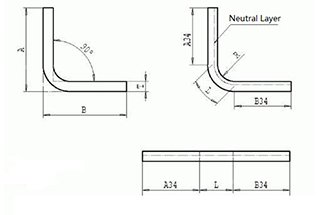
¿Alguna vez se ha preguntado por el arte y la ciencia que hay detrás de dar forma compleja a las chapas metálicas? En esta cautivadora entrada de blog, nos adentramos en el fascinante mundo del plegado de chapa metálica. Nuestro ingeniero mecánico experto desvela los secretos que se esconden tras las distintas técnicas de plegado, los materiales y los equipos, y ofrece valiosos conocimientos que le ayudarán a comprender mejor este proceso de fabricación crucial.
El plegado de chapa metálica es un proceso de conformado fundamental que altera la geometría de una chapa o panel metálico creando cambios angulares a lo largo de un eje lineal. Esta técnica versátil puede producir una amplia gama de perfiles, incluidas formas en V, en U y configuraciones más complejas, lo que permite la fabricación de diversos componentes para industrias como la automovilística, la aeroespacial y la de la construcción.
Lectura relacionada: Calculadora de fuerza de flexión en V y en U
Dos métodos principales dominan las operaciones de curvado de chapa: el curvado de moldes y el curvado de chapas. prensa plegadora flexión. Cada método ofrece ventajas únicas y se adapta a escenarios de producción específicos:
La selección entre estos métodos depende de factores como la complejidad de la pieza, el volumen de producción, las propiedades del material y las tolerancias requeridas. Ambas técnicas emplean principios distintos y ofrecen características únicas que responden a requisitos de aplicación específicos en los procesos modernos de fabricación de metales.
El plegado de chapa metálica es un proceso crítico en la fabricación moderna, en el que la selección de materiales desempeña un papel fundamental en el rendimiento y la rentabilidad del producto. Esta sección explora los metales más utilizados en el plegado de chapa metálica, detallando sus propiedades, aplicaciones y características únicas que influyen en la conformabilidad y la calidad del producto final.
El acero, una aleación de hierro y carbono, sigue siendo la piedra angular de la fabricación de chapa metálica por su excepcional relación resistencia/coste y su versatilidad. Las distintas calidades de acero ofrecen un espectro de propiedades adecuadas para diferentes aplicaciones de plegado:
Acero dulce (acero bajo en carbono): Contiene carbono de 0,05% a 0,25%, que ofrece una excelente conformabilidad y soldabilidad. Su bajo límite elástico facilita el doblado, por lo que es ideal para paneles de carrocería de automóviles, componentes estructurales y fabricación en general. Sin embargo, su susceptibilidad a la corrosión requiere revestimientos protectores para muchas aplicaciones.
Acero inoxidable: Aleado con un mínimo de 10,5% de cromo, el acero inoxidable proporciona una resistencia superior a la corrosión gracias a la formación de una capa de óxido de cromo autorregenerativa. Los grados más comunes son:
Acero de alta resistencia y baja aleación (HSLA): Ofrece mayor resistencia y conformabilidad en comparación con el acero dulce, gracias a elementos de microaleación como el niobio o el vanadio. Los aceros HSLA se utilizan cada vez más en los sectores aeroespacial y de automoción para reducir el peso manteniendo la integridad estructural.
Las aleaciones de aluminio ofrecen un equilibrio óptimo entre ligereza, resistencia a la corrosión y conformabilidad, lo que las hace indispensables en industrias que priorizan la reducción de peso y la durabilidad:
Aleación 5052: Excelente conformabilidad y resistencia a la corrosión; se utiliza comúnmente en aplicaciones marinas, recintos electrónicos y depósitos de combustible.
Aleación 6061: Buena resistencia y soldabilidad; ampliamente utilizada en componentes estructurales, equipos de transporte y piezas de maquinaria.
Aleación 3003: Alta conformabilidad y resistencia moderada; ideal para trabajos de chapa en general, componentes HVAC y utensilios de cocina.
Entre las principales ventajas del aluminio en el plegado de chapa se incluyen:
La combinación única de alta conductividad eléctrica, propiedades de gestión térmica y conformabilidad del cobre lo hace insustituible en determinadas aplicaciones:
Las calidades de cobre más comunes para el curvado de chapa son:
El latón, una aleación compuesta principalmente de cobre y zinc, ofrece una combinación única de propiedades que lo hacen valioso tanto para aplicaciones funcionales como estéticas:
Aleaciones de latón habituales para el plegado de chapa:
A la hora de seleccionar materiales para el plegado de chapa metálica, hay que tener en cuenta no sólo las propiedades del material, sino también los requisitos específicos de plegado, como el radio de curvatura, la compensación del springback y la posibilidad de que se produzcan grietas por tensión. Las herramientas avanzadas de análisis de elementos finitos (FEA) y simulación se utilizan cada vez más para optimizar la selección de materiales y los parámetros de plegado, garantizando resultados satisfactorios en operaciones complejas de conformado de chapa metálica.
Flexión por aire
El plegado por aire es una técnica versátil y ampliamente adoptada en la fabricación de chapas metálicas. El proceso consiste en colocar la pieza en una matriz con una abertura en forma de V, mientras un punzón desciende para aplicar una presión controlada. A medida que el punzón penetra, la chapa se deforma elástica y plásticamente, creando un pliegue. El ángulo de plegado final viene determinado por la profundidad de penetración del punzón, las propiedades del material (como el límite elástico y el grosor) y la anchura de la abertura de la matriz. Las principales ventajas del plegado por aire son:
Acuñación
El acuñado es una técnica de plegado de precisión que emplea una fuerza considerable para deformar plásticamente la chapa metálica en la cavidad de una matriz. Durante el proceso de acuñado, el punzón y la matriz se presionan entre sí con la pieza de trabajo intercalada, lo que hace que el material fluya y se ajuste con precisión a la geometría del utillaje. Este método ofrece varias ventajas:
Flexión en tres puntos
La flexión en tres puntos es una técnica fundamental utilizada tanto para ensayos de materiales como para aplicaciones prácticas de fabricación. En este método, la chapa metálica se apoya en dos puntos, aplicándose una fuerza controlada en un tercer punto entre los apoyos. Este método proporciona:
Doblado de matrices en V
El plegado en V es una técnica fundamental en la industria de la chapa metálica, que ofrece un equilibrio entre versatilidad y precisión. El proceso utiliza un punzón en forma de V y la matriz correspondiente, que aplican presión para formar el ángulo de plegado deseado. Las principales características del plegado en V son:
Prensas plegadoras
Las plegadoras de chapa son máquinas versátiles que ofrecen gran precisión y repetibilidad en la producción de formas complejas. Utilizan un sistema de punzones y matrices para aplicar una fuerza concentrada en la pieza de trabajo y crear plegados precisos. Las plegadoras modernas se presentan en varias configuraciones, como modelos hidráulicos, mecánicos y eléctricos servoaccionados, cada una de ellas adaptada a necesidades de producción específicas.
