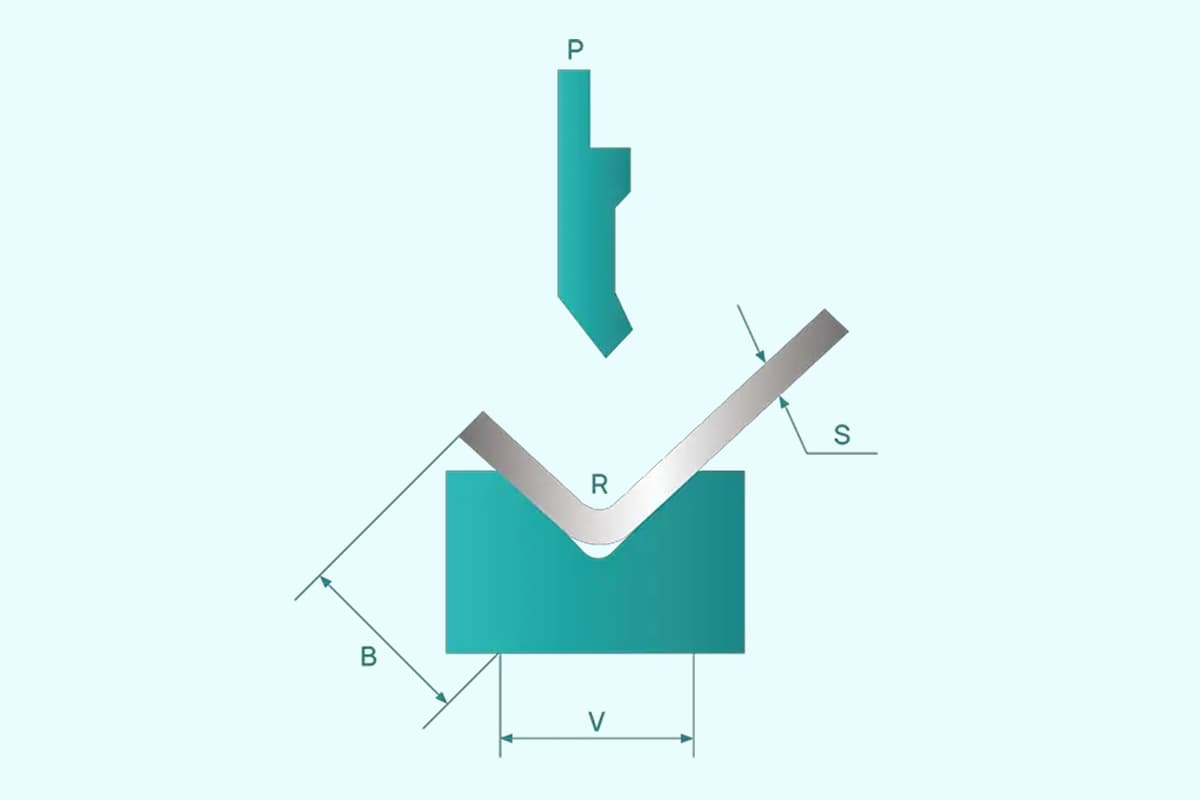
¿Alguna vez se ha preguntado por qué sus dobleces de metal no siempre son perfectos? El secreto está en el abombado de la prensa plegadora, una técnica que garantiza la precisión y la calidad en la fabricación de metal. Este artículo revela cómo los distintos métodos de coronado pueden transformar los resultados de plegado, mejorando la precisión y la uniformidad. Sumérjase y descubra la clave para un trabajo impecable del metal.
El abombado de prensas plegadoras es un proceso crítico en la fabricación de metales que garantiza la precisión y rectitud de las piezas dobladas. Esta técnica compensa la desviación natural que se produce durante el proceso de plegado, mejorando significativamente la calidad y consistencia del producto final.
Cuando una chapa metálica se somete a fuerzas de flexión en una prensa plegadora, la presión aplicada se concentra en el centro de la pieza. Esta concentración provoca una desviación no sólo en el material, sino también en los componentes de la máquina, incluidos el cilindro, la mesa de trabajo y las matrices superior e inferior. El resultado es una distribución desigual de la presión a lo largo de la línea de plegado, lo que puede provocar ángulos de plegado inconsistentes y comprometer la calidad de la pieza.
