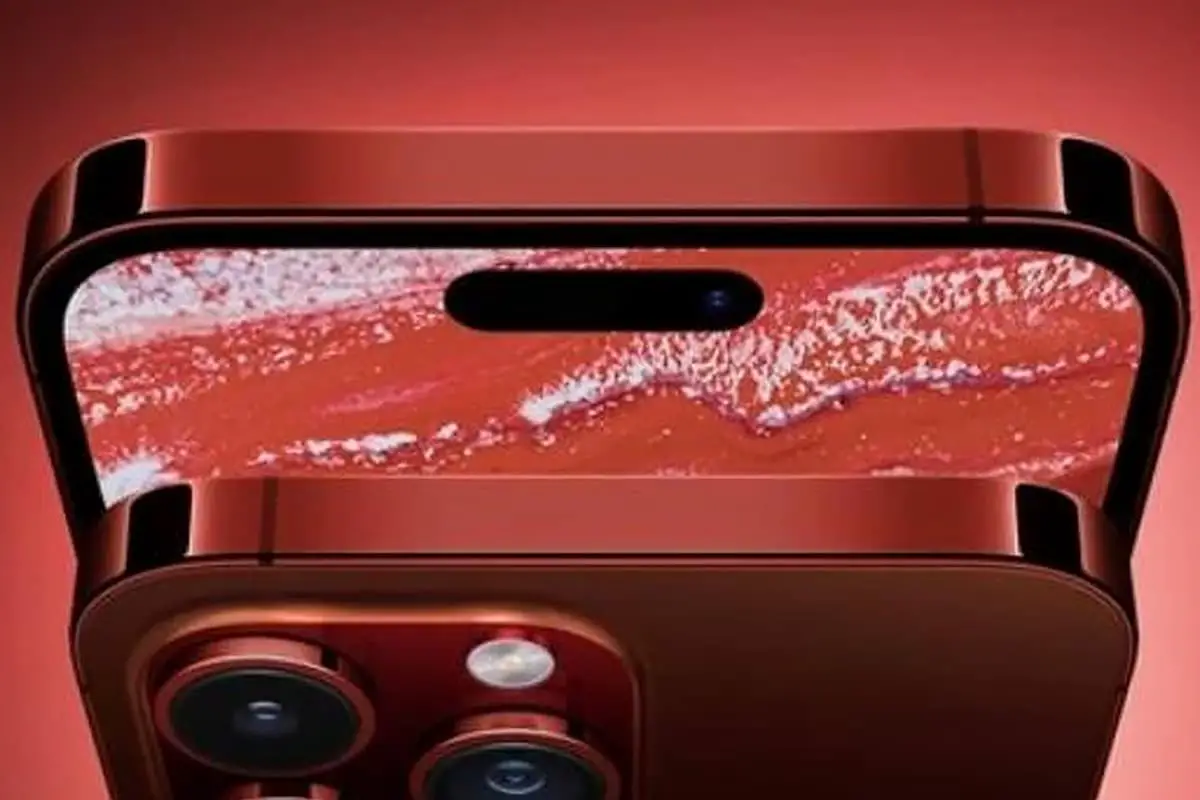
¿Se ha preguntado alguna vez cuál es el secreto de la resistencia y durabilidad de las aleaciones de titanio? En este artículo, nos sumergiremos en el fascinante mundo de las técnicas de tratamiento térmico que transforman estas aleaciones en materiales de alto rendimiento. Nuestro equipo de expertos le guiará a través de los principios, procesos y efectos de los distintos métodos de tratamiento térmico, proporcionando información valiosa tanto para ingenieros como para aficionados. Prepárese para descubrir la ciencia que se esconde tras las extraordinarias propiedades de las aleaciones de titanio.
(1) La transformación de fase martensítica no provoca cambios significativos en las propiedades de las aleaciones de titanio. Esta característica es diferente de la transformación de fase martensítica del acero. El refuerzo por tratamiento térmico de las aleaciones de titanio se basa en la descomposición por envejecimiento de la fase subestable formada por el temple, incluida la fase martensítica. Tratamiento térmico para el tipo a puro titanio es básicamente ineficaz; se utiliza principalmente para aleaciones de titanio de tipo α+β.
