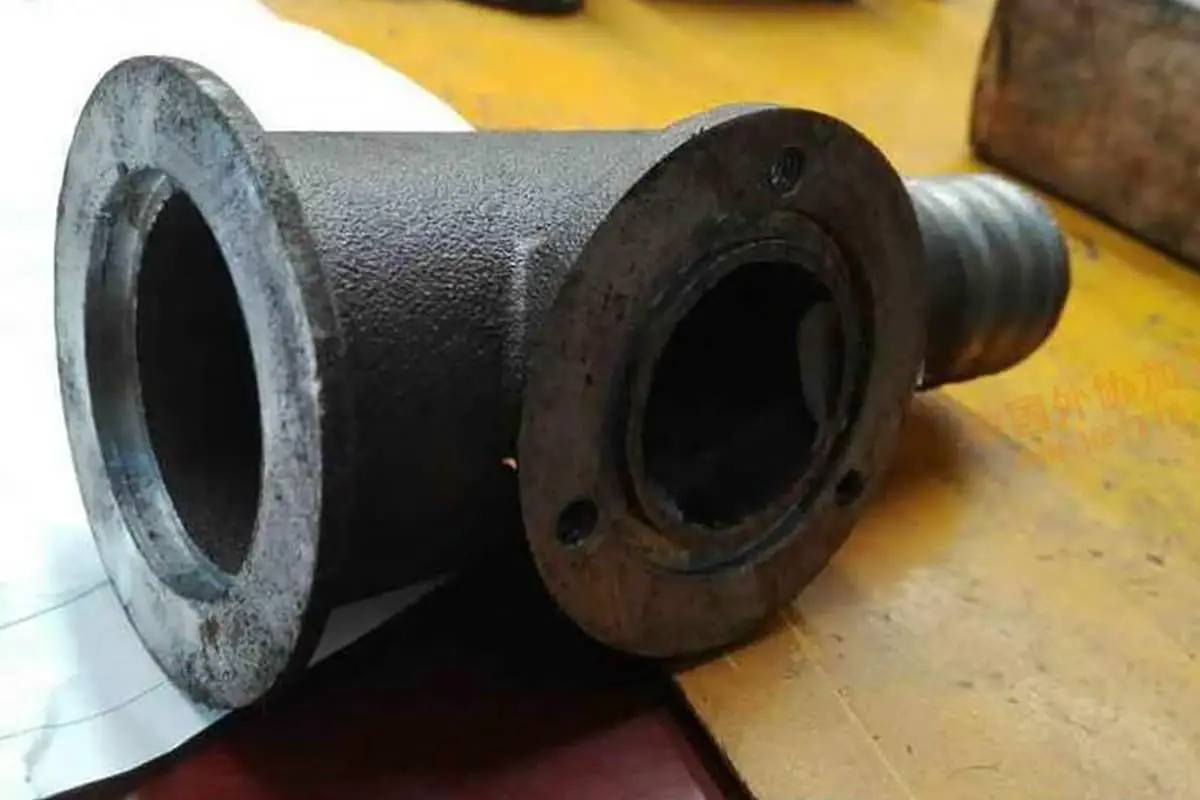
¿Alguna vez se ha preguntado cómo una maquinaria compleja se mantiene unida a la perfección? Este artículo se adentra en el fascinante mundo de la soldadura a tope, un método muy eficaz para unir metales. Conocerá sus aplicaciones, tipos y la ciencia que hay detrás de su eficacia. Prepárese para descubrir los secretos de esta técnica de soldadura esencial.
La soldadura por resistencia a tope, comúnmente conocida como soldadura a tope, es una sofisticada técnica de soldadura por resistencia que utiliza el calor generado por la resistencia eléctrica para unir simultáneamente dos piezas de trabajo a lo largo de todas sus caras extremas. Este proceso crea un cordón de soldadura fuerte y continuo sin necesidad de material de relleno.
La alta productividad, la facilidad de automatización y la versatilidad de la soldadura a tope han llevado a su adopción generalizada en diversas industrias. Sus aplicaciones pueden clasificarse en cuatro áreas principales:
La soldadura a tope se clasifica en soldadura a tope por resistencia y soldadura a tope por destello.
La soldadura a tope por resistencia consiste en presionar continuamente las caras extremas de dos piezas, calentarlas hasta que adquieran un estado plástico mediante calor por resistencia y, a continuación, aplicar rápidamente presión de forja (o mantener la presión de soldadura sin añadir presión de forja) para completar la soldadura.
(1) Resistencia y calentamiento en la soldadura por resistencia a tope
La distribución de la resistencia durante la soldadura a tope es la que se muestra en la figura 14-2. La resistencia total puede representarse mediante la siguiente fórmula:
R=2Rω+Rc+2Reω
Dónde,
Dado que la resistencia de contacto entre la pieza y el electrodo es pequeña y se encuentra lejos de la superficie de unión, a menudo no se tiene en cuenta. La resistencia interna de la pieza es proporcional a la resistividad ρ del metal soldado y a la longitud l0 de la pieza que se extiende desde el electrodo, e inversamente proporcional al área de la sección transversal s de la pieza.
Al igual que con soldadura por puntosLa resistencia de contacto en la soldadura por resistencia a tope depende del estado de la superficie, la temperatura y la presión de la superficie de contacto. Cuando hay óxidos apreciables u otras impurezas en la superficie de contacto, la resistencia de contacto aumenta. Los aumentos de temperatura o presión disminuirán la resistencia de contacto debido al aumento de la superficie de contacto real.
Al principio de la soldadura, la densidad de corriente en el punto de contacto es alta; una vez que la temperatura de la cara final aumenta rápidamente, la resistencia de contacto disminuye drásticamente. Cuando se calienta a cierta temperatura (600 grados para el acero, 350 grados para la aleación de aluminio), la resistencia de contacto desaparece por completo.
Al igual que la soldadura por puntos, la fuente de calor de la soldadura a tope también procede del calor por resistencia generado en la zona de soldadura. Durante la soldadura a tope por resistencia, la resistencia de contacto existe durante un tiempo extremadamente corto, y el calor producido representa menos de 10-15% del calor total.
Sin embargo, como esta porción de calor se genera en una zona muy estrecha cerca de la superficie de contacto, provocará un rápido aumento de la temperatura en esta zona y un rápido aumento de la resistencia interna. Aunque la resistencia de contacto desaparezca por completo, la intensidad del calor en esta zona sigue siendo superior a la de otras zonas.
Cuanto más duras sean las condiciones de soldadura utilizadas (es decir, cuanto mayor sea la corriente y menor el tiempo de electrificación), y cuanto menor sea la fuerza de compresión de la pieza, más pronunciado será el impacto de la resistencia de contacto en el calentamiento.
(2) Culo Soldadura por resistencia Ciclo, parámetros de proceso y preparación de la pieza de trabajo
1) Ciclo de soldadura:
Durante la soldadura a tope por resistencia, dos piezas siempre se presionan entre sí. Cuando la temperatura de la cara frontal alcanza el temperatura de soldadura Tω, la distancia entre las dos caras extremas de las piezas es de sólo unos pocos angstroms, y los átomos entre las caras extremas interactúan entre sí, produciendo granos comunes en la unión, formando una soldadura.
Existen dos tipos de ciclos de soldadura en la soldadura por resistencia a tope: isobárico y de presión de forja aumentada.
El primero tiene un mecanismo de presurización sencillo y es fácil de aplicar. El segundo ayuda a mejorar calidad de soldaduraSe utiliza principalmente para la soldadura a tope por resistencia de aceros aleados, metales no ferrosos y sus aleaciones.
Para obtener una deformación plástica suficiente y mejorar aún más la calidad de la unión, también debe establecerse un programa de recalcado con corriente eléctrica.
2) Parámetros del proceso:
Los principales parámetros del proceso de soldadura a tope por resistencia son: longitud de la protuberancia, corriente de soldadura (o densidad de corriente de soldadura), tiempo de encendido de la soldadura, presión de soldadura y presión de recalcado.
(a) Longitud de protrusión l0:
La longitud que la pieza sobresale de la cara del extremo del electrodo de la mordaza. Al elegir la longitud de la protuberancia, deben tenerse en cuenta dos factores: la estabilidad de la pieza durante el recalcado y la disipación de calor a la mordaza.
Si l0 es demasiado largo, la pieza será inestable y se doblará durante el recalcado. Si l0 es demasiado corto, debido a la mayor disipación de calor a la mordaza, la pieza se enfriará demasiado, dificultando la deformación plástica. Para una pieza con un diámetro d, generalmente acero bajo en carbono: l0=(0,5-1)d, aluminio y latón: l0=(1-2)d, cobre: l0=(1,5-2,5)d.
(b) Corriente de soldadura Iω y tiempo de soldadura tω:
Durante la soldadura por resistencia a tope, la corriente de soldadura suele expresarse en términos de densidad de corriente jω. jω y tω son los dos parámetros principales que determinan el calentamiento de la pieza. Ambos pueden ajustarse en consecuencia dentro de un rango determinado. Pueden adoptarse tanto una densidad de corriente grande y un tiempo corto (condiciones fuertes), como una densidad de corriente pequeña y un tiempo largo (condiciones débiles).
Sin embargo, si las condiciones son demasiado fuertes, es fácil que se produzcan defectos de no penetración; si las condiciones son demasiado blandas, se producirá una oxidación grave de la cara del extremo de la interfaz, granos gruesos en la zona de la junta y afectará a la resistencia de la junta.
