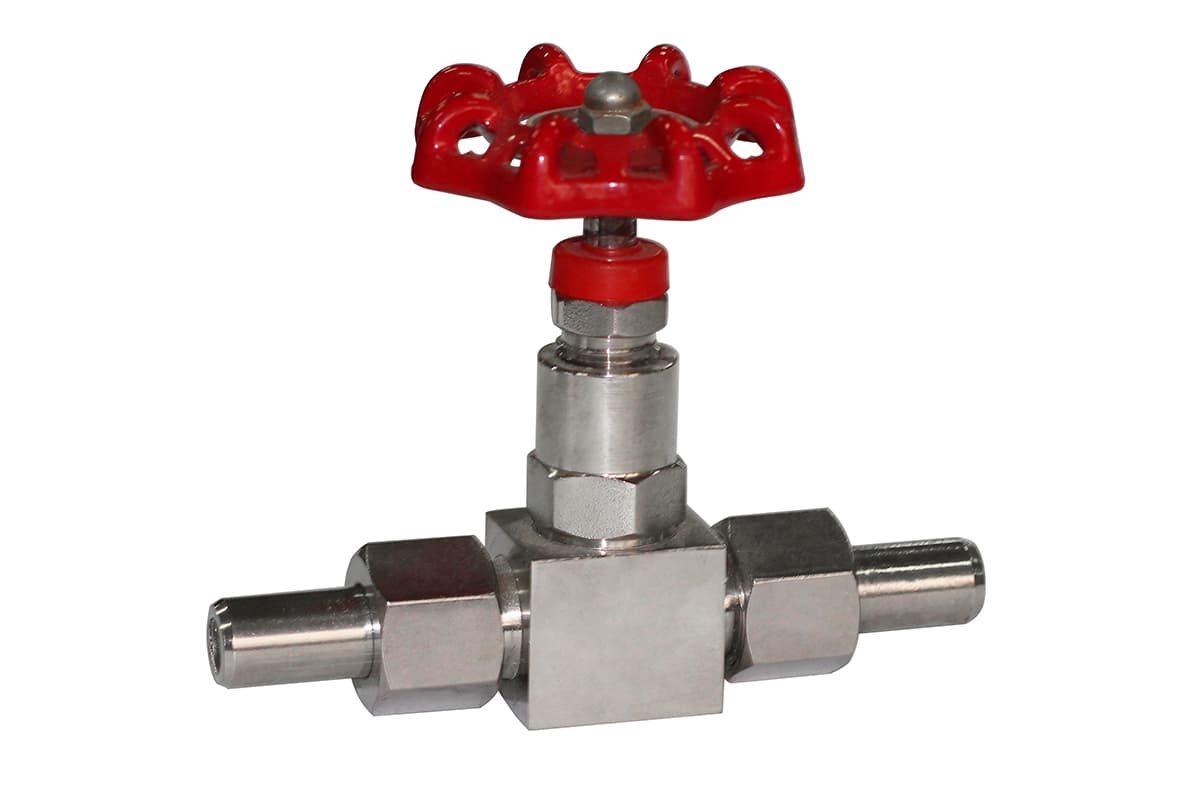
¿Ha pensado alguna vez en los peligros ocultos que acechan a las tuberías de oxígeno? En este artículo, nos sumergimos en el crítico proceso de desengrasado de tuberías de oxígeno, esencial para evitar riesgos de explosión. Conocerá la importancia de la eliminación del aceite, los pasos necesarios para el desengrasado, decapado y pasivado, y las medidas de seguridad necesarias para manipular estos materiales. Esta guía garantiza que sus operaciones con tuberías de oxígeno sigan siendo seguras y eficaces.
Todo el mundo sabe que las tuberías de oxígeno deben estar libres de aceite y desengrasadas. Hoy hablaremos del método de desengrase de las tuberías de oxígeno. Desengrasar, por definición, es eliminar las manchas de aceite de las superficies internas y externas de la tubería.
