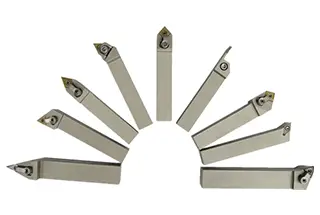
¿Alguna vez se ha preguntado cómo el fluido de corte adecuado puede transformar su proceso de mecanizado? Este artículo profundiza en los aspectos esenciales de la selección de fluidos de corte para el mecanizado CNC, destacando su impacto en la vida útil de la herramienta, la calidad de la superficie y la eficiencia. Descubra consejos prácticos y perspectivas para mejorar sus operaciones de mecanizado y lograr resultados superiores.
En el corte mecánico, se utilizan varios métodos cuando se emplean máquinas herramienta CNC, como el torneado, el fresado, el taladrado y el mandrinado. La cantidad de material extraído se divide en tres categorías: desbaste, semiacabado y acabado.
Los materiales utilizados para las herramientas de corte pueden clasificarse en cinco tipos: acero rápido, aleación dura, cerámica, diamante y nitruro de boro cúbico.
Las máquinas herramienta utilizadas pueden dividirse en cuatro categorías: las que requieren fluidos de corte a base de aceite, las que no, las herramientas de producción de lotes pequeños de una sola pieza y las líneas de producción por lotes o automáticas (sistemas de fabricación flexibles).
Es importante tener en cuenta que los distintos métodos de corte tienen características de corte diferentes para el mismo metal y pueden dar lugar a distintos niveles de dificultad de procesamiento.
Por ejemplo, al utilizar Q235 acero al carbono como material, puede ser un reto mecanizar roscas garantizando al mismo tiempo el índice de calidad de rugosidad superficial deseado. El proceso de acabado es más difícil que el de desbaste.
Los procesos de corte difíciles suelen requerir fluidos de corte de mayor calidad. El uso adecuado del fluido de corte puede garantizar la calidad del proceso, prolongar la vida útil de la herramienta y mejorar la eficiencia del proceso.
Al separar el desbaste y el acabado en una Máquina CNC o cuando la pieza no está acabada en una sola máquina, puede elegir el fluido de corte en función de las características de desbaste y acabado.
Durante el mecanizado de desbaste, una profundidad de corte y un avance grandes provocan una resistencia al corte y un calor considerables. Esto provoca la deformación de la pieza y el desgaste de la herramienta debido a la mayor transferencia de calor.
Debe utilizarse un fluido de corte a base de agua que principalmente refrigere y tenga algunos efectos lubricantes, de limpieza y de prevención de la oxidación, con un caudal elevado.
En el fresado o mecanizado de formas irregulares, márgenes desiguales y mecanizado intermitente, la velocidad de corte es menor, y el impacto de los golpes y vibraciones sobre la herramienta y la pieza es mayor que el calor de corte. El fluido de corte debe tener un efecto equilibrado de lubricación y refrigeración.
Cuando las condiciones lo permitan, puede utilizar orificios internos de suministro de líquido en la barra de orificio interior, cuchilla de perforación y ranurado cuchilla para el mecanizado de agujeros, o utilice el suministro de presión y pulverización para el mecanizado en bruto de materiales difíciles de mecanizar para obtener mejores resultados.
Por lo general, las tolerancias de mecanizado de las piezas de desbaste son grandes, y los requisitos de precisión de rugosidad superficial no son elevados cuando se procesan materiales difíciles de mecanizar y metales no ferrosos.
Por lo tanto, las emulsiones de extrema presión a base de agua pueden utilizarse sin componentes químicos elevados en el fluido de corte. Al desbastar hierro fundido y metales no férreos quebradizos, una característica común es el desconchado de virutas durante el corte.
Lectura relacionada: Metales ferrosos y no ferrosos
Las virutas finas se vuelven fluidas al ser impactadas por el fluido de corte, y la mayoría de ellas se asentarán cuando el fluido de corte circule por el depósito de fluido de corte.
Sin embargo, algunas virutas fluyen con el fluido de corte y se acumulan en pequeñas partes del tubo de transporte del fluido de corte, lo que puede bloquear la boquilla de refrigeración y hacer que las virutas se adhieran a las piezas móviles de la máquina herramienta, como el par de raíles guía.
Además, el fluido de corte reacciona químicamente con determinados componentes de la fundición, lo que provoca el deterioro del rendimiento del fluido de corte.
Debido a los problemas asociados a los fluidos de corte, generalmente se evitan. Si las condiciones lo permiten, se puede utilizar un dispositivo de extracción de polvo para eliminar el polvo, las virutas finas y algo de calor para reducir su impacto.