(c) Presión de soldadura Fω y presión de recalcado Fu:
Fω afecta tanto a la generación de calor como a la deformación plástica en la junta. Reducir Fω es beneficioso para la generación de calor, pero no para la deformación plástica.
Por lo tanto, es fácil calentar con un Fω menor y recalcar con un Fu mucho mayor. Sin embargo, Fω no puede ser demasiado bajo, ya que de lo contrario se producirían salpicaduras, aumentaría la oxidación de la cara frontal y se aflojaría cerca de la interfaz.
3) Preparación de la pieza:
En la soldadura por resistencia a tope, la forma de la cara extrema y el tamaño de las dos piezas deben ser iguales para garantizar un calentamiento y una deformación plástica uniformes de las piezas. La cara extrema de la pieza de trabajo y la superficie en contacto con la pinza deben limpiarse rigurosamente.
Los óxidos y la suciedad en la cara del extremo afectarán directamente a la calidad de la unión. Los óxidos y la suciedad en la superficie de la pieza de trabajo en contacto con la abrazadera aumentarán la resistencia de contacto, provocando la quemadura de la superficie de la pieza de trabajo, un mayor desgaste de la abrazadera y una mayor pérdida de potencia.
La pieza puede limpiarse con medios mecánicos, como muelas y cepillos de alambre, o con un lavado al ácido.
Las inclusiones de óxido se producen fácilmente en la resistencia uniones soldadas. Para metales raros, algunos aceros aleados y metales no férreos con elevados requisitos de calidad de soldadura, suelen utilizarse atmósferas protectoras como el argón y el helio.
Aunque la soldadura a tope por resistencia tiene ventajas como las juntas lisas, las rebabas pequeñas y la sencillez. proceso de soldadurasus propiedades mecánicas de unión son relativamente bajas, y la preparación de la cara del extremo de la pieza de trabajo requiere alta, por lo que sólo se utiliza para la soldadura a tope de pequeña sección transversal (menos de 250mm2) perfiles metálicos.
La soldadura a tope por chisporroteo puede dividirse en soldadura a tope por chisporroteo continuo y soldadura a tope por chisporroteo con precalentamiento. Ambas constan de dos fases principales: la fase de destello y la fase de forja. La soldadura a tope por destello con precalentamiento sólo añade una fase de precalentamiento antes de la fase de destello.
1. Las dos etapas de la soldadura a tope por chisporroteo
1. Fase intermitente
La función principal del flasheo es calentar las piezas. En esta fase, primero se enciende la fuente de alimentación y se ponen ligeramente en contacto los extremos de las dos piezas, creando numerosos puntos de contacto. Cuando pasa la corriente, los puntos de contacto se funden, formando puentes de metal líquido que conectan los dos extremos.
Debido a la altísima densidad de corriente en estos puentes, el metal líquido se evapora y los puentes estallan. A medida que la pinza móvil avanza lentamente, se forman y revientan continuamente nuevos puentes. Bajo la acción de la presión del vapor y la fuerza electromagnética, las partículas de metal líquido salen continuamente pulverizadas por el hueco entre las juntas, formando un chorro de chispas, o flash.
Durante el proceso de destello, las piezas se acortan gradualmente, y la temperatura de los extremos también aumenta gradualmente. A medida que aumenta la temperatura de los extremos, se acelerará la velocidad de ruptura del puente, y la velocidad de avance de la pinza móvil también debe aumentar gradualmente.
Antes de finalizar el proceso de flasheado, es necesario formar una capa de metal líquido en toda la superficie final de la pieza, y llevar el metal a una temperatura de deformación plástica a cierta profundidad.
Debido a la fuerte oxidación del vapor metálico y de las partículas metálicas producida por la rotura del puente, el contenido de oxígeno del medio gaseoso en la separación interfacial disminuye, reduciendo su capacidad de oxidación y mejorando así la calidad de la unión.
Sin embargo, el parpadeo debe ser estable e intenso. Estabilidad significa que no se produzca ningún circuito abierto o cortocircuito durante el proceso de intermitencia. Un circuito abierto debilita la autoprotección del junta de soldadura, provocando una fácil oxidación de la junta. Un cortocircuito puede provocar la sobrecombustión de la pieza de trabajo, provocando su desguace.
La intensidad se refiere a un número considerable de ráfagas de puente por unidad de tiempo. Cuanto más intenso sea el destello, mejor será la autoprotección de la junta de soldadura, especialmente en la fase posterior del destello.
2. Fase de forja
Al final de la fase de flasheo, se aplica inmediatamente a las piezas una presión final suficiente, la separación entre las juntas disminuye rápidamente, el puente deja de reventar y comienza la fase de forja.
El propósito de la forja es sellar el hueco y el agujero de fuego dejados por la rotura del puente en la superficie del extremo de la pieza, extruir el metal líquido y las inclusiones oxidadas de la superficie del extremo, hacer que el metal plástico limpio entre en estrecho contacto y producir cierta deformación plástica en la zona de unión. Esto promueve la recristalización, forma granos comunes y obtiene una unión firme.
Aunque hay metal fundido durante el proceso de calentamiento de la soldadura flash a tope, se trata esencialmente de una soldadura en estado plástico.
La soldadura a tope por destello con precalentamiento calienta primero la pieza con impulsos intermitentes de corriente antes de entrar en las fases de destello y forja.
Los objetivos del precalentamiento son los siguientes:
(a) Reducir el consumo de energía: Las piezas más grandes pueden soldarse en una máquina de soldar de menor capacidad. Sin precalentar la pieza a una temperatura determinada, es imposible iniciar un proceso de destello continuo cuando la capacidad de la máquina de soldar es insuficiente.
(b) Reducir la velocidad de enfriamiento tras la soldadura: Esto es beneficioso para evitar que las uniones de acero templado produzcan estructuras templadas y grietas durante el enfriamiento.
(c) Acortar el tiempo de intermitencia: Esto puede reducir el tiempo de destello y ahorrar metales preciosos.
Los inconvenientes del precalentamiento son:
(a) Prolonga el ciclo de soldadura y reduce la productividad.
(b) Hace más compleja la automatización del proceso.
(c) El control del precalentamiento es más difícil. Si el grado de precalentamiento es inconsistente, se reducirá la estabilidad de la calidad de la unión.
2. Resistencia y calentamiento en la soldadura Flash Butt
La resistencia de contacto (Rc) durante la soldadura flash a tope es la resistencia total a través de los puentes de metal líquido entre las caras extremas de las dos piezas. La magnitud de Rc viene determinada por el número y el área de la sección transversal de estos puentes, ambos influidos por el área de la sección transversal de la pieza de trabajo, la densidad de corriente y la velocidad a la que las piezas de trabajo se aproximan entre sí. A medida que aumentan estos parámetros, también aumentan el número y el área de la sección transversal de los puentes, con lo que disminuye Rc.
La soldadura a tope por chisporroteo tiene una Rc significativamente mayor que la soldadura por resistencia, que persiste durante toda la fase de chisporroteo. Aunque su resistencia disminuye gradualmente, sigue siendo mayor que la resistencia interna de la pieza hasta el momento en que comienza la forja, momento en el que Rc desaparece por completo.
La Figura 14-5 muestra las variaciones típicas de Rc, 2Rω y R durante la soldadura flash a tope. La disminución de Rc se atribuye al aumento del número y tamaño de los puentes debido al aumento de la temperatura de las caras extremas y a la creciente velocidad de aproximación de las piezas durante el proceso de flash.
Dado que Rc es grande y dura toda la fase de destello, el calentamiento en las uniones de soldadura a tope por destello depende principalmente de Rc.
3. Ciclo de soldadura, parámetros del proceso y preparación de la pieza para la soldadura a tope por chisporroteo
1. Ciclo de soldadura
El ciclo de soldadura a tope por destello, como se muestra en la Figura 14-7, incluye el tiempo de restablecimiento, es decir, el tiempo que tarda el móvil en soldar. sujeción que las mordazas vuelvan a su posición original después de soltar la pieza. Existen dos métodos de precalentamiento: precalentamiento por resistencia y precalentamiento rápido.
2. Parámetros del proceso
Los principales parámetros de la soldadura a tope por chisporroteo son: longitud de la protuberancia, corriente de chisporroteo, volumen de chisporroteo, velocidad de chisporroteo, volumen de recalcado, velocidad de recalcado, presión de recalcado, corriente de recalcado y fuerza de apriete de la pinza. La Figura 14-8 ilustra los volúmenes y longitudes de protrusión en la soldadura continua a tope por destello. A continuación se explica cómo afecta cada parámetro a la calidad de la soldadura y los principios para su selección:
(a) Longitud de protrusión (l0)
Al igual que la soldadura por resistencia, l0 afecta a la distribución de la temperatura a lo largo del eje de la pieza y a la deformación plástica de la unión. Además, al aumentar l0, también aumentan la impedancia del circuito de soldadura y la potencia necesaria. Para materiales de varilla y tubos de pared gruesa, l0 suele ser (0,7-1,0)d, donde d es el diámetro del material de varilla redonda o la longitud lateral del material de varilla cuadrada.
Para chapas finas (δ=1-4mm) para garantizar la estabilidad durante el volteo, l0 suele ser (4-5)δ.
En soldadura de diferentes metalesPara conseguir una distribución homogénea de la temperatura en ambas piezas, el l0 del metal con menor conductividad eléctrica y térmica debe ser menor. En la tabla 1 se indican los valores de referencia de l0 para la soldadura rápida a tope. diferentes metales.