(2) El tratamiento térmico debe evitar la formación de la fase ω, ya que hace que las aleaciones de titanio sean frágiles. La elección correcta del proceso de envejecimiento puede hacer que la fase ω se descomponga, como el uso de una temperatura de envejecimiento más alta.
(3) Es difícil refinar los granos de aleación de titanio mediante transformaciones de fase repetidas, a diferencia de los materiales de acero. La transformación de fase repetida de austenita y perlita (o ferrita, cementita) pueden controlar la nucleación y el crecimiento de nuevas fases para lograr el refinamiento del grano en la mayoría de los aceros. Este fenómeno no existe en las aleaciones de titanio.
(4) Una conductividad térmica deficiente puede provocar un endurecimiento deficiente de las aleaciones de titanio, especialmente de las aleaciones de titanio α+β. La tensión térmica de temple es grande, y las piezas son propensas a la deformación durante el temple. Debido a la mala conductividad térmica, la deformación de la aleación de titanio provoca fácilmente un aumento local de la temperatura, lo que puede hacer que la temperatura local supere el punto de transformación β y se forme la estructura Widmanstatten.
(5) Las propiedades químicas vivas hacen que las aleaciones de titanio reaccionen fácilmente con el oxígeno y el vapor de agua durante el tratamiento térmico. Se forma una capa o cascarilla rica en oxígeno en la superficie de la pieza, lo que reduce el rendimiento de la aleación. Al mismo tiempo, las aleaciones de titanio tienden a absorber hidrógeno durante el tratamiento térmico, provocando fragilización por hidrógeno.
(6) El punto de transición β varía significativamente, aunque se trate de la misma composición, debido a los diferentes hornos de fundición.
(7) Cuando se calienta en la región de la fase β, los granos β tienden a aumentar de tamaño. El engrosamiento de los granos β puede hacer que la plasticidad de la aleación disminuya bruscamente, por lo que la temperatura y el tiempo de calentamiento deben controlarse estrictamente. El tratamiento térmico para el calentamiento en la región de fase β debe utilizarse con precaución.
La transformación de fase de la aleación de titanio es la base del tratamiento térmico de la aleación de titanio. Para mejorar el rendimiento de las aleaciones de titanio, es necesario utilizar un tratamiento térmico adecuado además de una aleación razonable.
Existen muchos tipos de tratamientos térmicos para las aleaciones de titanio, como el tratamiento de recocido, el tratamiento de envejecimiento, el tratamiento térmico de deformación y el tratamiento térmico químico, entre otros.
El recocido es adecuado para diversas aleaciones de titanio, y su principal objetivo es eliminar tensiones, mejorar la plasticidad de la aleación y estabilizar la estructura.
Las formas de recocido incluyen el recocido de alivio de tensiones, el recocido de recristalización y el recocido doble, recocido isotérmicorecocido al vacío, entre otros.
La figura 1 muestra el intervalo de temperaturas de recocido de la aleación de titanio utilizando diversos métodos.
Figura 1 Diagrama esquemático del intervalo de temperaturas de recocido de diversos métodos en la aleación de titanio
(1) Recocido de distensión.
El recocido de distensión puede utilizarse para eliminar tensión interna generados durante la fundición, la deformación en frío y la soldadura.
La temperatura del recocido de distensión debe ser inferior a la temperatura de recristalización, normalmente entre 450-650 ℃.
El tiempo necesario depende del tamaño de la sección transversal de la pieza, del historial de procesamiento y del grado de alivio de tensiones requerido.
(2) Recocido ordinario.
La finalidad del recocido ordinario es eliminar las tensiones básicas del producto semiacabado de aleación de titanio y aumentar la resistencia y la plasticidad de acuerdo con las condiciones técnicas requeridas.
