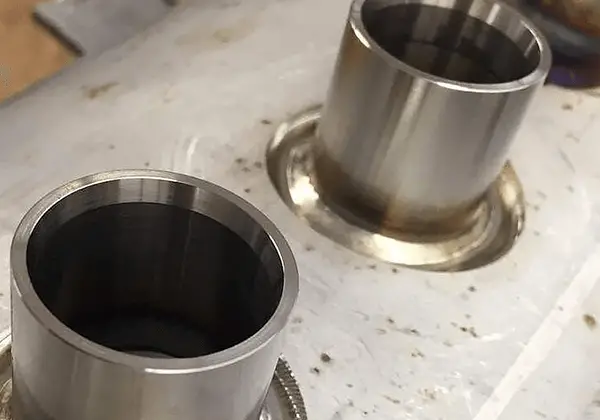
¿Se ha preguntado alguna vez cómo se sueldan a la perfección los depósitos de combustible y los bidones de aceite? La clave está en la soldadura por puntos, una fascinante técnica que utiliza electrodos de rodillo. En este artículo descubrirá cómo funciona este método, sus aplicaciones y las ventajas que ofrece para crear uniones fuertes y estancas en diversas industrias. Prepárese para explorar el fascinante mundo de la soldadura por puntos.
La soldadura por puntos es una técnica avanzada de soldadura por resistencia continua que utiliza un par de electrodos giratorios en forma de rueda en lugar de los electrodos cilíndricos fijos empleados en la soldadura por puntos. A medida que los electrodos ruedan a lo largo de la pieza de trabajo, generan una serie de pepitas de soldadura superpuestas, lo que da como resultado un cordón de soldadura continuo y herméticamente sellado.
Este proceso implica la aplicación tanto de presión como de corriente eléctrica para crear un calentamiento localizado en la interfaz de los materiales que se están uniendo. El calor generado por la resistencia eléctrica de las piezas hace que se fundan y se fusionen, mientras que la presión aplicada garantiza un contacto adecuado y ayuda a expulsar las impurezas de la zona de soldadura.
La soldadura por costura es especialmente eficaz para unir metales de calibre fino, normalmente de 0,5 a 3 mm de grosor. Ofrece varias ventajas, como alta velocidad de producción, excelentes propiedades de estanqueidad y mínima distorsión de las piezas. El proceso puede automatizarse fácilmente e integrarse en líneas de fabricación de gran volumen.
Este método de soldadura tiene una amplia aplicación en la fabricación de contenedores sellados y componentes críticos en diversas industrias. Se utiliza habitualmente en la producción de:
Los últimos avances en la tecnología de soldadura por costura incluyen la integración de sistemas de supervisión en tiempo real para el control de la calidad de la soldadura, el desarrollo de materiales de electrodo especializados para mejorar la durabilidad y la conductividad, y la aplicación de algoritmos de control adaptativos para optimizar los parámetros de soldadura sobre la marcha.
El electrodo utilizado en la soldadura por costura es un rodillo circular con un diámetro que oscila entre 50 y 600 mm, siendo 180-250 mm el rango más común. El grosor del rodillo suele oscilar entre 10 y 20 mm.
Se emplean dos geometrías principales de superficie de contacto: cilíndrica y esférica, con superficies cónicas utilizadas ocasionalmente para aplicaciones especializadas.
Los rodillos cilíndricos pueden presentar chaflanes de doble cara o de una cara, siendo estos últimos especialmente adecuados para la soldadura de bordes plegados. La anchura de la superficie de contacto (ω) varía entre 3 y 10 mm, en función del grosor de la pieza. En el caso de los rodillos esféricos, el radio de curvatura (R) oscila entre 25 y 200 mm.
Los rodillos cilíndricos se utilizan ampliamente en la soldadura de diversos aceros y aleaciones de alta temperatura debido a su versatilidad. Los rodillos esféricos, por su parte, se prefieren para aleaciones ligeras debido a sus características superiores de disipación del calor y distribución uniforme de la presión, lo que minimiza la indentación y reduce el riesgo de deformación del material.
Durante el funcionamiento, los rodillos suelen refrigerarse externamente. Para la soldadura de metales no ferrosos y acero inoxidable, basta con agua limpia del grifo como refrigerante. Cuando se sueldan aceros al carbono, se suele emplear una solución soluble en agua de bórax 5% para evitar la oxidación y prolongar la vida útil del electrodo. En algunos casos, sobre todo en las soldadoras de aleaciones de aluminio, se utilizan sistemas internos de refrigeración por circulación de agua para una gestión más eficaz del calor, aunque esta configuración aumenta considerablemente la complejidad del diseño del electrodo y del sistema en general.