(b) Corriente de reposo (If) y corriente de perturbación (Iu)
Si viene determinado por el área de la sección transversal de la pieza y la densidad de corriente (jf) necesaria para el destello. La magnitud de jf está relacionada con las propiedades físicas del metal que se está soldando, la velocidad de destello, el área y la forma de la sección transversal de la pieza de trabajo y el estado de calentamiento de la cara extrema. Durante el proceso de flasheo, a medida que vf aumenta gradualmente y Rc disminuye, jf también aumentará. Durante el recalcado, al desaparecer rápidamente Rc, la corriente aumentará hasta alcanzar la corriente de recalcado (Iu).
Tabla 1 Longitudes de protrusión para la soldadura a tope por chisporroteo de diferentes metales
Tipos de metales | Longitud extendida (mm) | ||
Izquierda | Derecha | Izquierda | Derecha |
Acero bajo en carbono | Acero austenítico | 1.2d | 0.5d |
Acero medio carbono | Acero rápido | 0.75d | 0.5d |
Acero | Latón | 1.5d | 1.5d |
Acero | Cobre | 2.5d | 1.0d |
Nota: d se refiere al diámetro de la pieza (mm).
Cuando se sueldan piezas de acero de sección transversal grande, para aumentar la profundidad de calentamiento de la pieza, debe adoptarse una velocidad de destello más lenta, y la densidad de corriente media utilizada no suele superar los 5A/mm2. La tabla 2 muestra los valores de referencia para la densidad de corriente (jf) y la energía eléctrica (ju) cuando se sueldan a tope piezas con una sección transversal de 200-1000mm2.
Tabla 2: Valores de referencia para la densidad de corriente (jf) y la energía eléctrica (ju) durante el soldeo a tope por chispa
Tipos de metales | jf (A/mm2) | jf(A/mm2) | |
Valor medio | Valor máximo | ||
Acero bajo en carbono | 5-15 | 20-30 | 40-60 |
Alta Acero aleado | 10-20 | 25-35 | 35-50 |
Aleación de aluminio | 15-25 | 40-60 | 70-150 |
Aleación de cobre | 20-30 | 50-80 | 100-200 |
Aleación de titanio | 4-10 | 15-25 | 20-40 |
La magnitud de la corriente viene determinada por la tensión en vacío, U20, del transformador de soldadura. Así, en la producción real, se suele fijar la tensión secundaria en vacío. Al seleccionar U20, es necesario tener en cuenta la impedancia del circuito de soldadura. Una mayor impedancia requiere un aumento correspondiente de U20. Cuando se sueldan piezas de gran sección transversal, a veces se utiliza un método de ajuste de la tensión secundaria por etapas. Inicialmente, se utiliza una U20 más alta para iniciar el arco, y luego se reduce a un valor adecuado.
(c) Caudal Flash δf
El volumen de intermitencia, δf, debe elegirse de modo que se forme una capa de metal fundido en toda la cara extrema de la pieza al final de la intermitencia, alcanzando al mismo tiempo la temperatura de deformación plástica a cierta profundidad. Si δf es demasiado pequeño, no podrá cumplir estos requisitos, lo que afectará a la calidad de la soldadura. Por el contrario, si δf es demasiado grande, resulta en un desperdicio de material metálico y reduce la productividad. La selección de δf también debe tener en cuenta si hay precalentamiento, ya que el precalentamiento de la soldadura a tope por destello puede reducir δf en 30-50% en comparación con la soldadura a tope por destello continua.
(d) Velocidad del flash vf
La velocidad del destello, vf, debe ser suficiente para garantizar la intensidad y la estabilidad del destello. Sin embargo, si vf es demasiado alta, se estrecha la zona de calentamiento, aumentando la dificultad de deformación plástica. Además, la corriente de soldadura requerida aumenta, profundizando la profundidad de la entalla tras el estallido del haz, lo que reduce la calidad de la unión. Al seleccionar vf, deben tenerse en cuenta los siguientes factores:
1) La composición y propiedades del material a soldar. Los materiales con muchos elementos fácilmente oxidables o buena conductividad y conductividad térmica requieren una vf mayor. Por ejemplo, soldar acero inoxidable austenítico y aleaciones de aluminio requiere una vf mayor que soldadura de acero con bajo contenido en carbono.
2) Si hay precalentamiento. El precalentamiento facilita el inicio de un destello, por lo que se puede aumentar la vf.
3) Antes del recalcado debe producirse un fuerte destello. La vf debe ser alta para garantizar una capa de metal uniforme en la cara del extremo.
(e) Caudal de forja sobrepasado δu
El volumen de recalcado, δu, influye en la expulsión del metal líquido y en el grado de deformación plástica. Si δu es demasiado pequeño, el metal líquido permanece en la interfaz, lo que puede causar defectos como aflojamiento, contracción y grietas. Si δu es demasiado grande, la tenacidad al impacto de la junta se reduce debido a la flexión severa del límite de grano. δu se selecciona en función del área de la sección transversal de la pieza, aumentando a medida que aumenta el área de la sección transversal.
Durante el recalcado, para evitar la oxidación de las interfaces, la corriente no se corta inmediatamente antes de que se cierren las interfaces de las caras frontales. Por lo tanto, el volumen de recalcado debe incluir dos partes: el volumen con corriente y el volumen sin corriente, siendo el primero 0,5-1 veces el segundo.
(f) Velocidad de forja vu
La velocidad de recalcado, vu, debe ser lo más rápida posible para evitar dificultades en la expulsión del metal líquido y la deformación plástica del metal en la interfase debido al enfriamiento del metal, así como para evitar la oxidación del metal de la cara final. La velocidad mínima de recalcado depende de las propiedades del metal.
Por ejemplo, la velocidad mínima de recalcado para soldar acero austenítico es el doble que la del acero perlítico. Los materiales con buena conductividad térmica, como aleaciones de aluminiorequieren una velocidad de recalcado elevada (150-200 mm/s). Para el mismo metal, un mayor gradiente de temperatura en la interfaz requiere una mayor velocidad de recalcado debido a un enfriamiento más rápido de la junta.
(g) Presión de Forja Fu
La presión de recalcado, Fu, suele representarse como una presión por unidad de superficie, también conocida como tensión de recalcado. La magnitud de la tensión de recalcado debe ser suficiente para expulsar el metal líquido de la interfaz y generar una cierta cantidad de deformación plástica en la junta. Si la tensión de recalcado es demasiado baja, la deformación es insuficiente, lo que reduce la resistencia de la unión. Si la tensión de recalcado es demasiado alta, la deformación es excesiva, provocando una flexión severa del límite de grano y reduciendo así la tenacidad al impacto de la unión.
La magnitud de la tensión de recalcado depende de las propiedades del metal, las características de distribución de la temperatura, el volumen y la velocidad de recalcado y la forma de la sección transversal de la pieza. Los metales resistentes a altas temperaturas requieren una tensión de recalcado elevada.
El aumento del gradiente de temperatura también requiere una mayor tensión de recalcado. Debido al aumento del gradiente de temperatura provocado por una alta velocidad de destello, los metales de soldadura con buena conductividad térmica, tales como cobre y aluminio aleaciones, requiere una tensión de recalcado elevada (150-400Mpa).
(h) Parámetros de precalentamiento para la soldadura a tope por chisporroteo:
Además de los parámetros de proceso mencionados, el temperatura de precalentamiento y la duración. La temperatura de precalentamiento se elige en función de la sección transversal y propiedades del material de la pieza. Al soldar acero con bajo contenido de carbono, la temperatura generalmente no debe superar los 700-900 grados Celsius.
A medida que aumenta la sección transversal de la pieza, la temperatura de precalentamiento debe aumentar proporcionalmente. La duración del precalentamiento depende de la potencia de la máquina de soldar, del tamaño de la sección transversal de la pieza y de las propiedades del metal, y puede variar dentro de un amplio margen. Depende de la temperatura de precalentamiento requerida. Durante el proceso de precalentamiento, la reducción causada por el precalentamiento es pequeña y no se establece como parámetro del proceso.
(i) La fuerza de apriete (Fc) de la pinza debe garantizar que la pieza no resbale durante el forjado.
Fc está relacionado con la presión de forja (Fu) y el coeficiente de fricción (f) entre la pieza y la pinza, siendo la relación: Fc≥Fu/2f. Normalmente, F0= (1,5-4,0)Fu, con el acero de bajo carbono de sección compacta en el límite inferior y el inoxidable laminado en frío chapa de acero en el límite superior. Cuando la pinza está equipada con un dispositivo de apoyo, la fuerza de apriete puede reducirse en gran medida, y en este momento Fc=0,5Fu es suficiente.
3. Preparación de la pieza:
La preparación de la pieza para la soldadura a tope por destello incluye: la geometría de la superficie del extremo, el mecanizado del extremo en blanco y la limpieza de la superficie. Al soldar a tope, la forma geométrica y el tamaño de las caras de unión de las dos piezas deben ser esencialmente idénticos.
De lo contrario, no será posible garantizar un calentamiento y una deformación plástica uniformes de las dos piezas, lo que afectará a la calidad de la unión. En la producción, la diferencia en el diámetro de las piezas de trabajo circulares no debe exceder de 15%, y la de las piezas de trabajo cuadradas y tubulares no debe exceder de 10%.
Cuando se sueldan a tope piezas con una sección transversal grande, es mejor biselar un extremo de la pieza para aumentar la densidad de corriente y facilitar el inicio del destello. En este caso, no es necesario precalentar ni aumentar la tensión secundaria al inicio del destello.