Hidráulica: Proporciona una fuerza constante en toda la carrera, ideal para aplicaciones de trabajo pesado.
Mecánica: Ofrece un funcionamiento a alta velocidad, adecuado para la producción de grandes volúmenes de piezas más sencillas.
Servo eléctrico: Ofrece una precisión y una eficiencia energética superiores, perfectas para componentes de precisión.
La capacidad de una plegadora viene determinada por factores como la longitud de trabajo, el tonelaje y la sofisticación del sistema de control. Las plegadoras avanzadas controladas por CNC pueden lograr plegados complejos en varios ejes, cambios de herramienta y supervisión de la fuerza en tiempo real para obtener resultados óptimos.
Máquina plegadora
Las plegadoras, también conocidas como curvadoras de paneles, son equipos especializados diseñados para la producción eficiente de piezas de chapa grandes y complejas. Emplean una viga de sujeción para fijar la pieza y una cuchilla de plegado para crear pliegues precisos. Este diseño permite manipular chapas de mayor tamaño y crear múltiples dobleces sin necesidad de reposicionar el material.
Manual: Utilizadas por técnicos cualificados para la producción de pequeños lotes o la creación de prototipos.
Automatizada: Equipada con controles CNC para la producción de piezas complejas de gran volumen con una intervención mínima del operario.
Las plegadoras destacan en la manipulación de una amplia gama de materiales, como aluminio, acero inoxidable y acero galvanizado. Su diseño exclusivo suele reducir las marcas en materiales delicados y permite fabricar piezas con bridas de menor longitud que las plegadoras tradicionales.
Matrices de plegado
Las matrices de plegado son componentes críticos en el conformado de chapa metálica, ya que influyen directamente en la geometría, la precisión y la calidad superficial de la pieza final. Se fabrican con materiales de alto rendimiento, como acero para herramientas, aleaciones mejoradas con carburo o carburo de tungsteno, para garantizar su longevidad y mantener la precisión con un uso repetido.
Cilindros en V: Versátiles y muy utilizados para el curvado por aire y por el fondo. Disponibles en varios ángulos para lograr diferentes radios de curvatura.
Matrices de plegado giratorias: Disponen de elementos giratorios que reducen significativamente la fricción, ideales para materiales propensos al rayado o cuando se trabaja con superficies preacabadas.
Troqueles de barrido: Emplean una acción de barrido para crear curvas de radio estrecho, a menudo utilizadas en la producción de perfiles y canales complejos.
Los diseños de troqueles avanzados pueden incorporar características como almohadillas de presión con resorte para mejorar el control del material o insertos de carburo para prolongar la vida útil de la herramienta en entornos de producción de gran volumen. La selección de las matrices adecuadas es crucial para lograr las tolerancias deseadas, minimizar el springback y optimizar la eficiencia general del plegado.
Normas ISO
Las operaciones de plegado de chapa metálica deben cumplir normas internacionales específicas para garantizar la calidad, la seguridad y la coherencia. La Organización Internacional de Normalización (ISO) desarrolla y mantiene estas normas. Para el plegado de chapa metálica, las normas pertinentes incluyen:
ISO 9013: Esta norma especifica los requisitos para los métodos de corte térmico, incluidos el corte por láser y el corte por plasma, que se utilizan a menudo en la preparación de chapas metálicas antes del plegado. Define las características de calidad, las condiciones técnicas de entrega y las tolerancias de las superficies cortadas térmicamente.
ISO 16630: Esta norma define los métodos de ensayo mecánico utilizados para verificar la integridad estructural y las propiedades mecánicas de los materiales de chapa metálica. En concreto, describe el procedimiento para realizar ensayos de aplanamiento de tubos, que son cruciales para evaluar la conformabilidad y ductilidad de los productos metálicos tubulares.
ISO 7438: Esta norma describe el método de ensayo de doblado para materiales metálicos, esencial para evaluar la ductilidad y la conformabilidad de las chapas metálicas utilizadas en operaciones de doblado.
ISO 6892-1: Esta norma especifica el método para el ensayo de tracción de materiales metálicos a temperatura ambiente, proporcionando datos valiosos sobre las propiedades de los materiales que influyen en el comportamiento a la flexión.
El cumplimiento de las normas ISO garantiza que las operaciones de plegado de chapa metálica produzcan productos fiables y de alta calidad para diversas industrias y aplicaciones, al tiempo que facilita el comercio y la colaboración internacionales.
Normas ASTM
La Sociedad Americana de Pruebas y Materiales (ASTM) también desempeña un papel crucial en el sector del plegado de chapa al establecer y mantener normas. Las normas ASTM relevantes para el plegado de chapa metálica incluyen:
ASTM A6/A6M: Esta norma describe los requisitos generales para chapas, perfiles, tablestacas y barras de acero laminado utilizados en diversas aplicaciones, incluido el plegado de chapas. Abarca las tolerancias dimensionales, las variaciones admisibles y los procedimientos de ensayo.
ASTM A480/A480M: Esta norma especifica los requisitos generales para chapas, hojas y bandas de acero inoxidable y resistente al calor laminadas planas utilizadas en el doblado de chapas metálicas. Incluye detalles sobre la composición química, las propiedades mecánicas y los requisitos de acabado superficial.
ASTM E290: Esta norma define las metodologías para realizar ensayos de doblado en materiales metálicos para evaluar la ductilidad y la conformabilidad. Proporciona directrices para diversas configuraciones de ensayos de flexión, incluidos los ensayos de flexión guiada y los ensayos de flexión libre.
ASTM E8/E8M: Esta norma describe los métodos para el ensayo de tracción de materiales metálicos, que es crucial para determinar las propiedades mecánicas que influyen en el comportamiento a la flexión.
ASTM B820: Esta norma cubre la especificación de láminas metálicas para aislamiento eléctrico, que es relevante para el doblado de chapas metálicas en aplicaciones eléctricas y electrónicas.
El cumplimiento de las normas ASTM garantiza que las operaciones de plegado de chapa metálica cumplan los requisitos del sector y mantengan un alto nivel de calidad en sus productos. Estas normas también proporcionan un lenguaje común para fabricantes, proveedores y clientes, facilitando una comunicación y unas expectativas claras en el sector de la chapa metálica.
Los fabricantes suelen considerar el curvado de moldes como método de procesamiento para piezas estructurales que tienen una capacidad anual de más de 5.000 piezas y un tamaño relativamente pequeño, por lo general de alrededor de 300 x 300.
La figura 1-17 muestra las matrices de doblado más utilizadas. Para aumentar la longevidad del molde, es aconsejable incorporar esquinas redondeadas al diseñar las piezas.