Para contrarrestar esta deflexión inherente, los ingenieros han desarrollado diversos dispositivos de compensación de la deflexión, siendo el abombamiento de las prensas plegadoras una de las soluciones más eficaces. El principio en el que se basa este sistema es introducir una curvatura calculada en los componentes de plegado que compense con precisión la desviación prevista durante el funcionamiento. Este ajuste preventivo garantiza que, al aplicar la fuerza de plegado, el borde de la matriz permanezca recto y uniforme en toda su longitud, lo que se traduce en plegados siempre precisos.
Existen tres métodos principales de abombado de prensas plegadoras:
Cada método de coronado tiene sus propias ventajas y limitaciones. Factores como el tamaño de la plegadora, la carga de trabajo habitual, la precisión requerida y el presupuesto desempeñan un papel crucial a la hora de determinar la solución de coronado más adecuada para un entorno de fabricación específico.
Comprender y aplicar la técnica de bombeo adecuada es esencial para los fabricantes que desean producir componentes curvados de precisión y alta calidad. No solo mejora la precisión de los doblados, sino que también prolonga la vida útil de las herramientas y reduce el desperdicio de material debido a las incoherencias.
Para aquellos que buscan optimizar sus procesos de fabricación de metales, una exploración más profunda de los métodos de coronado de prensas plegadoras y sus aplicaciones puede conducir a mejoras significativas en la calidad del producto, la eficiencia operativa y las capacidades generales de fabricación.
El coronado es un sofisticado sistema de compensación diseñado para contrarrestar la deformación inherente a las prensas plegadoras durante las operaciones de plegado. En una plegadora típica de 3 metros, la estructura elástica de la máquina puede inducir una desviación de hasta 0,15 mm a lo largo del eje Y en el centro del cilindro.
Para mitigar esta deformación, el coronado genera una fuerza opuesta que garantiza una distribución uniforme de la presión a lo largo de toda la chapa metálica durante el plegado. Este control de precisión evita problemas comunes de plegado, como perfiles curvos y ángulos incoherentes.
El cilindro de la prensa plegadora se acciona mediante dos cilindros de trabajo situados en sus extremos. En consecuencia, la fuerza de plegado se concentra en el centro, provocando que tanto el cilindro como la mesa de trabajo se desvíen junto con las matrices superior e inferior. Esta desviación provoca una distribución no uniforme de la presión a lo largo del borde de la matriz, lo que afecta directamente a la precisión y linealidad de la pieza doblada.
El sistema de coronación, o dispositivo de compensación de la deformación, está diseñado para contrarrestar esta deformación. Está precalibrado para inducir una deformación opuesta a la deflexión inducida por la fuerza en el cilindro, la matriz superior, la mesa de trabajo y la matriz inferior. La magnitud de esta deformación compensatoria se ajusta con precisión a las condiciones reales de trabajo, neutralizando eficazmente la deflexión no deseada.
Al aplicar el abombamiento, se minimiza la deformación relativa entre el cilindro y la mesa de trabajo, lo que da lugar a una distribución más uniforme de la presión en las matrices. Esta mejora incrementa significativamente la calidad del plegado y la precisión dimensional de los componentes de chapa metálica.
Las plegadoras modernas suelen incorporar avanzados sistemas automáticos de coronado. Estos pueden incluir:
En los sistemas de abombado activo, los sensores supervisan continuamente las fluctuaciones de presión y ajustan instantáneamente la compensación, manteniendo un control óptimo de la deformación durante todo el proceso de plegado. Esta adaptación en tiempo real garantiza una calidad de plegado homogénea en distintos grosores y longitudes de material, lo que mejora significativamente la precisión y la eficiencia generales de las operaciones de plegado.
El objetivo principal del abombamiento en las operaciones de plegado es compensar la desviación de la máquina y garantizar un plegado preciso y uniforme en toda la longitud de la pieza. Al proporcionar una curvatura calculada a la bancada o al pistón, el abombamiento mantiene una distribución uniforme de la fuerza en todo el proceso de plegado, contrarrestando la tendencia natural de la máquina a inclinarse bajo carga.