En función de los métodos de rotación y alimentación del rodillo, la soldadura por costura puede dividirse en soldadura por costura continua, soldadura por costura intermitente y soldadura por costura escalonada.
En la soldadura por costura continua, el rodillo gira continuamente y la corriente pasa continuamente a través de la pieza. Este método provoca fácilmente el sobrecalentamiento de la superficie de la pieza y un gran desgaste del electrodo, por lo que no se suele utilizar. Sin embargo, en la soldadura por costura de alta velocidad (4-15 m/min), se forma un punto de soldadura cada medio ciclo de la corriente alterna de 50 Hz, y el cruce por cero de la corriente alterna equivale a un tiempo de reposo, que es similar a la soldadura por costura intermitente siguiente. Por lo tanto, se ha aplicado en la industria de fabricación de cilindros y barriles.
En la soldadura por costura intermitente, el rodillo gira continuamente, y la corriente pasa intermitentemente a través de la pieza de trabajo, formando una costura compuesta de núcleos de fusión superpuestos. Debido a la corriente intermitente, el rodillo y la pieza de trabajo pueden enfriarse durante el tiempo de reposo, lo que puede mejorar la vida útil del rodillo, reducir la anchura de la zona afectada por el calor y la deformación de la pieza de trabajo, y lograr una mejor calidad de soldadura.
Este método se ha utilizado ampliamente en la soldadura por costura de diversos aceros, aleaciones de alta temperatura y titanio aleaciones inferiores a 1,5 mm. Sin embargo, en la soldadura por costura intermitente, el núcleo de fusión cristaliza bajo presión reducida cuando el rodillo abandona la zona de soldadura, lo que puede provocar fácilmente un sobrecalentamiento de la superficie, agujeros de contracción y grietas (como cuando se sueldan aleaciones a alta temperatura).
Aunque el metal fundido del último punto puede rellenar el agujero de contracción del punto anterior cuando la cantidad de solapamiento del punto de soldadura supera 50% de la longitud del núcleo de fusión, el agujero de contracción del último punto es difícil de evitar. Sin embargo, este problema ha sido resuelto por cajas de control de microordenadores desarrolladas en el país, que pueden reducir gradualmente la corriente de soldadura al principio y al final del cordón de soldadura.
En la soldadura por costura escalonada, el rodillo gira intermitentemente, y la corriente pasa a través de la pieza de trabajo cuando está parado. Dado que la fusión y la cristalización del metal se producen cuando el rodillo está parado, se mejoran las condiciones de disipación del calor y de compresión, lo que puede mejorar eficazmente la calidad de la soldadura y prolongar la vida útil del rodillo. Este método se utiliza sobre todo para la soldadura soldadura de aluminio y aleaciones de magnesio.
También puede mejorar eficazmente la calidad de la soldadura de aleaciones de alta temperatura, pero no se ha aplicado en China porque este tipo de máquina de soldadura de CA es poco frecuente.
Cuando se sueldan aluminio duro y diversos metales con un grosor de 4+4 mm o más, debe utilizarse la soldadura por puntos escalonada para aplicar presión de forja a cada punto de soldadura como en la soldadura por puntos, o bien deben utilizarse simultáneamente pulsos calientes y fríos. Sin embargo, este último caso se utiliza raramente.
Según el tipo de articulación, soldadura en ángulo puede dividirse en soldadura de juntas solapadas, soldadura de juntas planas a presión, soldadura de juntas de calce, soldadura de juntas con electrodo de alambre de cobre, etc.
Al igual que la soldadura por puntos, la soldadura solapada soldadura de juntas puede soldarse con un par de rodillos o con un rodillo y un electrodo de núcleo. El solape mínimo de la unión es el mismo que el de la soldadura por puntos.
Además de la soldadura por costura de doble cara comúnmente utilizada, también existen la soldadura por costura simple de una cara, la soldadura por costura doble de una cara y la soldadura por costura circunferencial de pequeño diámetro en la soldadura de juntas solapadas.
La soldadura de cordones circunferenciales de pequeño diámetro puede realizarse con
1) electrodo de rodillos que se desvía del eje de presión;
2) un dispositivo de posicionamiento acoplado a la máquina de soldadura de costura transversal;
3) un electrodo en forma de anillo cuya superficie de la pieza es cónica y cuya punta debe caer en el centro de la soldadura circunferencial de pequeño diámetro para eliminar el deslizamiento del electrodo sobre la pieza.