Figura 1-17 Molde de conformado especial
Utilizando un matriz dobladora con una altura de pestaña demasiado pequeña no es ideal para el conformado. Normalmente, la altura de la pestaña debe ser L ≥ 3t, teniendo en cuenta el grosor de la pared.
Los peldaños en forma de Z de chapa metálica con un perfil más bajo suelen doblarse utilizando moldes sencillos en punzonadoras o prensas hidráulicas para lotes pequeños. Para lotes más grandes, se puede utilizar una matriz escalonada en una máquina curvadora, pero la altura (H) debe estar normalmente entre 0 y 1,0 veces el espesor de la pared (t).
Si la altura está entre 1,0 y 4,0 veces el grosor de la pared, puede ser necesaria una forma de molde con una estructura de descarga. La altura puede ajustarse añadiendo un espaciador, pero mantener la longitud (L) y la verticalidad del lado vertical puede resultar complicado. Si la altura es mayor, debe considerarse el doblado en una máquina plegadora.
Figura 1-18 En forma de Z flexión por pasos
Existen dos categorías de curvadoras: las curvadoras ordinarias y las curvadoras Plegado CNC máquinas. Las curvadoras CNC se utilizan normalmente para plegado de chapa en dispositivos de comunicación debido a la necesidad de alta precisión y a la forma irregular de la curva.
El principio básico de la máquina consiste en dar forma a la pieza de chapa utilizando el molde superior, que es el punzón de plegado, y el molde inferior, que es la matriz en forma de V.
Ventajas:
Desventajas:
El principio básico del conformado se muestra en la Figura 1-19:
Figura 1-19 Principio básico del conformado
Los siguientes son dos componentes clave de la máquina curvadora:
1. Cuchilla dobladora (troquel superior)
En la figura 1-20 se muestra el aspecto de las cuchillas curvadoras. Su forma viene determinada principalmente por la forma de la pieza.
Normalmente, las herramientas de mecanizado disponen de una amplia selección de cuchillas curvadoras. Los fabricantes especializados incluso fabrican a medida una gran variedad de formas y especificaciones únicas para realizar tareas de plegado complejas.
La forma en V de la matriz inferior suele determinarse como V=6t (donde t representa el grosor del material).
El proceso de plegado se ve afectado por varios factores, como el radio de arco de la matriz superior, las propiedades del material, su grosor, la resistencia de la matriz inferior y el tamaño de la abertura en V de la matriz inferior.
Para satisfacer los distintos requisitos de los productos, los fabricantes han estandarizado las matrices de plegado, garantizando al mismo tiempo la seguridad de la plegadora.
Tener un conocimiento fundamental de las matrices de flexión disponibles es crucial durante el proceso de diseño estructural.
La figura 1-20 muestra el troquel superior a la izquierda y el inferior a la derecha.
Figura 1-20 Diagrama esquemático del prensa plegadora punzón y matriz
El principio básico de la proceso de plegado secuencia:
Las formas de doblado que suelen verse en las fábricas de subcontratación se muestran generalmente en la Figura 1-21.
Figura 1-21 Forma de flexión de prensa plegadora máquina
El radio de curvatura es un factor crítico que hay que tener en cuenta al curvar chapa. Es esencial elegir un radio de curvatura adecuado que no sea ni demasiado grande ni demasiado pequeño.
Si el radio de curvatura es demasiado pequeño, puede provocar grietas durante el curvado, y si es demasiado grande, es probable que se produzcan rebotes. La Tabla 1-9 muestra el radio de curvatura preferido (radio de curvatura interior) para diferentes materiales con distintos espesores.
Material | Estado recocido | Estado de endurecimiento por trabajo en frío | ||
---|---|---|---|---|
La posición correspondiente de la dirección de la línea de flexión y la dirección de la fibra | ||||
vertical | en paralelo | vertical | en paralelo | |
08,10 | 0.1t | 0.4 t | 0.4 t | 0.8 t |
15,20 | 0.1 t | 0.5 t | 0.5 t | 1.0 t |
25,30 | 0.2 t | 0.6 t | 0.6 t | 1.2 t |
45,50 | 0.5 t | 1.0 t | 1.0 t | 1.7 t |
65Mn | 1.0 t | 2.0 t | 2.0 t | 3.0 t |
Aluminio | 0.1 t | 0.35 t | 0.5 t | 1.0 t |
Cobre | 0.1 t | 0.35 t | 1.0 t | 2.0 t |
Latón blando | 0.1 t | 0.35 t | 0.35 t | 0.8 t |
Latón semiduro | 0.1 t | 0.35 t | 0.5 t | 1.2 t |
Bronce fosforoso | -- | -- | 1.0 t | 3.0 t |
Nota: t es el grosor de la chapa de la tabla.
Tenga en cuenta que los datos presentados en la Tabla 1-9 se facilitan únicamente a título de referencia y no deben considerarse definitivos. En la práctica real, la mayoría de los fabricantes utilizan cuchillas curvadoras con una esquina redondeada de 0,3, y sólo unos pocos emplean una esquina redondeada de 0,5.
Por eso, el radio interior de curvatura de nuestras piezas de chapa suele ser de 0,2. Aunque este radio es suficiente para las chapas normales de acero con bajo contenido en carbono, las chapas antioxidantes placas de aluminioEn el caso de las placas de acero con alto contenido de carbono, las placas de latón y las placas de cobre, puede que no sea adecuado para el acero con alto contenido de carbono, el aluminio duro y el aluminio superduro. En estos casos, una esquina redondeada de 0,2 puede provocar la rotura de la curva o el agrietamiento de la esquina exterior.
Figura 1-22 Diagrama de flexión y rebote
1) Ángulo de rebote Δα=b-a
En la fórmula:
2) El tamaño del ángulo de rebote
El ángulo de rebote en una curva de aire de 90° se muestra en la Tabla 1-10.
Tabla 1-10 Ángulo de rebote en curva de aire de 90 grados
Material | r/t | Espesor t(mm) | ||
---|---|---|---|---|
<0.8 | 0.8~2 | >2 | ||
Acero bajo en carbono | <1 | 4° | 2° | 0° |
Latón σb=350MPa | 1~5 | 5° | 3° | 1° |
Aluminio, zinc | >5 | 6° | 4° | 2° |
Acero al carbono medio σb=400-500MPa | <1 | 5° | 2° | 0° |
Cobre amarillo duro σb=350-400MPa | 1~5 | 6° | 3° | 1° |
Bronce duro σb=350-400MPa | >5 | 8° | 5° | 3° |
Acero con alto contenido en carbono σb>550Mpa | <1 | 7° | 4° | 2° |
1~5 | 9° | 5° | 3° | |
>5 | 12° | 7° | 6° |
La magnitud del ángulo de rebote es directamente proporcional al límite elástico del material e inversamente proporcional a su módulo elástico, E. Por lo tanto, cuando se trata de piezas de chapa que requieren gran precisión, es aconsejable utilizar acero con bajo contenido en carbono en lugar de acero con alto contenido en carbono o acero inoxidable para reducir el rebote.
