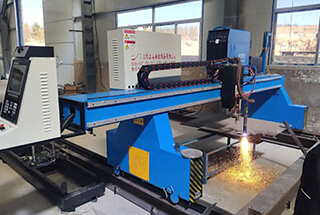
¿Alguna vez se ha preguntado cómo una máquina puede cortar el metal como un cuchillo caliente la mantequilla? Bienvenido al mundo del corte por plasma. En este artículo, descubrirá cómo funciona esta potente tecnología, sus aplicaciones industriales y el papel fundamental de los gases de trabajo. Prepárese para descubrir los secretos de esos cortes suaves y limpios.
El corte por plasma es un método avanzado de procesamiento térmico que emplea un arco de gas ionizado (plasma) a alta temperatura para cortar con precisión materiales conductores, principalmente metales. Este proceso utiliza el intenso calor del arco de plasma, que puede alcanzar temperaturas de hasta 30.000 °C (54.000 °F), para fundir, vaporizar e ionizar rápidamente el metal a lo largo de la trayectoria de corte deseada.
El mecanismo de corte por plasma implica los siguientes pasos clave:
Una máquina de corte por plasma es un sofisticado sistema que aprovecha esta tecnología para procesar diversos materiales metálicos con gran precisión y eficacia. Las modernas máquinas de corte por plasma CNC integran funciones avanzadas como:
El corte por plasma es un método avanzado de procesamiento térmico que aprovecha el intenso calor generado por un arco de plasma de alta temperatura para fundir, vaporizar y eliminar metal a lo largo de la trayectoria de corte (corte). Esta técnica aprovecha la energía cinética del chorro de plasma de alta velocidad para expulsar el material fundido, creando cortes precisos y eficaces. Especialmente eficaz para metales no férreos como el acero inoxidable, aluminio, cobre, titanio y aleaciones de níquel, el corte por plasma destaca allí donde el oxicorte tradicional se enfrenta a limitaciones debidas a las propiedades del material.
Una ventaja clave del corte por plasma es su excepcional velocidad, especialmente al procesar chapas metálicas de espesor fino a medio. Para chapas de acero al carbono normales, el corte por plasma puede alcanzar velocidades de corte de 5 a 6 veces superiores a las de los métodos convencionales de corte por oxígeno. Este proceso produce superficies de corte lisas y limpias con una distorsión térmica mínima y una zona afectada por el calor (HAZ) estrecha, lo que garantiza componentes de alta calidad con una excelente precisión dimensional.
La versatilidad y eficacia de los sistemas de corte por plasma han llevado a su adopción generalizada en diversos sectores industriales. Entre ellos se incluyen:
La evolución de la tecnología de corte por plasma ha revolucionado las características de corte, la calidad y la velocidad del proceso de arco de plasma. Un elemento central de este avance es la selección estratégica del gas de trabajo, que sirve como medio principal para conducir y transferir calor en el arco de plasma, distinto del metal fundido dentro del propio corte.
La elección del gas de trabajo influye significativamente en el rendimiento del corte, afectando a factores como la calidad del corte, la velocidad y la compatibilidad del material. Los gases de trabajo comunes empleados en el corte por arco de plasma incluyen:
Selección del gas plasma
El gas que entra en el arco de plasma se denomina corriente de iones.
Sus principales funciones son las siguientes:
A la luz de los efectos mencionados de los gases iónicos, deben tenerse en cuenta los siguientes requisitos a la hora de seleccionar los gases:
Algunos de los requisitos enumerados anteriormente son contradictorios, por lo que los requisitos principales deben cumplirse en función de las circunstancias específicas. Actualmente, los gases comúnmente utilizados en el plasma corte por arco incluyen el nitrógeno, el argón, el hidrógeno y sus mezclas gaseosas, siendo el nitrógeno el más utilizado.
El nitrógeno es asequible y fácil de conseguir, y su uso es relativamente seguro. Es un gas diatómico que es endotérmico cuando se descompone en la alta temperatura del arco.
N2->2N-1084000j/mol
Cuando se utiliza el corte por plasma, el tipo de gas de trabajo utilizado puede tener un impacto significativo en las características de corte, la calidad y la velocidad. Los gases de trabajo comunes incluyen nitrógeno, argón, hidrógeno y gases mixtos. De ellos, el nitrógeno es el más utilizado debido a su bajo coste y fácil disponibilidad, así como a su capacidad para crear condiciones favorables para el corte de materiales gruesos.
El nitrógeno, al ser un gas diatómico, se descompone en iones de nitrógeno cuando se expone a altas temperaturas en el arco de plasma, liberando el calor absorbido durante la descomposición. Esto permite que el arco de plasma alcance altas temperaturas en un amplio rango de longitudes, haciéndolo ideal para cortar materiales con alta conductividad térmica y poca fluidez de líquidos. La pureza del nitrógeno utilizado en el corte por plasma no debe ser inferior a 99,5% para evitar la oxidación del electrodo y la combustión de la boquilla.
El argón es un gas monoatómico con un bajo potencial de ionización y una combustión por arco estable, pero su elevado coste lo convierte en una opción menos práctica. Añadir hidrógeno al nitrógeno o al argón puede mejorar el efecto de compresión del arco, lo que da lugar a una superficie de corte más estrecha y lisa.
En el corte por plasma aire se utiliza aire comprimido en lugar de gases caros, lo que lo convierte en una opción más rentable. La velocidad de corte con alta corriente es muy superior a la del corte por llama, y la calidad de corte también es muy buena. Para chapas de acero al carbono de menos de 25 mm, la velocidad de corte es de 3 a 5 veces más rápida, y para chapas finas de 5 a 10 mm, es de 6 a 8 veces más rápida. El corte por plasma de aire ha sustituido corte con llama en muchas aplicaciones debido a su rentabilidad y buena calidad de corte.
Diversos parámetros del proceso de corte por arco de plasma afectan directamente a la estabilidad del proceso de corte, la calidad del corte y el efecto.
Las principales especificaciones de corte son las siguientes:
1) Corriente de corte
El parámetro más importante de la velocidad y el corte es el proceso de corte.
Impacto:
Por lo tanto, al preparar el corte por plasma, es importante elegir la corriente de corte adecuada y la boquilla correspondiente para el grosor del material.
Al seleccionar una fuente de alimentación para el corte por plasma, es importante evitar elegir una fuente de alimentación demasiado grande o demasiado pequeña.
Elegir una fuente de alimentación demasiado grande es un despilfarro en términos de reducción de costes, ya que no aprovecha toda la corriente.