El solape de la soldadura de juntas planas a presión es mucho menor que el de la soldadura de juntas generales, aproximadamente 1-1,5 veces el grosor de la chapa. Durante la soldadura, la junta se aplana simultáneamente y el grosor de la junta tras la soldadura es de 1,2-1,5 veces el grosor de la chapa.
Por lo general, se utilizan superficies de rodillos cilíndricos que cubren toda la parte solapada de la junta. Para obtener una calidad de soldadura estable, el solape debe controlarse con precisión y la pieza debe sujetarse firmemente o fijarse previamente con una soldadura de localización. Este método puede producir soldaduras de buen aspecto y se utiliza habitualmente para soldar productos como contenedores de alimentos y revestimientos de congeladores fabricados con acero de bajo contenido en carbono y acero inoxidable.
La soldadura de juntas de calce es un método para solucionar la soldadura de costuras de chapas gruesas. Porque cuando el espesor de la placa alcanza los 3 mm, si se utiliza una soldadura de junta solapada convencional, se produce un lento... velocidad de soldaduraSe requiere una gran corriente de soldadura y presión del electrodo, lo que puede provocar el sobrecalentamiento de la superficie y la adherencia del electrodo, dificultando la soldadura. Si se utiliza la soldadura con junta de calce, pueden superarse estas dificultades.
La soldadura de juntas de calce se presenta de la siguiente manera:
En primer lugar, se unen los bordes de las partes del panel y, cuando la unión pasa por el rodillo, se colocan constantemente dos tiras de lámina entre el rodillo y el panel. El grosor de la lámina es de 0,2-0,3 mm y la anchura de 4-6 mm. Dado que la lámina aumenta la resistencia de la zona de soldadura y dificulta la disipación del calor, es beneficiosa para la formación del núcleo fundido.
Las ventajas de este método son:
Las desventajas son: elevados requisitos de precisión para la unión; durante la soldadura, la lámina debe colocarse entre el rodillo y la pieza, lo que aumenta la dificultad de la automatización.
La soldadura de juntas con electrodo de alambre de cobre es un método eficaz para resolver la adherencia del revestimiento al rodillo en la soldadura de juntas de chapas de acero revestidas. Durante la soldadura, el alambre de cobre redondo se introduce continuamente entre el rodillo y la chapa.
El alambre de cobre tiene forma de espiral, pasa continuamente por el rodillo y se enrolla en otra bobina. El revestimiento sólo se adhiere al alambre de cobre y no contamina el rodillo.
Aunque el alambre de cobre debe desecharse después de su uso, no existe ningún otro método de soldadura por costura que pueda sustituirlo para las chapas de acero revestidas, especialmente las chapas de acero estañado. Dado que el valor de desecho del hilo de cobre es similar al del alambre de cobre, el coste de la soldadura no es elevado. Este método se utiliza principalmente para la fabricación de latas para alimentos.
La formación de una junta de soldadura a tope es esencialmente la misma que la de una soldadura por puntos y, por lo tanto, los factores que afectan a la calidad de la soldadura son similares. Los principales factores son la corriente de soldadura, la presión del electrodo, el tiempo de soldadura, el tiempo de pausa, la velocidad de soldadura y el diámetro del rodillo.
El calor necesario para formar un baño de fusión en una unión soldada a tope se genera por la resistencia de la zona de soldadura al flujo de corriente, que es la misma que en la soldadura por puntos. En determinadas condiciones, la corriente de soldadura determina la penetración de la fusión y el solapamiento del baño de fusión. Para soldar aceros con bajo contenido en carbono, la penetración media de la fusión del baño de fusión es de 30-70% del espesor de la chapa, siendo óptima de 45-50%. Para obtener una soldadura a tope estanca al gas, el solapamiento del baño de fusión no debe ser inferior a 15-20%.
Cuando la corriente de soldadura supera un determinado valor, el aumento de la corriente sólo incrementará la penetración de la fusión y el solapamiento del baño de fusión sin mejorar la resistencia de la unión, lo que resulta antieconómico. Si la corriente es demasiado alta, también puede provocar defectos como una excesiva indentación y quemaduras.
Debido a la importante desviación causada por el solapamiento de los charcos fundidos en una soldadura a tope, la corriente de soldadura suele aumentar en 15-40% comparación con la soldadura por puntos.
El efecto de la presión del electrodo sobre el tamaño del baño de fusión en soldadura a tope es la misma que en la soldadura por puntos. Una presión excesiva del electrodo provocará una indentación excesiva y acelerará la deformación y el desgaste del rodillo. Una presión insuficiente es propensa a la porosidad y puede hacer que el rodillo se queme debido a una resistencia de contacto excesiva, acortando su vida útil.