Es crucial comprender que el grado de deformación disminuye a medida que la temperatura relativa radio de curvaturar/t, aumenta. A la inversa, el ángulo de rebote, Δα, aumenta a medida que disminuye el radio de curvatura relativo, r/t.
Para lograr una mayor precisión, se recomienda optar por un radio de curvatura pequeño al diseñar las esquinas redondeadas de las curvas de chapa metálica. Evite en la medida de lo posible el uso de arcos grandes, como se muestra en la Figura 1-23, ya que son difíciles de producir y controlar en cuanto a calidad.
Figura 1-23 El arco de la chapa es demasiado grande
El estado inicial de la curva en forma de L se muestra en la Figura 1-24:
Figura 1-24 Curvatura en L
Un factor crucial aquí es la anchura "B" del molde inferior.
El proceso de doblado y la resistencia del molde exigen una anchura mínima del molde para distintos grosores de material. Si la anchura es inferior a este valor, pueden surgir problemas como dobleces desalineados o moldes dañados.
La experiencia práctica ha demostrado que la relación entre la anchura mínima del molde y el espesor del material puede expresarse mediante la siguiente ecuación:
Bmin = kT ①
Donde Bmin es la anchura mínima del molde, T es el espesor del material y k = 6 al calcular la anchura mínima del molde.
Las especificaciones de anchura de molde más utilizadas actualmente por los fabricantes son:
4, 5, 6, 8, 10, 12, 14, 16, 18, 20, 25
Basándose en la relación anterior, puede determinarse la anchura mínima del molde necesaria para diferentes grosores de material durante el doblado. Por ejemplo, al doblar un material de 1.5 mm de grosor placa, B = 6 * 1,5 = 9. De la serie anterior de anchos de molde, puede elegir un ancho de molde inferior de 10 mm u 8 mm.
A partir del diagrama de estado inicial del pliegue, está claro que el borde del pliegue no puede ser demasiado corto. Combinada con la anchura mínima del molde, la ecuación para determinar el borde de plegado más corto es:
Lmin = 1/2 (Bmin + Δ) + 0.5 ②
Donde Lmin es el borde de curvatura más corto, Bmin es la anchura mínima del molde, y Δ es el coeficiente de flexión de la chapa.
Al doblar una chapa de 1,5 mm de espesor, el borde de doblado más corto, Lmin = (8 + 2,5) / 2 + 0,5 = 5,75 mm (incluido el grosor de la placa).
Figura 1-25 Anchura mínima de la matriz
Cuadro 1-11: Radio de curvatura interior de chapa de acero laminada en frío tabla de referencia de material R y altura mínima de flexión
No. | Espesor | V apertura | Radio del punzón R | Altura mínima de flexión |
---|---|---|---|---|
1 | 0.5 | 4 | 0.2 | 3 |
2 | 0.6 | 4 | 0.2 | 3.2 |
3 | 0.8 | 5 | 0,8 o 0,2 | 3.7 |
4 | 1 | 6 | 1 ó 0,2 | 4.4 |
5 | 1.2 | 8(o 6) | 1 ó 0,2 | 5,5(o 4,5) |
6 | 1.5 | 10(u 8) | 1 ó 0,2 | 6,8(o 5,8) |
7 | 2 | 12 | 1,5 o 0,5 | 8.3 |
8 | 2.5 | 16(o 14) | 1,5 o 0,5 | 10,7(o 9,7) |
9 | 3 | 18 | 2 ó 0,5 | 12.1 |
10 | 3.5 | 20 | 2 | 13.5 |
11 | 4 | 25 | 3 | 16.5 |
Nota:
La altura mínima de curvatura viene determinada por el grosor del material.
Para las curvas en V agudas, la curva más corta debe aumentarse en 0,5.
En curvado del aluminio o de acero inoxidable, la altura mínima de doblado puede variar ligeramente. Concretamente, la placa de aluminio requerirá una altura de doblado menor, mientras que la de acero inoxidable chapa de acero necesitará uno mayor. Consulte la tabla anterior para obtener más información.
La Figura 1-26 muestra el estado inicial del doblado en Z. Los procesos de doblado en Z y en L comparten una similitud y se encuentran con el problema del borde mínimo de doblado. Sin embargo, el borde más corto del doblez en Z es mayor que el del doblez en L, debido a la estructura de la matriz inferior. La fórmula utilizada para calcular el borde mínimo del plegado en Z es:
Lmin=1/2(Bmin+Δ)+D + 0.5 + T ③
Lmin se refiere al borde de doblado más corto, mientras que Bmin es la anchura mínima del molde. Δ representa el coeficiente de flexión de la chapa, T se refiere al grosor del material, y D es el tamaño estructural de la matriz inferior hasta el borde, que suele ser superior a 5 mm.
Figura 1-26 Curva en Z
El tamaño mínimo de la curva L para curvas en Z de chapa metálica de diferentes espesores de material se muestra en la Tabla 1-12 a continuación:
Cuadro 1-12 Altura mínima de Curva Z
No | Espesor | V apertura | Radio del punzón R | Altura de curvatura Z L |
---|---|---|---|---|
1 | 0.5 | 4 | 0.2 | 8.5 |
2 | 0.6 | 4 | 0.2 | 8.8 |
3 | 0.8 | 5 | 0,8 o 0,2 | 9.5 |
4 | 1 | 6 | 1 ó 0,2 | 10.4 |
5 | 1.2 | 8(o 6) | 1 ó 0,2 | 11,7(o 10,7) |
6 | 1.5 | 10(u 8) | 1 ó 0,2 | 13,3(o 12,3) |
7 | 2 | 12 | 1,5 o 0,5 | 14.3 |
8 | 2.5 | 16(o 14) | 1,5 o 0,5 | 18,2(o 17,2) |
9 | 3 | 18 | 2 ó 0,5 | 20.1 |
10 | 3.5 | 20 | 2 | 22 |
11 | 4 | 25 | 3 | 25.5 |
Interferencias durante la flexión
En el caso del plegado secundario o de orden superior, es habitual que se produzcan interferencias entre la pieza y la herramienta. La figura 1-27 muestra la zona de interferencia, en negro, que puede impedir el plegado correcto o provocar deformaciones debido a la interferencia.
Figura 1-27 Interferencia de flexión
El problema de las interferencias en el plegado de chapa no es complejo. Simplemente implica comprender la forma y el tamaño de la matriz de plegado y evitarla al diseñar la estructura. La figura 1-28 muestra las formas de sección transversal de varias matrices de doblado típicas, que se detallan en el manual de moldes de chapa y tienen entidades de herramienta correspondientes en la biblioteca intralink.
