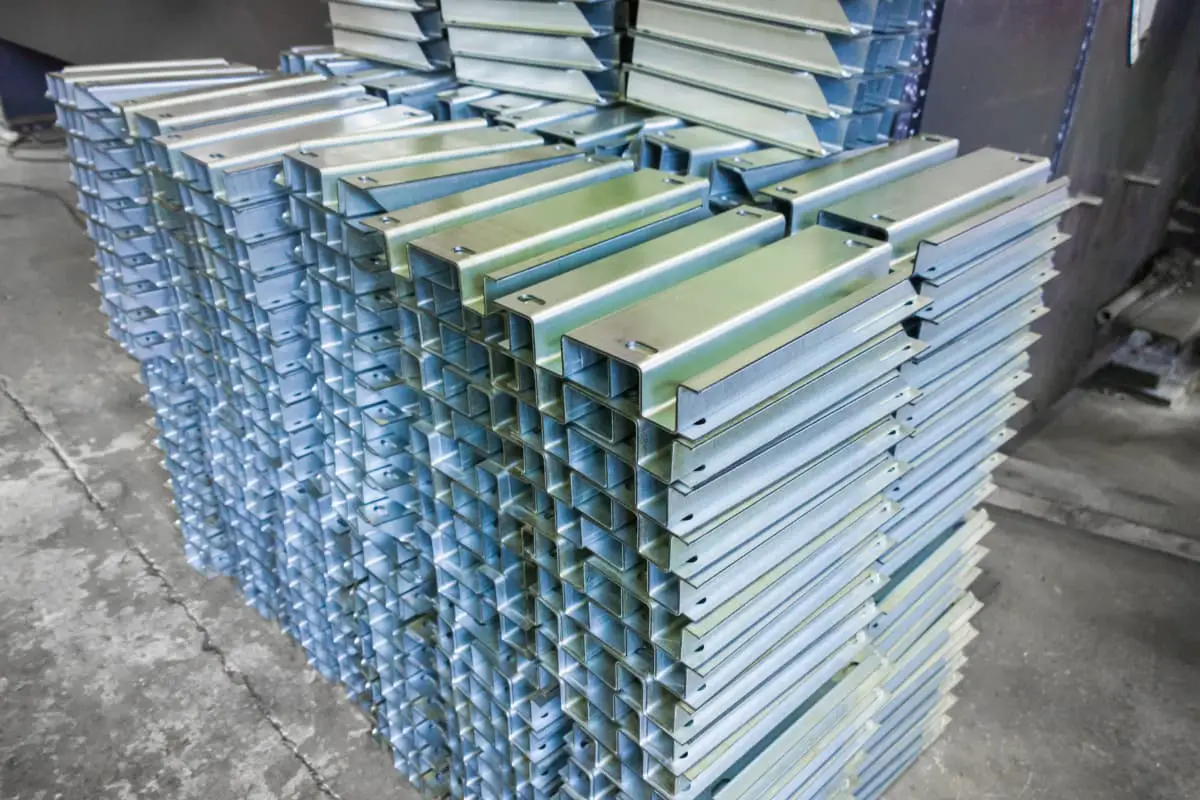
¿Cómo podemos garantizar uniones seguras y duraderas en la fabricación de chapas metálicas? En este artículo se analizan diversas técnicas de unión y fijación, como el remachado TOX, la soldadura y el remachado con clavos. Descubrirá los pros y los contras de cada método, sus aplicaciones prácticas y cómo contribuyen a la resistencia e integridad de las estructuras metálicas. Sumérjase para comprender qué técnicas se adaptan mejor a sus necesidades específicas de fabricación.
Existen varios tipos de conexiones, que pueden dividirse en dos categorías en función de si son extraíbles tras la conexión: conexiones extraíbles y conexiones no extraíbles.
Este capítulo trata principalmente de las uniones no desmontables, incluido el remachado TOX, la soldadura, el punzonado y remachado, y el remachado con clavos.
1. Definición:
Utilizando un molde convexo simple, la pieza de conexión se introduce a presión en el molde cóncavo. Bajo presión adicional, el material del interior del molde cóncavo fluye hacia el exterior, lo que da como resultado un punto de conexión circular liso y sin rebabas.
Esto no afectará a su resistencia a la corrosión, ni siquiera en el caso de materiales de chapa con revestimientos o capas pintadas. Esto se debe a que los revestimientos y las capas de pintura también se deforman y fluyen junto con el material.
El material se aprieta hacia ambos lados y se introduce en la placa por el lado cóncavo del molde, formando un punto de conexión TOX, como se muestra en el diagrama siguiente:
2. Método de conexión:
El remachado TOX puede utilizarse para unir dos o más capas de chapas de materiales y espesores iguales o diferentes.
En las mismas condiciones, la fuerza de conexión estática de un punto único TOX es de 50%-70% de soldadura por puntosLa resistencia de los puntos dobles es la misma que la de la soldadura por puntos.
