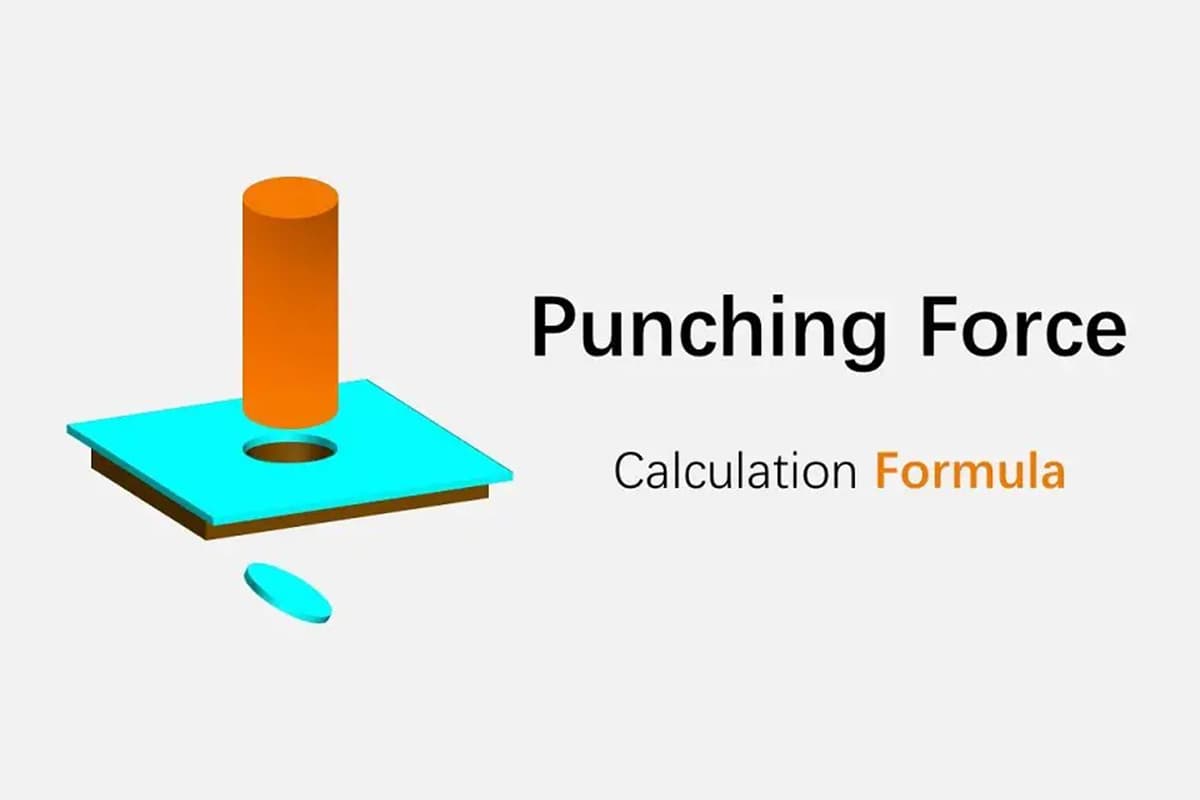
El procesamiento por láser consiste en utilizar un rayo láser para alterar la superficie de un material mediante efectos térmicos, lo que incluye la soldadura por láser, el corte por láser, la modificación de superficies, el marcado por láser, el taladrado por láser y el microprocesado. El rayo láser puede utilizarse para realizar diversas tareas, como punzonado, corte, trazado, soldadura y tratamiento térmico, en diferentes materiales. El láser es [...]
El procesamiento por láser consiste en utilizar un rayo láser para alterar la superficie de un material mediante efectos térmicos, lo que incluye la soldadura por láser, el corte por láser, la modificación de superficies, el marcado por láser, el taladrado por láser y el microprocesado.
El rayo láser puede utilizarse para realizar diversas tareas, como punzonado, corte, trazado, soldadura y tratamiento térmico, en distintos materiales.
El láser es capaz de procesar cualquier material, y desempeña un papel indispensable en el procesamiento y la fabricación de precisión y especializada, sobre todo en circunstancias especiales y con materiales especiales.
