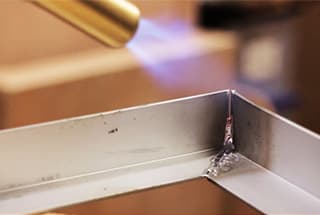
¿Te has preguntado alguna vez por qué el cobre y sus aleaciones son tan vitales en nuestra vida cotidiana? Este artículo explora las fascinantes propiedades del cobre, desde su increíble conductividad eléctrica hasta su impresionante resistencia a la corrosión. Al final, entenderá por qué el cobre sigue siendo una piedra angular de la ingeniería y la tecnología modernas.
El cobre y sus aleaciones se utilizan ampliamente en aplicaciones industriales debido a sus excepcionales propiedades, como una conductividad eléctrica y térmica superiores, una excelente resistencia a la corrosión y una gran conformabilidad. Estos materiales se clasifican en cuatro grupos principales: cobre puro (a menudo denominado cobre rojo), latón, bronce y cobre blanco (también conocido como alpaca).
1. Cobre puro: Caracterizado por su color rojizo anaranjado, el cobre puro (>99,3% Cu) ofrece la mayor conductividad eléctrica entre los metales comerciales, lo que lo hace indispensable en las industrias eléctrica y electrónica. También presenta una excelente conductividad térmica, resistencia a la corrosión y ductilidad.
2. Latón: Aleación compuesta principalmente de cobre y zinc, con un contenido de zinc que suele oscilar entre 5% y 45%. Los latones ofrecen un equilibrio entre resistencia, maquinabilidad y resistencia a la corrosión. Los tipos más comunes son:
3. Bronce: Tradicionalmente aleaciones de cobre y estaño, pero los bronces modernos pueden contener otros elementos como aluminio, silicio o berilio. Los bronces suelen ser más resistentes a la corrosión que los latones. Los tipos más destacados son:
4. Cobre blanco (alpaca): Aleación de cobre, níquel y zinc, que suele contener 10-20% de níquel. A pesar de su nombre, no contiene plata. El cobre blanco ofrece buena resistencia a la corrosión, solidez y un atractivo aspecto plateado, lo que lo hace adecuado para aplicaciones decorativas e instrumentos musicales.
El cobre rojo es una forma pura de cobre con un contenido de cobre de al menos 99,5%.
Según su contenido en oxígeno, puede dividirse en cobre puro y cobre libre de oxígeno.
Cu2O y óxidos de CuO pueden formarse en la superficie del cobre rojo.
A temperatura ambiente, la superficie de cobre se cubre con Cu2O.
A altas temperaturas, la cascarilla de óxido se compone de dos capas: la capa exterior es CuO y la capa interior es Cu2O.
Es importante señalar que el cobre puro no puede soldarse en una atmósfera reductora que contenga hidrógeno.
El latón se refiere a una aleación de cobre y zinc que tiene mayor fuerza, dureza y resistencia a la corrosión en comparación con el cobre rojo, al tiempo que conserva la tenacidad y una alta resistencia a la corrosión.
Diagrama metalográfico del latón
(1) Latón estañado:
El latón estañado contiene aproximadamente 1% de estaño (Sn) y la presencia de estaño no altera la composición de los óxidos superficiales.
La soldabilidad del latón estañado es comparable a la del latón, por lo que resulta fácil de soldar.
(2) Latón de plomo:
El latón al plomo contiene plomo, que al calentarse forma una escoria pegajosa que perjudica el efecto humectante y la fluidez de la soldadura.
Es importante seleccionar el fundente adecuado para garantizar una fluidez correcta.
(3) Latón manganeso:
La superficie del latón al manganeso está compuesta por óxido de zinc y óxido de manganeso.
El óxido de manganeso es relativamente estable y difícil de eliminar, por lo que es necesario utilizar un activo soldadura fundente para garantizar la humectabilidad del metal de aportación de soldadura fuerte.
Existen varios tipos de broncecada uno con diferentes elementos de aleación, lo que afecta a su soldabilidad.
Cuando el elemento de aleación añadido es estaño, o una pequeña cantidad de cromo o cadmio, tiene un impacto mínimo en la soldabilidad y, en general, es más fácil de soldar.
Sin embargo, si el elemento añadido es aluminio, especialmente cuando el contenido de aluminio es elevado (hasta 10%), el óxido de aluminio de la superficie es difícil de eliminar, lo que provoca un deterioro de la soldabilidad.
En tales casos, es necesario utilizar un fundente especial para soldadura fuerte.
Por ejemplo, cuando se añade silicio para formar bronce al silicio, éste se vuelve muy sensible a la fragilidad en caliente y al agrietamiento por tensión cuando se expone a la soldadura fundida.
Otro ejemplo es cuando el elemento de aleación añadido es el berilio.
Aunque se forma un óxido de BeO relativamente estable, el fundente de soldadura convencional es suficiente para eliminar la película de óxido.
Cobre blanco es una aleación de cobre y níquel que presenta excelentes propiedades mecánicas integrales.
Contiene níquel.
Al seleccionar el metal de aportación, es importante evitar los que contienen fósforo, como el metal de aportación de cobre-fósforo y el metal de aportación de cobre-fósforo-plata.
El cobre blanco es muy sensible al agrietamiento en caliente y al agrietamiento por tensión cuando se somete a soldadura fundida.
