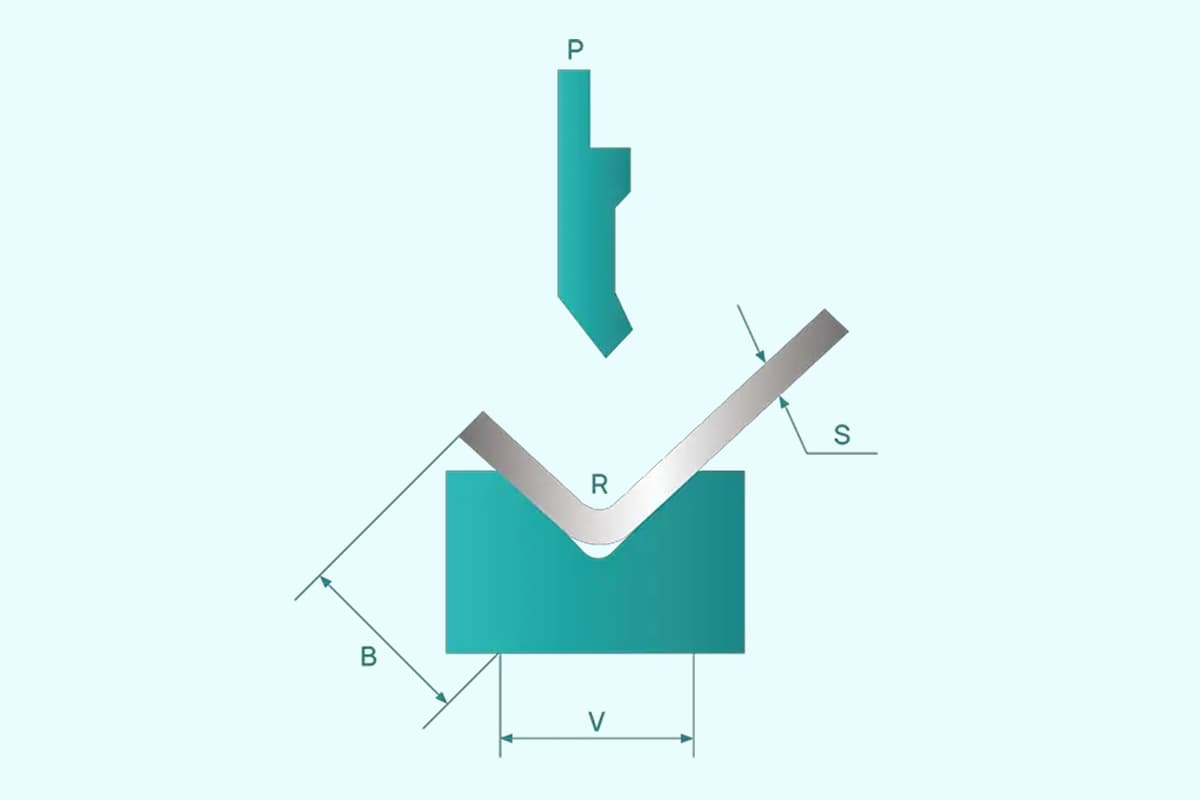
¿Se ha preguntado alguna vez cómo una simple chapa metálica se transforma en un objeto tridimensional complejo? La plegadora, un proceso crucial en la fabricación de metales, es la clave de esta fascinante transformación. En este artículo, nos sumergiremos en el mundo de las plegadoras, explorando los principios, tipos y mecanismos de trabajo que hay detrás de esta tecnología esencial. Prepárese para descubrir los secretos del plegado de precisión.
El plegado con prensa plegadora consiste en la deformación elástica de las chapas metálicas bajo la presión de la matriz superior o troquel inferior de una máquina plegadora, seguida de una deformación plástica.
Al inicio del plegado plástico, la chapa es libre de curvarse. Con la presión de la matriz superior o inferior aplicada a la chapa, ésta se amolda gradualmente a la superficie interior de la ranura en V de la matriz inferior, con el radio de curvatura e fuerza de flexión disminuyendo el brazo.
Esto continúa hasta que las matrices superior e inferior están en pleno contacto al final de la carrera, formando una V, lo que se conoce como plegado.
En general, el plegado con plegadora es una tecnología de proceso que modifica la chapa o el ángulo de la chapa ejerciendo presión sobre ella.
El plegado es una aplicación increíblemente extendida, visible dondequiera que se utilicen chapas metálicas, y podría decirse que toca todos los aspectos de la vida. La finalidad de una prensa plegadora es plegar chapas planas en una variedad de piezas tridimensionales necesarias para aplicaciones prácticas.
¿Cómo se consigue? Colocando la chapa horizontalmente en el troquel inferior, posicionándola mediante un calibrador trasero, y presionando la chapa en el interior del troquel inferior. Ranura en V con la matriz superior para conseguir el ángulo de plegado deseado, la chapa plana se transforma en una pieza tridimensional, como se muestra en la figura siguiente.
Hay muchos aspectos del curvado que merecen atención. Para los productos curvados, es importante tener en cuenta la precisión dimensional, el radio de curvatura, la precisión angular, la rectitud y la sangría.