El mecanizado del extremo de la pieza bruta para la soldadura a tope puede realizarse en cizallas, punzonadoras, tornos o mediante corte por plasma o llama, seguido de la limpieza de la cara extrema. En la soldadura a tope por chisporroteo, el metal del extremo se quema durante el chisporroteo, por lo que los requisitos de limpieza de la cara del extremo no son muy estrictos. Sin embargo, los requisitos de limpieza de la superficie de contacto entre la pinza y la pieza deben ser los mismos que para la soldadura a tope por resistencia.
4. Soldadura a tope por chisporroteo de metales comunes:
Casi todos los aceros y metales no férreos pueden soldarse a tope, pero para conseguir uniones de alta calidad es necesario tomar las medidas de proceso adecuadas en función de las propiedades del metal. El análisis es el siguiente:
(1) Conductividad eléctrica y térmica:
Para metales con buena conductividad eléctrica y térmica, se debe utilizar una potencia específica y una velocidad de destello mayores, y un tiempo de soldadura más corto.
(2) Resistencia a altas temperaturas:
Para los metales con alta resistencia a altas temperaturas, es necesario ampliar la región termoplástica y utilizar una fuerza de forja mayor.
(3) Rango de temperatura de cristalización:
Cuanto más amplio sea el intervalo de temperatura de cristalización, más amplia será la zona semifundida. Debe utilizarse una presión de forja y una retención de forja mayores para extrudir todo el metal fundido en la zona semifundida, a fin de evitar que queden agujeros de contracción, holguras, grietas y otros defectos en la unión.
(4) Sensibilidad al calor:
Existen dos situaciones comunes. La primera es la del acero templado, que tras la soldadura es propenso a formar una estructura de temple en la unión, lo que provoca un aumento de la dureza y una disminución de la plasticidad. En casos graves, pueden formarse grietas de temple.
En el acero templado se suele utilizar la soldadura a tope con precalentamiento en una zona de calentamiento amplia, y tras la soldadura se toman medidas de enfriamiento lento y revenido. La segunda situación afecta a los metales reforzados mediante trabajo en frío (como el acero inoxidable austenítico), en los que la unión y la zona afectada por el calor se ablandan durante la soldadura, reduciendo la resistencia de la unión. Al soldar este tipo de metales, se suele utilizar una mayor velocidad de flash y presión de forja para minimizar la zona reblandecida y mitigar el grado de reblandecimiento.
(5) Oxidación: Las inclusiones de óxido en las juntas perjudican seriamente su calidad. Por lo tanto, prevenir y eliminar la oxidación es crucial para mejorar la calidad de las juntas. La formación de oxidación varía con la composición del metal. Si el punto de fusión del óxido formado es inferior al del metal que se está soldando, el óxido posee buena fluidez y se exprime fácilmente durante el forjado.
Si el punto de fusión del óxido es superior al del metal que se está soldando, como SiO2, Al2O3, Cr2O3, sólo pueden expulsarse cuando el metal está todavía en estado fundido. Así, cuando aleación de soldadura aceros que contienen cantidades significativas de silicio, aluminio, cromo y elementos similares, deben adoptarse estrictas medidas de proceso para eliminar completamente los óxidos.
Estas son las características de la soldadura flash más utilizada materiales metálicos:
1) Flash Soldadura de acero al carbono: Estos materiales tienen altos coeficientes de resistencia, protegen la interfaz oxidando los elementos de carbono para proporcionar atmósferas de CO y CO2 durante el calentamiento, y no contienen elementos que formen óxidos de alto punto de fusión.
Por lo tanto, son relativamente fáciles de soldar. Como la contenido de carbono en el acero aumenta, el coeficiente de resistencia, el rango cristalográfico, la resistencia a altas temperaturas y la tendencia al endurecimiento también aumentan.
Por lo tanto, es necesario aumentar la presión de forja y la cantidad de forja en consecuencia. Para mitigar los efectos del endurecimiento, puede utilizarse la soldadura flash de precalentamiento, seguida de un tratamiento térmico posterior a la soldadura.
Al soldar acero al carbono por chisporroteo, el carbono se difunde hacia la cara del extremo calentada y se oxida fuertemente. Durante la forja, el metal fundido de la zona semifundida con un alto contenido de carbono se exprime, formando una capa sin carbono (de aspecto blanco, también llamada banda brillante) en la unión.
La anchura de la capa empobrecida en carbono aumenta con el aumento del contenido de acero y la prolongación del tiempo de precalentamiento; disminuye con el aumento del contenido de carbono y la reducción de la tendencia a la oxidación del medio gaseoso. Un tratamiento térmico prolongado puede eliminar la capa empobrecida en carbono.
La soldadura flash del acero al carbono es la más utilizada. Si las condiciones de soldadura se eligen correctamente, no suelen surgir dificultades. Esto se aplica incluso al hierro fundido, que es difícil de soldar por fusión.
En el hierro fundido se suele utilizar la soldadura por chispa precalentada, ya que la soldadura por chispa continua puede provocar fácilmente la formación de una boca blanca. Debido a su alto contenido en carbono, se produce una cantidad significativa de CO y CO2 se producen atmósferas protectoras durante el parpadeo, lo que proporciona una fuerte autoprotección.
Incluso con fluctuaciones significativas en los parámetros del proceso, sólo existe una pequeña cantidad de inclusiones de óxido en la interfaz.
2) Soldadura Flash de aceros aleados: La influencia del contenido de elementos de aleación en el rendimiento del acero y las medidas de proceso que deben adoptarse son las siguientes:
1) Aluminio, cromo, silicio y molibdeno en el acero forman fácilmente óxidos de alto punto de fusión; para reducir su oxidación, se debe aumentar la velocidad de flasheo y de forja.
2) A medida que aumenta el contenido de elementos de aleación, mejora la resistencia a altas temperaturas, lo que requiere un aumento de la presión de forja.
3) Para aceros perlíticos, como elementos de aleación la tendencia al endurecimiento aumenta, deben tomarse medidas para evitar la fragilidad por endurecimiento.
La tabla siguiente proporciona valores de referencia para los parámetros del proceso de soldadura flash para acero al carbono y acero aleado.
Valores de referencia de los principales parámetros de la soldadura flash para distintos tipos de acero.
Categoría | Velocidad media del flash (mm/s) | Velocidad máxima del flash (mm/s) | Velocidad de forja (mm/s) | Presión máxima de forja (Mpa) | Tratamiento térmico posterior a la soldadura | ||
Flash de precalentamiento | Flash continuo | Flash de precalentamiento | Flash continuo | ||||
Acero bajo en carbono | 1.5-2.5 | 0.8-1.5 | 4-5 | 15-30 | 40-60 | 60-80 | No requiere enfriamiento |
Acero de baja aleación | 1.5-2.5 | 0.8-1.5 | 4-5 | ≥30 | 40-60 | 100-110 | Revenido con enfriamiento lento |
Acero con alto contenido en carbono | ≤1.5-2.5 | 0.8-1.5 | 4-5 | 15-30 | 40-60 | 110-120 | Calor de templado |
Acero perlítico de alta aleación | 3.5-4.5 | 2.5-3.5 | 5-10 | 30-150 | 60-80 | 110-180 | Normalizar el calor |
Acero austenítico | 3.5-4.5 | 2.5-3.5 | 5-8 | 50-160 | 100-140 | 150-220 | Generalmente no es necesario |
Las características de soldadura de los aceros de baja aleación son similares a las de los aceros de medio carbono, mostrando una tendencia al endurecimiento, lo que requiere métodos de tratamiento térmico adecuados. Este tipo de acero tiene una alta resistencia a altas temperaturas y tiende a formar inclusiones de óxido. Requiere una presión de forja más alta y velocidades de flasheo y forja más rápidas.
Alta acero aleado al carbono no sólo presenta las características del acero con alto contenido en carbono, sino que también contiene cierta cantidad de elementos de aleación. Debido a su alto contenido en carbono y al amplio intervalo de temperaturas de cristalización, la zona semifundida en la interfase es amplia.
Si la presión de forja es insuficiente, o la deformación plástica no es suficiente, el metal líquido que queda en la zona semifundida formará una estructura porosa. Además, la presencia de elementos de aleación puede dar lugar a inclusiones de óxido de alto punto de fusión. Por lo tanto, se requieren mayores velocidades de flasheo y forja, mayor presión de forja y mayor cantidad de forja.
Los principales elementos de aleación del acero austenítico son el Cr y el Ni. Este acero tiene una elevada resistencia a altas temperaturas, una escasa conductividad eléctrica y térmica, un punto de fusión bajo (en comparación con los aceros con bajo contenido en carbono) y contiene un gran número de elementos de aleación que pueden formar fácilmente óxidos de alto punto de fusión (como el Cr).
Por lo tanto, requiere una presión de forja significativa y altas velocidades de flasheo y forja. Una alta velocidad de flasheo puede reducir la zona de calentamiento, evitando eficazmente el rápido crecimiento de granos en la zona afectada por el calor y una disminución de la resistencia a la corrosión.
3. Flash Soldadura del aluminio y sus aleaciones:
Estos materiales tienen una buena conductividad eléctrica y térmica, un punto de fusión bajo, se oxidan fácilmente con óxidos de alto punto de fusión y tienen un rango de temperatura plástica estrecho, lo que dificulta la soldadura.
En soldabilidad de la soldadura a tope de aleaciones de aluminio es deficiente. Si los parámetros del proceso no se seleccionan adecuadamente, es propensa a inclusiones de óxido, porosidad y otros defectos, lo que provoca una reducción significativa de la resistencia y plasticidad de la unión. Durante la soldadura flash, deben adoptarse velocidades de flasheo y forja muy altas, un gran volumen de forja y modos de forja forzada. El factor de potencia requerido también debe ser mucho más elevado que el del acero.