Nombre | Código | Composición química primaria (porcentaje en masa, %) | Temperatura de fusión/℃ | Tratamiento térmico | |||||||
ω(Cu) | ω(Zn) | ω(Sn) | ω(Pb) | ω(Mn) | ω(Al) | ω(Ni) | Otros | ||||
Cobre puro | T1 | ≤99.95 | - | - | - | - | - | - | 20.02 | 1083 | Recocido: 450~520℃ |
T2 | ≤99.90 | - | - | - | - | - | - | 20.06 | 1083 | Recocido: 500~630℃ | |
Cobre sin oxígeno | TU1 | ≤99.97 | - | - | - | - | - | - | 20.003 | 1083 | Recocido al vacío: 500℃ |
TU2 | ≤99.95 | - | - | - | - | - | - | 20.003 | 1083 | ||
TUMn | ≤99.60 | - | - | - | 0.1~0.3 | - | - | 20.003 | 1083 | ||
Latón | H96 | 95~97 | Rem. | - | - | - | - | - | - | 1056~1071 | Recocido: 600℃ |
H68 | 67~70 | Rem. | - | - | - | - | - | - | 910~939 | Recocido: 600℃ | |
H62 | 60.5~63.5 | Rem. | - | - | - | - | - | - | 899~906 | Recocido: 600℃ | |
Estaño Latón | HSn62-1 | 61~63 | Rem. | 0.7~1.1 | - | - | - | - | - | 886~907 | Recocido: 600℃ |
Latón al plomo | HPb59-1 | 57~60 | Rem. | - | 0.8~1.9 | - | - | - | - | 886~901 | Recocido: 600℃ |
Manganeso Latón | HMn58-2 | 57~60 | Rem. | - | - | 1~2 | - | - | - | 866~881 | Recocido: 600℃ |
Estaño Bronce | QSn6,5-0,1 | Rem. | - | 6~7 | - | - | - | - | P: 0.1~0.25 | ~996 | Recocido: 500~620℃ |
QSn4-3 | Rem. | 2.7~3.3 | 3.5~4.5 | - | - | - | - | - | ~1046 | ||
Aluminio Bronce | QAl9-2 | Rem. | - | - | - | 1.5~2.5 | 8~10 | - | - | ~1061 | Recocido: 700~750℃;Quenching880℃,Tempering400℃ |
QAl10-4-4 | Rem. | - | - | - | - | 9.5~11 | - | Fe: 3,5~4,5 | - | Recocido: 700~750℃;Quenching920℃,Tempering650℃ | |
Bronce berilio | QBe2 | Rem. | - | - | - | - | - | 0.2~0.5 | Be: 1,9~2,2 | 865~956 | Enfriamiento: 800℃,Envejecimiento:300℃ |
QBe1.7 | Rem. | - | - | - | - | - | 0.2~0.4 | Be: 1,6~1,8 | - | Enfriamiento: 800℃,Envejecimiento: 300℃ | |
Silicio Bronce | QSi3-1 | Rem. | - | - | - | 1~1.5 | - | - | Si: 2,75~3,5 | 971~1026 | Recocido: 600~680℃ |
Cromo Bronce | QCr0,5 | Rem. | - | - | - | - | - | - | Cr: 0.5~1.0 | 1073~1080 | Enfriamiento: 950~1000℃ |
Envejecimiento: 400~460℃ | |||||||||||
Bronce cadmio | QCd1 | Rem. | - | - | - | - | - | - | Cd: 0.9~1.2 | 1040~1076 | Recocido: 650℃ |
Zinc Níquel Plata | BZn15-20 | Rem. | 18~20 | - | - | - | - | 13.5~16.5 | - | ~1081 | Recocido: 700℃ |
Manganeso Níquel Plata | BMn40-1,5 | Rem. | - | - | - | 1~2 | - | 39~40 | - | 1261 | Recocido: 1050~1150℃ |
La soldadura fuerte del cobre y las aleaciones de cobre depende principalmente de los siguientes factores:
Las superficies de cobre puro pueden formar dos óxidos, Cu2O y CuO. A temperatura ambiente, una superficie de cobre está cubierta por Cu2O, mientras que a altas temperaturas, la película de óxido se divide en dos capas, con CuO en el exterior y Cu2O en el interior. Los óxidos de cobre son fáciles de eliminar, por lo que el cobre puro se suelda bien.
El cobre oxigenado es cobre refinado mediante pirometalurgia y cobre de brea electrolíticamente resistente. Contiene de 0,02% a 0,1% de oxígeno en masa, que existe como óxido de cobre, formando una organización eutéctica con el cobre. Esta organización eutéctica se distribuye en la matriz de cobre en forma globular.
Si el cobre oxigenado se suelda en una atmósfera reductora que contenga hidrógeno, éste se difunde rápidamente en el metal, reduciendo el óxido para producir vapor. Este vapor forma cavidades dentro de los cristales de cobre y se expande rápidamente, provocando fragilización por hidrógeno. En casos graves, el material de cobre puede fracturarse.
Si la atmósfera contiene monóxido de carbono y humedad, el monóxido de carbono puede reducir el vapor a hidrógeno, que se difunde en el metal, provocando la fragilización por hidrógeno. Por lo tanto, el cobre oxigenado no debe soldarse en atmósferas de amoníaco en descomposición, endotérmicas o exotérmicas reductoras.
El calentamiento prolongado del cobre oxigenado por encima de 920℃ provocará la acumulación de óxido de cobre en los límites de grano, reduciendo la resistencia y ductilidad del cobre. Por lo tanto, durante la soldadura fuerte, el material debe evitar la exposición prolongada a temperaturas superiores a 920℃.
El cobre no puede tratarse térmicamente para aumentar su resistencia, por lo que a menudo se utilizan métodos de trabajo en frío para incrementarla. El cobre endurecido en frío se ablanda cuando se calienta entre 230℃ y 815℃. El grado de reblandecimiento depende de la temperatura y de la duración a esta temperatura. Cuanto mayor sea la temperatura de calentamiento de la soldadura fuerte, más blando será el cobre endurecido en frío.
El cobre libre de oxígeno tiene un bajo contenido de oxígeno, y no hay constituyentes eutécticos de cobre y óxido de cobre en el cobre. Su conductividad eléctrica y su trabajabilidad en frío (como la embutición profunda y la hilatura) son mejores que las del cobre desoxidado.
El cobre sin oxígeno puede soldarse en una atmósfera protectora que contenga hidrógeno sin que se produzca fragilización por hidrógeno. El cobre libre de oxígeno endurecido en frío también se ablandará durante el calentamiento.
El latón común puede dividirse en tres categorías: latón bajo (fracción de masa de zinc inferior a 20%), latón alto (fracción de zinc superior a 20%) y latón aleado. Cuando la fracción másica de zinc en el latón es inferior a 15%, el óxido superficial consiste principalmente en Cu2O, que contiene pequeñas partículas de ZnO.