Es un paso crucial en la construcción de tuberías de oxígeno. Si hay alguna contaminación de aceite en el interior del tubo de oxígeno, puede producirse fácilmente una explosión al entrar en contacto con el oxígeno puro.
Las tuberías de oxígeno suelen utilizar tubos de acero sin soldadura de acero 20# o acero inoxidable. En el caso de los tubos de acero inoxidable, solo es necesario un tratamiento desengrasante.
Sin embargo, en el caso de los tubos de acero 20#, no sólo es necesario el desengrasado, sino también el decapado, la neutralización y el tratamiento de pasivación.
Durante la construcción, los extremos de los tubos desengrasados deben sellarse rápidamente para evitar una contaminación secundaria. Antes de entregarlos para su uso, deben limpiarse a fondo con aire comprimido sin aceite.
Los tubos de acero al carbono deben desengrasarse antes del decapado, ya que la grasa no es soluble en ácido. Si se decapan primero, no se eliminarán las manchas de aceite ni el óxido bajo las manchas de aceite.
El método de inmersión se utiliza habitualmente para desengrasar y decapar tubos de acero sin soldadura durante la construcción. Durante la inmersión, el nivel del líquido debe estar al menos 50 mm por encima de la superficie exterior del tubo.
Dado que las tuberías de oxígeno se someten a un tratamiento de desengrasado, decapado y pasivado, suelen prepararse cuatro tanques en función del diámetro real de la tubería. Se trata del tanque de desengrasado, el tanque de decapado, el tanque de neutralización y el tanque de pasivación.
El flujo del proceso de desengrasado y decapado para tuberías de oxígeno es el siguiente: desengrasado → aclarado con agua → decapado → aclarado con agua → neutralización → pasivación → aclarado con agua → secado.
La fórmula de la solución desengrasante es: cada litro de solución contiene de 20 g a 30 g de hidróxido sódico, de 35 g a 50 g de nitrato sódico y de 3 g a 5 g de silicato sódico.
El proceso operativo requiere: una temperatura del líquido de 70℃ a 80℃, y un tiempo de remojo determinado por la cantidad de aceite en la superficie de la tubería, normalmente entre 10 y 40 minutos.
El vapor puede utilizarse para calefacción.
Los elementos desengrasados deben inspeccionarse utilizando cualquiera de los métodos siguientes:
Aclarar abundantemente con agua limpia a una presión de 0,8 MPa.
El decapado utiliza una solución ácida para eliminar la piel de óxido y el óxido de la superficie del tubo de acero sin soldadura.
Los óxidos de hierro (Fe3O4, Fe2O3, FeO, etc.) reaccionan con la solución ácida para formar sales que son solubles en la solución ácida y así se eliminan. El ácido sulfúrico y el ácido clorhídrico son los más utilizados para el decapado. La fórmula de la solución de ácido sulfúrico es: la concentración de ácido sulfúrico es de 5% a 10%.
Los requisitos de funcionamiento son: una temperatura de 60℃ a 80℃ y un tiempo de remojo de 5 a 20 minutos. La fórmula de la solución de ácido clorhídrico es: la concentración de ácido clorhídrico es de 5% a 20%.
Los requisitos operativos son: una temperatura de 20℃ a 50℃ y un tiempo de remojo de 5 a 20 minutos.
Una vez decapado el tubo, compruebe que el óxido superficial se haya eliminado por completo y que el brillo del metal quede al descubierto. Se considera calificado si este es el caso.
Aclarar abundantemente con agua limpia a una presión de 0,8 MPa.
La fórmula de la solución de neutralización es NH4OH diluido hasta un valor de pH de 10 a 11. El requisito operativo es: remojo a temperatura ambiente durante 3 minutos.
Tras el decapado, el aclarado con agua y el blanqueado, la superficie metálica está muy limpia y muy activada, y es muy susceptible a la corrosión. Por lo tanto, el tratamiento de pasivación debe realizarse inmediatamente para formar una película protectora sobre la superficie metálica limpia que frene la corrosión.