La rectitud de los productos curvados depende de la rigidez del bastidor de la máquina (diseño del bastidor, elección del acero, etc.), mientras que las hendiduras pueden minimizarse o eliminarse aumentando el radio del hombro de la matriz inferior, utilizando una película antihendiduras o utilizando una matriz inferior sin hendiduras.
En cuanto a las prensas plegadoras, la precisión de los ejes Y y X, la estabilidad, las medidas de seguridad (como la protección antiatrapamiento manual) y la facilidad de manejo (Sistemas CNCTambién hay que tener en cuenta la posibilidad de instalar un eje T de seguimiento y apoyo, una sujeción hidráulica para las matrices superior e inferior, un cambio automático de herramientas y un plegado automatizado.
Prensas plegadoras son herramientas esenciales utilizadas en los procesos de fabricación industrial para doblar y conformar chapas metálicas con precisión y eficacia. Existen principalmente dos categorías de prensas plegadoras: prensa mecánica frenos y los que utilizan transmisión hidráulica.
Frenos de prensa mecánicos: Estas máquinas emplean un sistema de accionamiento mecánico, normalmente accionado por un volante de inercia, para generar fuerza. La fuerza se transfiere al utillaje a través de un mecanismo de manivela o un engranaje excéntrico, dependiendo del diseño de la máquina. Las plegadoras mecánicas funcionan a altas velocidades y ofrecen una precisión excelente, lo que las hace ideales para tareas de plegado sencillas y repetitivas en materiales de grosor fino a medio. Sin embargo, su inconveniente es que suelen requerir un mantenimiento más frecuente y son menos eficientes energéticamente en comparación con las plegadoras mecánicas. prensa hidráulica frenos.
Frenos de prensa hidráulicos: Por otro lado, transmisión hidráulica Las prensas plegadoras utilizan energía hidráulica para generar fuerza de plegado. Estas máquinas están equipadas con cilindros hidráulicosLa fuerza aplicada al utillaje se controla variando la presión del fluido hidráulico. Las prensas plegadoras hidráulicas ofrecen varias ventajas sobre sus homólogas mecánicas:
Aunque tanto las plegadoras mecánicas como las hidráulicas tienen ventajas y aplicaciones únicas, las máquinas hidráulicas son cada vez más populares por su versatilidad, precisión y facilidad de mantenimiento. Independientemente del tipo, la selección de la plegadora más adecuada para cualquier proyecto de fabricación dependerá de factores como los requisitos de material, el volumen de producción y las capacidades de rendimiento deseadas.
La prensa plegadora funciona según un principio fundamental de aplicación de fuerza controlada con precisión. La máquina consta de dos mesas de trabajo, una superior y otra inferior, en las que se fijan las matrices correspondientes. Estas matrices, fabricadas con geometrías específicas, actúan como herramientas de conformado. El movimiento relativo entre las mesas de trabajo se acciona principalmente mediante un sofisticado sistema de transmisión hidráulica, que permite un control preciso de la fuerza y el desplazamiento.
A medida que la matriz superior desciende, aplica una carga concentrada a la pieza colocada en la matriz inferior. Las formas cuidadosamente diseñadas de ambas matrices trabajan de forma concertada para guiar la deformación del material. Esta sinergia entre la geometría de la matriz y la fuerza aplicada permite el plegado controlado de placas metálicas para conseguir los ángulos y perfiles deseados.
El sistema hidráulico no sólo proporciona la potencia necesaria para el plegado, sino que también ofrece un control preciso del proceso de plegado. Las plegadoras modernas suelen incorporar avanzados sistemas CNC, que permiten programar secuencias de plegado con precisión repetible. Esta combinación de diseño mecánico robusto y mecanismos de control precisos hace de la plegadora una herramienta indispensable en la fabricación de chapa metálica, capaz de producir geometrías complejas con gran precisión y consistencia.
El plegado es un proceso fundamental de conformado en frío que transforma la chapa metálica en formas específicas mediante una deformación controlada. Esta técnica basada en la presión, que suele realizarse a temperatura ambiente, es lo suficientemente versátil como para manipular materiales metálicos, no metálicos y compuestos.
El proceso se basa en matrices de plegado de precisión y prensas plegadoras hidráulicas para lograr los resultados deseados. La precisión dimensional de los componentes curvados está garantizada por la sinergia entre las matrices superior e inferior y las capacidades del equipo de curvado.
La secuencia de conformado se desarrolla del siguiente modo: Una chapa de dimensiones predeterminadas se coloca entre las matrices. La matriz superior ejerce una fuerza de flexión calculada, mientras que la inferior proporciona puntos de apoyo que generan una fuerza reactiva. Esta interacción crea un momento de flexión que induce una deformación controlada en la chapa. El ángulo de curvatura final viene determinado con precisión por la profundidad de penetración de la matriz superior en la cavidad de la matriz inferior.
Los principales componentes funcionales de una prensa plegadora CNC incluyen:
Estos tres elementos son fundamentales para determinar la calidad y la precisión de la pieza acabada.
