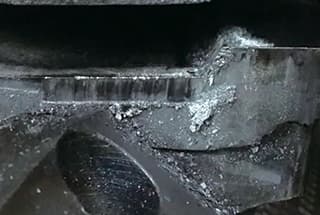
¿Por qué fallan inesperadamente algunas matrices de forja? En este artículo se examina el problema habitual de los fallos por rotura de las matrices en una línea de forja de alta velocidad de 3500T. Al explorar las causas y presentar medidas de mejora eficaces, el artículo ofrece soluciones prácticas que pueden prolongar la vida útil de las matrices y mejorar la eficacia de la producción. Los lectores comprenderán mejor los retos técnicos y aprenderán estrategias para evitar fallos similares en sus operaciones.
En 2005, nuestra empresa compró a Alemania una línea de producción automática de forja de categoría mundial (Figura 1). Esta línea de producción es capaz de forjar a alta velocidad y tiene una capacidad de 3500 t.
Fig. 1 Panorámica de la línea de producción automática de forja rápida de 3500 t
La velocidad máxima de producción del diseño es de 25 piezas por minuto.
La alimentación, el calentamiento, la forja y el tratamiento postcalentamiento se controlan automáticamente.
Se adopta el proceso de forja cerrada, que implica cinco pasos para lograr la conformación de la forja: preajuste, recalcado, preforja, forja final y punzonado.
Como se muestra en la figura 2, el sistema de refrigeración del molde utiliza la tecnología de pulverización automática. La dirección medio refrigerante es una mezcla de agua y agente desmoldeante en una proporción específica.
Fig. 2 refrigeración y lubricación automáticas por pulverización
Durante la producción real, se ha observado que ciertas variedades de forja no alcanzan su vida útil normal, siendo la principal forma de fallo el agrietamiento de la matriz (véase la Fig. 3).
Por término medio, unas 1.500 piezas se ven afectadas por el agrietamiento, lo que da lugar a unos 2.500 moldes desechados. En los casos más graves, unas 300 piezas experimentan grietas, lo que lleva a desechar aproximadamente 1200 moldes.
Fig. 3 Posición y forma de la grieta del molde (grieta en el círculo rojo)
El primer paso consistió en recuperar los registros de inspección física y química, así como los registros de inspección física y química del tratamiento térmico del acero para troqueles. También se verificó la dureza de la matriz averiada y no se encontraron anomalías evidentes.
En segundo lugar, se realizó una observación cuidadosa de la forma, el tamaño y la profundidad de la grieta en el molde de fallo de campo. Se descubrió que la altura de la grieta parecía haberse formado gradualmente por el corte con gas a alta temperatura y alta presión.
El tercer paso consistió en ensamblar las matrices superior e inferior de la forja final y las piezas en bruto preforjadas en caliente mediante CAD (como se muestra en la Fig. 4).
Aunque existía un espacio cerrado con una altura de aproximadamente 1,9 mm, con un orificio de escape, se comprobó que la grieta de la matriz era evidente durante la producción real. Por lo tanto, fue necesario analizar detenidamente esta cuestión utilizando un software de simulación de deformaciones.
Fig. 4 Dibujo CAD del ensamblaje final de las matrices superior e inferior de forja y de las piezas en bruto preforjadas en caliente
En cuarto lugar, utilizando la simulación Deform y una observación cuidadosa, se observó que durante la simulación de conformado de la forja final, en el paso 16, los arcos a ambos lados de los radios de la matriz superior de la forja final hacen contacto por primera vez con la pieza en bruto preforjada caliente. Esto da lugar a la formación de un espacio confinado independiente entre los dos orificios de escape más próximos a izquierda y derecha, como se muestra en la Fig. 5.
Fig. 5 simulación de la deformación del molde de falla (espacio confinado independiente en el círculo verde)
Tras realizar un análisis de simulación de deformación en varias matrices con grietas anormales, se descubrió que durante el proceso de forja se forma un espacio confinado independiente entre la pieza en bruto caliente y los dos orificios de escape más próximos a izquierda y derecha de las matrices superior e inferior. Este fenómeno se representa en la Fig. 6, Fig. 7 y Fig. 8.
