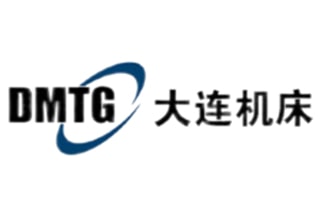
¿Cómo puede un simple polvo transformarse en uno de los materiales más resistentes de la Tierra? Este artículo explora el intrincado proceso de fabricación de las cuchillas, desde la pulvimetalurgia inicial hasta el recubrimiento final. Al final, comprenderá cada paso de la fabricación de estas herramientas esenciales, como la mezcla, el prensado, la sinterización, el rectificado y el tratamiento de los bordes. Sumérjase en el mundo de la fabricación de cuchillas y descubra la precisión y la tecnología que garantizan su resistencia y durabilidad.
Hoy en día, la pulvimetalurgia ha avanzado mucho y se ha acercado a la dureza del material más duro del mundo, el diamante.
El polvo puede parecer un candidato poco probable, pero sorprende saber que uno de los materiales más duros del mundo está hecho de él.
Podemos desvelar el misterio de la producción de cuchillas de carburo cementado, desde el polvo inicial hasta la cuchilla final.
El óxido de wolframio se mezcla con carbono y se procesa en un horno especial para producir carburo de wolframio, que sirve como materia prima principal para todos los carburo de cemento.
El carburo de wolframio es un material excepcionalmente duro y quebradizo que constituye el componente principal del carburo cementado.
El cobalto es un elemento crítico para las propiedades del carburo cementado cuando se combina con el carburo de wolframio.
Cuanto mayor sea la cantidad de cobalto, mayor será la tenacidad del carburo cementado. A la inversa, menos cobalto lo hace más duro y resistente al desgaste.
La relación de peso de los distintos componentes se mide meticulosamente con la máxima precisión.
Un lote de 420 kg de materias primas debe tener un margen de error no superior a 20 gramos.
La mezcla es una operación metalúrgica precisa.
Por último, la mezcla se tritura en un gran molino de bolas hasta obtener un polvo fino y delicado.
La mezcla de polvo debe someterse a un secado por pulverización para conseguir la fluidez adecuada.
Tras la molienda, el tamaño de las partículas del polvo alcanza entre 0,5 y 2,0 micrómetros.
Para empezar, la forma y el tamaño básicos de la hoja se obtienen mediante el punzonado con un troquel y una prensa altamente automatizada y controlada por CNC.
Aunque la cuchilla puede parecer similar a una cuchilla de carburo cementado real después del prensado, su dureza sigue estando lejos de la norma exigida.
Posteriormente, un robot transfiere la hoja prensada a un disco de material resistente al calor.
Para endurecer la hoja, se somete a un tratamiento térmico a 1500℃ durante 15 horas.
Durante el proceso de sinterización, las partículas de cobalto y carburo de wolframio se funden y se unen entre sí. Hay dos pasos cruciales en el proceso del horno de sinterización. En primer lugar, la hoja sufre una contracción evidente, y sólo una contracción precisa puede garantizar la obtención de la tolerancia correcta. En segundo lugar, la mezcla de polvo se transforma en nuevo material con propiedades metálicas, lo que se conoce como carburo cementado.
Aunque la cuchilla ha alcanzado la dureza esperada, aún necesita más procesamiento antes de poder ser entregada. Antes de pasar a la siguiente fase de producción, comprobamos cuidadosamente el tamaño de la cuchilla con una máquina de medición de coordenadas.
Sólo el rectificado con diamante puede garantizar que las plaquitas de metal duro tengan una forma precisa.
La hoja se rectifica según su ángulo geométrico.
La mayoría de las amoladoras incorporan controles de medición para comprobar y medir las cuchillas en distintas fases.
Para conseguir la máxima resistencia al desgaste necesaria para el mecanizado, el filo de corte se trata para obtener la forma correcta.
Estas cuchillas pueden cepillarse con un cepillo especial que tiene un revestimiento de carburo de silicio.
Independientemente del método de tratamiento utilizado, es esencial comprobar el resultado final.
Aproximadamente entre 90% y 95% de todas las cuchillas tienen algún tipo de revestimiento.
Es crucial asegurarse de que no haya partículas extrañas en la superficie de la cuchilla para evitar que se adhieran al revestimiento y afecten al rendimiento de la herramienta.
Existen dos tipos de métodos de revestimiento para cuchillas: Deposición química en fase vapor (CVD) y Deposición física en fase vapor (PVD). La selección del método de revestimiento adecuado depende del material y el procesamiento de la cuchilla.
El grosor del revestimiento viene determinado por la aplicación de la cuchilla, y la calidad del revestimiento es esencial para la durabilidad y la vida útil de la cuchilla.
Los conocimientos técnicos consisten en aplicar varios revestimientos finos, tales como titanio carburo, óxido de aluminio y nitruro de titanio, en la superficie del carburo cementado. Estos recubrimientos pueden mejorar significativamente la vida útil y la durabilidad de la cuchilla.
Si se utiliza el método CVD, la cuchilla se coloca en un horno y se expone a una mezcla de gases de cloruro y óxido, junto con metano e hidrógeno. Cuando la temperatura alcanza los 1000℃, estos gases reaccionan entre sí y depositan un revestimiento homogéneo de sólo unas milésimas de milímetro de grosor sobre la superficie de la cuchilla de carburo cementado.
Algunas cuchillas recubiertas tienen una superficie dorada y son más valiosas. Su durabilidad es cinco veces superior a la de las hojas sin recubrimiento.
PVD es un método utilizado para rociar la hoja a 400℃.
Después de que la cuchilla pase la inspección automática, procederemos a marcar el material de la cuchilla con un láser y, a continuación, la embalaremos.
Además, la caja de la cuchilla llevará una etiqueta con información sobre el producto, un número de serie y la fecha. Esto sirve como promesa a nuestros usuarios de que pueden esperar una calidad y un servicio excelentes.
Una vez embaladas, las cuchillas pueden entregarse a los clientes.