La fórmula de la solución de pasivación es: la concentración de NaNO2 es de 8% a 10%; la concentración de NH4OH es de 2%. El requisito de funcionamiento es: remojo a temperatura ambiente durante 10 minutos.
Aclarar con agua purificada a una presión de 0,8MPa hasta que quede limpio.
El secado debe realizarse con aire limpio, sin aceite y seco o con nitrógeno.
Limpie e inspeccione con papel de filtro blanco. Si no hay restos de aceite en el papel, se considera apto. Después de pasar la inspección, selle ambos extremos de la tubería con tela plástica y cinta adhesiva.
Los tubos de acero al carbono tratados de este modo tienen las paredes interiores limpias y brillantes y pueden permanecer sin oxidarse durante unos 2 meses; si se almacenan bien, este periodo puede prolongarse. Este método también puede aplicarse a los accesorios de tubería de acero al carbono.
En el caso de los tubos de acero inoxidable que sólo requieren desengrasado, además de los métodos mencionados anteriormente, la técnica de limpieza por frotamiento es especialmente eficaz para los tubos de mayor diámetro. Este método ofrece una limpieza de precisión para aplicaciones críticas en las que la integridad de la superficie es primordial.
Al emplear el método de limpieza, es crucial seleccionar materiales adecuados para evitar la contaminación. No se recomienda el hilo de algodón debido a su propensión a desprenderse. En su lugar, deben utilizarse paños que no suelten pelusa, tejidos de microfibra o materiales de fibra de vidrio, ya que minimizan el riesgo de residuos de fibra y garantizan un proceso de limpieza a fondo.
Para tuberías de gran longitud, puede emplearse una técnica especializada. Se pueden utilizar alambres de acero inoxidable limpios y pasivados (preferiblemente de grado 316 o superior) para fijar tiras de tela sin pelusa. Esta configuración permite movimientos bidireccionales de arrastre y limpieza, eliminando eficazmente los contaminantes aceitosos de las paredes interiores de la tubería. El enfoque bidireccional garantiza una cobertura completa y mejora la eficacia de la limpieza.
Tras el desengrase, es obligatorio realizar una inspección meticulosa de la superficie del componente. Este paso es fundamental para detectar y eliminar cualquier fibra textil orgánica que pueda haberse adherido durante el proceso de limpieza. Pueden emplearse métodos de inspección avanzados, como el examen con luz ultravioleta o la inspección con luz blanca, para obtener resultados óptimos.
Tras una inspección satisfactoria, es imperativo sellar inmediatamente los extremos de los tubos. Esto evita la recontaminación y mantiene la limpieza de las superficies internas. Los métodos de sellado adecuados incluyen el uso de tapas o tapones limpios y sin pelusa, o cubiertas de plástico termorretráctiles para aplicaciones más exigentes.
Para las tuberías que requieren tanto desengrasado como decapado o pasivado, es esencial seguir un proceso secuencial. El desengrasado debe preceder siempre al decapado o la pasivación para garantizar la eficacia de estos tratamientos posteriores y mantener los más altos niveles de acabado superficial y resistencia a la corrosión.
Para alojar la válvula más grande, construya un recipiente de desengrase a medida utilizando placas de acero inoxidable resistentes a la corrosión o modifique un bidón industrial adecuado. Asegúrese de limpiar a fondo la superficie interior del recipiente y de inspeccionarla en busca de contaminantes con un paño blanco sin pelusas.
Antes de desengrasar, limpie meticulosamente los accesorios de tubería y las válvulas de acero inoxidable con paños de microfibra sin pelusa. Suspenda los componentes utilizando alambre de acero inoxidable 316 o cables recubiertos de PTFE para evitar posibles contaminaciones.
Seleccione un disolvente desengrasante adecuado, respetuoso con el medio ambiente y menos peligroso, como los desengrasantes a base de cítricos o las soluciones alcalinas acuosas, como alternativas más seguras al tetracloruro de carbono. Llene el recipiente con el disolvente elegido, manteniendo un margen de seguridad de al menos 200 mm desde la parte superior para evitar derrames y garantizar una ventilación adecuada.