3. Rango de conexión de los diferentes puntos de remache: (unidad mm)
Diámetro del remache | 12 | 10 | 8 | 6 | 5 | 4 | 3 |
Gama de espesores de material para la conexión | 4~11 | 1.75~7 | 1.6~6.0 | 1.0~3.0 | 0.9~2.5 | 0.6~2.0 | 0.5~1.5 |
Distancia mínima del borde al centro del remache TOX | 10 | 8 | 7 | 6 | 6 | 5 | 4 |
Nota: El diámetro del remache TOX está estrechamente relacionado con la resistencia de la conexión. Cuanto mayor sea el diámetro, más resistente será la conexión.
4. Defectos del remachado TOX:
(1) Se basa en dispositivos de posicionamiento o mordazas para el posicionamiento.
(2) La anchura mínima del material conectado se ve afectada por el diámetro del molde TOX.
5. Ventajas del moho TOX:
Además de utilizarse en equipos especializados, también es apto para la punzonadoraspor lo que su rango de remachado es mucho mayor que el que requiere TOX.
En el caso de materiales de chapa con revestimientos o capas pintadas, la capa protectora en el punto de conexión no se daña y se conservan las propiedades anticorrosión originales.
6. Diagrama esquemático de la formación de remaches TOX:
La esencia de la proceso de soldadura consiste en utilizar procesos físicos y químicos adecuados para acercar los átomos metálicos de dos superficies separadas a la distancia de retícula (0,3-0,5 nm), formando un enlace metálico, de modo que los dos metales se conecten en uno solo y logren el propósito de la soldadura.
En el proceso de fabricación, el gas inerte de tungsteno Soldadura por arco (TIG), la soldadura por arco con gas inerte metálico (MIG) y la soldadura por puntos son los métodos de soldadura más comunes. A continuación se ofrece una breve introducción a estos tres métodos de soldadura:
A. Soldadura por arco con gas inerte de tungsteno
La soldadura TIG es una proceso de soldadura en el que el electrodo y la zona del arco, así como el metal fundido, están protegidos por gas argón, aislándolos del aire.
El electrodo está hecho de tungsteno o de una varilla de aleación de tungsteno, y no se funde durante el proceso de combustión del arco, lo que da como resultado un proceso de soldadura estable.
Cuando se utiliza gas helio como gas protectorse denomina soldadura por arco de helio.
Soldadura TIG se utiliza ampliamente en industrias como la fabricación aeronáutica, la energía atómica, la ingeniería química y la textil.
Es adecuado para soldar metales no ferrosos fácilmente oxidables y sus aleaciones, acero inoxidable, aleaciones de alta temperatura, titanio y aleaciones de titanio, y metales reactivos difíciles de fundir como el molibdeno, el niobio y el circonio.
Sin embargo, la capacidad de transporte de corriente de los electrodos de wolframio es limitada, y la potencia del arco está restringida, lo que resulta en poca profundidad de soldadura, baja velocidad de soldaduray sólo es adecuado para soldar piezas con un grosor inferior a 6 mm.
B. Soldadura por arco con gas inerte metálico
La soldadura MIG, también conocida como Gas Arco metálico Soldadura (GMAW), utiliza un hilo de soldadura como electrodo, y el electrodo y la zona del arco están protegidos por un gas inerte como el argón.
Si se utiliza Ar-O2, Ar-CO2 o Ar-CO2-O2 como gas de protección, se denomina soldadura con gas activo metálico (MAG).
La soldadura MIG puede soldar casi todos los metales y es especialmente adecuada para soldar aluminio y sus aleaciones, cobre y sus aleaciones, acero inoxidable, etc.
Dado que se utiliza un hilo de soldadura como electrodo, puede emplearse una corriente de alta densidad, lo que da como resultado una gran profundidad de fusión y una rápida velocidad de llenado.
Es adecuada para soldar chapas gruesas de aluminio y cobre, y la deformación de la soldadura es menor que la de la soldadura TIG.
La soldadura MIG también puede utilizar la conexión inversa de CC y tiene un buen efecto de pulverización catódica al soldar aluminio y sus aleaciones.
Además, el efecto inherente de autoajuste del arco subsónico es más significativo en la soldadura MIG cuando se suelda aluminio y sus aleaciones.
C. Soldadura por puntos
La soldadura por puntos es un proceso de soldadura en el que la superficie de contacto y sus alrededores de la unión se funden por el calor de resistencia generado por el contacto entre los electrodos y la pieza, y luego se solidifican para formar un punto de soldadura.
Se puede utilizar para la soldadura mixta de aluminio y hierro, aluminio y cobre, acero inoxidable y hierro fundido, pero es más difícil de detectar soldar aluminio y aluminio.
D. Soldadura
La soldadura fuerte es un método de unión de dos o más piezas de metal mediante el uso de un metal de aportación con un punto de fusión inferior al del metal base.
El metal de aportación se funde y humedece el metal base por capilaridad, formando una unión resistente al solidificarse.
La soldadura fuerte requiere calentamiento y protección para evitar que el metal de aportación fundido entre en contacto con el aire.