Cuando la fracción másica de zinc es superior a 20%, el óxido está formado principalmente por ZnO. El óxido de zinc también es fácil de eliminar, por lo que la soldadura fuerte del latón es muy buena. El latón no es adecuado para la soldadura fuerte en atmósfera protectora, especialmente en la soldadura fuerte al vacío. Esto se debe a que el zinc tiene una alta presión de vapor (que alcanza 105Pa a 907℃).
Durante la soldadura fuerte en atmósfera protectora, especialmente la soldadura fuerte en vacío, el zinc del latón se volatiliza, la superficie se enrojece y afecta tanto a sus propiedades de soldadura fuerte como a sus propiedades inherentes. Si la soldadura fuerte debe realizarse en una atmósfera protectora o en vacío, debe galvanizarse previamente una capa de cobre o níquel en la superficie de las piezas de latón para evitar la volatilización del zinc. Sin embargo, el chapado puede afectar a la resistencia de la unión soldada.
La soldadura fuerte del latón requiere el uso de un fundente.
El latón estañado tiene aproximadamente 1% de ω (Sn). La presencia de estaño no afecta a la composición del óxido superficial. La soldadura fuerte del latón estañado es comparable a la del latón y es fácil de soldar.
El latón de plomo forma un residuo pegajoso cuando se calienta, lo que altera la acción humectante y la fluidez del material de soldadura fuerte, por lo que debe elegirse un fundente adecuado para garantizar la acción humectante del material de soldadura fuerte. Cuando se calienta, el latón al plomo tiende a agrietarse por tensión. Su sensibilidad al agrietamiento en caliente es directamente proporcional al contenido de plomo.
Por lo tanto, el tensión interna de latón con plomo debe reducirse al mínimo durante la soldadura fuerte, por ejemplo, recociendo antes de soldar para eliminar la tensión causada por el procesamiento de los componentes. La temperatura de calentamiento debe ser lo más uniforme posible para reducir la tensión térmica. El efecto de la soldadura fuerte es deficiente cuando ω (Pb) > 3%. Para el latón con plomo con ω (Pb) > 5%, no se recomienda la soldadura fuerte.
La superficie del latón al manganeso está compuesta por óxido de zinc y óxido de manganeso. El óxido de manganeso es relativamente estable y difícil de eliminar, por lo que debe utilizarse un fundente muy activo para garantizar la humectabilidad del material de soldadura fuerte.
El estaño bronce QSn6.5-0.1 forma dos óxidos en su superficie: una capa interna de SnO2 y una capa externa de óxido de cobre. Estos óxidos son fáciles de eliminar y la aleación se suelda bien, por lo que es adecuada para diversos métodos de soldadura, como la soldadura con gas protector y la soldadura al vacío.
Para la soldadura fuerte en aire pueden utilizarse fundentes convencionales. Para evitar el agrietamiento, las piezas de bronce al estaño que contienen fósforo deben someterse a un alivio de tensión de aproximadamente 290-340℃ antes de la soldadura fuerte.
El bronce de aluminio contiene una cantidad significativa de aluminio (hasta 10% en masa), formando una capa de óxido compuesta principalmente de óxido de aluminio en la superficie, que es difícil de eliminar. Por lo tanto, soldadura de aluminio bronce es todo un reto. El óxido de aluminio no puede reducirse en una atmósfera protectora y no puede eliminarse mediante calentamiento al vacío, por lo que se requiere un fundente especializado.
Si las piezas de bronce de aluminio se sueldan en un templado y revenido la temperatura de soldadura fuerte no debe superar la temperatura de revenido. Por ejemplo, la temperatura de revenido de QAl9-2 es de 400℃.
Si la temperatura de soldadura supera los 400℃, el material base se ablandará. Si la soldadura fuerte se realiza a altas temperaturas, la temperatura de soldadura fuerte debe coincidir con la temperatura de temple (880℃), seguida del revenido, para lograr las propiedades mecánicas deseadas del material base. Esto debe tenerse en cuenta al seleccionar un material de soldadura fuerte.
Aunque se forma un óxido de BeO relativamente estable en la superficie del bronce al berilio, el fundente convencional sigue satisfaciendo el requisito de eliminación de la película de óxido. El bronce al berilio se utiliza a menudo en situaciones en las que las piezas requieren elasticidad.
Para evitar que disminuya esta propiedad, la temperatura de soldadura fuerte debe ser inferior a su temperatura de envejecimiento (300℃) o la temperatura de soldadura fuerte debe coincidir con la temperatura de temple, seguida de un tratamiento de envejecimiento después de la soldadura fuerte.
El bronce al silicio, principalmente aleación QSi3-1 con aproximadamente 3% ω (Si), forma en su superficie un óxido compuesto principalmente de dióxido de silicio. Para la soldadura fuerte del bronce al silicio debe utilizarse el mismo fundente que para la soldadura fuerte del bronce al aluminio. El bronce al silicio bajo tensión es extremadamente sensible al agrietamiento térmico y al agrietamiento por tensión bajo la acción del material de soldadura fuerte fundido.
Para evitar el agrietamiento, la aleación debe someterse a un alivio de tensiones a una temperatura de entre 300-350℃ antes de la soldadura fuerte. Se debe elegir un material de soldadura de punto de fusión más bajo y utilizar un método de soldadura que caliente uniformemente durante la soldadura fuerte.
El bronce al cromo y el bronce al cadmio tienen pequeñas cantidades de cromo o cadmio, que no afectan significativamente al proceso de soldadura fuerte. Cuando se suelda bronce al cromo, debe tenerse en cuenta el régimen de tratamiento térmico del material base.
La soldadura fuerte debe realizarse por debajo de la temperatura de envejecimiento (460℃) o la temperatura de soldadura fuerte debe coincidir con la temperatura de enfriamiento (950-1000℃).
Plata níquel y plata manganeso. La alpaca contiene níquel, y los materiales de soldadura fuerte que contienen fósforo, como el material de soldadura fuerte de cobre-fósforo y el material de soldadura fuerte de cobre-fósforo-plata, deben evitarse al elegir un material de soldadura fuerte porque los materiales de soldadura fuerte que contienen fósforo pueden formar fácilmente fosfuro de níquel quebradizo en la interfaz después de la soldadura fuerte, reduciendo la resistencia y la tenacidad de la unión.
