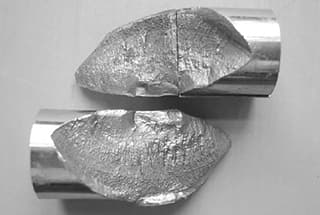
¿Por qué son tan importantes las pequeñas impurezas del acero? Estas inclusiones no metálicas, aunque diminutas, influyen profundamente en las propiedades y la utilidad del acero. Este artículo profundiza en sus orígenes, clasificaciones y avances en su control a lo largo de los años. Desde la mejora de la calidad del acero hasta la superación de los retos de producción, comprender estas inclusiones es clave. Siga leyendo para descubrir los mecanismos de su formación, el impacto de las modernas técnicas de fundición y el futuro del refinado del acero.
Resumen:
Las inclusiones no metálicas desempeñan un papel crucial en la determinación de muchas propiedades del acero y tienen un impacto significativo en el procesamiento y la utilización de los productos de acero.
Este artículo ofrece una visión general de los últimos avances en el origen y la clasificación de las inclusiones no metálicas y resume los trabajos de investigación realizados en las últimas décadas.
Destaca las condiciones dinámicas de formación de inclusiones y el efecto de las condiciones actuales de fundición en la composición, cantidad y distribución del tamaño de las inclusiones.
El estudio de la desnaturalización por inclusión se centra en tipos de acero como el alambre de acero radial, acero para muelles y acero para rodamientos para conseguir el tamaño y la forma deseados de las inclusiones.
Además, deben tomarse medidas para evitar la obstrucción de la boquilla de colada continua por el flujo floculante.
Gracias a los avances de la microscopía microelectrónica, ahora se conocen mejor las características de distribución de las inclusiones. También se ha abordado el apasionante campo de la "metalurgia de óxidos" en el contexto de la ingeniería de inclusiones.
Por último, el artículo aborda la mejora de las características de inclusión y los retos de realizar un análisis cuantitativo.
En las últimas décadas se ha avanzado notablemente en el control de la inclusiones en el aceroLa mejora de la calidad del acero se debe, en gran medida, a un conocimiento más profundo de la interacción entre la termodinámica, la composición de la escoria del acero fundido y el proceso de fabricación del acero. Esto permite optimizar las inclusiones y los procesos para mejorar las propiedades del acero.
Sin embargo, aún quedan algunos retos importantes por resolver, y el proceso de control y optimización de la inclusión debe mejorarse continuamente.
No fue hasta hace cincuenta años cuando se empezó a prestar atención al estudio del no metálico (NMI) en el acero. En aquella época, se creía que estas inclusiones eran el resultado de la corrosión de materiales refractarios y de la presencia de diversos fundentes de molde y escorias superiores.
Sin embargo, a pesar de su importancia, el estudio de las inclusiones no gozaba del reconocimiento que tiene hoy en día. Esto se debía a que los metalúrgicos físicos se centraban generalmente en el estudio de las fases metálicas, más que en el de las inclusiones. no metálico fases como inclusiones en el acero.
A medida que aumentaba la demanda de aceros de alto rendimiento con condiciones de servicio severas, se hizo más evidente la correlación entre el tipo, el tamaño y la distribución de las MNI y el rendimiento del acero. Esto condujo a un creciente interés por estudiar el origen, las características y el comportamiento de las inclusiones en la fundición y el procesamiento de los productos de acero.
Desde la década de 1980, se han realizado avances significativos en el control y el análisis cuantitativo de las NMI, y se ha investigado ampliamente el impacto de estas inclusiones en las propiedades del acero. La ingeniería de control de las inclusiones se ha convertido en un aspecto crucial de la fundición, con el objetivo de conseguir las características de inclusión deseadas mediante un diseño adecuado del proceso y la producción de acero.
En este artículo, abordamos el origen y el control de los NMI, el comportamiento de las inclusiones durante el mecanizado, el análisis cuantitativo y las características de distribución de las inclusiones, así como los últimos avances en ingeniería de control de inclusiones. Sin embargo, no profundizamos en la influencia de las inclusiones en las propiedades del acero, ya que se trata de un campo extenso y en rápido crecimiento.
Para los interesados en profundizar en este tema, los libros clásicos de Kiessling y las conferencias y ponencias de la Organización Internacional del Acero Limpio, celebradas cada 3-5 años y patrocinadas por la Asociación Minera y Metalúrgica de Hungría, son valiosas fuentes de conocimiento.
Con los continuos avances de la tecnología siderúrgica moderna, se observa que se emplean reacciones de oxidación y métodos de refinado para eliminar los elementos perjudiciales del acero.
Estas impurezas, como el azufre del carbón y el coque, pueden penetrar en el hierro y el acero líquidos, pero su solubilidad en el acero en solución sólida es bastante limitada.
Durante la solidificación, el acero fundido pasa del frente de cristalización al acero líquido, formando finalmente compuestos de bajo punto de fusión como el "FeO" y el "FeS" o eutécticos que contienen ambos compuestos. Como resultado, este acero no es apto para procesos de trabajo en caliente como el laminado y la forja.
Los óxidos, sulfuros y elementos de aleación (como el Mn) en el acero presentan una relación compleja. Sin embargo, para producir acero de alta calidad, es necesario reducir el contenido de oxígeno y azufre disuelto en el acero fundido.
Elementos como Mn, Al, Si pueden utilizarse como elementos de aleación en el acero, ya que poseen una gran afinidad con el oxígeno y pueden desoxidarse en el acero fundido. Estos elementos desoxidados se convierten en inclusiones no metálicas de óxido.
Por otra parte, el acero contiene azufre, y la solubilidad del Ca y el Mg en el acero es mínima. Su afinidad con las tierras raras y el S es lo suficientemente alta como para formar inclusiones de sulfuro no metálicas con un punto de fusión bajo.
Como resultado, la mayor parte del azufre del acero se elimina mediante el refinado y pasa a la escoria, mientras que el azufre restante precipita en inclusiones de sulfuro durante la solidificación.