Por otro lado, elegir una fuente de alimentación con una corriente demasiado pequeña en un esfuerzo por ahorrar costes tampoco es lo ideal, ya que no cumplirá las especificaciones de corte requeridas y puede causar daños a la propia máquina de corte CNC.
2) Velocidad de corte
La alta temperatura y la energía del arco de plasma determinan la velocidad de corte, que puede seleccionarse dentro del rango óptimo según las instrucciones del equipo o determinarse mediante experimentación. La velocidad de corte puede variar en función del grosor del material, sus propiedades (por ejemplo, punto de fusión, conductividad térmica, tensión superficial tras la fusión) y la calidad deseada.
Manteniendo la calidad del corte, la velocidad de corte debe aumentarse todo lo posible para mejorar la productividad y reducir la deformación y las zonas afectadas por el calor. Si la velocidad de corte no es la adecuada, se producirá el efecto contrario, lo que provocará un aumento de la adherencia de la escoria y una disminución de la calidad del corte.
Las principales manifestaciones son las siguientes:
Si se aumenta moderadamente la velocidad de corte, se puede mejorar la calidad del corte, es decir, el corte se estrecha ligeramente, la superficie de corte es más lisa y se reduce la deformación.
Si la velocidad de corte es demasiado rápida, la energía lineal de corte es inferior al valor requerido, y el chorro en el corte no puede expulsar inmediatamente el material de corte fundido, lo que provoca una gran cantidad de arrastre. Esto provoca que la escoria quede colgando en el corte, y la calidad de la superficie del corte disminuye.
Cuando la velocidad de corte es demasiado lenta, como la posición de corte es el ánodo del arco de plasma, para mantener la estabilidad del arco, el punto anódico o área anódica debe encontrar una corriente conductora cerca de la costura de corte más cercana al arco. Al mismo tiempo, transfiere más calor radialmente al chorro, haciendo que el corte se ensanche. El material fundido a ambos lados del corte se acumula y solidifica en el borde inferior, dificultando su limpieza. Además, el calentamiento y la fusión excesivos hacen que el borde superior del corte se redondee.
A velocidades muy bajas, el corte ancho puede incluso provocar la extinción del arco. Así pues, una buena calidad de corte y la velocidad son inseparables.
3) Atensión rc
Generalmente se considera que la tensión de salida normal de la fuente de alimentación es la tensión de corte para el corte por plasma. La máquina de plasma suele funcionar a una tensión más alta para el arco de plasma, especialmente para el corte por plasma aire.
Cuando la corriente es constante, un aumento de la tensión mejora la entalpía del arco y la capacidad de corte. Una mayor entalpía reduce el diámetro del chorro y aumenta el caudal de gas, lo que se traduce en una mayor velocidad de corte y una mejor calidad de corte.
La tensión en vacío y la tensión de la columna del arco son factores importantes en la fuente de alimentación de corte por plasma. La fuente de alimentación debe tener una tensión en vacío lo suficientemente alta para iniciar fácilmente el arco y mantener una combustión estable del arco de plasma.
La tensión en vacío suele oscilar entre 120 y 600 V, mientras que la tensión de la columna de arco suele ser la mitad de la tensión en vacío. Aumentar la tensión de la columna de arco mejora la potencia del arco de plasma, lo que permite cortar placas metálicas más gruesas a mayor velocidad.
La tensión de la columna del arco puede ajustarse modificando el caudal de gas y aumentando la contracción interna del electrodo, pero no debe superar los 65% de la tensión en vacío para mantener la estabilidad del arco de plasma.
4) Gas de trabajo y caudal
El gas de trabajo en el corte por plasma incluye tanto el gas de corte como el gas auxiliar, y algunos equipos también requieren un gas de arranque de arco.
El gas de trabajo adecuado debe elegirse en función del tipo de material que se va a cortar, su grosor y el método de corte.
El gas de corte no sólo debe formar el chorro de plasma, sino también eliminar eficazmente el metal fundido y los óxidos del corte.
Un caudal excesivo de gas puede restar demasiado calor al arco, lo que provoca un acortamiento de la longitud del chorro y una disminución de la capacidad de corte e inestabilidad del arco.
Si el caudal de gas es demasiado bajo, el arco de plasma puede perder su rectitudEl resultado son cortes menos profundos y un aumento de la formación de escoria.
Es importante que la velocidad de corte y el caudal de gas estén bien adaptados.
La máquina de corte por plasma suele controlar el caudal de gas. La presión de gas utilizada para cortar un determinado espesor de material debe elegirse basándose en los datos del fabricante, pero en aplicaciones especiales puede ser necesario determinarla mediante pruebas de corte reales.
Los gases de trabajo más utilizados son el argón, el nitrógeno, el oxígeno, el aire y el H35 (una mezcla de argón y nitrógeno).
Es poco probable que el argón reaccione con ningún metal a altas temperaturas y produce un arco de plasma estable. La boquilla y el electrodo utilizados tienen una larga vida útil, pero la tensión del arco de plasma de argón es baja, con una entalpía y una capacidad de corte limitadas. Esto se traduce en una reducción del espesor de corte de 25% en comparación con corte por aire.
Además, la tensión superficial del metal fundido es mayor en un entorno protegido con argón, aproximadamente 30% mayor que en un entorno de nitrógeno, lo que provoca más problemas de escoria. Aunque se utilice una mezcla de argón y otros gases, la escoria tiende a adherirse. Como resultado, el argón puro rara vez se utiliza para el corte por plasma.
El hidrógeno se utiliza habitualmente como gas auxiliar en combinación con otros gases. Por ejemplo, el popular gas H35 (35% de volumen de hidrógeno, el resto es argón) es uno de los gases más eficaces en el corte por arco de plasma, que debe gran parte de su potencia al hidrógeno.
El hidrógeno aumenta significativamente la tensión del arco, lo que da lugar a un chorro de plasma con una alta entalpía. Cuando se combina con argón, la capacidad de corte del chorro de plasma aumenta considerablemente.
El argón y el hidrógeno se utilizan habitualmente como gas de corte para materiales metálicos con un espesor superior a 70 mm. Al comprimir aún más el arco de plasma de argón + hidrógeno con un chorro de agua, se puede lograr una mayor eficiencia de corte.
El nitrógeno es un gas de trabajo de uso común. Cuando funciona con una tensión de alimentación más alta, el arco de plasma de nitrógeno tiene mejor estabilidad y mayor energía de chorro que el argón.
Al cortar materiales con alta viscosidad de metal líquido, como acero inoxidable y aleaciones base níquel, la cantidad de escoria en el borde inferior del corte es mínima.