Existen varios tipos de métodos de soldadura fuerte según las distintas fuentes de calor y condiciones de protección, como la soldadura fuerte por llama, la soldadura fuerte por inducción, la soldadura fuerte en horno de resistencia, la soldadura fuerte en baño de sales, etc.
Los equipos de soldadura existentes pueden dividirse a grandes rasgos en tres tipos: máquinas de soldadura por puntosMáquinas de soldadura manual (MIG y TIG) y robots de soldadura (MIG y TIG).
A. Máquina de soldadura por puntos:
Soldadora fija por puntos tipo C:
Qilong 100KVA AC IC máquina de soldadura por puntos de control síncrono
Soldadora por puntos de compensación de corriente secundaria controlada por microordenador Panasonic 100KVA AC (tecnología japonesa, producida por Panasonic Tangshan)
Lo anterior máquinas de soldadura por puntos puede soldar chapas de acero galvanizado, chapas de acero laminado en frío, chapas de acero inoxidable, hierro boca de caballo, chapas de acero laminado en caliente, con un rango de espesor de 0,3 mm-6 mm para la junta solapada de dos placas.
Máquina de soldadura por puntos suspendida:
Quanxing marca 48KVA suspendido máquina de soldadura por puntos (producido en Taiwán), puede soldar espesor de la placa rango de 0,2-3 mm para lap joint de dos placas.
Máquina de soldadura por puntos de tipo acumulador de condensadores:
Pengyuwei 4500J condensador de almacenamiento tipo de máquina de soldadura por puntos, puede soldar aluminio y aluminio placas de aleación con un grosor de 0,4 mm a 3,0 mm.
B. Máquina de soldadura manual MIG:
Existen la máquina de soldadura MIG de pulso DC 350P de OTC y la máquina de soldadura MIG350A de American Flymat, que pueden soldar acero blando con un grosor de placa de 0,8 mm o superior, y aluminio y aleaciones de aluminio con un grosor igual o superior a 2 mm.
C. Máquina de soldadura manual TIG:
Soldadora TIG de pulsos de doble uso Hitachi HITACHI AC/DC, que puede soldar acero blando con un espesor de chapa de 0,4 mm o superior, y aluminio y aleaciones de aluminio con un espesor de 1,0 mm o superior.
D. Robot de soldadura MIG:
Hay robots de soldadura MIG ABB suecos y robots de soldadura MIG MOTOMAN WF200 de la empresa japonesa YAKAWA, que pueden soldar placas de acero galvanizado, placas de acero laminado en frío, placas de acero inoxidable, hierro boca de caballo, placas de acero laminado en caliente, con un rango de espesor de 0,8 mm o superior.
E. Robot de soldadura TIG:
Hay robots suecos ABB TIG de soldadura sin relleno, que pueden soldar chapas de acero galvanizado, chapas de acero laminado en frío, chapas de acero inoxidable, hierro boca de caballo, chapas de acero laminado en caliente con un espesor de 0,4 mm o superior.
Símbolos de soldadura y los códigos de métodos de soldadura son símbolos o códigos normalizados que se utilizan en los planos estructurales de soldadura, y constituyen una especie de lenguaje de ingeniería.
Los símbolos de soldadura y los códigos de métodos de soldadura en China se definen en las normas nacionales GB324-88 "Método de representación de símbolos de soldadura" y GB5185-85 "Códigos de representación de soldadura y procesos afines en planos".
Estas normas son básicamente coherentes con las normas internacionales ISO2553-84 "Método de representación de símbolos de soldadura" e ISO4063-78 "Representación de la soldadura y procesos afines en diagramas".
Por lo tanto, pueden utilizarse indistintamente.
I. Símbolos de soldadura
La norma GB324-88 "Método de Representación de Símbolos de Soldadura" especifica que los símbolos de soldadura son aplicables tanto a la soldadura por fusión como al soldadura por resistencia.
La norma también especifica que, para simplificar el dibujo, deben utilizarse generalmente símbolos de soldadura para representar las soldaduras en el dibujo, pero también pueden emplearse métodos de dibujo técnico.
Los símbolos de soldadura especificados por la norma nacional incluyen símbolos básicos, símbolos suplementarios y símbolos de tamaño de soldadura.
Los símbolos de soldadura se componen generalmente de símbolos básicos y líneas de referencia, y pueden añadirse símbolos suplementarios, símbolos de tamaño de soldadura y otros símbolos según sea necesario.
Los símbolos básicos representan la forma de la sección transversal de la soldadura. Los 13 símbolos básicos especificados en la norma GB324-88 se muestran en la Tabla 1-3.
Los símbolos suplementarios de soldadura representan las características superficiales de la soldadura. Los tres símbolos suplementarios especificados en la norma GB324-88 se muestran en la Tabla 1-4.
Los símbolos adicionales de soldadura se utilizan para complementar ciertas características de la soldadura. Los símbolos adicionales especificados en la norma GB324-88 se muestran en la Tabla 1-5.