La alpaca es extremadamente sensible tanto al agrietamiento en caliente como al agrietamiento por tensiones bajo la acción del material de soldadura fuerte fundido. Por lo tanto, antes de proceder a la soldadura fuerte deben eliminarse las tensiones internas de las piezas y debe elegirse un material de soldadura fuerte con un punto de fusión más bajo.
Las piezas deben calentarse uniformemente, y debe permitirse la libre expansión y contracción de las piezas durante el calentamiento y el enfriamiento para reducir la tensión térmica durante la soldadura fuerte.
Brazabilidad del cobre común y de las aleaciones de cobre
Aleación | Soldabilidad | |
Cobre T1 | Excelente | |
Cobre sin oxígeno TU1 | Excelente | |
Latón | H96 | Excelente |
H68 | Excelente | |
H62 | Excelente | |
Estaño-bronce | HSn62-1 | Excelente |
Latón manganeso | HMn58-2 | Bien |
Estaño-bronce | QSn58-2 | Excelente |
QSn4-3 | Excelente | |
Latón al plomo | HPb59-1 | Bien |
aluminio bronce | QAl9-2 | Mal |
QAl10-4-4 | Mal | |
bronce de berilio | QBe2 | Bien |
QBe1.7 | Bien | |
bronce al silicio | QSi3-1 | Bien |
bronce cromado | QCr0,5 | Bien |
bronce cadmio | QCd11 | Excelente |
Aleación de zinc-cobre-níquel | BZn15-20 | Bien |
Mn aleación de cobre níquel | BMn40-1,5 | Difícil |
La soldadura con base de plata se utiliza ampliamente debido a su punto de fusión moderado, buena procesabilidad, cualidades de resistencia y dureza, conductividad, conductividad térmica y resistencia a la corrosión.
El principal elementos de aleación de las soldaduras a base de plata son el cobre, el zinc, el cadmio y el estaño. El cobre es el elemento de aleación más importante, ya que reduce la temperatura de fusión de la plata sin formar una fase quebradiza.
La adición de zinc reduce aún más la temperatura de fusión.
Aunque la adición de estaño puede reducir considerablemente la temperatura de fusión de las aleaciones de plata-cobre-estaño, esta baja temperatura de fusión provoca una fragilidad extrema y la falta de utilidad práctica.
Para evitar la fragilidad, el contenido de estaño en la soldadura de plata-cobre-estaño no suele ser superior a 10%.
Para reducir aún más la temperatura de fusión de la soldadura a base de plata, se puede añadir cadmio a la aleación de plata-cobre-zinc.
Composición química y principales propiedades del metal de aportación para soldadura fuerte a base de plata
Metal de aportación para soldadura fuerte | Composición química (peso %) | Temperatura de fusión/℃ | Resistencia a la tracción/MPa | Resistividad eléctrica/μΩ-m | Temperatura de soldadura/℃ | |||||
---|---|---|---|---|---|---|---|---|---|---|
Ag | Cu | Zn | Cd | Sn | otros | |||||
BAg72Cu. | 72±1 | Rem. | – | – | – | – | 779~779 | 375 | 0.022 | 780~900 |
BAg50Cu. | 50±1.1 | Rem. | – | – | – | – | 779~850 | – | – | – |
BAg70Cu. | 70±1 | 26±1 | Rem. | – | – | – | 730~755 | 353 | 0.042 | – |
BAg65Cu. | 65±1 | 20±1.1 | Rem. | – | – | – | 685~720 | 384 | 0.086 | – |
BAg60Cu | 60 ±1 | Rem. | – | 10±0.5 | – | – | 602~718 | – | 720~840 | |
BAg50Cu | 50±1.1 | 34±1.1 | Rem. | – | 10±0.5 | – | 677~775 | 343 | 0.076 | 775~870 |
BAg45Cu | 45±1 | 30+1 | Rem. | – | – | – | 677~743 | 386 | 0.097 | 745~845 |
BAg25CuZn. | 25±1. | 40±1 | Rem. | – | – | – | 745~775 | 353 | 0.069 | 800~890 |
BAg10CuZn | 10±1 | 53±1.1 | Rem. | – | – | – | 815~850 | 451 | 0.065 | 850~950 |
BAg50CuZnCd | 50±1 | 15.5±1 | 16.5±2 | – | – | – | 627~635 | 419 | 0.072 | 635~760 |
BAg45CuZnCd | 45±1. | 15±1 | 16±2. | – | – | – | 607~618 | – | – | 620~760 |
BAg40CuZnCdNi | 40±1 | 16±0.5 | 17.8±0.5 | – | – | Ni0,2±0,1 | 595~605 | 392 | 0.069 | 605~705 |
BAg34CuZnCd | 35±1 | 26±1 | 21±2 | – | – | 607~702 | 411 | 0.069 | 700~845 | |
BAg50CuZnCdNi | 50±1.1 | 15.5±1 | 15.5±2 | – | – | Ni3±0,5 | 632~688 | 431 | 0.105 | 690~815 |
BAg56CuZnSn | 56±1 | 22±1 | 17±2 | 50.5 | 50.5 | – | 618~652 | – | – | 650~760 |
BAg34CuZnSn | 34±1 | 36±1.1 | 27+2 | 30.5 | 30.5 | – | 630~730 | – | – | 730~820 |
BAg50CuZnSnNi | 50±1 | 21.5±1 | 27±1.1 | 10.3 | 10.3 | Ni0,30~0,65。 | 650~670 | – | – | 670~770 |
BAg40CuZnSnNi | 40±1 | 25±1 | 30.5±1 | 30.3 | 30.3 | Ni1,30~1,65 | 630~640. | – | – | 640~740 |
El metal de aportación para soldadura fuerte de cobre-fósforo se utiliza ampliamente en la soldadura fuerte de cobre y aleaciones de cobre debido a su favorable rendimiento tecnológico y rentabilidad.