El tratamiento por láser consiste en utilizar un rayo láser para alterar la superficie de una pieza mediante irradiación de alta energía. El resultado es la eliminación de material, la fusión o la modificación de las propiedades de la superficie. Se trata de un proceso sin contacto, es decir, la herramienta no genera resistencia al rectificar la superficie de la pieza, lo que lo convierte en un método rápido y eficaz.
Además, la energía y la velocidad del rayo láser pueden ajustarse, lo que permite aplicaciones versátiles a varios niveles y rangos.
Las características únicas del procesamiento por láser determinan sus ventajas en el campo del procesamiento:
(1) Como se trata de un procesamiento sin contacto, y la energía del rayo láser de alta energía y su velocidad de movimiento son ajustables, se puede utilizar para una variedad de propósitos de procesamiento.
(2) Puede procesar una gran variedad de materiales metálicos y no metálicos.materiales metálicosespecialmente los de gran dureza, fragilidad y punto de fusión.
(3) El procesamiento por láser no causa desgaste en la "herramienta" y no genera fuerzas de corte en la pieza.
(4) La densidad de energía del rayo láser es muy alta durante el procesamiento, lo que lo hace rápido y muy localizado, con un impacto mínimo en las zonas no expuestas a la irradiación láser.
De este modo, la zona afectada por el calor es pequeña, la deformación térmica de la pieza es mínima y se reduce la necesidad de tratamiento posterior.
(5) Se puede utilizar para el procesamiento dentro de un contenedor sellado a través de un medio transparente a la pieza de trabajo.
(6) El rayo láser es fácil de guiar y enfocar, lo que permite transformar la dirección y facilita el trabajo Sistemas CNC para el procesamiento de piezas complejas.
(7) El procesamiento por láser es muy eficaz, produce una calidad fiable y tiene un buen rendimiento económico.
Por ejemplo
(1) La General Electric Company de EE.UU. utiliza el procesamiento por láser de losa para cortar las ranuras perfiladas de los motores de los aviones, completando la tarea con alta calidad en menos de 4 horas, mientras que el método original de procesamiento por electroerosión tardaba más de 9 horas. Esto por sí solo ahorra $50.000 en el coste de cada motor.
(2) La eficacia de acero de corte con láser puede aumentar entre 8 y 20 veces, lo que supone una reducción de 15-30% en los costes de material. Esto se traduce en un importante ahorro de costes, al tiempo que proporciona un mecanizado de alta precisión y garantiza una calidad de producto estable y fiable.
Aunque el procesamiento por láser tiene muchas ventajas, sus limitaciones también son evidentes.
El procesamiento por láser consiste en utilizar un rayo láser para realizar diversos procesos, como punzonado, corte, trazado, soldadura y tratamiento térmico.
El procesamiento por láser tiene muchas ventajas:
① Alta densidad de potencia láser permite el rápido aumento de la temperatura y la fusión o vaporización de la pieza, incluso en el caso de materiales con altos puntos de fusión, gran dureza y fragilidad (como la cerámica y el diamante);
② El cabezal láser no entra en contacto directo con la pieza de trabajo, lo que elimina el problema del desgaste durante el procesamiento;
③ La pieza de trabajo está libre de fuerzas y no se contamina fácilmente;
④ La pieza puede procesarse en movimiento o dentro de una carcasa de vidrio sellada;
⑤ El ángulo de divergencia del haz láser puede ser inferior a la millonésima parte de un arco, con un diámetro de punto tan pequeño como unas pocas micras y un tiempo de acción de nanosegundos a picosegundos. Mientras tanto, la potencia de salida continua del láser de alta potencia puede alcanzar de kilovatios a diez kilovatios, lo que hace que el láser sea adecuado tanto para el microprocesamiento de precisión como para el procesamiento de materiales a gran escala;
⑥ El rayo láser es fácil de controlar y puede combinarse con maquinaria de precisión, tecnología de medición de precisión y ordenadores electrónicos para conseguir un alto grado de automatización y precisión en el procesamiento;
⑦ Los robots pueden utilizarse para el procesamiento por láser en entornos hostiles o en lugares donde es difícil que trabajen seres humanos.