Los símbolos de tamaño de soldadura representan las dimensiones características de la ranura y la soldadura. Los 16 símbolos de tamaño especificados en la norma GB324-88 se muestran en la Tabla 1-6.
Tabla 1-3: Símbolos básicos de soldadura.
Número de serie | Nombre | Diagrama esquemático | Símbolo |
1 | Soldadura de bordes (fusión completa del borde) | ![]() | ![]() |
2 | Soldadura en I | ![]() | ![]() |
3 | Soldadura en V | ![]() | ![]() |
4 | Soldadura en V por un solo lado | ![]() | ![]() |
5 | Soldadura en V con borde romo | ![]() | ![]() |
6 | Soldadura en V por un solo lado con borde romo | ![]() | ![]() |
7 | Soldadura en forma de U con borde romo | ![]() | ![]() |
8 | Soldadura en forma de J con borde romo | ![]() | ![]() |
9 | Soldadura por costura | ![]() | ![]() |
10 | Soldadura de esquina | ![]() | ![]() |
11 | Soldadura de tapón o de ranura | ![]() | ![]() |
12 | Soldadura por puntos | ![]() | ![]() |
13 | Soldadura a tope | ![]() | ![]() |
Tabla 1-4: Símbolos auxiliares de soldadura
número de serie | nombre | diagrama esquemático | símbolo | instrucción |
1 | Símbolo plano | ![]() | ![]() | Superficie de soldadura enrasada (generalmente se consigue mediante mecanizado) |
2 | Símbolo cóncavo | ![]() | ![]() | Superficie de soldadura cóncava |
3 | Símbolo convexo | ![]() | ![]() | Superficie de soldadura convexa |
Tabla 1-5: Símbolos de soldadura suplementarios
número de serie | nombre | diagrama esquemático | símbolo | instrucción |
1 | Símbolo de la barra de respaldo | ![]() | ![]() | Para indicar una soldadura con una barra de respaldo en la raíz |
2 | Símbolo de soldadura | ![]() | ![]() | Para indicar una soldadura en tres lados |
3 | Símbolo de soldadura circunferencial | ![]() | ![]() | Para indicar una soldadura alrededor de la circunferencia de una pieza de trabajo |
4 | Símbolo in situ | ![]() | Para indicar la soldadura realizada in situ o sobre el terreno | |
5 | Símbolo de cola" es la traducción de | ![]() | Puede consultar el contenido de GB5185 para marcar los métodos del proceso de soldadura, etc. |
Tabla 1-6: Símbolos de las dimensiones de soldadura
número de serie | nombre | diagrama esquemático | número de serie | nombre | diagrama esquemático |
d | Grosor de la pieza | ![]() | aa | Ángulo de bisel | ![]() |
b | Brecha radicular | ![]() | l | Longitud de soldadura" es la traducción de | ![]() |
p | Borde romo | ![]() | n | Número de segmento de soldadura | ![]() |
c | Anchura de soldadura | ![]() | e | Distancia entre soldaduras | ![]() |
d | Diámetro de fusión | ![]() | K | Tamaño del brazo de soldadura | ![]() |
S | Grosor efectivo de la garganta | ![]() | H | Profundidad de la ranura | ![]() |
N | Símbolo de cantidad para soldaduras idénticas | ![]() | h | Altura del refuerzo | ![]() |
R | Radio de la raíz | ![]() | b | Ángulo de bisel de la cara de la ranura | ![]() |
2. Códigos de métodos de soldadura
Para simplificar el marcado y la descripción de los métodos de soldadura, los distintos métodos de soldadura, como la soldadura metálica y la soldadura _, pueden representarse mediante números arábigos especificados en la norma nacional GB5185-85.
La tabla 1-7 muestra los códigos de los métodos de soldadura más utilizados especificados en la norma nacional GB5185-85.
Tabla 1-7: Códigos de los principales métodos de soldadura utilizados habitualmente.
Nombres de los métodos de soldadura | Códigos de métodos de soldadura | Nombres de los métodos de soldadura | Códigos de métodos de soldadura |
Soldadura por arco | 1 | Soldadura a presión | 4 |
Soldadura por arco de metal protegido (SMAW) | 111 | Soldadura por fricción | 42 |
Soldadura por arco sumergido (SAW) | 12 | Soldadura por difusión | 45 |
Gas soldadura por arco de tungsteno (GTAW) con gas de protección inerte, también conocido como soldadura con gas inerte de tungsteno (TIG) | 131 | Otros métodos de soldadura | 7 |
Soldadura por arco metálico con gas inerte (GMAW), también conocida como soldadura MIG (Metal Inert Gas) | 135 | Soldadura por electroescoria (ESW) | 72 |
Soldadura por arco metálico con gas (GMAW) con gas de protección no inerte, también conocida como soldadura con gas activo metálico (MAG). | 141 | Soldadura por electrogás (EGW) | 73 |
Arco de plasma soldadura (PAW) | 15 | Soldadura láser | 751 |
Soldadura por resistencia | 2 | Soldadura por haz de electrones | 76 |
Soldadura por puntos | 21 | Soldadura de pernos | 78 |
Soldadura por puntos | 22 | Soldadura fuerte | |
Soldadura flash | 24 | Soldadura fuerte | 9 |
Soldadura por resistencia a tope | 25 | Soldadura blanda | 91 |
Soldadura con gas | 3 | Soldadura. | 94 |
Soldadura por oxicorte. | 311 | – | – |
3. Colocación de símbolos de soldadura en los planos
3.1 Requisitos básicos:
El método completo de representación de soldaduras en dibujos incluye no sólo los símbolos básicos, los símbolos auxiliares y los símbolos suplementarios, sino también las líneas de referencia, algunos símbolos de cotas y datos.