Estas inclusiones no metálicas pueden clasificarse en dos categorías en función de su tipo: la composición química de las inclusiones (como inclusiones de óxido y sulfuro) y la fase de formación de la inclusión.
La solidificación marca el punto límite en la etapa de formación de las inclusiones. Las inclusiones formadas antes de la solidificación se conocen como inclusiones primarias, mientras que las formadas durante y después de la solidificación se denominan inclusiones secundarias.
Además de estas clasificaciones, otras utilizadas habitualmente también pueden resultar confusas, como la procedencia de las inclusiones. Las inclusiones formadas durante el proceso de fabricación del acero (como las inclusiones de óxido y sulfuro) se clasifican como inclusiones "endógenas", mientras que las procedentes de fuentes externas (como las virutas refractarias y el polvo de molde) se denominan inclusiones "exógenas".
En general, sólo hay unas pocas inclusiones exógenas de partículas grandes que permanecen independientes del acero fundido durante un largo período de tiempo y no reaccionan con él. Esto ha cambiado con respecto al pasado, cuando se creía que dichas inclusiones de partículas grandes procedían del refractario y del molde de fundición. Sin embargo, en el acero moderno, estas inclusiones de partículas grandes se han reducido considerablemente.
Algunos estudiantes pueden creer erróneamente que las inclusiones exógenas son las inclusiones no metálicas más importantes, pero esto no significa que la interacción entre el acero fundido y el refractario sea insignificante. La presencia de estas inclusiones en el acero indica que el acero fundido y el refractario influyen. Si se amplía la definición de inclusiones exógenas para incluir la oxidación secundaria y la participación del polvo de molde, se obtiene una definición más adecuada de inclusiones exógenas.
Sin embargo, sigue habiendo debate sobre la clasificación de estas inclusiones, ya que pueden cambiar durante el proceso de fundición y no siempre está claro de qué proceso se trata.
Por último, un método habitual para clasificar las inclusiones no metálicas se basa en su tamaño, dividiéndolas en macroinclusiones y microinclusiones. A menudo se utiliza la clasificación propuesta por Kiessling, en la que las inclusiones que causan daños instantáneos a los productos de acero durante su procesamiento o uso se consideran macroinclusiones.
Hay que tener en cuenta que la clasificación del tamaño de las inclusiones es subjetiva, y dividirlas al azar en macro y micro en función del tamaño es difícil de definir.
Fig. 1 Fractura de alambre radial de neumático durante el trefilado debido a la existencia de fase dura de partículas grandes.
La inclusión se indica con una flecha, y la foto se tomó utilizando la técnica de retrodispersión del microscopio electrónico de barrido.
La elevada temperatura durante la fabricación del acero hace que la reacción de formación de inclusiones se aproxime al estado de equilibrio. En consecuencia, la termodinámica se ha convertido en una herramienta crucial para comprender las inclusiones.
Durante mucho tiempo, la base termodinámica de la formación de inclusiones ha sido objeto de investigación. Sin embargo, los datos termodinámicos de formación relacionados con las inclusiones en el óxido de aluminio siguen siendo incoherentes y contradictorios, por lo que es un área que merece un estudio más profundo.
El aluminio se utiliza habitualmente como desoxidante en la fabricación de acero, y el cálculo termodinámico de las inclusiones generadas durante el proceso no plantea problemas. Sin embargo, el proceso de fundición de materiales siderúrgicos de nueva generación con alto contenido en aluminio y manganeso introduce incertidumbre.
La situación se complica cuando la disolución de Mg y Ca en el acero es extremadamente limitada. A pesar de ello, se siguen estudiando ampliamente los datos termodinámicos relacionados de estos elementos en el proceso de fabricación del acero.
En las últimas décadas, el cálculo termodinámico se ha aplicado para resolver problemas complejos en la producción y fundición de hierro y acero. Sin embargo, los métodos de cálculo convencionales siguen teniendo dificultades para abordar estas cuestiones.
Numerosas literaturas han discutido la aplicación del cálculo termodinámico en diversos aspectos de la producción y fundición de hierro y acero, así como los problemas de inclusión relacionados.
Clasificar las inclusiones en primarias y secundarias puede ser útil para analizar su formación y eliminación. En principio, es posible eliminar las inclusiones primarias en el acero.
Sin embargo, las inclusiones secundarias se forman durante la solidificación y no pueden eliminarse. Lo mejor que se puede hacer es modificarlas para minimizar su impacto negativo en el acero.
3.1.1 Nucleación y estructura de las inclusiones
Desde la perspectiva de que las inclusiones primarias que se forman en el acero líquido están estrechamente ligadas al proceso termodinámico, se toman en consideración dos aspectos clave: su nucleación y las estructuras que resultan de ella.
En general, cuando se añade un desoxidante al acero fundido, éste se nuclea rápidamente. Esto se debe a que se observa una elevada sobresaturación durante la adición y disolución del desoxidante. Sigworth y Elliott realizaron una evaluación exhaustiva de las condiciones de nucleación del silicio y descubrieron que el oxígeno disuelto sobresaturado es un requisito.
Sin embargo, la investigación de Miyashita y las observaciones industriales no demostraron una clara sobresaturación durante la desoxidación de silicio en la fabricación de acero. Miyashita también comparó el oxígeno disuelto y el oxígeno total y encontró que la tasa de reducción de oxígeno total es determinada por la tasa de remoción de productos desoxidados, como se ilustra en la Figura 2.
Fig. 2 El oxígeno total y el oxígeno disuelto en el acero tras la desoxidación del silicio en el baño fundido se miden en función del tiempo.
En muchos estudios sobre desoxidación, la diferencia entre el contenido total de oxígeno y el contenido de oxígeno disuelto en el acero depende de la cantidad de inclusiones de óxido que se generen. Esta conclusión clave se demuestra en la figura 3.
Fig. 3
Esta es una ilustración básica de cómo el oxígeno total y el oxígeno disuelto en el acero se ven afectados por la cantidad de inclusiones de óxido.
En el ejemplo, la desoxidación comienza en el punto "a" y se añade aluminio al acero, partiendo de un determinado porcentaje de oxígeno disuelto, Oi.