La temperatura de recocido y la temperatura de recristalización suelen ser equivalentes o ligeramente inferiores a la temperatura inicial. Este proceso de recocido se utiliza generalmente en productos metalúrgicos de fábrica y también puede denominarse recocido de fábrica.
(3) Recocido completo.
El objetivo del recocido completo es eliminar completamente el endurecimiento por proceso, estabilizar la organización y mejorar la plasticidad. Este proceso se produce principalmente por recristalización y también se conoce como recocido de recristalización.
La temperatura de recocido se sitúa preferentemente entre la temperatura de recristalización y la temperatura de transición de fase. Si la temperatura supera la temperatura de transición de fase, se formará la estructura Widmanstatten y se deteriorarán las propiedades de la aleación.
El tipo de recocido, la temperatura y los métodos de enfriamiento son diferentes para los distintos tipos de aleaciones de titanio.
(4) Doble recocido.
El doble recocido puede utilizarse para mejorar la plasticidad de la aleación, la tenacidad a la fractura y la estabilidad de la organización. Tras el recocido, la organización de la aleación es más uniforme y cercana al estado de equilibrio.
Este tipo de recocido suele utilizarse para garantizar la estabilidad de la estructura y el rendimiento de las aleaciones de titanio termorresistentes sometidas a altas temperaturas y esfuerzos prolongados.
El recocido doble consiste en calentar y enfriar con aire la aleación dos veces. La temperatura de calentamiento del primer recocido a alta temperatura es superior o cercana a la temperatura final de recristalización, de modo que la recristalización pueda avanzar completamente sin un crecimiento significativo del grano de cristal, y se controla la fracción de volumen de la fase ap.
La estructura no es suficientemente estable tras el enfriamiento por aire, y es necesario un segundo recocido a baja temperatura. La temperatura de recocido es inferior a la temperatura de recristalización, y la temperatura se mantiene durante mucho tiempo para descomponer completamente la fase β metaestable obtenida por recocido a alta temperatura.
(5) Recocido isotérmico.
El recocido isotérmico puede obtener la mejor plasticidad y estabilidad térmica y es adecuado para aleaciones de titanio de fase dual con un alto contenido de elementos β-estabilizadores.
El recocido isotérmico adopta el enfriamiento jerárquico, lo que significa que tras calentar a una temperatura superior a la de recristalización, la pieza se transfiere inmediatamente a otro horno de temperatura inferior (generalmente 600-650℃) para aislarla y, a continuación, se enfría con aire hasta alcanzar la temperatura ambiente.
El envejecimiento por enfriamiento rápido es la principal forma de fortalecer el tratamiento térmico de las aleaciones de titanio, utilizando el cambio de fase para producir un efecto de fortalecimiento, que también se conoce como fortalecimiento por tratamiento térmico.
El efecto fortalecedor del tratamiento térmico de las aleaciones de titanio viene determinado por la naturaleza del elemento de aleacióny las especificaciones del tratamiento térmico.
Estos factores afectan al tipo, composición, cantidad y distribución de la fase metaestable obtenida por temple de la aleación, así como a la naturaleza, estructura y dispersividad de la fase precipitada durante la descomposición de la fase metaestable, que está relacionada con la composición de la aleación, las especificaciones del proceso de tratamiento térmico y la estructura original.
Para aleaciones con una composición determinada, el efecto del refuerzo por envejecimiento depende del proceso de tratamiento térmico seleccionado.
Cuanto mayor sea la temperatura de enfriamiento, más evidente será el efecto de fortalecimiento por envejecimiento, pero un enfriamiento por encima de la temperatura de transformación β provocará fragilidad debido a granos excesivamente gruesos.
En el caso de las aleaciones de titanio bifásicas con menor concentración, puede utilizarse un temple a mayor temperatura para obtener más martensita.
Las aleaciones de titanio bifásicas con una mayor concentración deben templarse a una temperatura más baja para obtener una fase β más metaestable, de modo que pueda obtenerse el máximo efecto de refuerzo por envejecimiento.