Los símbolos de soldadura y los códigos de los métodos de soldadura deben representarse con precisión mediante líneas de referencia y especificaciones pertinentes.
Las líneas de referencia suelen constar de dos partes: una línea de flecha con una punta de flecha y dos partes de línea de base (una línea continua y otra discontinua).
3.2 Relación entre flecha y articulación:
La siguiente figura ofrece un ejemplo del significado del lado con flecha y del lado sin flecha de una junta:
La posición de las líneas de flecha:
Por lo general, no hay requisitos especiales para la posición de las líneas de flecha en relación con las soldaduras, pero cuando se indican soldaduras en V, en V simple y en forma de J, la línea de flecha debe apuntar hacia el lado de la pieza con la ranura. Si es necesario, la línea de flecha puede doblarse una vez.
3.4 Posición de la línea de base:
La línea discontinua de la línea de base puede dibujarse en la parte superior o inferior de la línea continua de la línea de base. Por lo general, la línea de base debe ser paralela al borde inferior del dibujo, pero también puede ser perpendicular al borde inferior en condiciones especiales.
3.5 Posición de los símbolos básicos respecto a la línea de base:
Si la soldadura y la línea de flecha están en el mismo lado de la junta, el símbolo básico de la soldadura debe marcarse en el lado de la línea sólida.
Por ejemplo, como se muestra en la siguiente figura:
Si la soldadura se encuentra en el lado no estrecho de la junta, el símbolo básico de la soldadura deberá marcarse en el lado de la línea discontinua de la línea de base.
Cuando se marcan soldaduras simétricas y soldaduras de doble cara, no es necesario añadir líneas discontinuas.
4. Símbolos de tamaño de soldadura y sus posiciones de anotación:
4.1 Los principios para el marcado de los símbolos y datos del tamaño de la soldadura se muestran en la siguiente figura:
El tamaño en la sección transversal de la soldadura se marca a la izquierda del símbolo básico.
El tamaño en la dirección longitudinal de la soldadura se marca a la derecha del símbolo básico.
Las medidas como el ángulo de la ranura, el ángulo de la cara de la ranura y la separación de la raíz están marcadas en la parte superior o inferior del símbolo básico.
El símbolo del número de soldaduras idénticas está marcado en la cola.
Cuando hay muchos datos de tamaño que son difíciles de distinguir, se puede añadir el símbolo de tamaño correspondiente delante de los datos.
Los principios anteriores no cambian cuando cambia la dirección de la flecha.
4.2 Explicación de los símbolos de cota:
Las dimensiones que determinan la ubicación de la soldadura no figuran en el símbolo de soldadura, sino que están marcadas en el patrón.
Cuando no hay ninguna anotación o explicación a la derecha del símbolo básico, significa que la soldadura es continua en toda la longitud de la pieza.
Cuando no hay ninguna anotación o explicación a la izquierda del símbolo básico, significa que la soldadura a tope debe estar totalmente penetrada.
Para las soldaduras de tapón y las soldaduras de ranura con bordes biselados, debe indicarse la dimensión del fondo del orificio.
1. Comprender el dibujo:
En el proceso de fabricación, cuando el personal de diseño de procesos recibe el dibujo, el primer paso es comprender la estructura de la pieza.
Basándose en esto, comprenda el contenido de la soldadura requerido por el cliente, incluida la ubicación de la soldadura, el método de soldadura que se utilizará, si se requiere pulido y otros requisitos especiales.
Es muy importante comprender la intención del cliente, que determina el flujo del proceso que adoptaremos más adelante.
2. Determinación del método de soldadura:
Por lo general, en el plano del cliente ya se han marcado claramente el método de soldadura y los requisitos: si se va a utilizar soldadura por puntos o por puntos, qué longitud debe tener el cordón de soldadura, el tamaño de la sección transversal, etc.
Sin embargo, en algunos casos, como cuando pensamos que sería mejor cambiar de la soldadura por puntos a la soldadura fuerte, podemos confirmar el cambio de método de soldadura con el cliente.
3. Determinación de la Junta de soldadura:
La unión de soldadura más común se produce cuando los dos lados de la pieza se cruzan verticalmente al auto soldarse. Como se muestra en la Figura 1 a continuación:
Tenga en cuenta que, en la mayoría de los casos, los clientes pueden no haber considerado soldabilidady es posible que la unión no cumpla necesariamente los requisitos reales de soldadura.