El nitrógeno puede utilizarse solo o en combinación con otros gases. Por ejemplo, el nitrógeno o el aire se utilizan a menudo como gas de trabajo en el corte automático.
Estos dos gases se han convertido en la norma para el corte a alta velocidad de acero al carbono.
En algunos casos, el nitrógeno también se utiliza como gas de arranque para el corte por arco de plasma de oxígeno.
El oxígeno puede aumentar la velocidad de corte del acero con bajo contenido en carbono.
El uso de oxígeno para cortar da lugar a modos de corte imaginativos, como el corte con llama.
Un arco de plasma de alta temperatura y alta energía da como resultado una mayor velocidad de corte, pero debe ir acompañado del uso de electrodos resistentes a la oxidación a alta temperatura y de una protección antiimpacto para prolongar la vida útil del electrodo durante el proceso de arco.
El aire contiene aproximadamente 78% de nitrógeno en volumen, lo que hace del corte por aire un método imaginativo para el corte de escoria y nitrógeno. El aire también contiene aproximadamente 21% de oxígeno.
Debido a la presencia de oxígeno, el corte de acero con poco carbono con aire también es muy rápido. Además, el aire es el gas de trabajo más rentable.
Sin embargo, cuando el corte por aire se utiliza solo, pueden surgir problemas como la adherencia de la escoria, la oxidación del corte y el aumento del nitrógeno.
Además, la corta vida útil del electrodo y la boquilla también afectará a la eficacia del trabajo y aumentará los costes de corte.
5) Altura de la boquilla
La altura de la boquilla se refiere a la distancia entre la cara extrema de la boquilla y la superficie de corte, y es un componente de la longitud total del arco.
Normalmente, la distancia oscila entre 4 y 10 mm.
Al igual que ocurre con el electrodo, es fundamental mantener una altura de boquilla adecuada para maximizar la eficacia del corte por arco de plasma. De lo contrario, la eficiencia y la calidad del corte se verán reducidas o la boquilla de corte puede quemarse.
Dado que el corte por arco de plasma suele utilizar fuentes de alimentación con características externas de corriente constante o caída pronunciada, la corriente permanece relativamente invariable aunque aumente la altura de la boquilla. Sin embargo, esto provoca un aumento de la longitud del arco y el correspondiente aumento de la tensión del arco, mejorando así la potencia del arco. Al mismo tiempo, la mayor longitud de arco expuesta al entorno también se traduce en una mayor pérdida de energía de la columna de arco.
Estos dos factores suelen contrarrestarse mutuamente, reduciendo la energía de corte efectiva y la capacidad de corte. Esto suele indicarse por una fuerza de soplado del chorro de corte debilitada, un aumento de la escoria residual en la parte inferior del corte, un borde superior sobrefundido y redondeado.
Además, el diámetro del chorro de plasma se expande a medida que sale de la boquilla, y el aumento de la altura de la boquilla dará lugar a un corte más ancho. Por lo tanto, es ventajoso elegir la menor altura de boquilla posible para mejorar la velocidad y la calidad del corte.
Sin embargo, si la altura de la boquilla es demasiado baja, puede producirse el fenómeno de doble arco.
Al utilizar una boquilla externa de cerámica, la altura de la boquilla puede ajustarse a cero, con la cara del extremo de la boquilla en contacto directo con la superficie de corte, lo que se traduce en un mejor rendimiento.
5) Potencia del arco
Para conseguir un corte por arco de plasma a alta presión, las boquillas de corte se diseñan con un diámetro menor, una longitud de canal mayor y una refrigeración mejorada, lo que aumenta la corriente que pasa por la sección efectiva de la boquilla, lo que se traduce en un aumento de la densidad de potencia del arco.
Sin embargo, esto también aumenta la pérdida de potencia del arco. Como resultado, la energía efectiva real para el corte es menor que la potencia de salida de la fuente de alimentación, con un índice de pérdida que suele oscilar entre 25% y 50%.
Algunos métodos, como el corte por arco de plasma comprimido con agua, tienen una mayor tasa de pérdida de energía, lo que debe tenerse en cuenta a la hora de diseñar los parámetros del proceso de corte o calcular los costes de corte.
Por ejemplo, la mayoría de las chapas metálicas utilizadas en la industria tienen un grosor inferior a 50 mm. El corte por arco de plasma convencional en este rango de grosor suele dar como resultado un corte con una parte superior ancha y una parte inferior estrecha, lo que disminuye la precisión del tamaño de la incisión y aumenta la cantidad de procesamiento posterior.
Cuando se utiliza el arco de plasma de oxígeno y nitrógeno para cortar acero al carbono, aluminio y acero inoxidable, el perpendicularidad del borde extremo es mejor con el aumento del grosor del material dentro del intervalo de 10 a 25 mm. Sin embargo, cuando el grosor de la placa es inferior a 1 mm, el error del ángulo de incisión aumenta de 3 a 4 grados a 15 a 25 grados a medida que disminuye el grosor de la placa.
Se cree que este fenómeno está causado por un desequilibrio en la entrada de calor del chorro de plasma en la superficie de corte, lo que significa que la liberación de energía del arco de plasma en la parte superior del corte es mayor que en la inferior. Este desequilibrio energético está estrechamente relacionado con diversos parámetros del proceso, como el grado de compresión del arco de plasma, la velocidad de corte y la distancia entre la boquilla y la pieza.
Aumentar el grado de compresión del arco puede hacer que el chorro de plasma de alta temperatura sea más largo y crear una zona de alta temperatura más uniforme, y aumentar la velocidad del chorro puede reducir la diferencia de anchura entre la parte superior e inferior de la incisión.
Sin embargo, la sobrecompresión de la boquilla convencional suele provocar un arco doble, que no sólo consume el electrodo y la boquilla, sino que también disminuye la calidad del corte.
Además, una velocidad de corte demasiado alta y una altura de boquilla demasiado grande pueden provocar un aumento de la anchura de la ranura.
6) Contracción del electrodo
El término "contracción interna" se refiere a la distancia entre el electrodo y la cara final de la boquilla de corte. Mantener una distancia adecuada permite una buena compresión del arco en la boquilla de corte, lo que da como resultado un arco de plasma con energía concentrada y alta temperatura para un corte eficaz.
Si la distancia es demasiado pequeña o demasiado grande, el electrodo se quemará en exceso, la boquilla de corte se quemará y la capacidad de corte se reducirá. La contracción interna típica es de 8-11 mm.
Selección del electrodo y la polaridad:
El electrodo utilizado en el corte por arco de plasma debe tener una baja pérdida por combustión para garantizar la estabilidad del proceso de corte. El tungsteno, que tiene un punto de fusión alto, sigue teniendo una pérdida por combustión importante y no puede garantizar un proceso de corte estable.