4. Flash Soldadura del cobre y sus aleaciones:
El cobre conduce el calor mejor que el aluminio y tiene un punto de fusión más alto, por lo que es más difícil de soldar que el aluminio. Durante la soldadura flash de cobre puro, es difícil formar una capa de metal líquido en la cara final, mantener un proceso de flasheo estable y lograr un buen rango de temperatura plástica. Por lo tanto, durante la soldadura se requiere una velocidad de destello final, una velocidad de forja y una presión de forja muy elevadas.
Las aleaciones de cobre (como el latón o el bronce) son más fáciles de soldar que el cobre puro. Durante la soldadura de latónLa evaporación del zinc reduce el rendimiento de la unión. Para disminuir la evaporación de zinc, se debe adoptar una velocidad de destello final, una velocidad de forja y una presión de forja muy altas.
Los parámetros de proceso para la soldadura flash de aluminio, cobre y sus aleaciones pueden consultarse en la tabla siguiente:
Condiciones de soldeo para la soldadura flash de metales no ferrosos y sus aleaciones.
Parámetros del proceso | Material Dimensiones (mm) | |||||||||||||||
Cobre | Latón (H62) | Latón (H59) | El espesor de la banda de latón (QSn6,5-1,5). | Varilla de aluminio, diámetro | Aleación de aluminio | |||||||||||
LD5 | LF6 | |||||||||||||||
Material de varilla con un diámetro de 10 | material tubular de 9,5 por 1,5 | material en hojas de 44,5 por 10. | Diámetro de la varilla | Chapa metálica Espesor | Espesor de chapa | |||||||||||
6.5 | 10 | 6.5 | 10 | 1-4 | 4-8 | 20 | 25 | 30 | 38 | 4 | 6 | 4-7 | ||||
Tensión en vacío (V) | 6.1 | 5.0 | 10.0 | 2.17 | 4.41 | 2.4 | 7.5 | – | – | – | – | – | – | – | – | – |
Corriente máxima (KA) | 33 | 20 | 60 | 12.5 | 24.3 | 13.5 | 41 | – | – | 58 | 63 | 6 | 6 | 6 | 6 | 6 |
Longitud extendida (mm) | 20 | 20 | – | 15 | 22 | 18 | 25 | 25 | 40 | 38 | 43 | 50 | 50 | 50 | 50 | 50 |
Cantidad de destello (mm) | 12 | – | – | 6 | 8 | 7 | 10 | 15 | 25 | 17 | 20 | 22 | 22 | 22 | 22 | 22 |
Duración del destello (s) | 1.5 | – | – | 2.5 | 3.5 | 2.0 | 2.2 | 3 | 10 | 1.7 | 1.9 | 2.8 | 2.8 | 2.8 | 2.8 | 2.8 |
Velocidad media del flash (mm/s) | 8.0 | – | – | 2.4 | 2.3 | 3.5 | 4.5 | 5 | 2.5 | 11.3 | 10.5 | 7.9 | 7.9 | 7.9 | 7.9 | 7.9 |
Velocidad máxima del flash (mm/s) | – | – | – | – | – | – | – | 12 | 6 | – | – | – | – | – | – | – |
Remanente de forja (mm) | 8 | – | – | 9 | 13 | 10 | 12 | – | – | 13 | 13 | 14 | 14 | 14 | 14 | 14 |
Velocidad de forja (mm/s) | 200 | – | – | 200-300 | 200-300 | 200-300 | 200-300 | 125 | 125 | 150 | 150 | 150 | 150 | 150 | 150 | 150 |
Presión de forja (Mpa) | 380 | 290 | 224 | – | 230 | – | 250 | – | 60-150 | 64 | 170 | 190 | 190 | 190 | 190 | 190 |
Cantidad de forja actual (mm) | 6 | – | – | – | – | – | – | – | – | 6.0 | 6.0 | 7.0 | 7.0 | 7.0 | 7.0 | 7.0 |
Factor de potencia (KVA/mm2) | 2.6 | 2.66 | 1.35 | 0.9 | 1.35 | 0.95 | 2.7 | 0.5 | 0.25 | – | – | – | – | – | – | – |
Las juntas de transición soldadas por chispa de aluminio y cobre se utilizan ampliamente en la industria del motor. Debido a la gran diferencia en sus puntos de fusión, ya que el aluminio se funde 4-5 veces más rápido que el cobre, es necesario aumentar en consecuencia la longitud de protrusión del aluminio. Los parámetros de proceso para la soldadura flash de aluminio y cobre pueden consultarse en la siguiente tabla.
Cuando se sueldan aluminio y cobre, se forma un compuesto intermetálico, CuAl2aumentando la fragilidad de la junta. Por lo tanto, es esencial expulsar la mayor cantidad de CuAl2 como sea posible de la interfaz durante la forja.
Condiciones de soldadura por chispa de cobre y aluminio:
Sección de soldadura(mm2) | ||||
Diámetro de la varilla | Material de la banda | |||
20 | 25 | 40*50 | 50*10 | |
Corriente máxima (KA) | 63 | 63 | 58 | 63 |
Longitud extendida (mm) para cobre y aluminio | 334 | 438 | 330 | 436 |
Residuo de quemado (mm) | 17 | 20 | 18 | 20 |
Tiempo de destello (s) | 1.511.3 | 1.910.5 | 1.611.3 | 1.910.5 |
Velocidad media del flash (mm/s) | 13 | 13 | 6 | 8 |
Tolerancia de forja (mm) | 100-120 | 100-120 | 100-120 | 100-120 |
Velocidad de forja (mm/s) | 190 | 270 | 225 | 268 |
5. Flash Soldadura del titanio y sus aleaciones
El principal problema de la soldadura flash del titanio y sus aleaciones es que el temple y la absorción de gases (como el hidrógeno, el oxígeno y el helio) reducen la plasticidad de la unión. La tendencia de las aleaciones de titanio al temple está relacionada con los elementos de aleación añadidos. Si se añaden elementos β-estabilizadores, la tendencia al temple aumenta, y la plasticidad se reducirá aún más.
Se pueden conseguir uniones satisfactorias utilizando la soldadura por destello continuo con destello intenso y sin gas protector. Cuando se utiliza la soldadura por chispa con precalentamiento y velocidades de chispa y forja más bajas, la soldadura debe realizarse en una atmósfera protectora de Ar o He. La temperatura de precalentamiento es de 1000-1200 grados, los parámetros del proceso son básicamente los mismos que cuando se suelda acero, excepto que la tolerancia de destello se incrementa ligeramente. En este momento, se pueden obtener uniones con mayor plasticidad.
Los materiales de alambre con un diámetro de d≤5mm suelen utilizar la soldadura por resistencia, y sus parámetros de proceso se pueden consultar en la siguiente tabla:
Material del alambre Condiciones de soldadura por resistencia:
Tipo de metal | Diámetro (mm) | Longitud de la protuberancia (mm) | Corriente de soldadura (A) | Tiempo de soldadura (s) | Presión de arranque (N) |
Acero al carbono | 0.8 | 3 | 300 | 0.3 | 20 |
Acero al carbono | 2.0 | 6 | 750 | 1.0 | 80 |
Acero al carbono | 3.0 | 6 | 1200 | 1.3 | 140 |
Cobre | 2.0 | 7 | 1500 | 0.2 | 100 |
Aluminio | 2.0 | 5 | 900 | 0.3 | 50 |
Aleación de níquel-cromo | 1.85 | 6 | 400 | 0.7 | 80 |
Nota: La tolerancia de forja es igual al diámetro del alambre, y la tolerancia de forja actual es igual a 0,2-0,3 veces el diámetro.
Los alambres de diámetro muy pequeño, los alambres de distintos materiales y los alambres con piezas estampadas (como las tapas de las resistencias y los diodos) pueden soldarse mediante soldadura capacitiva de almacenamiento de energía.
La característica de este tipo de soldadura es que las condiciones de soldadura son muy rígidas y el rango de calentamiento es extremadamente estrecho, lo que reduce en gran medida el impacto de las propiedades termofísicas del metal soldado en la formación de la unión.
El más utilizado en el sector de la construcción, soldadura de armaduras suele utilizar la soldadura por resistencia para diámetros d10mm; y la soldadura por destello precalentado para d>30mm. Cuando se utiliza una máquina de soldadura manual, debido a la baja potencia de la máquina de soldadura (normalmente no superior a 50KVA), la soldadura por destello precalentado se utiliza generalmente cuando d=15-20mm.
En la soldadura con varilla pueden utilizarse electrodos de pinza semicirculares o en forma de V, estos últimos para diversos diámetros, por lo que su aplicación está muy extendida. Las varillas tienen una sección transversal sólida y una gran rigidez, lo que permite longitudes de saliente más largas. Los parámetros de proceso de la soldadura por resistencia de varillas de acero con bajo contenido en carbono y de la soldadura flash pueden consultarse en las tablas siguientes:
Condiciones de soldadura por resistencia de varillas de acero con bajo contenido en carbono:
Sección transversal (mm)2) | Longitud del saliente (mm)2) | Cantidad de contracción de soldadura (mm) | Densidad de corriente (A/mm2) | Tiempo de soldadura (s) | Presión de soldadura (MPa) | |
Encendido | Sin energía | |||||
25 50 100 250 | 6+6 8+8 10+10 12+12 | 0.5 0.5 0.5 10 | 0.9 0.9 1.0 1.8 | 200 160 140 90 | 0.6 0.8 1.0 1.5 | 10-20 |
1) Aumentar en 20-30% al soldar acero templado.