Si hay incertidumbre en el diseño, se puede realizar una prueba de interferencia de montaje directo utilizando la herramienta basada en el principio que se muestra en la figura.
Figura 1-28 Cuchilla dobladora
Al realizar el doblado de agujeros, es importante evitar diseñar D (como se muestra en la Figura 1-29) demasiado pequeño. El valor mínimo de D puede calcularse o trazarse en función de varios factores, como el grosor del material, el diámetro exterior del agujero pasante, la altura del agujero de la brida y los parámetros seleccionados de la herramienta de doblado.
Por ejemplo, si está realizando un roscado de orificio abatible M4 en una chapa de 1,5 mm, D debe ser superior a 8 mm para evitar que la herramienta de doblado entre en contacto con la pestaña.
Figura 1-29 Doblado del rebordeado de agujeros y golpeteo
La figura 1-30 ilustra que si el borde del orificio se coloca demasiado cerca de la línea de plegado, el proceso de plegado puede hacer que la forma del orificio cambie, ya que no se puede acomodar. Para evitar que esto ocurra, es fundamental asegurarse de que la distancia entre el borde del orificio y la línea de plegado es mayor o igual que el margen mínimo del orificio, que es X ≥ t + R.
Figura 1-30 Distancia mínima del agujero redondo al borde doblado
Tabla 1-13 Distancia mínima del agujero redondo al borde doblado
Espesor | 0.6~0.8 | 1 | 1.2 | 1.5 | 2 | 2.5 |
---|---|---|---|---|---|---|
Distancia mínima X | 1.3 | 1.5 | 1.7 | 2 | 3 | 3.5 |
La figura 1-31 revela que el agujero alargado está situado demasiado cerca de la línea de plegado. En consecuencia, durante el proceso de plegado, el material no puede acomodarse correctamente, lo que provoca una deformación en la forma del orificio. Por lo tanto, es fundamental asegurarse de que la distancia entre el borde del orificio y la línea de pliegue es mayor que el margen mínimo del orificio especificado en la Tabla 1-14. Además, el radio de curvatura se puede encontrar en la Tabla 1-9.
Figura 1-31 Distancia mínima entre el orificio redondo largo y el borde doblado
Tabla 1-14 Distancia mínima del orificio redondo largo al borde doblado
L | <26 | 26~50 | >50 |
---|---|---|---|
Distancia mínima X | 2t+R | 2,5t+R | 3t+R |
Para los agujeros sin importancia, pueden ampliarse hasta el línea de plieguecomo se ilustra en la Figura 1-32. Sin embargo, esto tiene el inconveniente de afectar a la apariencia.
Figura 1-32 Mejorada diseño de plegado
Si la distancia entre el orificio más cercano a la línea de doblado y el borde doblado es inferior a la distancia mínima requerida, pueden producirse deformaciones tras el doblado. Para cumplir los requisitos del producto, puede consultar las posibles soluciones en la Tabla 1-15. No obstante, es fundamental tener en cuenta que estos métodos carecen de precisión técnica, por lo que debe evitarse el diseño estructural siempre que sea posible.
Tabla 1-15 Tratamiento especial cuando el orificio está cerca de la curva
![]() 1) Presionar la ranura antes de doblar.En el diseño real, debido a las necesidades de diseño estructural, la distancia real es menor que la distancia anterior.El fabricante de procesamiento a menudo realiza el prensado de la ranura antes de la flexión, como se muestra en la Figura 1-31.La desventaja es: se necesita un proceso adicional para el procesamiento de flexión, la eficiencia es menor, la precisión es menor, y en principio, debe evitarse tanto como sea posible. |
---|
![]() 2) Cortar agujero o línea a lo largo de la línea de curvatura: cuando la línea de curvatura no tiene ningún efecto sobre la apariencia de la pieza de trabajo o es aceptable, a continuación, utilizar el corte de agujero para mejorar sus técnicas.Desventajas: afectan a la apariencia. Y cuando se corta una línea o cortar una ranura estrecha, por lo general es necesario cortar con una máquina láser. |
![]() 3) Terminación al tamaño de diseño después de doblar en el borde del agujero cerca de la línea de doblado.Cuando se requiere el margen del agujero, se puede manejar de esta manera.Generalmente, esta eliminación de material secundario no se puede completar en una punzonadora, y el segundo corte sólo se puede realizar en el máquina de corte por láserLa colocación es problemática y el coste de procesamiento es elevado. |
![]() 4) Después de la flexión, el proceso de escariado de agujeros sólo tiene uno o varios agujeros de píxeles a la línea de plegado y la distancia es menor que la distancia mínima entre los agujeros.Cuando la apariencia del producto es estricta, con el fin de evitar el dibujo durante el plegado, el píxel se puede realizar en este momento.Tratamiento de contracción, es decir, cortar un pequeño círculo concéntrico (por lo general Φ1,0) antes de la flexión, y el escariado al tamaño original después de la flexión.Desventajas: muchos proyectos, baja eficiencia. |
![]() 5) El ancho mínimo de la matriz superior de la máquina dobladora es de 4.0mm (actual).Debido a esta limitación, el agujero en la parte de doblado de la pieza de trabajo no debe ser inferior a 4.0mm.De lo contrario, la abertura debe ser ampliada o utilizar matriz fácil de formar para realizar el doblado.Desventajas: baja eficiencia en la fabricación del molde fácil, baja eficiencia en la producción del molde fácil; el escariado afecta la apariencia. |
Orificios de proceso, ranuras de proceso y muescas para piezas curvas
Al diseñar el doblez, se recomienda añadir un orificio de proceso de punzonado, una ranura de proceso o una muesca de proceso antes del troquelado si es necesario realizar el doblez en la cara interior de la pieza en bruto, como se muestra en la Figura 1-33.
Figura 1-33 Añadir perforación, proceso o muesca de proceso
Al diseñar una pieza doblada, para evitar el desgarro y la distorsión de los bordes, suele ser necesario crear una ranura para evitar grietas o una hendidura de corte. Esto es especialmente importante cuando el radio de curvatura interior es inferior a 60 grados. La anchura de la hendidura debe ser mayor que el espesor del material (t), y la profundidad de la hendidura debe ser al menos 1,5 veces el espesor del material. Como se muestra en la Figura 1-34, la Figura b se considera una mejor opción de diseño que la Figura a.
Figura 1-34 Doblado de la chapa con la ranura o hendidura de fisura
Las muescas y orificios de proceso deben procesarse adecuadamente. Si la apariencia de las piezas de trabajo es una preocupación y son visibles desde el panel, los agujeros de proceso de esquina para doblado pueden omitirse (por ejemplo, la muesca de proceso no se añade durante el procesamiento del panel para mantener un estilo uniforme). Sin embargo, otros dobleces deben incluir un orificio de proceso de esquina, como se muestra en la Figura 1-35.