La adición de una pequeña cantidad de elementos de bajo potencial de ionización, como el torio, al tungsteno reduce significativamente la pérdida por combustión del electrodo de tungsteno con torio. Esto se debe a que el electrodo de tungsteno con torio tiene una fuerte emisión térmica de electrones, lo que hace que la mayor parte de la energía en la cara del extremo del electrodo escape en forma de electrones, reduciendo así la temperatura de la cara del extremo del electrodo.
Además, el electrodo de tungsteno toriado tiene un efecto débil sobre el oxígeno, reduciendo su pérdida por combustión a alta temperatura. El electrodo de tungsteno con torio utilizado habitualmente contiene entre 1,5% y 2,5% de torio. Sin embargo, el torio es radiactivo, por lo que los electrodos no radiactivos de cerio tungsteno o lantano tungsteno se utilizan ampliamente como alternativas.
En el corte por arco de plasma, se suele utilizar la polaridad directa, conectando la varilla de tungsteno toriado al electrodo negativo y la pieza de trabajo al electrodo positivo. Esto beneficia la emisión térmica de electrones, estabiliza la combustión isoeléctrica del arco y reduce la pérdida por quemado del electrodo.
Además de las técnicas convencionales de corte por plasma, han surgido variaciones avanzadas como el corte por plasma con inyección de agua, que amplían las capacidades de esta versátil tecnología.
Los métodos más utilizados en aplicaciones industriales son el corte por plasma estándar y el corte por plasma aire, cada uno de los cuales ofrece ventajas únicas para materiales y requisitos de corte específicos.
Corte general
El corte por plasma estándar utiliza una única corriente de gas que sirve tanto de gas de trabajo como de medio de corte, eliminando la necesidad de un gas de protección independiente. El proceso comienza con un gas de ionización de bajo flujo para iniciar el arco. Durante el corte, se introduce una corriente de gas de alta velocidad para expulsar el metal fundido de la ranura, garantizando cortes limpios y precisos.
Corte por aire
El corte por plasma de aire emplea aire comprimido como gas primario de ionización y corte, ofreciendo una solución rentable y fácilmente disponible. En este proceso, el aire comprimido se calienta, disocia e ioniza rápidamente dentro del arco de plasma. El plasma de alta temperatura resultante contiene especies reactivas de oxígeno que no sólo cortan el metal por acción térmica, sino que también inducen reacciones exotérmicas de oxidación, aumentando significativamente la velocidad de corte. El plasma de aire totalmente ionizado presenta una entalpía excepcionalmente alta, lo que se traduce en una mayor densidad de energía del arco y velocidades de corte más rápidas en comparación con otros gases.
Este método es especialmente eficaz para cortar acero dulce y acero inoxidable, ya que ofrece un equilibrio entre calidad de corte, velocidad y costes operativos. Sin embargo, para materiales sensibles a la oxidación o cuando se requiere una calidad de filo superior, pueden ser más adecuados gases alternativos o sistemas híbridos.
Equipo de corte
El sistema de corte por plasma consta principalmente de una unidad de suministro de gas, una unidad de refrigeración, una fuente de alimentación y una antorcha de corte. Para las antorchas refrigeradas por agua, se requiere un sistema de circulación de refrigeración adicional.
(1) Unidad de suministro de gas
Para el corte por arco de plasma con aire, el componente principal del sistema de suministro de gas es un compresor de aire con una potencia superior a 1,5 kW. La presión de aire necesaria suele oscilar entre 0,3 y 0,6 MPa. Cuando se necesitan gases alternativos, se pueden utilizar gases embotellados tras pasar por un regulador de presión.
(2) Fuente de alimentación
El corte por plasma utiliza una fuente de alimentación de CC que presenta una característica de caída pronunciada o de corriente constante. Para garantizar una ignición y estabilización eficaces del arco, la tensión en vacío de la fuente de alimentación suele mantenerse aproximadamente al doble de la tensión del arco. Las fuentes de alimentación de corte típicas funcionan con una tensión en vacío de entre 350 y 400 V.
(3) Soplete de corte
El diseño del soplete de corte viene determinado principalmente por su corriente nominal. Las estructuras refrigeradas por aire se emplean normalmente para los sopletes con una corriente nominal inferior a 60 A, mientras que los diseños refrigerados por agua son preferibles para los que superan los 60 A. El electrodo del soplete de corte puede fabricarse con diversos materiales, como tungsteno puro, tungsteno toriado, tungsteno de lantano o electrodos de cobre con inserción de hafnio. Los electrodos de cobre con inserción de hafnio son especialmente apreciados por su durabilidad y capacidad para cortar eficazmente una amplia gama de materiales conductores.
Una mesa de agua debe ser un componente integral de la sección inferior de la instalación de corte por plasma. Durante la operación, la pieza de trabajo debe estar parcialmente sumergida en agua, lo que reduce significativamente la emisión de humos tóxicos, minimizando así los riesgos para la salud de los operadores y el personal cercano.
Debe evitarse estrictamente la exposición visual directa al arco de plasma debido a su intensa radiación ultravioleta e infrarroja. Los operarios deben llevar el equipo de protección individual (EPI) adecuado, incluidas máscaras de soldadura autooscurecibles con el número de tono correcto (normalmente 8-11 para el corte por plasma) y pantallas faciales resistentes a las llamas para evitar daños oculares y quemaduras cutáneas.
Los procesos de corte por plasma generan cantidades considerables de humos metálicos y partículas. Deben implantarse sistemas de ventilación adecuados, como la ventilación de extracción local (LEV) o mesas de tiro descendente, para capturar y filtrar estas emisiones en la fuente. Los operarios deben llevar respiradores aprobados por NIOSH con filtros adecuados (mínimo P100) para protegerse contra la inhalación de sustancias nocivas.
Durante las operaciones de corte por plasma es esencial llevar ropa de protección completa. Esto incluye monos ignífugos, guantes de cuero que lleguen hasta los antebrazos, botas con puntera de acero y mangas protectoras para evitar chispas, salpicaduras de metal fundido y posibles quemaduras.
Aunque los campos electromagnéticos de alta frecuencia generados durante el corte por plasma han suscitado preocupación por los posibles efectos a largo plazo sobre la salud, incluidos los problemas reproductivos, el consenso científico al respecto sigue sin ser concluyente. No obstante, es prudente respetar el principio de exposición ALARA (tan baja como sea razonablemente posible). La aplicación de técnicas adecuadas de conexión a tierra, el mantenimiento correcto de los equipos y la reducción al mínimo del tiempo de exposición innecesario son medidas de precaución recomendadas.