Sin condiciones de nucleación en el límite de nucleación, el óxido de aluminio se forma en el punto donde el oxígeno disuelto y el contenido de aluminio alcanzan el punto "c".
El contenido total de aluminio en el acero corresponde al oxígeno disuelto (O%) en el acero. El oxígeno que entra en la inclusión de óxido de aluminio permanece en el acero fundido y corresponde al punto "b".
El proceso de desoxidación del punto "a" al "c" reacciona 2Al+3O=Al2O3 según la ecuación química.
Nota: Generalmente, la diferencia entre el aluminio total y el aluminio soluble en ácido (% Als) es pequeño y difícil de medir.
La relación entre el contenido de inclusión y el contenido total de oxígeno (% Ot) en el acero está establecida en la bibliografía. Un bajo contenido de inclusión y de oxígeno total requiere una medición cuidadosa, como se ilustra en la Fig. c.
El análisis del oxígeno total consiste en determinar la densidad de las inclusiones de óxido en la muestra de análisis químico y contarlas mediante SEM (microscopía electrónica de barrido).
Suitu y sus colegas estudiaron la formación de inclusiones de alúmina en una investigación de laboratorio de oxígeno sobresaturado.
El uso de Si (silicio) como desoxidante no presenta ningún problema en la fabricación de acero. Sin embargo, en las operaciones reales de fundición, la nucleación heterogénea es abundante y las condiciones observadas en el laboratorio no pueden reproducirse en los centros de producción industrial.
Es importante estudiar la microestructura del óxido de aluminio como núcleo de inclusión y su crecimiento en el acero. Por ello, el acero con óxido de aluminio es crucial para la producción industrial a gran escala.
Varios autores han investigado en detalle la microestructura del óxido de aluminio, su relación con el oxígeno sobresaturado en el acero y el impacto del tiempo de fundición.
La Fig. 4, presentada por Steinmetz y sus colaboradores, muestra la forma de la inclusión correspondiente a la actividad típica del desoxidante y del oxígeno. La figura sugiere que el oxígeno disuelto sobresaturado desempeña un papel crucial en la morfología de la estructura de la inclusión.
Recientemente, Tiekink y colaboradores intentaron observar la relación funcional entre la estructura de inclusión de óxido de aluminio, el oxígeno sobresaturado y el composición del aluminiocomo se muestra en la Fig. 5. Este esfuerzo es bastante complicado.
Fig. 4 Relación funcional entre la actividad regional del oxígeno, la actividad del aluminio y el crecimiento del óxido
Fig. 5 Resumen de la morfología de las inclusiones de alúmina correspondientes a diferentes actividades de oxígeno y contenido de Al en el acero
La estructura de las inclusiones de óxido tiene un gran impacto en las propiedades del producto final. Es importante señalar que las inclusiones formadas y crecidas en las primeras etapas del acero líquido tienen estructuras morfológicas distintas, como se muestra en las figuras 4 y 6, debido al efecto de las inclusiones entre sí (como se ilustra en la figura 7). Si se prolonga el tiempo de afino, la forma de la inclusión cambiará como consecuencia de la energía superficial.
Fig. 6 Estructura de algunas inclusiones de alúmina.
Se disuelven las inclusiones extraídas de la matriz del tocho de fundición. La estructura en árbol del óxido de aluminio está representada por la línea punteada a. Se utiliza un elemento filtrante fibroso para retener las inclusiones durante el proceso de disolución y actúa como telón de fondo de las inclusiones.
Fig. 7 Racimo de alúmina muestreado de la cuchara, profundamente corroído con ácido pícrico.
3.1.2 Eliminación de inclusiones
La flotación de inclusiones no metálicas en un baño estático de acero fundido puede calcularse mediante un método sencillo basado en las limitaciones de la ley de Stokes. A profundidades normales de la cuchara, la velocidad de flotación de las inclusiones de partículas pequeñas está restringida, y se necesita un tiempo considerable para que alcancen la superficie de la escoria de acero. Este tiempo de flotación prolongado no es factible, especialmente para las inclusiones de óxido de aluminio. Sin embargo, la polimerización por impacto entre las inclusiones les ayuda a flotar, por lo que su polimerización en racimo es crítica.
La importancia de esta agregación ascendente ha sido observada en línea por Emi y sus colegas. Observaron el comportamiento de las inclusiones en la interfaz entre el acero y el gas y descubrieron que la agrupación de óxido de aluminio se produce rápidamente en estas condiciones. Por otro lado, las inclusiones de aluminato cálcico tienen dificultades para agregarse, y la colisión completa sólo se produce en el líquido.
Wikstrom y sus colaboradores ampliaron la observación en línea de la superficie de la escoria de acero y las inclusiones en la escoria y confirmaron los hallazgos de Emi en la interfaz acero-escoria. Emi y sus colaboradores también observaron que cuando el fenómeno se produce en la interfaz gas-acero, como en la superficie de las burbujas, no indica directamente cómo el acero líquido se agrupa en racimos, lo que es especialmente significativo en el caso de las inclusiones líquidas. En este caso pueden ser relevantes otras fuerzas.
Independientemente de que la inclusión sea sólida o líquida, desempeña un papel crucial en la polimerización por aglomeración. Durante mucho tiempo se creyó que la agitación favorecía la aglomeración de las inclusiones, pero el factor más importante para las inclusiones es sumergirlas en la escoria de refinado y el refractario de la pared de la cuchara. Lindskog y sus colaboradores utilizaron un trazador radiactivo para probar y rastrear esta inclusión crucial en la escoria de refinado y la pared de la cuchara.
Debido a las limitaciones actuales, el BaO es el único trazador adecuado que puede utilizarse para evaluar la escoria de refinado y el fundente de molde capturados finalmente en el acero y su impacto en la limpieza del acero. El uso de trazadores de BaO es muy eficaz para determinar el efecto de la corrosión refractaria de la cuchara en la limpieza del acero de número térmico.