El coronado desempeña un papel crucial en las operaciones de plegado:
Los métodos de coronado abarcan desde ajustes manuales mediante sistemas mecánicos (por ejemplo, cuñas o calces) hasta sofisticados sistemas hidráulicos o electromecánicos controlados por CNC. Las tecnologías de coronado avanzadas ofrecen:
La implantación de un sistema de abombado eficaz es esencial para que los operarios de prensas plegadoras consigan una precisión de plegado, una uniformidad y una eficacia óptimas. No solo mejora la calidad de las piezas, sino que también aumenta la productividad al reducir los tiempos de preparación y minimizar las tasas de desechos, especialmente en aplicaciones de alta precisión o cuando se trabaja con materiales difíciles.
En la fabricación moderna de chapas metálicas, el abombado de las plegadoras es una técnica fundamental para compensar la desviación de la máquina y garantizar un plegado uniforme a lo largo de toda la pieza. En la actualidad, existen tres tipos principales de sistemas de abombado de plegadoras empleados en la industria:
Los fabricantes de prensas plegadoras suelen evitar este método de coronado debido a sus limitaciones. La técnica consiste en mecanizar la mesa de trabajo en forma de arco convexo, con una ligera elevación en el centro, para contrarrestar la desviación causada durante las operaciones de plegado.
Como complemento, la matriz superior está rectificada con precisión y presenta una sutil curvatura en su sección central. Este diseño tiene como objetivo mantener un borde de matriz recto cuando el cilindro experimenta una deflexión hacia arriba, garantizando teóricamente una distribución uniforme de la fuerza de flexión a lo largo de toda la línea de plegado.
Aunque el coronado geométrico ofrece ventajas como la rentabilidad y la relativa facilidad de fabricación, presenta inconvenientes importantes:
El principal reto reside en la falta de flexibilidad del método para adaptarse a las distintas propiedades de los materiales, las variaciones de grosor y los diversos escenarios de flexión. La fabricación moderna exige técnicas de compensación más dinámicas que puedan ajustarse a las condiciones de plegado en tiempo real.
A pesar de su capacidad para lograr cierto grado de compensación de la desviación, la aplicación práctica del abombamiento geométrico resulta muy complicada en la industria metalúrgica de precisión actual. Por ello, en los diseños actuales de prensas plegadoras han cobrado importancia métodos de abombamiento más avanzados y adaptables.
El abombado hidráulico se emplea predominantemente en plegadoras CNC electrohidráulicas síncronas, donde es esencial un control preciso de la compensación. Este método se ve favorecido por su compatibilidad con controladores avanzados como DA52S, DA66T y sistemas similares, lo que permite un ajuste dinámico y preciso durante el proceso de plegado.
El sistema consta normalmente de cuatro cilindros hidráulicos: dos cilindros primarios situados a ambos lados del bastidor de la plegadora y dos cilindros auxiliares situados en el centro. Durante el funcionamiento, los cilindros auxiliares se presurizan con fluido hidráulico, creando una deflexión descendente controlada que compensa la flexión natural de la viga bajo carga.
Una variante avanzada de este sistema incorpora cilindros hidráulicos auxiliares debajo de la mesa de trabajo. Esta configuración genera una fuerza ascendente, creando así un sistema de abombado automático que puede adaptarse en tiempo real a las propiedades variables del material y a los requisitos de plegado.
El mecanismo de compensación de la presión es un sofisticado conjunto formado por varios cilindros de aceite pequeños, una placa base, una placa auxiliar, ejes de pasador y un cilindro de compensación integrado en la mesa de trabajo. Una válvula de alivio proporcional regula el sistema, garantizando un control preciso de la presión. Durante el funcionamiento, la placa auxiliar proporciona apoyo a los cilindros de aceite, que a su vez ejercen la fuerza ascendente suficiente sobre la placa base para contrarrestar la deformación combinada del cilindro y la mesa de trabajo.
El dispositivo de abombado se rige por un sistema de control numérico que calcula la precarga óptima en función de parámetros críticos como el grosor del material, la anchura de apertura de la matriz y la resistencia a la tracción de la pieza. Esto permite una compensación adaptativa en una amplia gama de materiales de chapa y escenarios de plegado.