Además, para garantizar un entorno de trabajo seguro en las operaciones de corte por plasma, deben aplicarse controles periódicos de la salud de los operarios, incluidas pruebas audiométricas debido a los elevados niveles de ruido, así como programas exhaustivos de formación en seguridad.
Al considerar la compra de una cortadora de plasma, es importante tener en cuenta el factor presupuesto. Ignorar el presupuesto puede resultar en la elección de un producto que exceda el presupuesto, incluso si cumple con las especificaciones deseadas.
Las cortadoras de plasma se dividen actualmente en dos categorías: nacionales e importadas. Las cortadoras de plasma nacionales tienen tres especificaciones: baja, media y alta, y suelen ser aceptables para la mayoría de los usuarios.
Las cortadoras de plasma importadas son mucho más caras, con precios varias veces o incluso docenas de veces superiores a los de sus homólogas nacionales. Los consumibles, como las boquillas de corte y los electrodos, también son más caros.
Aunque las cortadoras de plasma importadas ofrecen mejores resultados de corte en comparación con los modelos nacionales de las mismas especificaciones, su elevado coste y los gastos continuos pueden dificultar su aceptación por parte de muchas empresas.
Independientemente del tipo de plasma utilizado, éste tiene su propio rango óptimo de tamaño de corte. Es comúnmente conocido que el plasma de baja potencia es el más adecuado para cortar placas delgadas. Sin embargo, si la potencia del plasma es demasiado alta, no es adecuado para cortar chapas finas.
Actualmente, el corte por plasma doméstico de 40-60A se utiliza ampliamente para acero de corte por debajo de 2 mm, mientras que el plasma importado se utiliza ocasionalmente pero en cantidades limitadas debido a su elevado coste. Es importante tener en cuenta que, para chapas de acero de menos de 2 mm, solo son adecuadas las máquinas de corte por plasma de sobremesa de alta velocidad y que otros modelos, como los portátiles y los de tipo pórtico, no lo son.
Si la chapa de acero tiene un grosor superior a 2 mm, no hay restricciones y puede cortarse con máquinas portátiles o de pórtico. Para chapas de acero de entre 2 y 16 mm, pueden utilizarse máquinas portátiles y de pórtico. Sin embargo, para espesores de 25 mm o más, sólo son adecuadas las máquinas de pórtico.
Es ampliamente conocido entre el personal relacionado con el procesamiento de metales que el corte por plasma es el método preferido para corte de acero inoxidable y otros materiales aleados. Por otro lado, las planchas de acero al carbono se cortan principalmente con el método de oxicorte. En consecuencia, cuando se trata de acero inoxidable, es esencial disponer de una máquina de corte por plasma. No se puede cortar con el método de oxicorte.
La calidad del corte depende principalmente de factores como la escoria, la zona afectada por el calor, el filete superior y el ángulo de corte. Entre ellos, el corte por plasma supera al corte por llama en términos de escoria y zona afectada por el calor, ya que no hay escoria residual en el borde de las piezas cortadas por plasma, y la zona afectada por el calor es significativamente menor.
El proceso de plasma implica el uso de gas cargado a alta temperatura para fundir el metal y soplar el material fundido de la superficie de corte. Por otro lado, el oxicorte utiliza la reacción química entre el oxígeno y el acero para cortar, lo que da lugar a la producción de escoria de óxido de hierro.
Debido a estas diferencias tecnológicas, el corte por plasma produce menos escoria y la escoria adherida es más fácil de eliminar. Esta escoria puede eliminarse fácilmente sin necesidad de rectificado o procesamiento adicional, lo que reduce el tiempo necesario para el procesamiento secundario. Esto se traduce en una mayor productividad, ya que se requieren menos operaciones de rectificado.
El tamaño del zona afectada por el calor (HAZ) es un factor crítico en el corte de metales. Cuando el metal se expone a altas temperaturas, puede cambiar su estructura química, haciendo que el borde se oscurezca (adquiera un color de revenido) y se deforme. Si no se elimina el borde calentado, es posible que la pieza no sea apta para una soldadura secundaria.
La velocidad a la que se mueve la antorcha influye directamente en el tamaño de la zona afectada por el calor. El corte por plasma es conocido por su capacidad de corte rápido, que se traduce en una zona afectada por el calor más pequeña, lo que reduce el tiempo necesario para el procesamiento secundario para eliminar el borde calentado.
Los usuarios de oxicorte también pueden fijarse en el color del fuego. Mientras que la zona afectada por el calor no es visible desde el exterior, el color del revenido sí puede verse y puede cambiar el color del metal. Al igual que con la zona afectada por el calor, el corte rápido del plasma da como resultado una zona más pequeña de color del fuego.
Con Corte por plasma CNC y velocidades de perforación hasta 8,5 veces más rápidas que el oxicorte, pueden lograrse importantes aumentos de productividad, por no mencionar el tiempo que se ahorra en el precalentamiento y el procesamiento secundario.
A la hora de evaluar los costes, es esencial distinguir entre los costes operativos y el coste por pieza o por metro. Para determinar el coste real del corte de una pieza, es importante tener en cuenta varios factores, como el coste operativo por metro y el coste por pieza.
El coste de funcionamiento por metro se calcula dividiendo el coste total del corte por hora entre la longitud total que se puede cortar en una hora. Los costes de corte incluyen las piezas consumibles, la electricidad, el gas, la mano de obra y los gastos de sostenibilidad. Por otro lado, el coste por pieza se determina multiplicando la longitud total de corte necesaria para producir una pieza por el coste de funcionamiento por metro.
Dado que el sistema de corte por plasma funciona más rápido, es capaz de producir más piezas en un tiempo determinado, lo que reduce significativamente el coste por pieza. Para el corte manual, es aconsejable calcular el coste de cada trabajo o tarea para evaluar con precisión el ahorro de costes. El coste del trabajo puede calcularse multiplicando el coste de funcionamiento por hora por el tiempo total necesario para completar la tarea.
Al considerar el oxicorte, es necesario tener en cuenta el tiempo de precalentamiento y el tiempo prolongado de procesamiento secundario, ya que se suman al tiempo total necesario para completar el trabajo.
El menor coste por pieza del sistema de plasma se traduce directamente en una mayor rentabilidad. Cada pieza que se corta con este método puede suponer un ahorro de costes, aumentando así el margen de beneficios. Cuanto mayor sea el número de piezas que se pueden cortar por hora, mayor será el aumento global de los beneficios.