El IRSID ha desarrollado el uso del elemento lantano como trazador de inclusiones de óxido. La2O3 es muy estable y, cuando se añade al acero, las inclusiones de alúmina ya existentes pueden identificarse mediante lantano. Las inclusiones exógenas, que proceden del fundente para moldes, pueden rastrearse utilizando óxidos alcalinos. El fundente de molde se suele utilizar sólo en el proceso continuo. proceso de fundición y contiene óxidos alcalinos apreciables.
La mayoría de las inclusiones eliminadas durante el período de refinado de la cuchara son productos desoxidados y pasan por tres etapas: producción/aglomeración de inclusiones separadas, movimiento hacia la escoria de refinado o la pared refractaria de la cuchara, y absorción por la escoria de refinado y el refractario. El movimiento de las inclusiones tiene dos factores cruciales: la agitación del baño de fusión y el arrastre hacia arriba por las burbujas ascendentes.
La mayoría de los resultados de refinado en cuchara muestran que el tamaño de las burbujas de agitación de argón en la cuchara es demasiado grande para eliminar eficazmente las inclusiones y reducirlas en el acero, a menos que se utilice una gran cantidad de argón. Sin embargo, los cálculos de Zhang y Taniguchi indican que la agitación con argón es eficaz cuando la velocidad de flujo del acero fundido es alta y las burbujas son pequeñas.
La tobera sumergida SEN y la tobera larga de cuchara de colada continua tienen un efecto notable en la prevención de la oxidación secundaria, y también se han observado algunas ventajas en el flujo de acero del elevador de tratamiento de vacío RH. La agitación en cuchara de colada favorece que la inclusión flote en la escoria en grupos. Las investigaciones han demostrado que el aumento de la potencia de agitación (mediante agitación electromagnética) supone un aumento de la constante de energía cinética para eliminar la inclusión (medida por el contenido total de oxígeno en el acero).
Fig. 8 El contenido total de oxígeno en el horno de afino de cuchara ASEA-SKF es función de la corriente de agitación y del tiempo de tratamiento.
El contenido final de oxígeno viene determinado por el contenido de aluminio residual en cada horno.
Las observaciones industriales sugieren que la eliminación de inclusiones alcanzará su valor máximo a una energía de mezcla específica.
Suzuki y su equipo fueron los primeros en comunicar esta observación.
Sus resultados se presentan en función del trabajo específico de la energía de mezclado, lo que pone de relieve la importancia de la energía de mezclado. La reducción de la eficacia del afino para eliminar las inclusiones se debe probablemente a la adición de refractario al acero tras la corrosión, o a la envoltura del acero con escoria, ya que las inclusiones de tipo CaO y MgO aumentan bajo agitación fuerte. Estos resultados se ilustran en la figura 9.
Fig. 9 Influencia de la potencia de mezcla en el grado de oxidación secundaria. El punto del círculo ha alcanzado un contenido total de oxígeno inferior a 20 ppm.
Posteriormente, Neifer y su equipo, junto con Ek y su equipo, utilizaron la dinámica de fluidos computacional y modelos físicos para investigar la eliminación de inclusiones de óxido. La relación entre el caudal de argón en la cuchara y la eliminación de inclusiones se trató como una relación funcional.
Los resultados del modelo de Neifer indicaron que la eficacia de la eliminación de las inclusiones metálicas mejoraba mediante la optimización del caudal de gas. Sin embargo, observaron que el aumento del caudal de gas no tenía ningún efecto en la reducción del contenido total de oxígeno en el acero, lo que atribuyeron a la oxidación secundaria del acero fundido en contacto con la atmósfera. Estas conclusiones coinciden con los hallazgos del equipo de Suzuki.
El equipo de Ek descubrió que la influencia del caudal de argón en la eliminación de inclusiones era bastante baja y sugirió utilizar un caudal menor para eliminar las inclusiones y limpiar el acero fundido. Sin embargo, las mediciones industriales del equipo de Neifer indicaron que el contenido total de oxígeno en el acero disminuía al aumentar el caudal de gas. Recomendaron utilizar el transporte por convección natural en los experimentos industriales para obtener resultados óptimos. Sin embargo, debido a la escasez de datos de medición en las pruebas industriales de cuchara de colada, es difícil extraer conclusiones definitivas.
Recientemente, Zhang y Thomas recopilaron muchas constantes cinéticas para utilizarlas en la relación funcional entre la eliminación de la inclusión de óxido y la potencia de agitación, como se muestra en la figura 10. Recopilaron datos de mediciones e intentaron determinar el esquema de mezcla óptimo. También realizaron simulaciones numéricas para reproducir los datos de comportamiento esperados de la parte circundante de la Figura 10.
Fig. 10 La constante de eliminación de oxígeno es una función de la potencia de agitación en diferentes recipientes de reacción metalúrgica secundaria en la fórmula d% Ot/dt=- kt
El equipo de Suzuki destacó que optimizar el proceso de mezclado puede provocar una oxidación secundaria. Una mezcla excesiva puede provocar la apertura de escoria en la parte superior de la cuchara, exponiendo el acero fundido a la atmósfera y provocando el recubrimiento de escoria en el borde de la apertura.
La figura 11 ilustra el cambio en la composición química de las inclusiones no metálicas durante el proceso de desulfuración con fuerte agitación. La presencia de Ca y Mg en las inclusiones confirma que la escoria se ha emulsionado.
Fig. 11 La relación entre la composición media de todas las inclusiones no metálicas y la intensidad de agitación se analizó tomando muestras del horno de afino, del cristalizador y de la losa.
El equipo de Kaushik descubrió que una fuerte agitación mejora la emulsificación de la escoria durante la desulfuración. La prueba estaba en el alto contenido de calcio en las inclusiones. En caso de agitación excesiva con argón y escoria de baja cima, se regeneran las inclusiones de óxido de aluminio. Por tanto, es crucial optimizar la potencia de agitación para eliminar las inclusiones durante el afino de acero fundido limpio.
Nunca se insistirá lo suficiente en la importancia de la oxidación secundaria para la limpieza del acero. El equipo de Nadif informó de la importancia de controlar la oxidación secundaria. Las acerías han tomado diversas medidas en las últimas décadas para regular la oxidación secundaria tras el refinado.