Si es necesario utilizar líquido de corte, se recomienda utilizar líquido de corte a base de agua, y es importante filtrar y purificar adecuadamente el líquido de corte para evitar su deterioro y la disminución de su concentración.
Durante el desbaste, la concentración del fluido de corte suele ser menor que durante el acabado.
El acabado puede clasificarse en acabado de alta velocidad y acabado de baja velocidad en función de la velocidad de corte.
Durante el acabado a alta velocidad, el uso de fluido de corte a base de aceite puede mejorar la calidad de la superficie de la pieza y prolongar la vida útil de la herramienta. Sin embargo, el aceite mineral que contiene tiene baja viscosidad y punto de inflamación, y a menudo produce humos de aceite, neblina de aceite y vapor de aceite que pueden liberar componentes tóxicos, afectando al entorno de producción y perjudicando la salud física y mental del operario.
Por lo tanto, en el acabado de alta velocidad, es mejor utilizar un fluido de corte con base de agua con una emulsión o microemulsión que contenga aditivos de extrema presión, y la concentración debe ser mayor que durante el mecanizado en bruto.
En el acabado a baja velocidad, la temperatura de corte es baja y es menos probable que se produzcan estos problemas.
Para mantener la precisión de la pieza, debe utilizarse líquido de corte a base de aceite.
En comparación con el desbaste, la velocidad de corte durante el acabado es mayor. El calor de corte generado por la deformación de la viruta es menor que el calor de corte generado por la fricción en el flanco de la herramienta, y la fuerza de corte es menor.
Incluso durante el corte a alta velocidad, la deformación térmica de la pieza por el calor de corte no es tan pronunciada como durante el mecanizado en bruto.
La principal razón para utilizar fluidos de corte en herramientas de corte es reducir el desgaste del flanco de la herramienta.
Durante el acabado, la velocidad de corte relativa es alta y la temperatura en el momento en que se retira la viruta de la pieza es muy elevada.
Incluso con el uso de fluido de corte, si éste tiene una permeabilidad deficiente o una presión insuficiente, no penetrará lo suficiente en la zona de corte, lo que provocará que la herramienta sea muy susceptible al desgaste del flanco.
Aunque la herramienta pueda seguir utilizándose, la calidad de la rugosidad superficial de la pieza no cumplirá los requisitos y será necesario sustituirla.
Por lo tanto, durante el acabado, es importante utilizar un fluido de corte con buena lubricación y permeabilidad para prolongar la vida útil de la herramienta y garantizar los requisitos de calidad de precisión de mecanizado y rugosidad superficial de la pieza.
Para el acabado a baja velocidad de materiales ferrosos, puede utilizarse aceite de corte de presión extrema activo. Para el acabado a baja velocidad de metales no ferrosos, se debe utilizar aceite de corte a presión extrema no reactivo.
Para el acabado a alta velocidad de metales no ferrosos, puede utilizarse una emulsión con aditivos de extrema presión inactivos.
En el mecanizado CNC, el mecanizado de agujeros consiste principalmente en taladrar, escariar, tornear agujeros interiores en un torno y mandrinar en una mandrinadora.
Debido a los problemas de evacuación de virutas y disipación del calor, la herramienta (varilla) tiene poca rigidez, y la velocidad de corte para el mecanizado de agujeros es menor y más difícil que para el mecanizado de contornos exteriores.
La perforación suele utilizar un broca espiralque se considera mecanizado en bruto.
La extracción de virutas es difícil durante perforaciónAdemás, es difícil disipar el calor de corte, lo que a menudo provoca el reblandecimiento de la cuchilla y afecta a la vida útil de la broca y a su eficacia de procesamiento.
Utilizar un fluido de corte con buenas prestaciones puede prolongar considerablemente la vida útil de la perforadora y aumentar significativamente la productividad.
Normalmente, se utiliza emulsión de presión extrema o fluido de corte sintético de presión extrema. Este último tiene baja tensión superficial, buena permeabilidad y puede enfriar la broca con prontitud, por lo que resulta muy eficaz para prolongar la vida útil de la herramienta y mejorar la eficiencia del procesamiento.
Para materiales difíciles de cortar, como el acero inoxidable y las aleaciones resistentes al calor, pueden utilizarse aceites de corte de baja viscosidad y extrema presión.
Al taladrar, tanto si se trata de un taladrado normal como de un taladrado profundo, las malas condiciones de disipación del calor generan mucho calor de corte. La dirección de descarga de la viruta es opuesta a la dirección de avance de la broca, y el fluido de corte tiene que penetrar en la broca para lubricar, refrigerar y ayudar a la evacuación de la viruta.