Principios clave para un plegado eficaz con plegadora:
Siguiendo estos principios y aprovechando la precisión de las modernas plegadoras CNC, los fabricantes pueden conseguir plegados uniformes y de alta calidad en una amplia gama de materiales y geometrías.
Durante el plegado, el cilindro de una prensa plegadora puede moverse hacia abajo a distintas velocidades en función de la fase de trabajo para plegar correctamente sin lesionar al operario.
Hay cuatro fases diferentes:
FASE 1 - VELOCIDAD RÁPIDA, hasta la chapa.
Se trata de una velocidad fija que no puede ser controlada por el programa. Las cámaras superiores de los cilindros reciben un gran caudal de aceite a baja presión directamente del depósito, de modo que el ariete cae libremente aprovechando su propio peso.
FASE 2 - VELOCIDAD DE TRABAJO, que se puede configurar en el control numérico.
La velocidad máxima de trabajo permitida es de 10 mm/s, en cumplimiento de la normativa de seguridad vigente. Cuando, durante el descenso a velocidad rápida, el cilindro se aproxima al cambio de velocidad (a unos 20 mm de la chapa). Comienza a reducir la velocidad; esto se consigue ajustando la presión del aceite en las cámaras inferiores de los cilindros.
La velocidad rápida pasa a velocidad de trabajo y las cámaras superiores de los cilindros reciben aceite a alta presión, que proporciona la fuerza necesaria para deformar la chapa. La presión del aceite se ajusta mediante dispositivos reguladores en función de las necesidades de trabajo y de la fuerza máxima de las herramientas utilizadas. La velocidad de trabajo debe ajustarse de modo que el operario pueda mover la chapa sin dañar la superficie.
FASE 3 - BAJA VELOCIDAD (DWELL)
Cuando el cilindro alcanza la posición correcta a lo largo del eje Y para lograr el ángulo requerido, espera unos segundos. Este tiempo puede configurarse en el control numérico y cuanto más largo sea, más cederá la chapa con la consiguiente reducción de su springback.
FASE 4 - VELOCIDAD DE RETORNO
Una vez finalizado el plegado, el cilindro de la plegadora vuelve hacia arriba debido a la presurización de los cilindros inferiores y la despresurización de los cilindros superiores. Si el producto doblado es grande o pesado, la velocidad de retorno debe reducirse para evitar que caiga hacia el operario antes de que éste haya tenido tiempo de agarrarlo.
El operario de la plegadora también debe configurar la carrera Y del cilindro. Para reducir el tiempo de plegado, la velocidad de retorno debe mantenerse al mínimo para facilitar la manipulación y retirada del producto.
La flexión libre, la flexión en tres puntos y la flexión de corrección son algunos ejemplos. La distinción entre estos tres métodos puede verse en el diagrama siguiente.
Flexión libre
El plegado libre, también conocido como plegado por aire, es menos complejo que otros métodos. El sitio ángulo de flexión se controla mediante la profundidad de la matriz superior en la ranura en V de la matriz inferior.
La precisión de las piezas dobladas depende de varios factores, como Y1, Y2 y los moldes y placas superior e inferior del eje V.
Sin embargo, su uso está muy extendido debido a su versatilidad y amplio rango de procesamiento. Se aplica a estructuras de estructura sencilla, gran volumen o rendimiento no demasiado grande.
Flexión en tres puntos
El curvado de tres puntos, también denominado curvado de matriz (bottoming), tiene un ángulo de curvatura que viene determinado por la altura de la cuña en la matriz inferior.
La matriz superior sólo proporciona suficiente fuerza de flexión y elimina el no paralelismo entre las matrices mediante la almohadilla hidráulica del cilindro.
Este método permite fabricar piezas de gran precisión, es decir, con ángulos pequeños y rectitud errores. Se utiliza para estructuras complejas, pequeño volumen y procesamiento en masa.
Corrección Doblado
El doblado de corrección se forma en la cavidad compuesta por las matrices superior e inferior, lo que permite obtener una forma de sección ideal. Sin embargo, requiere una gran fuerza de doblado y repetidas reparaciones del molde, y tiene poca versatilidad de molde.
Este método de curvado se utiliza a menudo cuando existen requisitos especiales o formas de sección especiales que no pueden conseguirse mediante el curvado libre.
Plegado de escenarios
El plegado por etapas consiste en montar una prensa plegadora con diferentes herramientas al mismo tiempo para acelerar el proceso de plegado.
El plegado por etapas es necesario cuando hay que producir un perfil utilizando diferentes juegos de herramientas; los operarios pueden mover la chapa de un juego de herramientas a otro a lo largo del eje Z de la plegadora para realizar los diferentes plegados.
Es importante que el operador:
Curva de radio grande
Las curvas de gran radio pueden obtenerse utilizando portaherramientas de radio, que pueden alojar herramientas de radio de diferentes dimensiones para obtener el radio de curvatura necesario.
Estas herramientas de radio son muy útiles para prensas plegadoras pequeñas y medianas, que tienen mesas demasiado pequeñas para montar las grandes matrices necesarias para obtener plegados de radio grande.