2) Para el acero templado, aumentar en 100%.
El momento y el flujo de la soldadura flash para varillas de acero con bajo contenido en carbono.
Diámetro de soldadura (mm) | Precalentamiento de la soldadura Flash Butt | Precalentamiento de la soldadura Flash Butt | |||||||
Medida de reserva (mm) | Tiempo (s) | Medida de reserva (mm) | Tiempo (s) | ||||||
Caudal total | Precalentamiento e intermitencia | Forja molesta | Precalentamiento | Flash y forja | Caudal total | Flash | Forja molesta | ||
5 | – | – | – | – | – | 6 | 4.5 | 4.5 | 2 |
10 | – | – | – | – | – | 8 | 6 | 6 | 3 |
15 | 9 | 6.5 | 2.5 | 3 | 4 | 13 | 10.5 | 10.5 | 6 |
20 | 11 | 7.5 | 3.5 | 5 | 6 | 17 | 14 | 14 | 10 |
30 | 16 | 12 | 4 | 8 | 7 | 25 | 21.5 | 21.5 | 20 |
40 | 20 | 14.5 | 5.5 | 20 | 8 | 40 | 35.5 | 35.5 | 40 |
50 | 22 | 15.5 | 6.5 | 30 | 10 | – | – | – | – |
70 | 26 | 19 | 7 | 70 | 15 | – | – | – | – |
90 | 32 | 24 | 8 | 120 | 20 | – | – | – | – |
La soldadura de tuberías se utiliza ampliamente en la fabricación de calderas, ingeniería de tuberías y fabricación de equipos petrolíferos. Dependiendo de la sección transversal y el material del tubo, se selecciona la soldadura flash continua o precalentada. El electrodo de pinza puede ser semicircular o en V.
En general, cuando la relación entre el diámetro del tubo y el grosor de la pared es superior a 10, puede elegirse una forma semicircular para evitar que el tubo se aplaste. Cuando la relación es inferior a 10, puede elegirse una forma en V.
Para evitar que el tubo resbale en el electrodo de sujeción, éste debe tener una longitud de trabajo adecuada. Cuando el diámetro del tubo es de 20-50mm, la longitud de la pieza de trabajo es de 2-2,5 veces el diámetro del tubo; cuando el diámetro del tubo es de 200-300mm, es de 1-1,5 veces. Los parámetros del proceso para la soldadura flash continua de tuberías de acero de bajo carbono y aleación de acero se pueden consultar en la siguiente tabla:
Condiciones de soldadura de flash continuo para tubos de acero 20#, 12Cr1MoV y 12Cr18Ni12Ti:
Tipo de acero | Tamaño (mm) | Tensión secundaria en vacío (V) | Longitud de extensión 2L (mm) | Desplazamiento del flash (mm) | Velocidad media del flash (mm/s) | Holgura de forja (mm) | Cantidad de forja actual (mm) |
20 | 25×3 32×3 32×4 32×5 60×3 | 6.5-7.0 | 60-70 | 11-12 11-12 15 15 15 | 1.37-1.5 1.22-1.33 1.25 1.0 1.15-1.0 | 3.5 2.5-4.0 4.5-5.0 5.0-5.5 4.0-4.5 | 3.0 3.0 3.5 4.0 3.0 |
12Cr1MoV | 324 | 6-6.5 | 60-70 | 17 | 1.0 | 5.0 | 4.0 |
12Cr18Ni12Ti | 324 | 6.5-7.0 | 60-70 | 15 | 1.0 | 5.0 | 4.0 |
Los tubos de acero de gran diámetro y paredes gruesas suelen soldarse mediante un proceso de precalentamiento, con los parámetros técnicos que se indican en la tabla siguiente:
Las condiciones de soldadura para la soldadura flash de tubos de acero de bajo carbono de gran sección transversal después del precalentamiento.
Sección transversal del tubo (mm2) | Tensión secundaria en vacío (v) | Longitud extendida 2L (mm) | Tiempo de precalentamiento (segundos) | Tolerancia al destello (mm) | Velocidad media del flash (mm/s) | Desplazamiento permitido (mm) | Cantidad de sobrecarga eléctrica (mm) | |
Tiempo total | Duración del pulso | |||||||
4000 | 6.5 | 240 | 60 | 5.0 | 15 | 1.8 | 9 | 6 |
10000 | 7.4 | 340 | 240 | 5.5 | 20 | 1.2 | 12 | 8 |
16000 | 8.5 | 380 | 420 | 6.0 | 22 | 0.8 | 14 | 10 |
20000 | 9.3 | 420 | 540 | 6.0 | 23 | 0.6 | 15 | 12 |
32000 | 10.4 | 440 | 720 | 8.0 | 26 | 0.5 | 16 | 12 |
La soldadura a tope de chapas finas se utiliza mucho en las líneas de producción continua para laminar chapas de acero en la industria metalúrgica. La anchura de las chapas oscila entre 300 y más de 1.500 mm, y el grosor oscila entre menos de 1 mm y varios milímetros. Los materiales incluyen acero al carbono, acero aleado y metales no ferrosos y sus aleaciones, etc.
Tras la soldadura a tope de chapas, la unión sufrirá un laminado y producirá una gran deformación plástica, por lo que no sólo debe tener cierta resistencia, sino también una elevada plasticidad. Para chapas de acero con un grosor inferior a 5 mm, la soldadura a tope por destello continuo se utiliza generalmente con un electrodo plano conductor en un lado. Cuando la chapa es gruesa, se utiliza la soldadura a tope por destello precalentado con conducción por ambos lados para garantizar un calentamiento uniforme a lo largo de toda la cara del extremo.
Al soldar chapas finas, la relación entre la longitud y la anchura de la sección transversal es grande, el área está dispersa, la unión se enfría rápidamente y la autoprotección durante el proceso de parpadeo es débil.
Al mismo tiempo, el puente líquido es pequeño, y la capa de metal líquido en la cara del extremo es delgada, lo que es propenso a la oxidación y solidificación.
Por lo tanto, es necesario aumentar la velocidad de destello y forja. Después de soldar, las rebabas deben eliminarse mientras la unión está todavía caliente utilizando un dispositivo de corte de rebabas. Los parámetros del proceso para la soldadura flash de chapas de acero de bajo contenido en carbono y de acero inoxidable pueden consultarse en las dos tablas siguientes:
Flash y retención de forja de chapa de acero de bajo carbono:
Espesor (mm) | Anchura (mm) | Subsidio(mm) | ||||
Caudal total | Flash Remainder | Indemnización por forja | ||||
Caudal total | Con potencia | Sin energía | ||||
2 | 100 | 9.5 | 7 | 2 | 1 | 1 |
400 | 11.05 | 9 | 2.5 | 1.5 | 1 | |
1200 | 15 | 11 | 4 | 2 | 2 | |
2000 | 17.5 | 15 | 4.5 | 2 | 2.5 | |
3 | 100 | 12 | 9 | 3 | 2 | 1 |
400 | 15 | 11 | 4 | 2.5 | 2 | |
1200 | 16 | 13 | 5 | 2 | 3 | |
2000 | 20 | 14 | 6 | 3 | 3 | |
4-5 | 100 | 14 | 10 | 4 | 2 | 2 |
400 | 17 | 12 | 5 | 2 | 2 | |
1200 | 20 | 14 | 6 | 3 | 3 | |
2000 | 21 | 15 | 6 | 3 | 3 |
Caudal para flash soldadura de acero inoxidable platos.
Espesor (mm) | Distancia de sujeción final (mm) | Tolerancia al destello (mm) | Desplazamiento permitido (mm) | Longitud total de la protuberancia (mm) |
1.0 | 3 | 5.5 | 1.5 | 10 |
1.5 | 5 | 8 | 2 | 15 |
2 | 6 | 10.5 | 2.5 | 19 |
2.5 | 7 | 13 | 3.0 | 23 |
3 | 9.5 | 15 | 3.5 | 27 |
4 | 11 | 15 | 4 | 30 |
5 | 15 | 18 | 5 | 38 |
6 | 16 | 18 | 6 | 40 |
10 | 18 | 20 | 7 | 55 |
– | – | – | – | – |
Cuando se sueldan piezas anulares (como llantas de rueda, anillos de cadena, anillos de rodamiento, bordes de montaje de motores a reacción, etc.), además de tener en cuenta las reglas generales de la soldadura a tope, también deben tenerse en cuenta los efectos de la derivación y el springback de deformación de las piezas anulares. Debido a la existencia de derivaciones, es necesario aumentar la potencia requerida en 15-50%. La derivación aumenta con la disminución del diámetro de la pieza anular, el aumento de la sección transversal y la disminución de la resistividad del material.
En la soldadura a tope de piezas anulares, la selección de la presión de forja debe tener en cuenta el impacto del rebote de la deformación. Sin embargo, dado que la derivación tiene un efecto de calentamiento en el rebote del anillo, el aumento de la presión de forja no es grande.
Las llantas de acero de bicicletas y motocicletas, así como las llantas de los automóviles, se sueldan a tope por chisporroteo continuo. El extremo delantero del electrodo de pinza debe coincidir con la sección transversal de la pieza. Durante el forjado, para evitar que la fuerza de rebote afecte a la calidad de la unión o incluso la abra, es necesario prolongar el tiempo de forjado sin corriente.