En la soldadura a tope, el tamaño del baño de fusión se controla principalmente mediante el tiempo de soldadura, y el solapamiento se controla mediante el tiempo de enfriamiento. A velocidades de soldadura bajas, una relación de tiempo de soldadura/tiempo de pausa de 1,25:1-2:1 puede lograr resultados satisfactorios. Cuando aumenta la velocidad de soldadura, aumenta la distancia entre soldaduras, por lo que debe aumentarse la relación para lograr el mismo solapamiento. Por lo tanto, a velocidades de soldadura más altas, la relación entre el tiempo de soldadura y el tiempo de pausa es de 3:1 o superior.
La velocidad de soldadura está relacionada con el metal que se suelda, el grosor de la chapa y los requisitos de resistencia y calidad de la soldadura. Cuando se sueldan aceros inoxidables, aleaciones de alta temperatura y metales no ferrosos, suelen utilizarse velocidades de soldadura más bajas para evitar salpicaduras y obtener soldaduras de alta densidad. A veces, la soldadura a tope por etapas se utiliza para realizar todo el proceso de formación del baño de fusión mientras el rodillo está parado. La velocidad de soldadura de este tipo de soldadura a tope es mucho menor que la de la soldadura a tope intermitente.
La velocidad de soldadura determina el área de contacto entre el rodillo y la placa, así como el tiempo de contacto entre el rodillo y el área de calentamiento, lo que afecta al calentamiento y enfriamiento de la unión. Cuando aumenta la velocidad de soldadura, debe incrementarse la corriente de soldadura para obtener suficiente calor. Una velocidad de soldadura excesiva puede provocar el quemado de la superficie de la placa y la adherencia del electrodo, lo que limita la velocidad de soldadura incluso con refrigeración externa por agua.
La optimización de los parámetros del proceso de soldadura de cordones es fundamental para conseguir soldaduras de alta calidad y está influida principalmente por las propiedades del material, el espesor, los requisitos de calidad y el equipo disponible. Aunque la selección inicial de parámetros puede basarse en datos recomendados, el ajuste fino mediante pruebas experimentales es esencial para obtener resultados óptimos.
La selección del tamaño de los rodillos sigue principios similares a la selección de electrodos en la soldadura por puntos. Las tendencias recientes favorecen los rodillos estrechos con superficies de contacto de 3-5 mm de ancho, lo que ofrece varias ventajas:
La interacción entre la geometría del rodillo y las características de la pieza influye significativamente en la calidad de la soldadura:
1. Diámetro del rodillo y curvatura de la placa:
2. Configuraciones asimétricas:
Cuando se sueldan espesores o materiales distintos, los métodos de corrección del desplazamiento de la pepita son análogos a las técnicas de soldadura por puntos. Las estrategias incluyen:
Para la soldadura por costura de chapas con diferencias de espesor significativas:
Optimizar los procesos de soldadura por costura:
Seleccionando y ajustando cuidadosamente estos parámetros, los fabricantes pueden conseguir soldaduras de alta calidad con una resistencia, aspecto y eficacia óptimos en una amplia gama de aplicaciones y combinaciones de materiales.
Los principios de diseño de las uniones a tope por soldadura de ranura comparten similitudes con los de las uniones solapadas y la soldadura por puntos, con notables excepciones en las técnicas de soldadura de ranura aplanada y soldadura de ranura calzada. Sin embargo, una distinción clave radica en el utillaje: a diferencia de los electrodos de soldadura por puntos, las ruedas de rodadura de soldadura por costura no pueden personalizarse en formas especializadas. Esta limitación obliga a tener muy en cuenta la accesibilidad de las ruedas de rodadura a la hora de diseñar estructuras para la soldadura de ranuras.
Cuando se sueldan piezas con radios de curvatura pequeños, surge un reto importante. El radio mínimo alcanzable de la rueda de rodadura interior está limitado, lo que puede provocar un desplazamiento hacia el exterior del baño de soldadura fundido. En casos extremos, este desplazamiento puede provocar una fusión inadecuada de la placa exterior, comprometiendo la integridad de la unión.
Para mitigar estos problemas, es aconsejable evitar diseños con radios de curvatura excesivamente pequeños siempre que sea posible. Sin embargo, en aplicaciones en las que son inevitables tanto las secciones planas como las zonas con radios de curvatura muy pequeños, como en la fabricación de depósitos de combustible de motocicletas, se pueden emplear parámetros de soldadura adaptativos. En concreto, aumentar la corriente de soldadura al procesar las secciones de radio pequeño puede ayudar a garantizar una fusión y penetración completas.