Por lo tanto, generalmente se requieren ajustes al soldar en casos como uniones perpendiculares de 90 grados.
Como se muestra en las figuras 2 y 3, la figura 2 es la más adecuada para la soldadura TIG con materiales finos (menos de 2,0), mientras que la figura 3 es adecuada para la soldadura MIG con materiales gruesos.
En cuanto a la forma de envolver los bordes, puede determinarse en función de la situación real, considerando generalmente el ángulo de flexióny es mejor utilizar el lado largo para envolver el lado corto.
4. Posicionamiento de la soldadura:
Cuando se sueldan dos o más piezas, se requiere una relación que pueda determinar la posición de cada una, lo que constituye el problema de posicionamiento.
En función de si la propia pieza tiene una estructura de posicionamiento, se puede dividir en autoposicionamiento y posicionamiento de fijación.
A continuación se describen estos dos tipos de posicionamiento por separado:
(1) Autoposicionamiento:
En una pieza se realiza un determinado saliente o paso reservado, y en la otra pieza se realiza el correspondiente rebaje u orificio para realizar el posicionamiento entre las piezas.
Actualmente, los tipos más utilizados son dos: media cizalla - colocación en fosa cóncava y espiga - colocación en ranura cuadrada.
La estructura típica de la colocación de media cizalla - fosa cóncava se muestra en la figura siguiente.
En los casos en que los requisitos no son elevados (como cuando la superficie soldada de la pieza no es visible), la fosa cóncava puede transformarse en un orificio pasante, pero está terminantemente prohibido hacer un orificio pasante si la pieza está expuesta al exterior.
Otra estructura alternativa de este método es convertir la media cizalla circular y la fosa cóncava en un rectángulo, pero no es recomendable.
El procesamiento de media cizalla y fosa cóncava se realiza generalmente en NCT. Ambas especificaciones de media cizalla, ya sea ascendente o descendente, disponen de utillaje.
No existe un utillaje específico para las picaduras cóncavas frontales, pero pueden procesarse mediante el uso de herramientas combinadas.
Existe un utillaje específico para picaduras cóncavas inversas con un diámetro de 3,1, pero actualmente no existe ningún utillaje para picaduras cóncavas inversas con un diámetro de 2,4, y no se pueden procesar.
El método de utilizar el posicionamiento de media cizalla - fosa cóncava tiene ciertas limitaciones: debido a la adopción de la estructura de media cizalla, el efecto de media cizalla no es ideal para placas gruesas (por encima de T2,0), y la parte saliente de la media cizalla tiene forma de arco y no puede servir como función limitadora.
Y como la fosa cóncava se forma apretando a la fuerza el material, sólo puede aplicarse a materiales relativamente blandos (como AL, CRS, GI, etc.), y es imposible conseguirlo en materiales más duros (como SPHC, SUS, etc.).
En resumen, este método es adecuado para materiales con un rango de 2,0 mm o menos de GI, CRS y AL chapa metálica.
La colocación de la espiga - ranura cuadrada se muestra en la figura siguiente:
Cuando se utiliza este tipo de método de posicionamiento, el primer paso es determinar las especificaciones de la ranura de posicionamiento.
Si se utiliza el corte NCT, es mejor considerar que el agujero cuadrado se puede mecanizar en una sola pasada con herramientas NCT.
Si corte por láser el tamaño puede determinarse en función de la situación real. Por lo general, el agujero de la ranura puede ser 0,1 mm mayor que la espiga, y la parte que sobresale de la espiga no debe superar el espesor de la placa en la ranura de posicionamiento.
La ranura no tiene que ser necesariamente un agujero rectangular (tipo cerrado) y puede hacerse de tipo abierto en función de la situación específica.
(2) Ámbito de aplicación de dos métodos de autoposicionamiento:
Comparando los dos métodos de posicionamiento anteriores, se puede observar que cuando las superficies de soldadura de dos piezas de trabajo son paralelas entre sí, el método de posicionamiento de media cizalla y fosa cóncava es mejor.
Cuando las superficies de soldadura de dos piezas son perpendiculares entre sí, el método de posicionamiento espiga - ranura cuadrada es más adecuado.
(3) Posicionamiento de la fijación:
Si el autoposicionamiento no puede cumplir los requisitos del plano o se necesitan elevados requisitos de posicionamiento, se puede utilizar un sistema especial de sujeción Hay que hacer arreglos y cooperar con los departamentos pertinentes (como el de investigación y desarrollo de la automatización).
5. Requisitos del proceso de soldadura por puntos:
(1) Espesor total de la soldadura por puntos:
El grosor total de la soldadura por puntos no debe superar los 8 mm, y el tamaño del punto de soldadura suele ser de 2T+3 (2T representa el grosor de las dos partes soldadas).
Dado que el electrodo superior es hueco y está refrigerado por agua de refrigeración, no puede reducirse sin límite, y el diámetro mínimo suele ser de 3-4 mm.