El abombado hidráulico ofrece ventajas significativas, especialmente en su capacidad para proporcionar una compensación de deformación variable continua con gran flexibilidad. Esto lo hace ideal para operaciones de plegado complejas y espesores de material variables. Sin embargo, es importante tener en cuenta que la complejidad del sistema y su coste inicial relativamente alto pueden ser factores limitantes para algunas aplicaciones.
Para optimizar el uso de la corona hidráulica, los fabricantes deben tener en cuenta:
El coronado mecánico es un método de compensación de la deflexión muy eficaz y rentable, ampliamente adoptado en las plegadoras convencionales. Su popularidad se debe a su sencillez operativa y a su fácil manejo, lo que lo convierte en una herramienta inestimable para los operarios de prensas plegadoras en entornos de fabricación reales.
Esta innovadora técnica de compensación emplea normalmente un mecanismo de cuña oblicua triangular. El principio básico gira en torno al uso de dos bloques de cuña triangulares, cada uno con un ángulo específico α. La cuña superior está constreñida en la dirección X pero puede moverse libremente a lo largo del eje Y. Cuando la cuña inferior se desplaza una distancia △x a lo largo del eje X, la cuña superior es forzada hacia arriba una altura H debido a la fuerza reactiva de la cuña inferior.
En los sistemas de compensación mecánica actuales, se colocan estratégicamente dos placas de apoyo de longitud completa en la mesa de trabajo de la plegadora. Estas placas están interconectadas mediante muelles de disco y pernos de precisión, lo que permite un movimiento relativo controlado. Tanto la placa superior como la inferior incorporan una serie de cuñas oblicuas con pendientes variables. Este diseño permite que un sistema accionado por motor induzca el movimiento relativo entre las placas, generando un perfil curvo ideal compuesto por múltiples posiciones convexas a lo largo de la longitud del freno.
La precisión de este sistema permite ajustar con precisión la distribución de la fuerza de plegado, contrarrestando eficazmente la tendencia natural de la viga de la plegadora a desviarse bajo carga. Al ajustar las posiciones relativas de las cuñas, los operarios pueden conseguir ángulos de plegado uniformes en toda la pieza, incluso cuando trabajan con materiales más largos o gruesos que normalmente plantearían problemas debido a la desviación de la viga.
El coronado es un proceso crítico en las operaciones de plegado que compensa la desviación de la máquina durante el plegado, garantizando ángulos de plegado uniformes en toda la longitud de la pieza. Para configurar el sistema de abombado, los operarios introducen parámetros clave en el sistema de control de la máquina, como el grosor de la chapa, la longitud del material, la apertura de la matriz y la resistencia a la tracción del material. Los avanzados sistemas de control utilizan el análisis de elementos finitos (FEA) para calcular la deflexión precisa de la mesa y el cilindro, determinando la precarga óptima necesaria para cada plegado.
En las plegadoras modernas se emplean tres métodos principales de abombado:
Los métodos manuales y semiautomatizados suelen implicar el calce de la matriz en la bancada o el ajuste de cuñas mecánicas para corregir la alineación y mantener la precisión del plegado. Estos métodos, aunque rentables, pueden llevar mucho tiempo y ser propensos a errores por parte del operario. Los sistemas de coronado CNC programables ofrecen una precisión y eficacia superiores al ajustar automáticamente la curvatura de la bancada o el cilindro en función de la desviación calculada, lo que reduce significativamente el tiempo de preparación y mejora la repetibilidad.
La manipulación y alineación adecuadas de la pieza de trabajo son cruciales para lograr unos resultados de plegado óptimos. La chapa metálica debe colocarse cuidadosamente en la plegadora, asegurándose de que está a escuadra con la matriz y centrada a lo largo de la longitud de plegado. Muchas plegadoras modernas incorporan sistemas de posicionamiento por láser o calibres de retroceso CNC para ayudar en la alineación precisa de la pieza de trabajo.
Antes de iniciar el ciclo de plegado, los operarios deben verificar que el sistema de abombado está correctamente ajustado para el trabajo específico. Esto puede implicar realizar curvas de prueba en material de desecho y medir los ángulos resultantes a lo largo de la longitud de la curva para confirmar la uniformidad.
