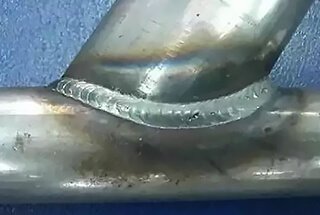
La soldadura de estructuras de acero exige precisión y experiencia. ¿Qué errores comunes pueden poner en peligro sus proyectos de soldadura? En este artículo, exploramos consejos esenciales para soldar con éxito estructuras de acero. Aprenda a manejar las tensiones de soldadura, a reducir las deformaciones y a conocer los mejores métodos de soldadura para diferentes situaciones. Si domina estas técnicas, se asegurará de que sus soldaduras sean resistentes, fiables y cumplan las normas más exigentes. Descubra las estrategias clave para elevar sus habilidades de soldadura y mejorar la integridad de sus estructuras de acero.
Ventajas de la conexión por soldadura:
Estructura simple, sin debilitamiento de la sección de componentes, procesamiento sencillo, diversos métodos de soldaduraEl funcionamiento es automático, ahorra acero, tiene alta eficiencia, gran rigidez, buena integridad y buen rendimiento de sellado.
Desventajas de la conexión por soldadura:
La zona del acero afectada por el calor sufre cambios en su estructura metalográfica, lo que provoca que los materiales locales se vuelvan frágiles.
La soldadura produce tensión residual y deformación, que disminuyen la capacidad portante de los elementos de compresión.
Las estructuras soldadas son muy susceptibles al agrietamiento. Si se producen grietas locales, son propensas a propagarse ampliamente, y la fragilidad en frío a baja temperatura es más pronunciada.
Acero soldabilidad se refiere a la facilidad con la que los materiales pueden soldarse cumpliendo las prestaciones estructurales requeridas en condiciones de diseño y trabajo adecuadas. La soldabilidad del acero suele estar influida por su composición química, método de laminacióny el espesor de la chapa.
Para evaluar el impacto de la composición química sobre la soldabilidad, ésta se expresa generalmente en carbono equivalente (Ceq). El soldabilidad del acero es mejor cuando el Ceq es menor porque indica una menor tendencia al endurecimiento del material. Por el contrario, cuando el Ceq es mayor, la soldabilidad del acero es peor debido a su mayor tendencia al endurecimiento.
El valor de carbono equivalente Ceq (porcentaje) puede calcularse mediante la siguiente fórmula:
En proceso de soldadura de una estructura de acero implica un calentamiento y enfriamiento desiguales. Durante la soldadura, la temperatura de la soldadura y sus alrededores es muy alta, mientras que el metal situado a cierta distancia permanece sin calentar. Como resultado, la expansión y contracción del metal principal es desigual.
Al enfriarse, el cordón de soldadura experimentará diversos grados de contracción y tensión interna (tanto longitudinales como transversales), lo que provoca diferentes deformaciones en la estructura de soldadura.
Para reducir la tensión y la deformación de la soldadura, se pueden abordar dos aspectos: el diseño y la tecnología de procesamiento.
Medidas de diseño:
La posición de la soldadura debe estar razonablemente dispuesta.
La selección del tamaño de la soldadura debe basarse en la razonabilidad.
El número de soldaduras debe mantenerse al mínimo y no deben estar excesivamente concentradas. Además, es esencial evitar crear un entrecruzamiento tridimensional de soldaduras.
Es importante evitar en la medida de lo posible las tensiones de contracción en la dirección del espesor del metal base.
Medidas de proceso:
Organizar razonablemente la secuencia de soldadura;
Adoptar la deformación inversa;
Precalentamiento antes de soldar y templado después de la soldadura.
Los métodos de soldadura más utilizados en estructuras de acero son la soldadura por arco manual, la soldadura por arco sumergido automática (o semiautomática) y la soldadura con gas de protección.
Lectura relacionada: Soldadura por arco manual frente a soldadura con gas protector de CO2
Soldadura por arco manual:
Tras ser electrificado, se genera un arco eléctrico para fundir el hilo de soldadura en el electrodo y dejarlo caer en el pequeño charco de fusión de la ranura soplado por el arco eléctrico en la pieza soldada.
La escoria y el gas formados por el revestimiento del electrodo cubren el baño de fusión para evitar que el aire entre en contacto con el metal líquido fundido y se formen compuestos frágiles y propensos a las grietas.
Soldadura por arco sumergido:
Este método de soldadura utiliza un arco que arde bajo una capa de fundente. A diferencia de los métodos tradicionales, el hilo de soldadura no se recubre con ningún material adicional. En su lugar, el extremo de soldadura está cubierto por fundente granular, que fluye automáticamente desde el cabezal de fuga de fundente.