Para quienes usan el corte por llama, lleva tiempo y práctica dominar el ajuste de los parámetros químicos de la llama y mantener el equilibrio químico de la misma. Por otro lado, la serie Powermax de Hypertherm funciona con aire comprimido, eliminando la necesidad de mezclar o regular gases.
Si utiliza un sistema de plasma mecánico con CNC o una consola de gas automática, todos los parámetros estarán preajustados por el fabricante y no será necesario ajustar manualmente el gas.
Además, el sistema de plasma manual Powermax incorpora la función de corte por arrastre, que permite al operario mover la antorcha a lo largo de la superficie metálica sin tener que mantener una distancia específica, un aspecto crucial en el corte por llama.
Además, los sistemas de corte por plasma son más fáciles de usar, con sus sencillos dispositivos de control, lo que facilita a los operarios el aprendizaje y el corte según plantillas y patrones, especialmente los que tienen curvas. La facilidad de uso se debe a la falta de ajuste del gas y a la capacidad de corte por arrastre.
El sistema de plasma es capaz de cortar cualquier metal conductor, incluidos el acero inoxidable, el aluminio, el cobre y el latón, mientras que el sistema de máquina de oxicorte se limita a cortar acero de bajo contenido en carbono únicamente mediante la reacción química entre el oxígeno y el hierro. El sistema de plasma también es versátil y puede utilizarse para cepillar, marcar o incluso cortar metal oxidado, pintado o apilado.
Además, el sistema de plasma es capaz de realizar corte de ranuras o corte de malla de acero, que es difícil de lograr para el corte de llama.
El combustible utilizado en el oxicorte es una mezcla de oxígeno y gas, siendo los combustibles más utilizados el acetileno, el propano, el MAPP, el propileno y el gas natural. Entre ellos, el acetileno es el más utilizado, ya que produce una temperatura de llama más alta y una velocidad de perforación más rápida en comparación con los demás. Sin embargo, el acetileno es un gas inestable y muy inflamable que es muy sensible a la alta presión, la temperatura e incluso la electricidad estática. Un explosión de acetileno pueden causar daños materiales de decenas de miles de dólares y provocar lesiones graves a las personas que se encuentren cerca.
En cambio, algunos sistemas de plasma, como la serie Powermax de Hypertherm, funcionan con aire comprimido y no requieren el uso de gases inflamables. Los sistemas de plasma HPR y HSD de Hypertherm también pueden usar una variedad de gases, como aire, oxígeno y nitrógeno, que son más estables y no requieren tratamiento especial.
Hay que tener en cuenta que todas las formas de corte térmico producen algo de olor y ruido, pero corte de agua y los sistemas de corte por plasma CNC pueden reducir significativamente el olor y el ruido producidos. Por el contrario, el corte por llama no debe realizarse bajo el agua debido al riesgo de explosión.
(1) Los operarios deben llevar un equipo de protección individual (EPI) completo que incluya cascos de soldador con niveles de sombra adecuados, guantes resistentes al calor, ropa ignífuga, botas con puntera de acero y protección respiratoria con filtración adecuada para los humos metálicos. La exposición directa al arco de plasma sin la protección ocular adecuada está estrictamente prohibida, y toda la piel debe protegerse de la posible radiación UV y de las salpicaduras de alta temperatura.
(2) Los operarios deben situarse a barlovento de la zona de corte para minimizar la exposición a humos y partículas. Deben emplearse sistemas de ventilación adecuados, como mesas de tiro descendente o sistemas de extracción de humos, para capturar y filtrar eficazmente las emisiones de corte en la fuente.
(3) Antes de la operación, verifique la integridad del sistema eléctrico, incluyendo la correcta conexión a tierra, las conexiones seguras de la antorcha y el aislamiento de todos los componentes conductores. Si se detecta una tensión en vacío excesiva, aplique medidas de seguridad adicionales, como superficies de trabajo aisladas o dispositivos de corriente residual (RCD) en el circuito de alimentación.
(4) Asegurarse de que el generador de alta frecuencia está adecuadamente blindado para evitar interferencias electromagnéticas. Implemente mecanismos automáticos de corte de alta frecuencia que se desactiven inmediatamente después del inicio del arco para minimizar la exposición prolongada a CEM.
(5) Cuando utilice electrodos de tungsteno toriado, siga estrictamente las directrices descritas en el artículo JGJ33-2001, sección 12.7.8, incluidos los procedimientos adecuados de manipulación, almacenamiento y eliminación para mitigar los posibles riesgos radiológicos.
(6) Todo el personal que participe en operaciones de corte debe estar debidamente formado en protocolos de seguridad, incluida la seguridad eléctrica, la protección contra caídas, la detección de gases peligrosos y las técnicas de prevención de incendios. Deben realizarse auditorías de seguridad periódicas y cursos de actualización para mantener un alto nivel de concienciación en materia de seguridad.
(7) Proteger los equipos de soldadura y corte de los factores ambientales almacenándolos en recintos resistentes a la intemperie cuando no se utilicen. Asegúrese de que haya equipos de extinción de incendios fácilmente accesibles y debidamente mantenidos en las inmediaciones de todas las operaciones de corte.
(8) Para trabajos elevados, implemente un sistema integral de protección contra caídas que incluya arneses de cuerpo entero, eslingas y puntos de anclaje seguros. Establezca una guardia de incendios designada con equipos de extinción adecuados y cree un sistema de barrera para contener las chispas y el material fundido. Designe a un supervisor de seguridad cualificado para supervisar las operaciones de alto riesgo y garantizar el cumplimiento de todos los protocolos de seguridad.
1.Montar correctamente el soplete de corte
Asegúrese de que la instalación del soplete de corte es correcta y cuidadosa para garantizar el ajuste correcto de todas las piezas y el flujo adecuado de gas y aire de refrigeración. Coloque todos los componentes sobre un trozo de franela limpia para evitar que se adhiera suciedad.
2.Las piezas consumibles deben sustituirse a tiempo antes de que se dañen por completo.
Las piezas consumibles no deben sustituirse después de estar completamente dañadas, ya que los electrodos, boquillas y anillos vortex muy desgastados pueden producir un arco de plasma incontrolable, que fácilmente puede causar graves daños a la antorcha de corte.
Por lo tanto, cuando se observa por primera vez una disminución de la calidad de corte, las piezas consumibles deben inspeccionarse con prontitud.
3.Limpiar la rosca de conexión del soplete cortador
Al sustituir las piezas consumibles o realizar el mantenimiento y la inspección diarios, es necesario asegurarse de que las roscas internas y externas del soplete de corte estén limpias. Si es necesario, las roscas de conexión deben limpiarse o repararse.