Durante el proceso de plegado, el cilindro desciende, aplicando fuerza a la pieza. El sistema de abombado compensa dinámicamente la desviación de la máquina ajustando la curvatura de la bancada o del cilindro. Esta compensación garantiza que la fuerza de plegado se distribuya uniformemente a lo largo de toda la pieza, lo que da como resultado ángulos de plegado uniformes y minimiza las variaciones del springback.
Para piezas complejas o requisitos de alta precisión, algunas plegadoras avanzadas incorporan sistemas de control adaptativo y supervisión de la fuerza en tiempo real. Estos sistemas pueden realizar ajustes minuciosos del perfil de abombamiento durante el ciclo de plegado, compensando las variaciones del material o los efectos de la expansión térmica.
En resumen, el proceso de coronado en las operaciones de plegado es una sofisticada interacción entre la configuración de la máquina, las propiedades del material y la compensación dinámica. Al aprovechar los sistemas de abombado avanzados y las técnicas de manipulación de piezas adecuadas, los fabricantes pueden lograr una calidad de plegado superior, reducir las tasas de desecho y mejorar la productividad general en las operaciones de conformado de chapa metálica.
Cuando la prensa máquina de frenado está en funcionamiento, provocará deformaciones, que se deben principalmente a la aplicación de fuerza en ambos extremos de la máquina. Esta fuerza, generada durante el proceso de curvado, provoca deformaciones en el carnero y en la mesa de trabajo, dando lugar a incoherencias entre los dos extremos de la pieza y su ángulo central.
Para analizar la máquina plegadora, se utiliza ampliamente el método de los elementos finitos debido a su rapidez y precisión.
Curva convexa de la máquina plegadora de 100 toneladas y 3 metros obtenida por el método de los elementos finitos:
Existen varios métodos para compensar la deformación por desviación:
La mesa de trabajo tiene un diseño de tablilla de tres capas, con cilindros de aceite compensadores situados por toda la estructura.
Cuando el sistema aplica presión a los cilindros de compensación, empuja hacia arriba la férula central de la férula de tres capas, lo que produce una compensación de la deformación.
Para controlar la posición, se prevé una compensación en el punto correspondiente durante la flexión para contrarrestar la deformación elástica de la máquina.
La compensación mecánica se consigue mediante un grupo de cuñas con planos inclinados, que pueden proporcionar compensación inversa.
Antes de la carga de flexión, estado preconvexo
Después de cargar la flexión, se cambia el estado de compensación real
Animación de simulación de carga de la mesa de trabajo convexa
Modo de conducción
Cuando se trata de curvar piezas, hay dos factores clave que determinan su precisión:
Fig. 1 Esquema de Tx y Ty
Cuanto mayor sea la profundidad de la matriz superior de la plegadora en el troquel inferiormenor es el ángulo de flexión.
Basándose en la figura 2, se puede calcular que al doblar un carbono de 2 mm chapa de acero a 135° utilizando la matriz inferior V12, una desviación de la dirección de la altura de 0,045 mm puede dar lugar a una desviación del ángulo de 1,5°.
Fig. 2 Influencia de la desviación de la dirección de la altura en la desviación del ángulo
Más información:
Cuando se dobla una pieza de trabajo con una plegadora, los largueros superior e inferior pueden sufrir flexiones y deformaciones debido a sus características estructurales y a la fuerza de flexión como se ilustra en la figura 3.
Fig. 3 Diagrama de flexión y deformación de las vigas superior e inferior
Actualmente, hay una inconsistencia en la profundidad de la matriz superior que entra en la abertura de la matriz inferior a lo largo de toda la longitud de la pieza. Esta inconsistencia puede causar una desviación excesiva de la ángulo de flexión de la pieza en toda su longitud.
Esta incoherencia suele dar lugar a una pieza con un ángulo central grande y ángulos más pequeños en ambos extremos, como se muestra en la Fig. 4.
Fig. 4 Diagrama esquemático del ángulo de flexión
Por lo tanto, para garantizar la uniformidad del ángulo de plegado en toda la longitud de la pieza, es necesario introducir un sistema de abombado en la plegadora.