Como resultado, el arco queda completamente enterrado en el fundente, lo que hace que el calor se concentre y penetre profundamente. Esto lo convierte en un método ideal para soldar chapas gruesas con una alta productividad manteniendo una buena calidad de soldadura y una deformación mínima de la soldadura.
Soldadura con gas protector:
Se trata de un método de soldadura por fusión de arco que emplea dióxido de carbono u otros gases inertes como medio protector. El gas protector forma una capa protectora local alrededor del arco, que ayuda a evitar la invasión de gases nocivos y garantiza la estabilidad del proceso de soldadura.
En comparación con la soldadura por arco manual, este método produce soldaduras de mayor resistencia, excelente plasticidad y resistencia a la corrosión. Es adecuado para todas las soldaduras de posición, incluidos los métodos de avance y retroceso.
A continuación se muestran las posiciones de soldadura, formas de unión, formas de ranura, tipos de soldadura y códigos de forma de nodos de estructura de tuberías más comunes:
Código | Posición de soldadura |
F | soldadura descendente |
H | Soldadura en posición horizontal |
V | Soldadura vertical |
O | Soldadura en posición elevada |
Lectura relacionada: ¿Qué significan 1G, 2G, 3G, 4G, 5G y 6G en soldadura?
Tipo de junta y código de forma de la ranura
Tipo de articulación | Forma de la ranura | ||||
Código | Nombre | Código | Nombre | ||
I | Ranura en I | ||||
Junta de la placa | B | Junta a tope | V | Ranura en V | |
T | Junta en T | X | Ranura en X | ||
X | cruz de tubo | L | Ranura en V unilateral | ||
C | unión en filete | K | Ranura en K | ||
F | Junta solapada | U1 | Ranura en U | ||
Junta de tubo | T | Junta en T | J1 | Ranura en U unilateral | |
K | Junta K | Nota: 1. Cuando el espesor de la chapa de acero es ≥ 50mm, se puede utilizar ranura en forma de U o en forma de J. | |||
Y | Junta en Y |
En defectos de soldadura se dividen en seis categorías: grietas, cavidades, inclusiones sólidas, fusión incompleta, penetración incompleta y defectos de forma.
Crujido:
Grietas calientes y grietas frías son dos tipos comunes de defectos de soldadura.
Las grietas en caliente se deben principalmente a la escasa resistencia a la fisuración del metal de base, la baja calidad materiales de soldaduraUna selección inadecuada de los parámetros del proceso de soldadura y una tensión interna de soldadura excesiva.
Por otra parte, las grietas frías suelen ser el resultado de un diseño poco razonable de la estructura de soldadura, una disposición inadecuada de los cordones de soldadura y unas medidas inadecuadas del proceso de soldadura, como la falta de precalentamiento antes de soldar y de enfriamiento rápido después de soldar.
Para tratar este tipo de grietas, uno de los métodos consiste en perforar orificios de detención de grietas en ambos extremos de la grieta o retirar el metal de soldadura en la grieta para realizar una soldadura de reparación.
Cavidad:
Los defectos en la soldadura se dividen generalmente en dos tipos: agujeros de aire y contracción de cráteres.
Los agujeros de aire están causados principalmente por varios factores, entre los que se incluyen daños graves en el revestimiento del electrodo, falta de cocción del electrodo y el fundente, manchas de aceite u óxido en el metal base, corriente de soldadura insuficiente, longitud de arco excesivamente larga y rápida velocidad de soldadura.
El tratamiento de los orificios de aire consiste en eliminar el metal de soldadura defectuoso en el lugar del orificio de aire y, a continuación, realizar un procedimiento de soldadura de reparación.
La contracción en cráter, por otro lado, está causada principalmente por una corriente de soldadura excesiva, una alta velocidad de soldadura, un enfriamiento rápido del arco y una adición insuficiente de metal de aportación para enfriar repetidamente el arco.
El tratamiento para la contracción del cráter consiste en realizar una operación de soldadura de reparación en el lugar del cráter.
Inclusión sólida:
Existen dos tipos de defectos que pueden producirse durante la soldadura: la inclusión de escoria y la inclusión de wolframio.
Las principales causas de la inclusión de escoria son la escasa calidad de la soldadura materiales, soldadura con una corriente demasiado baja, soldadura a una velocidad demasiado rápida, alta densidad de escoria que bloquea la capacidad de flotación de la escoria y la no limpieza de la escoria durante la soldadura multicapa.