Figura 1-35 Agujero de proceso de esquina doblada
Al diseñar los planos, se recomienda evitar marcar la separación entre las intersecciones de doblado en la dirección de 90 grados, a menos que exista un requisito específico. Un marcado incorrecto de la separación puede afectar al diseño del proceso de fabricación. Normalmente, los fabricantes diseñan el proceso con una separación de 0,2 a 0,3, como se ilustra en la Figura 1-36.
Figura 1-36 el espacio entre la curva lapeado
La zona de flexión de un componente doblado debe mantenerse alejada de las zonas con cambios bruscos en la forma del componente. La distancia L de la línea de doblado a la zona de deformación debe ser mayor que el radio de doblado (r), lo que significa L ≥ r, como se muestra en la Figura 1-37.
Figura 1-37 La zona de flexión debe evitar la ubicación del cambio brusco de la pieza
El método para dobladillar: La chapa se dobla primero en un ángulo de 30 grados utilizando una matriz de doblado de 30 grados, como se muestra en la Figura 1-38, y luego se aplana el lado doblado.
Figura 1-38 Método de dobladillado
La dimensión mínima del borde de curvatura, "L", en la Figura 1-38 es 0,5t, donde "t" representa el espesor del material, de acuerdo con el tamaño mínimo del borde de una curvatura descrito anteriormente. La técnica del "borde muerto prensado" se utiliza comúnmente para materiales como el acero inoxidable, chapa galvanizaday chapa de aluminio-cinc. Sin embargo, no deben utilizarse piezas chapadas, ya que puede producirse un atrapamiento de ácido en el lugar del dobladillo.
El método del doblez de 180 grados: Como se muestra en la Figura 1-39, primero doble la placa en un ángulo de 30 grados utilizando una cuchilla de doblado de 30 grados. A continuación, enderece el borde doblado y, por último, retire el protector.
Figura 1-39 Método de la curva de 180 grados
La dimensión mínima del borde de la curva (L) en la figura es igual a la dimensión mínima del borde de la curva de una sola curva más el espesor del material (t). La altura (H) debe seleccionarse entre los tamaños de placa utilizados habitualmente, como 0,5, 0,8, 1,0, 1,2, 1,5 o 2,0. Por lo general, no se recomienda elegir una altura superior a estas opciones. Por lo general, no se recomienda elegir una altura superior a estas opciones.
Como se muestra en la Figura 1-40, primero hay que doblar la forma y luego el borde. Al diseñar, tenga en cuenta las dimensiones de cada componente para garantizar que cada paso del proceso cumple el tamaño mínimo de plegado, evitando así la necesidad de un postprocesado adicional.
Figura 1-40 Dobladillo de plegado triple
Tabla 1-16 Tamaño mínimo del borde de apoyo requerido para el aplanamiento final del borde de flexión
Espesor | 0.5 | 0.6 | 0.8 | 1.0 | 1.2 | 1.5 | 2.0 | 2.5 |
---|---|---|---|---|---|---|---|---|
Tamaño del borde de apoyo L | 4.0 | 4.0 | 4.0 | 4.0 | 4.5 | 4.5 | 5.0 | 5.0 |
Cuando se trabaja con el plegado de chapa metálica, es fundamental dar prioridad a la seguridad y seguir las mejores prácticas del sector para minimizar los riesgos de accidente y garantizar la eficacia operativa. Las siguientes directrices exhaustivas abordan aspectos cruciales de la seguridad en el lugar de trabajo, la manipulación de materiales y la optimización de procesos:
Equipos de protección individual (EPI): Exija el uso de EPI adecuados, como gafas de seguridad con protección lateral, guantes resistentes a los cortes, calzado de seguridad con puntera de acero y protección auditiva. Para las operaciones que impliquen materiales pesados o trabajos por encima de la cabeza, los cascos son esenciales. Cuando se trabaje con metales galvanizados o recubiertos, puede ser necesaria protección respiratoria para protegerse de los humos nocivos.
Sistemas de protección y seguridad de las máquinas: Asegúrese de que todas las prensas plegadoras y máquinas curvadoras estén equipadas con mecanismos de protección adecuados, como cortinas de luz, mandos a dos manos o dispositivos de detección de presencia. Pruebe y mantenga periódicamente estos sistemas de seguridad para garantizar su eficacia en la prevención de accidentes.
Consideraciones ergonómicas: Aplique soluciones ergonómicas para reducir el riesgo de lesiones por esfuerzo repetitivo. Esto puede incluir puestos de trabajo de altura regulable, ayudas para la manipulación de materiales y formación adecuada sobre técnicas de elevación. Para piezas grandes o pesadas, utilice dispositivos mecánicos de elevación o procedimientos de elevación en equipo.
Mantenimiento de herramientas y equipos: Establezca un riguroso programa de mantenimiento preventivo para todos los equipos de plegado, troqueles y herramientas. Las inspecciones, la limpieza y la lubricación periódicas son fundamentales para evitar fallos de funcionamiento que podrían provocar accidentes o problemas de calidad. Mantenga registros de mantenimiento detallados y aborde con prontitud cualquier problema identificado.
Formación exhaustiva de los empleados: Desarrollar y aplicar un programa de formación exhaustivo que abarque:
Selección y manipulación de materiales:
Optimización de procesos:
Organización del espacio de trabajo:
Control de calidad y mejora continua:
Si se siguen meticulosamente estas directrices de seguridad y buenas prácticas, las operaciones de plegado de chapa metálica pueden realizarse con un alto grado de profesionalidad, eficacia y, lo que es más importante, seguridad. Este enfoque integral no sólo protege a los trabajadores, sino que también contribuye a mejorar la calidad del producto y la excelencia operativa general.
Con el rápido desarrollo del sector mundial de equipos industriales, cada vez más equipos de automatización de alto rendimiento han entrado en el campo del procesamiento de chapa metálica, proporcionando garantías de productividad fundamentales para el desarrollo de alta calidad de la industria de procesamiento de chapa metálica. El desarrollo de la globalización industrial también ha traído consigo más competencia y desafíos, y las demandas del mercado cambian constantemente. Esto no sólo requiere que el equipo principal tenga un alto nivel de productividad, sino que también plantea mayores exigencias en cuanto a la flexibilidad y la capacidad de cambio rápido de todo el sistema de producción.