Este enfoque adaptativo es especialmente factible con los modernos sistemas de soldadura controlados por microordenador, que ofrecen un ajuste preciso y en tiempo real de los parámetros de soldadura. Estos sistemas pueden programarse para modular automáticamente la corriente, el voltaje y la velocidad de desplazamiento en función de la geometría que se esté soldando, garantizando una calidad de soldadura uniforme en distintos contornos.
Además, para obtener resultados óptimos en la soldadura de ranuras de geometrías complejas:
Integrando estas consideraciones de diseño y las tecnologías avanzadas de soldadura, los fabricantes pueden conseguir uniones a tope por soldadura de ranura de alta calidad en una amplia gama de geometrías, garantizando tanto la integridad estructural como la calidad estética del producto final.
El acero con bajo contenido en carbono es el mejor material para la soldadura por costura debido a su excelente soldabilidad. Para la soldadura de solapes de acero con bajo contenido en carbono, pueden adoptarse esquemas de alta velocidad, velocidad media y baja velocidad, en función de la finalidad y el uso.
Las condiciones de soldadura para el cordón de solape de aceros con bajo contenido en carbono se indican en la tabla siguiente. Cuando se desplaza manualmente la pieza, se suele utilizar una velocidad media para facilitar la alineación con la posición de soldadura predeterminada.
Cuando se suelda automáticamente, pueden utilizarse velocidades altas o superiores si la capacidad de la máquina de soldar es suficiente. Si la capacidad de la máquina de soldar no es suficiente y no se puede garantizar una anchura y profundidad de fusión elevadas sin reducir la velocidad, se deberá utilizar una velocidad baja.
Condiciones de soldadura de cordones de acero con bajo contenido en carbono
Espesor de la placa(mm) | Tamaño del rodillo(mm) | Fuerza del electrodo(KN) | Solapamiento mínimo(mm) | Soldadura de alta velocidad | Soldadura a velocidad media | Soldadura a baja velocidad | |||||||||||||
---|---|---|---|---|---|---|---|---|---|---|---|---|---|---|---|---|---|---|---|
Mínimo b | Estándar b | Máximo B | mínimo | estándar | Mínimo b | Estándar b | Tiempo de soldadura (semana) | Tiempo de descanso (semana) | Corriente de soldadura (KA) | Velocidad de soldadura (cm/min) | Tiempo de soldadura (semana) | Tiempo de descanso (semana) | Corriente de soldadura (KA) | Velocidad de soldadura (cm/min) | Tiempo de soldadura (semana) | Tiempo de descanso (semana) | Corriente de soldadura (KA) | Velocidad de soldadura (cm/min) | |
0.4 0.6 0.8 1.0 1.2 1.6 2.0 2.3 3.2 | 3.7 4.2 4.7 5.1 5.4 6.0 6.6 7.0 8.0 | 5.3 5.9 6.5 7.1 7.7 8.8 10.0 11.0 13.6 | 11 12 13 14 14 16 17 17 20 | 2.0 2.2 2.5 2.8 3.0 3.6 4.1 4.5 5.7 | 2.2 2.8 3.3 4.0 4.7 6.0 7.2 8.0 10 | 7 8 9 10 11 12 13 14 16 | 10 11 12 13 14 16 17 19 20 | 2 2 2 2 2 3 3 4 4 | 1 1 1 2 2 1 1 2 2 | 12.0 13.5 15.5 18.0 19.0 21.0 22.0 23.0 27.5 | 280 270 260 250 240 230 220 210 170 | 2 2 3 3 4 5 5 7 11 | 2 2 2 3 3 4 5 6 7 | 9.5 11.5 13.0 14.5 16.0 18.0 19.0 20.0 22.0 | 200 190 180 180 170 150 140 130 110 | 3 3 2 2 3 4 6 6 6 | 3 3 4 4 4 4 6 6 6 | 8.5 10.0 11.5 13.0 14.0 15.5 16.5 17.0 20.0 | 120 110 110 100 90 80 70 70 60 |
Las dos tablas siguientes muestran las condiciones de soldadura para la soldadura eléctrica continua de solapado y la soldadura de banda por retroceso de aceros con bajo contenido en carbono.
