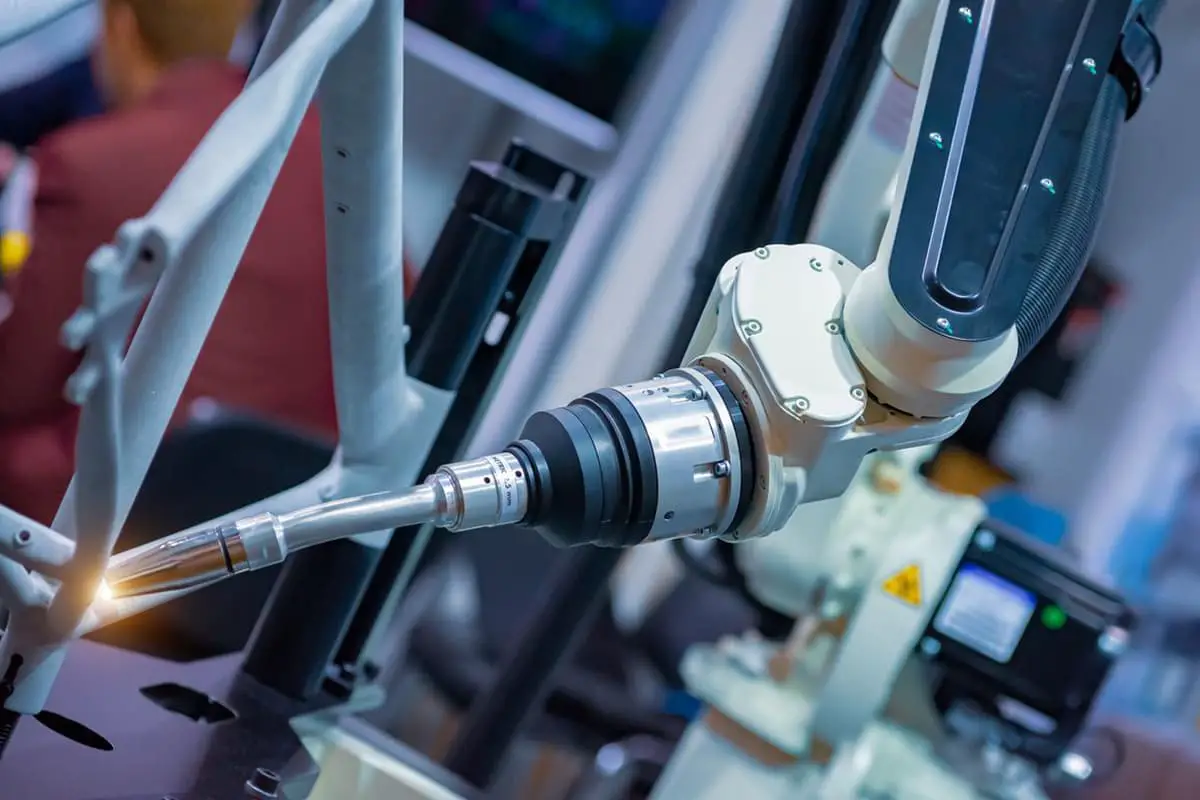
¿Por qué a veces las soldaduras láser desarrollan poros que comprometen su integridad? Este artículo explora las causas de estas pequeñas cavidades y ofrece métodos prácticos para evitarlas. Si comprende cómo influyen factores como la potencia del láser, la velocidad de soldadura y la dinámica del gas en la formación de poros, podrá optimizar su proceso de soldadura para obtener resultados más sólidos y sin defectos. Sumérjase y aprenda estrategias prácticas que mejorarán la calidad y fiabilidad de sus soldaduras láser.
La soldadura láser se ha convertido en una tecnología fundamental en la fabricación moderna, apreciada en todos los sectores por su capacidad para suministrar energía altamente concentrada, una precisión excepcional y una calidad de soldadura superior. Esta avanzada técnica de unión ofrece numerosas ventajas, como zonas mínimas afectadas por el calor, alta velocidad de soldadura y capacidad para unir materiales distintos.