El láser pulsado se utiliza para perforacióncon una anchura de impulso de 0,1 a 1 milisegundo. Es especialmente adecuado para crear orificios y agujeros perfilados con una apertura de aproximadamente 0,005 a 1 mm. El taladrado por láser se ha adoptado ampliamente en la producción de piezas como relojes, cojinetes de piedras preciosas, matrices de trefilado de diamantes y hileras de fibras químicas.
Las industrias de construcción naval y fabricación de automóviles suelen utilizar láseres de CO2 continuos de cientos de kilovatios a millones de vatios para cortar piezas de gran tamaño, lo que garantiza una forma precisa del espacio curvado al tiempo que proporciona una mayor eficacia de procesamiento.
Los láseres de estado sólido de potencia media y pequeña o los láseres de CO2 se utilizan habitualmente para cortar piezas pequeñas. En microelectrónica, los láseres se utilizan habitualmente para cortar silicio o hacer rendijas, lo que resulta rápido y tiene una pequeña zona afectada por el calor.
El láser puede utilizarse para rotular o marcar piezas en la cadena de montaje sin afectar a la velocidad de ésta, y los caracteres grabados pueden mantenerse de forma permanente.
El uso de láseres de media y baja potencia se aplica para eliminar partes de los componentes electrónicos del material con el fin de alterar parámetros eléctricos como la resistencia, la capacitancia y la frecuencia de resonancia.
El ajuste fino por láser es muy preciso y rápido, y resulta adecuado para la producción a gran escala.
Se pueden utilizar principios similares para reparar máscaras defectuosas de circuitos integrados, mejorar el rendimiento de la memoria de circuitos integrados y realizar ajustes precisos del equilibrio dinámico en giroscopios.
Soldadura láser se caracteriza por su alta resistencia, mínima deformación térmica, sellado eficaz, tamaño y naturaleza de soldadura consistentes y capacidad para soldar materiales con puntos de fusión elevados (como los cerámicos) y aquellos propensos a la oxidación.
La soldadura láser es especialmente útil para los marcapasos, que se sellan eficazmente y tienen una larga vida útil, además de un tamaño reducido.
Con la irradiación láser del material, se puede seleccionar la longitud de onda adecuada, el control del tiempo de irradiación y la densidad de potencia para provocar la fusión y recristalización de la superficie del material, logrando el objetivo de enfriamiento o recocido.
Calor láser tiene la ventaja de poder controlar con precisión la profundidad del tratamiento térmico y seleccionar la zona específica a tratar.
La deformación de la pieza de trabajo es mínima, y puede manipular con eficacia formas complejas e intrincadas, así como procesar orificios ciegos y profundos en paredes interiores.
Por ejemplo, el tratamiento térmico por láser puede prolongar la vida útil de un pistón de cilindro y restaurar los daños causados por el bombardeo de iones en materiales de silicio.
La tecnología Laser Surface Strengthening utiliza un rayo láser de alta densidad energética para calentar y autoenfriar rápidamente la pieza de trabajo.
En el refuerzo láser de superficies metálicas, cuando la densidad de energía del haz láser es baja, puede utilizarse para la transformación de superficies metálicas. Cuando la densidad del haz es alta, la superficie de la pieza actúa de forma similar a un crisol móvil, lo que permite una serie de procesos metalúrgicos, como la refundición superficial, la carbonatación superficial, la aleación superficial y el revestimiento superficial.
Estas funciones tienen el potencial de aportar importantes beneficios económicos a la industria manufacturera a través de la tecnología de sustitución de materiales.
En la modificación del material de las herramientas, el tratamiento por fusión es la principal aplicación. Consiste en fundir el material metálico superficie bajo la irradiación de un rayo láser, solidificándose después rápidamente para formar una nueva capa superficial.
Los cambios en la superficie del material pueden clasificarse en varios tipos, como aleación, disolución, refinado por refundición, glaseado y compuesto superficial.