(2) Punzonado y rebabado de puntos de soldadura:
La pieza de trabajo de la soldadura por puntos debe perforar y rebabar puntos de soldadura en una de las superficies que están en contacto entre sí para aumentar resistencia a la soldadura.
Por lo general, el tamaño de la rebaba es Φ1,5-2,5 mm, y la altura es de aproximadamente 0,3 mm. El procesamiento de algunas pequeñas protuberancias en una de las piezas a soldar puede mejorar el proceso de soldadura.
Como se muestra en la figura siguiente, cuando el cabezal de soldadura presiona el saliente durante el proceso de soldadura y se aplica electricidad, el pequeño saliente se funde, haciendo que la conexión sea más firme y fiable.
(3) Distancia entre dos soldaduras:
A medida que aumenta el espesor de la pieza soldada, también aumenta la distancia entre las dos soldaduras.
Si la distancia es demasiado pequeña, la pieza es propensa al sobrecalentamiento y la deformación, mientras que si es demasiado grande, la resistencia de la unión puede ser insuficiente y pueden aparecer grietas entre las dos piezas.
En general, la distancia entre dos soldaduras no debe superar los 35 mm (para materiales inferiores a 2 mm).
(4) Separación entre las piezas soldadas:
Antes de la soldadura por puntos, la separación entre las dos piezas no debe superar los 0,8 mm.
Cuando la pieza se dobla y luego se suelda por puntos, la posición y la altura de las soldaduras son muy importantes.
Si no se colocan correctamente, la soldadura por puntos puede desalinearse o deformarse, dando lugar a errores mayores.
(5) Daños superficiales causados por la soldadura por puntos:
Es fácil que se formen rebabas en el punto de soldadura por puntos, que hay que pulir y antioxidar.
Cuando sea necesario, la zona de soldadura por puntos puede recubrirse con pintura plateada. Si es necesario pintar la zona de soldadura por puntos, debe pulirse antes de pintarla.
(6) Soldadura por puntos de chapas de acero galvanizado:
Las chapas de acero galvanizado incluyen principalmente chapas galvanizadas, chapas recubiertas de plomo, chapas recubiertas de aluminio y chapas recubiertas de estaño, etc.
En la producción, es habitual la soldadura por puntos de chapas de acero galvanizado y piezas galvanizadas.
El grosor de la capa de zinc suele ser inferior a 20um.
En comparación con la soldadura por puntos de chapas de acero ordinarias, la presencia del revestimiento de zinc no sólo reduce la densidad de corriente en la zona de soldadura, sino que también hace que la distribución del campo de corriente sea inestable.
El aumento de la corriente también favorece aún más la formación de la aleación Cu-Zn en la cara del extremo de trabajo del electrodo, lo que acelera el desgaste del electrodo y el daño del revestimiento.
Al mismo tiempo, el revestimiento de zinc de bajo punto de fusión provoca la aparición de grietas y poros durante el proceso de cristalización del zona de fusión.
Por lo tanto, el rango de especificaciones de soldadura por puntos adecuado para las chapas de acero galvanizado es estrecho, y la resistencia de la unión fluctúa mucho, con una soldabilidad deficiente.
(7) Gama de procesamiento de interferencias de la soldadura por puntos:
A continuación se muestra un diagrama esquemático de la soldadura por puntos mediante una máquina de soldar, con los datos que indican el rango de procesamiento proporcionados por el grupo de soldadura por puntos el 16 de octubre de 2000.
1. Definición
El remachado por extrusión de orificios es un proceso que conecta dos piezas, una con un orificio perforado y otra con un orificio avellanado, utilizando una matriz de remachado para formar una unión inseparable.
Ventajas: El punzonado y el avellanado proporcionan un posicionamiento inherente para las dos piezas. El remachado por extrusión de orificios da como resultado una unión de gran resistencia y alta eficiencia mediante el uso de utillaje especializado.
Hoja de datos de remaches avellanados
Número de artículo Número de serie | Espesor del materialT(mm) | Altura del avellanadorH(mm) | Diámetro exterior del avellanador D(mm) | |||||||||||
3.0 | 3.8 | 4.0 | 4.8 | 5.0 | 6.0 | |||||||||
Correspondiente al diámetro interior d de la avellanadora y al orificio prepunzonado d0 | ||||||||||||||
d | d0 | d | d0 | d | d0 | d | d0 | d | d0 | d | d0 | |||
1 | 0.5 | 1.2 | 2.4 | 1.5 | 3.2 | 2.4 | 3.4 | 2.6 | 4.2 | 3.4 | / | / | / | / |
2 | 0.8 | 2.0 | 2.3 | 0.7 | 3.1 | 1.8 | 3.3 | 2.1 | 4.1 | 2.9 | 4.3 | 3.2 | / | / |
3 | 1.0 | 2.4 | / | / | / | / | 3.2 | 1.8 | 4.0 | 2.7 | 4.2 | 2.9 | 5.2 | 4.0 |
4 | 1.2 | 2.7 | / | / | / | / | 3.0 | 1.2 | 3.8 | 2.3 | 4.0 | 2.5 | 5.0 | 3.6 |
5 | 1.5 | 3.2 | / | / | / | / | 2.8 | 1.0 | 3.6 | 1.7 | 3.8 | 2.0 | 4.8 | 3.2 |
Nota: El principio general del remachado avellanado es H=T+T'+(0,3~0,4), D=D'-0,3, y D-d=0,8T. Cuando T≧0,8mm, el espesor de la pared del avellanado es 0,4T. Cuando T<0.8mm, el espesor de la pared del avellanador es usualmente 0.3mm. H' se suele tomar como 0,46±0,12.