Como se ha mencionado anteriormente, cuando la prensa plegadora dobla la pieza, los largueros superior e inferior, debido a sus características estructurales, sufren una deformación de flexión bajo la fuerza de plegado. Esto puede provocar una desviación excesiva del ángulo de flexión de la pieza en toda su longitud.
Sin embargo, el sistema de abombamiento puede compensar eficazmente la deformación de la plegadora. Utilizando el sistema de abombamiento en la viga superior o inferior, se puede garantizar la consistencia del ángulo de plegado en toda la longitud de la pieza.
El sistema de coronación se divide en dos categorías:
El sistema hidráulico de coronación funciona según el principio de incrustar varios cilindros hidráulicos en la viga inferior de la prensa plegadora. Cada cilindro hidráulico puede controlarse por separado, haciendo que la viga inferior forme un cierto abombamiento, como se ilustra en la figura 1.
En teoría, el uso de más cilindros hidráulicos aumenta el número de puntos de compensación, lo que se traduce en una mayor precisión de compensación.
La coronación hidráulica es un método de compensación discreto incorporado.
Para lograr un efecto de compensación de alta resolución y una elevada precisión de plegado, el número de cilindros hidráulicos y su sistema de control hidráulico deben cumplir requisitos más exigentes, lo que se traduce en una estructura general más compleja y un mayor coste de la prensa plegadora.
No es posible reequipar el sistema de abombado hidráulico en una plegadora existente del cliente.
Fig. 1 Diagrama esquemático del sistema de bombeo hidráulico
El sistema de abombado mecánico utiliza el método de llenado para compensar la viga inferior/troquel inferior. Su principio fundamental consiste en generar diversas curvas de compensación mediante el movimiento mutuo de un par de cuñas de compensación de la desviación, como se demuestra en la figura 2.
Fig. 2 Esquema del sistema de coronado mecánico
Existen muchos tipos de sistemas de coronas mecánicas en el mercado.
Tomemos el ejemplo del banco de trabajo de compensación mecánica de Wila. Pertenece a la categoría de compensación externa relativamente continua. Este sistema puede instalarse directamente en la viga inferior de la prensa plegadora y es apto tanto para prensas plegadoras nuevas como antiguas.
Las curvas de compensación de este sistema pueden ajustarse continuamente para diversas aplicaciones, como se demuestra en la Fig. 3.
Más información:
La longitud de un plegado de chapa afecta en gran medida a su precisión. Cuanto más larga es la chapa, mayor es la fuerza de plegado necesaria, lo que provoca mayores inclinaciones del equipo y deformaciones del carnero, haciendo que la precisión sea más difícil de garantizar. Esta precisión de plegado, incluida la longitud total de plegado, se denomina "precisión de línea recta".
Sin medidas efectivas, cantidades inconsistentes de matriz cóncava entrando en la dirección de longitud completa de la matriz superior de doblado pueden causar que la pieza de doblado tenga un efecto de "barco bello". Para abordar esta cuestión, se utilizó un método de simulación de elementos finitos para analizar la fuerza y el desplazamiento de deformación del pistón. Se extrajo y modificó la curva de compensación de la deformación y se combinó con datos empíricos para diseñar y fabricar un nuevo dispositivo mecánico de compensación de la deformación.
La precisión lineal de las grandes prensas plegadoras puede mejorarse utilizando un motor de accionamiento o un ajuste manual para compensar la desviación en toda la longitud o en parte de ella.
Modelado
En prensa plegadora El ariete está formado por chapas de acero de diversas formas. Durante el proceso de modelado, sólo se tiene en cuenta la estructura principal del ariete, mientras que se ignoran los detalles que tienen poca repercusión en los resultados. Las dimensiones del cuerpo principal son 8000 mm x 2500 mm x 120 mm.
El módulo elástico se fija en 2 x 105 MPa, la relación de Poisson a 0,27 y la densidad a 7,8 x 103 kg/m3. Dadas las características estructurales del ariete, se seleccionó para el análisis un elemento solid95 definido por 20 nodos.
Este elemento tiene la capacidad de adaptarse a modelos de límites curvos y analizar con precisión la deformación elástica del ariete, ya que tiene una orientación 3D arbitraria.