Durante el plegado de gran radio, la chapa cede menos que durante otros tipos de plegado, por lo que el springback es mayor y difícil de calcular.
Por lo tanto, es necesario realizar una prueba de flexión para determinar el valor exacto del springback, que depende del material y de su espesor, así como del radio que se desea obtener.
Además, hay que tener en cuenta que el springback influye en el radio de curvatura interior, por lo que la herramienta de radio a utilizar debe ser menor que el radio de curvatura interior requerido.
En la tabla siguiente se estima el springback medio y la punta de punzón necesaria para obtener diferentes radios de curvatura interna en función de los distintos espesores de chapa:
Una vez determinado el radio, otra dificultad es decidir la anchura de la matriz en V con la que se conseguirá la curvatura correcta. De hecho, es importante encontrar la proporción correcta entre ambos valores.
Las siguientes fórmulas dan una idea del troquel más adecuado para utilizar:.
Durante el curvado de radio grande, la chapa puede salir de la zona de contacto con la herramienta de radio y crear una burbuja de aire en el radio de curvado interno. Esto se conoce como curvado prematuro. Por tanto, el resultado no es muy preciso.
Si necesita un radio interior muy preciso, es mejor utilizar troqueles con insertos de plástico, que empujan la chapa contra la herramienta de radio evitando así un doblado prematuro .
Si se necesitan herramientas de radio seccionado, los portaherramientas tradicionales con orificios roscados para fijar las herramientas de radio no son adecuados. En este caso, los operarios deben elegir herramientas de radio seccionado con un tornillo pasante que también pueda alojar segmentos de herramienta de radio corto.
Otro problema al que tienen que enfrentarse los operarios durante las curvas de gran radio es el de entender el dibujo y definir la distancia entre las galgas traseras (eje x) y el eje de flexión (eje Y).
Operadores de prensas plegadoras A menudo obtienen esta dimensión realizando pruebas con chapa de desecho hasta obtener el perfil deseado. Recomendamos a los diseñadores que indiquen en los planos la dimensión entre el centro de la curva y el punto de contacto de la chapa con las galgas traseras.
Por ejemplo, en el dibujo de la derecha, la dimensión externa de 28 mm es inútil para el operario de la plegadora, que en realidad necesita la dimensión desde el centro de la curva hasta el punto de contacto de la chapa con las galgas traseras (lado ya doblado), que es de 25,2 mm.
Bump Bending
Si el radio interno necesario es muy grande y no puede obtenerse de una sola vez, es posible que los operarios tengan que obtenerlo mediante formación de protuberancias. El conformado por chaflán consiste en doblar con varios golpes de prensa plegadora para obtener una curvatura similar a la del curvado por rodillo.
Las curvas de gran radio realizadas mediante conformado por chaflán son estéticamente bastante pobres, ya que el radio se compone de una serie de lados rectos cortos que son claramente visibles.
Para utilizar el conformado por deformación, hay que tener en cuenta una serie de factores. En primer lugar, el operario debe calcular el número de golpes de plegadora necesarios
y luego, para conocer la distancia y el ángulo entre cada curva, debe:
1. Calcular el desarrollo de la chapa:
2. Una vez definido el número de golpes, determine el espaciado, es decir, la dimensión x de cada curva
3. Una vez definido el número de golpes, calcula el ángulo de cada curva
Si un operario ajusta el control numérico de su plegadora utilizando estos parámetros, obtendrá el radio y el ángulo requeridos.
Durante este tipo de flexiónun operario debe comprobar que la chapa
presiona contra las galgas traseras; si esto no es posible, debe trazar líneas de plegado directamente sobre la chapa y plegar a lo largo de ellas sin utilizar galgas traseras.
Ejes Y1 e Y2: Controla el movimiento del ariete hacia arriba y hacia abajo
Eje V: Controla la compensación de la desviación de la prensa plegadora
Eje X, R, Z1, Z2 y X': Son los ejes de control del sistema de posicionamiento trasero, responsables de controlar la posición de posicionamiento del tope trasero (consulte la definición de cada eje en la ilustración).
Eje T1 y T2: Servo soporte de material (seguidor de chapa). Durante el proceso de plegado, la chapa procesada sigue al soporte, y los seguidores de chapa proporcionan apoyo al material.
Los siguientes ejes son necesarios para cada máquina plegadora: Y1, Y2 y V. Los usuarios pueden seleccionar el tope trasero y los ejes de soporte de material de seguimiento servo en función de las necesidades de las piezas procesadas.
Es importante tener en cuenta que el eje X' no puede seleccionarse por separado y debe utilizarse junto con los ejes Z1 y Z2 para que tenga algún significado práctico.
Eje V es el eje de compensación de la desviación, y existen dos métodos de aplicación.
Uno es el control de posición, que compensa la deformación de deflexión elástica de la máquina durante el plegado proporcionando una cantidad igual de deformación inversa en sus puntos correspondientes basándose en la curva de deformación de deflexión de la mesa de trabajo durante el plegado.
El otro método es el control de presión, que ajusta la presión de múltiples cilindros de compensación de flexión para generar una fuerza de reacción contra la fuerza de flexión en múltiples puntos de la placa vertical del banco de trabajo para evitar la deformación por flexión.