El fósforo cumple dos funciones en el cobre:
En primer lugar, reduce considerablemente el punto de fusión del cobre.
En segundo lugar, actúa como fundente autosoldante durante la soldadura fuerte en aire.
Para reducir aún más la temperatura de fusión de la aleación Cu-P y mejorar su tenacidad, también puede añadirse plata.
Es importante señalar que los metales de aportación cobre-fósforo y cobre-ratón-plata sólo pueden utilizarse para la soldadura fuerte de cobre y aleaciones de cobre y no pueden utilizarse para la soldadura fuerte de acero, aleaciones de níquel o aleaciones de cobre-níquel con un contenido de níquel superior a 10%.
Este tipo de metal de aportación puede dar lugar a segregación cuando se calienta lentamente, por lo que es mejor adoptar un método de soldadura fuerte de calentamiento rápido.
Composición química y propiedades de la soldadura de cobre y fósforo
Metal de relleno | Composición química (fracción másica) (%) | Temperatura de fusión | Resistencia a la tracción MPa | Resistividad/μΩ-m | ||||
---|---|---|---|---|---|---|---|---|
Cu | P | Ag | Sn | otros | ||||
Bcu95P. | Rem. | 5±0.3 | – | – | 710~924 | – | – | |
Bcu93P | Rem. | 6.8~7.5 | – | – | 710~800 | 470.4 | 0.28 | |
Bcu92PSb | Rem. | 6.3±0.4 | – | – | Sb1,5~2,0 | 690~800 | 303.8 | 0.47 |
Bcu91Ag | Rem. | 7±0.2 | 2±0.2 | – | – | 645~810 | – | – |
Bcu89Ag | Rem. | 5.8~6.7 | 5±0.2 | – | – | 650~800 | 519.4 | 0.23 |
Bcu80Pag | Rem. | 4.8~5.3 | 15±0.5 | – | – | 640~815 | 499.8 | 0.12 |
HLAgCu70-5 | Rem. | 5±0.5 | 25±0.5 | – | – | 650~710 | – | – |
HLCuP6-3 | Rem. | 5.7±0.3 | – | 3.5±0.5 | – | 640~680 | – | 0.35 |
Cu86SnP | Rem. | 5.3±0.5 | – | 7.5±0.5 | 0.8±0.4 | 620~660 | – | – |
Bcu80PSnAg | Rem. | 5.3±0.5 | 5±0.5 | 10±0.5 | – | 560~650 | – | – |
Cu77NiSnP. | 77.6 | 7.0 | 9.7 | – | Ni5.7 | 591~643 | – | – |
Al soldar cobre con soldaduras con base de Sn, es frecuente la formación del compuesto intermetálico Cu6Sn5 en la interfase entre la soldadura y el metal base. Por lo tanto, es importante considerar cuidadosamente la temperatura de soldadura fuerte y el tiempo de mantenimiento.
Cuando se utiliza un soldador, la capa de compuesto suele ser fina y tiene un impacto mínimo en el rendimiento de la unión.
Las uniones de latón soldadas con metal de aportación estaño-plomo son más resistentes que las uniones de cobre soldadas con el mismo metal de aportación. Esto se debe a que la disolución del latón en el metal de aportación líquido es más lenta, lo que da lugar a la formación de menos compuestos intermetálicos frágiles.
Metal de aportación para soldadura fuerte | Composición química | Temperatura de fusión | Resistencia a la tracción | Alargamiento | |||
---|---|---|---|---|---|---|---|
Sn | Ag | Sb | Cu | ||||
HL606 | 96.0 | 4.0 | – | – | 221 | 53.0 | – |
Sn95Sb | 95.0 | – | 5.0 | – | 233 | 39.2 | 43 |
Sn92AgCuSb | 92.0 | 5.0 | 1.0 | 2.0 | 250 | 49.0 | 2.3 |
Sn85AgSb | 84.5 | 8.0 | 7.5 | – | 270 | 80.4 | 8.8 |
Metal de aportación para soldadura fuerte | Composición química | Temperatura de fusión | ||
---|---|---|---|---|
97.0 | 3.0 | Sn | ||
HLAgPb97 | 97.5 | 1.5 | – | 304-305 |
HLAgPb97,5-1,0 | 92 | 2.5 | 1.0 | 310-310 |
HLAgPb92-5,5 | 83.5 | 1.5 | 5.5 | 287-296 |
HLAgPb83,5-15-1,5 | 97.0 | 3.0 | 15.0 | 265-270 |
Composición química y propiedades de las soldaduras a base de cadmio
Metal de relleno | Composición química (fracción másica) (%) | Temperatura de fusión/ | Resistencia a la tracción/MPa | ||
---|---|---|---|---|---|
Cd | Ag | Zn | |||
HL503 | 95 | 5 | 338~393 | 112.8 | |
HLAgCd96-1 | 96 | 3 | 1 | 300~325 | 110.8 |
Cd79ZnAg | 79 | 5 | 16 | 270~285 | 200 |
HL508 | 92 | 5 | 3 | 320~360 | – |
Soldadura sin plomo para soldar tubos de cobre
Marca | Composición (fracción de masa) | Línea de fase sólida/℃ | Liquidus/℃ |
E | 95Sn-4,5Cu-0,5Ag | 226 | 360 |
HA | 94.5Sn-3Sb-1.5Zn-0.5Ag-0.5Cu | 215 | 228 |
HB | 91.225Sn-5Sb-3.5Cu-0.275Ag | 238 | 360 |
CA | 96.25n-3.25Bi-0.2Cu-0.35Ag | 206 | 234 |
OA | 95,9Sn-3Cu-1Bi-0,1Ag | 215 | 238 |
AM | 95,45n-3Cu-1Sb-0,6Ag | 221 | 231 |
Resistencia de uniones de cobre y latón soldadas con parte de soldadura blanda
Marca de soldadura | Resistencia al cizallamiento/MPa | Resistencia a la tracción/MPa | ||
---|---|---|---|---|
cobre | latón | cobre | latón | |
S-Pb80Sn18Sb2 | 20.6 | 36.3 | 88.2 | 95.1 |
S-Pb68Sn30Sb2 | 26.5 | 2740 | 89.2 | 86.2 |
S-Pb58Sn40Sb2 | 36.3 | 45.1 | 76.4 | 78.40 |
S-Sn90Pb10 | 45.1 | 44.1 | 63.7 | 68.6 |
S-P697Ag3 | – | 29.4 | – | 49.0 |
S-Cd96Ag3Zn1 | 73.5 | – | 57.8 | - |
S-Sn95Sb5 | 37.2 | – | - | |
S-sn85Ag8Sb7 | – | 82.3 | – | – |
S-Sn92AgSCu2Sb1 | 35.3 | – | – | – |
S-Sn96Ag4P | 35.339.2~49.0 | – | 5.339.2~49.0 | – |
Los fundentes para soldadura fuerte comúnmente utilizados consisten en una matriz de bórax, ácido bórico o una mezcla de ambos, y se complementan con fluoruros o fluoroboratos de metales alcalinos o alcalinotérreos para lograr una temperatura de activación adecuada y mejorar la capacidad de eliminación de óxido.