Como una de las tecnologías de proceso clave en el campo del procesamiento de metales, el plegado de chapa desempeña un papel indispensable en la producción de productos metálicos. El método tradicional de producción de operaciones de plegado con una sola máquina tiende a provocar tiempos de inactividad de los equipos durante los cambios de pedido. Hay una excesiva intervención manual en la comprobación de planos, la programación del plegado, el ajuste de los parámetros del equipo, el desmontaje y montaje de los moldes de plegado y la manipulación del material. Por lo tanto, el equipo tiene que parar y esperar para el cambio de pedido y el transporte del material, lo que se traduce en elevados costes de producción.
Para abordar los problemas mencionados en el proceso de plegado de chapa metálica, se puede investigar desde las perspectivas del diseño de procesos, la innovación de moldes, la automatización, la informatización y la tecnología inteligente. Se trata de integrar e introducir tecnologías avanzadas en el proceso de plegado de chapa. Por ejemplo, optimizando el diseño de la estructura del proceso del producto, mejorando la controlabilidad de los materiales del molde y la velocidad de cambio de la estructura, utilizando la tecnología industrial de Internet para la transmisión y comunicación de la información, integrando sistemas de control interactivo PLC y aplicando sistemas de gestión de la informatización de la producción.
El sistema de gestión de la información permite recopilar, procesar y analizar datos en tiempo real durante el proceso de producción de plegado de chapa metálica. A través de la plataforma de computación en la nube, se puede lograr la supervisión y gestión remotas de los datos, optimizando los procesos de producción. Además, la aplicación de líneas de producción automatizadas que integran equipos como máquinas herramienta y robots industriales, sistemas de carga y descarga automatizados y sistemas de inspección en línea mejora enormemente la capacidad de control de todo el proceso de producción. La aplicación de la tecnología de control interactivo automatizado reduce eficazmente la intervención manual y permite una producción continua, lo que mejora la eficacia de la producción y da lugar a productos de plegado más estables y fiables.
El desarrollo de la tecnología de plegado de chapa se basa en la actualización y aplicación de la tecnología de automatización, informatización y sistemas inteligentes dentro de la industria. Como eslabón fundamental de la industria metalúrgica, la evolución de los procesos de plegado de chapa refleja la mejora de las capacidades de fabricación industrial e indica las direcciones futuras de la industria manufacturera. Desde las operaciones manuales iniciales hasta la moderna integración de la automatización CNC, el proceso de plegado de chapa ha experimentado múltiples transformaciones significativas. Cada salto tecnológico ha ido acompañado de mejoras sustanciales en la eficiencia de la producción y la calidad del producto.
En las primeras etapas del doblado manual, las planchas de metal se doblaban utilizando herramientas sencillas y experiencia. Aunque el proceso de plegado manual era muy adaptable, estaba limitado por la precisión y estabilidad de las operaciones humanas. Esto se traducía en una baja eficiencia de la producción y dificultaba satisfacer las necesidades de la producción estandarizada a gran escala. Con la aceleración de la industrialización, la industria metalúrgica empezó a introducir gradualmente equipos de plegado mecánico, como las plegadoras manuales y las plegadoras mecánicas. Estos dispositivos proporcionaban una fuerza estable a través de principios mecánicos, mejorando significativamente la eficiencia de la producción y la consistencia del producto.
Las modernas líneas de producción de plegado de chapa metálica suelen estar equipadas con avanzadas máquinas de plegado CNC, que pueden controlar con precisión los ángulos y las posiciones de plegado, mejorando significativamente la precisión y la repetibilidad del plegado de chapa metálica.
La programación informática permite controlar con precisión las acciones de las plegadoras y fabricar rápidamente piezas metálicas de formas complejas. Con la adopción del diseño asistido por ordenador (CAD) y la fabricación asistida por ordenador (CAM), la producción de moldes es más eficaz y precisa. La aplicación de la tecnología de prototipado rápido facilita las modificaciones y optimizaciones de moldes, acortando el tiempo desde el diseño hasta la comercialización. El desarrollo de moldes modulares inteligentes permite realizar cambios rápidos y un mantenimiento oportuno durante su uso, mejorando la eficacia productiva de las operaciones de plegado.
El diseño estructural de los productos de plegado de chapa metálica debe incorporar la aplicación de conocimientos multidisciplinares, como las propiedades de procesamiento de los materiales metálicos, los principios de ingeniería mecánica relacionados y los procesos de fabricación. Los requisitos funcionales y el entorno de uso del producto también influirán en la selección de materiales y el diseño estructural. Es necesario elegir materiales metálicos de alta resistencia y resistentes a la corrosión y diseñar las estructuras de refuerzo correspondientes. Además, teniendo en cuenta el grosor del material, la procesabilidad de las estructuras del producto y las características de deformación plástica de los materiales, es crucial establecer áreas de flexión razonables para evitar el estiramiento o la compresión excesivos, garantizando la precisión dimensional y la resistencia estructural del producto. En la figura siguiente se muestra un diagrama esquemático del proceso de plegado de chapa metálica.
Además, durante la fase de diseño deben tenerse en cuenta las limitaciones de producción, como el radio de curvatura y los ángulos de curvatura. Es importante seguir los principios de la secuencia de curvado: curvar de dentro a fuera, curvar de pequeño a grande, curvar primero las formas especiales y después curvar las formas generales, asegurándose de que el proceso de conformado inicial no afecta ni interfiere con los procesos posteriores.
El diseño del proceso es un paso clave para garantizar que los productos se fabrican de acuerdo con unas normas de calidad y una eficiencia de producción predeterminadas. Esto incluye la selección del equipo de plegado adecuado, el establecimiento de diseños detallados del flujo del proceso y el diseño de moldes precisos. Al seleccionar el equipo de plegado, es esencial tener en cuenta la precisión y estabilidad del equipo y su idoneidad para materiales de distintos grosores y niveles de dureza.
El diseño de los moldes de plegado también es una parte importante del diseño del proceso, ya que afecta directamente a la calidad del producto y a la eficiencia de la producción. Un buen diseño de molde debe garantizar un flujo suave del metal durante el doblado, reducir el riesgo de grietas y roturas, y tener en cuenta la durabilidad y los costes de mantenimiento del molde. Con el desarrollo de las tecnologías de diseño asistido por ordenador y fabricación asistida por ordenador, el diseño de moldes moderno puede ser más preciso y eficaz, permitiendo incluso la simulación y optimización en la fase de diseño. Al desarrollar los flujos del proceso, también es necesario tener en cuenta la eficacia de la producción y el control de costes, al tiempo que se garantiza que cada paso consigue los resultados de procesamiento esperados.
Los procesos tradicionales de plegado de chapa dependen en gran medida de los operarios, y la calidad del producto se ve fácilmente influida por el estado del operario. Suele ser un cuello de botella en el proceso de transformación de productos metálicos. Por lo tanto, el desarrollo y la adopción de tecnología de procesamiento automatizado para sustituir gradualmente las operaciones de plegado manual es de gran importancia para mejorar la eficiencia de la producción. En la figura 2 se muestra el procesamiento de piezas mediante equipos de plegado manuales.
