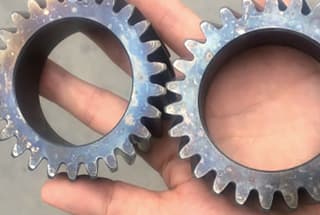
¿Se ha preguntado alguna vez por qué sus piezas templadas carecen de la dureza esperada? Este problema común en los procesos de tratamiento térmico puede afectar gravemente al rendimiento de sus componentes. Este artículo profundiza en los factores clave que provocan deficiencias de dureza durante el temple, explorando la selección de materias primas, los procesos de calentamiento y los métodos de enfriamiento. Al final, obtendrá información práctica para identificar y resolver estos problemas, garantizando que sus piezas templadas alcancen una dureza y fiabilidad óptimas.
En el proceso de producción, no es infrecuente que haya una dureza insuficiente después del temple, que es un defecto común en el tratamiento térmico y el temple.
Hay dos manifestaciones de este defecto: una dureza baja en toda la pieza y puntos insuficientes o blandos en zonas localizadas.
Cuando se produce una dureza insuficiente, es necesario realizar un ensayo de dureza o un análisis metalográfico para determinar la causa y, a continuación, investigar los posibles factores contribuyentes, como las materias primas, el proceso de calentamiento, el medio de enfriamiento, el método de enfriamiento y la temperatura de revenido, con el fin de encontrar una solución.
Es importante elegir el material adecuado para las piezas a fin de evitar una dureza insuficiente o puntos blandos. Acero al carbono medio o acero con alto contenido en carbono en lugar de acero con bajo contenido en carbono, y acero aleado para herramientas en lugar de acero normal con alto contenido en carbono.
En el ejemplo 1, el uso de acero #45 en lugar de acero #25 para el engranaje da como resultado una dureza de temple de 60HRC en comparación con la dureza de 380hbs.
En el ejemplo 2, se recomienda utilizar 9mn2v para el molde en lugar de acero T8, ya que el proceso de enfriamiento para 9mn2v se siguió erróneamente con enfriamiento en aceite, lo que dio lugar a una dureza de sólo 50HRC.
Ambos casos ilustran la insuficiente dureza global que puede detectarse mediante un ensayo de dureza o metalográfico.
Para evitar estos problemas, se recomienda:
La presencia de segregación o agregación de carburos, como la agregación de ferrita, grafito, o una estructura Widmanstatten severa en la microestructura puede dar lugar a deficiencias de dureza o puntos blandos.
Para solucionar este problema, se recomienda homogeneizar la microestructura mediante un tratamiento repetido de forja o precalentamiento, como la normalización o la homogeneización. recocido antes del enfriamiento.
La dureza del acero hipoeutectoide puede verse afectada cuando la temperatura de calentamiento cae entre AC3 y AC1, ya que la ferrita no se disuelve completamente en austenitaEsto da lugar a una mezcla de ferrita y martensita en lugar de una martensita uniforme tras el enfriamiento. Esto puede observarse mediante análisis metalográficos.
Del mismo modo, un calentamiento o un tiempo de mantenimiento insuficientes pueden impedir que la perlita se transforme en austenita en el acero con alto contenido en carbono, especialmente en el acero de alta aleación, lo que afecta a la dureza de la pieza.
En la producción, estos problemas pueden producirse a menudo debido a desviaciones en las lecturas de temperatura o a una temperatura desigual del horno, así como a estimaciones incorrectas del grosor del material.
Para evitar estos problemas, se recomienda:
En los aceros para herramientas como el T8, a una temperatura de enfriamiento de 780e, se forman austenita y carburo (Fe3C). La cantidad de carbono disuelto en la austenita es ligeramente superior a 0,77%. Al enfriarse, la austenita se transforma en martensita.
Sin embargo, si la temperatura de calentamiento es demasiado alta o el tiempo de mantenimiento es demasiado largo, una gran cantidad de carbono del carburo se disolverá en la austenita, lo que aumentará su estabilidad y hará que la austenita se transforme en martensita cuando la temperatura empiece a descender. Esto da lugar a una gran cantidad de austenita retenida presente en la pieza después del temple, dando lugar a una microestructura de m + AC.
Austenita retenida tiene propiedades austeníticas y baja dureza, lo que provoca una disminución de la dureza tras el temple. El contenido de austenita retenida puede verse influido tanto por la temperatura de calentamiento como por la de revenido.
Para evitar este problema, se recomienda:
Tras el temple, la superficie del acero #45 presenta ferrita y martensita de bajo contenido en carbono mediante análisis metalográfico. Sin embargo, tras eliminar la descarburización capa, la dureza cumple los requisitos.
Este problema suele deberse al calentamiento en un horno de caja sin la protección adecuada o con una protección deficiente, o al calentamiento en un baño de sales con una desoxidación deficiente, lo que provoca la reacción de los átomos de oxígeno y carbono de la pieza para formar CO, reduciendo el contenido en carbono en la superficie de la pieza y provocando una dureza superficial insuficiente.
Para evitar este problema, se recomienda:
La dureza de las piezas templadas por agua o baño salino y enfriadas con aceite suele ser baja debido a la insuficiente capacidad de enfriamiento y a la lenta velocidad de enfriamiento, lo que provoca la transformación de austenita en perlita (AYP) en lugar de martensita (m), sobre todo en el núcleo de la pieza.
Por ejemplo, la dureza de un martillo de mano T10 templado en aceite es sólo de unos 45HRC, según se desprende del análisis metalográfico, que muestra la presencia de troostita en lugar de martensita.
Para solucionar este problema, es importante seleccionar el medio refrigerante en función del material, la forma y el tamaño de la pieza.
Al enfriar continuamente un gran número de piezas mediante enfriamiento en agua, la falta de un sistema de refrigeración por circulación puede hacer que aumente la temperatura del agua y disminuya la capacidad de refrigeración, lo que puede provocar fallos en el endurecimiento.
Cuando se utiliza la refrigeración por aceite, la baja temperatura y la escasa fluidez del aceite al principio del proceso pueden provocar una capacidad de refrigeración insuficiente y fallos en el endurecimiento.
Para evitar estos problemas, se recomienda:
Un exceso de impurezas en el baño alcalino (sal) o una cantidad insuficiente de agua pueden provocar la aparición de puntos blandos durante el enfriamiento.
Para evitar este problema, es importante cambiar regularmente el medio de enfriamiento y controlar adecuadamente el contenido de agua en el baño alcalino (sal).
Cuando se fabrican piezas de conmutación con secciones transversales complejas o grandes a partir de acero al carbono, se recurre al temple en agua y al enfriamiento en aceite para evitar deformaciones y grietas. Sin embargo, debido a la elevada temperatura de la pieza y, sobre todo, a la lenta velocidad de enfriamiento del núcleo, no se puede obtener una martensita uniforme y completa.
Para resolver este problema, se recomienda:
En conclusión, el fenómeno del enfriamiento insuficiente se produce a menudo, y el operador debe determinar las razones y encontrar soluciones basadas en análisis específicos y diferentes situaciones.