Cuando se calienta, el ácido bórico (H3BO3) se descompone para formar anhídrido bórico (B2O3).
La fórmula de reacción es la siguiente:
2H3BO3→B2O3+3H2O
El punto de fusión del anhídrido bórico es de 580°C.
Puede reaccionar con óxidos de cobre, zinc, níquel y hierro para formar un borato soluble, que flota en la unión soldada como escoria. Esto no solo elimina la película de óxido, sino que también proporciona protección mecánica.
MeO+B2O3→MeO-B2O3
Bórax Na2B4O7 se funde a 741 ℃:
Na2B4O7→B2O3+2NaBO2
El anhídrido bórico y los óxidos metálicos reaccionan para formar boratos solubles. El metaborato sódico y los boratos se combinan para formar compuestos con una temperatura de fusión más baja, lo que facilita su ascenso a la superficie de las juntas de soldadura.
MeO+2NaBO2+B2O3>(NaBO2)2Me(BO2)2
La combinación de bórax y ácido bórico es un fundente muy utilizado. La adición de ácido bórico puede reducir la tensión superficial del fundente de bórax y mejorar su extensión. El ácido bórico también mejora la capacidad del residuo de fundente para desprenderse limpiamente de la superficie. Sin embargo, cuando se utiliza fundente de bórax-ácido bórico con metal de aportación de plata, su temperatura de fusión sigue siendo demasiado elevada y su viscosidad sigue siendo demasiado alta.
Para disminuir aún más la temperatura de fusión, se puede añadir fluoruro potásico. La función principal del fluoruro potásico es reducir la viscosidad del fundente y mejorar su capacidad para eliminar óxidos. Para reducir aún más la temperatura de fusión y aumentar su actividad, el KBF4 puede añadirse.
El punto de fusión del KBF4 es 540 ℃, y la descomposición de fusión es:
KBF4→KF+BF3
Marca | Composición (fracción de masa) (%) | Temperatura de acción ℃ | Propósito |
FB101 | Ácido bórico 30, fluoroborato potásico 70 | 550~850℃ | Fundente para soldadura de plata |
FB102 | Fluoruro potásico anhidro 42, fluoroborato potásico 25, anhídrido bórico 35 | 600~850℃ | El fundente para soldadura de plata más utilizado |
FB103 | Fluoborato de potasio>95, carbonato de potasio<5 | 550~750℃ | Para soldadura de plata, cobre, zinc y cadmio |
FB104 | Bórax 50, ácido bórico 35, fluoruro potásico 15 | 650~850℃ | Soldadura fuerte en horno con metal de aportación a base de plata |
Número | Componente | Propósito |
1 | ZnCl21130g,NH4Cl110g,H2O4L | Soldadura fuerte de cobre y aleaciones de cobre, acero |
2 | ZnCl21020g,NaCI280g,NH4CI,HCI30g,H2O4L | Soldadura del cobre y aleaciones de cobre, acero |
3 | ZnCl2600g,NaCl170g | Recubrimiento de soldadura por inmersión |
4 | ZnCl2710g, NH4Cl100g, Vaselina 1840g, H2O 180 g | Soldadura fuerte de cobre y aleaciones de cobre, acero |
5 | ZnCl21360g,NH4Cl140g,HC185g,H2O4L | Soldadura fuerte de bronce al silicio, bronce al aluminio y acero inoxidable |
6 | H3P04960g,H20455g | Bronce al manganeso soldado, Acero inoxidable |
QJ205 | ZnCl250g,NH4Cl15,CdCl230,NaF6 | Soldadura fuerte de cobre y aleaciones de cobre con metales de aportación a base de cadmio |
Número | Componente | Propósito |
1 | Clorhidrato de ácido glutámico 540g, urea 310g, agua 4L | Cobre, latón, bronce |
2 | Monobromuro de hidracina 280 g, agua 2550 g, agente humectante no iónico 1,5 g | Cobre, latón, bronce |
3 | Ácido láctico (85%) 260 g, agua 1190 g, agente humectante 3 g | Bronce arrugado |
El principal componente del fundente no corrosivo es la colofonia.
Existen tres fundentes de colofonia de uso común:
El cobre y sus aleaciones presentan una excelente soldabilidad debido a su elevada conductividad térmica y a sus favorables características de humectación. Pueden emplearse varios métodos de soldadura fuerte, cada uno de los cuales ofrece distintas ventajas para aplicaciones específicas:
Al soldar cobre y sus aleaciones, es necesario tener en cuenta consideraciones especiales:
Para la soldadura fuerte de cobre a alta frecuencia, el proceso requiere una cuidadosa optimización debido a la baja resistencia eléctrica del cobre. Las estrategias para superar este reto incluyen:
En la soldadura fuerte del cobre, la coordinación del metal de aportación y el fundente es la siguiente:
Cuando se sueldan superficies limpias, especialmente con soldaduras de estaño-plomo y estaño-plata, puede utilizarse fundente de colofonia. Para otras superficies, se puede utilizar colofonia activa, fundente corrosivo débil o fundente corrosivo.
Es importante señalar que el cobre puro no debe soldarse en atmósfera reductora, excepto el cobre libre de oxígeno, para evitar la fragilización por hidrógeno.