Fig. 6 simulación de la deformación del molde de falla II (espacio confinado independiente en el círculo verde)
Fig. 7 simulación de tres deformaciones del molde de falla (espacio confinado independiente en el círculo verde)
Fig. 8 simulación de la deformación de cuatro moldes fallidos (espacio confinado independiente en el círculo verde)
El quinto paso consiste en analizar detalladamente la información presentada anteriormente.
Las características de producción de la línea de producción automática de forja de alta velocidad de 3500t dictan que cuando el deslizador alcanza el punto muerto superior, el sistema de pulverización se extenderá rápidamente hacia los moldes superior e inferior de los cinco pasos y aplicará una cantidad significativa de agente de desmoldeo y mezcla de agua sobre ellos durante aproximadamente un segundo.
La aplicación oportuna de una gran cantidad de refrigerante (es decir, la mezcla de desmoldeante y agua) tiene dos propósitos importantes. En primer lugar, garantiza un desmoldeo y expulsión rápidos y estables de las piezas forjadas calientes y, en segundo lugar, ayuda a mantener la temperatura de trabajo de la matriz dentro de un rango específico de baja temperatura. Esto es crucial para evitar que la matriz se dañe debido a un grave desgaste o deformación causada por un aumento repentino de la temperatura en un corto período de tiempo.
En resumen, la aplicación oportuna de una cantidad significativa de refrigerante es una medida crucial para garantizar el buen funcionamiento de la forja automática de alta velocidad y es absolutamente esencial.
Durante la forja, la pieza en bruto caliente (que tiene una temperatura de alrededor de 1150300 ℃) a una alta velocidad. Este contacto instantáneo puede hacer que el refrigerante se convierta en gas a alta temperatura y alta presión. Sin embargo, particularmente en un espacio confinado independiente, el gas de alta temperatura y alta presión no se puede descargar suavemente a través del orificio de escape, y finalmente actúa sobre el molde caliente, lo que lleva a daños en el corte.
A partir de los resultados del análisis anterior, se han formulado las medidas de mejora.
Inicialmente, el prematriz de forja para la matriz I, que había fallado anteriormente, se han realizado modificaciones experimentales. Ahora, la superficie del radio de la matriz superior de forja final entra primero en contacto con el radio en bruto de preforja caliente cuando se coloca en la cavidad de forja final para forjar. No hay espacio confinado independiente entre los dos orificios de escape más cercanos a izquierda y derecha.
Durante la forja, se genera una gran cantidad de gas a alta temperatura y alta presión, que ahora se puede descargar de forma suave y oportuna por el orificio de escape, el hueco entre las varillas eyectoras superior e inferior y el molde, y el hueco entre los moldes divididos, como se muestra en la figura 9.
El plan experimental de mejora del molde I ha demostrado su eficacia durante la verificación práctica. La vida útil del molde ha alcanzado ya las 15.000 piezas y no se han vuelto a producir fallos por grietas en el molde.
Fig. 9 simulación de la deformación del molde de falla después de la mejora (no hay espacio confinado independiente en el círculo verde)
Basándonos en la exitosa experimentación, hemos mejorado secuencialmente otros moldes problemáticos. Esto garantiza que cuando una nueva pieza en bruto de forja en caliente llegue al paso problemático, no habrá ningún espacio confinado aislado entre la pieza en bruto y los dos orificios de escape más cercanos en los lados izquierdo y derecho del molde. El método de mejora se detalla en las figuras 10, 11 y 12.
Fig. 10 simulación de la deformación tras la mejora del molde II averiado (no hay espacio confinado independiente en el círculo verde)
Fig. 11 simulación de la deformación tras la mejora del molde de falla III (no hay espacio confinado independiente en el círculo verde)
Fig. 12 simulación de la deformación tras la mejora del molde IV averiado (no hay espacio confinado independiente en el círculo verde)
Los moldes, a saber, I, II, III y IV, se mejoraron individualmente y los resultados fueron muy eficaces. La vida media de los moldes ha aumentado a 15.000 piezas sin que se produzcan fallos por grietas.