Condiciones de soldadura de cordones de acero con bajo contenido en carbono
Espesor de la placa(mm) | Solapamiento(mm) | Fuerza del electrodo(KN) | Corriente de soldadura(KA) | Velocidad de soldadura(cm/min) |
0.8 1.2 2.0 | 1.2 1.8 2.5 | 4 7 11 | 13 16 19 | 320 200 140 |
Condiciones de soldadura para la soldadura de banda de refuerzo de acero con bajo contenido en carbono
Espesor de la placa(mm) | Fuerza del electrodo(KN) | Corriente de soldadura(KA) | Velocidad de soldadura(cm/min) |
0.8 1.0 1.2 1.6 2.3 3.2 4.5 | 2.5 2.5 3.0 3.2 3.5 3.9 4.5 | 11.0 11.0 12.0 12.5 12.0 12.5 14.0 | 120 120 120 120 100 70 50 |
Al soldar temple rápido acero aleadoTambién es necesario un tratamiento térmico posterior a la soldadura para eliminar la estructura de enfriamiento, que debe realizarse utilizando un método de calentamiento de doble pulso.
Durante la soldadura y el templado, la pieza no debe moverse y debe realizarse en una máquina de soldadura de costura escalonada. Si no se dispone de este equipo y sólo se dispone de máquina de soldadura de costura intermitente, se recomienda utilizar un tiempo de soldadura más largo y condiciones más débiles. La siguiente tabla muestra los valores recomendados para soldar acero aleado templado utilizando estas condiciones.
Condiciones de soldadura del cordón de acero de baja aleación
Espesor de la placa(mm) | Anchura del disco(mm) | Fuerza del electrodo(KN) | Tiempo (semana) | Corriente de soldadura(KA) | Velocidad de soldadura(cm/min) | |
---|---|---|---|---|---|---|
soldadura | cesar | |||||
0.8 1.0 1.2 1.5 2.0 2.5 | 5-6 7-8 7-8 7-9 8-9 9-11 | 2.5-3.0 3.0-3.5 3.5-4.0 4.0-5.0 5.5-6.0 6.5-8.0 | 6-7 7-8 8-9 9-10 10-12 12-15 | 3-5 5-7 7-9 8-10 10-13 13-15 | 6-8 10-12 12-15 15-17 17-20 20-24 | 60-80 50-70 50-70 50-60 50-60 50-60 |
Nota: El diámetro de laminación es de 150-200 mm.
Cuando la costura soldadura de acero galvanizado placas, debe prestarse atención para evitar que se agriete y dañe la estanqueidad de la soldadura. La razón del agrietamiento es que el zinc que queda en el zona de fusión y se difunde en la zona afectada por el calor hace que la junta se vuelva frágil, quedando sometida a tensiones. El método para evitar el agrietamiento consiste en seleccionar los parámetros de proceso correctos.
Las pruebas han demostrado que cuanto más pequeño es el penetración de la soldadura (10-26%), menores serán los defectos de fisuración. Una alta velocidad de soldadura del cordón puede provocar una mala disipación del calor, un sobrecalentamiento de la superficie y una mayor profundidad de fusión, lo que puede causar fácilmente grietas. Generalmente, bajo las condiciones de asegurar el diámetro de fusión y la resistencia de la unión, se debe seleccionar, en la medida de lo posible, una corriente pequeña, una velocidad de soldadura baja y una fuerte refrigeración externa por agua.
Los rodillos pueden utilizar fácilmente la transmisión de la rueda de acero de la flor para ajustar el tamaño y limpiar la superficie de los rodillos en cualquier momento. La siguiente tabla muestra las condiciones de soldadura para galvanizado. chapa de acero soldadura por costura.