(1) Constraints
En condiciones reales, el ariete está siempre en movimiento. Sin embargo, para realizar un análisis estático del ariete, es necesario simplificar y aproximar las restricciones del ariete. Para ello, se imponen restricciones simétricas en los nodos situados en el plano medio de simetría del ariete.
El ariete se fija conectando el raíl guía del bastidor a su parte trasera, donde se aplica una restricción total. Esto garantiza que el cilindro permanezca en una posición fija durante el análisis.
(2) Load condition
La carga superficial se aplica a la zona de contacto entre la parte inferior del cilindro hidráulico y el bloque del ariete. Como la deformación vertical del bloque del ariete es pequeña en comparación con su longitud total, se considera una pequeña deformación elástica. Como resultado, se aplica una carga uniforme a la superficie de tensión en la parte inferior del bloque del ariete en el modelo.
Para garantizar que la fuerza se transmite uniformemente del bloque del cilindro a la matriz superior, la parte inferior del bloque del cilindro está conectada a la matriz superior mediante un bloque de conexión. Esto garantiza que la carga se distribuya uniformemente y no cause desequilibrios en el sistema.
Extracción y análisis de los resultados de la simulación
En la figura 1 se muestra el diagrama de desplazamiento del bloque del ariete bajo carga. La trayectoria se establece en ANSYS para el procesamiento de resultados, y la deformación curva de deformación de la superficie de tensión en la parte inferior del ariete se extrae y se muestra en la figura 2.
Como se observa en la figura, el desplazamiento máximo aparece en el centro del ariete y disminuye gradualmente hacia ambos lados en forma parabólica. Al mismo tiempo, el desplazamiento de la deformación en cualquier posición a lo largo del longitud de flexión proporcionando datos de apoyo para el diseño de cuñas con diferentes ángulos de disposición para formar la curva de deflexión.
El análisis muestra que cuando una prensa máquina de frenado se carga, su superficie de tensión en el carnero produce una deformación parabólica debido a su propia estructura, lo que da lugar a ángulos de flexión incoherentes de la pieza en toda su longitud. Además, el desgaste local en el matriz dobladora también afecta a la rectitud de la pieza doblada.
En la actualidad, existen dos métodos habituales para resolver este problema. El primero consiste en instalar un cilindro superior en una posición adecuada del cilindro superior o de la mesa de trabajo inferior de la plegadora y controlar la altura de eyección de cada cilindro superior para compensar la deformación. El segundo método consiste en utilizar un dispositivo mecánico de compensación de la deformación en la mesa de trabajo inferior, que compensa la deformación ajustando los bloques de cuña con diferentes ángulos.
El sistema hidráulico cilindro superior es fácil de utilizar y cumple los requisitos generales de precisión de la producción de piezas curvadas. Sin embargo, para piezas de plegado de gran tamaño y alta precisión, se utiliza principalmente el método de compensación de desviación mecánica.
El método tradicional para el abombamiento mecánico implica el ajuste manual del bloque de compensación o la adición de una junta en las zonas desgastadas, lo que lleva mucho tiempo, requiere mucha mano de obra y no es muy eficaz, por lo que resulta difícil garantizar la precisión.
Por otro lado, las plegadoras más avanzadas disponen de mecanismos de compensación de la desviación automáticos o semiautomáticos, como los dispositivos de compensación de tipo cuña y de tipo varilla de tracción, de uso común. El dispositivo de tipo cuña puede asegurar ángulos consistentes y mejorar la precisión de plegado, pero requiere mucho trabajo manual y no es muy eficiente. Por otro lado, el dispositivo de varilla de tracción compensa fácilmente la desviación a lo largo de toda la longitud, pero no resuelve el problema del desgaste local.
Las figuras 3 (a) y (b) muestran dos tipos de dispositivos de compensación de la deformación.
Fig. 3 Dispositivo mecánico común de compensación de desviaciones
Para solucionar el problema del desgaste local, nuestra empresa de moldes diseñó un dispositivo de compensación de la desviación de la cuña de cuatro piezas. Este dispositivo no solo compensa automáticamente toda la desviación de la pieza, sino que también permite el ajuste manual para compensar el desgaste local de la matriz.