Generalmente se acepta que el control de posición da como resultado una mayor precisión de plegado y se utiliza en máquinas plegadoras de más de 500T. Un diagrama esquemático del principio convexo de la mesa de trabajo se puede ver en la siguiente figura.
La precisión de los ejes Y1, Y2 y V es crucial para el ángulo y la rectitud de las piezas dobladas. Es importante señalar que, en el caso de las chapas finas (<3 mm), la precisión de las piezas dobladas viene determinada directamente por la calidad de la propia chapa, como el tamaño del error de espesor, la uniformidad del material y la dirección de la textura de laminado.
Tras la flexión en forma de V, la superficie interior del pieza de flexión de la pieza experimenta una deformación por compresión, mientras que la superficie exterior experimenta una deformación por tracción.
La mayor deformación se produce en la superficie del material, y disminuye a medida que aumenta el espesor de la placa.
Existe una línea neutra, llamada línea X-X, que no está ni comprimida ni estirada.
Para determinar la posición de la capa neutra, considere lo siguiente:
Si el IR (radio interior) de la pieza es 5 veces mayor que el espesor de la chapa, la capa neutra se coloca en el centro del espesor de la chapa.
Si el IR de la pieza es 5 veces menor que el espesor de la chapa, la posición de la capa neutra se desplaza hacia el interior a medida que disminuye el IR, con lo que el espesor del posición de flexión convirtiéndose en t.
La relación entre el radio de la capa neutra (representado por P) y el IR puede describirse del siguiente modo:
La capa neutra tiene la característica de no estar ni estirada ni comprimida, por lo que su longitud se utiliza como la longitud expandida de la pieza doblada.
El plegado en plegadora consiste en aplicar fuerza para dar forma a la chapa metálica en las geometrías deseadas. Dos conceptos vitales en el plegado con plegadora son el factor K y el eje neutro. Comprender estos elementos es crucial para conseguir operaciones de plegado precisas y repetibles.
Factor K es un valor que representa la posición del eje neutro dentro de la chapa durante el proceso de plegado. El eje neutro no experimenta ni compresión ni alargamiento mientras se dobla la chapa. Con un rango entre 0 y 0,5, el factor K varía según el material y el proceso de plegado. Normalmente, el valor del factor K se sitúa en torno a 0,33, lo que indica que el eje neutro se encuentra aproximadamente a un tercio de la profundidad del material.
Un factor K exacto es esencial para calcular las deducciones por plegado o los márgenes de plegado, garantizando que las dimensiones finales de la pieza plegada cumplan unas especificaciones precisas. Hay varios factores que afectan al factor K, como el tipo de material, el grosor, la dirección del grano y el propio proceso de plegado. Es fundamental tener en cuenta estas variables para obtener resultados precisos y uniformes en las operaciones de plegado.
En eje neutro es una línea imaginaria dentro de la chapa metálica en la que las fibras del material no experimentan tensión durante el proceso de plegado. Situado en paralelo al eje de plegado, separa el material en dos zonas: la sección interior que experimenta compresión y la sección exterior que experimenta tensión. Al conocer el eje neutro, los operarios pueden garantizar un mejor control de las dimensiones resultantes y de la deformación. propiedades del material después de doblarla.
En resumen, el factor K y el eje neutro desempeñan un papel fundamental en las operaciones de plegado de las plegadoras. Determinando con precisión el factor K y comprendiendo el eje neutro, los operarios pueden conseguir plegados precisos y consistentes en piezas de chapa metálica. Es fundamental tener en cuenta el tipo de material, el grosor, la dirección del grano y el proceso de plegado al aplicar estos conceptos para garantizar unos resultados de plegado óptimos.
El plegado en prensa plegadora implica un conocimiento preciso de factores clave como los radios, la deducción de plegado y el springback. Comprender estos conceptos le ayudará a conseguir plegados precisos y uniformes.
Radios se refiere a las distintas medidas del radio de curvatura, un factor esencial para determinar el resultado de una curva. La dirección radio de curvatura es la distancia desde el centro del pliegue hasta el interior del material que se está doblando. La dirección radio de curvatura interior es la distancia desde el punto más interior de la curva hasta la posición inicial del material. Es crucial determinar los radios adecuados para garantizar una curva suave y evitar tensiones o grietas en el material.
Deducción por flexión es otro concepto fundamental en el plegado con plegadora. La página deducción por flexión se refiere a la diferencia de longitud entre una pieza recta de material y la pieza doblada. Para calcular la deducción de la curva, hay que tener en cuenta el radio interior de la curva y el grosor del material. Es necesario calcular con precisión la deducción de curvatura para conseguir curvaturas uniformes con los ángulos de curvatura deseados.
Springback es la tendencia natural de un material a volver a su forma original después de ser doblado. Cuando la plegadora aplica fuerza para doblar un material, las propiedades elásticas del material hacen que se mueva hacia atrás y reduzca el ángulo de plegado. Para contrarrestar el springback, el ángulo de plegado debe ser ligeramente sobre-doblado para compensar este efecto. Los distintos materiales presentan diferentes grados de recuperación elástica, por lo que es crucial tener en cuenta este factor en el proceso de plegado.