El método de refrigeración suele ser por agua o por aceite, y el proceso de enfriamiento debe ser rápida para evitar la descomposición de la fase β durante el proceso de transferencia y reducir el efecto de refuerzo por envejecimiento.
La temperatura y el tiempo de envejecimiento deben elegirse para obtener los mejores criterios de rendimiento global, con una temperatura general de envejecimiento de 500-600℃ en la aleación de titanio de tipo α + β y un tiempo de 4-12 horas.
La temperatura de envejecimiento de la aleación de titanio de tipo β es de 450-550℃, el tiempo es de 8-24 horas, y el método de enfriamiento es la refrigeración por aire.
El tratamiento térmico por deformación es una combinación eficaz del procesamiento por presión (forja, laminado, etc.) y la tecnología de tratamiento térmico, que permite tanto el refuerzo por deformación como el refuerzo por tratamiento térmico para obtener una organización y un rendimiento globales que no pueden lograrse con un único método de refuerzo.
En la figura 2 se muestra un proceso habitual de tratamiento térmico por deformación.
Diferentes tipos de termomecánica tratamiento térmico se clasifican según la relación entre la temperatura de deformación y la temperatura de recristalización y la temperatura de transición de fase.
Según la temperatura de deformación, puede dividirse en:
Figura 2 Representación esquemática del proceso de tratamiento térmico por deformación en la aleación de titanio.
(a) Tratamiento térmico de deformación a alta temperatura;
(b) Tratamiento térmico de deformación a baja temperatura
(1) Tratamiento termomecánico a alta temperatura
Consiste en calentar por encima de la temperatura de recristalización, deformar de 40% a 85%, enfriar rápidamente y someter a continuación a un tratamiento térmico de envejecimiento convencional.
(2) Tratamiento termomecánico a baja temperatura
La deformación se realiza a unos 50% por debajo de la temperatura de recristalización, seguida de un tratamiento de envejecimiento convencional.
(3) Tratamiento termomecánico compuesto
Es un proceso que combina el tratamiento termomecánico a alta temperatura y el tratamiento termomecánico a baja temperatura.
Las aleaciones de titanio tienen un elevado coeficiente de fricción y una escasa resistencia al desgaste (en general, unos 40% menos que el acero), lo que las hace propensas a adherirse a las superficies de contacto y a provocar corrosión por fricción.
Las aleaciones de titanio son más resistentes a la corrosión en medios oxidantes, pero menos resistentes a la corrosión en medios reductores (como ácido clorhídrico, ácido sulfúrico, etc.).
Para mejorar estas propiedades, la galvanoplastia, la pulverización y el tratamiento térmico químico (como el nitruraciónoxigenación, etc.).
La dureza de la capa nitrurada tras la nitruración es de 2 a 4 veces superior a la de la capa superficial sin nitrurar, lo que mejora significativamente la resistencia al desgaste de la aleación, al tiempo que mejora la resistencia a la corrosión de la aleación en medios reductores.
La infiltración de oxígeno puede aumentar la resistencia a la corrosión de la aleación entre 7 y 9 veces, pero la plasticidad y la resistencia a la fatiga de la aleación se perderán en distinta medida.
Características microestructurales de la aleación de titanio
En las aleaciones de titanio, especialmente en las aleaciones de titanio dúplex α+β, puede observarse una gran variedad de estructuras.
Estas estructuras difieren en morfología, tamaño de grano y estructura intragranular, dependiendo principalmente de la composición de la aleación, el proceso de deformación y el proceso de tratamiento térmico.
En general, las aleaciones de titanio tienen dos fases básicas: la fase α y la fase β.
Las propiedades mecánicas de las aleaciones de titanio dependen en gran medida de la proporción, morfología, tamaño y distribución de estas dos fases.
Los tipos estructurales de las aleaciones de titanio pueden dividirse básicamente en cuatro categorías: Estructura widmanstatten (estructura laminar), estructura de tejido de cesta, estructura bimodal y estructura isométrica.
La figura 3 muestra las características morfológicas típicas de los distintos tipos de aleaciones de titanio.