Aplique medidas de seguridad sólidas, incluidos equipos de protección individual (EPI) adecuados, ventilación local por aspiración y cumplimiento de las normas de seguridad pertinentes (por ejemplo, la normativa de la OSHA). Realice las operaciones de desengrasado en una zona bien ventilada o bajo una campana extractora para minimizar los riesgos de exposición.
Sumerja los componentes en la solución desengrasante durante el tiempo recomendado por el fabricante, normalmente 1-2 horas. Una vez retiradas, enjuague bien las piezas con agua desionizada y séquelas con aire comprimido limpio y sin aceite o con paños que no suelten pelusa. Deje que se sequen completamente al aire en un entorno controlado y sin polvo.
Después del desengrasado, realice una inspección de calidad exhaustiva utilizando luz ultravioleta y pruebas de limpieza con paño blanco para garantizar la eliminación completa de contaminantes. Envuelva y selle individualmente los componentes aprobados en bolsas de plástico limpias y antiestáticas para evitar la recontaminación.
Para las válvulas, realizar el rectificado y la prueba de presión antes del desengrase. Desmonte las válvulas, eliminando todos los residuos y productos de corrosión antes de sumergirlas en la solución desengrasante. Preste especial atención a los componentes internos intrincados y a las cavidades.
Aplique el mismo proceso de desengrase a pernos, juntas metálicas y otros componentes pequeños. Para cuerpos de válvula grandes no aptos para inmersión, utilice métodos de desengrase por pulverización o frotamiento con disolventes adecuados.
Trate las juntas no metálicas por separado, utilizando disolventes compatibles y métodos de desengrase más suaves para evitar la degradación del material. Después del desengrase, seque estos componentes en un entorno controlado con circulación de aire filtrado por HEPA hasta que se eliminen todos los restos de disolvente.
Para los componentes que contengan amianto, consulte la normativa vigente sobre manipulación de amianto. Si está permitido, considere materiales aislantes alternativos para altas temperaturas. Si es necesario utilizar amianto, siga protocolos de seguridad estrictos para el tratamiento térmico y la posterior aplicación del revestimiento.
Implantar un sistema de control de calidad exhaustivo, que incluya inspecciones previas y posteriores al desengrase, para garantizar una limpieza y una preparación de la superficie uniformes en todos los componentes. Documente todos los procesos y mantenga registros detallados para la trazabilidad y la mejora continua.
Antes de iniciar las actividades de construcción, el personal técnico deberá realizar sesiones informativas exhaustivas sobre seguridad y técnica para todo el personal de construcción. Todas las herramientas, instrumentos de medición y equipos auxiliares destinados a los procesos de desengrase, inspección e instalación deberán someterse a un tratamiento de desengrase previo en estricta conformidad con las especificaciones de los componentes que vayan a desengrasarse.
El uso de equipos no desengrasados está estrictamente prohibido. Los protocolos de seguridad para las operaciones de desengrasado y decapado deben cumplir las directrices pertinentes recogidas en el "Reglamento técnico de seguridad en la construcción petroquímica". Estas operaciones deben realizarse exclusivamente en entornos exteriores bien ventilados para minimizar los riesgos de exposición.
El equipo de protección individual (EPI) debe aplicarse rigurosamente durante todas las fases de trabajo. El conjunto de EPI obligatorios incluye:
En situaciones que impliquen una mayor exposición a sustancias químicas o espacios confinados, los trabajadores deben ir equipados con equipos de respiración autónomos (SCBA) o respiradores con suministro de aire, según determine un profesional de seguridad cualificado.
Además, deben seguirse procedimientos adecuados de manipulación y eliminación de agentes desengrasantes y soluciones de decapado para garantizar el cumplimiento de las normas medioambientales y la seguridad de los trabajadores. Deben realizarse auditorías periódicas de seguridad e inspecciones de los equipos para mantener la integridad de todas las medidas de seguridad.