Entender y emplear adecuadamente estos conceptos de radios, deducción de doblado y springback conducirá a operaciones de doblado en plegadora con éxito, dando como resultado doblados precisos y consistentes.
La flexión es la deformación de una placa causada por esfuerzos de tracción y compresión en su parte anterior y posterior.
Después de ser doblado hasta el ángulo deseado, el material tenderá a volver a su forma original una vez que se libere la presión, dando lugar a un fenómeno conocido como springback de doblado.
Este springback suele expresarse en términos del ángulo que provoca y está influido por diversos factores como el material, el espesor de la placa, la presión y la radio de curvatura.
Calcular con precisión la cantidad de recuperación elástica por flexión es todo un reto.
La fuerza aplicada durante la flexión y la contrafuerza que crea son diferentes, y una vez eliminada la fuerza de presión, el ángulo disminuirá debido al rebote restaurador.
1) Cuando se utiliza el mismo punzón con el mismo espesor de material, el valor de resiliencia para SPCC es inferior a AL y AL es inferior a SUS.
2) Cuando se utiliza el mismo punzón con el mismo material, una placa más fina tiene más resistencia.
3) Cuando se utiliza el mismo material, el que tiene un IR mayor tiene más resistencia.
4) A mayor fuerza de presión, menor resiliencia.
Método de plegado | Ancho en V | IR | Precisión angular | Características |
---|---|---|---|---|
Flexión por aire | 12T-15T | 2t~2,5t | >±45' | Puede conseguir una gama más amplia de ángulos de curvatura. |
Hasta el fondo | 6T-12T | 1t~2t | ±15'-30' | La mayor precisión de plegado se obtiene con la menor fuerza de prensado. |
Acuñación | 5T(4T-6T) | 0t~0.5t | ±10' | Puede lograr una gran precisión de flexión, pero la fuerza de flexión es muy grande. |
La flexión por aire se refiere a un proceso de plegado donde sólo una parte del material entra en contacto con el utillaje.
Como se muestra en la imagen, el utillaje sólo toca los puntos A, B y C del metal durante el plegado (la punta del punzón y los hombros de la matriz), mientras que el resto del material permanece intacto.
Como resultado, el ángulo real del utillaje pasa a ser intrascendente. El ángulo de curvatura viene determinado por la profundidad a la que desciende el punzón en la matriz; cuanto más desciende el punzón, más agudo es el ángulo de curvatura.
Esto significa que los fabricantes pueden conseguir una amplia gama de ángulos de plegado con un solo juego de utillaje, ya que el ángulo de plegado se controla mediante la profundidad de la carrera y no mediante el propio utillaje.
Sin embargo, es importante tener en cuenta que en el plegado por aire se producirá cierto grado de retroceso por resorte, por lo que el ángulo de plegado deseado puede conseguirse doblando el metal en un ángulo ligeramente más agudo.
Características del curvado por aire:
Véase también:
El "doblado de fondo" se refiere a un método de doblado en el que el punzón se presiona hasta el fondo de la matriz, lo que hace que el material entre en contacto tanto con la punta del punzón como con las paredes laterales de la abertura en forma de V.
Este método permite fabricar piezas con una buena precisión de plegado utilizando menos presión, y es muy utilizado en la industria.
Anchura de apertura en V
La anchura de apertura en V de la matriz puede consultarse en la tabla siguiente:
T | 0.5-2.6 | 3-8 | 9-10 | ≥12 |
---|---|---|---|---|
V | 6T | 8T | 10T | 12T |
IR de la pieza
El radio interior de la pieza se denomina comúnmente IR.
En el proceso de doblado del fondo, el IR es aproximadamente 1/6 de la apertura en V de la matriz (IR = v/6).
Sin embargo, el IR puede variar según los materiales, como el SUS y el Al, que tienen valores IR distintos.
Precisión de plegado inferior
El ángulo después de la flexión inferior se verá afectado por el retorno elástico, por lo que el retorno elástico de flexión se tendrá en cuenta al elegir la flexión inferior.
La solución habitual para obtener el ángulo objetivo es la sobredotación.
Al adoptar el plegado inferior, debe respetarse el principio de utilizar el mismo ángulo tanto para los punzones como para las matrices.
El término "acuñación" procede del proceso de fabricación de monedas, conocido por su gran precisión.
En el proceso de acuñado, se utiliza un tonelaje suficiente de la prensa plegadora para dar forma a la chapa según el ángulo preciso del punzón y la matriz. La chapa no solo se dobla, sino que también se comprime entre el punzón y la matriz.
El acuñado no sólo es preciso, sino que también da como resultado un radio interior (IR) muy pequeño de la pieza. El tonelaje necesario para el acuñado es entre 5 y 8 veces superior al requerido para el plegado inferior.
Anchura de apertura en V
La anchura de la abertura en V necesaria para el acuñado es menor que la necesaria para el plegado inferior y suele ser 5 veces el grosor de la chapa. Esto se hace para reducir el IR de la pieza y minimizar el estampado de la posición IR de la pieza por la punta del punzón. Al reducir el tamaño de la abertura en V, se puede conseguir una mayor presión superficial.