Sin embargo, la sofisticada naturaleza de los sistemas de soldadura láser introduce complejidades potenciales que requieren una cuidadosa consideración. Un funcionamiento incorrecto, unos parámetros de proceso subóptimos o una preparación inadecuada del material pueden provocar defectos en la soldadura, siendo la porosidad un problema especialmente común y complicado.
La porosidad en las soldaduras láser se manifiesta en forma de pequeños huecos o cavidades dentro del cordón de soldadura, lo que puede comprometer la integridad estructural de la unión, su resistencia a la corrosión y su rendimiento general. Para mitigar eficazmente este problema, es esencial adoptar un enfoque sistemático. Esto implica un análisis exhaustivo de la causa raíz para identificar los factores específicos que contribuyen a la formación de porosidad, seguido de la aplicación de soluciones específicas.
Porosidad en soldadura láser se debe al atrapamiento de gas durante el proceso de solidificación del metal de soldadura. La velocidad de enfriamiento del metal de soldadura en la soldadura láser es significativamente más rápida en comparación con la soldadura convencional, lo que dificulta la salida del gas y provoca la formación de poros.
Hay dos causas principales de porosidad en la soldadura láser:
Proceso de formación de la soldadura
Existe una correlación entre el número de poros en una soldadura y el tamaño del potencia del láser utilizado. Un aumento de la potencia del láser se asocia a un aumento del número de poros.
Se cree que el elevado calor generado por el aumento de la potencia del láser hace que el metal fundido alcance temperaturas extremadamente altas, lo que provoca la producción de vapor de metal, vuelve inestable el metal líquido de la piscina de fusión y provoca turbulencias.
Para reducir la formación de poros, se recomienda reducir la potencia del láser y aumentar la velocidad de soldadura. Esto reducirá la producción de vapor de metal y minimizará la formación de poros.
La formación de poros en la soldadura láser puede minimizarse mediante una combinación de principios metalúrgicos y técnicas de soldadura avanzadas. Un método eficaz consiste en introducir un gas activo que se disuelve en el baño de soldadura o reacciona con el metal fundido para formar compuestos estables. Este proceso ayuda a reducir la nucleación y el crecimiento de burbujas de gas que conducen a la porosidad.
La soldadura por láser pulsado es otra técnica sofisticada empleada para controlar el comportamiento de los orificios pequeños y reducir la entrada de gas de protección. Mediante la modulación de la potencia del láser, la soldadura por pulsos crea una serie de soldaduras por puntos superpuestos, lo que permite controlar mejor la entrada de calor y la dinámica del baño de fusión.
Aunque estos métodos reducen significativamente la porosidad, la eliminación completa sigue siendo un reto. En la soldadura láser de penetración profunda, el método de oscilación del haz ha demostrado ser especialmente eficaz para minimizar o eliminar los poros. Esta técnica consiste en la oscilación controlada del haz láser a través del cordón de soldadura.
El movimiento alternativo de la viga sobre la soldadura tiene múltiples propósitos:
Para complementar estas técnicas de soldadura, es fundamental aplicar estrictas medidas de control de calidad. La utilización de herramientas de inspección avanzadas, como medidores de limpieza de superficies y analizadores RFU (unidades de flujo residual), permite una evaluación rápida y precisa de la limpieza de las piezas. Este enfoque basado en datos elimina la subjetividad inherente a los procesos de inspección manual, lo que permite optimizar los procedimientos de limpieza para lograr una mayor eficacia.
Al integrar estos métodos avanzados de soldadura con un control preciso de la limpieza, los fabricantes pueden reducir significativamente la aparición de agujeros de aire en las uniones soldadas por láser. Este enfoque integral no solo mejora la calidad de la soldadura, sino que también minimiza las repeticiones, reduce los costes de producción y mejora la eficiencia general de la fabricación.