El procesamiento automático de plegado de chapa metálica es una representación típica de la aplicación de tecnología avanzada en la producción durante la era industrial, con la aplicación de unidades de procesamiento automatizadas de alta eficiencia, alta calidad y gran flexibilidad cada vez más maduras.
Desde el desarrollo del procesamiento automatizado de plegado de chapa metálica, existen principalmente tres tipos de tecnologías de procesamiento automatizado: procesamiento de plegado con manipulador fijo, procesamiento de plegado con robot industrial y procesamiento automático con unidad de plegado multiborde. Cada tipo de método de procesamiento automatizado de plegado tiene sus ventajas, y los directores de fábrica necesitan considerar los beneficios integrales cuando los introducen simultáneamente.
La unidad de plegado automático del brazo mecánico puede dividirse en unidad de plegado integrada de manipulador de tres ejes X, Y y unidad de plegado integrada de robot industrial según los diferentes dispositivos de integración de automatización. El plegado con manipulador de tres ejes se utiliza principalmente para la producción en masa y productos de chapa de estructura espacial relativamente simple, como piezas en forma de caja, piezas de ranura, piezas de caja, etc. Su principal ventaja es el bajo coste de inversión, la alta eficiencia para piezas producidas en masa, pero debido a las limitaciones de su pista de rodadura espacial y la poca flexibilidad estructural, no puede hacer frente al cambio frecuente de producción.
Por otro lado, la unidad automática de plegado integrada con robots industriales es más ventajosa en el proceso de desarrollo de la demanda del mercado moderno. Para superar las limitaciones del rango operativo de los robots de seis ejes existentes, la integración de la pista móvil inferior puede lograr operaciones de movimiento flexibles del robot en diferentes estaciones de trabajo, lo que aumenta aún más la compatibilidad de la unidad de plegado para el procesamiento de productos.
El robot se desplaza hasta la posición de la máquina curvadora, coloca la lámina de material plana sobre la matriz inferior de la máquina curvadora y, a través del sensor de calibre trasero de la máquina curvadora, realiza un posicionamiento preciso. Una vez completado el posicionamiento, el robot envía la señal de doblado a la máquina dobladora y completa la acción de doblado en coordinación con la máquina dobladora.
La precisión de curvado de la unidad de curvado del robot industrial depende de la precisión de la propia máquina curvadora, la precisión de posicionamiento del robot y el control coordinado del robot y la máquina curvadora. La unidad estándar de procesamiento de plegado por robot está centrada en el robot industrial y la máquina plegadora, equipada con dispositivos mecánicos, estantes de materia prima, pilas de descarga, bancos de trabajo de posicionamiento, estantes de volteo, dispositivos de cambio de mano y varios sensores de detección. La unidad de plegado integrada con el robot industrial se muestra en la Figura 3.
El manipulador es la "mano" que el robot utiliza para sustituir a los humanos en la recogida y colocación de las piezas de trabajo. El manipulador del robot plegador suele estar compuesto por múltiples ventosas instaladas en un bastidor metálico, y puede ajustar con flexibilidad la posición y la estructura de ramificación de las ventosas para lograr la compatibilidad con distintos tamaños de piezas y ángulos de plegado. Las mesas de carga y descarga suelen utilizar palés apilados, pero también pueden emplearse cintas transportadoras u orugas para transportar materias primas y productos acabados.
La mesa de trabajo de posicionamiento es una plataforma inclinada con bordes elevados, con bolas ligeramente elevadas distribuidas por la superficie de la mesa. El robot transfiere la placa de acero a la mesa de posicionamiento, donde la placa se desliza libremente hasta el borde elevado debido a la gravedad. Cuando el robot vuelve a sujetar la placa, la posición de la placa y de la pinza se ha ajustado con precisión, lo que proporciona una referencia para el siguiente paso del plegado.
La unidad automática integrada de plegado por varios lados se diferencia del método en el que el manipulador agarra las piezas para plegarlas. En su lugar, utiliza el manipulador para mover las piezas en coordinación con la máquina dobladora para completar el proceso de doblado. Generalmente, el molde de doblado configurado en esta unidad también tiene una gran flexibilidad. La exitosa aplicación de la unidad integrada de plegado automático de múltiples lados en la industria manufacturera ha mejorado significativamente las capacidades de mecanizado y fabricación de los equipos de máquinas herramienta de China.
La unidad integrada de plegado automático por varios lados incluye un dispositivo de carga, un dispositivo transportador de lanzadera, un manipulador de la plegadora principal y un dispositivo de descarga, como se muestra en la figura 4. El manipulador está situado directamente delante de la plegadora principal, con los sistemas automáticos de carga y descarga situados en los lados izquierdo y derecho de la plegadora, respectivamente. El manipulador está situado directamente delante de la máquina curvadora principal, y los sistemas de carga y descarga automáticos están situados en los lados izquierdo y derecho de la máquina curvadora, respectivamente.
Los dispositivos automáticos de carga y descarga y el dispositivo transportador de lanzadera conectan automáticamente con el almacén vertical para colocar las materias primas, sustituyendo el trabajo manual para colocar las chapas o piezas de trabajo en el lugar de procesamiento, y permiten la entrada y salida automática de piezas al banco de trabajo. El manipulador presiona y dobla las placas para su procesamiento; la máquina dobladora principal completa el trabajo de doblado y conformado de placas de acuerdo con los códigos de lenguaje de máquina del programa. Mediante el control de procesamiento de piezas de alta precisión, el tratamiento especial de la superficie del molde y el control especial sobre la pista de rodadura del molde, la máquina dobladora de múltiples caras garantiza el procesamiento eficaz y de alta calidad de las piezas de chapa metálica.
Durante el proceso de plegado, el sistema de servoaccionamiento eléctrico controla el movimiento del molde de plegado, lo que permite una respuesta de alta velocidad y un rápido movimiento curvo del molde, logrando acciones de plegado rápidas y precisas, y realizando un procesamiento de plegado de alta velocidad. Mediante el control de la lógica de acción y la pista de funcionamiento de un conjunto de moldes, se puede realizar el procesamiento de piezas complejas. Este conjunto de moldes se denomina molde universal.
La plegadora, que utiliza un único conjunto de moldes versátiles, puede realizar diversos procesos, como plegado en ángulo positivo y negativo, arcos de gran tamaño y bordes planos complejos, logrando una gran flexibilidad en el procesamiento. El dispositivo automático de cambio de troquel consta de piezas como el troquel de holgura intermedia, el troquel de sección estándar, el dispositivo de movimiento del embrague y el dispositivo de pieza de inserción giratoria. Tiene dos funciones principales: retracción de la holgura para el canteado y ajuste automático de la longitud, para facilitar las operaciones de doblado en diferentes dimensiones direccionales.