Límite de presión
Debido a la gran presión que se ejerce al doblarlo, el grosor del SPCC no debe superar los 2 mm y el del SUS no debe superar los 1,5 mm. Por ejemplo, 2mm Material SPCC requiere 1100KN de presión para el doblado, lo que excede los 1000KN de presión permitida de algunos utillajes. Tenga en cuenta que los diferentes utillajes tienen diferentes presiones admisibles, por lo que no todos los utillajes pueden utilizarse para doblar material SPCC de 2 mm.
Problemas de acuñación
Debido a la gran fuerza de flexión implicada en el acuñado, es necesario aumentar el tonelaje de la prensa plegadora, lo que puede provocar un grave desgaste del utillaje. Por tanto, para el acuñado solo pueden utilizarse utillajes con una presión admisible elevada.
1. La selección del punzón superior viene determinada por la forma de la pieza.
En términos más sencillos, no debe producirse ninguna colisión entre el punzón y la pieza durante el proceso de plegado.
Para garantizar que el punzón y la pieza no interfieran entre sí, es crucial determinar la secuencia de plegado adecuada.
Al seleccionar la forma del punzón superior, puede utilizarse una figura 1:1 o una ilustración de la sección transversal del punzón superior.
2. La selección de la punta del punzón R
El radio interior (IR) de la pieza viene determinado por la apertura en V de la matriz inferior (IR = V/6), y en la selección del radio de la punta del punzón (R) influyen varios factores.
El IR de la pieza puede calcularse mediante la fórmula IR = V/6, y el radio de la punta del punzón puede ser ligeramente inferior al IR. Sin embargo, en los últimos años se ha recomendado una punta de punzón de 0,6R para el plegado de chapas finas porque:
3. Selección del ángulo de la punta del punzón
Para la acuñación se utiliza un punzón de 90°.
Sin embargo, si el retroceso elástico de la pieza es mínimo al doblar piezas blandas chapa de acero inferior a 2 mm, también puede utilizarse un punzón de 90°.
Para materiales con una cantidad significativa de retroceso elástico (como SUS, Al o chapa media), se puede seleccionar el punzón de 88°, luego el punzón de 84° y, por último, el punzón de 82° en función del nivel de retroceso elástico del material.
Es importante tener en cuenta que el ángulo de la matriz debe coincidir con el ángulo de la punta del punzón.
Radios comunes de la punta del punzón (R):
Los ángulos estándar de la punta del punzón incluyen: 90°, 88°, 86°, 60°, 45°, 30°, etc.
Para un plegado a 90°, el ángulo de punta de punzón utilizado habitualmente es de 88°.
4. La segmentación de punzones y matrices
La resistencia a la tracción del material
La cantidad de resorte de flexión
Método de acuñación
T | 0.5-2.6 | 3-8 | 9-10 | ≥12 |
---|---|---|---|---|
V | 6T | 8T | 10T | 12T |
Confirme la anchura mínima de plegado (b) del producto y asegúrese de que la apertura en V seleccionada cumple este requisito (b=0,7V).
Nota:
Cuanto menor sea la abertura en V, mayor será la presión necesaria para la flexión.
Si ir no se especifica en los planos, utilice el valor R estándar (R=espesor).
Si se especifica ir, se selecciona la apertura en V estrictamente en función de la ir especificada (ir=V/6).
La apertura en V seleccionada puede tener que ser mayor o menor que la anchura de la apertura en V objetivo en función de las condiciones.
Tras determinar la anchura de la abertura en V, realice un cálculo de la fuerza de flexión.
Confirme lo siguiente para la fuerza de flexión calculada:
En el proceso de flexión, debido a la compresión en el interior y al estiramiento en el exterior del material, se produce una extensión parcial del material, denominada índice de alargamiento.
La fórmula para determinar el índice de alargamiento es A + B - longitud de expansión.
La velocidad de alargamiento del material no es constante y se ve afectada por diversos factores, entre ellos:
El índice de alargamiento del material se calcula ahora por ordenador, y el método de cada fabricante está protegido como tecnología patentada y, por tanto, no se divulga.
Sin embargo, durante el procesamiento real, puede haber desviaciones en el cálculo de la tasa de alargamiento, por lo que la medición más precisa debe obtenerse mediante pruebas reales.
C lista de coeficientes correctores:
V | 5T | 6T | 8T | 10T | 12T | 16T |
---|---|---|---|---|---|---|
C | 1.45 | 1.4 | 1.33 | 1.28 | 1.24 | 1.2 |
﹡La fórmula de cálculo anterior de la fuerza de flexión se obtiene mediante experimentos.
También puede consultar este artículo para conocer las 3 formas de calcular la fuerza de flexión necesaria.
A cada utillaje le corresponde un valor de tonelaje máximo admisible. Si la presión aplicada durante el procesamiento supera el valor admisible del utillaje, puede provocar la deformación, el doblado o incluso la rotura del utillaje.