La tobera sumergida SEN y la tobera de cuchara se utilizan habitualmente para aislar la atmósfera en la colada continua de desbastes. En la fabricación de productos largos, el artesa y el cristalizador están protegidos por gas inerte, lo que se ha convertido en la norma para producir calidades de acero de alta calidad.
Debe prestarse especial atención al diseño de la válvula de gas inerte para evitar la intrusión de aire causada por la presión negativa en el sistema de válvulas. La contribución de la tensión superficial de las inclusiones adheridas a la escoria de refinado es la mayor, seguida de la capacidad de la escoria para disolver inclusiones.
Independientemente de la composición de la escoria, la mayor parte de la escoria de refinado y las inclusiones están húmedas debido a la diferencia de energía superficial entre las inclusiones y el acero fundido, y las inclusiones y la escoria de refinado. Este fenómeno se ha debatido durante muchos años y ha sido resumido por Olette. La fracción líquida de la escoria de afino favorece la eliminación de las inclusiones no metálicas, lo que se conocía por la bibliografía anterior y se confirmó mediante experimentos.
Sin embargo, sigue habiendo algunas incoherencias en la viscosidad de la escoria. Nakajima y Okamura propusieron un modelo para explicar el proceso de paso de inclusiones a través de la interfaz acero-escoria. Posteriormente, muchos estudios profundizaron en el tema de la absorción de inclusiones por la escoria. Nakajima y Okamura sugirieron que, en determinadas condiciones, las inclusiones entran en la escoria desde el acero, que puede incluir una película metálica de la interfaz a modo de canal, mientras que en otros casos, especialmente con inclusiones sólidas, no existe tal película metálica, como se muestra en la Fig. 12.
La Fig. 12 muestra dos tipos de inclusiones que atraviesan la interfaz escoria-acero, introducidas a partir de Nakajima. El número de Reynolds de las inclusiones que alcanzan la interfaz determina su comportamiento
La conclusión del equipo de Sridhar es que la viscosidad de la escoria y la energía superficial asociada son factores cruciales para determinar el paso de las inclusiones a través de la interfaz y reducir la probabilidad de que vuelvan al acero fundido. Esto se resume en el número de Reynolds cuando la inclusión está cerca de la interfaz.
Recientemente, el equipo observó el canal de flujo de esta película en línea, lo que es un hecho habitual. En la mayoría de los casos, la trayectoria de la inclusión que entra en la escoria se prolonga. Una vez que sale del acero fundido, la inclusión líquida se disuelve inmediatamente en la escoria.
La observación en línea permite estudiar experimentalmente la termodinámica de la disolución de las inclusiones sólidas. En algunos casos, la disolución está controlada por el transporte (difusión en la capa intermedia), mientras que en otros, como en el caso de la inclusión de MgO, la formación de la capa intermedia depende de la composición química de la escoria y puede dificultar la disolución en diversas etapas químicas del refinado. Así lo confirman los resultados obtenidos con métodos técnicos comunes anteriores.
Recientemente, el equipo de Yan estimó la disolución de MgO en la escoria y descubrió que todos los datos estaban controlados por la transmisión de calidad.
El equipo de Holappa estudió la actividad del agente de recubrimiento del distribuidor, que es crucial para absorber las inclusiones. Observaron una compleja interacción entre la composición química, las condiciones termodinámicas, la tensión superficial y la viscosidad de la escoria cuando se disuelven inclusiones sólidas no metálicas. El equipo llegó a la conclusión de que es necesario seguir investigando sistemáticamente para comprender mejor este campo y desarrollar métodos de optimización.
Es bueno que las inclusiones no metálicas se adsorban en la superficie refractaria de la cuchara, pero estas inclusiones también pueden convertirse en la fuente de inclusiones en el horno siguiente, dependiendo de la composición de la escoria de la cuchara.
Si las inclusiones se adsorben en el canal de la tubería de acero fundido, puede causar problemas significativos, como un largo tiempo de tratamiento y un alto coste debido a la obstrucción de la boquilla en el proceso de colada continua. Este fenómeno de obstrucción de la boquilla está bien descrito en las referencias.
Se observa que el flujo floculento en la boquilla se debe a la adhesión y acumulación de inclusiones de óxido de aluminio y FeO, que pueden formarse en la oxidación secundaria. Este fenómeno se describe claramente en las referencias.
Existe una amplia bibliografía sobre la absorción de inclusiones primarias por el polvo de moldeo durante la colada continua y la colada de lingotes. El consenso entre estas fuentes es que este fenómeno es realmente posible.
El fundente de molde utilizado en la colada continua y en la colada en molde (que es similar al agente de recubrimiento de la artesa de colada) debe tener múltiples funciones y poseer fluidez. Sin embargo, está sujeto a varias restricciones dentro del molde, como evitar la inclusión de fundente de molde en la superficie de la cáscara verde primaria. Esto, en cierta medida, restringe el movimiento de las inclusiones y las mantiene dentro del fundente del molde. Al mismo tiempo, optimiza el flujo de acero fundido en el artesa y el molde, permitiendo que el acero fundido llegue a la interfaz de la escoria con las inclusiones. Sin embargo, esto crea objetivos contradictorios con otros objetivos metalúrgicos relevantes.
La mejor manera de eliminar las inclusiones causadas por la convección es mediante el afino en cuchara, y también es crucial evitar que la oxidación secundaria cree nuevas inclusiones, aspecto crucial para producir un acero limpio.
Otra cuestión es el movimiento de las inclusiones primarias en el planchón de colada continua. Se ha reconocido ampliamente que las inclusiones se distribuyen asimétricamente en la sección transversal debido al proceso de colada continua por arco. Esta asimetría suele estar relacionada con la obstrucción del flujo de flóculos en la boquilla.
Sichen ha demostrado recientemente el impacto del modelo de refinado secundario, en particular el proceso del horno de refinado. El modelo trata de explicar la reacción de interfaz de la escoria de acero, la apertura de la capa de escoria de agitación de transición, la generación, nucleación, crecimiento, separación y eliminación por flotación de las inclusiones, utilizando la mayoría de las tecnologías disponibles.