Las cadenas de anclaje, las cadenas de transmisión y otros anillos de cadena se fabrican principalmente con acero de bajo contenido en carbono y acero de baja aleación. Cuando el diámetro d 20mm, se puede utilizar la soldadura a tope por precalentamiento. El propósito del precalentamiento es asegurar un calentamiento uniforme en la interfaz y producir fácilmente una cierta deformación plástica durante el forjado.
Los parámetros del proceso de soldadura a tope de anillos de cadena pueden consultarse en las dos tablas siguientes:
Condiciones de soldadura a tope por chispa para cadenas de anclaje:
Diámetro de la cadena de anclaje (mm) | Tensión secundaria (V) | Corriente primaria (A) | Número de interrupciones de precalentamiento | Tiempo de encendido de la soldadura (s) | Velocidad de desplazamiento (mm/s) | Velocidad de intermitencia (mm/s) | 留量(mm) | ||||||
Flash | Cortocircuito | Liquidación natural | Velocidad constante | Aceleración | Con componente eléctrico | Sin componente eléctrico | Total | ||||||
28 | 9.27 | 420 | 550 | 2-4 | 19±1 | 45-50 | 0.9-1.1 | 1.5 | 4 | 2 | 1.0-1.5 | 1.5 | 10-11 |
31 | 10.3 | 450 | 580 | 3-5 | 22±1.5 | 45-50 | 0.9-1.1 | 2 | 4 | 2 | 1.0-1.5 | 1.5 | 10-11 |
34 | 10.3 | 460 | 620 | 3-5 | 24±2 | 45-50 | 0.8-1.0 | 2 | 4 | 2 | 1.5 | 1.5 | 11-12 |
37 | 8.85 | 480 | 680 | 4-6 | 28±2 | 30 | 0.8-1.0 | 2.5 | 5 | 2 | 1.5 | 1.5-2 | 12-13 |
40 | 10.0 | 500 | 720 | 5-7 | 30±2 | 30 | 0.7-0.9 | 2 | 5 | 2 | 1.5-2 | 2 | 12-13 |
Condiciones de soldadura para el soldeo por resistencia de anillos de cadena de pequeño diámetro.
Diámetro (mm) | Potencia nominal de la máquina de soldar (KVA) | Tensión secundaria (V) | Tiempo de soldadura (segundos) | Número de eslabones de cadena soldados por minuto. | |
Encendido | Apagado | ||||
19.8 | 250 | 4.4-4.55 | 4.5 | 1.0 | 6.4 |
16.7 | 250 | 3.4-3.55 | 5.0 | 1.0 | 6.4 |
15.0 | 175 | 3.8-4.0 | 3.0 | 1.0 | 6.6 |
13.5 | 175 | 3.8-4.0 | 2.5 | 1.0 | 8.8 |
12.0 | 175 | 2.8 | 1.5 | 0.8 | 8.6 |
La soldadura a tope de herramientas es actualmente uno de los métodos de fabricación utilizados en la industria de fabricación de herramientas para fabricar piezas brutas, y consiste principalmente en la soldadura a tope de acero rápido (W8Cr4V, W-9Cr4V2) y acero al carbono medio. La soldadura a tope de herramientas tiene las siguientes características:
1) El acero de alta velocidad y el acero de carbono medio presentan diferencias significativas en cuanto a conductividad térmica y resistividad. A temperatura ambiente, para el acero de carbono medio, λ=0,42W/(cm℃), ρ0=18-22μΩcm; para el acero de alta velocidad, λ=0,23W/(cm℃), ρ0=48Ωcm. Para que la distribución de la temperatura a ambos lados de la junta sea básicamente la misma, la longitud de protrusión del acero de alta velocidad debe ser 30-50% menor que la del acero de carbono medio. Por lo general, la longitud de protrusión del acero rápido es de (0,5-1,0)d. Para evitar que el calor se disipe demasiado rápido, la longitud de protrusión no es inferior a 10 mm.
2) El acero rápido tiene una gran tendencia a enfriarse, y la dureza aumentará mucho después de la soldadura, y pueden producirse grietas de enfriamiento. Para evitar la aparición de grietas, se puede utilizar la soldadura a tope con precalentamiento. Durante el precalentamiento, el metal dentro de un rango de 5-10mm cerca de la interfaz se calienta a 1100-1200℃. Después de la soldadura, recocido se realiza manteniendo a 600-700℃ en un horno eléctrico durante 30 minutos.
3) Cuando el acero rápido se calienta a altas temperaturas, puede producirse un agrandamiento del grano o formarse eutéctica de ledeburita en los límites del grano semifundido, lo que hace que la unión sea frágil. El eutéctico de ledeburita no puede eliminarse mediante tratamiento térmico. Por lo tanto, es necesario un forjado suficiente para eliminar esta estructura. Los parámetros del proceso para la soldadura a tope con herramienta pueden consultarse en la tabla siguiente:
Condiciones de soldadura a tope:
Diámetro (mm) | Superficie (mm2) | Tensión secundaria (V) | Longitud extendida (mm) | Margen (mm) | |||||||
Precalentamiento | Flash | Forja molesta | Caudal total | Reserva de acero para herramientas | Reserva de acero al carbono | ||||||
Acero para herramientas | Acero al carbono | Powered | Sin alimentación | ||||||||
8-10 | 50-80 | 3.8-4 | 10 | 15 | 1 | 2 | 0.5 | 1.5 | 5 | 3 | 2 |
11-15 | 80-180 | 3.8-4 | 12 | 20 | 1.5 | 2.5 | 0.5 | 1.5 | 6 | 3.5 | 2.5 |
16-20 | 200-315 | 4-4.3 | 15 | 20 | 1.5 | 2.5 | 0.5 | 1.5 | 6 | 3.5 | 2.5 |
21-22 | 250-380 | 4-4.3 | 15 | 20 | 1.5 | 2.5 | 0.5 | 1.5 | 6 | 3.5 | 2.5 |
23-24 | 415-450 | 4-4.3 | 18 | 27 | 2 | 2.5 | 0.5 | 2 | 7 | 4 | 3 |
25-30 | 490-700 | 4.3-4.5 | 18 | 27 | 2 | 2.5 | 0.5 | 2 | 7 | 4 | 3 |
31-32 | 750-805 | 4.5-4.8 | 20 | 30 | 2 | 2.5 | 0.5 | 2 | 7 | 4 | 3 |
33-35 | 855-960 | 4.8-5.1 | 20 | 30 | 2 | 2.5 | 0.5 | 2 | 7 | 4 | 3 |
36-40 | 1000-1260 | 5.1-5.5 | 20 | 30 | 2.5 | 3 | 0.5 | 2 | 8 | 5 | 3 |
41-46 | 1320-1660 | 5.5-6.0 | 20 | 30 | 2.5 | 3 | 1.0 | 2.5 | 9 | 5.5 | 3.5 |
47-50 | 1730-1965 | 6.0-6.5 | 22 | 33 | 2.5 | 3 | 1.0 | 2.5 | 9 | 5.5 | 3.5 |
51-55 | 2000-2375 | 6.5-6.8 | 25 | 40 | 2.5 | 3 | 1.0 | 3.5 | 10 | 6 | 3.5 |
55-30 | – | 7.0-8.0 | 25 | 40 | 2.5 | 4 | 1.5 | 4 | 12 | 7 | 5 |
1) Soldadura a tope por destello de tensión reducida controlada por programa:
Este método se caracteriza por utilizar una tensión de circuito abierto secundaria más alta al principio de la etapa de destello para facilitar la iniciación del destello. Una vez que aumenta la temperatura de la superficie final, se utiliza un destello de menor tensión manteniendo constante la velocidad de destello para mejorar la eficiencia térmica.
Al acercarse a la fase de forja, la tensión secundaria vuelve a aumentar para intensificar el destello y potenciar el efecto de autoprotección. En comparación con la soldadura a tope por destello de precalentamiento, la soldadura a tope por destello de tensión reducida controlada por programa presenta ventajas como un tiempo de soldadura más corto, una menor necesidad de potencia y un calentamiento más uniforme.
2) Soldadura a tope por impulsos:
La característica de este método es que, durante el movimiento de avance de la pinza dinámica, se superpone un recorrido de vibración alternativo a través de un dispositivo de vibración hidráulico. La amplitud es de 0,25-1,2 mm, y la frecuencia se puede ajustar uniformemente entre 3-35 Hz. La vibración hace que las superficies de los extremos de la pieza entren en cortocircuito y se separen alternativamente, generando así destellos pulsantes.
En comparación con la soldadura a tope por chisporroteo ordinaria, la soldadura a tope por chisporroteo pulsante puede más que duplicar la eficiencia térmica debido a la ausencia de explosión espontánea sobre el haz. Las partículas de salpicadura son más pequeñas y la boca de fuego es poco profunda, lo que permite reducir la tolerancia de forja a 2/3-1/2.
Los dos métodos anteriores están diseñados principalmente para satisfacer las necesidades de la soldadura a tope por chisporroteo de piezas de gran sección.
3) Soldadura a tope por destello de onda rectangular:
En comparación con la soldadura a tope por destello de onda sinusoidal de CA de frecuencia industrial, este método puede mejorar significativamente la estabilidad del destello. Porque cuando la tensión de la fuente de alimentación de onda sinusoidal es cercana a cero, hará que el destello se interrumpa instantáneamente, mientras que la onda rectangular puede generar destellos uniformemente a lo largo de todo el ciclo, independientemente de la fase de tensión.