La fusión por láser consiste en utilizar parámetros láser para fundir y condensar rápidamente la superficie del material, lo que da lugar a una organización más refinada y homogénea con propiedades superficiales mejoradas. Se trata de una tecnología de modificación de superficies.
Entre las ventajas de la fusión superficial por láser se incluyen:
El haz puede dirigirse a través de una trayectoria óptica, lo que permite procesar piezas con posiciones especiales y formas complejas.
Combinando las ventajas de la tecnología con las limitaciones de las técnicas más utilizadas, la aplicación de la tecnología láser para el refuerzo superficial de los materiales de las herramientas mejora la resistencia al desgaste y la vida útil de la herramienta, sobre todo en el caso de las herramientas de corte de cerámica y carburo de alta dureza y resistencia al calor.
Esto mejora la eficacia y la precisión del procesado y permite procesar materiales como el acero templado en condiciones difíciles.
A pesar de su gran dureza y resistencia al calor, la cerámica y el carburo herramientas de corte tienen una aplicación limitada debido a su resistencia relativamente baja y a su escasa tenacidad. La aplicación del láser endurecimiento superficial a estos materiales es, por tanto, objeto de importantes investigaciones y tiene una amplia gama de aplicaciones potenciales.
Seleccionando la longitud de onda láser adecuada y utilizando diversas técnicas de optimización y aproximación al límite de difracción del sistema de enfoque, se puede obtener un haz de luz estable y de alta calidad con un punto focal de tamaño micro.
Sus características de "cuchilla" afilada y precisa se utilizan para grabar micromarcas de alta densidad y escribir directamente información de alta densidad.
También puede aprovechar su efecto de "fuerza" de trampa óptica para manipular diminutos objetos transparentes, por ejemplo mediante el grabado de rejillas de alta precisión.
Con la ayuda de software CAD/CAM para simular y controlar patrones o texto, se puede conseguir un marcado de alta fidelidad.
Además, su "fuerza vinculante" de trampa óptica puede utilizarse para la manipulación de células biológicas, lo que se conoce como pinzas biológicas de luz.
El proceso de mecanizado fino
La mayoría de los cortes finos en la superficie convexa (exterior) se realizan con herramientas o cortadores de diamante monocristalino. El radio de la punta es de aproximadamente 100 μm, y el disco de diamante tiene una superficie de corte cónica de 45° cuando gira.
El tamaño mínimo mecanizable de la superficie cóncava (interior) está limitado por el tamaño de la herramienta. Por ejemplo, una broca espiral puede utilizarse para mecanizar un orificio de 50 μm, pero para orificios más pequeños debe utilizarse una broca plana, ya que no se dispone de productos de broca helicoidal.
Un reto clave en la microfabricación es garantizar que la postura de instalación de la herramienta y su alineación coaxial con el eje del husillo sean coherentes con el sistema de coordenadas. De lo contrario, puede resultar difícil conseguir una pequeña cantidad de corte. Para solucionar este problema, se puede utilizar la misma máquina herramienta tanto para la producción de herramientas como para el microprocesado, evitando así sujeción errores causados por el uso de diferentes condiciones de trabajo.
Se puede utilizar una rectificadora de descarga de alambre en la máquina herramienta para producir una ranura de 50 μm de ancho.
Tecnología de procesamiento eléctrico fino
El mecanizado de microejes y barras de sección perfilada puede lograrse mediante el rectificado por descarga de hilo (WEDG). Su exclusivo circuito de descarga permite un mecanizado de sólo una centésima parte del EDM ordinario. Para conseguir una superficie más lisa, puede utilizarse WECG tras el mecanizado WEDG, que elimina una fina capa superficial utilizando agua desionizada a baja corriente.
Para este proceso pueden utilizarse máquinas de micro-EDM, como la MG-ED71 de la japonesa Matsushita Electric Industrial Co. Estas máquinas tienen una resolución de control de posicionamiento de 0,1 μm y la abertura de procesamiento más pequeña es de 5 μm, lo que da como resultado una rugosidad superficial de 0,1 μm.