El metal de aportación y el fundente utilizados para la soldadura fuerte del latón suelen ser similares a los utilizados para la soldadura fuerte del cobre. Sin embargo, debe tenerse en cuenta que, debido a la presencia de óxido de zinc en la superficie del latón, no puede soldarse con colofonia inactiva. Además, cuando se suelda con cobre fósforo y soldadura de plata, debe utilizarse fundente FB102.
Para la soldadura fuerte de estaño-plomo, debe utilizarse un fundente de solución de ácido fosfórico. La soldadura fuerte con base de plomo requiere el uso de un fundente para soldadura fuerte con solución de óxido de zinc. El fundente Q205 se utiliza para la soldadura fuerte a base de cadmio. Las soldaduras BAg45CuCdNi y BAg45CuCd deben soldarse con los fundentes FB102 o FB103. Otras soldaduras con base de plata, así como las soldaduras de cobre-fósforo y cobre-fósforo-plata, deben soldarse con el fundente FB102. Se recomienda realizar la soldadura fuerte con el fundente FB104 en una atmósfera protectora dentro de un horno.
Cuando se suelda el bronce al berilio en su estado de envejecimiento por enfriamiento y soldadura blanda, es importante seleccionar un metal de aportación para soldadura fuerte con una temperatura de fusión inferior a 300°C. La combinación preferida para esta aplicación es 63Sn-37Pb en combinación con un fundente corrosivo débil o un fundente corrosivo.
Además, la soldadura fuerte y el tratamiento con solución deben realizarse simultáneamente durante el proceso de soldadura.
La soldadura blanda tiene un impacto mínimo en el índice de rendimiento del bronce al berilio, por lo que para la soldadura fuerte se pueden utilizar soldaduras blandas y fundentes similares a los utilizados para el bronce al berilio.
Es importante señalar que el bronce al cromo no debe soldarse en su estado de envejecimiento en solución, sino en el estado de tratamiento en solución seguido de envejecimiento.
Cuando se utiliza un método de calentamiento rápido para la soldadura fuerte, se recomienda utilizar la soldadura de plata con la temperatura de fusión más baja, como BAgA0 CuZnCdNi.
La soldadura fuerte del estaño-bronce es similar a la soldadura fuerte del cobre y el latón, pero con la ventaja añadida de evitar la fragilización por hidrógeno y la volatilización del zinc cuando se suelda en una atmósfera protectora.
No obstante, hay que tener en cuenta que el estaño-bronce que contiene fósforo tiene tendencia al agrietamiento por tensión.
Para la soldadura blanda, se recomienda utilizar un fundente corrosivo fuerte que contenga ácido clorhídrico.
Durante la soldadura fuerte, existe una tendencia al agrietamiento por tensión y a la penetración intergranular del metal de aportación. La temperatura de soldadura debe ser inferior a 760°C.
Pueden utilizarse soldaduras de plata con temperaturas de fusión más bajas, como BAg65CuZn, BAg50 CuZnCd, BAg40 CuZnCdNi y BAg56 CuZnSn. Cuanto más baja sea la temperatura de fusión, mejor.
Para obtener resultados óptimos, se recomienda utilizar los fundentes FB102 y FB103.
Al realizar soldaduras blandas, es importante utilizar un fundente corrosivo fuerte que contenga ácido clorhídrico para eliminar la película de óxido de la superficie. La soldadura más utilizada para este proceso es la de estaño-plomo.
Para la soldadura fuerte, se suele utilizar metal de aportación de plata. Para evitar que el aluminio se difunda en la soldadura de plata, el tiempo de calentamiento de la soldadura debe ser lo más corto posible. El chapado de la superficie del bronce de aluminio con cobre o níquel también puede impedir la difusión del aluminio en la soldadura.
El proceso de soldadura del cobre blanco de zinc es similar al del latón. Para la soldadura fuerte se suelen utilizar las siguientes soldaduras de plata: BAg56CuZnSn, BAg50CuZnSnNi, BAg40CuZnNi y BAg56CuZnCd, entre otras. Los fundentes recomendados para su uso son FB102 y FB103.
Para soldar cobre blanco con zinc, puede utilizarse un fundente de solución de ácido fosfórico o la superficie puede recubrirse previamente con cobre.
Los metales de aportación para soldadura fuerte que pueden utilizarse son, entre otros, BAg60CuZn, BAg45CuZn, BAg40CuZnCdNi y BAg50 CuZnCd.
No se recomienda utilizar soldadura de cobre-fósforo-plata, ya que el fósforo y el níquel formarán una fase compuesta quebradiza.
Resistencia de las uniones de cobre y latón soldadas con soldadura de plata
Metal de relleno | Resistencia al cizallamiento/MPa | Resistencia a la tracción/MPa | ||
---|---|---|---|---|
cobre | latón | cobre | latón | |
BAg45CuZn | 177 | 215 | 181 | 325 |
BAg50CuZn | 171 | 208 | 174. | 334 |
BAg65CuZn | 171 | 208 | 177 | 334 |
BAg70CuZn | 166 | 199 | 185 | 321 |
BAg40CuZnCdNi | 167 | 194 | 179 | 339 |
BAg50CuZnCd | 167 | 226 | 210 | 375 |
BAg35CuZnCd | 164 | 190 | 167 | 328 |
BAg40CuZnSnNi | 98 | 245 | 176 | 295 |
BAg50CuZnSn | – | – | 220 | 240 |
Propiedades mecánicas de uniones de cobre soldadas con soldaduras de cobre fósforo y cobre fósforo plata
Metal de relleno | Resistencia a la tracción /MPa | Resistencia al cizallamiento /MPa | Ángulo de flexión (°) | Resistencia al impacto /J - cm-2 |
BCu93P | 186 | 132 | 25 | 6 |
BCu92PSb | 233 | 138 | 90 | 7 |
BCu80PAg | 255 | 154 | 120 | 23 |
BCu89PAg | 242 | 140 | 120 | 21 |
Para las aleaciones de cobre endurecibles por envejecimiento, como el bronce al berilio, que han sido sometidas a tratamiento térmico, el único paso después de la soldadura fuerte es eliminar el fundente residual y limpiar la superficie de la pieza.