Sin embargo, Sichen señaló que las principales variables del proceso de refinado en cuchara, como la eficiencia de la transferencia de masa, la tasa de eliminación de inclusión flotante, la apertura de la capa de escoria sobreagitada y el caudal de argón, son difíciles de simular debido a las incertidumbres de la producción industrial, como el tapón de venteo de la cuchara y las fugas de la tubería de gas.
Controlar y detectar la velocidad del flujo de argón en el refinado industrial de cucharas es todo un reto. La tecnología de cámaras y analizadores de imágenes puede utilizarse para supervisar la apertura de la capa de escoria de la cuchara, mientras que la medición de vibraciones puede utilizarse para controlar el flujo de argón. Estas tecnologías ya han sido adoptadas por algunas plantas siderúrgicas.
Durante la solidificación, la fuerza impulsora de la precipitación de la inclusión secundaria aumenta la segregación de los elementos solutos, y la solubilidad de los óxidos y sulfuros en el acero disminuye a medida que baja la temperatura.
El fenómeno de la precipitación de inclusiones debido a cambios en la solubilidad del acero ha sido objeto de debate durante algún tiempo.
Desde la década de 1960, se han establecido los términos "inclusiones primarias" y "secundarias", y se ha definido la relación entre la segregación y la precipitación de las inclusiones.
En aquel momento se presentó el primer modelo que explicaba este proceso.
Turkdogan y Flemings hicieron una importante contribución a nuestra comprensión del impacto global de los cambios de solubilidad con la disminución de la temperatura en la segregación de la inclusión secundaria.
Durante las décadas de 1980 y 1990, Nippon Steel e IRSID desarrollaron modelos avanzados, que posteriormente se aplicaron a la precipitación de nitruro en acero microaleado HSLA durante la solidificación.
Estos modelos allanaron el camino para el estudio de la ingeniería de la inclusión.
Hoy sabemos que combinando una base de datos termodinámica y una base de datos cinética, podemos simular la solidificación y calcular la formación de inclusiones.
Estos cálculos parten de la composición química deseada del acero, predicen la precipitación de inclusiones y guían el diseño de la composición de la escoria de afino durante el afino en cuchara para producir acero limpio.
La interacción entre el acero líquido, las dendritas y las inclusiones formadas en el frente de solidificación es un importante campo de estudio.
Las observaciones en línea indican que las condiciones de solidificación desempeñan un papel crucial en la formación de inclusiones que son empujadas a la fase líquida en la interfase y engullidas por las inclusiones.
En teoría, estos resultados pueden calcularse y ajustarse para tener en cuenta los efectos de la tensión superficial y la densidad.
La investigación teórica se centra principalmente en la composición del metal matrices, y los resultados relativos a las inclusiones no metálicas en el acero también se ajustan más a las condiciones reales.
Los resultados indican que la velocidad crítica de crecimiento (V) puede representarse como V = k/R, donde R es el radio de engullimiento y repulsión de la interfaz de inclusión, y k depende del tipo de inclusión.
La estructura de las inclusiones secundarias se ve afectada significativamente por las reacciones que se producen durante la precipitación, siendo la precipitación de carburos uno de los mejores ejemplos.
Desde que Sims observó por primera vez en 1930 el impacto de la reoxidación en la estructura de los sulfuros, propuso posteriormente tres tipos distintos de sulfuros, que han sido descritos minuciosamente por diversos autores.
Recientemente, el equipo de Ishida ha puesto de relieve que, además del tipo de reacción que acompaña a la formación del sulfuro, la tensión superficial también desempeña un papel crucial en la conformación de la estructura del sulfuro.
El equipo de Gaye ha presentado la explicación más completa y perspicaz de la aplicación termodinámica de la ingeniería de inclusión en el acero.
La figura 13 ofrece una ilustración concisa en dos diagramas de fase ternarios adiabáticos.
Una vez identificadas las inclusiones necesarias, puede determinarse la composición química del acero que las producirá.
La composición de la escoria de afino utilizada para el afino puede calcularse a partir de la composición química del acero mediante un balance de escorias de acero.
El dicho de que "el acero sólo puede fabricarse fundiendo escoria" está bien fundado y se ha aplicado con éxito en la producción de diversos productos. tipos de acero.
En la producción de acero, es importante evitar las inclusiones compuestas de óxido de aluminio en fase dura (como la espinela).
Por ejemplo, en la producción de acero para rodamientos, la inclusión actúa como núcleo de nucleación durante la transformación de fase que se produce durante el enfriamiento.
El tratamiento con calcio transforma las inclusiones en inclusiones líquidas y, junto con el calcio, modifica los sulfuros para evitar la obstrucción de las boquillas.
Aunque el proceso de modificación de la inclusión puede parecer sencillo, también es un tema de debate en este capítulo.
La Fig. 13 muestra el proceso de transformación de las inclusiones. Desde el punto de vista termodinámico, el Al2O3 se espera obtener inclusiones en el acero Si Mn matado.
Las inclusiones esperadas se muestran en el diagrama de fases simplificado de MnO-SiO2-Al2O3 sistema ternario.
El diagrama de la izquierda muestra el sistema en la isoterma de 1470 ℃. La región se indica como fase líquida 100%, confinada dentro de la línea delgada, como se representa en la figura.
La isopleta sólida y gruesa a la temperatura especificada representa el contenido de aluminio en el acero fundido con inclusiones líquidas en equilibrio. La línea de puntos, por su parte, indica la composición química de las inclusiones en el acero 0,35% Si, 1% Mn a una temperatura determinada, que varía con el contenido de aluminio del grado de acero.
Según el diagrama, si se quiere tener inclusiones líquidas, el contenido de aluminio del acero no debe superar el círculo gris (8ppm).
La figura de la derecha muestra la escoria de refinado en cuchara simplificada de CaO-SiO2-Al2O3 sistema.
La isoterma 1520 ℃ representa las condiciones en el horno de afino de cuchara y muestra que la región de inclusión líquida 100% está confinada a la línea sólida fina.