El fluido de corte debe tener una buena permeabilidad y el método de suministro de fluido, el caudal y la presión también deben cumplir los requisitos.
Cuando se trata de mejorar los indicadores de vida útil de las perforadoras, los fluidos de corte a base de aceite suelen ser mejores que los fluidos de corte a base de agua, y las microemulsiones de extrema presión en fluidos de corte a base de agua son las mejores.
De todos los fluidos de corte, el aceite sulfurizado activo de baja viscosidad en fluidos de corte a base de aceite tiene el mejor rendimiento global.
El escariado es una operación de acabado de velocidad media-baja, por lo que al escariar un agujero deben tenerse en cuenta dos indicadores de calidad, la precisión dimensional y la precisión de la rugosidad superficial del agujero escariado, así como la vida útil del escariador y la precisión de sujeción.
En cuanto al control del índice del diámetro de los poros, todos los fluidos de corte a base de aceite aumentan el diámetro de los poros: el aceite mineral lo aumenta, el aceite de corte a presión extrema lo reduce y el aceite activo sulfurado y clorado lo reduce al mínimo.
Los fluidos de corte a base de agua reducen el tamaño de los poros, siendo las microemulsiones y las microemulsiones de presión extrema que contienen azufre las que minimizan el tamaño de los poros, la emulsión centrada y el fluido de corte sintético el más pequeño.
Por lo tanto, para controlar el tamaño del orificio escariado, cuando se utiliza un escariador nuevo, se debe utilizar líquido de corte a base de agua para dificultar la expansión del orificio. Cuando el escariador está desgastado hasta cierto punto, se puede utilizar líquido de corte a base de aceite para expandir ligeramente la abertura.
En términos de reducción de la rugosidad superficial del agujero escariado, el fluido de corte a base de agua es mejor que el fluido de corte a base de aceite.
Entre los fluidos de corte a base de aceite, el aceite clorado sulfurizado activo tiene el mejor efecto, seguido del aceite de extrema presión que contiene cloro, el aceite mineral mezclado y el aceite mineral puro son los peores.
Entre los fluidos de corte a base de agua, las emulsiones, las microemulsiones y las microemulsiones de presión extrema que contienen azufre tienen básicamente el mismo efecto, y el fluido de corte sintético tiene el peor efecto.
En términos de control de la vida útil del escariador, el aceite de corte de presión extrema inactivo y el aceite de corte antifricción en fluido de corte a base de aceite tienen el mejor rendimiento.
Entre los líquidos de corte a base de agua, el líquido de corte sintético es el que tiene el peor efecto.
El torneado de agujeros interiores y el mandrinado, salvo en el caso de las herramientas de mandrinar flotantes, son operaciones de corte de un solo filo.
Las condiciones de disipación del calor son peores que en los círculos exteriores.
Cuando se utiliza fluido de corte, al igual que en la perforación y el escariado, el caudal y la presión deben aumentarse adecuadamente.
El procesado de roscas es un tipo de proceso de conformado.
Al realizar las operaciones de aterrajado y roscado, entra en la categoría de corte de varios filos y baja velocidad.
Debido al material de corte que rodea el filo de corte, el par de corte es significativo, y la eliminación de virutas es todo un reto.
La falta de un arranque de viruta adecuado provoca la acumulación de calor, lo que puede hacer que las virutas se congestionen y vibren, provocando el desgaste de la herramienta.
Las condiciones de roscado son especialmente exigentes, ya que el espacio de arranque de viruta es estrecho, lo que dificulta que las virutas se rompan y salgan. El resultado es una fuerza de corte y una fuerza de fricción elevadas, lo que aumenta el riesgo de rotura del macho de roscar.
Para mitigar estos problemas, es esencial utilizar un fluido de corte con un bajo coeficiente de fricción y una buena permeabilidad. Esto reducirá la resistencia a la fricción de la herramienta y prolongará su vida útil.
Cuando se cortan materiales metálicos ferrosos, generalmente se recomienda utilizar fluidos de corte a base de aceite que contengan altos niveles de aditivos de azufre y cloro, con baja viscosidad y buena permeabilidad.
Cuando se utiliza acero rápido para el torneado de roscas a baja velocidad, los criterios para seleccionar un fluido de corte son los mismos que para el roscado con macho y el roscado con manguito.
