldadura por penetración profunda con láser, una de las principales causas de la porosidad de la soldadura es el cierre de gas en el pequeño orificio del baño de soldadura.
Al utilizar la soldadura láser de doble punto, la apertura del pequeño orificio aumenta debido a la influencia de dos fuentes de luz, lo que facilita la salida del vapor metálico interno y mejora la estabilidad del pequeño orificio, reduciendo así la porosidad de la soldadura.
Los estudios sobre la soldadura láser de las aleaciones de aluminio A356, AA5083, 2024 y 5A90 han demostrado que la soldadura láser de doble punto puede reducir significativamente la porosidad de la soldadura.
Soldadura híbrida por arco láser
La soldadura híbrida láser-arco es un método de soldadura en el que tanto el láser como el arco influyen en el mismo baño de fusión. Normalmente, el láser es la principal fuente de calor, y la interacción entre el láser y el arco mejora la penetración y la velocidad de soldadura de la soldadura láser, al tiempo que reduce la precisión del ensamblaje de la soldadura.
El uso de alambre de relleno ayuda a controlar la microestructura y las propiedades de las juntas soldadas, y el efecto auxiliar del arco mejora la estabilidad de los orificios de soldadura láser, contribuyendo a reducir la porosidad de la soldadura.
En el proceso de soldadura híbrida por arco láser, el arco afecta a la nube de vapor metálico/plasma generada por el proceso láser, favoreciendo la absorción de la energía láser y la estabilidad de los pequeños orificios.
Los estudios sobre la soldadura híbrida por arco láser de aleaciones de aluminio han confirmado su eficacia para reducir la porosidad de la soldadura.
Soldadura por láser de fibra
El efecto de ojo de cerradura en la soldadura por penetración profunda con láser se produce debido a la fuerte vaporización del metal bajo la influencia del láser. La fuerza de vaporización del metal está estrechamente relacionada con la densidad de potencia del láser y la calidad del haz, lo que afecta tanto a la penetración de la soldadura láser como a la estabilidad de los orificios.
Seiji et al. estudiaron el acero inoxidable SUS304 láser de fibra de alta potencia y demostraron que:
Durante la soldadura a alta velocidad, el baño de fusión se alarga, las salpicaduras se controlan, las fluctuaciones del orificio pequeño son estables y no hay burbujas en la punta del orificio pequeño. Cuando se utiliza un láser de fibra para la soldadura de alta velocidad soldadura de titanio y aleaciones de aluminio, también se puede producir una soldadura sin poros.
Investigación sobre gas protector tecnología de control para la soldadura por láser de fibra de aleaciones de titanio por Allen et al. s¿Qué te parece?
Al controlar la posición del gas de protección de soldaduraDe este modo, es posible evitar la implicación de gas, disminuir el tiempo de cierre del pequeño orificio, estabilizar el pequeño orificio de soldadura y alterar el comportamiento de solidificación del baño de fusión, reduciendo así la porosidad de la soldadura.
Soldadura por láser pulsado
En comparación con la soldadura láser continua, el modo de pulso de la salida láser puede mejorar el flujo periódico y constante del baño de fusión, lo que ayuda a la liberación de burbujas y reduce la porosidad de la soldadura.
T.Y. Kuo y S.L. Jeng investigaron el impacto del modo de salida de potencia de soldadura láser YAG sobre la porosidad y las características de las soldaduras realizadas con acero inoxidable SUS 304L y la superaleación Inconel 690.
Los resultados indican que para la soldadura por láser de pulsos de onda cuadrada, a medida que la potencia de base aumenta hasta 1700W, la porosidad de la soldadura disminuye con el aumento de la amplitud del pulso ΔP. Concretamente, la porosidad del acero inoxidable disminuye de 2,1% a 0,5%, y la de la superaleación disminuye de 7,1% a 0,5%.
Tecnología de tratamiento de compuestos posterior a la soldadura
En aplicaciones prácticas de ingeniería, a pesar del estricto tratamiento de la superficie antes de la soldadura y de un proceso de soldadura estable, la porosidad sigue siendo un problema común en la soldadura láser de aleaciones de aluminio.
Por lo tanto, los métodos de tratamiento post-soldadura para eliminar la porosidad son cruciales.
Actualmente, el principal método utilizado es la soldadura modificada.
Uno de estos métodos para eliminar la porosidad interna y por contracción en el aluminio fundiciones de aleación es la tecnología de prensado isostático en caliente.
Al combinar esto con el tratamiento térmico de tensión después de la soldadura láser de aleación de aluminio, se forma un proceso compuesto de prensado isostático en caliente y tratamiento térmico de componentes de soldadura láser de aleación de aluminio. Esto no solo elimina la porosidad de la soldadura, sino que también mejora el rendimiento de la unión.
La aplicación de la soldadura láser de alta potencia en aleaciones de aluminio sigue planteando muchos retos debido a sus características únicas.
Uno de los principales retos es controlar los defectos de porosidad de la soldadura y mejorar calidad de soldadura.
Para mejorar la estabilidad del proceso de soldadura y controlar la porosidad en la soldadura láser de aleaciones de aluminio, es esencial un enfoque global que tenga en cuenta todos los aspectos, desde la presoldadura hasta el proceso de soldadura y el tratamiento postsoldadura.
Para hacer frente a este reto, se han desarrollado varias tecnologías y procesos nuevos, como la limpieza por láser antes de la soldadura, la optimización de los parámetros del proceso de soldadura mediante el control de la relación de anchura de retroceso, la soldadura por láser de doble haz, la soldadura híbrida láser-arco, la soldadura por láser de pulsos y láser de fibra óptica soldadura.