4.Limpiar la superficie de contacto entre el electrodo y la boquilla
En muchos sopletes de corte, la superficie de contacto entre la boquilla y el electrodo es una superficie de contacto cargada. Si hay suciedad en estas superficies de contacto, el soplete de corte no puede funcionar correctamente.
5.Compruebe el gas y el gas refrigerante todos los días
Compruebe diariamente el caudal y la presión del gas y del aire de refrigeración. Si el caudal es insuficiente o hay una fuga, apague la máquina inmediatamente para eliminar el fallo.
6.Evitar daños por colisión del soplete cortador
Para evitar daños por colisión en el soplete de corte, es necesario programar correctamente y evitar la sobrecarga del sistema. La instalación de un dispositivo anticolisión puede evitar eficazmente daños en el soplete de corte durante una colisión.
7.Las causas más comunes de daños en los sopletes de corte
① Colisión del soplete de corte.
② Arco de plasma destructivo debido al daño de los consumibles.
③ Arco de plasma destructivo causado por la suciedad.
④ Arco de plasma destructivo causado por piezas sueltas.
8.Precauciones
① No engrase el soplete de corte.
② No utilice lubricante para juntas tóricas en exceso.
③ No pulverice productos químicos a prueba de salpicaduras mientras la funda protectora esté todavía en el soplete de corte.
④ No utilice el soplete de corte manual como martillo.
1.1 Con el fin de reducir el consumo de energía y mejorar la vida útil de la boquilla y el electrodo, debe utilizarse el corte de "bajo grado" cuando se corten piezas más finas.
1.2 Cuando el interruptor de "selección de espesor de corte" está ajustado en "alto grado", debe utilizarse el tipo de corte sin contacto (excepto en casos especiales), y debe preferirse el soplete de corte por agua.
1.3 Cuando sea necesario cambiar el interruptor de "selección de grosor", deberá desconectarse primero el interruptor de alimentación del host para evitar daños en las piezas.
1.4 Cuando instale, desmonte o traslade el host, desconecte primero la fuente de alimentación para evitar accidentes.
1.5 El interruptor de alimentación de la máquina anfitriona debe apagarse antes de instalar y retirar accesorios y componentes de la misma (como el soplete de corte, el cable de masa de corte, el electrodo, la boquilla, el distribuidor, la tapa de presión, el manguito protector, etc.). Evite abrir repetida y rápidamente el interruptor de la antorcha para evitar dañar el sistema de cebado del arco o los componentes relacionados.
1.6 Cuando es necesario iniciar el corte por arco desde el centro de la pieza, se puede perforar y cortar directamente acero inoxidable de hasta 20 mm de espesor.
El método es el siguiente:
Coloque el soplete de corte en el punto inicial de la costura de corte y sitúe el eje de la boquilla del soplete de corte en un ángulo de unos 75° con el plano de la pieza a cortar. A continuación, encienda el interruptor del soplete de corte para iniciar la perforación del arco.
Al mismo tiempo, ajuste lentamente el ángulo entre el eje de la boquilla y la superficie de la pieza hasta que el corte a través de la pieza se ajuste a 90°.
Después de cortar a través de la pieza de trabajo, se puede cortar normalmente a lo largo de la dirección de la costura de corte.
Sin embargo, si el espesor es superior al indicado anteriormente, es necesario taladrar un pequeño orificio (diámetro no limitado) en el punto de inicio del corte para comenzar el corte por arco desde el orificio pequeño. De lo contrario, es fácil dañar la boquilla del soplete de corte.
1.7 El bastidor principal tiene un ritmo de trabajo continuo de 70% (cuando el interruptor de "selección del grosor de corte" está ajustado a un nivel bajo, el trabajo continuo puede acercarse a 100%).
Si el tiempo de trabajo continuo es demasiado largo y la temperatura del motor principal es demasiado alta, el sistema de protección de temperatura se apagará automáticamente, y deberá enfriarse durante unos 20 minutos antes de poder seguir trabajando.
1.8 Si la presión del aire comprimido es inferior a 0,22 MPa, el equipo entrará inmediatamente en estado de parada de protección.
En este momento, debe revisarse el sistema de suministro de gas. Después de solucionar el problema, la presión puede volver a 0,45 MPa.
1.9 Si la alimentación trifásica de entrada está desfasada, el motor principal no funcionará correctamente y se encenderá la luz roja de "indicación de pérdida de fase" de algunos modelos.
Es necesario eliminar el fallo antes del corte normal.
1.10 Para las máquinas refrigeradas por agua, el depósito de agua debe llenarse con agua del grifo y el enchufe de alimentación de la bomba de agua debe estar enchufado.
1.11 Gire el interruptor de encendido a la posición "start". Si el indicador de "presión de aire insuficiente" está encendido, ajústelo a 0,45MPa según sea necesario, entonces el indicador debería apagarse. La dirección de rotación del ventilador debe coincidir con la dirección de la señal. La dirección de la bomba de agua del enfriador de agua también debe cumplir con los requisitos, de lo contrario, la luz indicadora de "presión de agua insuficiente" estará encendida, y la fase de potencia de entrada debe ser ajustada.
1.12 Según el grosor de la pieza a cortar, gire el interruptor de "selección del grosor de corte" a la posición correspondiente y seleccione el soplete de corte adecuado. El soplete de corte tiene varias especificaciones, de pequeño a grande, según el rango de uso. No exceda el rango de corriente nominal, o se dañará. Coloque el soplete de corte en el punto de inicio del corte de la pieza a cortar y pulse el interruptor del soplete. Si la antorcha no se enciende durante un tiempo, pulse de nuevo el interruptor de la antorcha. El cebado del arco se realiza correctamente y se inicia el corte.
1.13 Cada cuatro a ocho horas de funcionamiento (el tiempo de intervalo depende de la sequedad del aire comprimido), debe aflojarse el tornillo de purga del "reductor de presión del filtro de aire" para drenar el agua acumulada, a fin de evitar que entre agua en exceso en la máquina o en el soplete de corte y provoque averías.
1.14 Cuando el sistema de refrigeración de agua está en mala circulación, el motor principal estará en el estado de parada de protección. En este momento, debe comprobarse y solucionarse según los métodos descritos en los capítulos correspondientes. Después de que la presión del agua vuelva a la normalidad, el soplete de corte refrigerado por agua puede seguir utilizándose.
1.15 Cuando se trabaja en un ambiente frío, es importante tener en cuenta que cuando la temperatura ambiente es inferior al punto de congelación, no se debe utilizar el método de refrigeración por agua para el corte. De lo contrario, el sistema de refrigeración por agua circulante no funcionará correctamente, y el soplete de corte con refrigeración por agua puede resultar dañado.