La figura 4 es una vista en sección bidimensional del dispositivo, cuyo principio de funcionamiento se describe a continuación:
Fig. 4 Dispositivo de compensación de la deformación de cuatro piezas de tipo cuña
(1) En la base hay una ranura rectangular a lo largo (es decir, longitudinalmente). En esta ranura se distribuyen longitudinalmente grupos impares de mecanismos de cuña. Cada grupo consta de dos pares de cuatro cuñas, es decir, Cuña I, Cuña II, Cuña III y Cuña IV, apiladas de abajo hacia arriba.
(2) En cada grupo de cuñas, el par inferior, Cuña I y Cuña II, forman un mecanismo de ajuste local. Los planos inclinados de cada par coinciden correspondientemente y están dispuestos en dirección transversal.
Los orificios de los tornillos se colocan en el centro de las paredes delantera y trasera del asiento de la base, en correspondencia con el extremo grande de la cuña I. Los pernos de ajuste se instalan en la parte exterior de la pared de la base y cada uno de ellos se extiende hacia el interior de la base para conectar con la cuña I.
Para lograr la compensación local, el perno puede ajustarse manualmente para mover la cuña I hacia delante y hacia atrás (transversalmente), ajustando así la placa de cubierta superior y haciendo que la mesa de trabajo se mueva hacia arriba y hacia abajo.
(3) El par superior, Cuña III y Cuña IV, forman un mecanismo de ajuste integral. Están colocadas longitudinalmente en cada grupo y forman un dispositivo de cuña inclinada de ajuste integral.
Cada par de cuñas III coincide con el plano inclinado de las cuñas IV, con la mayor inclinación situada en el centro de la ranura rectangular de la base. La inclinación disminuye gradualmente hacia los lados izquierdo y derecho de la ranura. Cuando las Cuñas III se mueven equidistantemente a lo largo de la dirección de longitud, la elevación media es sustancial, formando una curva que ajusta la deflexión basada en el movimiento de las Cuñas. Esto realiza la compensación global de la deflexión.
El eje corto de cada cuña IV está dispuesto simétricamente en las paredes laterales delantera y trasera. En la parte superior de las paredes laterales delantera y trasera de la ranura rectangular de la base hay una muesca vertical que corresponde al eje corto. El eje corto de cada cuña IV se desliza en cada ranura de muesca, permitiendo únicamente el movimiento hacia arriba y hacia abajo y asegurando el efecto de elevación de la cuña IV.
(4) Los orificios longitudinales para tornillos se colocan en la cuña III del extremo derecho, mientras que los orificios longitudinales pasantes con la misma línea central que los orificios para tornillos se colocan en la otra cuña III. Se instala un manguito espaciador hueco entre cada par de cuñas III adyacentes. Se instala una barra de tracción en cada cuña III y en cada manguito espaciador hueco. El extremo derecho de la varilla de tracción se enrosca en la cuña III por el extremo derecho. Se instala un tornillo de ajuste en la parte derecha del orificio del tornillo de la cuña III en el extremo derecho, y se instala un motor en el extremo del tornillo de ajuste para poner en marcha el motor, que puede lograr la compensación automática de la desviación general.
La figura 5 muestra un dispositivo de 8 metros de longitud para la compensación de la desviación de la cuña de cuatro piezas de la barra de tracción doble.
Fig. 5 Dispositivo de compensación de deformaciones tipo cuña de doble montante de 8 m
En este post, se simula y analiza la pequeña deformación elástica del carnero en una máquina plegadora, y se extraen los datos de deformación de la superficie de tensión en la parte inferior del carnero.
Basándose en los datos de la experiencia, se ha diseñado un dispositivo de compensación de la desviación de la cuña de cuatro piezas. No solo ajusta automáticamente la compensación global de la desviación de las piezas procesadas, sino que también permite ajustar manualmente la compensación local del desgaste de la matriz.
El dispositivo tiene una estructura bien diseñada, es cómodo y fiable de usar, mejora la calidad y la eficiencia de la producción de chapa metálica piezas curvadas, y proporciona una nueva solución para la compensación de curvado de gran precisión.