A la temperatura elegida, la línea sólida gruesa representa el contenido de aluminio del acero en estado de equilibrio dentro del sistema de escorias. La línea gris muestra el correspondiente contenido de oxígeno en el acero examinado.
Si se desean inclusiones líquidas (a la izquierda del diagrama), la composición de la escoria de afino debe elegirse como indica el diagrama para garantizar que el contenido de aluminio en el acero sea inferior a 8ppm.
El alambre de acero radial para neumáticos está fabricado con acero de alto contenido en carbono desoxidado con silicio-manganeso.
También se utilizan métodos similares en la fabricación de muchos aceros para muelles de automoción.
Las inclusiones no metálicas frágiles, normalmente inclusiones de óxido de aluminio o inclusiones con alto contenido de óxido de aluminio, tienen un impacto significativo tanto en el rendimiento de trefilado del alambre de acero como en la calidad del acero para muelles.
Para evitar la formación de inclusiones de óxido de aluminio o de inclusiones ricas en óxido de aluminio, hay que ajustar la composición del acero. Esto implica un control estricto del contenido de óxido de aluminio en la escoria, la supervisión de las materias primas y auxiliares para evitar la entrada de aluminio en el acero y el uso de un sistema de escoria binaria de baja alcalinidad.
Esta solución era inicialmente contradictoria con las operaciones de refinado predominantes en la época.
Existen numerosos ejemplos y artículos excelentes que abordan la termodinámica de control del tratamiento de inclusión del acero radial y para muelles de los neumáticos.
El impacto de un único tipo de inclusión en la vida a fatiga del acero para rodamientos sigue siendo un tema de debate. Sin embargo, está ampliamente aceptado que el tamaño y la cantidad de inclusiones en el acero afectan significativamente a la vida a fatiga del acero para rodamientos.
Es bien sabido que las inclusiones de aluminato cálcico y espinela afectan negativamente al rendimiento del acero para rodamientos.
En consecuencia, hay quien opina que la producción de acero para rodamientos debería tener como objetivo alcanzar un contenido total de oxígeno muy bajo y un contenido de azufre y aluminio muy bajo, para mantener al mínimo las inclusiones no metálicas.
Además, la introducción de magnesio procedente de la escoria puede dar lugar a la formación de inclusiones de espinela, que deben evitarse.
Para producir acero para rodamientos de alta calidad, las distintas plantas siderúrgicas adoptan diferentes métodos de proceso en función de sus condiciones específicas.
Sin embargo, el control de la composición química de la escoria de refinado es siempre un factor crítico para controlar las inclusiones no metálicas en el acero para rodamientos.
La figura 14 muestra la influencia de los contenidos de Al, O y Ag en el acero para rodamientos 100Cr6 (AISI52100) en la composición de la escoria. También se muestra la comparación de los contenidos de aluminio y oxígeno calculados y medidos en el acero.
Fig. 14
a. En el estado de equilibrio del acero portante, la escoria de afino% Al2O3=5%,% CaO=48% permanecen inalterados, y la influencia del MgO sobre el Al, el O y el Mg se calcula utilizando las bases de datos Thermo calc y SLAG2 a 1540 ℃.
b. Comparar el valor calculado y el valor medido del acero para rodamientos tras finalizar el afino del horno 3, y para el cálculo se utiliza la base de datos Thermo calc® y SLAG2.
El tratamiento con calcio se utiliza para eliminar las inclusiones de sulfuro y regular la anisotropía de los materiales laminados en caliente o las piezas forjadas. También ayuda a mejorar la trabajabilidad de las inclusiones.
La práctica de utilizar el tratamiento con calcio para transformar las inclusiones de óxido de aluminio en inclusiones compuestas líquidas para evitar la obstrucción de los flóculos de las boquillas se ha generalizado en las últimas décadas, a pesar de ser un método controvertido.
El proceso de tratamiento con calcio es complejo y requiere la consideración de factores como la solubilidad del calcio, el rendimiento y la elevada presión de vapor causada por la oxidación durante la adición de calcio. Estos factores se han investigado a fondo.
También se han realizado estudios sobre el mecanismo de desnaturalización de la inclusión y la cantidad ideal de calcio necesaria para lograr el resultado deseado.
La formación de inclusiones es un proceso complejo. La capa exterior, a menudo compuesta de óxidos, se cubre con un revestimiento de compuestos ricos en azufre. Este fenómeno y la distribución de los distintos elementos se ilustran en la figura 15.
Fig. 15
El tratamiento con calcio se utiliza para mejorar la colabilidad del acero. Disuelve las inclusiones de partículas grandes compuestas de aluminato cálcico, sulfuro y AgO que se encuentran en el planchón durante la colada continua.
El magnesio también se reduce de la escoria al acero durante el proceso de tratamiento.
Como resultado del tratamiento, una parte significativa de las inclusiones se convierte en fase líquida y no obstruirá la boquilla durante la colada.
Sin embargo, si la temperatura del acero fundido es demasiado baja, la fundición se convertirá en un reto.
La reacción de las inclusiones no metálicas formadas durante la solidificación es un proceso complejo, como se ilustra en la figura 16.
Fig. 16
La muestra de la losa contiene grandes inclusiones rotas de aluminato cálcico con fases complejas, y la envoltura de la inclusión muestra una estructura de solidificación dendrítica.
La cantidad de calcio necesaria para modificar las inclusiones de óxido de calcio depende del contenido total de oxígeno en el acero.
Desgraciadamente, no existe un método actual para determinar con precisión el contenido total de oxígeno en el acero en tiempo real, lo que dificulta la determinación de la cantidad adecuada de calcio que debe añadirse.
Esto supone un reto importante para la producción industrial.
Una solución es utilizar la termodinámica para comprender la obstrucción del flujo de flóculos en la boquilla y establecer la ventana de colada para la colada continua.
El nivel de oxígeno disuelto puede medirse, y estos datos también pueden utilizarse para controlar la eficacia del tratamiento con calcio, como se muestra en la Figura 17.