La razón principal para eliminar los residuos es evitar la corrosión en la pieza y, en algunos casos, conseguir un buen aspecto o preparar la pieza para su posterior procesamiento.
En la Tabla 10 se muestra la resistencia de las uniones soldadas blandas de cobre y latón utilizando varios materiales de soldadura blanda de uso común.
Tabla 10: Resistencia de las uniones por soldadura blanda de cobre y latón
Grado del material de soldadura | Resistencia al cizallamiento /MPa | Resistencia a la tracción /MPa | ||
Cobre | Latón | Cobre | Latón | |
S-Pb80Sn18Sb2 | 20.6 | 36.3 | 88.2 | 95.1 |
S- Pb68Sn30Sb2 | 26.5 | 27.4 | 89.2 | 86.2 |
S-Pb58Sn405b2 | 36.3 | 45.1 | 76.4 | 78.4 |
S-Pb97Ag3 | 33.3 | 34.3 | 50.0 | 58.8 |
S-Sn90Pb10 | 45.1 | 44.1 | 63.7 | 68.6 |
S-Sn95Sb5 | 37.2 | – | – | – |
S-Sn92Ag5Cu2Sb1 | 35.3 | – | – | – |
S-Sn85Ag85B7 | 一 | 42.3 | – | – |
S-Cd96Ag3Znl | 57.8 | – | 73.8 | – |
S-Cd95Ag5 | 44.1 | 46.0 | 87.2 | 88.2 |
S-Cd92Ag5Zn3 | 48.0 | 54.9 | 90.1 | 96.0 |
En cobre de soldadura con soldadura de estaño-plomo, pueden utilizarse fundentes no corrosivos como la solución de alcohol de colofonia o una mezcla de colofonia activada y solución acuosa de ZnCl2 + NH4Cl. Este último también puede utilizarse para soldadura latón, bronce y bronce al berilio.
Para la soldadura fuerte de latón de aluminio, bronce de aluminio y latón de silicio, puede utilizarse un fundente consistente en cloruro de cinc en solución de ácido clorhídrico. Para la soldadura fuerte del bronce al manganeso, se puede utilizar como fundente una solución de ácido fosfórico.
Cuando se utilizan soldaduras con base de plomo, se puede utilizar como fundente una solución acuosa de cloruro de zinc, y para las soldaduras con base de cadmio, se puede utilizar el fundente FS205.
Materiales y fundentes para soldadura fuerte
Para soldar cobre, se pueden utilizar soldaduras con base de plata y soldaduras de cobre-fósforo. La soldadura con base de plata tiene un punto de fusión moderado, buena procesabilidad y excelentes propiedades mecánicas, eléctricas y de conductividad térmica. Es el material de soldadura fuerte más utilizado.
Para aplicaciones que requieran una alta conductividad eléctrica, debe elegirse una soldadura que contenga plata, como B-Ag70CuZn. Para la soldadura fuerte en vacío o en horno con atmósfera protectora, deben utilizarse soldaduras con base de plata sin elementos volátiles, como B-Ag50Cu y B-Ag60CuSn.
Las soldaduras con menor contenido de plata son más baratas pero tienen mayor temperaturas de soldadura y menor tenacidad de la unión, lo que las hace adecuadas para aplicaciones de soldadura fuerte con menores requisitos de cobre y aleaciones de cobre.
Las soldaduras de cobre-fósforo y cobre-fósforo-plata sólo pueden utilizarse para la soldadura fuerte del cobre y sus aleaciones. La soldadura B-Cu93P tiene una excelente fluidez y es adecuada para la soldadura fuerte de piezas en las industrias mecánica, eléctrica, de instrumentación y de fabricación que no estén sometidas a cargas de impacto.
El tamaño ideal de la separación es de 0,003-0,005 mm. Las soldaduras de cobre-fósforo-plata (como B-Cu70Pag) tienen mejor tenacidad y conductividad eléctrica que la soldadura de cobre-fósforo y se utilizan principalmente para uniones eléctricas de alta conductividad. En la Tabla 11 se muestra el rendimiento de varios materiales de soldadura fuerte comúnmente utilizados para la soldadura fuerte de uniones de cobre y latón.
Tabla 11: Rendimiento de las uniones de cobre y latón con soldadura fuerte
Grado del material de soldadura | Resistencia al cizallamiento /MPa | Resistencia a la tracción /MPa | Ángulo de flexión /(°) | Energía de absorción de impactos /J | ||
Cobre | Latón | Cobre | Latón | Cobre | Cobre | |
H62 | 165 | - | 176 | - | 120 | 353 |
B-Cu60ZnSn-R | 167 | - | 181 | - | 120 | 360 |
B-Cu54Zn | 162 | - | 172 | - | 90 | 240 |
B-Zn52Cu | 154 | - | 167 | - | 60 | 211 |
B-Zn64Cu | 132 | - | 147 | - | 30 | 172 |
B-Cu93P | 132 | - | 162 | 176 | - | 58 |
B-Cu92PSb | 138 | - | 160 | 196 | 25 | - |
B-Cu93Pag | 159 | 219 | 225 | 292 | - | - |
B-Cu80Pag | 162 | 220 | 225 | 343 | 120 | 205 |
B-Cu90P6Sn4 | 152 | 205 | 202 | 255 | 120 | 182 |
B-Ag70CuZn | 167 | 199 | 185 | 321 | 90 | - |
B-Ag65CuZn | 172 | 211 | 177 | 334 | - | - |
B-Ag55CuZn | 172 | 208 | 174 | 328 | - | - |
B-Ag45CuZn | 177 | 216 | 181 | 325 | - | - |
B-Ag25CuZn | 167 | 184 | 174 | 316 | - | - |
B-Ag10CuZn | 158 | 161 | 167 | 314 | - | - |
B-Ag72Cu | 165 | - | 177 | - | - | - |
B-Ag50CuZnCd | 177 | 226 | 210 | 375 | - | - |
B-Ag40CuZnCd | 168 | 194 | 179 | 339 | - | - |