El tonelaje admisible del utillaje se mide en kiloNewtons por metro y se calcula en función de la longitud de las piezas dobladas.
Por ejemplo, si la longitud del producto es de 200 mm y el marcado del utillaje es de 1000KN/M, la fuerza máxima de flexión se calcula de la siguiente manera:
1000KN/M x 0,2M = 200KN/M (20 ton)
Por lo tanto, la fuerza máxima de flexión no debe superar las 20 toneladas.
Tomemos como ejemplo el material HRC47:
El tonelaje máximo admisible calculado (KN/M) puede determinarse mediante la fórmula 9,42 x H^2/L x 10.
Por ejemplo, si H = 15 y L = 30, el tonelaje máximo admisible puede calcularse como:
9,42 x (225/30) x 10 = 9,42 x 7,5 x 10 = 706,5 KN/M = 70 TON/M.
① Ranura de evasión abierta, perforadora o algún otro trabajo adicional.
Agujero abierto y ranura en la bocina
② Cuando el calentamiento y la dureza disminuyen.
Cuando se utiliza la máquina de corte con muela abrasiva para fabricar el cuerno, la dureza del punzón disminuye debido al calor.
③ Hay un poco de agrietamiento
Sigue utilizándose aunque haya pequeñas grietas
La carrera se calcula del siguiente modo:
Ictus = altura de la abertura - altura de la placa intermedia - altura del punzón - altura de la base de la matriz - (altura de la matriz - 0,5V+t)
Por ejemplo:
altura de apertura: 370 mm
Carrera máx: 100 mm
Carrera (sobre fig.) = 370-120-70-75-(26-0,5*8+t) = (83-t) mm
Debe prestarse atención al seleccionar la altura del utillaje:
0,5V< carrera < carrera máx.
Durante la flexión, la capa exterior está sometida a un esfuerzo de tracción, mientras que la capa interior está sometida a un esfuerzo de compresión. Existe una capa de transición, denominada capa neutra, que no está sometida ni a tracción ni a compresión.
Esta capa neutra mantiene la misma longitud antes y después del doblado y sirve de referencia para calcular la longitud de la pieza doblada.
Factores comunes que afectan al coeficiente de flexión:
1. El impacto del grosor de la placa en la carrera
(diferencia de espesor medio de la chapa)< (espesor nominal) < (cambios de espesor de la chapa)
2. La influencia de los cambios del coeficiente del material en la carrera
(Cuanto mayor sea el ángulo de flexión, más susceptible será el cambio de coeficiente)
AL < SPCC < SUS aumentando gradualmente.
No es la misma bobina < Diferencias de material dentro del mismo fabricante < Diferentes fabricantes < La manipulación del material es diferente, aumentando gradualmente en función de la condición.
Independientemente de si usted es un operario de prensa plegadora o el jefe del departamento de producción, es importante comprender la importancia del paralelismo en las piezas de trabajo de plegado. Voy a describirle 4 pasos para ajustar el paralelismo de las piezas de trabajo de plegado.
1) Vuelva a colocar el pistón de la prensa plegadora en la posición inicial y reduzca el valor del manómetro al valor más bajo que apenas mueva el pistón.
2) Coloque dos bloques de igual altura sobre la mesa, a ser posible debajo de los cilindros izquierdo y derecho.
3) Cambiar el sistema hidráulico plegado de chapas ponga la máquina en el modo de "ajuste por impulsos", retire los moldes superior e inferior y cualquier otro accesorio, eleve el bloque mecánico a su posición más alta y desconecte el acoplamiento del engranaje del eje de transmisión del bloque mecánico.
4) Coloque con cuidado el ariete sobre los dos bloques (la cara inferior del molde del ariete debe tocar los bloques).
Las prensas plegadoras son sofisticadas máquinas de conformado de metales que requieren estrictos protocolos de seguridad, especialmente cuando se fabrican diversos productos en cantidades variables. La complejidad de las operaciones aumenta el potencial de accidentes, lo que exige un enfoque integral de la gestión de la seguridad.
Las consideraciones de seguridad en las operaciones de plegado van más allá del propio proceso de plegado e incluyen la instalación de la matriz y los procedimientos de cambio. Los principales riesgos son las lesiones en el punto de operación, como el atrapamiento de los dedos entre el punzón y la matriz o el pellizco de la pieza de trabajo.
Aunque las protecciones físicas, como las cortinas de luz y las vallas protectoras, son esenciales, deben formar parte de una estrategia de seguridad de varios niveles. Los elementos clave de un programa de seguridad eficaz incluyen:
Al integrar estos elementos en una estrategia de seguridad global, los fabricantes pueden reducir significativamente el riesgo de accidentes en las operaciones de plegado, independientemente del volumen de producción o la variedad de productos. La evaluación y mejora continuas de las medidas de seguridad son cruciales para mantener un entorno de trabajo seguro en el dinámico campo del conformado de metales.
Confirmar el tonelaje admisible de las herramientas
Confirmar que el centro del utillaje es consistente antes del cierre del punzón y la matriz.
Al desmontar los utillajes, procure introducir el punzón en la matriz inferior para evitar que el punzón se caiga y se haga daño en el dedo.