Por ejemplo, un acero inoxidable de 9 dientes engranaje de acero con un diámetro de 300 μm y un grosor de 100 μm puede mecanizarse. El contorno rugoso se perfora primero con un electrodo de φ24 μm y, a continuación, el contorno se explora con un electrodo de φ31 mm de acuerdo con el perfil del diente, lo que da como resultado una precisión de ± 3 μm.
Esta tecnología también puede utilizarse para procesar un eje escalonado en miniatura con un diámetro mínimo de 30 μm y una sección de chavetero procesada de 10 μm x 10 μm. Los electrodos para el mecanizado de piezas pequeñas deben fabricarse en la misma máquina herramienta; de lo contrario, puede resultar difícil procesar orificios de menos de 100 μm de diámetro debido a errores de conexión y montaje de los electrodos.
Por ejemplo, para procesar microagujeros de 5 a 10 μm pueden utilizarse electrodos de micro-EDM o herramientas de procesamiento por ultrasonidos. En comparación con el micromecanizado y el mecanizado fino, las tasas de arranque de material son bajas, pero el tamaño de procesamiento puede ser menor, y la relación de diámetro del orificio puede llegar a ser de 5 a 10. Esto lo hace especialmente superior para el procesamiento de cavidades cóncavas finas y complejas.
Con el desarrollo de la industria láser y los cambios en las demandas de la industria transformadora, los equipos láser de media y alta potencia se han convertido en el centro de atención del mercado. En particular, la aparición de 20 kW, o incluso de mayor potencia, corte por láser de fibra han impulsado la maduración de la tecnología láser, ampliando constantemente los límites del grosor de corte.
De cara al futuro, con la modernización de los equipos de corte por láser, las máquinas de corte por láser de alta potencia y alta velocidad sustituirán a los equipos de mecanizado tradicionales debido a sus extraordinarias ventajas de eficiencia y precisión, mejorando significativamente la eficiencia y la calidad del procesamiento industrial.
En la era de la economía digital, el avance de la tecnología digital ha mejorado enormemente la eficiencia de la producción y la innovación. La integración efectiva de la tecnología láser con la tecnología de control numérico dará a los equipos de corte por láser la capacidad de analizar, juzgar, inferir y tomar decisiones sobre el proceso de corte, realizando así la automatización y la inteligentización de todas las partes del equipo de fabricación.
Al mismo tiempo, el aumento de los costes laborales en la industria del láser y la actualización e iteración de la tecnología industrial también impulsan la necesidad de que los equipos de corte por láser evolucionen hacia mayores niveles de automatización e inteligencia.
Como podemos prever, con el rápido avance de las estrategias de fabricación inteligente, la digitalización y la inteligentización en el campo del corte por láser se convertirán en una tendencia inevitable. Los equipos de corte por láser multifuncionales altamente inteligentes seguirán apareciendo, mejorando en gran medida la eficiencia del procesamiento industrial y logrando una gestión eficiente de la producción.
En la era de la fabricación inteligente, los escenarios de procesamiento de usuarios posteriores son cada vez más diversos y complejos, lo que aumenta la demanda de equipos de procesamiento láser personalizados. Esto requiere empresas de corte por láser ser más flexibles en las aplicaciones de sus productos para adaptarse a diferentes escenarios de procesamiento y satisfacer las diversas necesidades de los clientes.
Por lo tanto, el uso del diseño modular para mejorar la integración, adaptabilidad y funcionalidad de los equipos, y para lograr una producción flexible orientada al consumidor, se convertirá en una importante dirección de desarrollo para la futura industria de equipos de corte por láser.
Como fundador de MachineMFG, he dedicado más de una década de mi carrera a la industria metalúrgica. Mi amplia experiencia me ha permitido convertirme en un experto en los campos de la fabricación de chapa metálica, mecanizado, ingeniería mecánica y máquinas herramienta para metales. Estoy constantemente pensando, leyendo y escribiendo sobre estos temas, esforzándome constantemente por mantenerme a la vanguardia de mi campo. Deje que mis conocimientos y experiencia sean un activo para su empresa.