La Tabla 1 proporciona los índices de rendimiento de la aleación de titanio TC4 en cuatro estados estructurales típicos, que muestran que el rendimiento de las diferentes estructuras varía enormemente.
Tabla 1: Influencia de cuatro tejidos típicos en el rendimiento de la aleación TC4
Propiedades mecánicas | Resistencia a la compresión σ /MPa | Alargamiento δ /% | Resistencia al impacto αk /(KJ*m-2) | Resistencia a la fractura KIC /(MPa*m1/2) |
estructura laminar | 1020 | 9.5 | 355.3 | 102 |
estructura de cestería | 1010 | 13.5 | 533 | ___ |
estructura bimodal | 980 | 13 | 434.3 | ___ |
estructura isométrica | 961 | 16.5 | 473.8 | 58.9 |
Figura 3 Organización típica en las aleaciones de titanio
(a) tejido laminar; (b) tejido en cesto; (c) tejido bimodal; (d) tejido isométrico
Ltejido amelar
Se caracteriza por granos de cristal β originales gruesos y fase α de límite de grano completo, formando "haces" de gran tamaño en los granos de cristal β originales, y hay más en los mismos "haces". Las láminas son paralelas entre sí y tienen la misma orientación, como se muestra en la figura 3(a).
Este tipo de microestructura es la estructura que se forma cuando la aleación no se deforma o se deforma después de calentarse en la región de fase beta, y se enfría lentamente desde la región de fase beta. Cuando la aleación tiene esta estructura, su tenacidad a la fractura, durabilidad y resistencia a la fluencia son buenas, pero su plasticidad, resistencia a la fatiga, sensibilidad a la entalla, estabilidad térmica y resistencia a la corrosión bajo tensión térmica son muy pobres. Estas propiedades varían con el tamaño del "haz" α y el grosor del límite de grano α. El "haz" α se hace más pequeño, el límite de grano α se hace más fino y el rendimiento general mejora.
Btejido asketweave
Su característica es que el límite de grano β original se destruye durante el proceso de deformación, y no aparece ningún límite de grano α granular disperso, o sólo una pequeña cantidad, y las rodajas α del grano β original se acortan.
El tamaño del "haz" α es pequeño, y los racimos están dispuestos de forma escalonada, como una cesta tejida, como se muestra en la figura 3(b).
Este tipo de microestructura se forma generalmente cuando la aleación se calienta o comienza a deformarse en la región de fase β o la cantidad de deformación en la región de fase dual (α+β) no es lo suficientemente grande.
La estructura de cesta de malla fina no sólo tiene mejor plasticidad, tenacidad al impacto, tenacidad a la fractura y resistencia a la fatiga de alto ciclo, sino que también tiene mejor resistencia térmica.
Bimodal tejido
Su característica es que los α primarios no conectados se distribuyen en la matriz del tejido de transformación p, pero el contenido total no supera los 50%, como se muestra en la figura 3(c).
Cuando la temperatura de calentamiento de la deformación térmica o del tratamiento térmico de la aleación de titanio es inferior a la temperatura de transformación β, generalmente se puede obtener una estructura de doble estado.
La estructura bimodal se refiere a que la α-fase de la organización tiene dos formas: una es la α-fase primaria equiaxada, y la otra es la α-fase laminar de la organización β-transformada, que corresponde a la α-fase primaria.
También se denomina fase α secundaria o fase α secundaria.
Esta estructura se forma cuando la aleación se encuentra a mayor temperatura y mayor deformación en la zona de doble fase (α+β).
Itejido sométrico
Su característica es que una cierta cantidad de estructura β transformada se distribuye sobre la matriz de la fase α primaria con un contenido uniformemente distribuido de más de 50%, como se muestra en la Figura 3(d).
El procesamiento de deformación y el tratamiento térmico de la aleación de titanio se llevan a cabo todos en la zona de fase dual (α+β) o en la zona de fase α, y cuando la temperatura de calentamiento es mucho más baja que la temperatura de transformación β, se puede obtener generalmente una estructura equiaxial.