2.1 Después de conectar el equipo (por favor, preste especial atención al cable de tierra de seguridad), compruebe cuidadosamente y proceda a la siguiente operación si todo es normal.
2.2 Cierre el interruptor de alimentación para suministrar corriente al host. Nota: la corriente alterna de entrada es de unos 65 A, que no debe ser demasiado pequeña; de lo contrario, el host no puede funcionar correctamente. Compruebe que el ventilador del motor principal cumple los requisitos; en caso contrario, ajuste la fase de alimentación de entrada hasta que el sentido de la dirección sea coherente.
2.3 Coloque el "interruptor de encendido" del host en la posición "on". En este momento, la luz del "indicador de alimentación" debe estar encendida. Sin embargo, la luz del "indicador de falta de fase" no debe estar encendida; de lo contrario, la fuente de alimentación trifásica tiene un fenómeno de pérdida de fase, que es necesario comprobar y resolver.
Nota: si la carcasa principal del motor no está correctamente conectada al cable de tierra de seguridad, el indicador de pérdida de fase puede mostrar resultados erróneos.
2.4 Suministre aire al motor principal y coloque los interruptores de "prueba de gas" y "corte" en la posición de "prueba de gas". En este momento, debe salir aire comprimido por la boquilla del soplete de corte. Después de tres minutos de prueba, la luz roja de "presión de aire insuficiente" no debe estar encendida.
Compruebe que el valor de indicación del manómetro del "filtro reductor de aire" no sea inferior a 0,42MPa. De lo contrario, indica que la presión de la fuente de aire es inferior a 0,45MPa o que el caudal es inferior a 300L/min. También puede ser que la tubería de suministro de aire sea demasiado pequeña y la caída de presión del aire sea demasiado grande.
Si existen los problemas anteriores, compruébelos y resuélvalos. Además, preste atención a si el "reductor de presión del filtro de aire" está desequilibrado. Si es así, debe ser reajustado.
El método de ajuste es el siguiente:
Gire la manivela en el sentido de las agujas del reloj para aumentar la presión, de lo contrario disminuirá. Ajuste el valor de indicación del manómetro a 0,42MPa. Si el suministro de aire es normal, la luz indicadora de "presión de aire insuficiente" se apagará. En este momento, coloque el interruptor de "corte" y "prueba de gas" en la posición de "corte".
3.1 Corte manual sin contacto:
3.1.1 Ponga en contacto el rodillo del soplete de corte con la pieza y ajuste la distancia entre la boquilla y el plano de la pieza a 3-5mm (cuando la máquina anfitriona esté cortando, ponga el interruptor de "selección de espesor" en el nivel alto).
3.1.2 Encienda el interruptor de la antorcha de corte para encender el arco de plasma. Después de cortar a través de la pieza a cortar, muévase hacia la dirección de corte a una velocidad media. La velocidad de corte es: cortar a través es la premisa, que debe ser rápido en lugar de lento. Demasiado lento afectará a la calidad de la incisión e incluso romper el arco.
3.1.3 Después del corte, apague el interruptor de la antorcha y el arco de plasma se extinguirá. En este momento, se expulsará aire comprimido para enfriar la antorcha de corte. Tras unos segundos, el chorro se detendrá automáticamente. Retire la antorcha de corte y complete todo el proceso de corte.
3.2 Corte manual por contacto:
3.2.1 Cuando el interruptor de "selección de espesor" está en la marcha baja, se puede utilizar cuando se corta chapa fina con una sola máquina.
3.2.2 Coloque la boquilla de la antorcha en el punto inicial de la pieza a cortar, encienda el interruptor de la antorcha, encienda el arco de plasma, corte a través de la pieza a cortar y, a continuación, desplácese uniformemente a lo largo de la dirección de la costura de corte.
3.2.3 Después del corte, abra y cierre el interruptor de la antorcha. En este momento, el aire comprimido sigue expulsándose. Después de unos segundos, la pulverización se detendrá automáticamente. Retire el soplete de corte y complete todo el proceso de corte.
3.3 Corte automático:
3.3.1 El corte automático es adecuado principalmente para cortar piezas gruesas. Seleccione la posición del interruptor "selección de espesor".
3.3.2 Después de retirar el rodillo del soplete de corte, el soplete de corte está firmemente conectado con la máquina de corte semiautomática, y hay piezas de conexión en los accesorios adjuntos.
3.3.3 Conecte la fuente de alimentación de la máquina de corte semiautomática, e instale el carril guía o la varilla de radio de acuerdo con la forma de la pieza de trabajo (si se utiliza el carril guía para el corte lineal, si se corta el arco circular o circular, se debe seleccionar la varilla de radio).
3.3.4 Si se ha retirado la clavija del interruptor de la linterna, sustituya la clavija del interruptor del mando a distancia (incluida en los accesorios adjuntos).
3.3.5 Ajuste la velocidad de marcha en función del grosor de la pieza. Los interruptores de "marcha atrás" y "marcha adelante" de la máquina de corte semiautomática se colocan en la dirección de corte.
3.3.6 Ajuste la distancia entre la boquilla y la pieza de trabajo a 3~8mm y ajuste la posición central de la boquilla a la franja inicial de la costura de corte de la pieza de trabajo.
3.3.7 Encienda el interruptor del control remoto. Después de cortar a través de la pieza de trabajo, encienda el interruptor de alimentación de la máquina de corte semiautomático para cortar. En la etapa inicial de corte, se debe prestar atención a la costura de corte en cualquier momento y ajustar la velocidad de corte adecuada. Y prestar atención a si las dos máquinas funcionan normalmente en cualquier momento.
3.3.8 Después del corte, apague el interruptor del mando a distancia y el interruptor de alimentación de la máquina de corte semiautomática. Hasta aquí, todo el proceso de corte se ha completado.
3.4 Corte manual de círculos:
En función del material y el grosor de la pieza, seleccione el modo de corte de máquina simple o máquina paralela, y elija el método de corte correspondiente. Apriete el travesaño en el orificio del tornillo del soporte del soplete de corte.
Si la longitud de una pieza no es suficiente, puede conectarse a la longitud de radio requerida de una en una. Después de eso, la distancia entre la punta y la boquilla de la antorcha de corte se puede ajustar de acuerdo con la longitud del radio de la pieza (considerar la anchura de ranurado).
Una vez finalizado el ajuste, apriete el tornillo de fijación superior para evitar que se afloje y afloje el tornillo moleteado de la jaula.
En este punto, la pieza puede cortarse en forma redonda.