El número de destellos por unidad de tiempo de una fuente de energía de onda rectangular es 30% mayor que el de la corriente alterna de frecuencia industrial, y las partículas metálicas salpicadas son finas, con una boca de fuego poco profunda y un alto rendimiento térmico. La frecuencia de onda rectangular puede ajustarse dentro de un rango de 30-180Hz. Este método se utiliza a menudo para la soldadura flash continua a tope de chapas finas y llantas de aleación de aluminio.
Los cordones de soldadura a tope incluyen las soldaduras a tope penetradas y las juntas en forma de T combinadas con juntas angulares (en lo sucesivo, soldaduras a tope), así como las soldaduras a tope parcialmente penetradas y las juntas en forma de T combinadas con juntas angulares.
Dado que la fuerza experimentada por las soldaduras a tope parcialmente penetradas es similar a la de las soldaduras de esquina, este aspecto se tratará en el siguiente apartado.
Las soldaduras a tope suelen requerir que las piezas se hagan en una ranura, de ahí que también se denominen soldaduras de ranura. La forma de la ranura está relacionada con el grosor de la pieza. Cuando el espesor de la pieza es muy pequeño (soldadura manual 6 mm, sumergida soldadura por arco 10 mm), se puede utilizar una costura de borde recto.
Para piezas de grosor general, puede adoptarse una soldadura en V por un solo lado o en V con una ranura inclinada.
La ranura inclinada y la ranura de raíz c forman conjuntamente un espacio de soldadura donde la varilla de soldadura puede girar, haciendo que la costura de soldadura fácil de penetrar; el borde romo p desempeña la función de sostener el metal fundido.
Para piezas más gruesas (t>20 mm), se utilizan las ranuras en forma de U, K y X (figura 3.2.1). Para los cordones en forma de V y de U, es necesario rellenar la raíz del cordón de soldadura.
(a) Ranura de borde recto
(b) Una cara Ranura en V
(c) Ranura en V
(d) Ranura en U
(e) Ranura K
(f) Ranura X
En la unión de soldaduras a tope, cuando la anchura de la pieza varía o la diferencia de espesor supera los 4 mm, debe formarse un ángulo de bisel no superior a 1:2,5 en uno o ambos lados en la dirección de la anchura o del espesor (3.2.2). Esto facilita una transición transversal más suave y reduce la concentración de tensiones.
Defectos como las picaduras de arco suelen producirse al principio y al final del cordón de soldadura, lo que afecta significativamente a la capacidad de carga.
Por lo tanto, es práctica común establecer un golpe de arco Durante la soldadura, se instalan una placa de protección y una placa de evacuación del arco (figura 3.2.3), que se retiran posteriormente. Cuando sea difícil instalar una placa de desprendimiento del arco para estructuras bajo cargas estáticases permisible no organizarlos.
En este caso, la longitud calculada del cordón de soldadura puede ser igual a la longitud real menos 2t (donde t es el espesor de la pieza más fina).
(a) Modificar la anchura.
(b) Cambia el grosor.
La resistencia de una unión soldada a tope está relacionada con varios factores, como el grado de acero utilizado, la tipo de varilla de soldaduray las normas de inspección de la calidad del cordón de soldadura.
Si no hay defectos en la soldadura, la resistencia del metal soldado supera la del metal base. Sin embargo, debido a tecnología de soldadura problemas, pueden aparecer en la soldadura defectos como porosidad, inclusión de escoria, socavaduras y penetración incompleta.
Los experimentos han demostrado que defectos de soldadura tienen poco impacto en la resistencia a la compresión y al cizallamiento de las uniones soldadas a tope. Por lo tanto, se supone que la resistencia a la compresión y al cizallamiento de las uniones soldadas a tope es igual a la resistencia del material base.
Sin embargo, las uniones soldadas a tope a tracción son muy sensibles a los defectos. Cuando la relación entre el área del defecto y el área de la sección transversal de la soldadura supera los 5%, la resistencia a la tracción de la unión soldada a tope disminuirá notablemente. Dado que a las soldaduras que se someten a una inspección de tercer nivel se les permiten más defectos, su resistencia a la tracción es 85% de la soldadura principal. resistencia del metal.
Por otra parte, la resistencia a la tracción de las soldaduras sometidas a inspecciones de primer o segundo nivel puede considerarse igual a la resistencia del material base.
Como la unión soldada a tope forma parte de la sección transversal de la soldadura, la distribución de tensiones en la soldadura es casi idéntica a la de la soldadura original. Por lo tanto, el método de cálculo es el mismo que el utilizado para el cálculo de la resistencia de los componentes estructurales.
(1) Soldaduras a tope de carga axial
En las uniones a tope y en T, la resistencia de las soldaduras a tope perpendiculares a las fuerzas axiales de tracción o compresión (N) (figura 3.2.4) debe calcularse mediante la siguiente fórmula:
En la ecuación:
En cumplimiento de las normas de construcción y aceptación, deben aplicarse placas de cebado de arco en todas las soldaduras a tope para evitar defectos de iniciación y terminación del arco en ambos extremos del cordón de soldadura.
Por lo tanto, la longitud calculada del cordón de soldadura debe ser equivalente a la longitud real. Sin embargo, en algunos casos especiales, como las uniones en T, si resulta difícil aplicar la chapa de desencofrado, la longitud calculada de cada cordón de soldadura debe reducirse en 2t.
Por lo tanto, bajo arco general llamativo soldadura de chapas todas las soldaduras a tope comprimidas y cortadas, así como las soldaduras de tracción de primer y segundo nivel, tienen la misma resistencia que el metal base y no requieren cálculo. Sólo es necesario calcular las soldaduras de tracción del tercer nivel.
Si las soldaduras directas no pueden cumplir los requisitos de resistencia, pueden utilizarse soldaduras oblicuas a tope. La soldadura oblicua de tensión axial que se muestra en la figura 3.2.5 puede calcularse mediante la siguiente fórmula:
En la fórmula, lw representa la longitud calculada del cordón de soldadura: cuando se añade la placa de arco, l = b/sinθ; sin la placa de arco, lw = b/sinθ - 2t.
Fvw - Valor de cálculo de la resistencia al cizallamiento de la costura de soldadura a tope.
Cuando el ángulo de inclinación θ de la costura de soldadura oblicua es menor o igual a 56,3°, o en otras palabras, cuando la tangente de θ es menor o igual a 1,5, puede considerarse tan resistente como el material base, y no es necesario realizar cálculos.
Las soldaduras a tope oblicuas se utilizaban mucho en la década de 1950. Sin embargo, debido al gran consumo de materiales y al incómodo proceso de construcción, fueron cayendo en desuso y se sustituyeron por soldaduras rectas a tope.
Las uniones rectas suelen soldarse con una placa de arco de plomo. Si la resistencia a la tracción no cumple los requisitos, se puede adoptar una norma de inspección secundaria o desplazar la posición de la unión a un lugar con menos fuerza interna.
[Ejemplo 3-1] Compruebe la resistencia del cordón de soldadura a tope de la chapa de acero mostrada en la figura 3.2.6. En la figura, a = 540mm, t = 22mm, y el valor de diseño de la fuerza axial es N = 2500kN. El acero es Q235-B, soldado manualmente, con varilla de soldadura tipo E43, norma de inspección de tercer nivel del cordón de soldadura, y se añade una placa de arco de plomo durante la soldadura.
[Solución] La longitud calculada de la unión recta es lw=54cm. La tensión normal del cordón de soldadura es:
Si no cumple los requisitos, utilice una soldadura diagonal a tope, con una pendiente de corte de 1,5:1, es decir, 8=56 °, y una longitud de soldadura de:
Por lo tanto, la tensión normal en este momento es:
El esfuerzo cortante es:
Esto indica que cuando tanθ ≤ 1,5, la resistencia de la soldadura puede garantizarse y no hay necesidad de verificación.
(2) Costuras de soldadura a tope sometidas al efecto combinado del momento de flexión y la fuerza cortante
La junta a tope representada en la figura 3.2.7(a) soporta la influencia combinada del momento flector y la fuerza cortante.
Dado que la sección transversal del cordón de soldadura es rectangular, los perfiles de tensiones normales y tensiones de cizalladura se manifiestan con formas triangulares y parabólicas, respectivamente. Sus valores máximos deben cumplir las siguientes condiciones de resistencia.
En la fórmula:
La figura 3.2.7(b) ilustra una unión de una viga de sección en I, en la que se emplea una soldadura a tope. Además de comprobar por separado la tensión máxima de tracción y la tensión máxima de cizalladura, en las zonas sometidas a tensiones de tracción y cizalladura importantes, como la unión del alma y el ala, también debe comprobarse la tensión equivalente mediante la siguiente ecuación:
En la fórmula, σ1 y τ1 representan la tensión normal y la tensión de cizalladura en el punto de verificación del cordón de soldadura, respectivamente.
1.1 - Teniendo en cuenta que la tensión máxima equivalente sólo aparece localmente, aumentamos adecuadamente el valor de cálculo de la resistencia.
(3) Costuras de soldadura a tope bajo la acción combinada de fuerza axial, momento de flexión y fuerza cortante.
Cuando la fuerza axial se combina con el momento flector y la fuerza cortante, la tensión normal causada por la fuerza axial y el momento flector en el cordón de soldadura debe superponerse. El esfuerzo cortante debe verificarse de acuerdo con el ensayo (3.2.5), y el esfuerzo equivalente debe verificarse de acuerdo con el ensayo (3.2.6).
Aparte de considerar si se reduce la longitud de la costura de soldadura o si es necesario descontar la resistencia de la costura de soldadura, el método de cálculo de la costura de soldadura a tope es completamente idéntico al cálculo de la resistencia del material base.