En comparación con otras estructuras, esta estructura tiene mejor plasticidad, resistencia a la fatiga y estabilidad térmica, pero su tenacidad a la fractura, durabilidad y resistencia a la fluencia son peores.
Como esta estructura tiene un mejor rendimiento global, es la más utilizada actualmente.
Efecto del proceso de tratamiento térmico en la evolución de la microestructura de una aleación de titanio
En la figura 4 se muestra el proceso de tratamiento térmico de las aleaciones de titanio.
Los principales parámetros que se controlan durante el proceso son la temperatura de la solución sólida, el tiempo de solución sólida, el método de enfriamiento (incluyendo enfriamiento en agua(enfriamiento en aceite, enfriamiento en aire), enfriamiento en horno, temperatura de envejecimiento y tiempo de envejecimiento.
Figura 4 Diagrama del proceso de un tratamiento térmico típico
Efecto de la temperatura de la solución sólida en la microestructura de la aleación TC21
La figura 5 muestra la microestructura de la aleación TC21 a diferentes temperaturas de solución sólida.
Se observa que a medida que aumenta la temperatura de la solución sólida, disminuye la fracción volumétrica de la fase αp.
Cuando la temperatura de la solución sólida es superior a Tβ, la fase αp desaparece.
Durante el tratamiento de disolución a 940°C, debido a la obstrucción de la fase αp equiaxada, los límites de grano de los granos β se doblan y arquean, como muestra la flecha de la figura 5(c).
Cuando se aplica un tratamiento de disolución a una temperatura superior a Tβ (es decir, 1000°C), la fase αp desaparece.
A medida que desaparecen los obstáculos al movimiento de los límites de los granos β, los granos β crecen bruscamente, con un diámetro medio de unos 300 μm, como se muestra en la Figura 5(d).
Se puede observar que la temperatura de disolución tiene un efecto significativo en la microestructura de la aleación TC21.
Cuando la región de fase dual (α+β) se trata con solución sólida, el tamaño, la morfología y la distribución de la fase αp afectarán directamente al tamaño de los granos de cristal β.
La fase αp y el tamaño de grano β de la aleación de titanio desempeñan un papel vital en las propiedades mecánicas de la aleación.
Para evitar el rápido crecimiento de los granos β, la temperatura de disolución sólida de la aleación TC21 debe seleccionarse por debajo de Tβ, de modo que pueda obtenerse un tamaño de grano relativamente adecuado y una estructura de estado dual compuesta por fases primarias y secundarias.
Figura 5 Efecto de la temperatura de disolución en la microestructura de la aleación TC21
(a)850℃/AC; (b)910℃/AC; (c)940℃/AC; (d)1000℃/AC
Efecto del tiempo de solución en la microestructura de la aleación TC21
La figura 6 muestra la microestructura de la aleación TCIZ tras el tratamiento en solución y el enfriamiento al aire durante 4 horas.
De las figuras 6, 5(a) y 5(b) se desprende que la fracción volumétrica y la distribución de la fase ap en la aleación TC21 no cambian significativamente con el aumento del tiempo de disolución.
Es evidente que cuando el tratamiento en solución alcanza un cierto tiempo, la microestructura de la aleación TC21 no es sensible al tiempo de tratamiento en solución, pero la temperatura de tratamiento en solución desempeña un papel decisivo en la estructura de solución sólida de la aleación.
Figura 6 Efecto del tiempo de disolución en la microestructura de la aleación TC21
(a)850℃/4h, AC; (b)910℃/4h, AC
Efecto del método de enfriamiento en la microestructura de la aleación TC21
La figura 7 muestra el efecto de los métodos de enfriamiento sobre la microestructura de la aleación TC21.
Se puede observar que el método de enfriamiento tiene un efecto significativo en la microestructura de la aleación TC21 tras el tratamiento de disolución.
En condiciones WQ y OQ, debido a la mayor velocidad de enfriamiento, sólo se forma β metaestable, pero no se forma βT.