Además de garantizar la calidad del aspecto de las piezas forjadas, se puede observar un importante ahorro de costes (Tabla 1) gracias a la reducción de los costes de las matrices. Por otra parte, al evitar la necesidad de reparar posteriormente las piezas forjadas, también se previene el derroche innecesario de mano de obra y recursos materiales.
Tabla 1 tabla de ahorro de costes del molde mejorado
NO. |
Demanda de forja (10000 piezas / mes) |
Demanda de molde antes de la mejora (pieza / mes) |
Demanda de molde tras la mejora (pieza / mes) |
Troquel salvado tras la mejora (pieza / mes) |
Coste ahorrado tras la mejora (10000 yuanes / mes) |
Ahorro mensual (10000 yuanes / mes) |
Ahorro anual (10000 yuanes) |
Molde I |
3 |
12~20 |
3~4 |
10 |
4.5 |
18 |
216 |
Molde II |
|||||||
Molde III |
|||||||
Molde IV |
(1)Para mantener el funcionamiento estable de la línea de producción automática de forja de alta velocidad de 3500t, se debe rociar una gran cantidad de refrigerante de niebla. Sin embargo, cuando el dispositivo de pulverización funciona mal, como el fallo de la válvula de aire (lo que resulta en la falta de aire para la pulverización del molde superior e inferior) o el fallo de la válvula de agua (la válvula de pulverización del molde superior no pulveriza, la válvula de pulverización del molde inferior pulveriza durante mucho tiempo, o tanto el molde superior como el inferior pulverizan durante mucho tiempo), pueden surgir problemas.
Además, el fallo de la válvula del agente desmoldeante (la válvula del agente desmoldeante del molde superior no pulveriza, la válvula del agente desmoldeante del molde inferior pulveriza durante mucho tiempo, o tanto el molde superior como el inferior pulverizan durante mucho tiempo) puede dar lugar a que quede agua o una mezcla de agua y agente desmoldeante en el cóncavo inferior de la pieza en bruto caliente. Esto puede dar lugar a que el molde superior no se lubrique y enfríe a tiempo, lo que provoca un rápido aumento de la temperatura. El molde es entonces más propenso a ser cortado y dañado por el gas a alta temperatura y alta presión.
(2) Cuando el gas a alta temperatura y alta presión actúa sobre una matriz caliente, puede causar daños por corte. Esto plantea la cuestión de por qué no se corta la forja en caliente, sino sólo la matriz.
Más tarde se descubrió que la forja en caliente, que tiene una temperatura de alrededor de 1150 ~ 1200 ℃, tiene una plasticidad extremadamente alta, mientras que la matriz, con una temperatura de trabajo de alrededor de 200 ~ 300 ℃, no tiene la misma plasticidad.
Tanto las piezas forjadas en caliente como las matrices en caliente están sometidas a altas temperaturas y gas a alta presión, pero la huella de corte en las piezas forjadas en caliente se reparará por sí sola debido a su gran plasticidad. Por otro lado, la matriz debe permanecer a una temperatura relativamente baja para mantener su dureza, y no puede tener ninguna plasticidad debido a un aumento brusco de la temperatura. Como resultado, incluso una pequeña grieta causada por la alta temperatura y la alta presión corte con gas no puede repararse por sí sola y, a medida que prosigue el trabajo de forja y conformado, la grieta se irá extendiendo lentamente y acabará provocando el desguace del molde.
(3) La práctica ha demostrado que esta mejora tiene éxito y el efecto es muy notable, lo que puede considerarse una cura para el problema.
Después de un largo período de observación y verificación, la línea de producción automática de forja de alta velocidad de 3500t ya no experimenta fallos de grietas en la matriz.
Los diseñadores pertinentes de la sala de proceso de forja del grupo de conformación en caliente del centro físico y químico de materiales de la empresa del grupo también han reconocido esta mejora, y se han publicado planos actualizados.
La resolución con éxito del problema de la rotura de la matriz en la línea de producción automática de forja de alta velocidad de 3500 toneladas ofrece valiosas perspectivas para la diseño de troqueles de la misma línea de producción.
Gracias a esta mejora, ha aumentado la calidad del aspecto de las piezas forjadas y se ha reducido considerablemente el coste de las matrices.