Para remediar la inclusión de escoria, debe eliminarse el metal de soldadura alrededor de la zona afectada y, a continuación, puede continuar el proceso de soldadura.
La inclusión de wolframio se produce normalmente cuando el electrodo de wolframio entra en contacto con el metal de la piscina fundido durante soldadura por arco de argón.
Para reparar este defecto, hay que excavar el metal defectuoso en la inclusión de tungsteno, y entonces se puede reanudar el proceso de soldadura.
Fusión y penetración incompletas:
Hay varias razones principales para una soldadura incompleta, incluyendo una corriente de soldadura demasiado pequeña, una velocidad de soldadura demasiado rápida, una separación de ángulo de ranura demasiado pequeña y una tecnología de funcionamiento deficiente.
El método de tratamiento de la no fusión consiste en eliminar el metal de soldadura en la posición de no fusión y, a continuación, reparar la soldadura.
Para tratar la penetración incompleta, el método consiste en reparar la penetración incompleta en un lado de la estructura con buena apertura directamente en la parte posterior de la soldadura.
En el caso de soldaduras importantes que no pueden repararse directamente mediante soldadura, debe eliminarse el metal de soldadura incompleto y volver a realizarse la soldadura.
Defecto de forma:
Incluidos socavado, solapamiento, pandeo, contracción de la raíz, desalineación, desviación del ángulo, peralte de la soldadura, irregularidad de la superficie, etc.
Para las uniones en forma de T, en forma de cruz y en esquina, cuando el espesor de la placa de la brida no es inferior a 20 mm, con el fin de evitar o reducir la gran tensión de contracción de la soldadura en la dirección del espesor de la placa de metal base, se debe adoptar el siguiente diseño de la estructura de la unión:
Cambie la dirección de la tensión de la junta de la placa gruesa para reducir la tensión en la dirección del espesor;
Para los nudos sometidos a carga estática, bajo la condición de cumplir los requisitos del cálculo de la resistencia de la unión, la soldadura de ranura totalmente penetrada se sustituirá por la soldadura a tope parcialmente penetrada y soldadura en ángulo.
Una vez finalizada la soldadura y la inspección de la misma, el primer paso de la inspección será la inspección del aspecto. Se utilizará la inspección visual o una lupa para observar si hay defectos como socavaduras, quemaduras, penetración incompleta, grietas, bordes escalonados, estancamiento, y para comprobar si las dimensiones generales de la soldadura cumplen los requisitos.
Los defectos en el interior de la soldadura suelen detectarse mediante ondas ultrasónicas. Este método se basa en el principio de que las ondas ultrasónicas pueden propagarse dentro del metal y reflejarse y refractarse al encontrar la interfaz de dos medios, lo que ayuda a inspeccionar los defectos dentro de la soldadura. La forma de onda puede utilizarse para determinar la presencia y la ubicación del defecto.
Dado que existe una superficie reflectante entre la sonda y la pieza de ensayo, durante la inspección por ultrasonidos, el agente de acoplamiento debe recubrir la superficie de la soldadura. Sin embargo, el método ultrasónico no puede determinar el tipo y el tamaño de los defectos.
La inspección radiográfica se utiliza a veces en ensayos no destructivos para detectar defectos en las soldaduras. Existen dos tipos de inspección radiográfica: La inspección por rayos X y la inspección por rayos γ. El principio es que cuando el rayo pasa a través de la soldadura inspeccionada, cualquier defecto provocará una menor atenuación del rayo que pasa por esa zona.
Como resultado, la película negativa del reverso de la soldadura es muy sensible a la luz, y aparecerán manchas o rayas negras en el lugar del defecto después de lavar la película.
La inspección por rayos X tiene un tiempo de exposición corto, alta velocidad y gran capacidad de penetración, pero el equipo es complejo, costoso y adecuado para probar soldaduras con un grosor inferior a 30 mm. En cambio, los equipos de inspección por rayos gamma son portátiles, fáciles de manejar y tienen una gran capacidad de penetración.
Criterios de aceptación de lotes de soldaduras:
Criterios de inspección adicionales:
Aparte de las exenciones enumeradas en el código nacional de soldadura de estructuras de acero, cualquier combinación de acero, materiales de soldadura, métodos de soldadura, formas de unión, posiciones de soldadura, sistemas de tratamiento térmico posterior a la soldadura, parámetros del proceso de soldadura, medidas de precalentamiento y postcalentamiento, y otros parámetros utilizados por la unidad de construcción por primera vez, deberán someterse a una evaluación del proceso de soldadura antes de fabricar e instalar los elementos de la estructura de acero.