Condiciones de soldadura para diversos tipos de soldadura de cordones de chapa de acero galvanizado
Tipo y grosor del revestimiento | Grosor del tablero(mm) | Anchura del disco(mm) | fuerza del electrodo(KN) | Tiempo (semana) | corriente de soldadura(KA) | Velocidad de soldadura(cm/min) | |
---|---|---|---|---|---|---|---|
soldadura | cesar | ||||||
Galvanizado en caliente(15-20um) | 0.6 0.8 1.0 1.2 1.6 | 4.5 5.0 5.0 5.5 6.5 | 3.7 4.0 4.3 4.5 5.0 | 3 3 3 4 4 | 2 2 2 2 1 | 16 17 18 19 21 | 250 250 250 230 200 |
Top de plata(2-3um) | 0.6 0.8 1.0 1.2 1.6 | 4.5 5.0 5.0 5.5 6.5 | 3.5 3.7 4.0 4.3 4.5 | 3 3 3 4 4 | 2 2 2 2 1 | 15 16 17 18 19 | 250 250 250 230 200 |
Fosfato de calcio tratado antioxidante chapa de acero | 0.6 0.8 1.0 1.2 1.6 | 4.5 5.0 5.0 5.5 6.5 | 3.7 4.0 4.5 5.0 5.5 | 3 3 3 4 4 | 2 2 2 2 1 | 14 15 16 17 18 | 250 250 250 230 200 |
Las condiciones de soldadura para el primer tipo de soldadura del cordón de chapa de acero galvanizado se muestran en la tabla siguiente:
Condiciones de soldadura para el soldeo por costura de chapas de acero aluminizado
Espesor de la placa(mm) | Anchura del disco(mm) | Fuerza del electrodo(KN) | Tiempo (semana) | Corriente de soldadura(KA) | Velocidad de soldadura(cm/min) | ||
---|---|---|---|---|---|---|---|
soldadura | cesar | ||||||
0.9 1.2 1.6 | 4.8 5.5 6.5 | 3.8 5.0 6.0 | 2 2 3 | 2 2 2 | 20 23 25 | 220 150 130 |
Para el segundo tipo de chapa de acero aluminizado, al igual que en la soldadura por puntos, la corriente debe aumentarse en 15-20%. Debido al fenómeno de adhesión más severa que la de la chapa de acero galvanizado, los rodillos deben ser mantenidos regularmente.
Las chapas de acero aluminizado son resistentes a la corrosión de la gasolina, por lo que suelen utilizarse para depósitos de combustible de automóviles. La soldadura por costura de las chapas de acero aluminizado es similar a la de las chapas de acero galvanizado, y la principal preocupación son los problemas de agrietamiento. Los parámetros del proceso pueden consultarse en la tabla siguiente:
Condiciones de soldadura para Chapa de acero galvanizado Soldadura por costura
Espesor de la placa(mm) | Anchura del disco(mm) | Fuerza del electrodo(KN) | Tiempo (semana) | Corriente de soldadura(KA) | Velocidad de soldadura(cm/min) | ||
---|---|---|---|---|---|---|---|
soldadura | cesar | ||||||
0.8 | 7 | 3.6-4.5 | 3 5 | 2 2 | 17 18 | 150 250 | |
1.0 | 7 | 4.2-5.2 | 2 5 | 1 1 | 17.5 18.5 | 150 250 | |
1.2 | 7 | 4.5-5.5 | 2 4 | 1 1 | 18 19 | 150 250 |
Costura soldadura de acero inoxidable es menos difícil y suele realizarse mediante soldadura CA. La tabla siguiente muestra las condiciones de soldadura para la soldadura de cordones de acero inoxidable:
Condiciones de soldadura del cordón de acero inoxidable (1Cr18Ni9Ti) (HB/Z78-84)
Espesor de la placa(mm) | Anchura del disco(mm) | Fuerza del electrodo(KN) | Tiempo (semana) | Corriente de soldadura(KA) | Velocidad de soldadura(cm/min) | ||
---|---|---|---|---|---|---|---|
soldadura | cesar | ||||||
0.3 0.5 0.8 1.0 1.2 1.5 2.0 | 3-3.5 4.5-5.5 5.0-6.0 5.5-6.5 6.5-7.5 7.0-8.0 7.5-8.5 | 2.5-3.0 3.4-3.8 4.0-5.0 5.0-6.0 5.5-6.2 6.0-7.2 7.0-8.0 | 1-2 1-3 2-5 4-5 4-6 5-7 7-8 | 1-2 2-3 3-4 3-4 3-5 5-7 6-9 | 4.5-5.5 6.0-7.0 7.0-8.0 8.0-9.0 8.5-10 9.0-12 10-13 | 100-150 80-120 60-80 60-70 50-60 40-60 40-50 |
Durante la soldadura de cordones de aleaciones de alta temperatura, debido a su alta resistividad eléctrica y al calentamiento repetido de la soldadura, es más probable que se produzca segregación de cristales y estructuras sobrecalentadas, e incluso que salgan rebabas de la superficie de la pieza.