1. Clasificación:
Los remaches de tracción se dividen en dos tipos: de cabeza plana y de cabeza redonda (también conocidos como cabeza de paraguas).
Para remaches de cabeza plana, el lado en contacto con la cabeza del remache debe tener un agujero avellanado. Para remaches de cabeza redonda, la superficie de contacto es plana.
2. Definición:
Tirar del vástago del remache a través de las dos piezas con orificios pasantes utilizando una pistola remachadora hasta que se rompa, haciendo que el manguito exterior del remache se expanda y se convierta en una conexión no desmontable.
3. Parámetros de la unión remachada por tracción:
Categoría de remaches. | El diámetro nominal del remache D | El diámetro del orificio para remachar chapas de acero D1 | LongitudL | M | Diámetro de la cabeza H | Altura de la cabeza P | Espesor del chapa de acero para remachar | Resistencia a la rotura.(N) | |||
En forma de paraguas | Cabeza plana | avellanado | cabeza plana con resistencia al cizallamiento | Resistencia al cizallamiento | resistencia a la tracción | ||||||
Remache ciego de aluminio | 2.4 | 2.5 | 5.7 7.3 8.9 | 1.42 | 4.8 | 0.7 | 0.8 | 1.0~3.2 3.2~4.8 4.8~6.4 | 1.6~3.2 3.2~4.8 4.8~6.4 | 490 | 735 |
3.0 | 3.1 | 6.3 8.0 9.8 | 1.83 | 6.0 | 0.9 | 1.0 | 1.0~3.2 3.2~4.8 4.8~6.4 | 1.6~3.2 3.2~4.8 4.8~6.4 | 735 | 1180 | |
3.2 | 3.3 | 6.3 8.0 9.8 | 1.83 | 6.4 | 0.9 | 1.1 | 1.6~3.2 3.2~4.8 4.8~6.4 | 1.6~3.2 3.2~4.8 4.8~6.4 | 930 | 1420 | |
4.0 | 4.1 | 6.9 8.6 10.4 | 2.28 | 8.0 | 1.2 | 1.4 | 1.2~3.2 3.2~4.8 4.8~6.4 | 1.6~3.2 3.2~4.8 4.8~6.4 | 1470 | 2210 | |
remache de aluminio | 4.8 | 4.9 | 7.5 9.3 11.1 | 2.64 | 9.6 | 1.4 | 1.6 | 1.6~3.2 3.2~4.8 4.8~6.4 | 2.3~3.2 3.2~4.8 4.8~6.4 | 2260 | 3240 |
remache de tracción de acero | 3.2 | 3.3 | 6.4 9.5 | 1.93 | 9.5 | 1.0 | 1.0~3.2 3.2~6.4 | 1270 | 1770 | ||
4.0 | 4.1 | 10.2 | 2.41 | 11.9 | 1.25 | 3.2~6.4 | 2060 | 2940 | |||
4.8 | 4.9 | 10.8 | 2.90 | 15.9 | 1.9 | 3.2~6.4 | 2750 | 3920 |
Nota: El diámetro del agujero pasante para el remache en la pieza suele ser 0,2~0,3 mm mayor que el diámetro nominal D del remache. La distancia desde el centro del agujero del remache hasta el borde debe ser superior a 2 veces el tamaño del agujero del remache para obtener la mejor resistencia de remachado. Si la distancia es demasiado pequeña, la resistencia se reducirá considerablemente.
4. Diagrama de las formas de los remaches:
Nota:
(1) Los remaches de tracción de cabeza plana se utilizan principalmente para superficies con requisitos estrictos en las que no se permite conectar elementos de fijación que sobresalgan. La cabeza plana del remache se introduce en un orificio avellanado del elemento de fijación para que la cabeza no sobresalga de la superficie.
(2) El color del remache de tracción puede adaptarse a la pieza de montaje mediante ennegrecimiento u otros tratamientos para satisfacer los requisitos del cliente. Por ejemplo, la cabeza del remache de tracción puede pintarse para permitir el remachado en piezas pintadas.
5. Para el remache de tracción más utilizado, 3B010-01
Se trata del remache de tracción de cabeza plana y extremo abierto mencionado anteriormente. El diámetro exterior D del remache es de 0,125 pulgadas, es decir, 3,175 mm. El agujero avellanado correspondiente es Φ6.5XΦ3.5X120°, y el agujero pasante correspondiente es Φ3.4.