Al tornear roscas con herramientas de metal duro, la velocidad de corte es alta, la fuerza de impacto es considerable, la temperatura de corte es elevada y el área del filo de corte es pequeña. Esto se traduce en una gran fuerza de corte, y el perfil de la rosca debe ser preciso para evitar problemas que afectan a la calidad superficial de la rosca, como la acumulación de virutas y las espinas de cascarilla.
Para mantener la elevada vida útil de la herramienta, es crucial disponer de un fluido de corte que proporcione la refrigeración, lubricación y penetración adecuadas.
En este caso, conviene utilizar un fluido de corte a base de agua que contenga aditivos de extrema presión.
Para evitar daños debidos a un calentamiento desigual de la herramienta, se suele utilizar el corte en seco cuando se corta con herramientas de metal duro.
Sin embargo, para obtener la máxima eficacia, un ahorro de costes integral y una calidad de mecanizado óptima, lo mejor es utilizar líquido de corte cuando se trabaja en Máquinas herramienta CNC.
Cuando se utilizan herramientas de metal duro para el mecanizado, se suelen emplear fluidos de corte a base de agua cuando la velocidad de corte es relativamente alta. Es importante mantener un caudal elevado y vigilar cuidadosamente la alineación de la boquilla con la posición de corte.
Para el corte a baja velocidad con herramientas de acero de alta velocidad, se suelen utilizar fluidos de corte a base de aceite que proporcionan lubricación.
El uso de herramientas de cerámica, cermet, diamante y nitruro de boro cúbico es adecuado principalmente para el corte de alta velocidad, el corte en seco y los métodos de corte duro, y el fluido de corte no siempre es necesario.
Sin embargo, para evitar temperaturas de corte excesivas, en la mayoría de los casos se utilizan fluidos de corte cuando se emplean estas herramientas.
Debido a su alta velocidad de corte, se recomienda utilizar fluidos de corte a base de agua cuando se utilicen estas herramientas.
La selección del fluido de corte debe tener en cuenta múltiples factores, como la máquina herramienta, la herramienta de corte y el proceso de mecanizado. El tipo de fluido de corte, ya sea base aceite o base agua, se determina en función de las limitaciones de seguridad y tratamiento de fluidos residuales.
Si se da prioridad a la prevención de incendios y a la seguridad, deben considerarse los fluidos de corte a base de agua. Al elegir fluidos de base acuosa, deben tenerse en cuenta las cuestiones relativas a la emisión de residuos, y las empresas deben disponer de instalaciones de tratamiento de residuos. Para algunas operaciones, como el rectificado, los fluidos de corte base agua suelen ser la única opción. En los procesos de mecanizado con herramientas de metal duro, suelen preferirse los fluidos de corte con base de aceite.
Para las máquinas herramienta de alta velocidad que obligan a utilizar fluidos de corte a base de aceite, no es aconsejable cambiar a fluidos a base de agua, ya que podría afectar al rendimiento de la máquina. Tras considerar estos factores, se puede decidir el tipo de fluido de corte adecuado. Una vez determinado el tipo de fluido de corte principal, se puede hacer una selección secundaria basada en el método de mecanizado, la precisión requerida, la rugosidad de la superficie y otros factores. Si el fluido de corte elegido no cumple las expectativas, debe volver a evaluarse, identificar y corregir la causa del problema y tomar una decisión definitiva.
Con una amplia variedad de fluidos de corte disponibles, una selección inadecuada puede conducir a resultados adversos. Los fluidos de corte a base de agua deben elegirse en las siguientes situaciones:
Los fluidos de corte a base de aceite deben considerarse en las siguientes situaciones:
El uso adecuado de los fluidos de corte desempeña un papel crucial en la mejora de la eficacia del mecanizado, el aumento de la calidad del mecanizado, la prolongación de la vida útil de la herramienta y la reducción de los costes generales durante el corte NC.
Sin embargo, los fluidos de corte pueden suponer un riesgo para la salud del operario y contribuir a la contaminación medioambiental a través de la eliminación y el vertido de fluidos residuales.
En apoyo de la fabricación ecológica, es importante que los operarios exploren métodos alternativos que minimicen o eliminen el uso de fluidos de corte.
La industria y las organizaciones de investigación deben seguir desarrollando fluidos de corte con mejores prestaciones, credenciales ecológicas, versatilidad y asequibilidad para satisfacer las necesidades de los usuarios.
Los responsables de las máquinas herramienta, los técnicos de procesos y los operarios deben mantenerse informados y promover activamente el uso de nuevos fluidos de corte y tecnologías de refrigeración y lubricación respetuosos con el medio ambiente en la producción. Esto garantizará que se utilicen en la práctica los fluidos de corte y las tecnologías más adecuados.