Para evitarlo, debe adoptarse una velocidad de soldadura muy lenta y un tiempo de enfriamiento más largo para facilitar la disipación del calor. La tabla siguiente muestra las condiciones de soldadura para la soldadura de cordones de aleación a alta temperatura:
Condiciones de soldadura para el soldeo por puntos de aleaciones de alta temperatura (GH33, GH35, GH39, GH44)
Espesor de la placa(mm) | Fuerza del electrodo(KN) | Tiempo (semana) | Corriente de soldadura(KA) | Velocidad de soldadura(cm/min) | |
---|---|---|---|---|---|
soldadura | cesar | ||||
0.3 0.5 0.8 1.0 1.2 1.5 2.0 2.5 3.0 | 4-7 5-8.5 6-10 7-11 8-12 8-13 10-14 11-16 12-17 | 3-5 4-6 5-8 7-9 8-10 10-13 12-16 15-19 18-23 | 2-4 4-7 8-11 12-14 14-16 19-25 24-30 28-34 30-39 | 5-6 5.5-7 6-8.5 6.5-9.5 7-10 8-11.5 9.5-13.5 11-15 12-16 | 60-70 50-70 30-45 30-45 30-40 25-40 20-35 15-30 15-25 |
Cuando la costura soldadura de aleaciones de aluminioDebido a su alta conductividad eléctrica y a su grave desviación, es necesario aumentar la corriente de soldadura en 15-50% en comparación con la soldadura por puntos, y aumentar la presión del electrodo en 10%.
Además, las máquinas de soldadura por costura de CA monofásica de alta potencia afectarán gravemente al equilibrio de las cargas trifásicas de la red eléctrica.
Por lo tanto, la soldadura por costura de aleación de aluminio doméstica generalmente utiliza máquinas de soldadura por pulso de corriente directa trifásica o rectificador secundario paso a paso. La siguiente tabla muestra las condiciones de soldadura para la soldadura de aleación de aluminio utilizando la máquina de soldadura de costura de pulso de corriente directa FJ-400.
Condiciones de soldadura para el cordón de aleación de aluminio
Espesor de la placa(mm) | Radio esférico del disco de rodadura (mm) | Distancia de paso (distancia entre puntos) | LF21、LF3、LF6 | LY12CZ、LC4CS | ||||||
---|---|---|---|---|---|---|---|---|---|---|
Fuerza del electrodo(KN) | Tiempo de soldadura (semana) | Corriente de soldadura (KA) | Puntos por minuto | Presión del electrodo (KN) | Tiempo de soldadura (KA) | Corriente de soldadura (KA) | Puntos por minuto | |||
1.0 1.5 2.0 3.0 3.5 | 100 100 150 150 150 | 2.5 2.5 3.8 4.2 4.2 | 3.5 4.2 5.5 7.0 – | 3 5 6 8 – | 49.6 49.6 51.4 60.0 – | 120-150 120-150 100-120 60-80 – | 5.5 8.5 9.0 10 10 | 4 6 6 7 8 | 48 48 51.4 51.4 51.4 | 120-150 100-120 80-100 60-80 60-80 |
Para mejorar la disipación del calor, la soldadura por costura de aleación de aluminio debe utilizar preferentemente un rodillo de cara frontal esférico y debe estar refrigerado externamente por agua.
La excepcional conductividad eléctrica y térmica del cobre y de la mayoría de las aleaciones de cobre presenta importantes retos para los procesos de soldadura por costura. Estas propiedades provocan una rápida disipación del calor, lo que dificulta alcanzar y mantener la temperatura necesaria para la fusión en la interfaz de soldadura. Sin embargo, algunas aleaciones de cobre con conductividad eléctrica reducida, como el bronce fosforoso, el bronce al silicio y el bronce al aluminio, pueden soldarse con éxito en condiciones específicas.
Cuando se sueldan por costura estas aleaciones de cobre, los parámetros del proceso deben ajustarse cuidadosamente para compensar las características únicas del material:
Es fundamental tener en cuenta que, incluso con estos ajustes, la soldabilidad y las propiedades de unión resultantes pueden no igualar las conseguidas con materiales más fácilmente soldables. Por lo tanto, en las aplicaciones con cobre y aleaciones de cobre de alta conductividad en las que la soldadura por costura resulte poco práctica o insatisfactoria, deben considerarse métodos de unión alternativos como la soldadura fuerte, la soldadura blanda o la fijación mecánica.
La soldadura por costura del titanio y sus aleaciones requiere una cuidadosa consideración de sus propiedades únicas, aunque el proceso comparte algunas similitudes con la soldadura del acero inoxidable. La elevada relación resistencia-peso, la excelente resistencia a la corrosión y la baja conductividad térmica del titanio requieren parámetros y técnicas de soldadura específicos.
Aunque las condiciones generales de soldadura son comparables a las utilizadas para el acero inoxidable, son esenciales varios ajustes clave:
Si se tienen en cuenta estas consideraciones y se emplean las técnicas adecuadas, la soldadura por costura del titanio y sus aleaciones puede producir soldaduras duraderas y de alta calidad adecuadas para las exigentes aplicaciones aeroespaciales, médicas e industriales.