Fig. 17
La figura anterior muestra la correlación entre el contenido de calcio y el oxígeno disuelto calculado en acero con una composición de 0,025% Al, 0,01% S, y contenidos variables de oxígeno total de 20, 25 y 30 ppm de izquierda a derecha, a una temperatura de 1540 ℃.
La presencia de fases no metálicas se indica dentro de cada intervalo de composición.
Los cálculos se realizaron utilizando las bases de datos Thermo-Calc® y SLAG3.
Cada punto representa la medición experimental del contenido de oxígeno disuelto en el acero, que se obtuvo sin ningún bloqueo en la boquilla.
El proceso final de fundición se enfrenta a un reto que exige controlar la microestructura y no puede depender únicamente de la laminación en caliente.
Las investigaciones han demostrado que la presencia de ferrita en el metal de soldadura influye positivamente en la formación de inclusiones no metálicas.
La teoría de la nucleación de la inclusión sugiere que la formación de la inclusión agota el Mn de la matriz circundante, lo que parece ser eficaz.
Las inclusiones de óxidos no metálicos sirven como núcleos de nucleación para las inclusiones de MnS y han producido resultados favorables en aplicaciones.
Además, la oxidación secundaria de titanio en el acero al silicio-manganeso transforma las inclusiones en óxido de titanio, mientras que el óxido y el nitruro tienen una alta eficiencia de nucleación en la ferrita, como se ha confirmado.
Koseki, Inoue, Suito y Park han demostrado que el nitruro de titanio puede actuar eficazmente como agente nucleante, promoviendo la aparición de grandes granos equiaxiales en continuo. fundición de acero inoxidable y los procesos de soldadura.
Park y Kang han realizado recientemente avances en este campo.
Los cálculos termodinámicos y las simulaciones de modelos demuestran que el diseño de aleaciones y el diseño de procesos en la metalurgia del óxido pueden ser muy beneficiosos.
En las últimas décadas, la industria siderúrgica se ha enfrentado al reto de clasificar y cuantificar con precisión las inclusiones no metálicas mediante gráficos e imágenes de comparación tradicionales. Para mejorar el análisis cuantitativo de las inclusiones, incluida la información sobre tamaño, fracción volumétrica y composición, han surgido nuevos métodos.
En muchos casos, es necesario emplear varios métodos simultáneamente para obtener una comprensión global de la naturaleza y el proceso de las inclusiones no metálicas. La investigación ha demostrado que determinadas características dependen de la distribución de las inclusiones, mientras que otras dependen de otros factores. Por ejemplo, el comportamiento a fatiga del acero se ve influido por el tamaño de la mayor inclusión.
La limpieza de los productos de acero varía mucho, salvo en los productos de gama baja. El contenido total de oxígeno del acero con bajo contenido de carbono y aluminio (LCAK) es de aproximadamente 40 ppm, mientras que el acero para rodamientos típico tiene un contenido total de oxígeno de unas 5 ppm. La fracción volumétrica de las inclusiones de óxido es muy diferente, pero no se menciona la presencia de inclusiones de sulfuro.
La estadística de valores extremos y su aplicación desempeñan un papel fundamental en el análisis de la fatiga. Estos métodos no están ampliamente cubiertos en la literatura general, pero se incluyen en esta revisión bibliográfica con referencias proporcionadas para lecturas adicionales. El método de grado de evaluación de inclusión mediante estadística de valores extremos, propuesto por Murakami en el programa, se ha utilizado ampliamente en el campo de la fatiga y ha dado excelentes resultados.
Es importante señalar que este método no tiene en cuenta el tamaño máximo de inclusión en el análisis de fatiga. De hecho, la fracción de volumen de las inclusiones causada por las inclusiones de partículas grandes puede aumentar. Este aspecto del método puede no coincidir con las expectativas de los fabricantes de acero, ya que no tiene en cuenta la inclusión de la partícula de mayor tamaño.
En la industria siderúrgica está muy arraigado el dicho: "Una buena escoria conduce a un buen acero".
En las últimas décadas, el reconocimiento del impacto de las inclusiones no metálicas en las propiedades del acero ha hecho que el proceso de fabricación de acero haya pasado de la mera prevención de la contaminación por inclusiones a la optimización de la composición, la cantidad y la distribución de las inclusiones en el acero.
Esta transformación afecta a todos los aspectos del proceso siderúrgico, desde la materia prima hasta el producto final. selección de materiales (como evitar la contaminación por aluminio), al diseño de la composición de la escoria, a la optimización de las condiciones de refinado secundario (como el tiempo del proceso de refinado y las condiciones hidrodinámicas), y al cuidadoso control del funcionamiento de los artesones y los moldes.
Se ha convertido en una práctica habitual en la producción de diversos tipos de acero controlar cuidadosamente la oxidación secundaria en todos los procesos.
La termodinámica desempeña un papel fundamental en la investigación de la influencia de las inclusiones en el acero. En la actualidad se estudia ampliamente la termodinámica, la composición química del acero y la escoria de afino, así como las interacciones entre las condiciones del proceso de fabricación del acero.
También se ha producido una mejora significativa en las herramientas de modelado, lo que permite un enfoque más basado en la ciencia para controlar las inclusiones en el acero.
Estas tecnologías se han adoptado ampliamente y siguen evolucionando en el campo de la modificación de las inclusiones no metálicas. Sin embargo, sigue siendo necesario mejorar continuamente la escoria de afino y comprender plenamente el papel de las inclusiones no metálicas en el acero.
La modificación de inclusiones y la ingeniería metalúrgica de óxidos se utilizan ahora ampliamente en las plantas siderúrgicas, lo que da lugar a aceros que son al menos un orden de magnitud más limpios que hace varias décadas. Esto también ha planteado nuevos retos para el análisis cualitativo y cuantitativo de las inclusiones no metálicas.
El análisis cuantitativo de todas las inclusiones y su impacto en las propiedades y el comportamiento del acero es ahora un requisito básico, y existe un amplio margen para el debate y la investigación futura.
A pesar de los avances y conocimientos resumidos en esta revisión, el reto permanente en las próximas décadas será mejorar continuamente diversas tecnologías y mejorar la calidad del acero.