En condiciones de corriente alterna, se forma una cierta cantidad de βT.
El tamaño de la fase αp obtenido en condiciones WQ y OQ es ligeramente inferior al obtenido en condiciones AC.
Esta diferencia se debe a la lenta velocidad de enfriamiento de la CA, que permite que la fase αp de la aleación crezca por completo durante el proceso de enfriamiento (lo que hace que el contenido de fase αp en la aleación aumente y se produzca un crecimiento agregado en condiciones de CA).
En el proceso de enfriamiento más lento, la fase β a alta temperatura también puede transformarse completamente para formar βT.
Figura 7 Efecto del método de enfriamiento en la microestructura de la aleación TC21
(a)910℃/1h, WQ; (b)910℃/1h, OQ; (c)910℃/1h, AC
Efecto de la temperatura de envejecimiento en la estructura de la aleación TC21
La figura 8 muestra una fotografía de la microestructura de la aleación TC21 envejecida a 500°C y 600°C.
De la figura 8 se desprende que la estructura de la aleación tras el envejecimiento se compone de fase αp y fase βT.
A medida que avanza el envejecimiento, la fase α secundaria crece y se fusiona.
La fase α secundaria aumenta gradualmente con el incremento de la temperatura de envejecimiento.
Como se representa en la Figura 8(a), (b), y (c), a 500 °C de envejecimiento, debido a la baja temperatura de envejecimiento, la β subestable obtenida del tratamiento con solución sólida carece de fuerza motriz para la descomposición durante el proceso de envejecimiento, por lo que se forman menos fases secundarias.
Figura 8 Efecto de la temperatura de envejecimiento en la estructura de la aleación TC21
Efecto del tiempo de envejecimiento en la estructura de la aleación TC21
La figura 9 muestra fotos de la microestructura de la aleación TC12 envejecida a 550°C durante diferentes tiempos.
Puede observarse en la figura 9 que, con el aumento de la duración del envejecimiento, aumenta la fracción volumétrica de la fase βT, mientras que el tamaño de la fase αp no cambia significativamente, pero se producen fenómenos de aglomeración y crecimiento.
Las fases α secundarias más grandes, similares a bandas, también parecen fusionarse y crecer.
Figura 9 Efecto del tiempo de envejecimiento en la estructura de la aleación TC21
Efecto del tratamiento térmico en la microestructura de una aleación típica de titanio
Controlando las condiciones del proceso de tratamiento térmico de la aleación TC12 y la aleación Ti60, se obtienen dos tipos principales de microestructura laminar y microestructura bimodal, como se muestra en la Figura 10.
Figura 10 Efecto del tratamiento térmico en la microestructura de una aleación de titanio típica
La figura 10 muestra que la aleación Ti600 puede obtener estructuras LM y BM seleccionando la temperatura de solución sólida por encima y por debajo de Tb (1010°C), respectivamente.
El grosor de la laminilla en el tejido LM es de 2-3 μm, y la fracción de volumen de la fase αp en el tejido BM es de aproximadamente 20%, con un diámetro medio de unos 15 μm.
La figura 10(f) muestra la microestructura de la aleación Ti600 con estructura BM tras 100h de exposición térmica (TE) a 600℃.
Las diferencias entre los tejidos BM y BM+TE no pueden distinguirse únicamente a partir de los tejidos microscópicos mostrados en la Figura 10(e) y (f).
La fase αp rica en Al de las aleaciones de titanio de alta temperatura es propensa a precipitar la fase α2 (Ti3Al) durante el envejecimiento a largo plazo o la exposición térmica.
Por microscopía electrónica de transmisión, se encontró la fase α2 en la fase αp de la aleación Ti600 del tejido BM después de la exposición térmica, como se muestra en la Figura 11.
Figura 11 Morfología TEM y patrón de difracción de electrones de área seleccionada de la fase α2 en la aleación Ti600 tras la exposición térmica.
(a) Topografía TEM; (b) patrón de difracción de electrones de área seleccionada.